Change Your Cabin Air Filter: How Often to Change It (2025)
Introduction: Navigating the Global Market for how often to change cabin air filter
Navigating the complexities of the global market can be a daunting task for B2B buyers, especially when it comes to sourcing the right components for vehicle maintenance. One of the critical components often overlooked is the cabin air filter. Understanding how often to change cabin air filters is essential for ensuring optimal air quality and vehicle performance, which directly impacts customer satisfaction and operational efficiency.
This guide delves into the various types of cabin air filters available, their applications across different vehicle models, and the best practices for maintenance. It also addresses the importance of supplier vetting, allowing you to identify trustworthy partners who can provide high-quality products at competitive prices. Additionally, we will explore the cost implications of cabin air filter replacements, helping you make informed budgetary decisions that align with your business objectives.
For international B2B buyers, particularly those operating in diverse markets such as Africa, South America, the Middle East, and Europe, this guide serves as a vital resource. By equipping you with actionable insights and data-driven recommendations, we empower you to make strategic purchasing decisions that enhance operational efficiency and improve the overall customer experience. Whether you’re in Brazil, Thailand, or any other region, understanding the nuances of cabin air filter maintenance can help you stay ahead in a competitive landscape.
Understanding how often to change cabin air filter Types and Variations
Type Name | Key Distinguishing Features | Primary B2B Applications | Brief Pros & Cons for Buyers |
---|---|---|---|
Standard Replacement Schedule | Change every 15,000 to 30,000 km or annually | Fleet management, logistics companies | Pros: Consistent performance; Cons: May be excessive for low-mileage users. |
Heavy-Duty Filters | Designed for extreme conditions; change every 10,000 km | Mining, construction, and agricultural sectors | Pros: Enhanced filtration; Cons: Higher initial cost. |
Seasonal Change Approach | Change based on seasonal use (e.g., before summer) | Tourism, hospitality vehicles | Pros: Optimizes air quality for specific conditions; Cons: Requires tracking seasonal usage. |
Advanced Filtration Systems | Incorporate activated charcoal or HEPA; change every 20,000 km | High-end transportation services | Pros: Superior air quality; Cons: More expensive and complex installation. |
DIY Maintenance Schedule | User-replaceable filters; check every 5,000 km | Small businesses with in-house mechanics | Pros: Cost-effective; Cons: Requires basic mechanical knowledge. |
What is the Standard Replacement Schedule for Cabin Air Filters?
The Standard Replacement Schedule recommends changing cabin air filters every 15,000 to 30,000 kilometers or at least once a year. This approach is widely adopted across various sectors, including fleet management and logistics companies. It ensures that vehicles maintain optimal air quality and performance. B2B buyers should consider their fleet’s mileage and operational conditions, as excessive replacements may lead to unnecessary costs, especially for low-mileage vehicles.
How Do Heavy-Duty Filters Differ from Standard Filters?
Heavy-Duty Filters are designed for extreme conditions and are typically recommended to be changed every 10,000 kilometers. These filters are essential for industries such as mining, construction, and agriculture, where dust and particulate matter are prevalent. While they provide enhanced filtration capabilities, the initial investment is higher than standard filters. B2B buyers in these sectors should weigh the benefits of improved air quality against the increased costs.
Why Consider a Seasonal Change Approach?
The Seasonal Change Approach suggests changing cabin air filters based on usage patterns, particularly before high-demand seasons like summer or winter. This method is particularly beneficial for businesses in tourism and hospitality, where vehicles are used more intensively during specific times of the year. Although it optimizes air quality for seasonal conditions, it requires meticulous tracking of vehicle usage, which may add administrative burden for some companies.
What Are the Benefits of Advanced Filtration Systems?
Advanced Filtration Systems incorporate technologies such as activated charcoal or HEPA filters and are generally recommended for replacement every 20,000 kilometers. These systems are ideal for high-end transportation services that prioritize air quality for passengers. While they offer superior filtration, the costs and complexities associated with installation can be a deterrent for some buyers. Organizations must assess their customer base and service level expectations when considering this option.
How Can a DIY Maintenance Schedule Benefit Small Businesses?
A DIY Maintenance Schedule allows businesses with in-house mechanics to replace cabin air filters themselves, typically suggesting checks every 5,000 kilometers. This approach is especially advantageous for small businesses looking to reduce maintenance costs. However, it requires some mechanical knowledge and may not be suitable for all organizations. B2B buyers should evaluate their workforce skills and the potential savings before opting for this maintenance strategy.
Related Video: How To: Change Your Vehicle’s Cabin Air Filter
Key Industrial Applications of how often to change cabin air filter
Industry/Sector | Specific Application of how often to change cabin air filter | Value/Benefit for the Business | Key Sourcing Considerations for this Application |
---|---|---|---|
Automotive Manufacturing | Regular maintenance schedules for assembly line vehicles | Enhances air quality for workers and reduces equipment wear | Ensure compatibility with various vehicle models and OEM standards |
Public Transportation | Maintenance protocols for buses and trains | Improves passenger comfort and safety, reducing health risks | Bulk purchasing agreements with reliable suppliers |
Agriculture | Air quality management in agricultural vehicles | Protects equipment and enhances operator health | Sourcing filters that withstand harsh environmental conditions |
Construction | Air filtration in heavy machinery and site vehicles | Reduces downtime and maintenance costs | Consider filters with high dust-holding capacity |
Mining | Cabin air quality control in mining vehicles | Ensures operator safety and compliance with health regulations | Evaluate filters for durability and resistance to contaminants |
How is the Cabin Air Filter Change Frequency Applied in Automotive Manufacturing?
In the automotive manufacturing sector, maintaining a regular schedule for changing cabin air filters is crucial. This practice not only enhances the air quality for assembly line workers but also reduces wear on manufacturing equipment. For international B2B buyers, especially those in Africa and South America, understanding the specific OEM standards and compatibility of filters with various vehicle models is essential. This ensures compliance and promotes operational efficiency, ultimately leading to a safer and more productive work environment.
What Role Does Cabin Air Filter Maintenance Play in Public Transportation?
For public transportation systems, such as buses and trains, the frequency of cabin air filter changes directly impacts passenger comfort and safety. Regular maintenance protocols help mitigate health risks associated with poor air quality, which is particularly vital in densely populated urban areas in Europe and the Middle East. B2B buyers in this sector should consider bulk purchasing agreements with reliable suppliers to ensure consistent quality and availability of filters, thus optimizing operational costs and enhancing service quality.
How is Cabin Air Filter Management Relevant in Agriculture?
In agriculture, the air quality within agricultural vehicles is paramount for operator health and equipment longevity. Regularly changing cabin air filters can help protect sensitive machinery from dust and contaminants, which is particularly important in regions with harsh environmental conditions, such as parts of Africa and South America. B2B buyers in this industry must source filters that are robust and designed to withstand these challenges, ensuring minimal downtime and maximum productivity in the field.
Why is Cabin Air Filter Maintenance Critical for Construction Equipment?
In the construction industry, maintaining air quality in heavy machinery and site vehicles is essential for both operator safety and equipment performance. Regularly changing cabin air filters reduces downtime and lowers maintenance costs, which is crucial for project timelines and budgets. Buyers should focus on sourcing filters with a high dust-holding capacity to ensure longevity and effectiveness, especially in construction sites located in dusty or polluted environments.
How Does Cabin Air Filter Quality Impact Mining Operations?
In mining operations, controlling cabin air quality in vehicles is critical for ensuring operator safety and compliance with health regulations. Regularly changing cabin air filters helps to mitigate exposure to harmful dust and particulate matter, which can be prevalent in mining environments. International B2B buyers should evaluate filters for their durability and resistance to contaminants, ensuring that they meet the rigorous demands of mining operations while also adhering to safety standards.
Related Video: How To Change A Cabin Air Filter (And Why You Should Do It)
3 Common User Pain Points for ‘how often to change cabin air filter’ & Their Solutions
Scenario 1: Inconsistent Cabin Air Quality Across Fleets
The Problem:
For international B2B buyers managing fleets of vehicles, ensuring consistent air quality can be a challenge. Many fleet managers struggle with varying cabin air filter replacement schedules across different vehicle models and makes. This inconsistency can lead to poor air quality, affecting driver comfort and health, and ultimately impacting productivity. Additionally, many fleet operators may not be aware of the specific needs of each vehicle type, leading to neglect in maintenance schedules.
The Solution:
To address this issue, fleet managers should implement a standardized maintenance protocol that includes a clear schedule for cabin air filter changes based on manufacturer recommendations and usage conditions. Investing in a fleet management software that tracks maintenance schedules can be invaluable. This software should allow users to input the make and model of each vehicle, automatically generating alerts for when filters need changing. Furthermore, conducting regular training sessions for maintenance staff on the importance of cabin air quality can help reinforce best practices. By centralizing information and using technology, fleet managers can ensure that all vehicles maintain optimal air quality.
Scenario 2: Cost Concerns Over Frequent Filter Changes
The Problem:
B2B buyers often face budget constraints when it comes to vehicle maintenance, and cabin air filters are sometimes overlooked in favor of more pressing repairs. This can lead to a false economy; while saving money in the short term, ignoring filter changes can result in increased vehicle wear and tear, higher fuel consumption, and ultimately, more costly repairs. Buyers in regions with harsh climates, like the Middle East or parts of Africa, may find their filters clogging more quickly, compounding the cost issues.
The Solution:
To mitigate costs while maintaining air quality, B2B buyers should consider investing in high-efficiency particulate air (HEPA) filters, which can last longer than standard filters and provide better air quality. Additionally, conducting a cost-benefit analysis comparing the expenses of frequent replacements versus the costs associated with vehicle inefficiencies can provide a clearer picture. Building a maintenance budget that accounts for cabin air filter changes as a necessary operating expense will help prioritize this aspect of vehicle upkeep. Moreover, negotiating bulk purchase agreements with suppliers can significantly reduce filter costs, ensuring that quality maintenance is not sacrificed for budgetary concerns.
Scenario 3: Lack of Awareness About Environmental Impact
The Problem:
Many B2B buyers may not fully understand the environmental impact of cabin air filters and their replacement schedules. In regions like South America and Europe, where there is a growing emphasis on sustainability and environmental responsibility, neglecting the timely change of cabin air filters can contribute to higher emissions and poor air quality. This lack of awareness can reflect poorly on a company’s sustainability initiatives and corporate responsibility.
The Solution:
To combat this knowledge gap, businesses should prioritize education on the environmental benefits of regular cabin air filter maintenance. This can include workshops, informational resources, and partnerships with environmental organizations to provide insights into how cleaner air can contribute to reduced emissions and better health outcomes. Establishing a sustainability policy that includes regular maintenance of cabin air filters can also enhance a company’s image and comply with local regulations. Furthermore, leveraging social media and corporate communications to highlight these efforts can position the company as a leader in environmental responsibility, appealing to both customers and potential business partners who value sustainability.
Strategic Material Selection Guide for how often to change cabin air filter
When selecting materials for cabin air filters, it is essential to consider various factors that influence performance, durability, and cost. This analysis will focus on four common materials: fiberglass, activated carbon, pleated paper, and synthetic fibers. Each material has distinct properties and implications for international B2B buyers, particularly in regions such as Africa, South America, the Middle East, and Europe.
What are the Key Properties of Fiberglass in Cabin Air Filters?
Fiberglass is a widely used material in cabin air filters due to its excellent filtration capabilities. It can withstand high temperatures and has a good pressure rating, making it suitable for various automotive applications. Its corrosion resistance is moderate, which is acceptable for standard environments but may not perform well in highly corrosive conditions.
Pros & Cons: Fiberglass filters are relatively low-cost and easy to manufacture, making them an economical choice for mass production. However, they tend to have a shorter lifespan compared to other materials, which may lead to increased replacement frequency and associated costs.
Impact on Application: Fiberglass filters are effective in trapping larger particles but may not be as efficient in capturing smaller pollutants or allergens. This limitation can affect customer satisfaction, particularly in regions with high air pollution levels.
Considerations for International Buyers: Compliance with local standards such as ASTM or DIN is crucial. Buyers should also assess the environmental impact of fiberglass disposal, as regulations may vary significantly across regions.
How Does Activated Carbon Enhance Cabin Air Filter Performance?
Activated carbon is renowned for its exceptional ability to absorb odors and volatile organic compounds (VOCs). It operates effectively at ambient temperatures and is resistant to moisture, which is beneficial in humid climates.
Pros & Cons: The primary advantage of activated carbon filters is their superior air quality enhancement, making them suitable for markets where air quality is a significant concern. However, they are generally more expensive to produce than fiberglass filters and may require more complex manufacturing processes.
Impact on Application: Activated carbon filters are particularly valuable in urban areas with high levels of pollution, as they can significantly improve the in-cabin air quality. This makes them a preferred choice for luxury vehicles and markets that prioritize passenger comfort.
Considerations for International Buyers: Buyers should ensure that activated carbon filters meet local health and safety regulations. Additionally, understanding the supply chain for activated carbon is essential, as sourcing may vary based on regional availability.
What are the Benefits of Using Pleated Paper in Cabin Air Filters?
Pleated paper filters are designed to increase the surface area for filtration, enhancing their ability to capture dust and pollen. They can operate effectively under a range of temperatures and pressures, making them versatile for various applications.
Pros & Cons: These filters are often cost-effective and can be manufactured with relative ease. However, they may not be as durable as synthetic options, leading to potential issues in high-humidity environments where they could degrade faster.
Impact on Application: Pleated paper filters are suitable for general use in passenger vehicles, particularly in regions with moderate air quality concerns. Their ability to trap particulates makes them a good choice for everyday driving conditions.
Considerations for International Buyers: Buyers should verify that pleated paper filters comply with international filtration standards. Additionally, understanding the local market demand for these filters can help in making informed purchasing decisions.
How Do Synthetic Fibers Compare in Cabin Air Filters?
Synthetic fibers, such as polyester or polypropylene, offer excellent durability and filtration efficiency. They can withstand a wide range of temperatures and are resistant to moisture and mold, making them suitable for various climates.
Pros & Cons: The primary advantage of synthetic fiber filters is their long lifespan and high filtration efficiency. However, they tend to be more expensive than traditional materials, which could impact budget-sensitive buyers.
Impact on Application: Synthetic filters are ideal for regions with extreme weather conditions, where durability is paramount. They are also effective in capturing smaller particles, which is increasingly important in today’s health-conscious market.
Considerations for International Buyers: Buyers should consider the availability of synthetic materials in their region and whether local manufacturers can meet quality standards. Additionally, understanding the environmental impact of synthetic materials is essential for compliance with sustainability regulations.
Summary Table of Material Selection for Cabin Air Filters
Material | Typical Use Case for how often to change cabin air filter | Key Advantage | Key Disadvantage/Limitation | Relative Cost (Low/Med/High) |
---|---|---|---|---|
Fiberglass | Standard passenger vehicles | Economical and widely available | Shorter lifespan | Low |
Activated Carbon | Luxury vehicles and urban areas with high pollution | Superior odor and VOC absorption | Higher production cost | High |
Pleated Paper | General use in moderate air quality regions | Cost-effective with good filtration | Less durable in high humidity | Medium |
Synthetic Fibers | Extreme weather conditions and health-focused markets | Long lifespan and high efficiency | Higher initial cost | High |
This comprehensive analysis provides international B2B buyers with essential insights into the strategic selection of materials for cabin air filters, helping them make informed decisions that align with their operational needs and regional market conditions.
In-depth Look: Manufacturing Processes and Quality Assurance for how often to change cabin air filter
What Are the Key Manufacturing Processes for Cabin Air Filters?
The manufacturing of cabin air filters involves several critical stages that ensure the final product meets quality standards and performance expectations. Understanding these processes is essential for B2B buyers looking to source reliable cabin air filters, particularly in regions such as Africa, South America, the Middle East, and Europe.
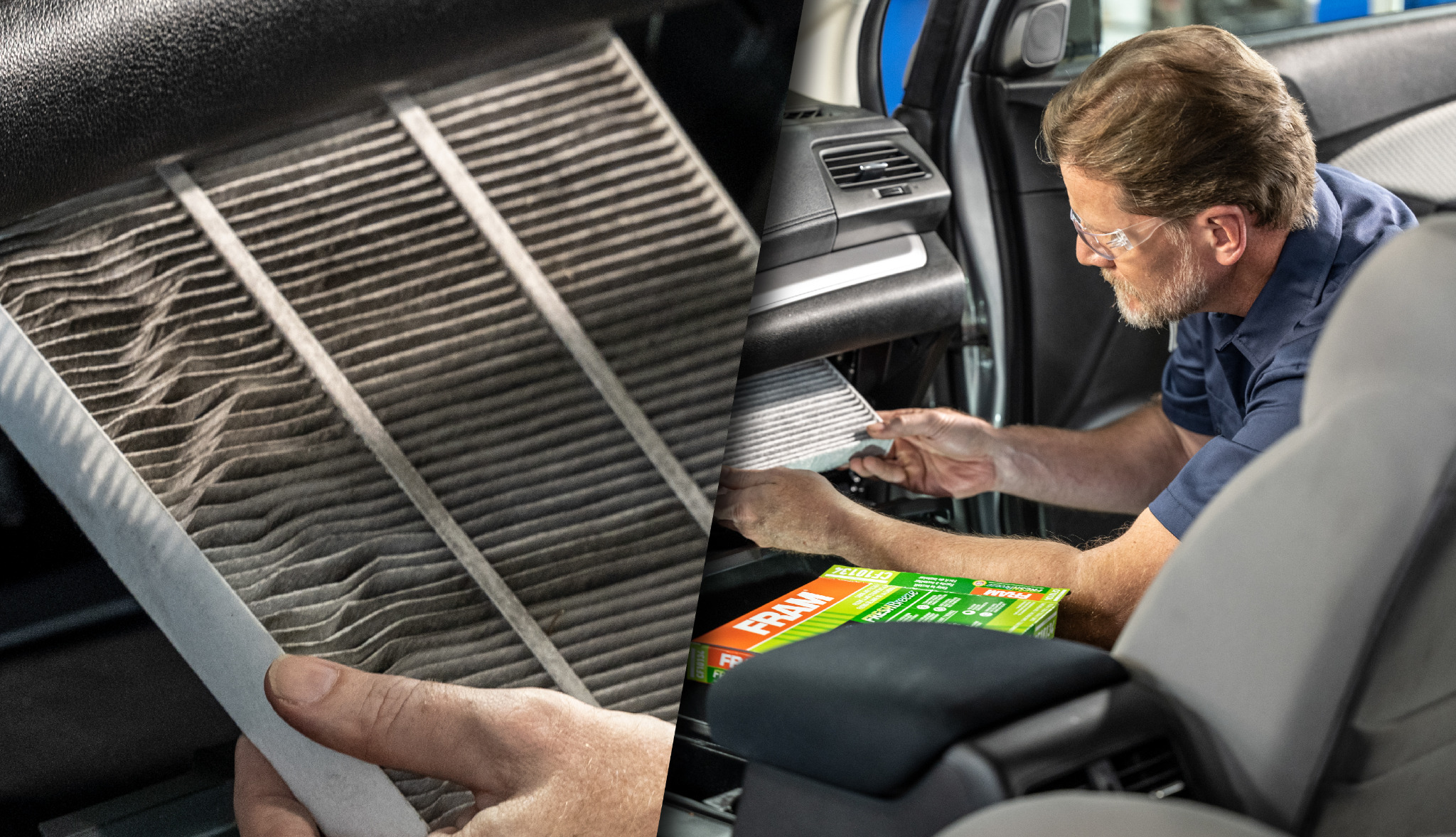
A stock image related to how often to change cabin air filter.
1. Material Preparation: What Materials Are Used in Cabin Air Filter Manufacturing?
The first stage in the manufacturing process is material preparation. Cabin air filters are typically made from a combination of synthetic fibers, activated carbon, and sometimes, electrostatic media. These materials are chosen for their ability to trap pollutants, including dust, pollen, and harmful gases.
Key Techniques:
– Fiber Blending: This involves mixing different types of fibers to achieve the desired filtration efficiency and strength.
– Impregnation: In some cases, activated carbon is impregnated with additional chemicals to enhance its adsorption properties.
2. Forming: How Are Cabin Air Filters Shaped?
After material preparation, the next step is forming the filter media into the desired shape. This process often uses techniques such as:
- Thermal Bonding: Heat is applied to fuse the fibers together without the use of adhesives, ensuring a strong and durable product.
- Die-Cutting: The shaped filter media is cut to fit specific dimensions, which is crucial for proper installation in vehicles.
3. Assembly: What Does the Assembly Process Entail?
The assembly stage involves combining the formed filter media with the structural components of the cabin air filter. This includes:
- Frame Attachment: The filter media is attached to a frame, often made of plastic or metal, which adds stability and facilitates installation.
- Sealing: Edges are sealed to prevent air bypass, which can compromise filtration efficiency.
4. Finishing: How Is Quality Ensured in the Final Product?
Finishing touches may involve adding identification labels, packaging, and conducting final inspections. This stage is critical as it ensures that the product is ready for distribution and meets all necessary specifications.
What Quality Assurance Standards Are Relevant for Cabin Air Filter Manufacturing?
Quality assurance in cabin air filter manufacturing is paramount to ensure reliability and safety. International standards, such as ISO 9001, provide a framework for quality management systems, while industry-specific certifications like CE and API can indicate adherence to specific performance criteria.
Key Quality Control Checkpoints: How Are They Implemented?
Quality control (QC) is integrated at various stages of the manufacturing process:
- Incoming Quality Control (IQC): Raw materials are inspected upon arrival to ensure they meet specified standards.
- In-Process Quality Control (IPQC): Ongoing inspections during the manufacturing process help catch defects early, which can save costs and time.
- Final Quality Control (FQC): The finished products undergo rigorous testing to verify that they meet quality and performance standards.
What Testing Methods Are Commonly Used for Cabin Air Filters?
Various testing methods are employed to assess the effectiveness of cabin air filters:
- Filtration Efficiency Testing: Measures the filter’s ability to capture particles of different sizes.
- Pressure Drop Testing: Evaluates how easily air flows through the filter, which is crucial for maintaining vehicle performance.
- Chemical Absorption Tests: Assess the filter’s ability to adsorb harmful gases and odors.
How Can B2B Buyers Verify Supplier Quality Control?
For international B2B buyers, particularly from regions like Africa, South America, the Middle East, and Europe, verifying a supplier’s quality control processes is essential. Here are some strategies:
- Supplier Audits: Conducting on-site audits can provide firsthand insight into the manufacturing processes and quality control measures in place.
- Requesting Quality Reports: Suppliers should be able to provide documentation of their quality control processes and any certifications they hold.
- Third-Party Inspections: Engaging third-party inspection services can add an additional layer of verification, ensuring that the products meet international standards.
What Are the Nuances of Quality Control for International B2B Buyers?
When sourcing cabin air filters from international suppliers, B2B buyers need to be aware of certain nuances:
- Regulatory Compliance: Different regions have varying regulations regarding automotive components. Understanding these can prevent future compliance issues.
- Cultural Differences: Approach to quality control may differ across cultures, making it vital to establish clear communication and expectations.
- Logistical Challenges: International shipping can introduce additional variables, such as delays or damage, making robust packaging and handling processes crucial.
Conclusion: What Should B2B Buyers Focus On?
B2B buyers sourcing cabin air filters should prioritize suppliers who demonstrate robust manufacturing processes and comprehensive quality assurance practices. By understanding the various stages of production and the importance of quality control, buyers can make informed decisions that ensure the reliability and performance of the cabin air filters they purchase. Engaging in due diligence through audits, inspections, and compliance checks will further safeguard their investments, ultimately leading to better outcomes for their operations.
Practical Sourcing Guide: A Step-by-Step Checklist for ‘how often to change cabin air filter’
The purpose of this guide is to provide international B2B buyers with a practical checklist for sourcing cabin air filters, specifically focusing on determining how often they should be changed. Understanding the maintenance requirements for these filters can significantly impact the performance of vehicles and equipment, enhancing customer satisfaction and operational efficiency.
Step 1: Identify Your Requirements for Cabin Air Filters
Understanding the specific needs of your business is crucial. Consider factors such as the type of vehicles or equipment, the environment in which they operate, and the expected usage frequency. This assessment will guide you in selecting filters that meet your operational demands, ensuring optimal air quality and equipment performance.
Step 2: Research Recommended Replacement Intervals
Different manufacturers provide varying recommendations for how often cabin air filters should be replaced. Research these guidelines, which are often based on vehicle type and usage conditions. Understanding these intervals will help you establish a maintenance schedule that minimizes downtime and extends the life of your vehicles or equipment.
Step 3: Evaluate Supplier Certifications and Standards
Before committing to a supplier, verify that they adhere to industry standards and certifications. Look for ISO certifications or compliance with local regulations relevant to your region, such as those in Africa, South America, the Middle East, or Europe. Certifications ensure that the products meet quality and safety standards, reducing the risk of purchasing subpar filters.
Step 4: Request Samples for Quality Assessment
Always request samples from potential suppliers before making a bulk purchase. This allows you to assess the quality of the cabin air filters firsthand. Examine the material, filtration efficiency, and durability, which are critical factors for effective air filtration. A thorough quality assessment can prevent future operational issues.
Step 5: Inquire About Supplier Lead Times and Availability
Understanding lead times is essential for effective inventory management. Inquire about the supplier’s ability to meet your demand promptly. This is particularly important for businesses operating in regions with unpredictable supply chains, where delays can lead to increased operational costs.
Step 6: Evaluate Pricing Models and Bulk Discounts
Consider the pricing structures offered by suppliers, including any bulk discounts. Compare prices across multiple suppliers while factoring in the quality of the filters. A lower price does not always equate to better value; ensure that the filters meet your performance requirements while being cost-effective.
Step 7: Establish a Clear Communication Channel
Maintain open lines of communication with your supplier. This facilitates quick resolution of any issues that may arise, such as delays or quality concerns. A reliable supplier should be responsive and willing to provide support, fostering a long-term partnership that can adapt to your changing needs.
By following these steps, B2B buyers can effectively source cabin air filters that align with their operational needs and ensure the longevity and performance of their vehicles and equipment.
Comprehensive Cost and Pricing Analysis for how often to change cabin air filter Sourcing
What Are the Key Cost Components for Cabin Air Filter Sourcing?
When analyzing the cost structure for sourcing cabin air filters, several critical components come into play. Understanding these elements can help international B2B buyers make informed purchasing decisions.
-
Materials: The type of materials used in manufacturing cabin air filters significantly impacts the overall cost. Common materials include activated carbon and synthetic fibers, which can vary in price based on quality and availability. Buyers should consider sourcing from regions where these materials are abundantly available to reduce costs.
-
Labor: Labor costs can fluctuate based on the country of manufacture. For example, labor-intensive processes in countries with higher wage standards may increase the overall price. On the other hand, countries with lower labor costs may offer more competitive pricing but could compromise on quality.
-
Manufacturing Overhead: This includes all indirect costs associated with production, such as utilities, rent, and equipment depreciation. Buyers should inquire about the manufacturing processes to understand how overhead impacts the final price.
-
Tooling: The cost of tooling is essential, particularly for custom or specialized filters. If a unique design is required, the initial tooling investment can be significant. Buyers should evaluate whether the tooling cost justifies the long-term benefits of custom products.
-
Quality Control (QC): Rigorous QC processes ensure that the filters meet specified performance standards. While robust QC adds to the cost, it is crucial for maintaining product reliability, especially in markets with stringent regulations.
-
Logistics: Shipping costs can vary widely depending on the origin of the products, destination, and chosen shipping methods. Buyers should consider the entire logistics chain, including customs duties and import taxes, which can significantly affect the total cost.
-
Margin: Supplier margins can vary based on market conditions and competition. Understanding the markup applied by suppliers can assist buyers in negotiating better terms.
How Do Price Influencers Impact Cabin Air Filter Costs?
Several factors influence the pricing of cabin air filters, and recognizing these can help buyers optimize their purchasing strategies.
-
Volume/MOQ: Minimum Order Quantities (MOQs) can significantly affect pricing. Higher order volumes often lead to lower per-unit costs, making it advantageous for businesses with large-scale needs to consolidate orders.
-
Specifications and Customization: Filters that require specific certifications or custom features typically command higher prices. Buyers should assess whether these additional specifications are essential for their operations.
-
Material Quality and Certifications: Filters made from high-quality materials that meet international standards may incur higher costs. Buyers in regions like Europe, which often have strict regulatory requirements, should prioritize certified products despite the higher price tag.
-
Supplier Factors: Supplier reputation and reliability can also influence pricing. Established suppliers may charge a premium for their proven track record, while emerging suppliers might offer lower prices to gain market share.
-
Incoterms: The choice of Incoterms can impact the final cost of goods significantly. Understanding the responsibilities and liabilities under different Incoterms can help buyers avoid unexpected expenses.
What Buyer Tips Can Enhance Cost Efficiency in Cabin Air Filter Sourcing?
International B2B buyers can employ several strategies to enhance cost efficiency when sourcing cabin air filters.
-
Negotiation: Effective negotiation can lead to better pricing. Buyers should prepare by researching market rates and being clear about their needs and expectations.
-
Total Cost of Ownership (TCO): Evaluating the TCO rather than just the purchase price can provide a more comprehensive understanding of costs. This includes maintenance, replacement frequency, and potential downtime caused by poor-quality filters.
-
Pricing Nuances for International Markets: Buyers from Africa, South America, the Middle East, and Europe should be aware of regional pricing trends and economic factors that may affect costs. Currency fluctuations, import tariffs, and local market conditions can all play a significant role.
-
Supplier Diversification: Relying on a single supplier can be risky. Diversifying the supplier base can lead to better pricing options and reduce the risk of supply chain disruptions.
-
Long-term Partnerships: Establishing long-term relationships with suppliers can lead to preferential pricing and better service. Loyalty often translates into cost savings over time.
Disclaimer on Indicative Prices
The prices for cabin air filters can vary widely based on the aforementioned factors. It is essential for buyers to conduct thorough research and obtain multiple quotes to ensure they are making the most cost-effective purchasing decisions.
Alternatives Analysis: Comparing how often to change cabin air filter With Other Solutions
When considering the optimal approach to maintaining vehicle air quality, it is crucial for B2B buyers to evaluate not only the frequency of changing cabin air filters but also alternative solutions that might offer similar benefits. Understanding the various options available can empower businesses to make informed purchasing decisions that align with their operational needs and budgetary constraints.
Comparison Aspect | How Often To Change Cabin Air Filter | Alternative 1: Air Purification Systems | Alternative 2: High-Efficiency Filters |
---|---|---|---|
Performance | Effective in removing particulates and odors when changed regularly. | Provides continuous air quality improvement, often with HEPA filters. | Enhanced filtration capability, targeting finer particles. |
Cost | Low initial cost, but recurring costs for regular replacements. | Higher upfront investment but lower ongoing maintenance costs. | Moderate cost with potential for longer lifespan than standard filters. |
Ease of Implementation | Simple to replace with basic tools and knowledge. | Requires professional installation and setup. | Can be a direct replacement but may require specific sizing. |
Maintenance | Requires regular monitoring and changing every 15,000 to 30,000 km. | Minimal maintenance; periodic filter replacement needed. | Regular checks needed, but longer intervals between changes. |
Best Use Case | Ideal for standard vehicles in urban environments. | Best for high-pollution areas or specialized vehicles (e.g., ambulances). | Suitable for vehicles in extreme conditions, such as industrial sites. |
What Are the Advantages and Disadvantages of Air Purification Systems?
Air purification systems serve as a robust alternative to traditional cabin air filters. They continuously clean the air within the vehicle, often utilizing HEPA filters that capture a higher percentage of airborne particles, allergens, and pollutants. The primary advantage of air purifiers is their ability to maintain a consistently high air quality level without the need for frequent replacements. However, these systems often come with a higher initial investment and may require professional installation, which can be a deterrent for some businesses, especially those operating on tight budgets.
How Do High-Efficiency Filters Compare to Regular Cabin Air Filters?
High-efficiency filters are designed to provide superior filtration compared to standard cabin air filters. They are capable of capturing smaller particles, including dust, pollen, and smoke, which can be critical for businesses operating in areas with high levels of air pollution. While the cost of high-efficiency filters can be moderate, their longer lifespan can lead to reduced replacement frequency and lower overall maintenance costs. However, they may not fit all vehicle models seamlessly, necessitating careful consideration of compatibility during the purchasing process.
Conclusion: How Can B2B Buyers Select the Right Air Quality Solution?
When choosing the right solution for maintaining air quality in vehicles, B2B buyers should consider their specific operational needs, budget constraints, and environmental factors. Regularly changing cabin air filters offers a low-cost, straightforward solution suitable for most commercial vehicles. However, for businesses in high-pollution areas or those requiring enhanced air quality, investing in air purification systems or high-efficiency filters could yield better long-term benefits. By analyzing the performance, cost, and maintenance requirements of each option, buyers can make informed decisions that support their overall fleet management strategy.
Essential Technical Properties and Trade Terminology for how often to change cabin air filter
What Are the Key Technical Properties of Cabin Air Filters?
Understanding the essential technical properties of cabin air filters is crucial for B2B buyers, particularly those in regions like Africa, South America, the Middle East, and Europe. Here are some critical specifications:
-
Material Grade
– Cabin air filters are typically made from materials such as activated carbon, HEPA (High-Efficiency Particulate Air), or synthetic fibers. The material grade affects filtration efficiency and durability. Activated carbon filters are excellent for odor removal, while HEPA filters capture fine particulate matter. Buyers must assess their specific requirements based on environmental conditions and vehicle usage. -
Filtration Efficiency
– This specification indicates the filter’s ability to trap airborne particles, measured in percentage terms. A higher filtration efficiency means better air quality inside the vehicle. For B2B buyers, understanding the filtration efficiency is essential to ensure compliance with local air quality regulations and customer satisfaction. -
Service Life
– The recommended service life of a cabin air filter can vary significantly, typically ranging from 12,000 to 30,000 kilometers (approximately 7,500 to 18,600 miles). Service life can be influenced by factors such as vehicle type, driving conditions, and local air quality. B2B buyers should consider these variables when determining inventory turnover and customer education on replacement schedules. -
Tolerance Levels
– Tolerance refers to the acceptable limits of variation in the filter’s dimensions. It ensures that the filter fits snugly within the cabin air intake system, preventing air bypass. This property is crucial for maintaining optimal performance and preventing potential damage to the HVAC system. Buyers should verify tolerance specifications against vehicle models to ensure compatibility. -
Pressure Drop
– Pressure drop measures the resistance to airflow through the filter. A lower pressure drop indicates better airflow and less strain on the vehicle’s HVAC system. Understanding pressure drop is vital for buyers to ensure that the chosen filter does not negatively impact vehicle performance, especially in regions with extreme temperatures.
What Are Common Trade Terms Associated with Cabin Air Filters?
Familiarizing yourself with industry jargon is essential for effective communication and negotiation in the B2B landscape. Here are some common terms related to cabin air filters:
-
OEM (Original Equipment Manufacturer)
– OEM refers to manufacturers that produce parts that are identical to those supplied in new vehicles. B2B buyers often prefer OEM parts for reliability and compatibility. Understanding the distinction between OEM and aftermarket parts can help buyers make informed sourcing decisions. -
MOQ (Minimum Order Quantity)
– MOQ is the smallest quantity a supplier is willing to sell. This term is crucial for B2B buyers as it affects inventory management and cash flow. Knowing the MOQ helps in planning purchases and negotiating better terms with suppliers. -
RFQ (Request for Quotation)
– An RFQ is a formal process where buyers request pricing information from suppliers for specific products. It allows buyers to compare quotes and terms, aiding in budget planning and supplier selection. Utilizing RFQs can lead to better pricing and contract terms. -
Incoterms (International Commercial Terms)
– Incoterms define the responsibilities of buyers and sellers in international trade, including who is responsible for shipping, insurance, and tariffs. Understanding Incoterms is vital for B2B transactions, especially for international buyers, as it clarifies risk and cost allocation. -
Lead Time
– Lead time refers to the time taken from placing an order until the product is delivered. For B2B buyers, understanding lead times is critical for inventory planning and ensuring timely availability of cabin air filters, especially in markets with high demand fluctuations. -
Aftermarket
– Aftermarket parts are components produced by manufacturers other than the OEM. While often less expensive, they may vary in quality. B2B buyers should weigh the benefits and risks associated with aftermarket filters, considering factors such as warranty and performance.
By understanding these technical properties and trade terms, international B2B buyers can make informed decisions regarding cabin air filters, optimizing both procurement strategies and product offerings to meet market demands.
Navigating Market Dynamics and Sourcing Trends in the how often to change cabin air filter Sector
What Are the Current Market Dynamics Influencing Cabin Air Filter Sourcing?
The global market for cabin air filters is shaped by several key dynamics that international B2B buyers must understand. A significant driver is the increasing awareness of air quality and its impact on health, especially in regions with rising urbanization rates, such as Africa and South America. Consumers are demanding higher-quality air filtration systems, prompting manufacturers to innovate and enhance their product offerings. Additionally, the automotive industry’s shift towards electric vehicles (EVs) is creating new opportunities for cabin air filter suppliers, as these vehicles require specialized filters to manage unique airflow and particulate challenges.
Emerging technologies, such as smart sensors and IoT-enabled monitoring systems, are also influencing sourcing trends. These innovations allow for predictive maintenance, enabling fleet operators to replace filters based on actual usage rather than fixed intervals. This not only reduces costs but also enhances vehicle performance. Moreover, international trade agreements and tariffs can affect sourcing strategies, especially for buyers in the Middle East and Europe, where trade regulations can vary significantly.
How Can Sustainability and Ethical Sourcing Impact Cabin Air Filter Procurement?
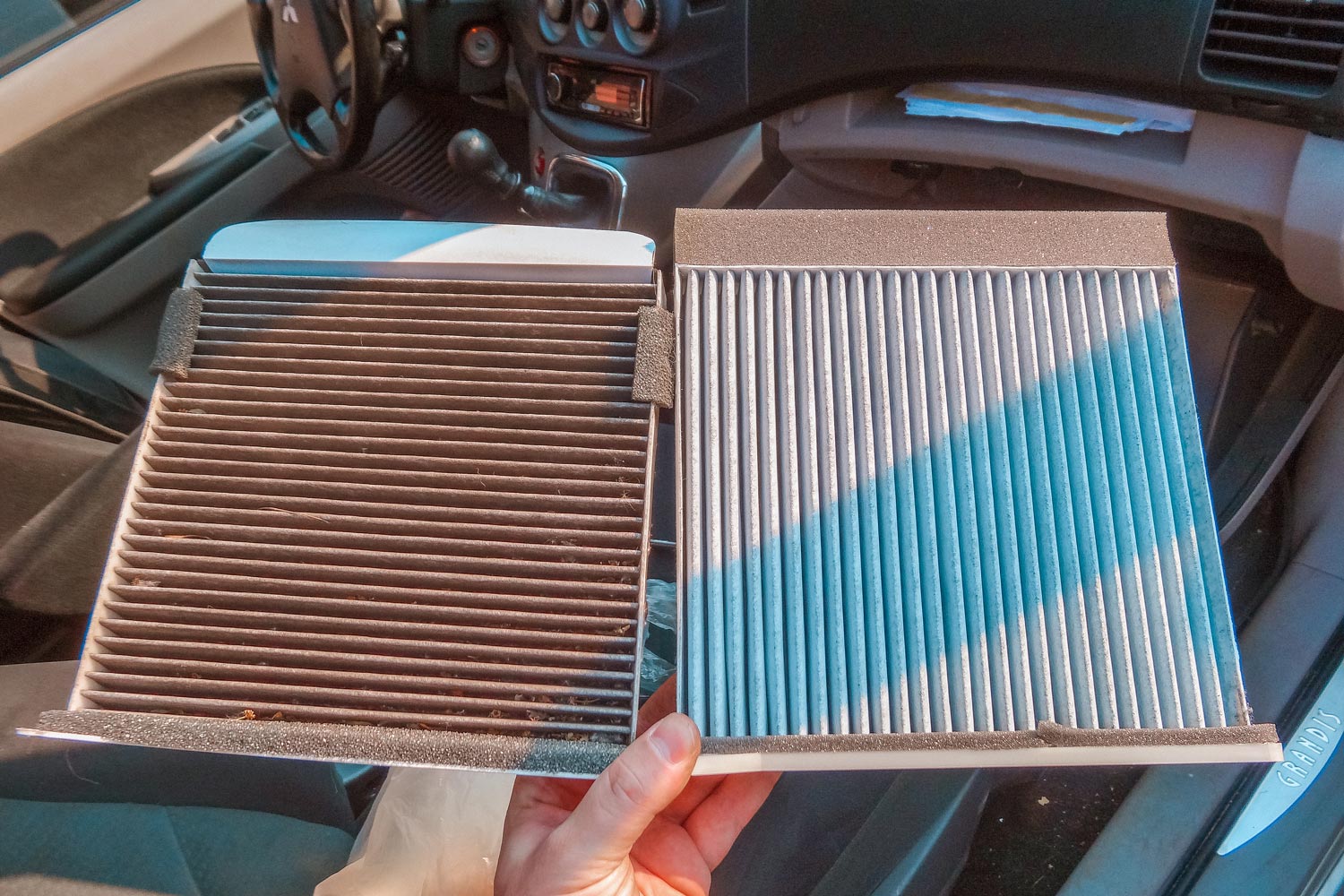
A stock image related to how often to change cabin air filter.
Sustainability is becoming a cornerstone of procurement strategies for B2B buyers across the globe. As environmental concerns gain prominence, the demand for eco-friendly cabin air filters made from sustainable materials is on the rise. Buyers are increasingly looking for suppliers who can demonstrate a commitment to sustainability through certifications such as ISO 14001 or the Global Recycled Standard (GRS).
Ethical sourcing is equally critical, as companies must ensure that their supply chains are free from exploitation and harmful practices. This not only mitigates risk but also enhances brand reputation in the eyes of environmentally-conscious consumers. In regions like Europe, where regulatory frameworks are stringent, adherence to sustainability practices can also be a competitive differentiator. Buyers should prioritize partnerships with manufacturers that utilize recycled materials or offer take-back programs for used filters, thereby closing the loop on product life cycles.
How Has the Cabin Air Filter Market Evolved Over Time?
The cabin air filter market has undergone significant evolution, particularly in the last two decades. Initially, these filters were primarily viewed as basic components for vehicle comfort and safety. However, as scientific research highlighted the health impacts of air quality, the perception shifted. Today, cabin air filters are recognized not only for their role in enhancing passenger comfort but also for their critical function in protecting health by filtering out pollutants, allergens, and harmful particulates.
The rise of stringent automotive regulations, particularly in Europe and North America, has further propelled advancements in filter technology. Manufacturers are now investing in research and development to create high-efficiency particulate air (HEPA) filters and activated carbon filters that provide superior performance. This evolution reflects a broader trend within the automotive industry towards integrating health and wellness features, aligning with the growing consumer demand for safer and more efficient vehicles. For international B2B buyers, understanding this evolution is essential for making informed sourcing decisions that align with market expectations and future trends.
Frequently Asked Questions (FAQs) for B2B Buyers of how often to change cabin air filter
-
How often should I change the cabin air filter in my fleet vehicles?
The frequency of changing cabin air filters can vary based on several factors, including the vehicle type, environmental conditions, and usage patterns. Generally, it’s recommended to replace cabin air filters every 15,000 to 30,000 kilometers (about 9,000 to 18,000 miles). However, if your vehicles operate in dusty or polluted environments, consider more frequent replacements, potentially every 10,000 kilometers (6,000 miles). Regular maintenance not only ensures better air quality but also enhances the longevity of your vehicles. -
What are the signs that indicate a cabin air filter needs to be replaced?
B2B buyers should look for several signs indicating that a cabin air filter needs replacement. These include reduced airflow from the air conditioning system, unpleasant odors inside the vehicle, and increased dust accumulation on the dashboard. If passengers experience allergies or respiratory issues while traveling, it could also signify that the cabin air filter is clogged. Regular inspections can help identify these issues early, ensuring a healthier environment for drivers and passengers. -
What is the best cabin air filter for international shipping?
When sourcing cabin air filters for international shipping, prioritize filters that comply with global quality standards. Look for HEPA filters or activated carbon filters for superior air purification. Additionally, consider suppliers that offer customizable options to meet specific regional requirements. Ensure the filters are packaged securely to prevent damage during transit. Researching suppliers with a proven track record in logistics can also enhance the reliability of your supply chain. -
How can I vet suppliers for cabin air filters in different regions?
To effectively vet suppliers for cabin air filters, conduct thorough research into their reputation and reliability. Look for reviews and testimonials from other B2B buyers in your region. Request samples to assess product quality and ensure compliance with local regulations. Additionally, inquire about their certifications and manufacturing processes. Engaging in direct communication can also help you gauge their responsiveness and customer service capabilities. -
What are the minimum order quantities (MOQ) for cabin air filters?
Minimum order quantities for cabin air filters can vary significantly between suppliers. While some may offer flexible MOQ options, others may require larger bulk orders. It’s essential to discuss your specific needs with potential suppliers to negotiate terms that suit your business model. Establishing a good relationship with suppliers can sometimes lead to more favorable MOQ arrangements, especially if you anticipate regular future orders. -
What payment terms should I consider when sourcing cabin air filters?
When sourcing cabin air filters, consider payment terms that align with your cash flow and risk management strategies. Common terms include net 30, 60, or 90 days, which allow time for inspection and quality assurance before payment. For international transactions, consider using letters of credit or escrow services to ensure secure payments. Always clarify payment methods, currencies, and any additional fees upfront to avoid misunderstandings later.
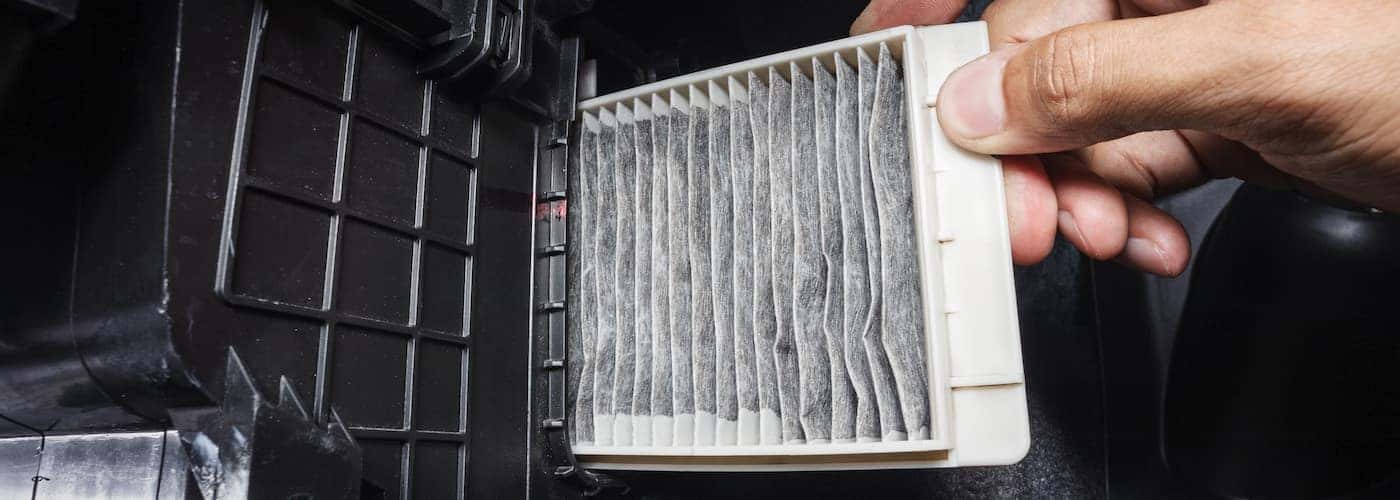
A stock image related to how often to change cabin air filter.
-
How can I ensure quality assurance (QA) for cabin air filters sourced internationally?
To ensure quality assurance for cabin air filters sourced internationally, establish clear quality standards and testing protocols with your suppliers. Request certifications and third-party testing results to verify compliance with industry standards. Implementing a quality control process, such as inspecting samples before bulk orders, can help mitigate risks. Additionally, consider establishing a partnership with a local inspection agency to conduct on-site audits of the supplier’s manufacturing processes. -
What logistics considerations should I keep in mind for importing cabin air filters?
When importing cabin air filters, consider logistics aspects such as shipping methods, customs regulations, and potential tariffs. Evaluate the most cost-effective shipping options, whether by air or sea, based on your timeline and budget. Be aware of the import duties applicable in your region and ensure all paperwork is in order to avoid delays. Collaborating with a reliable logistics partner can facilitate smoother transactions and help navigate the complexities of international shipping.
Important Disclaimer & Terms of Use
⚠️ Important Disclaimer
The information provided in this guide, including content regarding manufacturers, technical specifications, and market analysis, is for informational and educational purposes only. It does not constitute professional procurement advice, financial advice, or legal advice.
While we have made every effort to ensure the accuracy and timeliness of the information, we are not responsible for any errors, omissions, or outdated information. Market conditions, company details, and technical standards are subject to change.
B2B buyers must conduct their own independent and thorough due diligence before making any purchasing decisions. This includes contacting suppliers directly, verifying certifications, requesting samples, and seeking professional consultation. The risk of relying on any information in this guide is borne solely by the reader.
Strategic Sourcing Conclusion and Outlook for how often to change cabin air filter
In conclusion, understanding the optimal frequency for changing cabin air filters is crucial for international B2B buyers focused on maintaining vehicle performance and ensuring passenger comfort. Key takeaways highlight the importance of considering factors such as local climate, driving conditions, and vehicle usage patterns. For example, businesses operating in urban areas with high pollution levels may need to change filters more frequently than those in cleaner environments.
Implementing strategic sourcing practices can significantly enhance procurement efficiency, leading to cost savings and improved supply chain reliability. By establishing relationships with reputable suppliers who understand regional needs, buyers can ensure they receive high-quality cabin air filters that meet international standards.
Looking ahead, it is vital for B2B buyers in Africa, South America, the Middle East, and Europe to stay informed about evolving industry trends and technological advancements in air filtration systems. Embrace proactive maintenance strategies and leverage data analytics to optimize filter change schedules. As you evaluate your sourcing strategies, consider how these actions can enhance operational efficiency and contribute to overall business sustainability.