The Ultimate Guide to Automatic Spray Painting (2025)
Introduction: Navigating the Global Market for automatic spray painting
As the demand for high-quality finishes in manufacturing and industrial applications grows, sourcing the right automatic spray painting solutions becomes a critical challenge for international B2B buyers. With diverse markets in regions such as Africa, South America, the Middle East, and Europe, understanding the nuances of automatic spray painting technology can significantly impact operational efficiency and product quality. This guide serves as a comprehensive resource for buyers seeking to navigate the complexities of the global automatic spray painting market.
The scope of this guide encompasses various types of automatic spray painting systems, their applications across different industries, and essential considerations for supplier vetting. We delve into the cost structures associated with these systems, providing insights into budgeting and ROI analysis, which are particularly valuable for businesses looking to optimize their investments. Additionally, we will address common questions that arise during the sourcing process, such as how to evaluate the performance and reliability of different technologies.
By equipping B2B buyers with actionable insights, this guide empowers decision-makers to make informed choices that align with their operational goals. Whether you are in the automotive sector in South Africa, the furniture industry in Brazil, or manufacturing in Europe, understanding the global landscape of automatic spray painting is crucial for enhancing productivity and maintaining competitive advantage.
Understanding automatic spray painting Types and Variations
Type Name | Key Distinguishing Features | Primary B2B Applications | Brief Pros & Cons for Buyers |
---|---|---|---|
Robotic Spray Painting | High precision, programmable movements | Automotive, Aerospace, Electronics | Pros: Consistent quality, reduced labor costs. Cons: High initial investment. |
Electrostatic Spray Painting | Uses charged particles for improved paint adhesion | Furniture, Metal Fabrication, Plastics | Pros: Less overspray, efficient material usage. Cons: Requires specialized equipment. |
Airless Spray Painting | High-pressure system for thick coatings | Construction, Industrial Equipment | Pros: Faster application, suitable for heavy materials. Cons: Requires skilled operators. |
HVLP (High Volume Low Pressure) | Low pressure with high volume for fine finishes | Woodworking, Automotive Refinishing | Pros: Minimal overspray, excellent finish quality. Cons: Slower application speed. |
Automated Paint Booths | Enclosed systems with environmental controls | Large-scale manufacturing, Powder Coating | Pros: Improved safety, reduced contamination. Cons: Space-intensive and costly. |
What are the Key Characteristics of Robotic Spray Painting?
Robotic spray painting utilizes advanced robotic arms programmed to perform precise movements, allowing for intricate designs and consistent application. This type is particularly suitable for industries like automotive and aerospace, where high-quality finishes are critical. B2B buyers should consider the initial investment cost against long-term savings from reduced labor and increased efficiency. Maintenance and software updates are also essential factors to ensure optimal performance.
How Does Electrostatic Spray Painting Improve Efficiency?
Electrostatic spray painting employs charged particles that enhance paint adhesion to surfaces, minimizing overspray and maximizing material usage. This technique is widely used in furniture manufacturing and metal fabrication. B2B buyers should evaluate the cost of specialized equipment and training against the benefits of reduced waste and improved finish quality. This method is particularly advantageous for businesses looking to optimize their production processes while maintaining high standards.
In What Scenarios is Airless Spray Painting Most Effective?
Airless spray painting operates at high pressure, allowing for the application of thicker coatings, making it ideal for construction and industrial applications. This method delivers a fast application rate, which can significantly reduce project timelines. However, it requires skilled operators to achieve the best results and avoid issues such as overspray. B2B buyers should assess their workforce capabilities alongside the equipment investment to ensure effective implementation.
What Advantages Does HVLP Spray Painting Offer?
HVLP (High Volume Low Pressure) spray painting is known for its ability to produce fine finishes with minimal overspray, making it a popular choice in woodworking and automotive refinishing. The method’s slower application speed can be a drawback for high-volume operations, but the quality of the finish often justifies the time investment. B2B buyers should weigh the benefits of reduced waste and superior quality against the need for potentially longer project durations.
Why Consider Automated Paint Booths in Large-Scale Operations?
Automated paint booths provide controlled environments that enhance safety and reduce contamination risks. This type of system is particularly beneficial for large-scale manufacturing and powder coating applications. While the initial setup can be costly and requires significant space, the long-term benefits in safety, efficiency, and finish quality make it an attractive option for B2B buyers focused on scaling their operations. Evaluating the total cost of ownership, including maintenance and operational costs, is crucial for making informed purchasing decisions.
Related Video: Automatic spray painting system for wood furniture panels
Key Industrial Applications of automatic spray painting
Industry/Sector | Specific Application of Automatic Spray Painting | Value/Benefit for the Business | Key Sourcing Considerations for this Application |
---|---|---|---|
Automotive Manufacturing | Painting car bodies and components | Enhanced finish quality and consistency | Supplier reliability, equipment compatibility, and local support |
Furniture Production | Coating wooden and metal furniture | Improved durability and aesthetic appeal | Material compatibility, environmental regulations, and customization options |
Electronics & Appliances | Coating circuit boards and appliance casings | Protection against corrosion and improved appearance | Precision in application, compliance with safety standards, and supplier certifications |
Construction & Infrastructure | Painting structural steel and facades | Increased lifespan of materials and visual appeal | Weather resistance, adherence to local regulations, and project timelines |
Aerospace | Coating aircraft components | Weight reduction and enhanced corrosion resistance | Certification requirements, specialized coatings, and performance testing |
How is Automatic Spray Painting Used in Automotive Manufacturing?
In the automotive sector, automatic spray painting is crucial for applying high-quality finishes to car bodies and components. This technology addresses challenges such as inconsistent paint application and long drying times, which can lead to defects. Buyers in this industry, particularly in regions like South Africa and Europe, must consider supplier reliability and the compatibility of spray painting equipment with existing assembly lines. Additionally, local support for maintenance and training can significantly affect operational efficiency.
What are the Applications of Automatic Spray Painting in Furniture Production?
In furniture production, automatic spray painting is employed to coat wooden and metal furniture items, ensuring a uniform finish that enhances durability and aesthetic appeal. This application solves problems related to manual painting, such as uneven coverage and longer production times. B2B buyers should focus on material compatibility and environmental regulations when sourcing equipment, especially in regions like South America, where sustainability is increasingly prioritized. Customization options for colors and finishes can also be a deciding factor for buyers.
How Does Automatic Spray Painting Benefit Electronics and Appliances?
In the electronics and appliances industry, automatic spray painting is utilized to coat circuit boards and appliance casings. This application provides essential protection against corrosion while improving the overall appearance of products. International buyers must prioritize precision in application, compliance with safety standards, and supplier certifications when sourcing painting solutions. Understanding the specific requirements for different electronic components is critical for ensuring quality and longevity.
What is the Role of Automatic Spray Painting in Construction and Infrastructure?
Automatic spray painting is used in construction to coat structural steel and building facades, offering benefits such as increased lifespan of materials and enhanced visual appeal. This technology addresses challenges like weather resistance and the need for quick application in large projects. Buyers from the Middle East and Africa should consider adherence to local regulations, the weather resistance of coatings, and project timelines when sourcing painting solutions. The ability to deliver consistent results across large surfaces is also vital.
How is Automatic Spray Painting Applied in Aerospace?
In the aerospace industry, automatic spray painting is essential for coating aircraft components, where it contributes to weight reduction and enhanced corrosion resistance. This application is critical due to the stringent certification requirements and specialized coatings needed for aviation standards. B2B buyers in Europe and beyond must ensure that suppliers meet these certifications and provide performance testing data. Additionally, understanding the specific environmental conditions that the coatings will face is crucial for long-term durability and safety.
Related Video: Machines Spray Paint Roads With Incredible Precision
3 Common User Pain Points for ‘automatic spray painting’ & Their Solutions
Scenario 1: Inconsistent Paint Finish Across Production Batches
The Problem: One of the most common challenges faced by manufacturers using automatic spray painting is achieving a consistent finish across different production batches. Variability in paint viscosity, environmental conditions, and equipment settings can lead to discrepancies in color and texture, resulting in rejected products and increased costs. This inconsistency can be particularly detrimental for companies in sectors like automotive and consumer goods, where brand reputation heavily relies on product quality.
The Solution: To combat this issue, B2B buyers should invest in high-quality paint materials and ensure that their automatic spray painting systems are equipped with advanced viscosity control and temperature regulation features. Regular maintenance of the spray equipment is essential to prevent clogs and ensure even distribution. Additionally, implementing a standardized quality control process that includes regular sampling and testing of finished products can help detect inconsistencies early. Buyers should also consider collaborating with suppliers who can provide technical support and training on the proper use and settings of spray painting equipment, ensuring their team is well-versed in optimizing the painting process.
Scenario 2: High Operational Costs Due to Inefficient Processes
The Problem: Many B2B buyers find that operational costs associated with automatic spray painting can escalate quickly due to inefficient processes. Factors such as excessive paint waste, high energy consumption, and prolonged downtime for equipment maintenance can significantly impact the bottom line. Companies in regions like Africa and South America may face additional challenges, such as limited access to high-quality materials or technical expertise, making it crucial to maximize the efficiency of existing systems.
The Solution: To reduce operational costs, buyers should conduct a thorough audit of their current painting processes. Implementing a closed-loop paint system can minimize waste by recirculating excess paint back into the system. Additionally, investing in energy-efficient spray painting equipment can lead to substantial savings on energy bills over time. Buyers should also explore automation solutions that can streamline workflows and reduce manual labor. Lastly, establishing partnerships with local suppliers for maintenance and support can help ensure that equipment runs smoothly, minimizing downtime and reducing overall costs.
Scenario 3: Difficulty in Adapting to Diverse Material Requirements
The Problem: In a global market, B2B buyers often face challenges when adapting their automatic spray painting processes to accommodate a variety of materials, such as metals, plastics, and composites. Each material may require different paint formulations and application techniques, leading to confusion and potential errors during production. This is particularly relevant for businesses in industries like electronics or construction, where the integrity of the finish is critical for product performance.
The Solution: Buyers should prioritize sourcing spray painting systems that offer versatility and adaptability for different materials. Investing in multi-functional spray guns and adjusting the nozzle configurations can allow for different paint types and viscosities to be used effectively. Conducting thorough research on material compatibility and consulting with paint suppliers for tailored solutions can further enhance the adaptability of the painting process. Additionally, providing training for staff on the specific requirements for each material will ensure a smoother transition and minimize the risk of errors. Establishing a feedback loop with production teams can also help identify issues quickly and facilitate ongoing improvements in the spray painting process.
Strategic Material Selection Guide for automatic spray painting
When selecting materials for automatic spray painting, it is crucial to consider the specific properties, advantages, and limitations of each material. This analysis focuses on four common materials used in the industry: acrylics, polyurethanes, epoxies, and water-based paints. Each material has unique characteristics that can significantly impact the performance and suitability of the final product.
What Are the Key Properties of Acrylics in Automatic Spray Painting?
Acrylic paints are known for their excellent adhesion, quick drying time, and UV resistance. They typically perform well at moderate temperatures and pressures, making them suitable for a variety of applications. Their low viscosity allows for smooth application, which is essential in automatic spray painting processes.
Pros & Cons: Acrylics are durable and versatile, suitable for both indoor and outdoor applications. However, they may not be as resistant to chemicals as other options, which can limit their use in industrial environments. Additionally, while they are relatively affordable, the need for a primer in some applications can add to overall costs.
Impact on Application: Acrylics are compatible with a wide range of substrates, including metal, wood, and plastic. However, their performance may vary based on the surface preparation and environmental conditions during application.
Considerations for International Buyers: Buyers from regions like Africa and South America should ensure compliance with local environmental regulations regarding VOC emissions. Standards such as ASTM D4236 for safety and labeling may also apply.
How Do Polyurethanes Compare for Automatic Spray Painting?
Polyurethane paints offer exceptional durability and chemical resistance, making them a popular choice for industrial applications. They can withstand high temperatures and pressures, which is advantageous in demanding environments.
Pros & Cons: The key advantage of polyurethanes is their long-lasting finish and resistance to abrasion and chemicals. However, they can be more expensive than acrylics and require a more complex application process, including the use of hardeners and specific spray equipment.
Impact on Application: Polyurethanes are ideal for automotive and industrial coatings due to their robust performance. However, they may not adhere well to certain surfaces without proper preparation.
Considerations for International Buyers: Buyers should be aware of the specific curing times and conditions required for polyurethanes, as these can vary significantly by region. Compliance with standards such as DIN EN 71 for toy safety may also be necessary in certain markets.
What Are the Advantages of Epoxies in Automatic Spray Painting?
Epoxy paints are renowned for their strong adhesion and resistance to moisture, making them suitable for environments exposed to water or chemicals. They typically perform well under high-pressure conditions and offer excellent durability.
Pros & Cons: The primary advantage of epoxies is their superior bonding capabilities, which result in a long-lasting finish. However, they can be more expensive and may require longer curing times, which can affect production schedules.
Impact on Application: Epoxies are often used in industrial settings where corrosion resistance is critical, such as in marine applications. Their compatibility with various substrates enhances their versatility.
Considerations for International Buyers: Buyers must consider local regulations on epoxy usage, particularly regarding health and safety standards. Compliance with JIS standards may be essential for buyers in Japan and neighboring regions.
Are Water-Based Paints a Viable Option for Automatic Spray Painting?
Water-based paints are gaining popularity due to their lower environmental impact and ease of cleanup. They typically have lower VOC levels, making them a safer choice for indoor applications.
Pros & Cons: The key advantage of water-based paints is their environmental friendliness and user safety. However, they may not provide the same durability or chemical resistance as solvent-based options, which can limit their use in harsh environments.
Impact on Application: Water-based paints are suitable for a variety of substrates but may require specific conditions to ensure proper adhesion and finish quality.
Considerations for International Buyers: Buyers should verify compliance with local regulations regarding VOC emissions and ensure that the paints meet relevant standards, such as ASTM D3359 for adhesion.
Summary Table of Material Selection for Automatic Spray Painting
Material | Typical Use Case for automatic spray painting | Key Advantage | Key Disadvantage/Limitation | Relative Cost (Low/Med/High) |
---|---|---|---|---|
Acrylics | General-purpose applications | Excellent adhesion and UV resistance | Limited chemical resistance | Medium |
Polyurethanes | Automotive and industrial coatings | Exceptional durability and chemical resistance | Higher cost and complex application process | High |
Epoxies | Marine and industrial environments | Superior adhesion and moisture resistance | Longer curing times | High |
Water-Based Paints | Indoor applications and eco-friendly projects | Lower VOC emissions and easy cleanup | Limited durability in harsh conditions | Low |
This guide aims to equip international B2B buyers with actionable insights for selecting the most suitable materials for automatic spray painting, taking into account regional considerations and compliance standards.
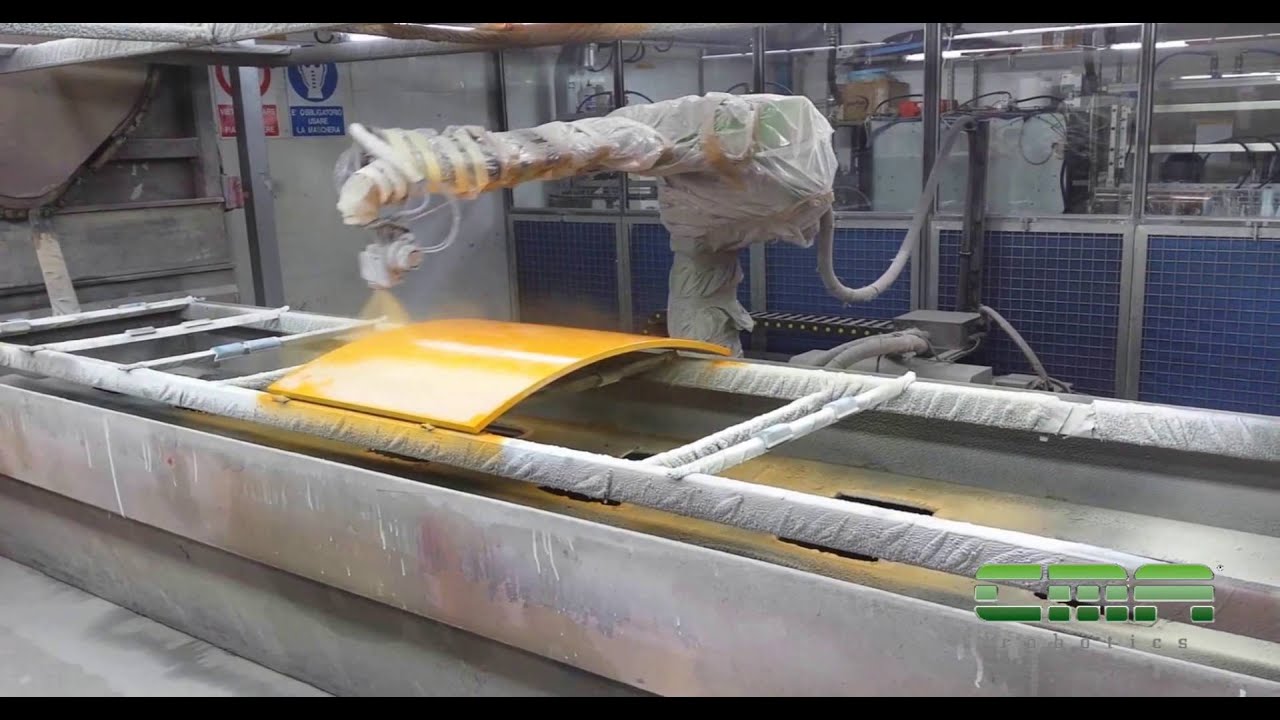
A stock image related to automatic spray painting.
In-depth Look: Manufacturing Processes and Quality Assurance for automatic spray painting
What Are the Key Stages in the Manufacturing Process of Automatic Spray Painting?
The manufacturing process for automatic spray painting involves several critical stages, each contributing to the overall quality and efficiency of the finished product. Understanding these stages can help B2B buyers from regions like Africa, South America, the Middle East, and Europe make informed decisions when sourcing suppliers.
1. Material Preparation
The first stage of the manufacturing process involves selecting and preparing the materials. This includes choosing the right type of paint, which can vary based on the application (e.g., automotive, industrial, or consumer goods). Proper preparation also involves surface cleaning and pre-treatment to ensure maximum adhesion of the paint. Techniques like sandblasting or chemical cleaning are often employed to remove contaminants.
2. Forming
After material preparation, the next step is forming the components that will be painted. This can involve processes such as molding, stamping, or machining, depending on the specific requirements of the product. It’s crucial to use precision techniques to maintain dimensional accuracy, which is vital for the final appearance and function of the painted surface.
3. Assembly
Once the individual parts are formed, they may need to be assembled before the painting process. This stage can include welding or fastening components together. For buyers, understanding the assembly process is essential, as it can impact the overall quality of the paint finish. A well-assembled product will have fewer defects and inconsistencies in the coating.
4. Finishing
The finishing stage is where the automatic spray painting occurs. This process typically involves the use of robotic arms equipped with advanced spray technology. These robots can achieve a consistent and uniform application of paint, reducing overspray and waste. Buyers should inquire about the specific equipment and techniques used, as advancements in technology can lead to better outcomes, such as improved finish quality and faster turnaround times.
How Is Quality Assurance Implemented in Automatic Spray Painting?
Quality assurance (QA) is an integral part of the manufacturing process, ensuring that the final products meet the required standards. For B2B buyers, understanding the QA protocols used by suppliers can significantly influence purchasing decisions.
What Are the Relevant International Standards for Quality Assurance?
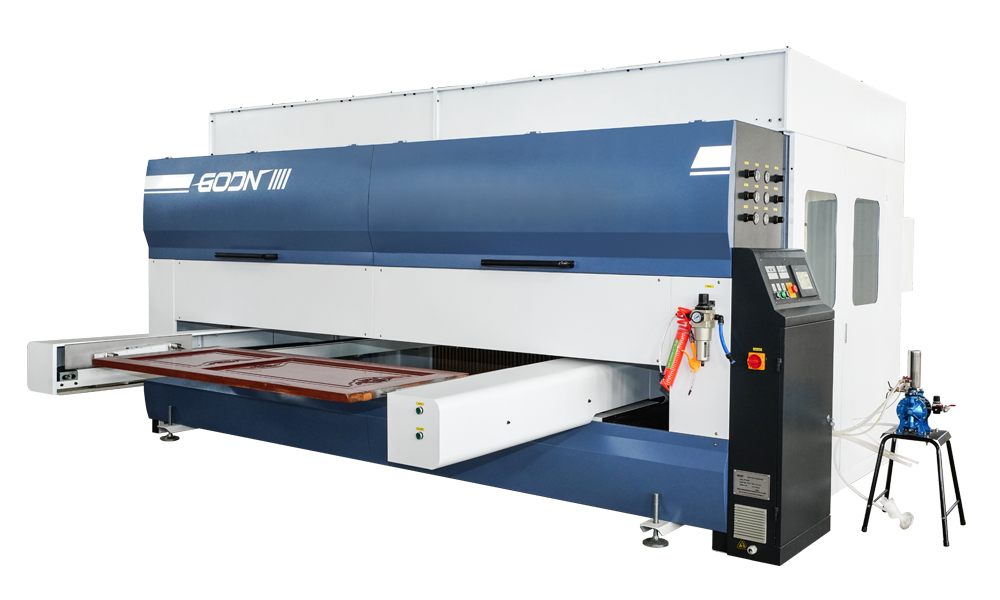
A stock image related to automatic spray painting.
Several international standards govern quality assurance in manufacturing, particularly in the context of automatic spray painting. ISO 9001 is one of the most recognized standards, focusing on quality management systems (QMS). Compliance with ISO 9001 indicates that a supplier has established processes to consistently provide products that meet customer and regulatory requirements.
In addition to ISO standards, industry-specific certifications may apply. For example, CE marking is essential for products sold in the European Union, indicating compliance with safety and environmental protection standards. In the oil and gas sector, the American Petroleum Institute (API) certification is often required.
What Are the Key QC Checkpoints in the Manufacturing Process?
Quality control (QC) checkpoints are critical for maintaining product integrity throughout the manufacturing process. Common checkpoints include:
-
Incoming Quality Control (IQC): This involves inspecting raw materials upon arrival to ensure they meet specified standards. For B2B buyers, verifying that suppliers perform rigorous IQC can help prevent issues later in the manufacturing process.
-
In-Process Quality Control (IPQC): During the manufacturing stages, IPQC ensures that processes are followed correctly, and any deviations are addressed immediately. This can include monitoring paint viscosity, application techniques, and environmental conditions.
-
Final Quality Control (FQC): After the painting process, FQC involves a thorough inspection of the finished product. This may include visual inspections, adhesion tests, and thickness measurements to ensure the paint meets quality standards.
What Common Testing Methods Are Used in Quality Assurance?
Quality assurance in automatic spray painting relies on various testing methods to ensure product integrity. Some of the most common methods include:
-
Adhesion Testing: This assesses the strength of the bond between the paint and the substrate. Techniques like cross-hatch testing or peel testing are commonly used.
-
Thickness Measurement: Ensuring the paint is applied at the correct thickness is vital for performance and aesthetics. Non-destructive methods, such as ultrasonic thickness gauges, are often employed.
-
Color Matching: For products requiring specific color standards, color matching is essential. Spectrophotometers are commonly used to ensure consistency with color specifications.
How Can B2B Buyers Verify Supplier Quality Control?
To ensure that suppliers maintain high-quality standards, B2B buyers can take several steps:
-
Conduct Audits: Regular audits of suppliers can help verify compliance with quality standards. This could involve on-site inspections or reviewing documentation related to their quality management systems.
-
Request Quality Reports: Buyers should ask suppliers for detailed quality reports that include data from IQC, IPQC, and FQC stages. These reports can provide insights into the supplier’s performance and adherence to standards.
-
Utilize Third-Party Inspections: Engaging third-party inspection agencies can provide an unbiased assessment of a supplier’s quality control processes. This is particularly important for buyers in regions where local standards may differ from international expectations.
What Are the Quality Control and Certification Nuances for International B2B Buyers?
For international buyers, particularly those from Africa, South America, the Middle East, and Europe, understanding the nuances of quality control and certification is crucial. Different regions may have varying standards and regulations, making it essential for buyers to ensure that their suppliers are compliant with both local and international requirements.
Buyers should be aware of the potential challenges in sourcing from suppliers in different regions, including language barriers, differing regulatory frameworks, and varying levels of expertise in quality assurance practices. Establishing clear communication and expectations regarding quality standards from the outset can help mitigate these challenges.
In conclusion, understanding the manufacturing processes and quality assurance protocols in automatic spray painting is essential for B2B buyers looking to source high-quality products. By focusing on key manufacturing stages, relevant standards, QC checkpoints, and verification methods, buyers can make informed decisions that ensure their procurement strategies align with quality expectations.
Practical Sourcing Guide: A Step-by-Step Checklist for ‘automatic spray painting’
Introduction
In the competitive landscape of automatic spray painting, sourcing the right equipment and suppliers is crucial for ensuring quality, efficiency, and cost-effectiveness. This practical sourcing guide provides a step-by-step checklist designed for international B2B buyers, particularly those from Africa, South America, the Middle East, and Europe. By following these actionable insights, you can streamline your procurement process and make informed decisions.
Step 1: Define Your Technical Specifications
Before initiating the sourcing process, it’s essential to clearly outline your technical requirements. Consider factors such as the type of materials you will be painting, the scale of production, and the desired finish quality.
- Material Compatibility: Ensure that the spray painting equipment is suitable for the specific materials you plan to use, such as metal, wood, or plastic.
- Production Volume: Assess your production needs to determine whether you require high-speed, automated systems or more versatile, manual options.
Step 2: Conduct Market Research
Thorough market research will help you identify potential suppliers and understand industry standards. This step is vital to stay competitive and informed about the latest technologies.
- Industry Trends: Look for innovations in automatic spray painting technologies that could enhance your operations.
- Regional Suppliers: Focus on suppliers that have a strong presence in your target market or region to facilitate easier communication and logistics.
Step 3: Evaluate Potential Suppliers
Before committing to a supplier, a comprehensive evaluation is necessary to ensure reliability and quality. Request documentation such as company profiles, case studies, and references from existing clients.
- Reputation: Research supplier reviews and ratings in the industry to gauge their standing.
- Experience: Consider suppliers who have a proven track record in your specific application area.
Step 4: Verify Supplier Certifications
Certifications and compliance with international standards are critical indicators of a supplier’s quality and reliability. Ensure that potential suppliers have the necessary certifications relevant to automatic spray painting.
- ISO Certification: Look for ISO 9001 or other relevant certifications that demonstrate a commitment to quality management.
- Safety Standards: Verify compliance with safety regulations applicable in your region, which can mitigate risks during operations.
Step 5: Request Samples and Demonstrations
Obtaining samples or arranging for demonstrations of the equipment can provide insights into its performance and suitability for your needs. This step is crucial for assessing quality firsthand.
- Performance Testing: Evaluate how the equipment performs under your specific conditions, including application speed and finish quality.
- Support and Training: Inquire about the supplier’s support services, including installation, maintenance, and operator training.
Step 6: Negotiate Terms and Conditions
Once you have identified a suitable supplier, negotiate favorable terms and conditions that align with your business objectives. This step can significantly impact your long-term relationship with the supplier.
- Pricing Structure: Discuss payment terms, discounts for bulk purchases, and potential future price adjustments.
- Delivery Timelines: Confirm lead times for equipment delivery and setup, ensuring they align with your production schedules.
Step 7: Establish a Communication Plan
Effective communication with your supplier is vital for a successful partnership. Establish a clear communication plan that outlines key points of contact, preferred communication channels, and regular check-ins.
- Feedback Loops: Create a system for providing feedback on equipment performance and any issues that arise.
- Continual Improvement: Foster an environment for collaboration, allowing both parties to discuss improvements or adjustments needed over time.
By following this checklist, international B2B buyers can effectively navigate the complexities of sourcing automatic spray painting solutions, ensuring they select the best equipment and suppliers for their specific needs.
Comprehensive Cost and Pricing Analysis for automatic spray painting Sourcing
What Are the Key Cost Components in Automatic Spray Painting?
When sourcing automatic spray painting solutions, understanding the cost structure is essential for effective budgeting and decision-making. The primary cost components include:
-
Materials: The type of paint, solvents, and additives directly impact costs. High-quality materials often come with a higher price tag but can lead to superior finishes and durability.
-
Labor: Skilled labor is necessary for both the operation of spray painting equipment and the maintenance of quality standards. Labor costs can vary significantly based on the region and expertise required.
-
Manufacturing Overhead: This encompasses utilities, maintenance of equipment, and depreciation. Regions with lower operational costs may offer more competitive pricing.
-
Tooling: Initial investment in specialized tools or equipment can be substantial but is often amortized over time, especially with high-volume production.
-
Quality Control (QC): Implementing robust QC processes ensures that the final product meets specifications. While this may increase upfront costs, it can prevent costly reworks or returns.
-
Logistics: Transportation and shipping costs can fluctuate based on distance, shipping methods, and regional tariffs. Understanding these costs is crucial for accurate pricing.
-
Margin: Suppliers typically include a profit margin in their pricing. This margin can vary based on competition and the perceived value of the service.
How Do Pricing Influencers Affect Sourcing Decisions?
Several factors can influence the pricing of automatic spray painting services:
-
Volume and Minimum Order Quantity (MOQ): Larger orders often benefit from volume discounts, making it essential for buyers to negotiate MOQs that align with their production needs.
-
Specifications and Customization: Custom requirements, such as unique colors or finishes, can increase costs. Buyers should clearly define specifications to avoid unexpected charges.
-
Materials Quality and Certifications: Higher quality materials or specific certifications (e.g., environmental compliance) can lead to increased costs but may offer long-term benefits in performance and sustainability.
-
Supplier Factors: The supplier’s reputation, location, and operational efficiencies can all impact pricing. Engaging with multiple suppliers can help identify the best value.
-
Incoterms: The agreed-upon Incoterms can significantly affect the total landed cost of goods. Understanding terms like FOB (Free on Board) or CIF (Cost, Insurance, and Freight) is vital for pricing negotiations.
What Buyer Tips Can Enhance Cost-Efficiency in Automatic Spray Painting?
To optimize costs when sourcing automatic spray painting, consider the following strategies:
-
Negotiate Effectively: Engage suppliers in discussions about pricing, especially if you can provide them with bulk orders or long-term contracts. Building a solid relationship can yield better pricing over time.
-
Evaluate Total Cost of Ownership (TCO): Look beyond initial pricing. Consider maintenance, operational efficiency, and potential rework costs. A higher upfront cost may result in lower TCO if it leads to better quality and fewer issues.
-
Understand Pricing Nuances for International Sourcing: For buyers in Africa, South America, the Middle East, and Europe, be aware of regional market dynamics. Currency fluctuations, local economic conditions, and trade agreements can all influence final pricing.
-
Conduct Market Research: Investigate market trends and competitor pricing to ensure you are getting a fair deal. Leverage industry reports or trade shows to gather insights.
-
Be Aware of Indicative Prices: Pricing can vary widely based on market conditions, supplier negotiations, and order specifics. Always request detailed quotes and be cautious of prices that seem too low, as they may reflect compromised quality.
By understanding these cost components and pricing influencers, B2B buyers can make informed decisions that balance quality and cost, ultimately leading to successful sourcing outcomes in the automatic spray painting market.
Alternatives Analysis: Comparing automatic spray painting With Other Solutions
When considering automatic spray painting, B2B buyers often seek to understand how it stacks up against alternative solutions. This section will compare automatic spray painting with two prominent alternatives: Powder Coating and Manual Spray Painting. Each method has unique advantages and disadvantages, making it crucial for buyers to evaluate their specific needs and operational contexts.
Comparison Table of Automatic Spray Painting and Alternatives
Comparison Aspect | Automatic Spray Painting | Powder Coating | Manual Spray Painting |
---|---|---|---|
Performance | High precision and uniform coverage | Excellent durability and finish quality | Variable; depends on skill of operator |
Cost | Higher initial investment, lower operating costs | Moderate initial investment, lower material waste | Low initial investment, but high labor costs |
Ease of Implementation | Requires specialized equipment and training | Requires curing ovens and specific equipment | Simple setup, minimal training required |
Maintenance | Moderate; requires regular servicing | Low; minimal maintenance needed | High; frequent equipment cleaning and maintenance |
Best Use Case | High-volume production with consistent results | Heavy-duty applications needing durability | Small-scale projects or custom jobs |
What are the Pros and Cons of Powder Coating Compared to Automatic Spray Painting?
Powder Coating is a popular alternative known for its durability and finish quality. It involves applying a dry powder that is then cured under heat to form a hard finish.
Pros:
– Durability: Offers excellent resistance to scratching, chipping, and fading, making it ideal for outdoor applications.
– Environmental Benefits: Produces minimal volatile organic compounds (VOCs), making it a more environmentally friendly option.
Cons:
– Initial Investment: Requires specialized equipment, including curing ovens, which can elevate startup costs.
– Complexity: The process can be more complex, requiring careful control of environmental conditions.
How Does Manual Spray Painting Compare to Automatic Spray Painting?
Manual Spray Painting is a traditional method where operators use spray guns to apply paint. This method can be effective but varies significantly in outcome based on the operator’s skill level.
Pros:
– Cost-Effective: Lower initial investment compared to automated systems, making it accessible for small businesses.
– Flexibility: Ideal for custom jobs and small-scale projects where varied designs and colors are needed.
Cons:
– Inconsistency: The quality of the finish can vary widely based on the operator’s skill, leading to potential waste and rework.
– Labor Intensive: Requires more labor hours, which can lead to higher overall costs in large-scale operations.
How Can B2B Buyers Choose the Right Solution for Their Needs?
When selecting between automatic spray painting, powder coating, and manual spray painting, B2B buyers should consider their operational scale, budget constraints, and product requirements. For high-volume production where consistency is paramount, automatic spray painting may be the best option. Conversely, for projects demanding durability and a high-quality finish, powder coating could be the ideal choice. Meanwhile, for small-scale or custom projects, manual spray painting offers flexibility and lower initial costs. Each solution carries unique attributes that can align with specific business needs, making it essential for buyers to conduct a thorough analysis before making a decision.
Essential Technical Properties and Trade Terminology for automatic spray painting
What Are the Key Technical Properties for Automatic Spray Painting?
When considering automatic spray painting, understanding the essential technical properties is crucial for ensuring optimal performance and quality. Here are some key specifications that B2B buyers should be aware of:
1. Material Compatibility
Material compatibility refers to how well the spray paint adheres to different substrates, such as metal, plastic, or wood. This property is vital for ensuring a durable finish that meets the specific requirements of your project. B2B buyers should assess whether the spray painting equipment can handle the materials they work with, as improper compatibility can lead to issues like peeling or fading.
2. Spray Pattern Control
The ability to control the spray pattern is critical for achieving uniform coverage. This specification includes parameters such as fan width and droplet size. A wider fan can cover larger areas quickly, while a finer droplet size may be necessary for intricate details. Buyers should evaluate how different machines manage spray patterns to meet their production needs efficiently.
3. Viscosity Range
Viscosity indicates the thickness of the paint and is essential for achieving the desired finish. A machine’s ability to handle a specific viscosity range directly affects the application method and the final appearance. B2B buyers must ensure that the spray painting equipment they choose can accommodate the viscosity of the paints they intend to use, as this can impact both the quality and speed of the painting process.
4. Drying Time
Drying time is a critical property that influences production efficiency. Fast-drying paints can significantly reduce turnaround times, allowing for quicker project completion. Buyers should consider the drying time of the paints they plan to use and how the automatic spray painting equipment can be optimized to accommodate these requirements, especially in high-volume production environments.
5. Tolerance Levels
Tolerance refers to the allowable deviation from specified dimensions in the painted product. In industries where precision is key, such as automotive or aerospace, understanding the tolerance levels of both the equipment and the paint is essential. Buyers must inquire about the tolerances that the equipment can achieve to ensure they meet industry standards and client specifications.
What Are Common Trade Terms in Automatic Spray Painting?
Understanding industry terminology is equally important for navigating the procurement process. Here are some common trade terms relevant to automatic spray painting:
1. OEM (Original Equipment Manufacturer)
OEM refers to companies that produce parts or equipment that may be marketed by another manufacturer. In the context of spray painting, it is crucial for buyers to know whether they are sourcing products directly from the OEM or through a distributor, as this can affect pricing, warranty, and support.
2. MOQ (Minimum Order Quantity)
MOQ is the smallest quantity of a product that a supplier is willing to sell. For B2B buyers, understanding the MOQ can help manage inventory and cash flow effectively. It’s essential to negotiate terms that align with your production needs while ensuring you do not overcommit to inventory.
3. RFQ (Request for Quotation)
An RFQ is a document that buyers send to suppliers to request pricing for specific goods or services. In the context of automatic spray painting, issuing an RFQ can help buyers gather detailed pricing information, enabling them to make informed purchasing decisions.
4. Incoterms (International Commercial Terms)
Incoterms are a set of international rules that define the responsibilities of sellers and buyers in global trade. Understanding these terms is essential for B2B transactions, especially when sourcing equipment or materials from different countries. Familiarity with Incoterms can help avoid misunderstandings related to shipping, insurance, and import duties.
By grasping these technical properties and trade terminologies, B2B buyers can make informed decisions that enhance their operations in automatic spray painting, ultimately leading to better product quality and operational efficiency.
Navigating Market Dynamics and Sourcing Trends in the automatic spray painting Sector
What Are the Current Market Dynamics and Key Trends in Automatic Spray Painting?
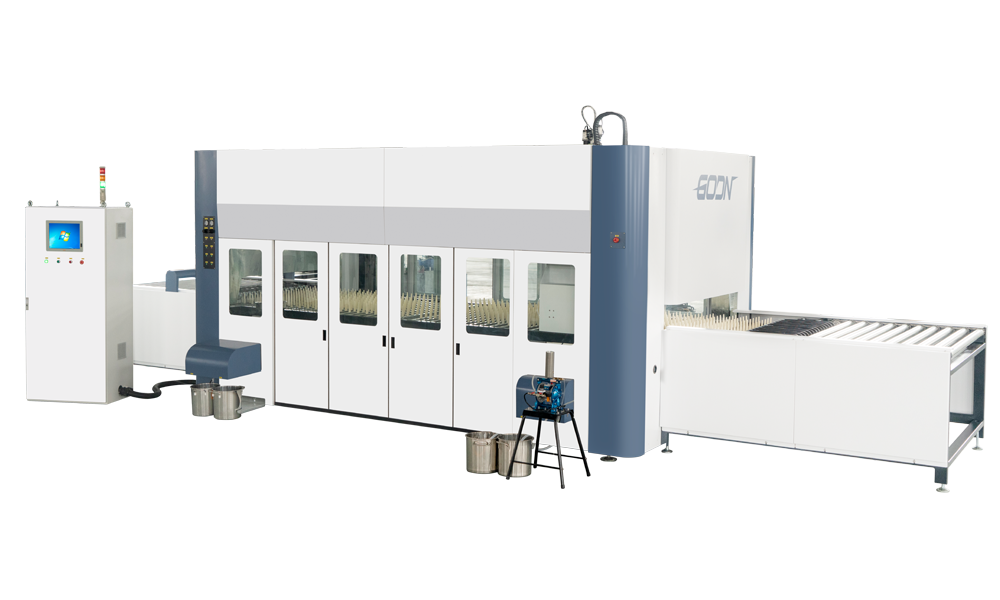
A stock image related to automatic spray painting.
The automatic spray painting sector is witnessing significant transformation driven by technological advancements, changing consumer preferences, and global market dynamics. Key trends include the increasing adoption of automation and robotics, which enhance precision and efficiency while reducing labor costs. This trend is particularly advantageous for B2B buyers in regions like Africa and South America, where labor shortages and rising wages are pressing concerns. Additionally, innovations in spray painting technology, such as electrostatic spraying and high-volume low-pressure (HVLP) systems, are gaining traction, offering improved transfer efficiency and reduced overspray, which is crucial for minimizing material wastage.
Another vital market driver is the growing demand for customization and personalization across industries such as automotive, aerospace, and consumer goods. B2B buyers are encouraged to seek suppliers that can offer flexible solutions tailored to specific project requirements. Furthermore, the increasing focus on digital transformation is reshaping sourcing strategies, with many companies integrating software solutions for real-time monitoring and quality control in their spray painting processes. This shift not only enhances operational efficiency but also provides buyers with better visibility into their supply chains.
How Does Sustainability and Ethical Sourcing Impact the Automatic Spray Painting Sector?
Sustainability is becoming a pivotal concern for international B2B buyers, particularly as regulatory pressures and consumer expectations evolve. The automatic spray painting sector faces scrutiny regarding its environmental impact, particularly concerning volatile organic compounds (VOCs) and hazardous materials used in traditional paint formulations. B2B buyers should prioritize suppliers that offer eco-friendly alternatives, such as water-based paints or low-VOC products, which not only comply with regulations but also align with sustainable business practices.
Moreover, ethical sourcing is increasingly important in building a responsible supply chain. Buyers should evaluate suppliers based on their commitment to ethical labor practices and sustainability certifications, such as ISO 14001 for environmental management and LEED for green building practices. Implementing a framework for assessing supplier sustainability can lead to long-term partnerships and enhanced brand reputation, particularly in regions like Europe where consumers are more environmentally conscious.
What Is the Evolution of Automatic Spray Painting Technology?
The evolution of automatic spray painting technology can be traced back to the early 20th century, when manual methods dominated the industry. The introduction of automated systems in the 1960s marked a turning point, significantly increasing production speeds and consistency. Over the decades, advancements in computer technology and robotics have enabled the development of sophisticated spray painting systems that offer unparalleled precision and efficiency.
Today, the integration of Industry 4.0 principles is revolutionizing the automatic spray painting landscape. B2B buyers now have access to cutting-edge technologies such as machine learning and artificial intelligence, enabling predictive maintenance and real-time quality assurance. As these technologies continue to evolve, they promise to further enhance the capabilities of automatic spray painting, making it an essential component of modern manufacturing processes.
International B2B buyers are thus encouraged to stay informed about these technological advancements and consider how they can leverage them to enhance their operations and competitive edge in the market.
Frequently Asked Questions (FAQs) for B2B Buyers of automatic spray painting
-
How do I select the right automatic spray painting system for my business needs?
Choosing the appropriate automatic spray painting system involves assessing your production volume, the types of materials you’ll be working with, and the specific finishes you require. Start by evaluating the size of your operation—whether you need a compact system for small batches or a high-capacity solution for large-scale production. Additionally, consider the compatibility of the system with your existing equipment and the flexibility it offers for different paint types. Engaging with suppliers who can provide demonstrations or case studies related to your industry can also aid in making an informed decision. -
What are the key factors to consider when sourcing suppliers for automatic spray painting?
When sourcing suppliers, evaluate their industry reputation, experience, and certifications. Look for suppliers who have a proven track record in your specific sector and offer after-sales support, including maintenance and training. Additionally, consider their production capabilities, lead times, and whether they can accommodate customization requests. It’s beneficial to request references or reviews from other B2B clients, particularly those in your region, to gauge reliability and service quality. -
What customization options are available for automatic spray painting equipment?
Many manufacturers offer customization options tailored to your specific operational needs. These may include adjustable spray patterns, varying paint application thicknesses, and modifications for different substrates. Additionally, consider options for automation integration, such as robotic arms or conveyor systems, to enhance efficiency. Discuss your requirements with suppliers to explore the range of modifications they can provide, ensuring they align with your production goals and budget. -
What are the typical minimum order quantities (MOQs) for automatic spray painting systems?
Minimum order quantities can vary significantly among suppliers based on the complexity and cost of the equipment. For large-scale systems, MOQs may be higher due to production costs, while smaller, modular systems may have lower MOQs. When negotiating, communicate your needs clearly and explore options for phased orders or shared shipments if your volume is below the standard MOQ. This approach can help you manage cash flow while still acquiring the necessary equipment. -
What payment terms should I expect when purchasing automatic spray painting systems?
Payment terms can differ based on the supplier’s policies and your business relationship. Common terms include a deposit upfront, followed by the balance upon delivery or installation. For international transactions, consider discussing options like letters of credit or escrow services to secure the payment process. Ensure clarity on currency exchange rates and any additional fees related to international shipping or customs to avoid unexpected costs. -
How do I ensure quality assurance (QA) in my automatic spray painting systems?
To guarantee quality assurance, request detailed specifications and performance metrics from your suppliers. Implement a rigorous inspection process upon delivery, including testing for operational efficiency and finish quality. Additionally, inquire about the supplier’s QA processes, including any certifications they hold, such as ISO standards. Establishing a clear communication channel for feedback and ongoing support will also help maintain quality in your operations. -
What logistics considerations should I keep in mind when importing automatic spray painting systems?
When importing equipment, factor in shipping times, customs clearance, and any applicable tariffs or duties. Coordinate with logistics providers who specialize in international shipping to ensure compliance with local regulations in your country. Additionally, assess the reliability of your chosen shipping method—air freight may be faster but more costly, while sea freight can be economical for larger shipments. Planning for potential delays and ensuring you have adequate insurance coverage will help mitigate risks. -
How can I evaluate the return on investment (ROI) for automatic spray painting systems?
To assess ROI, begin by calculating the total cost of ownership, including purchase price, maintenance, and operational expenses. Compare this with projected gains, such as increased production efficiency, reduced labor costs, and improved product quality. Conduct a break-even analysis to determine how long it will take to recoup your investment based on increased output and sales. Regularly review performance metrics post-implementation to adjust strategies and maximize ROI over time.
Important Disclaimer & Terms of Use
⚠️ Important Disclaimer
The information provided in this guide, including content regarding manufacturers, technical specifications, and market analysis, is for informational and educational purposes only. It does not constitute professional procurement advice, financial advice, or legal advice.
While we have made every effort to ensure the accuracy and timeliness of the information, we are not responsible for any errors, omissions, or outdated information. Market conditions, company details, and technical standards are subject to change.
B2B buyers must conduct their own independent and thorough due diligence before making any purchasing decisions. This includes contacting suppliers directly, verifying certifications, requesting samples, and seeking professional consultation. The risk of relying on any information in this guide is borne solely by the reader.
Strategic Sourcing Conclusion and Outlook for automatic spray painting
As businesses across Africa, South America, the Middle East, and Europe increasingly adopt automatic spray painting technologies, strategic sourcing emerges as a pivotal factor in achieving competitive advantage. Understanding the nuances of sourcing high-quality equipment and materials can significantly impact operational efficiency and product quality. Buyers must prioritize suppliers who not only provide advanced technology but also demonstrate sustainability and compliance with regional regulations.
What are the key benefits of strategic sourcing in automatic spray painting? Effective sourcing strategies can lead to cost savings, improved supplier relationships, and enhanced innovation. By leveraging local suppliers where possible, businesses can also reduce lead times and logistics costs, particularly relevant for companies in emerging markets.
Looking ahead, international B2B buyers should remain proactive in exploring partnerships that align with their long-term goals. As the demand for high-quality finishes continues to rise, investing in automation technology will be crucial for maintaining market relevance. Engage with suppliers who are committed to innovation and sustainability to stay ahead of industry trends. The future of automatic spray painting is bright, and those who strategically source their materials and equipment will be best positioned to thrive.