Enhance Efficiency: The Ultimate Rock Crusher Guide (2025)
Introduction: Navigating the Global Market for rock crusher
In the competitive landscape of construction and mining, sourcing the right rock crusher can be a daunting challenge for international B2B buyers. The diversity of rock crusher types—ranging from jaw crushers to cone crushers—coupled with varying applications across industries such as aggregate production and mineral processing, makes it essential to navigate the global market with a strategic approach. This comprehensive guide serves as a vital resource, addressing key factors such as supplier vetting, cost considerations, and maintenance requirements, all tailored to empower decision-makers from Africa, South America, the Middle East, and Europe, including regions like the UK and Spain.
Understanding the nuances of the rock crusher market is crucial for maximizing investment and ensuring operational efficiency. This guide delves into the specific types of rock crushers available, their applications in various sectors, and insights into the best practices for selecting suppliers who meet international standards. By providing actionable insights and data-driven recommendations, this resource equips B2B buyers with the knowledge needed to make informed purchasing decisions, ultimately leading to enhanced productivity and profitability. Whether you are looking to expand your operations or optimize existing processes, this guide will illuminate the path to successful sourcing and integration of rock crushers in your business strategy.
Understanding rock crusher Types and Variations
Type Name | Key Distinguishing Features | Primary B2B Applications | Brief Pros & Cons for Buyers |
---|---|---|---|
Jaw Crusher | Simple design, high compression ratio | Mining, construction, recycling | Pros: Durable, low maintenance; Cons: Limited size reduction capability. |
Cone Crusher | Conical shape, adjustable discharge size | Quarrying, mineral processing | Pros: Versatile, efficient; Cons: Higher operational costs. |
Impact Crusher | Uses impact force, produces cubical shapes | Recycling, aggregate production | Pros: Excellent for soft materials; Cons: Limited efficiency with hard rocks. |
Gyratory Crusher | Large capacity, continuous operation | Mining, large-scale operations | Pros: High throughput, effective for large rocks; Cons: Requires significant space. |
Roll Crusher | Two parallel rolls, low noise operation | Coal processing, cement industry | Pros: Low energy consumption; Cons: Limited to softer materials. |
What are the Characteristics and Suitability of Jaw Crushers?
Jaw crushers are one of the most common types of rock crushers, renowned for their straightforward design and functionality. They operate by using compressive force to break down materials, making them ideal for primary crushing in mining and construction sectors. When considering a jaw crusher for purchase, buyers should evaluate factors such as size, capacity, and the nature of the materials being processed. While they are generally durable and require low maintenance, jaw crushers may not be the best option for operations requiring significant size reduction.
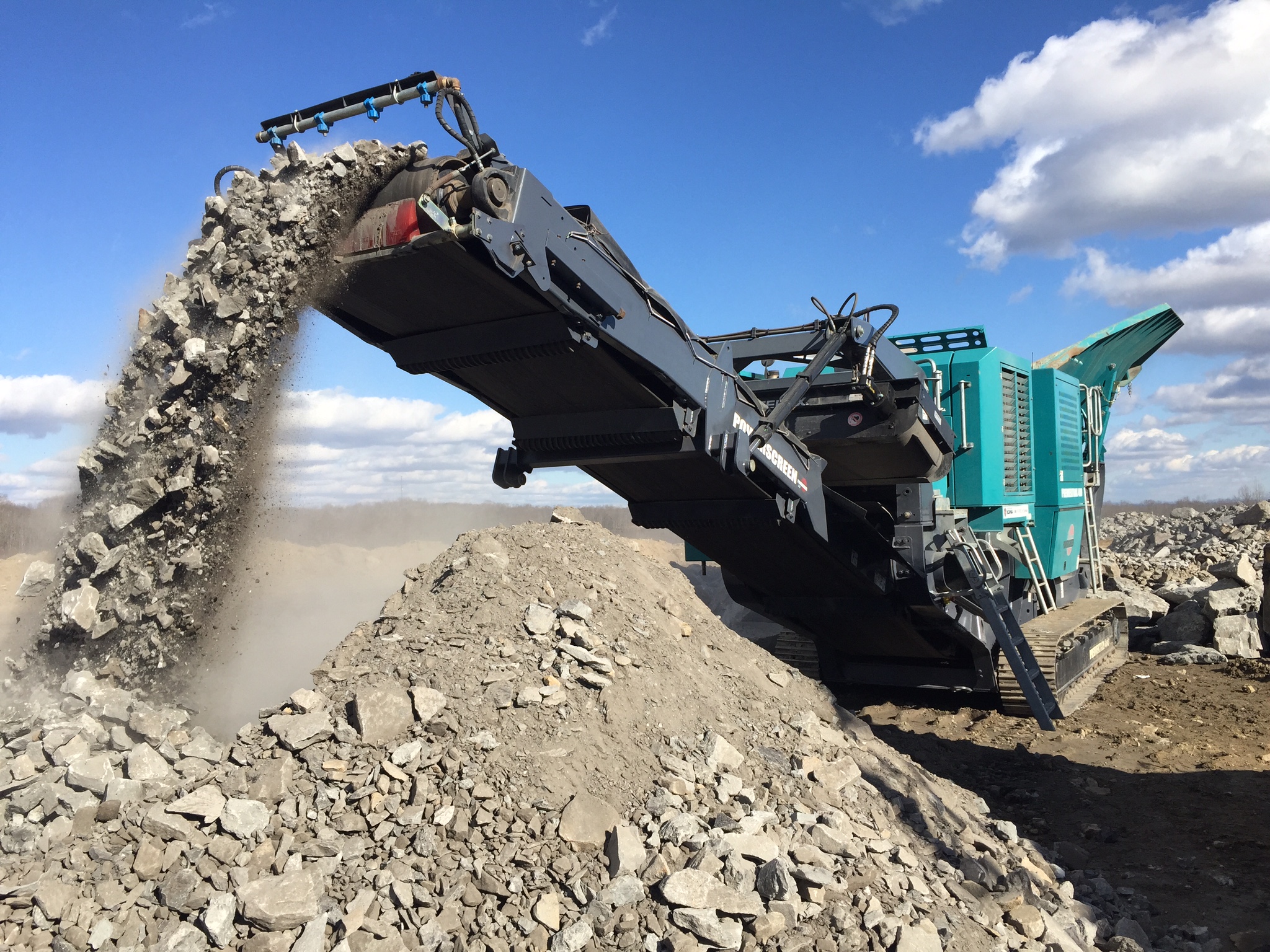
A stock image related to rock crusher.
How Do Cone Crushers Work and What Are Their Applications?
Cone crushers feature a conical design that allows for adjustable discharge sizes, which makes them suitable for various applications, including quarrying and mineral processing. They are particularly effective for secondary and tertiary crushing, providing a high reduction ratio. B2B buyers should consider the specific material characteristics and desired output when selecting a cone crusher. While they offer versatility and efficiency, the operational costs can be higher compared to other types, necessitating a thorough cost-benefit analysis.
What Are the Advantages of Impact Crushers for B2B Buyers?
Impact crushers utilize impact force to crush materials, producing cubical shapes that are highly desirable in aggregate production and recycling applications. They excel in processing softer materials, making them a preferred choice for projects that involve asphalt or concrete recycling. Buyers should assess the impact crusher’s feed size and desired output to ensure compatibility with their operations. While they offer excellent performance with softer materials, their efficiency decreases with harder rocks, which can limit their utility in certain projects.
Why Choose Gyratory Crushers for Large-Scale Operations?
Gyratory crushers are designed for high capacity and continuous operation, making them suitable for large-scale mining and industrial applications. Their ability to handle large rocks and produce significant throughput is a major advantage for B2B buyers in the mining sector. However, the space requirements for installation can be considerable, and potential buyers should factor in site dimensions and operational needs. While they can be a significant investment, their efficiency in high-volume applications often justifies the cost.
What Are the Key Considerations for Roll Crushers?
Roll crushers operate using two parallel rolls to crush materials, which results in a low-noise operation. They are commonly used in coal processing and the cement industry. B2B buyers should consider the hardness of the material being processed, as roll crushers are limited to softer materials. Their low energy consumption is a significant advantage, making them cost-effective for specific applications. However, buyers must weigh these benefits against the limitations in terms of material hardness and size reduction capabilities.
Related Video: Types of Rock Crusher Machines
Key Industrial Applications of rock crusher
Industry/Sector | Specific Application of Rock Crusher | Value/Benefit for the Business | Key Sourcing Considerations for this Application |
---|---|---|---|
Construction & Demolition | Aggregate production for concrete and asphalt | Efficient material recycling, cost savings, and reduced landfill waste | Durability, maintenance support, and availability of parts |
Mining | Ore processing and extraction | Enhanced extraction efficiency and improved ore quality | Compliance with local regulations, equipment size, and power needs |
Road Construction | Base material preparation for roads | Improved road stability and longevity | Material compatibility, ease of transport, and local sourcing options |
Quarrying | Stone and gravel production | High output capacity and reduced operational costs | Performance metrics, supplier reputation, and after-sales service |
Environmental Management | Waste management and recycling | Contribution to sustainable practices and reduced environmental impact | Technology for dust control, energy efficiency, and operational support |
How is Rock Crusher Used in Construction & Demolition?
In the construction and demolition sector, rock crushers are vital for producing aggregates used in concrete and asphalt. They facilitate the recycling of construction waste, turning it into reusable materials. This not only reduces costs associated with purchasing new materials but also minimizes landfill usage. International buyers must consider the machine’s durability and the availability of maintenance support, especially in regions like Africa and South America, where access to parts can be limited.
What Role Does Rock Crusher Play in Mining Operations?
In mining, rock crushers are essential for the processing and extraction of ores. They help in breaking down large rocks into smaller, manageable pieces, enhancing the efficiency of mineral extraction. This results in improved ore quality and higher yields. Buyers should focus on compliance with local mining regulations and ensure that the equipment can handle the specific power and size requirements of their operations, particularly in the Middle East and Europe.
How Does Rock Crusher Benefit Road Construction?
Rock crushers are used extensively in road construction for preparing base materials. They crush and screen rocks to produce a stable foundation for roads, which enhances durability and reduces maintenance costs. For B2B buyers, it’s crucial to evaluate the compatibility of the crushed materials with local soil types and the ease of transport to construction sites, especially in remote areas of South America and Africa.
What is the Importance of Rock Crusher in Quarrying?
In the quarrying industry, rock crushers are indispensable for producing stone and gravel. They provide high output capacity, which is essential for meeting demand in various construction projects. Effective sourcing involves assessing performance metrics and the supplier’s reputation to ensure reliability and quality. After-sales service is also a critical consideration, particularly for European buyers who may require ongoing support.
How Can Rock Crusher Contribute to Environmental Management?
Rock crushers play a significant role in environmental management by facilitating waste management and recycling efforts. They can process construction and demolition debris, contributing to sustainable practices and reducing environmental impact. Buyers should look for crushers equipped with technologies that control dust and enhance energy efficiency, which is increasingly important in environmentally conscious markets across Europe and the Middle East.
Related Video: “Big Rock Crusher Machine: A Giant in Action”Big Rock Crushing: A Powerful Process”
3 Common User Pain Points for ‘rock crusher’ & Their Solutions
Scenario 1: High Maintenance Costs of Rock Crushers
The Problem:
B2B buyers often grapple with the high maintenance costs associated with rock crushers. For companies operating in regions like Africa and South America, where access to spare parts can be limited and service technicians may be scarce, the financial burden can escalate quickly. Frequent breakdowns not only lead to increased downtime but also result in unexpected repair expenses, which can erode profit margins significantly. Buyers may feel trapped in a cycle of costly repairs, impacting their operational efficiency and overall productivity.
The Solution:
To mitigate high maintenance costs, B2B buyers should prioritize sourcing rock crushers with a strong reputation for durability and reliability. When selecting equipment, buyers should conduct thorough research into manufacturers known for their quality and after-sales support. It is advisable to look for models that come with comprehensive warranties and readily available spare parts. Additionally, implementing a proactive maintenance schedule, including regular inspections and preventive servicing, can help identify potential issues before they escalate into costly repairs. Investing in training for in-house maintenance staff can also empower teams to address minor repairs quickly, reducing reliance on external technicians.
Scenario 2: Inefficient Crushing Performance Leading to Production Delays
The Problem:
Another prevalent issue is inefficient crushing performance, which can lead to significant production delays. In industries such as construction and mining, the ability to process materials swiftly is crucial. Buyers often find themselves frustrated when the rock crushers they invested in fail to meet expected throughput rates, resulting in bottlenecks in production. This inefficiency can hinder project timelines and affect customer satisfaction, particularly in competitive markets in Europe and the Middle East.
The Solution:
To enhance crushing performance, buyers should focus on selecting the right type of rock crusher tailored to their specific material and processing needs. It is essential to understand the characteristics of the materials being crushed, such as hardness and size, to choose the appropriate crusher type—be it jaw, cone, or impact crushers. Collaborating with manufacturers or industry experts can provide insights into optimal configurations and settings that maximize efficiency. Additionally, integrating technology solutions such as automation and monitoring systems can help track performance metrics in real-time, allowing for timely adjustments and minimizing downtime.
Scenario 3: Environmental Regulations and Compliance Challenges
The Problem:
In many regions, particularly in Europe and the Middle East, stringent environmental regulations pose a significant challenge for B2B buyers of rock crushers. Compliance with noise, dust, and emissions standards can be daunting, especially for companies that are unprepared or unaware of the local regulations. Failure to adhere to these regulations can lead to fines, project delays, and reputational damage, creating a complex landscape for buyers who must balance operational efficiency with environmental responsibility.
The Solution:
To navigate environmental compliance challenges, B2B buyers should conduct a thorough assessment of local regulations before purchasing a rock crusher. Engaging with environmental consultants or legal experts can provide clarity on the specific requirements that must be met. Choosing rock crushers equipped with advanced dust suppression systems, noise reduction technologies, and energy-efficient designs can help companies stay compliant while maintaining productivity. Additionally, investing in training programs for staff on environmental best practices can foster a culture of compliance and awareness within the organization, ultimately protecting the company from potential regulatory issues.
Strategic Material Selection Guide for rock crusher
When selecting materials for rock crushers, international B2B buyers must consider various factors that influence performance, durability, and cost. The choice of material can significantly affect the operational efficiency and maintenance requirements of the equipment. Below, we analyze four common materials used in rock crushers, providing insights tailored for buyers from Africa, South America, the Middle East, and Europe.
What are the Key Properties of High Carbon Steel for Rock Crushers?
High carbon steel is a popular choice for rock crusher components due to its hardness and wear resistance. With a carbon content typically between 0.6% and 1.4%, this material can withstand high temperatures and pressures, making it suitable for crushing hard materials. Its excellent tensile strength enhances its durability, but it can be prone to brittleness under extreme conditions.
Pros & Cons: High carbon steel is relatively cost-effective and offers good performance in high-impact applications. However, it may require more complex manufacturing processes and can be susceptible to corrosion if not properly treated.
Impact on Application: This material is particularly effective for crushing hard rocks and aggregates, making it a preferred choice in construction and mining sectors.
Considerations for International Buyers: Buyers should ensure compliance with relevant standards such as ASTM or DIN. In regions like Europe and the Middle East, certifications for quality and environmental impact are crucial.
How Does Manganese Steel Enhance Rock Crusher Performance?
Manganese steel, known for its high impact strength and resistance to abrasion, is widely used in rock crushers. Typically containing around 12% to 14% manganese, this material becomes work-hardened during operation, increasing its toughness and wear resistance.
Pros & Cons: The key advantage of manganese steel is its ability to withstand severe wear and tear, making it ideal for heavy-duty applications. However, it is more expensive than other materials and can be challenging to machine.
Impact on Application: Manganese steel is particularly suited for the crushing of abrasive materials, such as granite and basalt, which are commonly found in Africa and South America.
Considerations for International Buyers: Buyers should be aware of the specific grades of manganese steel that meet local standards and regulations. In Europe, for example, compliance with EN standards is essential.
Why is Alloy Steel a Versatile Choice for Rock Crushers?
Alloy steel, which includes elements such as chromium, nickel, and molybdenum, offers a balance of strength, toughness, and corrosion resistance. Its properties can be tailored through heat treatment, making it suitable for various applications in rock crushing.
Pros & Cons: The versatility of alloy steel allows for customization based on specific operational needs, providing a good balance between cost and performance. However, the manufacturing process can be more complex, leading to higher production costs.
Impact on Application: Alloy steel is effective in a range of applications, including both primary and secondary crushing, and is suitable for diverse materials.
Considerations for International Buyers: Buyers should ensure that the alloy steel used meets international quality standards and certifications. In regions like the Middle East, where environmental conditions can be harsh, corrosion resistance is a significant factor.
What are the Benefits of Ceramic Composites in Rock Crushers?
Ceramic composites are emerging as a high-performance material for rock crushers, particularly in applications requiring high wear resistance and low weight. These materials can withstand extreme temperatures and corrosive environments, making them suitable for various applications.
Pros & Cons: The primary advantage of ceramic composites is their exceptional durability and lightweight nature, which can lead to reduced energy consumption. However, they can be more expensive and may require specialized handling and installation.
Impact on Application: Ceramic composites are particularly effective in applications where traditional materials may fail due to wear, such as in recycling operations or when processing abrasive materials.
Considerations for International Buyers: Buyers should evaluate the availability of ceramic composites in their region and consider the potential need for specialized equipment or expertise for installation and maintenance.
Summary Table of Material Selection for Rock Crushers
Material | Typical Use Case for Rock Crusher | Key Advantage | Key Disadvantage/Limitation | Relative Cost (Low/Med/High) |
---|---|---|---|---|
High Carbon Steel | Crushing hard rocks and aggregates | Cost-effective and durable | Prone to corrosion and brittleness | Medium |
Manganese Steel | Heavy-duty applications for abrasive materials | High impact strength and wear resistance | Expensive and difficult to machine | High |
Alloy Steel | Versatile applications in primary and secondary crushing | Customizable properties | Higher production costs | Medium |
Ceramic Composites | Recycling and processing abrasive materials | Exceptional durability and lightweight | High cost and specialized handling | High |
This guide provides a comprehensive overview of material options for rock crushers, assisting international B2B buyers in making informed decisions tailored to their specific operational needs and regional standards.
In-depth Look: Manufacturing Processes and Quality Assurance for rock crusher
What Are the Main Stages of Manufacturing a Rock Crusher?
The manufacturing process for rock crushers involves several critical stages, each designed to ensure durability, efficiency, and performance. The primary stages include:
Material Preparation
The first step is sourcing high-quality raw materials, typically high-strength steel and alloy components that can withstand the rigors of crushing. Suppliers must ensure that the materials meet international standards for chemical composition and mechanical properties. Buyers should inquire about the supplier’s material certification processes to verify that materials are sourced from reputable vendors.
Forming Processes
Once the materials are prepared, they undergo various forming processes. These may include:
- Casting: Metal is poured into molds to create complex shapes.
- Forging: Metal is shaped by applying compressive forces, enhancing its strength.
- Machining: Precision cutting and shaping of components to meet exact specifications.
These techniques are crucial as they affect the overall performance and longevity of the rock crusher. B2B buyers should ask suppliers about the forming techniques used and the associated tolerances to ensure they meet their operational needs.
Assembly Techniques
The assembly of rock crushers requires skilled labor and precision. Key components such as jaws, shafts, and bearings must be assembled with care to ensure proper alignment and functionality. Assembly techniques may include:
- Welding: For joining metal parts, ensuring structural integrity.
- Bolting: Allowing for easy disassembly and maintenance.
- Alignment Checks: Ensuring that all components are correctly positioned to prevent operational issues.
B2B buyers should request detailed assembly documentation from suppliers, including assembly diagrams and procedures, to understand how the crushers are put together.
Finishing Processes
Finishing processes are crucial to enhance the durability and aesthetic appeal of rock crushers. Common finishing techniques include:
- Surface Treatment: Processes like powder coating or galvanization to resist corrosion.
- Heat Treatment: Strengthening components through controlled heating and cooling.
- Quality Polishing: Improving surface quality to minimize wear and tear.
Buyers should evaluate the finishing processes used by suppliers, as they directly affect the rock crusher’s lifespan and maintenance needs.
How Is Quality Assurance Implemented in Rock Crusher Manufacturing?
Quality assurance (QA) is essential in the manufacturing of rock crushers to ensure that every unit meets performance standards. Key components of QA include:
What Are the Relevant International Standards for Quality Assurance?
International standards, such as ISO 9001, guide manufacturers in establishing effective quality management systems. Additionally, industry-specific standards like CE marking (for compliance in Europe) and API specifications (for equipment used in petroleum and natural gas industries) are vital for ensuring product safety and reliability.
B2B buyers should verify that suppliers hold relevant certifications. Requesting copies of these certifications can help assess the supplier’s commitment to quality.
What Are the Key Quality Control Checkpoints?
The quality control process typically consists of several checkpoints, including:
- Incoming Quality Control (IQC): Inspecting raw materials upon arrival to ensure they meet specifications.
- In-Process Quality Control (IPQC): Monitoring quality during the manufacturing process to catch defects early.
- Final Quality Control (FQC): Conducting comprehensive tests on the finished product before shipping.
B2B buyers should ask suppliers about their quality control procedures and the frequency of inspections at each checkpoint.
What Testing Methods Are Commonly Used for Rock Crushers?
Quality control in rock crusher manufacturing often involves rigorous testing to ensure performance under operational conditions. Common testing methods include:
- Dimensional Testing: Verifying that components meet specified measurements.
- Non-Destructive Testing (NDT): Techniques such as ultrasonic testing or X-ray to detect internal flaws without damaging the product.
- Performance Testing: Simulating operational conditions to assess crushing efficiency and durability.
Buyers should inquire about the specific testing methods employed by suppliers and request test reports to confirm compliance with performance standards.
How Can B2B Buyers Verify Supplier Quality Control?
Verifying a supplier’s quality control practices is crucial for B2B buyers, especially when sourcing rock crushers internationally. Here are actionable steps:
- Conduct Supplier Audits: Regular audits can help assess the supplier’s adherence to quality standards. Buyers may choose to perform these audits themselves or hire third-party firms.
- Request Quality Reports: Suppliers should provide documentation of their quality control processes, including test results and inspection reports.
- Engage Third-Party Inspection Services: Utilizing independent inspectors can provide an unbiased assessment of the supplier’s quality control practices.
What Are the Nuances of Quality Control for International B2B Buyers?
When sourcing rock crushers from international suppliers, particularly from regions like Africa, South America, the Middle East, and Europe, buyers must navigate several nuances:
- Regulatory Compliance: Ensure that the supplier complies with local regulations and international standards relevant to the buyer’s market.
- Cultural Considerations: Understanding cultural differences can impact communication and quality expectations. Buyers should establish clear quality criteria and communicate them effectively.
- Supply Chain Transparency: Buyers should seek suppliers who are transparent about their sourcing and manufacturing processes, as this can affect product quality.
By focusing on these aspects, B2B buyers can enhance their procurement strategies, ensuring they select reliable suppliers that meet their quality expectations for rock crushers.
Practical Sourcing Guide: A Step-by-Step Checklist for ‘rock crusher’
The following guide serves as a practical checklist for international B2B buyers seeking to procure a rock crusher. This step-by-step approach will help ensure that you make informed decisions, leading to a successful acquisition that meets your operational needs.
Step 1: Define Your Technical Specifications
Establishing clear technical specifications is crucial for identifying the right rock crusher for your operations. Consider factors such as capacity, material type, and desired output size. Additionally, think about the specific environment in which the machine will operate, as this will influence durability and maintenance requirements.
- Capacity Requirements: Determine the volume of material you need to process to select a model that meets your production goals.
- Material Compatibility: Ensure that the crusher is suitable for the types of rocks or minerals you will be handling.
Step 2: Research Market Trends and Innovations
Understanding the latest market trends and technological advancements in rock crushers can provide a competitive edge. Stay informed about innovations that improve efficiency and reduce operational costs.
- Energy Efficiency: Look for models that offer lower energy consumption without sacrificing performance.
- Automation Features: Consider crushers with automated features that can enhance safety and streamline operations.
Step 3: Evaluate Potential Suppliers
Before committing to a supplier, it’s essential to vet them thoroughly. Request company profiles, case studies, and references from previous buyers in similar industries or regions. This due diligence helps confirm the supplier’s credibility and reliability.
- Industry Experience: Choose suppliers with a proven track record in providing rock crushers within your specific market.
- Customer Reviews: Look for testimonials or reviews that highlight the supplier’s customer service and post-sale support.
Step 4: Verify Compliance and Certifications
Ensure that the rock crusher complies with relevant industry standards and regulations in your region. This step is vital for legal compliance and operational safety.
- ISO Certifications: Check for ISO or other relevant certifications that demonstrate quality management practices.
- Local Regulations: Be aware of any local regulations regarding emissions and noise levels that the equipment must meet.
Step 5: Request Detailed Quotations
Once you have shortlisted potential suppliers, request detailed quotations. This should include not only the price of the rock crusher but also additional costs such as shipping, installation, and maintenance.
- Breakdown of Costs: Ensure that the quotation clearly outlines all costs involved to avoid hidden fees later.
- Warranty and Service Terms: Look for clarity on warranty periods and the availability of service or support after the sale.
Step 6: Assess After-Sales Support and Training
After-sales support is a critical aspect of the procurement process. Evaluate what training and maintenance support the supplier offers to ensure smooth operation post-purchase.
- Training Programs: Ask about training programs for your staff to maximize the rock crusher’s efficiency.
- Availability of Spare Parts: Confirm that the supplier can provide spare parts easily and quickly to minimize downtime.
Step 7: Finalize the Purchase Agreement
Before finalizing your purchase, ensure that all terms are clearly outlined in a written agreement. This should include payment terms, delivery schedules, and penalties for non-compliance.
- Clear Terms: Make sure both parties agree on delivery dates, payment schedules, and conditions for returns or replacements.
- Legal Considerations: Consult with legal experts to ensure the contract is fair and protects your interests.
By following this checklist, international B2B buyers can streamline their procurement process for rock crushers, ensuring a successful investment that meets their operational needs.
Comprehensive Cost and Pricing Analysis for rock crusher Sourcing
What Are the Key Cost Components in Rock Crusher Manufacturing?
When sourcing rock crushers, understanding the cost structure is crucial for effective budgeting and procurement. The primary cost components include:
-
Materials: The choice of raw materials significantly influences the overall cost. High-quality steel and specialized alloys used in manufacturing rock crushers can raise the price but enhance durability and performance.
-
Labor: Skilled labor is essential for the assembly and quality control of rock crushers. The cost of labor varies by region, with countries in Europe generally facing higher labor costs compared to regions in Africa or South America.
-
Manufacturing Overhead: This includes costs associated with the production facility, utilities, and indirect labor. Efficient manufacturing processes can help minimize these costs.
-
Tooling: Custom tooling may be required for specific designs, impacting the initial investment. Buyers should consider whether standard tooling can suffice for their needs.
-
Quality Control (QC): Rigorous QC procedures ensure the reliability of the crushers. The cost of implementing these processes is a necessary investment to reduce the risk of defects.
-
Logistics: Shipping costs, including freight and insurance, can add significant expenses, especially for international buyers. Understanding local tariffs and import duties is essential.
-
Margin: Suppliers will include their profit margins in the final pricing. The margin can vary widely based on the supplier’s market positioning and the perceived value of the product.
How Do Price Influencers Impact Rock Crusher Sourcing?
Several factors can influence the pricing of rock crushers:
-
Volume and Minimum Order Quantity (MOQ): Higher purchase volumes can lead to lower per-unit costs. Buyers should negotiate MOQs to leverage bulk pricing.
-
Specifications and Customization: Custom specifications can significantly increase costs. Buyers should carefully assess whether custom features are necessary for their operations.
-
Materials and Quality Certifications: Crushers made from higher-grade materials or those with specific certifications (e.g., ISO) will typically cost more. However, these investments can lead to lower maintenance costs over time.
-
Supplier Factors: Supplier reputation, experience, and reliability can impact pricing. Established suppliers may charge a premium but offer better service and warranty options.
-
Incoterms: The choice of Incoterms (International Commercial Terms) affects the total landed cost of the equipment. Buyers should fully understand their responsibilities under different Incoterms to avoid unexpected expenses.
What Buyer Tips Can Help Optimize Rock Crusher Costs?
International B2B buyers should consider several strategies to optimize their rock crusher sourcing:
-
Effective Negotiation: Approach negotiations with a clear understanding of your needs and market prices. Building a relationship with suppliers can also lead to better deals and terms.
-
Focus on Cost-Efficiency: Evaluate the total cost of ownership (TCO), which includes purchase price, maintenance, and operational costs. A cheaper initial price may not always result in lower TCO.
-
Understand Pricing Nuances: Different regions may have varying pricing structures due to local economic conditions, labor costs, and material availability. Conduct thorough market research to understand these nuances.
-
Seek Multiple Quotations: Always request quotes from multiple suppliers to compare prices and terms. This practice can reveal discrepancies and provide leverage in negotiations.
Disclaimer on Indicative Prices
Prices for rock crushers can fluctuate based on market conditions, supplier pricing strategies, and geopolitical factors. Buyers should treat any indicative pricing as a starting point for negotiations and conduct their research to ensure they obtain the best value for their investment.
Alternatives Analysis: Comparing rock crusher With Other Solutions
Introduction to Alternative Solutions for Rock Crushing
When considering rock crushing solutions, it’s essential for international B2B buyers to evaluate not just the rock crusher itself but also viable alternatives that may better suit their operational needs. Different technologies and methods can provide various benefits, depending on factors such as performance requirements, cost considerations, and operational contexts. This analysis will compare rock crushers with two alternative solutions: impact crushers and jaw crushers, providing actionable insights tailored for buyers from Africa, South America, the Middle East, and Europe.
Comparison Table of Rock Crusher and Alternative Solutions
Comparison Aspect | Rock Crusher | Impact Crusher | Jaw Crusher |
---|---|---|---|
Performance | High throughput; efficient for hard materials | Moderate throughput; effective for softer materials | High crushing ratio; versatile for different materials |
Cost | Moderate initial investment; higher operational costs | Lower initial cost; moderate operational costs | Higher initial investment; lower operational costs over time |
Ease of Implementation | Requires specialized setup and training | Easier to implement; less specialized training needed | Requires significant setup; moderate training needed |
Maintenance | High maintenance needs; requires skilled technicians | Moderate maintenance; less frequent servicing | Low maintenance; straightforward repairs |
Best Use Case | Large scale mining and aggregates production | Recycling and soft material processing | Versatile applications; construction and mining |
What Are the Pros and Cons of Using an Impact Crusher?
Impact crushers are designed to break down materials using high-speed impacts. Their primary advantage is cost-effectiveness, as they typically have lower initial purchase costs compared to rock crushers. They are also easier to implement, making them a suitable choice for businesses with limited technical expertise. However, impact crushers may not perform as efficiently on harder materials, which can lead to higher operational costs if used outside their optimal range.
Why Choose a Jaw Crusher Over a Rock Crusher?
Jaw crushers are renowned for their versatility and high crushing ratios, making them suitable for a wide range of applications, including construction and mining. They tend to have lower operational costs due to their simple design, which translates into easier maintenance and repairs. However, the initial investment for jaw crushers is generally higher than that of rock crushers, and they require more significant setup efforts. Buyers should weigh the long-term benefits against the initial costs when considering this alternative.
Conclusion: How to Choose the Right Solution for Your Needs
Selecting the right rock crushing solution depends on various factors specific to your operations, including material types, project scale, and budget constraints. While rock crushers excel in high-throughput environments, alternatives like impact and jaw crushers offer unique advantages that may align better with certain operational needs. Buyers should conduct a thorough analysis of their specific requirements and consider both the short-term and long-term implications of their choice. By understanding these alternatives, B2B buyers can make informed decisions that enhance their operational efficiency and profitability.
Essential Technical Properties and Trade Terminology for rock crusher
What Are the Key Technical Properties of Rock Crushers?
Understanding the essential technical properties of rock crushers is critical for B2B buyers, particularly those looking to invest in heavy machinery for mining, construction, or recycling purposes. Here are some of the most important specifications to consider:
-
Material Grade
The material grade of a rock crusher determines its durability and performance. Common materials include high-strength steel and alloyed materials that can withstand heavy impacts and abrasive conditions. Selecting a crusher with the appropriate material grade ensures longevity and minimizes downtime, which is crucial for maintaining productivity in operations. -
Crushing Capacity
Measured in tons per hour (TPH), the crushing capacity indicates how much material the rock crusher can process in a given time frame. For international buyers, understanding this metric is essential for ensuring that the machine meets operational demands. A higher capacity often translates to better efficiency and reduced operational costs. -
Size Reduction Ratio
This property refers to the ratio of the size of the raw material to the size of the crushed output. A rock crusher with a higher size reduction ratio can produce finer materials, which is often required in applications like asphalt or concrete production. This specification is vital for buyers who need to meet specific product standards or specifications. -
Power Consumption
The power consumption of a rock crusher, usually measured in kilowatts, affects operational costs. Understanding the energy efficiency of a machine helps buyers calculate long-term expenses and ensure that they are making a cost-effective investment. Energy-efficient models can lead to significant savings, particularly in regions where electricity costs are high. -
Tolerance and Precision
Tolerance levels indicate how much deviation from a specified dimension is acceptable in the manufacturing process. For rock crushers, tighter tolerances often result in better performance and reduced wear and tear. Buyers should consider the tolerance levels when evaluating suppliers, as this can affect the operational reliability of the equipment.
Which Trade Terminology Should International B2B Buyers Understand?
Familiarity with trade terminology is essential for effective communication and negotiation in the procurement of rock crushers. Here are some key terms that buyers should know:
-
OEM (Original Equipment Manufacturer)
This term refers to companies that produce components or equipment that may be marketed by another manufacturer. Understanding OEM relationships can help buyers identify reliable suppliers and ensure that the parts they purchase are of high quality and compatible with their existing systems. -
MOQ (Minimum Order Quantity)
MOQ is the smallest number of units that a supplier is willing to sell. For international buyers, being aware of MOQs can help in budgeting and inventory management. It’s crucial to negotiate MOQs that align with operational needs while avoiding excess stock. -
RFQ (Request for Quotation)
An RFQ is a document that solicits price quotes from suppliers. Including detailed specifications in your RFQ can lead to more accurate responses and better pricing. This is particularly important for buyers in diverse markets like Africa and South America, where price competitiveness varies. -
Incoterms (International Commercial Terms)
Incoterms define the responsibilities of buyers and sellers in international transactions, including shipping costs, risk transfer, and delivery points. Understanding these terms is critical for international B2B buyers to ensure clarity in contracts and avoid unexpected costs. -
Lead Time
Lead time is the amount of time from placing an order to delivery. Buyers should consider lead times in their project planning to avoid delays. Shorter lead times can enhance project efficiency, making it essential to discuss this with suppliers during negotiations.
By grasping these technical properties and trade terminologies, international B2B buyers can make informed decisions, ensuring they select the right rock crusher for their specific needs while navigating the complexities of global procurement.
Navigating Market Dynamics and Sourcing Trends in the rock crusher Sector
What Are the Current Market Dynamics and Key Trends in the Rock Crusher Sector?
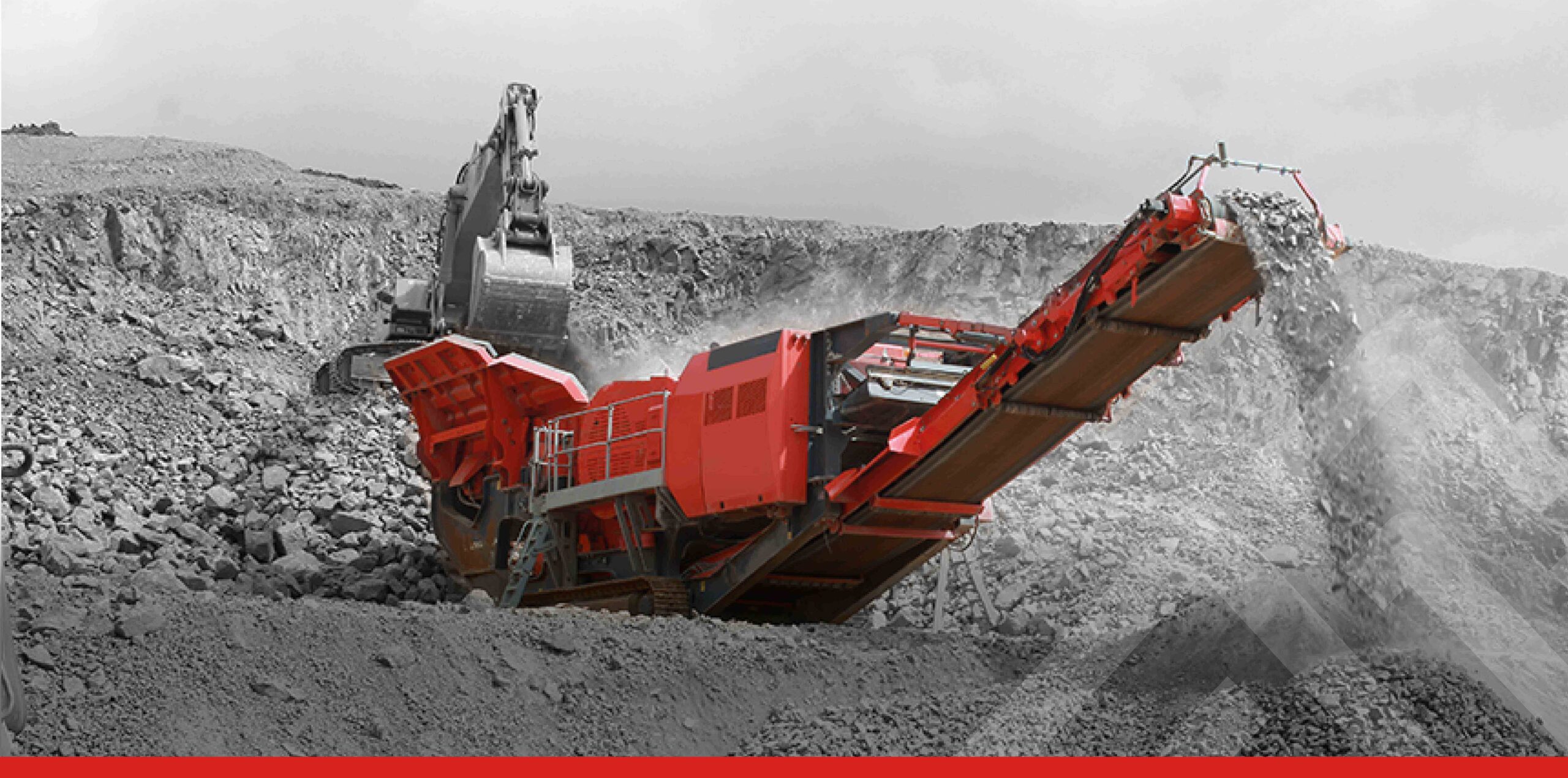
A stock image related to rock crusher.
The global rock crusher market is experiencing significant growth, driven by the surge in construction and mining activities across Africa, South America, the Middle East, and Europe. The increasing demand for crushed stone aggregates, essential for infrastructure projects, is a primary driver. In particular, emerging economies are investing heavily in urban development, creating a robust demand for efficient and durable rock crushing equipment.
Technological advancements are also reshaping the market landscape. The integration of automation and IoT technology allows for real-time monitoring and predictive maintenance, enhancing operational efficiency. For international B2B buyers, particularly in regions such as the UK and Spain, this presents an opportunity to source advanced machinery that not only meets production needs but also reduces downtime and maintenance costs.
Sourcing trends are evolving with a focus on supplier reliability and product quality. Buyers are increasingly favoring manufacturers that offer comprehensive service packages, including after-sales support and training. Additionally, the trend towards modular and mobile rock crushers is gaining traction, allowing companies to adapt quickly to varying project requirements without significant capital investment.
How Is Sustainability Impacting the Rock Crusher Sector?
Sustainability has become a critical factor in the rock crusher sector, prompting buyers to consider the environmental impact of their sourcing decisions. The extraction and processing of raw materials can lead to significant ecological degradation, making it essential for companies to adopt more sustainable practices. This includes sourcing from suppliers committed to reducing carbon footprints and implementing responsible mining practices.
Ethical supply chains are also gaining importance, with B2B buyers increasingly demanding transparency from manufacturers. Certifications like ISO 14001 (Environmental Management) and other ‘green’ credentials are becoming vital indicators of a supplier’s commitment to sustainability. Buyers are encouraged to engage with manufacturers who prioritize the use of recycled materials and environmentally friendly technologies in their rock crushing processes.
Investing in ‘green’ rock crushers not only aligns with corporate social responsibility goals but can also enhance brand reputation and meet regulatory requirements in various regions. For companies in Africa and South America, where environmental regulations are tightening, this shift toward sustainability is not just a trend but a necessity.
What Is the Historical Context of the Rock Crusher Industry?
The rock crusher industry has evolved significantly over the past century. Initially, the equipment was rudimentary, relying heavily on manual processes and basic mechanical systems. The introduction of electric power in the early 20th century marked a pivotal change, allowing for more efficient and powerful crushing operations.
Over the decades, innovations such as hydraulic systems and advanced materials have transformed rock crushers into high-performance machines capable of handling various materials with precision. This evolution has been crucial for international B2B buyers, as the availability of diverse rock crushing technologies has enabled companies to select equipment tailored to specific operational needs.
As the industry continues to advance, understanding this historical context is essential for buyers looking to navigate the complexities of sourcing in a competitive market. By recognizing past trends and technological developments, B2B buyers can make informed decisions that align with current market demands and future growth opportunities.
Frequently Asked Questions (FAQs) for B2B Buyers of rock crusher
-
How do I choose the right rock crusher for my business needs?
Selecting the right rock crusher involves understanding your specific requirements, such as material type, desired output size, and production capacity. Assess the hardness and abrasiveness of the materials you’ll be processing. Consider whether you need a portable or stationary unit, as well as any additional features like advanced automation or dust suppression systems. Engaging with suppliers for a demonstration or trial can also help determine the best fit for your operations. -
What factors should I consider when sourcing a rock crusher supplier?
When sourcing a rock crusher supplier, evaluate their industry experience, reputation, and product quality. Look for suppliers with positive customer reviews and case studies demonstrating successful implementations. Verify their compliance with international standards and certifications, especially if you’re importing to regions with strict regulations. It’s beneficial to establish communication channels for ongoing support and maintenance, ensuring you have a partner for the long term. -
What are the typical payment terms for international rock crusher purchases?
Payment terms for international purchases can vary significantly based on the supplier and the transaction size. Common terms include a deposit (typically 30-50%) upfront, with the balance due prior to shipment or upon delivery. Always confirm the acceptable payment methods, such as wire transfers, letters of credit, or escrow services. It’s advisable to negotiate terms that protect both parties, especially when dealing with large sums or new suppliers. -
What is the minimum order quantity (MOQ) for rock crushers?
Minimum order quantities for rock crushers can vary widely depending on the manufacturer and the specific model. Some suppliers may offer single units, while others might require bulk orders to optimize production costs. Before placing an order, inquire about flexible options, especially if you’re a smaller business or a startup. Suppliers may also provide leasing or rental options, which can be a cost-effective alternative to large purchases. -
How can I ensure quality assurance (QA) when buying a rock crusher?
To ensure quality assurance, request detailed product specifications and certifications from the supplier. Establish a clear inspection process before shipment, which may include third-party quality checks or factory audits. Some suppliers may offer warranties or guarantees on their equipment, which can serve as an additional assurance of quality. Consider engaging in a pilot project to evaluate performance before committing to a larger order. -
What logistics considerations should I keep in mind when importing a rock crusher?
Logistics is crucial when importing a rock crusher. Understand the shipping options available, including freight forwarding, customs clearance, and delivery timelines. Assess the total landed cost, which includes shipping, insurance, and import duties. Collaborating with a logistics expert familiar with the regulations of your country can streamline the process and prevent unexpected delays or costs.
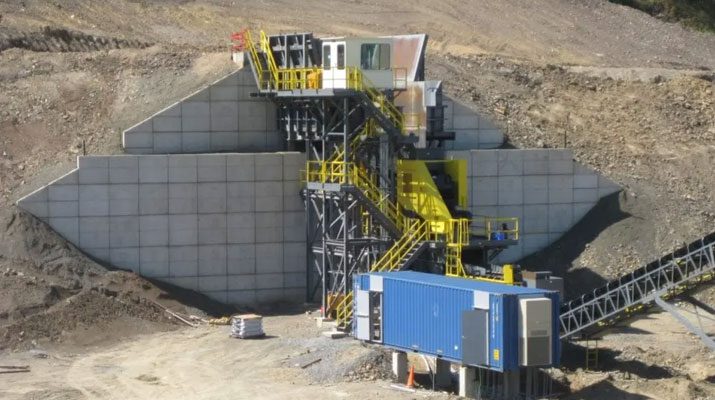
A stock image related to rock crusher.
-
Can I customize the specifications of my rock crusher?
Yes, many suppliers offer customization options for rock crushers to meet specific operational needs. Customizations may include adjustments to crushing capacity, size of discharge openings, or integration with existing machinery. Discuss your requirements with the supplier early in the negotiation process to ensure they can accommodate your needs and provide a solution that enhances your productivity. -
What are the common maintenance requirements for rock crushers?
Regular maintenance is essential for the longevity and efficiency of rock crushers. Common maintenance tasks include checking and replacing wear parts, lubricating moving components, and inspecting for structural integrity. Establish a maintenance schedule based on the manufacturer’s recommendations and the operational environment. Training your staff on routine checks can help prevent costly downtime and ensure optimal performance throughout the equipment’s lifespan.
Important Disclaimer & Terms of Use
⚠️ Important Disclaimer
The information provided in this guide, including content regarding manufacturers, technical specifications, and market analysis, is for informational and educational purposes only. It does not constitute professional procurement advice, financial advice, or legal advice.
While we have made every effort to ensure the accuracy and timeliness of the information, we are not responsible for any errors, omissions, or outdated information. Market conditions, company details, and technical standards are subject to change.
B2B buyers must conduct their own independent and thorough due diligence before making any purchasing decisions. This includes contacting suppliers directly, verifying certifications, requesting samples, and seeking professional consultation. The risk of relying on any information in this guide is borne solely by the reader.
Strategic Sourcing Conclusion and Outlook for rock crusher
What Are the Key Takeaways for B2B Buyers in the Rock Crusher Market?
In summary, the strategic sourcing of rock crushers requires a thorough understanding of market dynamics, supplier capabilities, and technological advancements. For international B2B buyers, especially in Africa, South America, the Middle East, and Europe, prioritizing quality and reliability over initial cost can lead to significant long-term savings. Engaging with multiple suppliers and leveraging competitive bidding can optimize procurement processes, ensuring access to the best equipment tailored to specific operational needs.
How Can Strategic Sourcing Enhance Your Business Operations?
The value of strategic sourcing in the rock crusher market cannot be overstated. By implementing a well-defined sourcing strategy, businesses can not only enhance their operational efficiency but also foster sustainable supplier relationships that contribute to innovation and competitive advantage. Buyers should regularly assess their sourcing strategies to adapt to changing market conditions and technological advancements.
What Should B2B Buyers Do Next in the Rock Crusher Market?
As we look to the future, it is crucial for international B2B buyers to stay informed about emerging technologies and trends within the rock crushing industry. Engage with industry experts, attend trade shows, and participate in webinars to gather insights that can influence purchasing decisions. Take proactive steps today to refine your sourcing strategies, ensuring your business remains at the forefront of the rock crusher market, ready to seize new opportunities as they arise.