Unlock Efficiency: The Ultimate Sliding Gate Guide (2025)
Introduction: Navigating the Global Market for sliding gate
As businesses expand their operations and look for effective security solutions, the demand for sliding gates has surged globally. However, sourcing the right sliding gate that meets specific needs while ensuring quality and cost-effectiveness can be a daunting challenge for international B2B buyers. This comprehensive guide is designed to empower you with actionable insights into the various types of sliding gates, their applications, and the critical factors to consider when making purchasing decisions.
From understanding the differences between manual and automated sliding gates to evaluating their suitability for industrial, commercial, and residential environments, this guide covers it all. We delve into the nuances of supplier vetting, ensuring you can identify reliable manufacturers or distributors who align with your business standards. Additionally, we explore the cost implications, helping you navigate budget considerations and potential return on investment.
For B2B buyers in regions like Africa, South America, the Middle East, and Europe—including key markets such as Poland and Egypt—this guide serves as a vital resource. It equips you with the knowledge to make informed decisions that enhance your operational efficiency and security. By understanding the global landscape of sliding gates, you can confidently select solutions that not only meet your immediate needs but also align with your long-term business objectives.
Understanding sliding gate Types and Variations
Type Name | Key Distinguishing Features | Primary B2B Applications | Brief Pros & Cons for Buyers |
---|---|---|---|
Cantilever Sliding Gate | No ground track; supported by rollers; ideal for uneven terrain | Industrial facilities, warehouses | Pros: Space-efficient, minimal maintenance; Cons: Higher initial cost, requires robust installation. |
Track Sliding Gate | Operates on a fixed track; offers smooth operation | Commercial properties, residential complexes | Pros: Cost-effective, reliable operation; Cons: Track maintenance needed, can be obstructed by debris. |
Bi-parting Sliding Gate | Splits in the middle to open; allows for wider access | Airports, large retail spaces | Pros: Fast opening, great for high-traffic areas; Cons: More complex installation, requires more space. |
Vertical Lift Gate | Moves vertically; ideal for limited horizontal space | Ports, logistics hubs | Pros: Saves space, secure; Cons: Higher energy consumption, complex mechanics. |
Motorized Sliding Gate | Automated operation; can integrate with access control systems | Corporate offices, gated communities | Pros: Enhanced security, convenience; Cons: Dependence on power supply, higher upfront costs. |
What Are the Key Features of Cantilever Sliding Gates?
Cantilever sliding gates are designed without a ground track, instead relying on rollers that support the gate from above. This unique feature makes them particularly suitable for uneven or sloped terrains, which is often a consideration for B2B buyers in regions like Africa and the Middle East where land conditions can vary greatly. When purchasing, consider the initial investment, as the installation can be more complex and costly compared to traditional gates. However, their low maintenance needs and space-saving design can justify the upfront costs, especially in industrial applications.
How Do Track Sliding Gates Operate and Where Are They Used?
Track sliding gates operate on a fixed track and are known for their smooth and reliable operation. They are often used in commercial properties and residential complexes where space allows for track installation. B2B buyers should note that while track sliding gates tend to be more cost-effective, they require regular maintenance to prevent debris from obstructing the track. Their straightforward design makes them a popular choice among businesses looking for a balance between cost and functionality.
What Advantages Do Bi-parting Sliding Gates Offer for High-Traffic Areas?
Bi-parting sliding gates are designed to open in the middle, allowing for wider access compared to standard sliding gates. This feature is particularly advantageous in high-traffic areas such as airports and large retail spaces, where quick access is essential. B2B buyers should consider the installation complexity and the space required for the gate to operate effectively. Although they may incur higher installation costs, their ability to facilitate rapid entry and exit can significantly enhance operational efficiency.
Why Choose Vertical Lift Gates for Limited Space Applications?
Vertical lift gates are engineered to move vertically, making them ideal for environments with limited horizontal space, such as ports and logistics hubs. These gates offer excellent security while maximizing available area. However, B2B buyers must be aware of the higher energy consumption associated with their operation and the complexity of their mechanics. When considering a vertical lift gate, assess the energy costs and the potential need for specialized maintenance to ensure long-term functionality.
How Do Motorized Sliding Gates Enhance Security and Convenience?
Motorized sliding gates are equipped with automated systems that can integrate seamlessly with existing access control solutions. This feature is especially beneficial for corporate offices and gated communities, where enhanced security and convenience are priorities. While the upfront costs can be higher, the benefits of increased security and ease of use often outweigh the initial investment. B2B buyers should also consider the reliability of the power supply, as dependence on electricity can pose risks in areas with unstable power sources.
Related Video: Turning Sectional Sliding Gate
Key Industrial Applications of sliding gate
Industry/Sector | Specific Application of Sliding Gate | Value/Benefit for the Business | Key Sourcing Considerations for this Application |
---|---|---|---|
Manufacturing | Access control for factories | Enhances security and controls access to sensitive areas | Durability, automation options, and maintenance support |
Logistics and Warehousing | Loading dock access and vehicle entry | Streamlines operations and improves safety during loading/unloading | Size specifications, weight capacity, and remote control features |
Agriculture | Livestock management and field access | Facilitates movement of livestock while preventing escapes | Weather resistance, ease of operation, and material choice |
Mining | Site perimeter security | Protects valuable resources and ensures safety on-site | Customization options, compliance with safety regulations, and installation support |
Construction | Site access for heavy machinery | Improves logistical efficiency and site security | Size, weight capacity, and compatibility with existing infrastructure |
How is Sliding Gate Used in the Manufacturing Industry?
In the manufacturing sector, sliding gates are primarily utilized for access control to factories and production areas. These gates provide a secure entry point, helping to manage who enters and exits sensitive zones. By enhancing security, sliding gates reduce the risk of theft and unauthorized access, which is crucial for protecting proprietary processes and materials. International buyers should prioritize durability and automation options, as well as maintenance support, to ensure long-term functionality in high-traffic environments.
What Role Does Sliding Gate Play in Logistics and Warehousing?
In logistics and warehousing, sliding gates are essential for managing vehicle entry and exit at loading docks. They streamline operations by allowing for efficient movement of goods while enhancing safety during loading and unloading processes. A well-designed sliding gate can minimize wait times and improve workflow. Buyers in this sector need to consider size specifications, weight capacity, and remote control features to ensure that the gates meet the operational demands of their facilities.
How is Sliding Gate Beneficial in Agriculture?
Sliding gates serve a critical role in agriculture, particularly in livestock management and field access. They allow for the controlled movement of livestock, preventing escapes while ensuring that animals can be easily moved as needed. This application is vital for maintaining farm efficiency and animal welfare. Buyers should focus on weather resistance, ease of operation, and material choice to ensure the gates withstand the elements and are user-friendly for farm workers.
Why is Sliding Gate Important for Mining Operations?
In the mining industry, sliding gates are vital for securing site perimeters and protecting valuable resources. They prevent unauthorized access to hazardous areas and help maintain safety standards for workers. Effective perimeter security is essential for compliance with regulations and for safeguarding equipment and materials. Buyers should seek customization options, ensure compliance with safety regulations, and consider installation support to facilitate a smooth setup.
How Do Sliding Gates Improve Construction Site Access?
Sliding gates are increasingly used in construction sites to manage access for heavy machinery and personnel. They enhance logistical efficiency by controlling entry and exit points, thereby improving overall site security. Proper access management is crucial for preventing theft and ensuring safety. When sourcing sliding gates for construction, buyers should evaluate size, weight capacity, and compatibility with existing infrastructure to ensure seamless integration into the site layout.
Related Video: Hi-Motions: Cantilever sliding gate system
3 Common User Pain Points for ‘sliding gate’ & Their Solutions
Scenario 1: Difficulty in Sourcing Quality Sliding Gates in Emerging Markets
The Problem:
B2B buyers in regions like Africa and South America often struggle to find reliable suppliers for sliding gates that meet international quality standards. The lack of established manufacturers and limited access to advanced materials can lead to concerns about durability and safety. Buyers may also face language barriers and cultural differences that complicate negotiations and trust-building with potential suppliers. This situation can result in delays, increased costs, and ultimately, dissatisfaction with the purchased gates.
The Solution:
To effectively source high-quality sliding gates, buyers should consider engaging with established manufacturers from regions with a strong reputation for metal fabrication, such as Europe. Utilizing platforms like Alibaba or Global Sources can help identify suppliers with verified credentials and positive reviews. It’s essential to conduct thorough due diligence by requesting samples and visiting the manufacturing facilities if possible.
Moreover, working with a local consultant or intermediary who understands the regional market can bridge communication gaps and facilitate smoother negotiations. Establishing clear specifications and quality standards upfront will also help ensure that the final product meets the buyer’s expectations. This proactive approach minimizes risks and fosters long-term supplier relationships.
Scenario 2: Installation Challenges Leading to Operational Issues
The Problem:
Many B2B buyers encounter significant installation challenges when integrating sliding gates into existing infrastructure. This is particularly prevalent in older facilities where space constraints and uneven ground can complicate the installation process. Poor installation not only affects the functionality of the gate but can also pose safety risks, leading to potential liability issues for businesses.
The Solution:
To overcome installation challenges, buyers should prioritize collaboration with experienced installation teams who specialize in sliding gates. Before installation, conducting a comprehensive site assessment is crucial. This assessment should evaluate the ground conditions, available space, and existing infrastructure to determine the best approach for installation.
Investing in professional installation services, even if they come at a higher initial cost, can save money in the long run by preventing future operational issues. Buyers should also ensure that the installation team is well-versed in the specific sliding gate model being used, as different models may have unique requirements. Providing detailed installation manuals and maintenance guidelines can further support the installation process and ensure optimal performance.
Scenario 3: Maintenance and Longevity Concerns for Sliding Gates
The Problem:
B2B buyers often express concerns regarding the maintenance and longevity of sliding gates, particularly in regions with extreme weather conditions, such as the Middle East and Europe. Factors like corrosion, wear and tear, and mechanical failures can significantly shorten the lifespan of sliding gates, leading to frequent repairs and replacements. This not only increases operational costs but can also disrupt business activities.
The Solution:
To enhance the longevity of sliding gates, buyers should invest in high-quality materials that are specifically designed to withstand local environmental conditions. For instance, selecting gates made from stainless steel or coated with anti-corrosive finishes can significantly reduce the risk of deterioration in harsh climates.
Establishing a regular maintenance schedule is equally important. Buyers should develop a checklist that includes inspections of mechanical components, lubrication of moving parts, and cleaning of tracks to prevent debris buildup. Training in-house maintenance staff on best practices can also empower businesses to address minor issues before they escalate into major problems. Collaborating with suppliers to receive ongoing support and advice on maintenance can further ensure that the sliding gates remain functional and safe throughout their operational lifespan.
Strategic Material Selection Guide for sliding gate
When selecting materials for sliding gates, international B2B buyers must consider various factors that affect performance, durability, and compliance with regional standards. Here, we analyze four common materials used in sliding gate construction: steel, aluminum, PVC, and composite materials. Each material has unique properties and implications for specific applications, particularly relevant to buyers from Africa, South America, the Middle East, and Europe.
What are the Key Properties of Steel for Sliding Gates?
Steel is a widely used material for sliding gates due to its high strength and durability. It typically offers excellent temperature and pressure ratings, making it suitable for heavy-duty applications. Steel’s resistance to deformation under load ensures long-lasting performance in various environments. However, it is susceptible to corrosion, especially in humid or coastal regions, necessitating protective coatings or treatments.
Pros & Cons of Steel
Pros:
– Exceptional strength and load-bearing capacity.
– High durability and resistance to impact.
– Suitable for custom designs and sizes.
Cons:
– Higher susceptibility to rust without proper treatment.
– Heavier than other materials, which may complicate installation.
– Generally higher manufacturing complexity due to welding and fabrication.
Impact on Application: Steel is ideal for high-security applications and environments with heavy traffic, but buyers must consider corrosion protection, especially in regions with high moisture levels.
How Does Aluminum Compare for Sliding Gates?
Aluminum is another popular choice for sliding gates, known for its lightweight and corrosion-resistant properties. It has a lower density than steel, making it easier to handle and install. Aluminum can withstand various environmental conditions, which is particularly advantageous in coastal areas.
Pros & Cons of Aluminum
Pros:
– Lightweight and easy to install.
– Naturally resistant to corrosion, reducing maintenance costs.
– Good aesthetic appeal with options for anodizing and painting.
Cons:
– Lower strength compared to steel, which may limit its use in high-load scenarios.
– More expensive than steel in some markets.
– Potential for dents and scratches in high-impact situations.
Impact on Application: Aluminum is suitable for residential and commercial applications where aesthetics and ease of installation are prioritized, but it may not be the best choice for heavy-duty industrial settings.
What Are the Benefits of Using PVC for Sliding Gates?
PVC is a synthetic plastic polymer that offers several advantages for sliding gates, particularly in terms of maintenance and cost. It is lightweight, resistant to corrosion, and does not require painting or staining, making it a low-maintenance option.
Pros & Cons of PVC
Pros:
– Excellent resistance to moisture and chemicals.
– Lightweight and easy to work with.
– Cost-effective for lower-budget projects.
Cons:
– Limited strength and durability compared to metals.
– Can become brittle in extreme temperatures.
– Not suitable for high-security applications.
Impact on Application: PVC is best suited for residential applications or temporary installations where low cost and ease of maintenance are essential. Buyers should be cautious about its performance in extreme weather conditions.
What Are the Advantages of Composite Materials for Sliding Gates?
Composite materials, which combine various substances, offer unique benefits for sliding gates. They can provide the aesthetic appeal of wood with the durability of synthetic materials. Composites are typically resistant to rot, insects, and weathering.
Pros & Cons of Composite Materials
Pros:
– High resistance to environmental factors, including moisture and UV rays.
– Aesthetic versatility that can mimic wood without the associated maintenance.
– Generally lighter than metal options.
Cons:
– Can be more expensive than traditional materials.
– Limited load-bearing capacity compared to steel.
– Manufacturing processes may vary, affecting consistency.
Impact on Application: Composite materials are ideal for decorative applications in residential settings but may not be suitable for heavy-duty industrial use.
Summary Table of Material Selection for Sliding Gates
Material | Typical Use Case for sliding gate | Key Advantage | Key Disadvantage/Limitation | Relative Cost (Low/Med/High) |
---|---|---|---|---|
Steel | High-security commercial gates | Exceptional strength and durability | Susceptible to corrosion | High |
Aluminum | Residential and light commercial | Lightweight and corrosion-resistant | Lower strength than steel | Medium |
PVC | Low-cost residential gates | Low maintenance and moisture resistant | Limited strength and durability | Low |
Composite | Decorative residential applications | Aesthetic appeal and weather resistance | Higher cost and variable quality | Medium |
In summary, the choice of material for sliding gates significantly impacts performance, cost, and suitability for specific applications. International B2B buyers should weigh these factors carefully, considering regional standards and environmental conditions to ensure optimal selection.
In-depth Look: Manufacturing Processes and Quality Assurance for sliding gate
What Are the Main Stages in the Manufacturing Process of Sliding Gates?
The manufacturing process for sliding gates consists of several critical stages that ensure both functionality and durability. Understanding these stages is vital for international B2B buyers, as it influences the quality and performance of the final product.
Material Preparation
The first step in the manufacturing process involves selecting high-quality materials. Common materials include steel, aluminum, and sometimes composite materials, depending on the gate’s intended use and location. For instance, buyers from humid regions like parts of South America and the Middle East might prefer corrosion-resistant materials, such as galvanized steel or aluminum.
After material selection, the preparation phase includes cutting the raw materials to specific dimensions using precision tools. This ensures that all components fit together correctly during assembly. Additionally, any necessary surface treatments, such as sandblasting or chemical cleaning, are performed to enhance adhesion for subsequent finishes.
What Techniques Are Used in Forming Sliding Gates?
Forming is a critical stage that shapes the materials into the desired gate structure. Common techniques include:
- Welding: For steel gates, welding is the primary method used to join components. This process can be MIG or TIG welding, depending on the required strength and finish.
- Extrusion: For aluminum gates, extrusion is often used to create specific shapes and profiles. This process allows for the efficient production of long sections without compromising structural integrity.
- Bending: This technique is employed to create curves and angles in the gate design, which can enhance aesthetics and functionality.
Each of these techniques requires skilled labor and precision machinery to ensure high-quality outputs.
How Is Assembly Conducted for Sliding Gates?
Once the components are formed, they are assembled into the final gate structure. This process typically includes:
- Joining Components: Using various methods such as welding, riveting, or bolting, the parts are securely fastened together. The choice of method often depends on the gate’s design and the materials used.
- Installation of Hardware: Rollers, tracks, and locking mechanisms are installed during assembly. These components are crucial for the gate’s functionality and security.
- Quality Checks: Throughout the assembly phase, quality control checks are conducted to ensure that all components meet design specifications.
What Finishing Processes Are Applied to Sliding Gates?
Finishing processes enhance the appearance and durability of sliding gates. Common techniques include:
- Powder Coating: This method provides a durable finish that is resistant to chipping, scratching, and fading. It’s particularly beneficial for gates exposed to harsh weather conditions.
- Painting: While not as durable as powder coating, painting can offer a wide range of color options. Buyers should consider the local climate when selecting paint types.
- Galvanization: For steel gates, hot-dip galvanization is often employed to prevent rust and corrosion, making it a preferred choice for buyers in humid climates.
These finishing processes not only improve aesthetics but also extend the lifespan of the sliding gates.
What International Standards Should Buyers Consider for Quality Assurance?
Quality assurance is paramount in the manufacturing process of sliding gates. International standards such as ISO 9001 ensure that manufacturers adhere to high-quality management practices. This standard focuses on continuous improvement and customer satisfaction, which is crucial for B2B buyers.
In addition to ISO standards, buyers should also be aware of industry-specific certifications such as:
- CE Marking: Required in Europe, this certification indicates that the product meets EU safety and environmental requirements.
- API Standards: Relevant for gates used in the oil and gas industry, these standards ensure that products meet specific performance and safety criteria.
What Quality Control Checkpoints Are Essential in the Manufacturing Process?
Quality control (QC) checkpoints play a vital role in maintaining product standards throughout the manufacturing process. Key QC checkpoints include:
- Incoming Quality Control (IQC): This step involves inspecting raw materials upon arrival to ensure they meet specified standards before they enter the production process.
- In-Process Quality Control (IPQC): Throughout the manufacturing stages, regular inspections are conducted to monitor the quality of work and materials. This helps to identify any issues early in the process.
- Final Quality Control (FQC): Once the sliding gate is fully assembled, a final inspection is performed to ensure it meets all specifications and quality standards before shipping.
How Can B2B Buyers Verify Supplier Quality Control?
For international B2B buyers, verifying a supplier’s quality control processes is crucial. Here are several actionable steps:
- Conduct Audits: Schedule regular audits of suppliers to assess their manufacturing processes and quality control measures. This can help identify potential issues before they affect your order.
- Request Quality Reports: Ask suppliers for detailed quality reports that outline their manufacturing processes, inspections, and compliance with international standards.
- Engage Third-Party Inspectors: Employ third-party inspection services to conduct independent quality assessments. This provides an unbiased evaluation of the supplier’s practices and product quality.
What Are the Nuances in Quality Control and Certification for International Buyers?
When sourcing sliding gates from international suppliers, particularly from regions like Africa, South America, and the Middle East, it is essential to understand the nuances of quality control and certification.
Buyers should be aware that not all suppliers may comply with the same international standards. Therefore, it is crucial to:
- Evaluate Local Standards: Understand the local regulations and standards that apply in the supplier’s country, as these may differ from international expectations.
- Consider Cultural Differences: Cultural approaches to quality control may vary, influencing how rigorously suppliers adhere to standards. Engage in open discussions to ensure alignment on quality expectations.
- Stay Updated on Compliance: Regularly check for updates on international standards and certifications to ensure that your suppliers remain compliant.
By comprehensively understanding these manufacturing processes and quality assurance measures, B2B buyers can make informed decisions when sourcing sliding gates, ensuring they receive high-quality products that meet their specific needs.
Practical Sourcing Guide: A Step-by-Step Checklist for ‘sliding gate’
In the competitive landscape of international B2B procurement, sourcing a sliding gate requires a strategic approach. This guide provides a practical checklist to help buyers from Africa, South America, the Middle East, and Europe navigate the complexities of sourcing sliding gates effectively. Follow these steps to ensure a successful procurement process.
Step 1: Define Your Technical Specifications
Before initiating the sourcing process, it’s essential to clearly define your technical specifications for the sliding gate. This includes dimensions, materials (e.g., steel, aluminum), weight capacity, and operational mechanisms (manual vs. automatic). Having detailed specifications helps streamline communication with suppliers and ensures that the products meet your operational needs.
- Consider environmental factors: Assess the local climate conditions, as this may influence the choice of materials.
- Identify security requirements: Determine if additional features such as access control systems or reinforced structures are necessary.
Step 2: Research Market Trends and Innovations
Understanding current market trends and technological innovations in sliding gates can provide a competitive edge. Research emerging features such as smart technology integrations (e.g., remote access, IoT capabilities) that can enhance functionality and security.
- Monitor industry publications: Subscribe to relevant trade journals and online forums for insights on new products and industry standards.
- Attend trade shows: Consider participating in industry exhibitions to see the latest offerings and network with potential suppliers.
Step 3: Evaluate Potential Suppliers
Before committing to a supplier, thorough vetting is crucial. Request company profiles, case studies, and references from buyers in similar industries or regions to gauge reliability and quality.
- Assess their experience: Look for suppliers with a proven track record in delivering sliding gates that meet your specifications.
- Verify certifications: Ensure that potential suppliers comply with international quality standards and regulations.
Step 4: Request and Compare Quotations
Once you’ve identified potential suppliers, request detailed quotations that break down costs, including materials, labor, shipping, and any additional fees. This step is vital for budgeting and ensures transparency.
- Compare pricing structures: Look beyond the initial cost—consider the total cost of ownership, including maintenance and warranty options.
- Check for hidden costs: Be vigilant about any additional charges that might arise during the procurement process.
Step 5: Conduct Site Visits or Virtual Inspections
If feasible, conduct site visits to the supplier’s manufacturing facility to assess their production capabilities and quality control processes. If a visit isn’t possible, arrange for a virtual inspection.
- Evaluate production standards: Look for adherence to quality assurance practices and machinery used in the manufacturing process.
- Inspect materials: Ensure that the materials used align with your specifications and quality expectations.
Step 6: Negotiate Terms and Conditions
Once you’ve selected a supplier, it’s time to negotiate the terms of the contract. This includes payment terms, delivery timelines, and warranty provisions. Clear agreements can prevent misunderstandings later.
- Clarify delivery schedules: Establish clear timelines for production and shipping to avoid delays.
- Discuss after-sales support: Ensure that the supplier offers adequate support for installation and maintenance.
Step 7: Finalize the Purchase and Monitor the Delivery
After negotiations, finalize the purchase and keep track of the delivery process. Establish communication with the supplier to monitor shipping updates and address any potential issues proactively.
- Prepare for installation: Coordinate with your team to ensure that the site is ready for the sliding gate installation upon arrival.
- Conduct a final inspection: Upon delivery, inspect the sliding gate thoroughly to ensure it meets all agreed specifications before acceptance.
By following this checklist, international B2B buyers can streamline the procurement process for sliding gates, ensuring they make informed decisions that align with their operational requirements and strategic goals.
Comprehensive Cost and Pricing Analysis for sliding gate Sourcing
What Are the Key Cost Components in Sliding Gate Sourcing?
When sourcing sliding gates, international B2B buyers should be aware of several cost components that can significantly influence pricing. These include:
-
Materials: The choice of materials directly affects the cost. Common options include steel, aluminum, and composite materials. Buyers should consider not only the initial material cost but also the longevity and maintenance requirements of each option.
-
Labor: Labor costs vary by region and are influenced by local wage standards. In countries like Poland and Egypt, labor may be more affordable, impacting the overall pricing structure.
-
Manufacturing Overhead: This encompasses utilities, rent, and equipment depreciation. Understanding a supplier’s overhead can provide insight into their pricing model.
-
Tooling: Custom designs may require specialized tooling, which can increase initial costs. Buyers should discuss tooling costs upfront, especially for custom specifications.
-
Quality Control (QC): Effective QC processes ensure that products meet safety and performance standards. The costs associated with QC can be a significant portion of the overall price, particularly in markets that demand high-quality certifications.
-
Logistics: Transportation costs are critical for international buyers. Factors such as distance, shipping method, and customs duties can add to the total cost of ownership.
-
Margin: Suppliers typically include a profit margin in their pricing. This can vary based on competition and market conditions.
How Do Price Influencers Affect Sliding Gate Sourcing?
Understanding the various price influencers can help buyers make informed decisions. Key factors include:
-
Volume/MOQ (Minimum Order Quantity): Ordering in larger quantities often results in lower per-unit costs. Buyers should evaluate their needs and negotiate for better pricing based on volume.
-
Specifications and Customization: Customized sliding gates with specific dimensions or features can lead to higher costs. It’s essential to balance customization needs with budget constraints.
-
Materials and Quality Certifications: Higher quality materials and certifications (e.g., ISO, CE marking) often come at a premium. Buyers should weigh the benefits of quality against the costs.
-
Supplier Factors: The reputation, reliability, and location of the supplier can influence pricing. Establishing relationships with reputable suppliers can lead to better pricing and service.
-
Incoterms: The choice of Incoterms (e.g., FOB, CIF) affects logistics costs and risk. Understanding these terms is critical for calculating the total cost of ownership.
What Buyer Tips Can Enhance Cost-Efficiency in Sliding Gate Sourcing?
International B2B buyers should adopt several strategies to improve cost-efficiency:
-
Negotiation Skills: Strong negotiation can lead to favorable terms. Buyers should prepare by understanding the market and the supplier’s cost structure.
-
Consider Total Cost of Ownership (TCO): TCO includes all costs associated with the product over its lifecycle, such as maintenance and operational costs. This holistic view can influence purchasing decisions.
-
Pricing Nuances for Different Regions: Buyers from Africa, South America, the Middle East, and Europe may encounter different pricing structures due to local economic conditions. Being aware of these nuances can aid in effective negotiation and supplier selection.
-
Research and Benchmarking: Conducting thorough market research and benchmarking against similar products can help buyers understand fair pricing and avoid overpaying.
Important Considerations Regarding Pricing
While the above insights provide a framework for understanding costs and pricing, it is essential to approach any pricing discussions with a clear understanding of the market dynamics. Prices can vary significantly based on factors such as supplier reputation and regional economic conditions. Always request detailed quotations and consider multiple suppliers to ensure competitive pricing.
In conclusion, effective sliding gate sourcing requires a comprehensive understanding of cost components, price influencers, and strategic buyer practices. By applying these insights, international B2B buyers can enhance their sourcing efficiency and make informed purchasing decisions.
Alternatives Analysis: Comparing sliding gate With Other Solutions
When considering security and access control for commercial properties, sliding gates are a popular option. However, it’s essential to evaluate other available solutions to ensure that your choice aligns with your specific requirements. Below, we analyze sliding gates against alternative options such as swing gates and barrier arms, providing actionable insights for international B2B buyers.
Comparison Aspect | Sliding Gate | Swing Gate | Barrier Arm |
---|---|---|---|
Performance | High security, suitable for large openings | Moderate security, ideal for smaller spaces | Limited security, effective for controlled entry |
Cost | Higher initial investment, long-term savings | Lower initial cost, moderate maintenance | Low initial cost, but potential for higher long-term operational costs |
Ease of Implementation | Requires professional installation, suitable for various terrains | Easier to install, flexible design options | Simple installation, minimal site modifications |
Maintenance | Requires regular maintenance due to moving parts | Generally low maintenance, fewer moving parts | Minimal maintenance, but electronic components may need attention |
Best Use Case | Ideal for industrial sites, large commercial properties | Suitable for residential areas, smaller commercial sites | Best for parking lots, toll booths, or low-security areas |
What Are the Pros and Cons of Using Swing Gates as an Alternative?
Swing gates are an alternative that offers flexibility and ease of installation, making them a popular choice for various applications. One of the primary advantages of swing gates is their lower initial cost compared to sliding gates. They are also easier to install, which can be a significant benefit for businesses looking to minimize labor costs. However, their performance is moderate in terms of security, making them less suitable for high-security environments. Additionally, swing gates require sufficient space to operate, which may not be feasible in tighter areas.
How Do Barrier Arms Compare as a Cost-Effective Solution?
Barrier arms are another alternative that presents a cost-effective solution for access control. They are particularly advantageous for applications such as parking lots or toll booths, where quick entry and exit are necessary. The installation process is straightforward, requiring minimal site modifications. However, barrier arms offer limited security, as they can be easily bypassed. Furthermore, while the initial costs are low, ongoing operational costs can accumulate, especially if electronic components require frequent maintenance or replacement.
How Can B2B Buyers Choose the Right Access Control Solution?
Choosing the right access control solution depends on several factors, including the specific security needs of your facility, budget constraints, and available space. B2B buyers should conduct a thorough assessment of their operational requirements and consider the long-term implications of their investment. For high-security environments, sliding gates may provide the best performance despite a higher initial investment. In contrast, if budget and ease of installation are priorities, swing gates or barrier arms may be more suitable. Ultimately, aligning the access control solution with your business objectives will lead to more effective security management and operational efficiency.
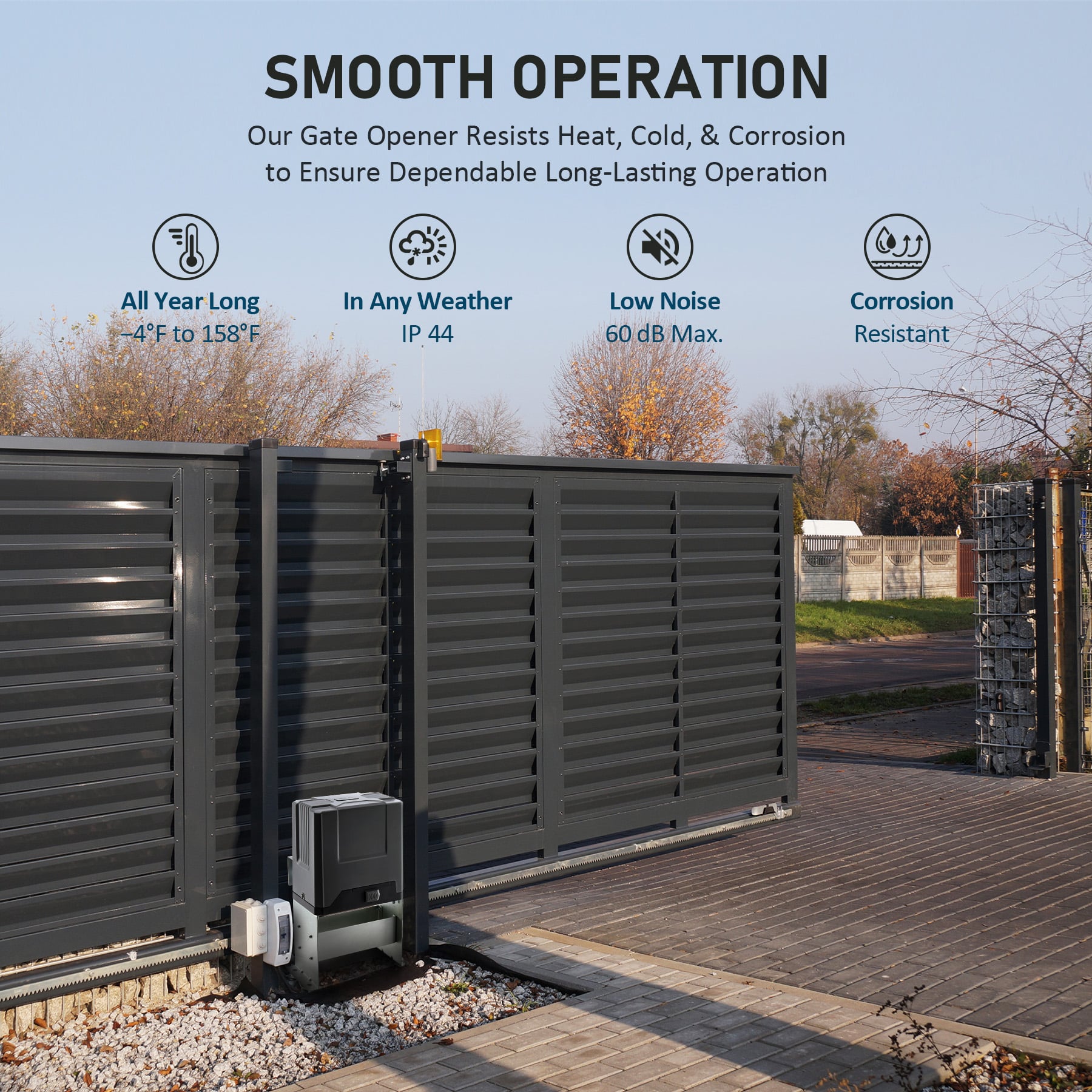
A stock image related to sliding gate.
Essential Technical Properties and Trade Terminology for sliding gate
What Are the Key Technical Properties of a Sliding Gate?
When evaluating sliding gates for purchase, understanding their technical properties is crucial for making informed decisions. Here are some essential specifications:
1. Material Grade: Why Does It Matter?
The material grade directly affects the durability and performance of a sliding gate. Common materials include steel, aluminum, and composite materials. Steel, for instance, is known for its strength and resistance to impact, making it suitable for high-security applications. Aluminum is lightweight and corrosion-resistant, ideal for environments with moisture. Selecting the appropriate material grade ensures longevity and reduced maintenance costs.
2. Load Capacity: How Much Weight Can It Handle?
Load capacity refers to the maximum weight a sliding gate can support while maintaining functional integrity. This specification is vital for international buyers as it determines the gate’s applicability in various settings, from residential to industrial. Understanding the load capacity helps in selecting a gate that can withstand the specific demands of its intended use, ensuring safety and reliability.
3. Tolerance Levels: What Are the Acceptable Variations?
Tolerance levels indicate the allowable deviation in measurements during manufacturing. This specification is crucial for ensuring that the sliding gate fits properly within its intended installation space. Tight tolerances minimize gaps that could compromise security or functionality. For international B2B buyers, understanding tolerance levels is key to ensuring compatibility with existing infrastructure.
4. Finish Type: How Does It Affect Durability?
The finish type, such as powder coating or galvanization, impacts both aesthetics and longevity. A high-quality finish can protect against corrosion and wear, extending the gate’s lifespan, especially in harsh climates found in regions like Africa or the Middle East. Buyers should prioritize finish types that align with their environmental conditions to reduce future maintenance needs.
5. Automation Compatibility: Is It Future-Proof?
As technology advances, many sliding gates now offer automation compatibility. This property allows for integration with access control systems, enhancing security and convenience. For B2B buyers, considering automation features can provide a competitive edge, especially in markets where security is paramount.
What Are Common Trade Terms Related to Sliding Gates?
Understanding trade terminology is vital for navigating the purchasing process effectively. Here are some common terms that every international B2B buyer should know:
1. OEM (Original Equipment Manufacturer): What Does It Mean?
OEM refers to a company that produces parts or equipment that may be marketed by another manufacturer. In the context of sliding gates, working with an OEM can ensure high-quality products tailored to specific requirements. Buyers should consider OEM relationships for custom gate solutions.
2. MOQ (Minimum Order Quantity): Why Is It Important?
MOQ is the smallest quantity of a product that a supplier is willing to sell. Understanding MOQ is essential for budgeting and inventory management. Buyers from regions like Europe or South America should negotiate MOQs that align with their purchasing capabilities to avoid excess inventory costs.
3. RFQ (Request for Quotation): How to Utilize It?
An RFQ is a document sent to suppliers requesting pricing and terms for specific products. For sliding gates, an RFQ can streamline the procurement process by ensuring that all potential suppliers provide comparable information. This approach helps in making well-informed purchasing decisions.
4. Incoterms: What Are They and Why Do They Matter?
Incoterms are international commercial terms that define the responsibilities of buyers and sellers in shipping goods. They clarify who is responsible for shipping, insurance, and tariffs. For international buyers, understanding Incoterms is crucial to avoid unexpected costs and ensure smooth transactions.
5. Lead Time: How Long Will It Take?
Lead time is the period between placing an order and receiving the product. Knowing the lead time is essential for project planning and inventory management. B2B buyers should factor in lead times when making purchasing decisions to ensure timely project execution.
By understanding these technical properties and trade terms, international B2B buyers can make more informed decisions when sourcing sliding gates, ultimately leading to better procurement outcomes.
Navigating Market Dynamics and Sourcing Trends in the sliding gate Sector
What Are the Current Market Dynamics and Key Trends in the Sliding Gate Sector?
The global sliding gate market is experiencing significant transformation driven by technological advancements, evolving consumer preferences, and regional economic developments. For international B2B buyers, particularly from regions such as Africa, South America, the Middle East, and Europe, understanding these dynamics is essential for informed sourcing decisions.
One of the primary drivers in the market is the increasing demand for automated and smart gate solutions. As urbanization accelerates, especially in developing regions, the need for efficient access control systems has surged. Technologies such as IoT (Internet of Things) integration and remote monitoring capabilities are becoming standard, allowing for enhanced security and operational efficiency. Buyers should consider suppliers that offer these innovative technologies, as they not only improve functionality but also provide a competitive edge.
Additionally, the emphasis on aesthetics and customization is gaining traction. B2B buyers are increasingly looking for sliding gates that not only serve a practical purpose but also complement the architectural design of their properties. This trend is particularly relevant in Europe and the Middle East, where the design is often a critical factor. Suppliers that can offer customizable solutions with various materials and finishes are likely to be more appealing to buyers.
Lastly, the impact of global trade dynamics, including tariffs and supply chain disruptions, cannot be overlooked. Buyers should remain agile and consider sourcing from local manufacturers or those with diversified supply chains to mitigate risks associated with global dependencies.
How Is Sustainability Shaping Sourcing Decisions in the Sliding Gate Sector?
Sustainability is no longer just a buzzword; it has become a crucial factor in B2B purchasing decisions. In the sliding gate sector, the environmental impact of materials and production processes is increasingly under scrutiny. Buyers from Africa, South America, the Middle East, and Europe are prioritizing suppliers who demonstrate a commitment to sustainable practices.
Ethical sourcing is paramount in today’s market. Buyers are encouraged to engage with suppliers who adhere to responsible manufacturing practices, which include reducing waste, using energy-efficient processes, and ensuring fair labor practices. This not only enhances a company’s brand reputation but also aligns with global sustainability goals.
Moreover, the use of ‘green’ certifications and sustainable materials is becoming a key differentiator. Buyers should look for suppliers who utilize recycled materials or those that have certifications like ISO 14001, which indicates effective environmental management systems. This commitment to sustainability can also result in cost savings over time through reduced energy consumption and waste management.
How Has the Sliding Gate Sector Evolved Over Time?
The sliding gate sector has undergone significant evolution over the last few decades. Initially, sliding gates were primarily manual and constructed from basic materials. However, advancements in technology and design have transformed these gates into sophisticated automated systems equipped with safety features and smart technology.
The introduction of electric sliding gates has revolutionized access control, making them a staple in both residential and commercial properties. Moreover, the integration of smart technology has opened new avenues for security and convenience, enabling users to control access remotely and monitor their properties in real-time. As a result, today’s sliding gates are not just functional barriers but integral components of modern security and architectural design.
In conclusion, international B2B buyers in the sliding gate sector must navigate a complex landscape shaped by technological advancements, sustainability concerns, and evolving consumer preferences. By focusing on innovative solutions and ethical sourcing practices, buyers can position themselves advantageously in this dynamic market.
Frequently Asked Questions (FAQs) for B2B Buyers of sliding gate
-
How do I determine the right sliding gate size for my property?
To choose the correct sliding gate size, first measure the width of the opening where the gate will be installed. Consider the height you desire for security and aesthetics. Additionally, factor in the gate’s track system, which may require extra space. It’s advisable to consult with suppliers who can provide tailored recommendations based on specific site conditions, ensuring compliance with local regulations and standards. -
What materials are best for sliding gates in different climates?
The choice of material for sliding gates largely depends on the climate of your region. For humid environments, such as parts of Africa and South America, galvanized steel or aluminum is preferable due to their corrosion resistance. In dry climates, wood can be an excellent choice, provided it is properly treated. In colder regions like Europe, insulated gates may be beneficial for energy efficiency. Always discuss material options with suppliers who understand your local conditions. -
What customization options are available for sliding gates?
Sliding gates can be customized in various ways, including size, material, color, and design. Many manufacturers also offer features like automated opening systems, integrated access control, and decorative elements. When sourcing, communicate your specific requirements to suppliers and inquire about their capabilities to ensure the gate meets your functional and aesthetic needs. -
What is the minimum order quantity (MOQ) for sliding gates?
The MOQ for sliding gates can vary significantly between suppliers. Some may offer single-unit purchases, while others might require bulk orders to achieve cost efficiency. As an international buyer, it’s essential to clarify the MOQ with potential suppliers early in negotiations to avoid misunderstandings and to ensure that you can meet your project needs without excess inventory. -
How do I vet suppliers for sliding gates?
Vetting suppliers is crucial to ensure quality and reliability. Start by checking their certifications and industry experience. Request references from previous clients, particularly those in your region. Additionally, assess their manufacturing processes and quality assurance practices. Engaging in a site visit or utilizing third-party inspection services can further validate their capabilities and commitment to quality.
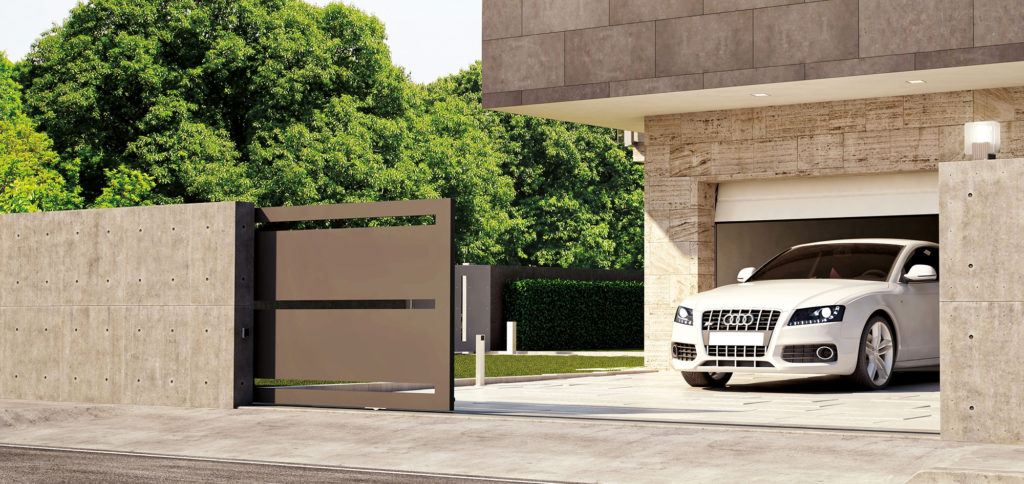
A stock image related to sliding gate.
-
What payment terms should I expect when purchasing sliding gates internationally?
Payment terms for international purchases can vary widely. Common options include letters of credit, advance payments, or net payment terms post-delivery. It’s vital to negotiate terms that protect your interests while also being acceptable to the supplier. Ensure clarity on currency exchange rates and potential fees associated with international transactions to avoid unexpected costs. -
How can I ensure quality assurance for sliding gates?
To ensure quality assurance, request detailed product specifications and test reports from suppliers. Implement a pre-shipment inspection process to verify that the gates meet your standards before they are dispatched. Consider building a quality control checklist that covers material integrity, finish quality, and functionality. Establishing a good relationship with your supplier can also facilitate better quality control throughout the production process. -
What logistics considerations should I keep in mind when importing sliding gates?
When importing sliding gates, consider factors such as shipping methods, customs duties, and local regulations. Determine whether you need to arrange for freight forwarding or if the supplier offers shipping services. Understand the timeline for delivery, including potential delays due to customs clearance. It’s also wise to discuss return policies and warranty coverage with suppliers to mitigate risks associated with international shipping.
Important Disclaimer & Terms of Use
⚠️ Important Disclaimer
The information provided in this guide, including content regarding manufacturers, technical specifications, and market analysis, is for informational and educational purposes only. It does not constitute professional procurement advice, financial advice, or legal advice.
While we have made every effort to ensure the accuracy and timeliness of the information, we are not responsible for any errors, omissions, or outdated information. Market conditions, company details, and technical standards are subject to change.
B2B buyers must conduct their own independent and thorough due diligence before making any purchasing decisions. This includes contacting suppliers directly, verifying certifications, requesting samples, and seeking professional consultation. The risk of relying on any information in this guide is borne solely by the reader.
Strategic Sourcing Conclusion and Outlook for sliding gate
In the evolving landscape of sliding gate procurement, strategic sourcing remains pivotal for international B2B buyers, particularly in Africa, South America, the Middle East, and Europe. By leveraging comprehensive market analysis and supplier relationships, businesses can identify the best value propositions, ensuring quality and compliance with local regulations. Key takeaways include the importance of understanding regional market dynamics, engaging with reliable suppliers, and considering factors such as installation, maintenance, and after-sales support.
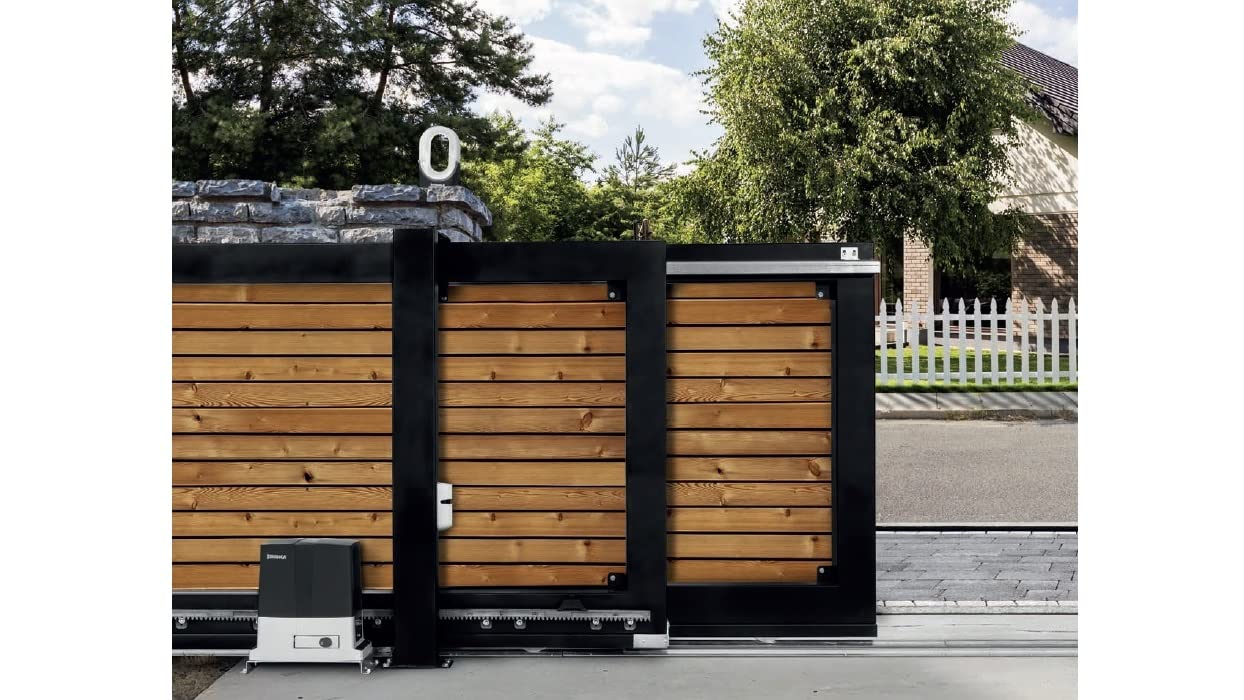
A stock image related to sliding gate.
What are the next steps for B2B buyers in the sliding gate market? As you navigate your sourcing strategies, prioritize building long-term partnerships with manufacturers who demonstrate innovation and sustainability. This approach not only enhances operational efficiency but also aligns with the growing emphasis on environmentally responsible practices across various industries.
Looking ahead, the sliding gate market is poised for growth, driven by increasing urbanization and security concerns. Now is the time to seize opportunities that align with your business goals. Engage with suppliers who can offer tailored solutions that meet your specific needs, and stay informed about technological advancements that could impact your procurement strategy. Your proactive engagement in strategic sourcing will position your business for success in an increasingly competitive global market.