Discover Cost-Saving Benefits of Airtight Inspection Covers (2025)
Introduction: Navigating the Global Market for airtight inspection cover
In the quest for optimal performance and safety in industrial applications, sourcing the right airtight inspection cover can be a daunting challenge for international B2B buyers. The need for reliable seals that prevent contamination and ensure compliance with stringent regulations has never been more critical. This comprehensive guide offers an in-depth exploration of the global market for airtight inspection covers, addressing various types, applications, and the nuances of supplier vetting.
Buyers from Africa, South America, the Middle East, and Europe, including countries like Spain and Italy, will find actionable insights tailored to their unique market conditions and regulatory environments. We will cover essential considerations such as material selection, industry-specific standards, and the implications of local sourcing versus international procurement. Additionally, this guide will delve into cost factors, helping you to navigate pricing structures and negotiate effectively with suppliers.
By equipping you with the knowledge to make informed purchasing decisions, this guide empowers you to enhance operational efficiency and product integrity. Whether you are looking for custom solutions or standardized products, understanding the landscape of airtight inspection covers is key to achieving your business objectives. Let’s dive into the critical aspects of this market to help you secure the best solutions for your needs.
Understanding airtight inspection cover Types and Variations
Type Name | Key Distinguishing Features | Primary B2B Applications | Brief Pros & Cons for Buyers |
---|---|---|---|
Standard Airtight Covers | Basic design, various sizes, and materials available | Industrial facilities, manufacturing | Pros: Cost-effective; Cons: Limited customization options. |
Heavy-Duty Inspection Covers | Reinforced materials, higher load-bearing capacity | Waste management, construction | Pros: Durable; Cons: Heavier and more expensive. |
Custom-Made Inspection Covers | Tailored dimensions and features to specific needs | Specialized industries (pharmaceuticals, food processing) | Pros: Perfect fit; Cons: Longer lead times. |
Quick-Access Airtight Covers | Features like hinged openings for easy access | Maintenance and inspection areas | Pros: Convenient; Cons: Potentially less airtight. |
Lockable Airtight Covers | Security features to prevent unauthorized access | Sensitive environments (data centers, laboratories) | Pros: Enhanced security; Cons: Higher cost. |
What are the Characteristics of Standard Airtight Covers?
Standard airtight covers are the most commonly used type in various industries due to their versatility and cost-effectiveness. These covers come in a range of sizes and materials, making them suitable for general applications in industrial facilities and manufacturing plants. When purchasing, B2B buyers should consider the specific dimensions and material properties to ensure compatibility with existing infrastructure. While they are budget-friendly, buyers may find limited customization options, which could impact their suitability for specialized applications.
How Do Heavy-Duty Inspection Covers Stand Out?
Heavy-duty inspection covers are designed to withstand significant weight and stress, making them ideal for applications in waste management and construction. These covers typically feature reinforced materials that enhance their load-bearing capacity. For B2B buyers, the durability of heavy-duty covers can result in lower long-term maintenance costs, although they may come at a higher upfront price. It’s essential to evaluate the specific environmental conditions and load requirements when considering this type.
Why Consider Custom-Made Inspection Covers?
Custom-made inspection covers offer tailored dimensions and features to meet the unique requirements of specialized industries such as pharmaceuticals and food processing. These covers can be designed to fit specific openings and incorporate additional features like gaskets for enhanced sealing. B2B buyers should weigh the benefits of a perfect fit against the longer lead times and potentially higher costs associated with custom solutions. It’s crucial to communicate specific needs with manufacturers to achieve the desired outcomes.
What Are the Advantages of Quick-Access Airtight Covers?
Quick-access airtight covers are designed with features such as hinged openings, allowing for easy inspection and maintenance. These are particularly useful in environments where frequent access is necessary, such as maintenance areas. While they offer convenience, B2B buyers should be aware that the design may compromise the airtight seal compared to standard covers. Evaluating the balance between accessibility and sealing efficiency is vital for making an informed purchasing decision.
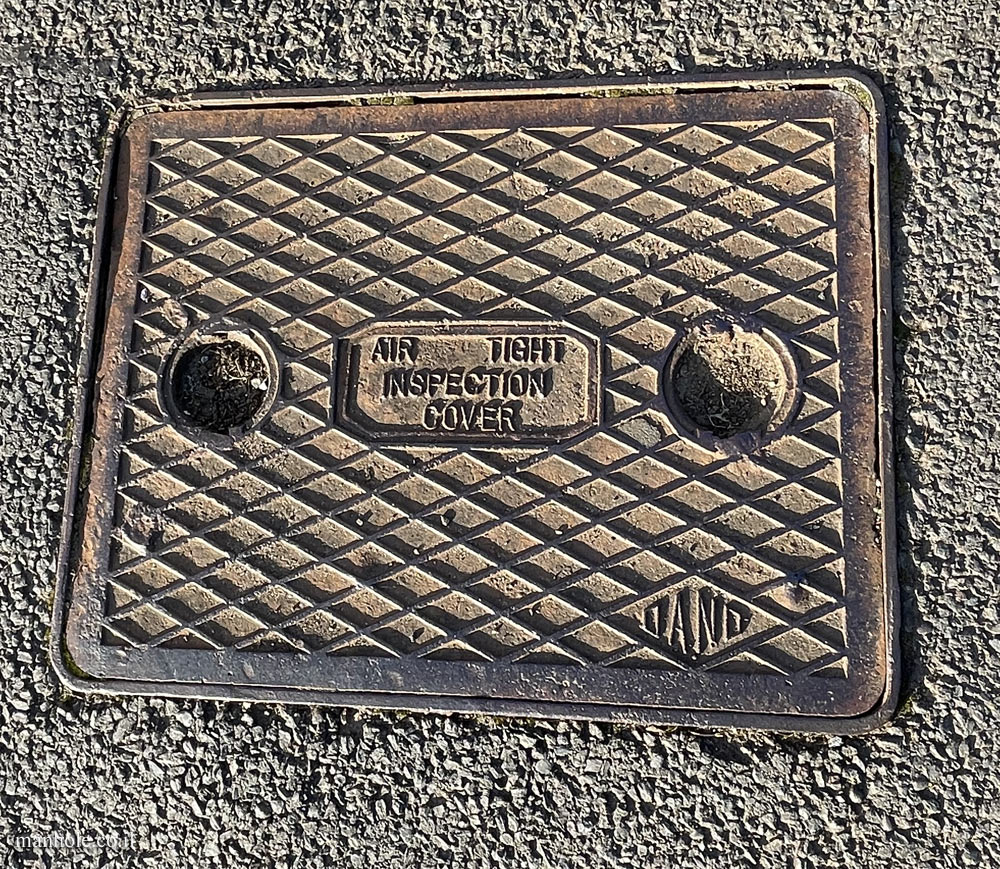
A stock image related to airtight inspection cover.
How Do Lockable Airtight Covers Enhance Security?
Lockable airtight covers provide an added layer of security, preventing unauthorized access in sensitive environments like data centers and laboratories. These covers are equipped with locking mechanisms that enhance safety while maintaining airtight properties. B2B buyers should consider the cost implications of these security features, as they often come at a premium. Understanding the specific security needs of the facility will help buyers determine if the investment in lockable covers is justified.
Key Industrial Applications of airtight inspection cover
Industry/Sector | Specific Application of Airtight Inspection Cover | Value/Benefit for the Business | Key Sourcing Considerations for this Application |
---|---|---|---|
Pharmaceutical | Quality Control in Clean Rooms | Ensures contamination-free environments, enhancing product safety and compliance with regulations. | Material certification, ease of cleaning, and customization options. |
Food and Beverage | Storage and Processing of Sensitive Ingredients | Prevents spoilage and contamination, preserving product integrity and extending shelf life. | Compliance with food safety standards, durability, and resistance to chemical exposure. |
Oil and Gas | Maintenance Access in Hazardous Environments | Provides safe, reliable access while preventing leaks and protecting sensitive equipment. | Explosion-proof ratings, material suitability for extreme conditions, and maintenance support. |
Chemical Manufacturing | Containment in Reaction Vessels | Minimizes the risk of leaks and exposure to hazardous substances, ensuring worker safety and regulatory compliance. | Compatibility with various chemicals, pressure ratings, and installation ease. |
Waste Management | Inspection in Waste Treatment Facilities | Facilitates safe monitoring and maintenance, preventing environmental contamination. | Durability against corrosive substances, ease of access for inspections, and regulatory compliance. |
How is Airtight Inspection Cover Used in the Pharmaceutical Sector?
In the pharmaceutical industry, airtight inspection covers are critical for maintaining clean room environments, where contamination can compromise product safety. These covers are typically installed on equipment and storage areas to provide controlled access while minimizing exposure to airborne particles. Buyers from this sector should prioritize covers that meet stringent material certifications and are easy to clean, ensuring compliance with health regulations. Additionally, customization options can be essential for unique equipment configurations.
What Role Do Airtight Inspection Covers Play in Food and Beverage Processing?
Within the food and beverage sector, airtight inspection covers are employed to protect sensitive ingredients during storage and processing. By preventing spoilage and contamination, these covers help maintain product quality and extend shelf life. For international buyers, especially in regions with varying food safety regulations, it is crucial to source covers that comply with local standards. Durability and resistance to chemical exposure are also key factors, ensuring that the covers withstand the rigorous demands of food processing environments.
Why are Airtight Inspection Covers Important in Oil and Gas Operations?
In the oil and gas industry, airtight inspection covers serve as a vital safety feature in hazardous environments. They provide reliable access to equipment while preventing leaks and protecting sensitive components from external contaminants. Buyers in this sector must consider explosion-proof ratings and material suitability for extreme conditions to ensure operational safety. Additionally, sourcing partners should offer comprehensive maintenance support to ensure longevity and reliability of the covers in challenging environments.
How Do Airtight Inspection Covers Enhance Safety in Chemical Manufacturing?
Airtight inspection covers are essential in chemical manufacturing for containment in reaction vessels. They minimize the risk of leaks and exposure to hazardous substances, which is critical for worker safety and compliance with environmental regulations. International B2B buyers should look for covers that are compatible with various chemicals and can withstand high pressures. Installation ease and ongoing maintenance considerations are also important for ensuring operational efficiency and safety.
What Benefits Do Airtight Inspection Covers Provide in Waste Management?
In waste management, airtight inspection covers facilitate safe monitoring and maintenance of waste treatment facilities. By preventing environmental contamination, these covers play a crucial role in compliance with local environmental regulations. Buyers need to ensure that the covers are durable against corrosive substances commonly found in waste materials. Additionally, ease of access for inspections is vital to maintaining operational efficiency and ensuring safety in waste management processes.
Related Video: Industrial Control Panel Basics
3 Common User Pain Points for ‘airtight inspection cover’ & Their Solutions
Scenario 1: Inadequate Sealing Leads to Contamination Risks
The Problem:
For international B2B buyers, particularly in sectors like pharmaceuticals and food processing, the integrity of an airtight inspection cover is paramount. Inadequate sealing can lead to contamination, which not only jeopardizes product quality but can also result in costly recalls and damage to reputation. Buyers often face difficulties in ensuring that the covers they procure are capable of providing the necessary airtight seal, especially when sourced from different manufacturers. This inconsistency can stem from variations in material quality, design flaws, or lack of proper installation guidance.
The Solution:
To overcome this challenge, buyers should prioritize sourcing airtight inspection covers from reputable suppliers who provide detailed specifications and testing certifications. When evaluating potential suppliers, request samples to conduct your own sealing tests, ensuring that the cover meets industry standards. Additionally, consider investing in training for your team on proper installation techniques. By ensuring a robust installation process, you can significantly reduce the risk of contamination and enhance overall operational efficiency. Regular maintenance checks and periodic replacements based on usage can also prolong the lifespan of the covers, ensuring continued protection against contaminants.
Scenario 2: High Maintenance Costs Due to Frequent Repairs
The Problem:
Another pain point for B2B buyers is the high maintenance costs associated with frequent repairs or replacements of airtight inspection covers. In many industrial applications, these covers are subjected to harsh environments, leading to wear and tear. Buyers often discover that their selected covers fail to withstand specific operational conditions, resulting in unexpected downtime and significant repair expenses. This issue is exacerbated in regions with limited access to quick replacement parts, adding to the logistical burden.
The Solution:
To mitigate high maintenance costs, buyers should conduct a thorough assessment of their operational environment before selecting airtight inspection covers. This includes understanding factors such as temperature fluctuations, humidity levels, and exposure to corrosive substances. Opting for covers made from durable materials, such as stainless steel or high-grade polymers, can provide greater resilience and longevity. Additionally, establishing a routine inspection schedule can help identify wear and tear early on, allowing for timely interventions before a complete failure occurs. Collaborating with suppliers who offer warranties or service agreements can also provide peace of mind and financial protection against unforeseen repairs.
Scenario 3: Difficulty in Compliance with Regulatory Standards
The Problem:
B2B buyers in industries such as food, pharmaceuticals, and chemicals often face stringent regulatory standards regarding product safety and quality. Failure to comply can result in severe penalties and loss of market access. Buyers may struggle to ensure that the airtight inspection covers they choose meet all necessary regulations, especially when sourcing from international suppliers who may not adhere to local standards. This uncertainty can lead to increased scrutiny during audits and inspections, putting companies at risk.
The Solution:
To navigate compliance challenges effectively, B2B buyers should familiarize themselves with the specific regulations that apply to their industry and region. When sourcing airtight inspection covers, it is crucial to select suppliers who provide comprehensive documentation, including compliance certifications and test results relevant to the buyer’s location. Engaging in open communication with suppliers about regulatory requirements can also ensure that the products you procure are compliant. Additionally, consider conducting periodic audits of your suppliers to verify that they maintain compliance with industry standards. This proactive approach not only protects your business but also builds trust with customers and regulatory bodies alike.
Strategic Material Selection Guide for airtight inspection cover
When selecting materials for airtight inspection covers, it is crucial to consider the specific properties and applications of each material. The choice of material can significantly affect the performance, durability, and compliance of the product, especially in diverse international markets. Below are analyses of four common materials used for airtight inspection covers, focusing on their properties, pros and cons, and considerations for international buyers.
What Are the Key Properties of Stainless Steel for Airtight Inspection Covers?
Stainless steel is renowned for its high corrosion resistance and strength, making it an ideal choice for environments exposed to moisture and chemicals. It typically has a temperature rating of up to 800°C and can withstand high pressure, which is essential for applications in the oil and gas industry or food processing plants.
Pros and Cons: The durability of stainless steel is one of its main advantages, providing a long lifespan even under harsh conditions. However, it is often more expensive than other materials and can be complex to manufacture, particularly for custom designs.
Impact on Application: Stainless steel is compatible with a wide range of media, including water, oils, and chemicals, making it versatile for various industrial applications.
Considerations for International Buyers: Buyers from regions like Europe may need to comply with standards such as DIN EN 10088, while those in Africa or South America should consider local regulations regarding corrosion resistance and safety.
How Does Aluminum Compare for Airtight Inspection Covers?
Aluminum is a lightweight and cost-effective material that offers good corrosion resistance, particularly when anodized. It typically has a temperature rating of up to 200°C, making it suitable for many industrial applications.
Pros and Cons: The lightweight nature of aluminum makes it easier to handle and install. However, it is less durable than stainless steel and may not be suitable for high-pressure applications. Additionally, its lower temperature rating limits its use in extreme environments.
Impact on Application: Aluminum is particularly compatible with non-corrosive media, making it ideal for applications in the food and beverage industry.
Considerations for International Buyers: Buyers should be aware of the varying standards for aluminum alloys in different regions, such as ASTM in the United States and EN standards in Europe.
What Are the Benefits of Composite Materials for Airtight Inspection Covers?
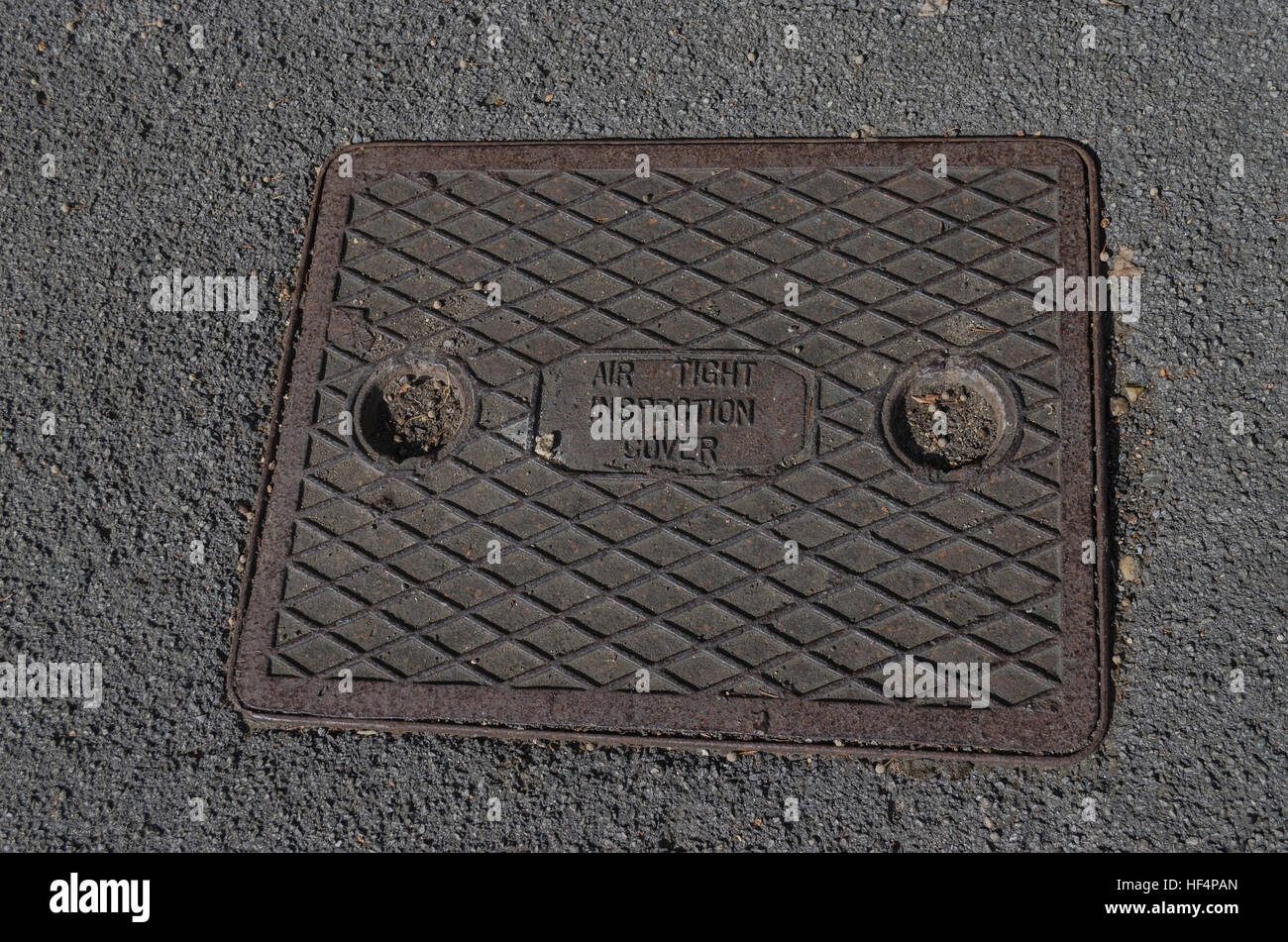
A stock image related to airtight inspection cover.
Composite materials, often made from a combination of fiberglass and resin, provide excellent corrosion resistance and can be tailored for specific applications. They typically have a temperature rating of up to 120°C.
Pros and Cons: Composites are lightweight and can be molded into complex shapes, offering design flexibility. However, they can be more expensive than metals and may have limitations in load-bearing capacity.
Impact on Application: These materials are particularly suited for corrosive environments, such as wastewater treatment facilities, where traditional metals may fail.
Considerations for International Buyers: Compliance with standards such as ASTM D638 for tensile strength is essential, and buyers should verify the manufacturer’s certifications to ensure quality.
Why Choose Cast Iron for Airtight Inspection Covers?
Cast iron is a traditional material known for its strength and durability, with a temperature rating typically around 300°C. It is often used in heavy industrial applications, such as in power generation and heavy machinery.
Pros and Cons: The primary advantage of cast iron is its ability to withstand heavy loads and high temperatures. However, it is prone to rust if not properly coated and is heavier than other materials, which can complicate installation.
Impact on Application: Cast iron is suitable for high-pressure applications but may not be ideal for corrosive environments unless adequately protected.
Considerations for International Buyers: Buyers should ensure compliance with standards such as ASTM A48 for gray iron castings, particularly in regions like North America and Europe, where stringent quality standards are enforced.
Summary Table of Material Selection for Airtight Inspection Covers
Material | Typical Use Case for Airtight Inspection Cover | Key Advantage | Key Disadvantage/Limitation | Relative Cost (Low/Med/High) |
---|---|---|---|---|
Stainless Steel | Oil and gas, food processing | High corrosion resistance | Higher cost and manufacturing complexity | High |
Aluminum | Food and beverage industry | Lightweight and cost-effective | Limited durability and temperature rating | Medium |
Composite | Wastewater treatment facilities | Excellent corrosion resistance | Higher cost and load limitations | High |
Cast Iron | Power generation, heavy machinery | High strength and durability | Prone to rust and heavier weight | Medium |
This strategic material selection guide provides valuable insights for international B2B buyers, enabling them to make informed decisions based on specific application needs and regional compliance requirements.
In-depth Look: Manufacturing Processes and Quality Assurance for airtight inspection cover
What are the Key Stages in the Manufacturing Process of Airtight Inspection Covers?
The manufacturing process of airtight inspection covers involves several critical stages, each contributing to the final product’s quality and effectiveness. Understanding these stages can help B2B buyers evaluate potential suppliers and ensure that they meet industry standards.
Material Preparation: What Materials Are Commonly Used?
The choice of materials is crucial for the performance of airtight inspection covers. Common materials include:
- Stainless Steel: Known for its corrosion resistance and durability, stainless steel is often preferred for environments exposed to harsh chemicals or extreme conditions.
- Aluminum: Lightweight and resistant to rust, aluminum is another popular choice, particularly for applications where weight is a consideration.
- Plastic Composites: For specific applications, high-grade plastic composites can be used, providing excellent sealing capabilities and resistance to chemicals.
Before manufacturing begins, raw materials undergo rigorous inspection to ensure they meet specified standards. This includes checking for impurities and verifying material certifications.
How is the Forming Process Conducted for Airtight Inspection Covers?
The forming process is where the raw materials are shaped into the desired form. This can include:
- Stamping: A common technique for metal covers, stamping uses a die to cut and shape materials into specific forms.
- Injection Molding: For plastic covers, injection molding allows for intricate designs and shapes, providing flexibility in product development.
- CNC Machining: This method is often employed for precision parts, allowing for tight tolerances essential in achieving an airtight seal.
The choice of forming technique impacts both the cost and the quality of the final product. Buyers should inquire about the specific techniques used by potential suppliers to ensure they align with their quality expectations.
What Does the Assembly Process Entail?
The assembly of airtight inspection covers involves putting together various components, including the cover itself, gaskets, and locking mechanisms. This stage is critical for ensuring that the final product achieves the intended airtight functionality.
- Manual Assembly: Often used for smaller batches or complex designs, manual assembly allows for greater attention to detail.
- Automated Assembly Lines: For larger production runs, automated processes increase efficiency and consistency, reducing the risk of human error.
During assembly, it’s essential to maintain cleanliness to prevent contamination, which could compromise the airtight seal.
What Finishing Techniques Are Applied?
Finishing processes enhance the durability and aesthetics of airtight inspection covers. Common techniques include:
- Coating: Applying protective coatings can increase resistance to chemicals and environmental factors.
- Polishing: This improves the surface finish, which can be crucial for visual inspections and overall product appeal.
Buyers should consider the finishing techniques employed, as these can significantly affect the product’s longevity and performance in various environments.
How is Quality Assurance Implemented in Manufacturing Airtight Inspection Covers?
Quality assurance (QA) is vital in ensuring that airtight inspection covers perform as expected. International standards and industry-specific certifications play a significant role in this process.
What International Standards Should Buyers Be Aware Of?
International standards such as ISO 9001 are essential for ensuring consistent quality across manufacturing processes. This standard focuses on quality management systems and continuous improvement, which can enhance customer satisfaction.
In addition to ISO standards, buyers should be aware of industry-specific certifications such as:
- CE Marking: Required in the European Union, indicating compliance with health, safety, and environmental protection standards.
- API Certification: For products used in the oil and gas industry, API certification ensures that the products meet specific industry standards.
Buyers should request documentation proving compliance with these standards to ensure that the products meet their quality expectations.
What are the Key Quality Control Checkpoints?
Quality control (QC) checkpoints are integral to the manufacturing process. Common checkpoints include:
- Incoming Quality Control (IQC): Inspects raw materials before they enter production.
- In-Process Quality Control (IPQC): Monitors processes during manufacturing to catch any defects early.
- Final Quality Control (FQC): Conducts a thorough inspection of finished products to ensure they meet specifications.
Each of these checkpoints plays a role in minimizing defects and ensuring that the final product meets the required standards.
Which Testing Methods Are Commonly Used for Airtight Inspection Covers?
Testing methods are essential for verifying the performance of airtight inspection covers. Common methods include:
- Leak Testing: This involves pressurizing the cover and checking for leaks, ensuring that it can maintain an airtight seal.
- Material Testing: Evaluating the strength and durability of materials used in the covers.
- Environmental Testing: Simulating conditions such as temperature and humidity to assess how the cover performs under stress.
B2B buyers should inquire about the specific testing methods used by suppliers to ensure the products can withstand their intended applications.
How Can B2B Buyers Verify Supplier Quality Control?
Verifying a supplier’s quality control processes is crucial for international buyers. Here are several strategies:
- Audits: Conducting regular audits of suppliers can provide insights into their manufacturing processes and adherence to quality standards.
- Quality Reports: Requesting detailed QC reports can help buyers assess the effectiveness of the supplier’s quality management systems.
- Third-Party Inspections: Engaging third-party inspection services can provide an unbiased evaluation of the supplier’s products and processes.
Understanding the nuances of quality control and assurance in manufacturing is essential for buyers from diverse regions, including Africa, South America, the Middle East, and Europe. This knowledge enables them to make informed decisions when selecting suppliers and ensures that they receive high-quality airtight inspection covers that meet their specific needs.
Practical Sourcing Guide: A Step-by-Step Checklist for ‘airtight inspection cover’
In the international B2B market, sourcing an airtight inspection cover requires careful consideration and strategic planning. This guide provides a practical checklist for buyers from regions such as Africa, South America, the Middle East, and Europe, ensuring a streamlined procurement process.
Step 1: Define Your Technical Specifications
Establishing clear technical specifications is the foundation of successful sourcing. Consider factors such as dimensions, weight capacity, material (e.g., stainless steel or aluminum), and environmental ratings. Detailed specifications will help suppliers understand your requirements and ensure that the product will perform optimally in your intended application.
Step 2: Research Market Trends and Standards
Understanding current market trends and regulatory standards is essential. Investigate industry-specific requirements, such as ISO certifications or local compliance guidelines relevant to your region. This knowledge not only aids in evaluating suppliers but also ensures that your procurement aligns with best practices and safety regulations.
Step 3: Evaluate Potential Suppliers
Before finalizing any agreements, thoroughly vet potential suppliers. Look for manufacturers with a proven track record in producing airtight inspection covers. Request documentation such as company profiles, product catalogs, and references from other businesses in your industry. A reliable supplier should also be willing to share case studies that demonstrate their capabilities.
Step 4: Request Samples and Conduct Quality Assessments
Obtaining product samples is crucial in assessing quality and fit for purpose. Examine the samples for material integrity, craftsmanship, and compliance with your specifications. Consider arranging a quality assessment through a third-party service to ensure that the product meets your standards, especially if the supplier is located in a different region.
Step 5: Negotiate Pricing and Terms
Once you have identified a suitable supplier, initiate negotiations on pricing and contract terms. Be prepared to discuss bulk order discounts, payment terms, and delivery schedules. It’s also advisable to include clauses that protect your interests, such as warranty conditions and remedies for non-compliance.
Step 6: Verify Supplier Certifications
Ensure that your selected supplier possesses the necessary certifications. This includes ISO certifications, product safety certifications, and environmental compliance documents. These certifications not only indicate quality assurance but also demonstrate the supplier’s commitment to adhering to international standards.
Step 7: Establish a Communication Protocol
Effective communication is vital for successful procurement. Set up a clear communication protocol with your supplier, outlining preferred channels, response times, and points of contact. Regular updates on production timelines and shipping can help mitigate risks and ensure that both parties are aligned throughout the sourcing process.
By following this checklist, B2B buyers can navigate the complexities of sourcing airtight inspection covers, ensuring that they make informed decisions that meet their operational needs.
Comprehensive Cost and Pricing Analysis for airtight inspection cover Sourcing
What Are the Key Cost Components in Sourcing Airtight Inspection Covers?
When sourcing airtight inspection covers, understanding the cost structure is crucial for effective budgeting and negotiation. The primary cost components include:
-
Materials: The choice of materials significantly impacts the price. Common materials include stainless steel, aluminum, and specialized polymers. Each material offers distinct benefits in terms of durability and resistance to environmental factors, which can influence both the initial cost and long-term performance.
-
Labor: Labor costs vary by region and manufacturing processes. For example, labor in countries like China may be lower compared to Europe or the Middle East. However, skilled labor is essential for quality production, particularly for customized or complex designs.
-
Manufacturing Overhead: This encompasses expenses related to factory operations, including utilities, equipment maintenance, and facility costs. Overhead can vary widely depending on the manufacturer’s location and efficiency.
-
Tooling: Custom tooling can be a significant upfront cost, especially for specialized designs. It is essential to factor in these costs when assessing the overall budget for sourcing.
-
Quality Control (QC): Implementing rigorous QC processes ensures that the products meet required specifications and certifications. This may add to the cost but is vital for maintaining product integrity, especially for buyers in regulated industries.
-
Logistics: Shipping costs can vary greatly based on distance, shipping method, and volume. Buyers must consider both the initial shipping costs and potential tariffs or duties that may apply.
-
Margin: Suppliers typically apply a margin to cover costs and generate profit. Understanding the supplier’s pricing strategy can help buyers negotiate better deals.
How Do Volume and Customization Affect Pricing of Airtight Inspection Covers?
Price influencers play a significant role in determining the final cost of airtight inspection covers. Key factors include:
-
Volume/MOQ: Suppliers often offer better pricing for larger orders due to economies of scale. Understanding minimum order quantities (MOQs) can help buyers optimize their purchasing strategies.
-
Specifications and Customization: Custom designs or specific requirements can significantly increase costs. Buyers should clearly define their needs to avoid unexpected expenses during the production phase.
-
Materials: The choice of materials directly influences the cost. High-performance materials may offer better durability but come at a higher price point.
-
Quality and Certifications: Products that meet international quality standards or possess certifications (e.g., ISO, CE) may command higher prices. Buyers should weigh the benefits of certified products against their budget constraints.
-
Supplier Factors: The supplier’s reputation, location, and production capabilities can affect pricing. Engaging with multiple suppliers can provide insights into competitive pricing.
-
Incoterms: Understanding Incoterms is essential for international transactions, as they dictate the responsibilities of buyers and sellers regarding shipping, insurance, and tariffs. This knowledge can help buyers avoid hidden costs.
What Are the Best Negotiation Strategies for International B2B Buyers?
For international buyers, especially from Africa, South America, the Middle East, and Europe, effective negotiation is key to achieving favorable pricing. Here are some actionable tips:
-
Research Market Prices: Familiarize yourself with market prices for similar products to establish a baseline for negotiations. Utilize industry reports and networking to gather data.
-
Build Relationships: Establishing strong relationships with suppliers can lead to better pricing and more favorable terms. Consider long-term partnerships rather than one-off transactions.
-
Leverage Total Cost of Ownership (TCO): Focus on the TCO rather than just the initial purchase price. Consider factors such as maintenance, lifespan, and operational efficiency when evaluating offers.
-
Be Transparent About Budget Constraints: Sharing your budget limitations can encourage suppliers to provide tailored solutions or suggest alternative products that fit within your price range.
-
Explore Payment Terms: Negotiating favorable payment terms can improve cash flow and make it easier to manage costs over time.
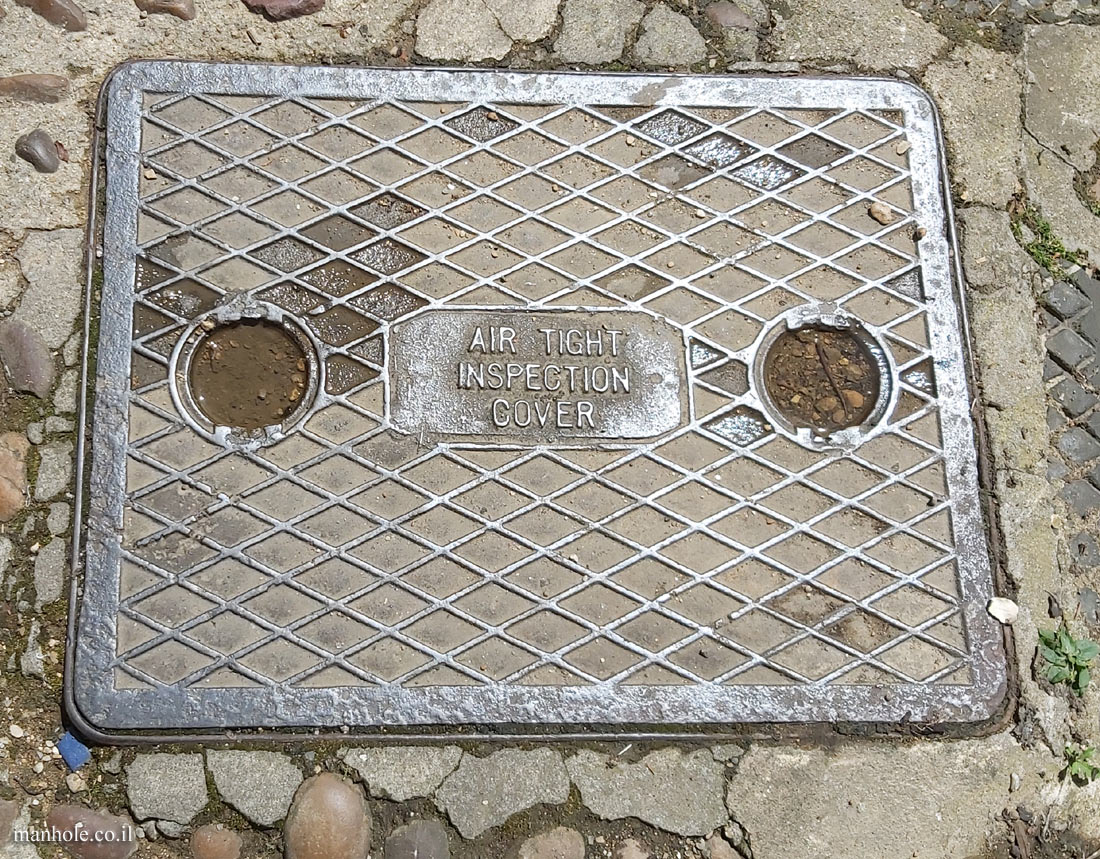
A stock image related to airtight inspection cover.
What Should Buyers Keep in Mind About Indicative Pricing?
Buyers should be cautious with indicative pricing, as it often serves as a starting point rather than a final quote. Prices can fluctuate based on market conditions, raw material costs, and other economic factors. Always seek detailed quotations and clarify all potential additional costs before finalizing a purchase. By doing so, international B2B buyers can ensure a more accurate understanding of their total financial commitment when sourcing airtight inspection covers.
Alternatives Analysis: Comparing airtight inspection cover With Other Solutions
When evaluating the best solutions for ensuring airtight conditions in various applications, it’s crucial to consider the available alternatives to airtight inspection covers. This analysis provides a comparative overview of airtight inspection covers against two other viable solutions: rubber gaskets and flanged access doors. Each option offers distinct benefits and drawbacks, making it essential for B2B buyers to assess their specific requirements before making a decision.
Comparison Aspect | Airtight Inspection Cover | Rubber Gasket | Flanged Access Door |
---|---|---|---|
Performance | High airtight integrity | Moderate airtight integrity | High airtight integrity |
Cost | Moderate to high | Low to moderate | Moderate to high |
Ease of Implementation | Moderate | Easy | Moderate |
Maintenance | Low | Low | Moderate |
Best Use Case | Industrial applications | General sealing applications | Access points in machinery |
What Are the Advantages and Disadvantages of Rubber Gaskets?
Rubber gaskets are widely used for sealing applications due to their affordability and ease of installation. They provide moderate airtight integrity, making them suitable for general sealing needs across various industries. The primary advantage of rubber gaskets is their low cost, which can significantly reduce overall project expenses. However, they may not withstand extreme temperatures or pressures as effectively as airtight inspection covers, potentially limiting their application in specialized environments.
How Do Flanged Access Doors Compare to Airtight Inspection Covers?
Flanged access doors are designed to provide an access point to systems requiring maintenance while maintaining high airtight integrity. They are typically used in industrial settings, where regular access is necessary for equipment servicing. The installation process is moderately complex, requiring specific mounting techniques. While they offer excellent sealing capabilities, the cost can be similar to that of airtight inspection covers. Maintenance is more demanding, as these doors require regular checks to ensure they remain airtight, which can add to operational costs.
Conclusion: How Can B2B Buyers Choose the Right Solution?
When deciding between airtight inspection covers, rubber gaskets, and flanged access doors, B2B buyers must assess their specific operational requirements, budget constraints, and the environmental conditions of their applications. Airtight inspection covers are ideal for high-performance needs in industrial applications, while rubber gaskets offer a cost-effective solution for less demanding sealing tasks. Flanged access doors provide a balance between accessibility and performance but may require more maintenance. By carefully analyzing these factors, international buyers from regions like Africa, South America, the Middle East, and Europe can make informed decisions that align with their operational goals.
Essential Technical Properties and Trade Terminology for airtight inspection cover
What Are the Key Technical Properties of an Airtight Inspection Cover?
When sourcing airtight inspection covers, understanding their technical specifications is crucial for ensuring product efficacy and compliance with industry standards. Here are some essential properties to consider:
1. Material Grade
The material grade refers to the specific composition of the cover, often made from metals like stainless steel or aluminum, or polymer composites. A higher grade typically indicates better corrosion resistance and durability, which are critical for applications in harsh environments. For B2B buyers, selecting the right material is essential to enhance the lifespan of the product and reduce maintenance costs.
2. Tolerance Levels
Tolerance levels define the permissible limits of variation in dimensions. For airtight inspection covers, tighter tolerances ensure a better seal, preventing leaks and contamination. This is particularly important in industries such as pharmaceuticals and food processing, where hygiene is paramount. Understanding tolerance levels helps buyers select products that will fit their specific applications without the need for costly adjustments.
3. Pressure Rating
The pressure rating indicates the maximum pressure the inspection cover can withstand without failing. This property is vital for applications involving high-pressure environments, such as chemical processing plants. Buyers should assess the operating conditions of their systems to ensure that the chosen cover meets or exceeds these pressure requirements, thus ensuring safety and operational efficiency.
4. Temperature Resistance
Temperature resistance refers to the cover’s ability to maintain its structural integrity under varying temperatures. This property is crucial for applications exposed to extreme heat or cold. Choosing a cover with the appropriate temperature resistance can prevent failures that lead to costly downtime and safety hazards.
5. Seal Type
The seal type is a critical aspect of airtight inspection covers, determining how effectively they can prevent the ingress of air, moisture, and contaminants. Common seal types include rubber gaskets and silicone seals. Selecting the right seal type is essential for maintaining the integrity of the environment being protected, especially in sectors like oil and gas, where contamination can have serious consequences.
What Are Common Trade Terms Related to Airtight Inspection Covers?
Navigating the procurement process for airtight inspection covers involves familiarizing oneself with industry-specific terminology. Here are some key terms that can facilitate effective communication and negotiation:
1. OEM (Original Equipment Manufacturer)
OEM refers to a company that produces parts or equipment that may be marketed by another manufacturer. Understanding OEM relationships is important for buyers who want to ensure they are sourcing high-quality components that meet their specifications.
2. MOQ (Minimum Order Quantity)
MOQ denotes the smallest quantity of a product that a supplier is willing to sell. This term is crucial for buyers to understand as it can affect budget planning and inventory management. Knowing the MOQ can help buyers negotiate better terms and avoid overstocking.
3. RFQ (Request for Quotation)
An RFQ is a document sent to suppliers to request pricing and availability of products. For B2B buyers, issuing an RFQ can streamline the procurement process and help in comparing different suppliers based on price and lead time.
4. Incoterms (International Commercial Terms)
Incoterms are a set of internationally recognized rules that define the responsibilities of buyers and sellers in international transactions. Familiarity with Incoterms, such as FOB (Free on Board) or CIF (Cost, Insurance, and Freight), is essential for buyers to understand shipping responsibilities, costs, and risk management in cross-border trade.
5. Lead Time
Lead time refers to the time taken from placing an order to its delivery. Understanding lead times is critical for B2B buyers to plan their production schedules effectively and avoid disruptions in operations.
By grasping these technical properties and industry terms, international B2B buyers can make more informed decisions when sourcing airtight inspection covers, ultimately leading to improved operational efficiency and cost savings.
Navigating Market Dynamics and Sourcing Trends in the airtight inspection cover Sector
What Are the Key Drivers Influencing the Airtight Inspection Cover Market?
The global market for airtight inspection covers is experiencing significant growth, driven by various factors including increased industrialization, stringent regulations regarding safety and environmental standards, and a growing focus on operational efficiency. Industries such as pharmaceuticals, food and beverage, and chemical manufacturing are particularly influential, as these sectors require reliable containment solutions to prevent contamination and ensure product integrity.
Emerging B2B technology trends, such as the integration of IoT (Internet of Things) and automation, are reshaping sourcing strategies. Companies are increasingly seeking airtight inspection covers equipped with smart technology that offers real-time monitoring and diagnostics. This trend not only enhances operational efficiency but also ensures compliance with safety regulations. Additionally, the rise of e-commerce platforms is facilitating easier access to suppliers, allowing international buyers, especially from Africa, South America, the Middle East, and Europe, to compare products and negotiate better terms.
Market dynamics indicate a shift towards more localized sourcing strategies. International buyers are increasingly looking for suppliers who can provide shorter lead times and reduced transportation costs. This trend is particularly relevant for buyers in Europe, such as Spain and Italy, where proximity to suppliers can significantly impact supply chain efficiency.
How Is Sustainability Shaping the Sourcing of Airtight Inspection Covers?
Sustainability is becoming a paramount consideration in the sourcing of airtight inspection covers. The environmental impact of manufacturing processes, materials used, and product lifecycle is under scrutiny from both consumers and regulatory bodies. As such, B2B buyers are prioritizing suppliers who demonstrate a commitment to sustainable practices.
Ethical sourcing is critical, with buyers seeking transparency in supply chains. This includes ensuring that materials are sourced responsibly and that suppliers adhere to fair labor practices. Certifications such as ISO 14001 (Environmental Management) and FSC (Forest Stewardship Council) are increasingly important in the purchasing decision. B2B buyers should actively seek out suppliers who can provide these certifications, as they not only reflect a commitment to sustainability but also mitigate risks associated with environmental and social governance (ESG) factors.
Furthermore, the use of ‘green’ materials, such as recycled metals and eco-friendly coatings, is gaining traction. By opting for these materials, buyers can enhance their brand reputation and appeal to environmentally-conscious consumers. This trend is especially relevant for industries in Europe, where regulatory pressure is high, and consumers increasingly demand sustainable products.
How Has the Airtight Inspection Cover Sector Evolved Over Time?
The evolution of the airtight inspection cover sector reflects broader industrial advancements and changing consumer expectations. Initially, these covers were primarily used in industries with stringent hygiene requirements, such as pharmaceuticals and food processing. Over the decades, advancements in materials science have led to the development of more robust, durable, and lightweight options, expanding their applicability across various sectors.
The introduction of smart technologies has further transformed the landscape, allowing for enhanced monitoring and control over production environments. As industries continue to adapt to the challenges posed by globalization and environmental concerns, airtight inspection covers are evolving to meet these new demands. The ongoing focus on efficiency, safety, and sustainability will likely shape the future trajectory of this sector, providing ample opportunities for international B2B buyers to innovate and differentiate themselves in the market.
Frequently Asked Questions (FAQs) for B2B Buyers of airtight inspection cover
-
How do I select the right airtight inspection cover for my industry needs?
When choosing an airtight inspection cover, consider the specific requirements of your industry, including size, material compatibility, and environmental factors such as pressure and temperature ranges. Analyze the standards and certifications relevant to your region, like ISO or ASTM, to ensure compliance. Engaging with suppliers who offer customization options can help meet niche specifications. Additionally, consult with industry experts or peers for recommendations based on their experiences with particular brands or models. -
What are the key features to look for in a quality airtight inspection cover?
Look for durability, resistance to chemicals, and ease of installation when evaluating airtight inspection covers. Ensure the cover has effective sealing mechanisms to prevent leaks and contamination. Materials like stainless steel or high-density polyethylene often provide superior performance in demanding environments. Additionally, consider features like inspection windows for monitoring without removal and built-in safety mechanisms, which can enhance operational efficiency and safety. -
What is the typical lead time for ordering airtight inspection covers internationally?
Lead times can vary significantly based on supplier location, production capabilities, and shipping logistics. Generally, expect a lead time of 4 to 12 weeks for custom orders. It’s advisable to communicate with suppliers upfront about your project timelines to align expectations. For urgent needs, inquire about expedited shipping options or suppliers with stock readily available in your region to minimize downtime. -
What are the common payment terms for international B2B transactions involving airtight inspection covers?
Payment terms often depend on the supplier’s policies and the buyer’s creditworthiness. Common arrangements include upfront payment, partial payment with the balance due upon delivery, or net payment terms (e.g., 30 or 60 days post-invoice). It’s prudent to negotiate terms that suit your cash flow while considering options like letters of credit or escrow services to mitigate risks in international transactions. -
How can I verify the credibility of suppliers for airtight inspection covers?
To assess supplier credibility, conduct thorough due diligence by checking online reviews, industry certifications, and client testimonials. Utilize platforms like LinkedIn to connect with other businesses that have previously engaged with the supplier. Request references and perform background checks through industry associations or trade organizations. Additionally, consider visiting the supplier’s facilities if feasible, or engage third-party inspection services to verify product quality before placing a bulk order. -
What customization options are available for airtight inspection covers?
Many manufacturers offer customization options, including size, shape, material, and sealing mechanisms to meet specific operational needs. You can also request features such as integrated lifting handles, inspection ports, or specific color coding for easier identification. Discuss your requirements with potential suppliers early in the process to ensure they can accommodate your needs and provide prototypes or samples for evaluation. -
What are the logistics considerations when importing airtight inspection covers?
Logistics considerations include understanding shipping methods, customs regulations, and import duties specific to your country. Ensure your supplier provides accurate shipping documentation to facilitate smooth customs clearance. It’s beneficial to work with logistics companies experienced in international shipping to handle customs and transport efficiently. Additionally, factor in lead times for shipping when planning your inventory to avoid stockouts. -
How do I ensure quality assurance for airtight inspection covers?
Quality assurance can be ensured by establishing clear quality standards and specifications in your purchase order. Request certifications and compliance documentation from the supplier, and consider conducting pre-shipment inspections to verify product quality. Engage in regular communication with the supplier throughout the production process to address any concerns. Implement a robust return and warranty policy to safeguard against defects or issues upon receipt of goods.
Important Disclaimer & Terms of Use
⚠️ Important Disclaimer
The information provided in this guide, including content regarding manufacturers, technical specifications, and market analysis, is for informational and educational purposes only. It does not constitute professional procurement advice, financial advice, or legal advice.
While we have made every effort to ensure the accuracy and timeliness of the information, we are not responsible for any errors, omissions, or outdated information. Market conditions, company details, and technical standards are subject to change.
B2B buyers must conduct their own independent and thorough due diligence before making any purchasing decisions. This includes contacting suppliers directly, verifying certifications, requesting samples, and seeking professional consultation. The risk of relying on any information in this guide is borne solely by the reader.
Strategic Sourcing Conclusion and Outlook for airtight inspection cover
What Are the Key Takeaways for B2B Buyers of Airtight Inspection Covers?
In conclusion, strategic sourcing of airtight inspection covers is essential for optimizing operational efficiency and ensuring compliance with industry standards. Buyers should prioritize suppliers who demonstrate a robust understanding of local regulations and offer high-quality products tailored to specific market needs. Establishing long-term partnerships with manufacturers can lead to better pricing, improved product quality, and enhanced support services.
How Can Buyers Approach Strategic Sourcing for Airtight Inspection Covers?
As international B2B buyers, particularly from Africa, South America, the Middle East, and Europe, it’s crucial to leverage market intelligence to navigate the complexities of sourcing. Engaging with suppliers who have a proven track record in your region can provide insights into best practices and innovative solutions. Additionally, consider using technology for seamless communication and order tracking, which can streamline the procurement process.
What Does the Future Hold for Airtight Inspection Cover Sourcing?
Looking ahead, the demand for airtight inspection covers is expected to grow, driven by increasing industrialization and heightened regulatory scrutiny. Buyers are encouraged to stay abreast of technological advancements that enhance product performance and sustainability. By focusing on strategic sourcing, companies can position themselves competitively while contributing to a more sustainable future.
Engage with trusted suppliers today to ensure your operations are not only compliant but also ready for tomorrow’s challenges.