Discover Cost Savings with Spheical Filter Screen Solutions (2025)
Introduction: Navigating the Global Market for spheical filter screen
In the competitive landscape of industrial manufacturing, sourcing the right spherical filter screen can present significant challenges for B2B buyers, especially those operating across diverse markets in Africa, South America, the Middle East, and Europe. With increasing demand for high-quality filtration solutions, understanding the nuances of spherical filter screens—ranging from material types to specific applications—becomes essential for making informed purchasing decisions.
This comprehensive guide aims to equip international buyers with critical insights into the various types of spherical filter screens available in the market, their applications across industries such as water treatment, food processing, and pharmaceuticals, and the importance of effective supplier vetting. We will delve into the factors influencing costs, including material quality and manufacturing processes, providing a detailed analysis that will help buyers optimize their procurement strategies.
By leveraging this guide, B2B buyers will gain a robust understanding of market dynamics, enabling them to navigate the complexities of sourcing spherical filter screens confidently. Whether you are in Brazil seeking innovative filtration solutions or in the Middle East exploring cost-effective suppliers, this resource is designed to empower you to make strategic, informed choices that align with your operational needs and budget considerations.
Understanding spheical filter screen Types and Variations
Type Name | Key Distinguishing Features | Primary B2B Applications | Brief Pros & Cons for Buyers |
---|---|---|---|
Standard Spherical Filter Screen | Uniform mesh size, made from stainless steel or nylon | Food processing, chemical filtration | Pros: Durable, easy to clean. Cons: Limited customization options. |
Micro Spherical Filter Screen | Extremely fine mesh, often less than 10 microns | Pharmaceutical, water treatment | Pros: High filtration efficiency. Cons: Prone to clogging. |
Self-Cleaning Spherical Filter Screen | Automated cleaning mechanism, reduces manual labor | Oil and gas, industrial wastewater | Pros: Low maintenance, continuous operation. Cons: Higher initial cost. |
Custom Spherical Filter Screen | Tailored mesh sizes and materials based on specifications | Aerospace, specialized manufacturing | Pros: Meets specific needs, enhances efficiency. Cons: Longer lead times. |
Multi-Layer Spherical Filter Screen | Multiple layers for enhanced filtration capabilities | Mining, environmental applications | Pros: Increased dirt holding capacity. Cons: Heavier, may require more support. |
What Are the Key Characteristics of Standard Spherical Filter Screens?
Standard spherical filter screens are typically constructed from durable materials like stainless steel or nylon, featuring a uniform mesh size. This type is ideal for applications in food processing and chemical filtration, where reliability and ease of cleaning are paramount. B2B buyers should consider their specific operational requirements, as standard options may lack the flexibility to accommodate unique filtration needs.
How Do Micro Spherical Filter Screens Enhance Filtration Efficiency?
Micro spherical filter screens are designed with extremely fine mesh, often measuring less than 10 microns, making them suitable for high-precision applications in pharmaceuticals and water treatment. While they offer exceptional filtration efficiency, buyers should be cautious of their tendency to clog, which can lead to increased maintenance requirements. It’s crucial to assess the frequency of cleaning and potential downtime in operations.
Why Choose Self-Cleaning Spherical Filter Screens for Industrial Applications?
Self-cleaning spherical filter screens feature an automated cleaning mechanism that minimizes manual intervention, making them particularly advantageous for industries like oil and gas and industrial wastewater management. While they significantly reduce maintenance efforts and downtime, the initial investment is typically higher than traditional filters. Buyers should evaluate the cost-benefit ratio based on their operational scale and maintenance capabilities.
What Are the Benefits of Custom Spherical Filter Screens for Specialized Needs?
Custom spherical filter screens are tailored to meet specific client requirements, including unique mesh sizes and materials. This adaptability makes them highly suitable for industries such as aerospace and specialized manufacturing. Although they provide a perfect fit for unique applications, buyers should be prepared for longer lead times and potentially higher costs. Proper planning and communication with suppliers can mitigate these challenges.
How Do Multi-Layer Spherical Filter Screens Improve Filtration Capacity?
Multi-layer spherical filter screens are designed with several layers to enhance filtration capabilities, making them ideal for demanding applications in mining and environmental sectors. These screens can hold more dirt and debris, which improves efficiency and reduces the frequency of replacements. However, their added weight may necessitate additional structural support in installation. Buyers should assess their operational needs and facility capabilities before choosing this option.
Related Video: Heat Pump Thermostat O, B, and C Terminal Variations Explained
Key Industrial Applications of spheical filter screen
Industry/Sector | Specific Application of Spherical Filter Screen | Value/Benefit for the Business | Key Sourcing Considerations for this Application |
---|---|---|---|
Water Treatment | Filtration of wastewater in municipal plants | Ensures compliance with environmental standards | Durability, chemical resistance, and size specifications |
Food and Beverage | Separation of solids in juice and beverage production | Enhances product quality and extends shelf life | Food-grade materials, easy cleaning, and maintenance |
Pharmaceutical | Filtration in drug manufacturing processes | Guarantees product purity and efficacy | Regulatory compliance, material integrity, and custom sizes |
Oil and Gas | Solid-liquid separation in drilling fluids | Improves operational efficiency and reduces waste | High-temperature resistance, corrosion resistance, and flow rate capacity |
Mining and Minerals | Separation of fine particles in mineral processing | Increases recovery rates and reduces contaminants | Custom mesh sizes, abrasion resistance, and material strength |
How is Spherical Filter Screen Used in Water Treatment?
In the water treatment sector, spherical filter screens are employed to filter wastewater at municipal plants. Their design allows for efficient removal of solids, ensuring compliance with local and international environmental standards. For international B2B buyers, particularly those in developing regions, sourcing durable and chemically resistant screens is critical due to the harsh conditions often present in wastewater treatment. Buyers must also consider size specifications to fit existing filtration systems.
What Role Does Spherical Filter Screen Play in Food and Beverage Production?
In the food and beverage industry, spherical filter screens are utilized to separate solids from liquids during juice and beverage production. This filtration process is vital for enhancing product quality and extending shelf life, thereby increasing market competitiveness. B2B buyers in this sector should prioritize food-grade materials that meet safety regulations, as well as screens that allow for easy cleaning and maintenance to ensure hygiene standards are upheld.
How is Spherical Filter Screen Critical in Pharmaceutical Manufacturing?
Pharmaceutical companies rely on spherical filter screens during drug manufacturing processes to ensure product purity and efficacy. The screens help eliminate contaminants that could compromise the quality of medications. B2B buyers in this industry must focus on sourcing screens that comply with stringent regulatory standards, as well as those that maintain material integrity under various processing conditions. Custom sizes may also be necessary to fit specialized equipment.
What Benefits Does Spherical Filter Screen Provide in Oil and Gas Operations?
In the oil and gas sector, spherical filter screens are crucial for solid-liquid separation in drilling fluids. Their use significantly improves operational efficiency by reducing waste and enhancing the recovery of valuable resources. Buyers in this sector should consider high-temperature and corrosion-resistant materials to withstand the challenging environments typical of oil extraction. Additionally, the flow rate capacity of the screens must align with operational requirements.
How Does Spherical Filter Screen Enhance Efficiency in Mining and Minerals?
Spherical filter screens are employed in mining and minerals processing to separate fine particles from slurries. This separation is essential for increasing recovery rates and minimizing contaminants in the final product. For B2B buyers in the mining industry, sourcing screens with custom mesh sizes and high abrasion resistance is vital to ensure effective filtration and durability in demanding conditions. Material strength is also a key factor in maintaining operational efficiency.
Related Video: Uses Technology in the Conduct of Survey || Joel Vacalares
3 Common User Pain Points for ‘spheical filter screen’ & Their Solutions
Scenario 1: Difficulty in Sourcing High-Quality Spherical Filter Screens
The Problem:
B2B buyers often encounter challenges when sourcing spherical filter screens that meet their specific quality and performance standards. This issue can be particularly acute in regions like Africa and South America, where local suppliers may not provide the necessary certifications or product specifications. Buyers may face uncertainty about the reliability of overseas manufacturers, leading to concerns about product durability, functionality, and compliance with local regulations. The risk of receiving subpar products can result in operational inefficiencies and increased costs.
The Solution:
To overcome sourcing challenges, buyers should implement a thorough supplier evaluation process. Start by conducting comprehensive research on potential manufacturers, focusing on those with established reputations in the industry. Request samples and detailed product specifications to assess quality firsthand. It is also advisable to inquire about certifications such as ISO or other relevant standards that demonstrate the manufacturer’s commitment to quality. Engaging in trade shows or industry events can provide opportunities to meet suppliers face-to-face, allowing for better relationship-building and negotiation. Additionally, consider leveraging online platforms that specialize in B2B transactions, as these often include supplier ratings and reviews that can guide your decision-making process.
Scenario 2: Inadequate Performance in Specific Applications
The Problem:
Another common pain point for buyers is discovering that the spherical filter screens they purchased do not perform adequately in their intended applications. This situation can arise when the filters are not designed for specific operating conditions, such as temperature fluctuations or varying pressure levels. Buyers may experience increased downtime due to clogging or failure to filter particles effectively, which can severely impact production processes and lead to financial losses.
The Solution:
To address performance issues, buyers should engage in detailed discussions with suppliers about their specific application needs before making a purchase. Providing data on flow rates, particle sizes, and operating conditions can help suppliers recommend the most suitable filter screen options. Additionally, investing in custom filter solutions may be necessary for unique applications, ensuring that the product is tailored to meet specific requirements. Implementing a trial period with the chosen filter screens can also allow for performance evaluation in real-world conditions, enabling adjustments to be made if necessary. Regular monitoring and maintenance of the filter screens will also prolong their life and maintain optimal performance.
Scenario 3: Challenges with Installation and Maintenance of Spherical Filter Screens
The Problem:
B2B buyers often struggle with the installation and ongoing maintenance of spherical filter screens, leading to operational disruptions. This challenge can be exacerbated in regions with limited technical support or training resources. Misaligned installations can result in leaks or inefficiencies, while a lack of understanding of maintenance protocols can lead to premature wear and tear of the filters. Such issues not only increase costs but also can compromise product quality.
The Solution:
To mitigate installation and maintenance challenges, buyers should prioritize suppliers that offer comprehensive support services. This includes access to installation guides, technical training, and customer support. Requesting on-site training for maintenance staff can also be beneficial, ensuring that employees are well-equipped to handle the care of the filter screens. Additionally, utilizing installation tools that simplify the process can help reduce errors and improve alignment. Establishing a maintenance schedule based on manufacturer recommendations will also help in identifying potential issues before they escalate, ensuring that the spherical filter screens operate efficiently over their intended lifespan.
Strategic Material Selection Guide for spheical filter screen
When selecting materials for spherical filter screens, it is critical to consider the specific properties and performance requirements that align with the intended applications. Below, we analyze four common materials used in the manufacturing of spherical filter screens, highlighting their key properties, advantages, disadvantages, and considerations for international B2B buyers.
What Are the Key Properties of Stainless Steel in Spherical Filter Screens?
Stainless Steel is one of the most widely used materials for spherical filter screens due to its excellent mechanical properties and resistance to corrosion. It typically has a temperature rating of up to 800°F (427°C) and can handle high-pressure applications, making it suitable for various industrial processes.
Pros: Stainless steel is highly durable, resistant to rust and corrosion, and has a long lifespan, which reduces replacement costs over time. It is also easy to clean and maintain, making it ideal for applications requiring hygiene, such as food and beverage processing.
Cons: The primary drawback is its higher initial cost compared to other materials. Additionally, stainless steel can be more challenging to manufacture into complex shapes, which may increase production lead times.
Impact on Application: Stainless steel is compatible with a wide range of media, including water, chemicals, and oils, making it versatile across industries such as petrochemical, pharmaceuticals, and food processing.
Considerations for International Buyers: Buyers from regions like Africa and South America should ensure compliance with local standards, such as ASTM or DIN, particularly in industries with strict regulations. European buyers may prefer specific grades of stainless steel that meet EU standards for food safety.
How Does Polypropylene Perform as a Material for Spherical Filter Screens?
Polypropylene is a thermoplastic polymer known for its lightweight and chemical resistance. It can withstand temperatures up to 200°F (93°C) and is suitable for low-pressure applications.
Pros: The main advantage of polypropylene is its low cost and ease of fabrication, allowing for rapid production of complex shapes. It is also resistant to many acids and bases, making it suitable for various chemical applications.
Cons: However, polypropylene has lower mechanical strength compared to metals and can degrade under UV exposure, limiting its use in outdoor applications. Its temperature and pressure limitations may also restrict its use in high-demand environments.
Impact on Application: Polypropylene is ideal for applications involving non-aggressive media, such as water filtration and certain chemical processes. It is not suitable for high-temperature or high-pressure applications.
Considerations for International Buyers: Buyers should verify compliance with local regulations regarding plastic materials, especially in food and beverage applications. In regions like the Middle East, where high temperatures are common, the material’s limitations should be carefully evaluated.
What Are the Advantages of Using Carbon Steel for Spherical Filter Screens?
Carbon Steel is another common material, particularly in industrial applications. It offers good strength and can handle pressures up to 1500 psi, with temperature ratings around 400°F (204°C).
Pros: Carbon steel is relatively inexpensive and provides good mechanical properties, making it suitable for heavy-duty applications. It can be easily welded and fabricated into various shapes.
Cons: The main disadvantage is its susceptibility to corrosion, which can lead to premature failure in harsh environments unless properly coated or treated. This may increase long-term maintenance costs.
Impact on Application: Carbon steel is suitable for applications involving water and some oils but should be avoided in corrosive environments unless protective measures are taken.
Considerations for International Buyers: Buyers in Europe and South America should consider compliance with corrosion resistance standards, particularly for applications in humid or corrosive environments. Proper coatings may be required to meet local regulations.
What Makes Titanium a Premium Choice for Spherical Filter Screens?
Titanium is a premium material known for its exceptional strength-to-weight ratio and corrosion resistance. It can withstand temperatures up to 1200°F (649°C) and is suitable for high-pressure applications.
Pros: The key advantage of titanium is its longevity and resistance to corrosion, making it ideal for harsh environments, including marine and chemical processing applications. Its lightweight nature also aids in reducing overall system weight.
Cons: The primary limitation is the high cost of titanium, which can be prohibitive for some applications. Additionally, the manufacturing process is more complex, leading to longer lead times.
Impact on Application: Titanium is compatible with aggressive media, including seawater and strong acids, making it ideal for specialized applications in aerospace, marine, and chemical industries.
Considerations for International Buyers: Buyers should be aware of the high costs associated with titanium and ensure that the benefits justify the investment. Compliance with international standards for aerospace and marine applications is crucial.
Summary Table of Material Selection for Spherical Filter Screens
Material | Typical Use Case for Spherical Filter Screen | Key Advantage | Key Disadvantage/Limitation | Relative Cost (Low/Med/High) |
---|---|---|---|---|
Stainless Steel | Food processing, petrochemical industries | High durability and corrosion resistance | Higher initial cost | High |
Polypropylene | Water filtration, non-aggressive chemicals | Low cost and easy fabrication | Limited temperature and pressure ratings | Low |
Carbon Steel | Heavy-duty industrial applications | Good strength and low cost | Susceptible to corrosion | Medium |
Titanium | Marine and aerospace applications | Exceptional strength and corrosion resistance | High cost and complex manufacturing | High |
This guide provides a comprehensive overview of material options for spherical filter screens, enabling international B2B buyers to make informed decisions based on their specific needs and regional considerations.
In-depth Look: Manufacturing Processes and Quality Assurance for spheical filter screen
What Are the Main Stages of Manufacturing a Spherical Filter Screen?
The manufacturing process of spherical filter screens involves several critical stages, each contributing to the overall quality and performance of the final product. Understanding these stages is essential for B2B buyers looking for reliable suppliers.
1. Material Preparation
The first step in manufacturing spherical filter screens is the selection and preparation of raw materials. Common materials include stainless steel, carbon steel, and specialized alloys, chosen for their durability and resistance to corrosion. The preparation process involves cutting raw materials into precise dimensions and treating them to enhance their properties. Buyers should inquire about the source and quality of materials used, as this can impact the filter screen’s lifespan and effectiveness.
2. Forming Techniques
Forming is a crucial stage where the prepared materials are shaped into the desired spherical form. Techniques include:
- Deep Drawing: A process where a flat sheet is transformed into a three-dimensional shape. This method is widely used for its ability to produce complex geometries with minimal waste.
- Metal Injection Molding (MIM): Ideal for producing intricate designs in high volumes. MIM combines metal powder with a binding agent, which is then shaped and sintered to create a solid product.
Buyers should assess the forming techniques employed by potential suppliers, as these directly affect the structural integrity and performance of the filter screens.
3. Assembly Processes
After forming, the components of the spherical filter screen are assembled. This may include welding or mechanical fastening of various parts. Assembly techniques must ensure that the final product is both robust and capable of withstanding operational stresses. B2B buyers should verify that suppliers have standardized assembly processes in place to ensure consistency across production batches.
4. Finishing Touches
The finishing stage involves surface treatments that enhance performance and longevity. Common finishing techniques include:
- Electropolishing: This process removes surface impurities and creates a smooth finish, which is crucial for applications requiring high cleanliness.
- Coating: Additional coatings may be applied for extra corrosion resistance or to meet specific regulatory requirements.
Buyers should ask suppliers about their finishing processes and whether they comply with international standards, as this can significantly impact the usability of the filter screens in various environments.
How Is Quality Assurance Integrated into the Manufacturing of Spherical Filter Screens?
Quality assurance (QA) is an integral aspect of the manufacturing process, ensuring that the final product meets both regulatory and customer-specific standards.
What International Standards Should B2B Buyers Be Aware Of?
When sourcing spherical filter screens, buyers should familiarize themselves with relevant international quality standards. Some key standards include:
- ISO 9001: This standard outlines the criteria for a quality management system and is applicable to any organization. Suppliers certified under ISO 9001 demonstrate their commitment to quality and customer satisfaction.
- CE Marking: Particularly important for products sold in the European market, CE marking indicates that the product meets EU safety and health requirements.
- API Standards: For applications in the oil and gas industry, suppliers may need to comply with specific American Petroleum Institute (API) standards.
Understanding these certifications helps buyers select suppliers who prioritize quality and compliance.
What Are the Key Quality Control Checkpoints?
Quality control (QC) checkpoints are essential for ensuring that the manufacturing process remains within set tolerances. Key checkpoints include:
- Incoming Quality Control (IQC): At this stage, raw materials are inspected for defects before they enter the production line. Buyers should inquire about the supplier’s IQC processes to ensure only high-quality materials are used.
- In-Process Quality Control (IPQC): During manufacturing, ongoing inspections are conducted to identify defects early in the process. This proactive approach can save time and resources.
- Final Quality Control (FQC): Once the product is completed, FQC checks ensure that the final product meets all specifications before shipment.
Buyers should request documentation that outlines the QC processes and results from their suppliers.
What Testing Methods Are Commonly Used for Spherical Filter Screens?
Testing methods play a crucial role in verifying the performance and reliability of spherical filter screens. Common methods include:
- Hydrostatic Testing: This method involves subjecting the filter screen to high-pressure water to check for leaks and structural integrity.
- Filtration Efficiency Testing: This assesses how well the filter screen performs under operational conditions, determining its effectiveness in separating particulates.
- Fatigue Testing: Particularly important for screens used in high-stress environments, this test evaluates the material’s durability over time.
Buyers should ask potential suppliers about their testing protocols and whether they use third-party laboratories for unbiased results.
How Can B2B Buyers Verify Supplier Quality Control?
Verifying a supplier’s quality control measures is essential for international B2B buyers. Here are several actionable steps:
- Conduct Audits: Regular audits of suppliers can provide insights into their manufacturing processes and adherence to quality standards. Buyers should establish a schedule for these audits, particularly for new suppliers.
- Request Quality Reports: Suppliers should be able to provide documentation demonstrating their compliance with international standards and the results of their QC processes.
- Engage Third-Party Inspectors: Utilizing independent inspection services can offer an additional layer of assurance regarding the quality of the products being sourced.
What Nuances Should Buyers Consider Regarding QC and Certification?
For buyers from regions such as Africa, South America, the Middle East, and Europe, it is crucial to understand the nuances of quality control and certification:
- Local Regulations: Different regions may have specific regulations regarding product standards. Buyers should be aware of these to ensure compliance.
- Cultural Differences: Understanding the local business culture can aid in building stronger relationships with suppliers, which may enhance transparency and cooperation regarding quality assurance.
- Supply Chain Considerations: The complexity of international supply chains can introduce risks. Buyers should evaluate the entire supply chain’s reliability, including logistics and warehousing.
By taking these factors into account, B2B buyers can make informed decisions when sourcing spherical filter screens, ensuring they partner with suppliers committed to quality and compliance.
Practical Sourcing Guide: A Step-by-Step Checklist for ‘spheical filter screen’
Introduction
Sourcing a spherical filter screen requires a strategic approach to ensure you acquire high-quality products that meet your specific operational needs. This step-by-step checklist is designed to guide international B2B buyers, particularly from Africa, South America, the Middle East, and Europe, through the essential stages of the procurement process. By following these actionable steps, you can streamline your sourcing efforts and establish reliable supplier relationships.
Step 1: Define Your Technical Specifications
Clearly outlining your technical specifications is the cornerstone of effective sourcing. Consider the material type, mesh size, and dimensions required for your specific application.
- Material Considerations: Different materials, such as stainless steel or nylon, offer varied durability and performance characteristics.
- Performance Criteria: Understand the operational conditions, such as temperature and pressure, to ensure compatibility with your requirements.
Step 2: Conduct Market Research for Suppliers
Before reaching out to potential suppliers, conduct thorough market research. This helps identify companies that specialize in spherical filter screens and have a proven track record.
- Industry Directories: Utilize online directories and trade associations relevant to your industry to find reputable suppliers.
- Local vs. International: Consider the benefits of sourcing locally versus internationally, including cost, shipping time, and support services.
Step 3: Evaluate Potential Suppliers
Before committing, it’s crucial to vet suppliers thoroughly. Request company profiles, case studies, and references from buyers in a similar industry or region.
- Company Reputation: Look for reviews and testimonials that speak to the supplier’s reliability and product quality.
- Experience in Your Market: Ensure the supplier has experience working with businesses in your region to facilitate smoother transactions.
Step 4: Verify Certifications and Compliance
Ensure that the suppliers you consider meet all relevant industry standards and certifications. This step is critical to guarantee product quality and regulatory compliance.
- ISO Certifications: Check for ISO certifications that reflect adherence to quality management standards.
- Regional Compliance: Familiarize yourself with any regional regulations that may impact the use of filter screens in your industry.
Step 5: Request Samples for Testing
Before making a bulk purchase, request samples of the spherical filter screens you are considering. This allows you to assess quality firsthand.
- Testing for Performance: Evaluate the samples under actual working conditions to ensure they meet your performance expectations.
- Quality Control: Observe the manufacturing quality and workmanship to identify any potential issues early on.
Step 6: Negotiate Terms and Conditions
Once you have selected a supplier, engage in negotiations to clarify terms and conditions. This includes pricing, payment terms, delivery schedules, and after-sales support.
- Transparent Pricing: Ensure all costs are detailed, including shipping and potential tariffs for international orders.
- Flexibility in Orders: Discuss minimum order quantities and the potential for future purchases to establish a long-term partnership.
Step 7: Establish a Communication Plan
Finally, set up a clear communication plan with your chosen supplier. Effective communication is essential to ensure a smooth procurement process and resolve any issues that may arise.
- Regular Updates: Agree on how frequently you will receive updates on order status and any potential delays.
- Point of Contact: Designate a point of contact for both parties to streamline communication and address concerns promptly.
By following this checklist, B2B buyers can effectively navigate the sourcing process for spherical filter screens, ensuring they make informed decisions that align with their operational needs.
Comprehensive Cost and Pricing Analysis for spheical filter screen Sourcing
When sourcing spherical filter screens, understanding the comprehensive cost structure and pricing analysis is crucial for international B2B buyers. This section delves into the essential cost components, price influencers, and practical buyer tips to enhance decision-making.
What Are the Key Cost Components for Spherical Filter Screens?
The cost structure for spherical filter screens can be broken down into several key components:
-
Materials: The primary material used in manufacturing spherical filter screens significantly impacts the overall cost. Common materials include stainless steel, polymers, and specialized alloys. The choice of material not only affects durability but also the filtration efficiency.
-
Labor: Labor costs vary by region and can be influenced by local wage standards, skill levels, and labor availability. In regions like Africa and South America, labor costs may be lower compared to Europe, but quality and expertise can also vary.
-
Manufacturing Overhead: This encompasses the indirect costs associated with production, such as utilities, rent, and equipment depreciation. Efficient manufacturing processes can help minimize these overheads, ultimately lowering the product price.
-
Tooling: Custom tooling for specific filter screen designs can be a significant upfront investment. However, it can lead to cost savings in mass production by improving efficiency and reducing scrap rates.
-
Quality Control (QC): Implementing robust QC measures ensures product reliability and compliance with industry standards. While this may increase initial costs, it can prevent costly recalls and reputational damage.
-
Logistics: Shipping and handling costs can vary greatly depending on the shipping method, distance, and customs duties. Understanding Incoterms is essential for buyers to determine who is responsible for various logistics costs.
-
Margin: Supplier margins can fluctuate based on market demand, competition, and the supplier’s strategic positioning. Buyers should expect to negotiate margins, especially for large orders.
How Do Price Influencers Affect Spherical Filter Screen Costs?
Several factors can influence the pricing of spherical filter screens:
-
Volume/MOQ (Minimum Order Quantity): Suppliers often provide discounts for bulk purchases. Understanding the MOQ can lead to significant cost savings, especially for large-scale projects.
-
Specifications and Customization: Custom specifications can lead to increased costs due to the complexity of manufacturing. Buyers should weigh the benefits of customization against potential price increases.
-
Material Quality and Certifications: Higher-quality materials and industry certifications (like ISO) can enhance product reliability but may also increase the price. Buyers should evaluate the necessity of these factors based on their application needs.
-
Supplier Factors: The reputation, location, and financial stability of suppliers can all impact pricing. Established suppliers may charge a premium for their reliability, while emerging suppliers might offer competitive pricing to gain market share.
-
Incoterms: The choice of Incoterms can significantly affect total costs. Terms like FOB (Free on Board) or CIF (Cost, Insurance, and Freight) dictate who bears the shipping costs and risks, influencing the overall pricing structure.
What Are the Best Practices for Negotiating Prices in Spherical Filter Screen Sourcing?
-
Conduct Thorough Market Research: Understanding the prevailing market rates for spherical filter screens can provide leverage during negotiations. Compare prices from multiple suppliers to identify competitive offers.
-
Focus on Total Cost of Ownership (TCO): Instead of just considering the upfront cost, evaluate the long-term costs associated with maintenance, replacement, and potential downtime. A slightly higher initial investment may result in lower TCO.
-
Be Prepared to Negotiate Terms: Leverage volume purchases to negotiate better terms, including pricing, payment terms, and shipping costs. Don’t hesitate to ask for discounts or additional services like extended warranties.
-
Consider Regional Variations: For buyers in Africa, South America, the Middle East, and Europe, understanding local economic conditions can provide insights into potential cost fluctuations. Currency exchange rates and local tariffs may also play a role in final pricing.
-
Stay Informed on Pricing Trends: Keep abreast of market trends and fluctuations in material costs. This knowledge can help in anticipating price increases or identifying optimal times to purchase.
Conclusion
Sourcing spherical filter screens involves navigating a complex landscape of costs and pricing influencers. By understanding the cost structure, leveraging negotiation tactics, and focusing on total cost of ownership, international B2B buyers can make informed purchasing decisions that align with their operational needs and budget constraints.
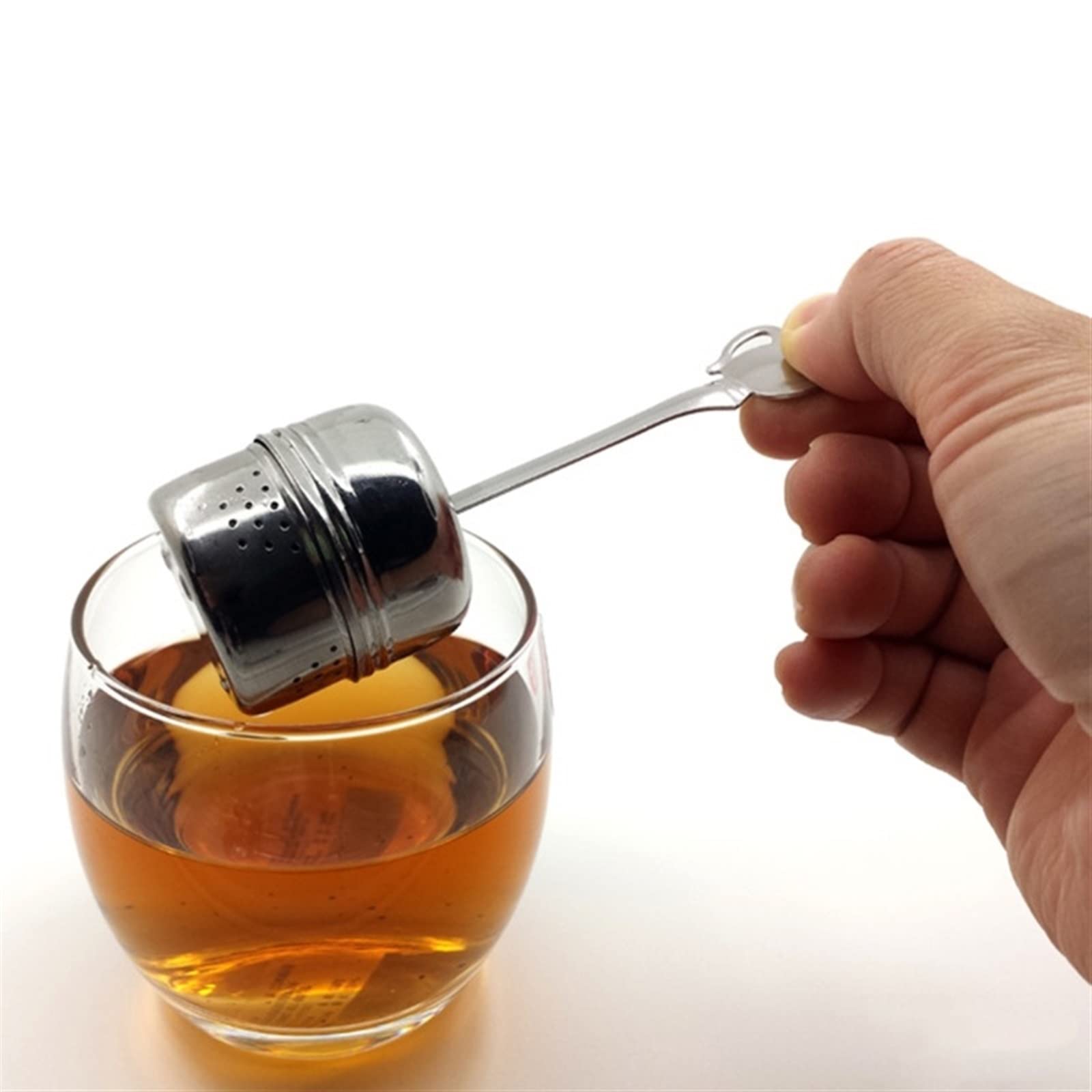
A stock image related to spheical filter screen.
Alternatives Analysis: Comparing spheical filter screen With Other Solutions
When evaluating filtration solutions, it’s crucial to understand the alternatives available in the market. The spherical filter screen is one such option, but various alternatives exist that might better suit specific needs or applications. This section compares the spherical filter screen with two viable alternatives: traditional mesh filters and automatic backwash filters, helping international B2B buyers make informed decisions.
Comparison Aspect | Spherical Filter Screen | Traditional Mesh Filter | Automatic Backwash Filter |
---|---|---|---|
Performance | High filtration efficiency, low pressure loss | Moderate efficiency, prone to clogging | High efficiency, self-cleaning mechanism |
Cost | Moderate initial investment, low long-term costs | Low initial cost, higher maintenance costs | Higher initial investment, low maintenance |
Ease of Implementation | Requires custom installation | Simple installation process | More complex installation, may require modifications |
Maintenance | Low maintenance; periodic cleaning needed | High maintenance; frequent replacement needed | Low maintenance; self-cleaning feature |
Best Use Case | Ideal for fine filtration in industries like pharmaceuticals | Suitable for general applications, low-cost solutions | Best for continuous operations with high solids content |
What are the advantages and disadvantages of traditional mesh filters compared to spherical filter screens?
Traditional mesh filters are often used for their cost-effectiveness and ease of installation. They provide a decent level of filtration but can be prone to clogging, particularly in applications with high levels of particulate matter. The maintenance requirements can be significant, as frequent replacements may be necessary, leading to higher long-term costs. They are best suited for general applications where budget constraints are a priority and the level of filtration required is moderate.
How do automatic backwash filters stack up against spherical filter screens?
Automatic backwash filters offer a self-cleaning mechanism, making them an attractive option for operations that require continuous filtration without interruption. They boast high filtration efficiency and are particularly effective in applications with high solids content. However, they come with a higher initial investment and more complex installation requirements. For businesses with a steady flow of contaminants and the need for consistent filtration, automatic backwash filters can be a great choice, albeit with a steeper upfront cost.
How can B2B buyers choose the right filtration solution for their needs?
When selecting a filtration solution, B2B buyers should consider several factors, including the specific application requirements, budget constraints, and maintenance capabilities. The spherical filter screen is an excellent choice for fine filtration with low maintenance, while traditional mesh filters may suffice for simpler applications with lower costs. For operations needing continuous filtration, automatic backwash filters are ideal despite the higher initial investment. Ultimately, understanding the unique needs of your operation and weighing the pros and cons of each solution will guide you to the most suitable filtration method.
Essential Technical Properties and Trade Terminology for spheical filter screen
What Are the Key Technical Properties of Spherical Filter Screens?
When sourcing spherical filter screens, understanding their technical properties is essential for making informed purchasing decisions. Here are some critical specifications to consider:
-
Material Grade
The material used in the construction of spherical filter screens significantly affects their durability and performance. Common materials include stainless steel, polypropylene, and nylon. For instance, stainless steel offers excellent corrosion resistance and strength, making it suitable for high-temperature applications. Buyers should consider the environmental conditions and the type of fluids being filtered to select the appropriate material grade. -
Mesh Size
Mesh size determines the filtration efficiency of the spherical filter screen. It is measured in microns and indicates the size of particles that can pass through. A finer mesh captures smaller particles but may require more frequent cleaning. Understanding the specific filtration needs of your application will guide you in selecting the right mesh size, ensuring optimal performance and longevity of the filter. -
Tolerance
Tolerance refers to the permissible limits of variation in the dimensions of the filter screen. High tolerance levels are crucial for ensuring proper fit and function within a filtration system. This is particularly important in industries such as pharmaceuticals and food processing, where precision is critical. Buyers should request tolerance specifications to ensure compatibility with their equipment. -
Flow Rate
The flow rate indicates the volume of fluid that can pass through the filter screen in a given time. This property is essential for ensuring that the filtration system operates efficiently without causing pressure drops. Understanding the required flow rate for your application helps in selecting the right spherical filter screen to maintain system performance. -
Temperature Resistance
Different applications may expose spherical filter screens to varying temperature ranges. Assessing the temperature resistance of the material is vital for ensuring that the filter screen does not deform or degrade under operational conditions. This property is particularly relevant in industries such as oil and gas, where high temperatures are common.
What Are Common Trade Terms Used in the Spherical Filter Screen Industry?
Familiarity with industry terminology can streamline the purchasing process and enhance communication with suppliers. Here are some essential trade terms:
-
OEM (Original Equipment Manufacturer)
OEM refers to companies that produce components or products that are used in another company’s end product. In the context of spherical filter screens, buyers may seek OEM suppliers for customized solutions that fit specific operational needs. Understanding the OEM landscape helps buyers identify reliable partners for tailored filtration solutions. -
MOQ (Minimum Order Quantity)
MOQ is the smallest quantity of a product that a supplier is willing to sell. This term is crucial for budgeting and inventory management. For international buyers, knowing the MOQ can influence purchasing decisions, especially when dealing with suppliers from different regions. It is advisable to discuss MOQs upfront to avoid potential delays. -
RFQ (Request for Quotation)
An RFQ is a formal document sent to suppliers requesting pricing and terms for specified products. When purchasing spherical filter screens, submitting an RFQ allows buyers to compare offers from multiple suppliers, ensuring they get the best value. Providing detailed specifications in the RFQ can lead to more accurate quotes. -
Incoterms (International Commercial Terms)
Incoterms define the responsibilities of buyers and sellers in international transactions, including shipping, insurance, and tariffs. Familiarity with these terms can help buyers understand their obligations and rights, reducing the risk of unexpected costs. Common Incoterms include FOB (Free On Board) and CIF (Cost, Insurance, and Freight), which clarify who bears the risk at various stages of the shipping process. -
Lead Time
Lead time refers to the time taken from placing an order to the delivery of the product. This term is vital for planning and inventory management. Understanding lead times from different suppliers can help buyers make strategic decisions about when to place orders to avoid production delays.
By grasping these technical properties and trade terms, B2B buyers can make better-informed decisions when sourcing spherical filter screens, ultimately enhancing their operational efficiency and cost-effectiveness.
Navigating Market Dynamics and Sourcing Trends in the spheical filter screen Sector
What Are the Current Market Dynamics in the Spherical Filter Screen Sector?
The spherical filter screen market is evolving rapidly, driven by several global factors. Increased industrialization and a growing emphasis on clean water and air have heightened the demand for effective filtration solutions. This demand is particularly pronounced in emerging markets like Africa and South America, where industrial growth and urbanization are accelerating. Furthermore, advancements in materials science are leading to more efficient and durable filter screens, enhancing their performance across various applications.
International B2B buyers should be aware of the trend towards automation and digitalization in sourcing processes. Platforms that facilitate real-time procurement, such as e-marketplaces, are becoming essential for buyers looking to streamline their operations. Additionally, the rise of Industry 4.0 is influencing the design and manufacture of spherical filter screens, integrating IoT capabilities for better monitoring and maintenance. Buyers in Europe and the Middle East should also consider the regulatory landscape, as stricter environmental regulations are pushing suppliers to innovate and comply with higher standards.
How Does Sustainability Impact Sourcing in the Spherical Filter Screen Sector?
Sustainability has become a central theme in the sourcing strategies of international B2B buyers. In the spherical filter screen sector, the environmental impact of production processes and materials used is under scrutiny. Buyers are increasingly prioritizing suppliers who adopt sustainable practices, including the use of recycled materials and energy-efficient manufacturing processes.
Ethical sourcing is also gaining traction, with businesses recognizing the importance of transparent supply chains. This involves ensuring that materials are sourced from suppliers that adhere to fair labor practices and environmental regulations. Certifications like ISO 14001 (Environmental Management) and the Global Recycled Standard are valuable indicators of a supplier’s commitment to sustainability. Buyers from Africa and South America, in particular, are urged to assess these certifications as they align with global sustainability goals, thereby enhancing their brand reputation and compliance with international standards.
What Is the Evolution of the Spherical Filter Screen Technology?
The evolution of spherical filter screens can be traced back to the increasing need for efficient filtration solutions across various industries. Initially, these screens were simple mesh designs, primarily used in water treatment applications. Over time, technological advancements have led to the development of sophisticated materials and designs that enhance filtration efficiency and durability.
The introduction of advanced materials such as stainless steel, polymers, and composite materials has significantly improved the performance of spherical filter screens. Moreover, innovations in manufacturing techniques, such as 3D printing, have enabled the creation of complex geometries that optimize fluid flow and particle capture. As international B2B buyers navigate the current market, understanding the historical context of these advancements can provide insights into future trends and opportunities for investment in cutting-edge filtration solutions.
Frequently Asked Questions (FAQs) for B2B Buyers of spheical filter screen
-
How do I choose the right spherical filter screen for my application?
Choosing the appropriate spherical filter screen involves assessing your specific filtration requirements. Consider factors such as the type of material being filtered, the required mesh size, and the operational conditions like temperature and pressure. It’s also essential to evaluate the screen’s compatibility with your existing machinery. Engaging with suppliers who offer expert guidance can help you make an informed decision. Request samples or prototypes to test performance before committing to a bulk order. -
What are the benefits of using a spherical filter screen in industrial applications?
Spherical filter screens provide several advantages, including enhanced filtration efficiency and reduced clogging due to their unique shape. Their design allows for better flow dynamics, which can lead to improved productivity and lower maintenance costs. Additionally, these screens often have a longer lifespan compared to traditional flat screens, resulting in lower replacement frequency and overall cost savings. Understanding these benefits can help you justify the investment to stakeholders within your organization. -
What customization options are available for spherical filter screens?
Many manufacturers offer customization options for spherical filter screens to meet specific operational needs. Customizations can include variations in mesh size, materials (such as stainless steel or polymer), and dimensions to fit particular equipment. Some suppliers can even provide coatings or treatments for enhanced corrosion resistance or specific chemical compatibility. Discuss your unique requirements with potential suppliers to ensure you receive a product tailored to your application. -
What is the minimum order quantity (MOQ) for spherical filter screens?
The MOQ for spherical filter screens can vary significantly depending on the supplier and the complexity of the product. Some manufacturers may have a low MOQ for standard models, while custom designs might require a higher minimum. It’s essential to clarify these details during initial discussions to avoid any misunderstandings later. If your needs are for smaller quantities, consider negotiating with suppliers or looking for those who specialize in low-volume orders. -
What payment terms should I expect when purchasing spherical filter screens internationally?
Payment terms for international purchases of spherical filter screens typically range from upfront payments to net 30 or net 60 terms, depending on the supplier’s policies and your relationship with them. Common methods include wire transfers, letters of credit, and payment platforms like PayPal. Always ensure that the payment method is secure and that you understand any fees associated with international transactions. Establishing clear terms in the contract can help avoid disputes later. -
How can I vet suppliers of spherical filter screens for reliability and quality?
To vet suppliers effectively, start by researching their reputation in the industry. Look for customer reviews, case studies, and references from other businesses. Request certifications that demonstrate adherence to international quality standards, such as ISO 9001. Additionally, consider visiting their manufacturing facilities if possible or utilizing third-party inspection services. Engaging in direct communication can also provide insights into their responsiveness and customer service. -
What quality assurance measures should I expect from suppliers of spherical filter screens?
Reputable suppliers of spherical filter screens should implement rigorous quality assurance (QA) measures throughout the production process. This includes incoming material inspections, in-process testing, and final product evaluations against specified criteria. Ask potential suppliers about their QA protocols, including any certifications or testing methodologies they use. A strong QA program not only ensures product reliability but also reduces the risk of operational disruptions in your processes. -
What logistics considerations should I keep in mind when importing spherical filter screens?
When importing spherical filter screens, logistics considerations include shipping methods, customs duties, and delivery timelines. Choose a reliable freight forwarder familiar with international trade regulations in your region. Understand the total landed cost, which includes shipping, insurance, and any tariffs. Ensure that your supplier provides all necessary documentation, such as invoices and packing lists, to facilitate smooth customs clearance. Additionally, plan for potential delays in transit to avoid operational interruptions.
Important Disclaimer & Terms of Use
⚠️ Important Disclaimer
The information provided in this guide, including content regarding manufacturers, technical specifications, and market analysis, is for informational and educational purposes only. It does not constitute professional procurement advice, financial advice, or legal advice.
While we have made every effort to ensure the accuracy and timeliness of the information, we are not responsible for any errors, omissions, or outdated information. Market conditions, company details, and technical standards are subject to change.
B2B buyers must conduct their own independent and thorough due diligence before making any purchasing decisions. This includes contacting suppliers directly, verifying certifications, requesting samples, and seeking professional consultation. The risk of relying on any information in this guide is borne solely by the reader.
Strategic Sourcing Conclusion and Outlook for spheical filter screen
In the dynamic landscape of international sourcing for spherical filter screens, strategic sourcing emerges as a critical approach for B2B buyers. By leveraging a comprehensive understanding of supplier capabilities, market trends, and technological advancements, businesses can enhance their procurement strategies, ultimately driving efficiency and cost-effectiveness. Key takeaways include the importance of building strong supplier relationships, embracing innovation in filtration technology, and remaining adaptable to the evolving demands of global markets.
How can businesses in Africa, South America, the Middle East, and Europe optimize their sourcing strategies for spherical filter screens? The answer lies in cultivating a proactive sourcing mindset. Engage with suppliers who not only meet quality standards but also align with your sustainability goals and operational needs. Moreover, consider regional suppliers to reduce lead times and foster local economies.
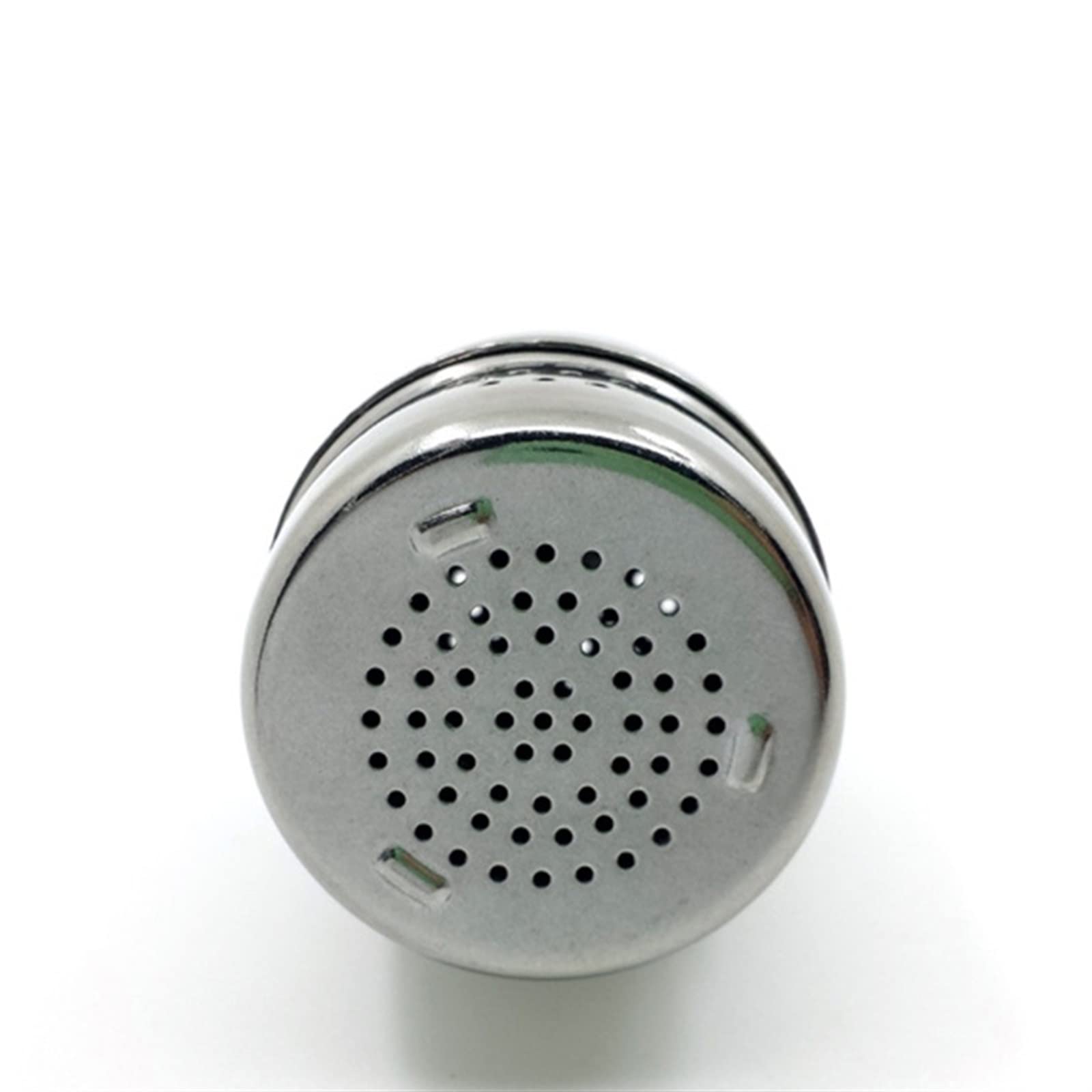
A stock image related to spheical filter screen.
As we look toward the future, the demand for high-performance filtration solutions will continue to grow. Now is the time for international B2B buyers to evaluate their sourcing strategies, invest in long-term partnerships, and prioritize innovation. Embrace the opportunities ahead, and position your business as a leader in the filtration industry.