Enhance Efficiency: The Ultimate Cement Mixer Mixer Guide (2025)
Introduction: Navigating the Global Market for cement mixer mixer
In today’s competitive construction landscape, sourcing the right cement mixer mixer can be a daunting task for international B2B buyers. With a multitude of options available, each with varying specifications and price points, making an informed decision is crucial. This guide aims to demystify the complexities of the global market for cement mixer mixers, providing a comprehensive overview of different types, their applications, and key considerations for supplier vetting.
As the demand for efficient construction equipment continues to rise across regions like Africa, South America, the Middle East, and Europe—including markets in Australia and the UK—buyers must navigate challenges such as fluctuating costs, varying regulatory standards, and logistical hurdles. This guide equips B2B buyers with actionable insights to streamline their purchasing process, ensuring they select the most suitable mixers for their specific needs.
By addressing critical factors such as performance, durability, and operational efficiency, this resource empowers buyers to make strategic decisions that align with their project requirements and budget constraints. Whether you are a contractor seeking reliable equipment for large-scale projects or a small business looking to enhance your service offerings, understanding the nuances of cement mixer mixers will enable you to invest wisely and drive success in your operations.
Understanding cement mixer mixer Types and Variations
Type Name | Key Distinguishing Features | Primary B2B Applications | Brief Pros & Cons for Buyers |
---|---|---|---|
Drum Mixer | Rotating drum design, suitable for small to medium batches | Construction sites, small-scale projects | Pros: Affordable, portable; Cons: Limited mixing capacity, inconsistent mixing quality. |
Twin-Shaft Mixer | Two horizontal shafts for efficient mixing, high output | Large-scale construction, precast concrete plants | Pros: High mixing efficiency, uniform consistency; Cons: Higher initial investment, requires more maintenance. |
Pan Mixer | Flat mixing pan with a central mixing blade, versatile | Concrete batching plants, block-making facilities | Pros: Effective for dry mixes, quick batch changes; Cons: Not ideal for wet mixes, limited capacity. |
Vertical Shaft Mixer | Vertical axis of rotation, suitable for high-viscosity materials | Heavy-duty applications, refractory materials | Pros: Excellent for thick mixtures, minimal segregation; Cons: Requires more space, higher energy consumption. |
Mobile Mixer | Portable and self-contained unit, often truck-mounted | Remote construction sites, on-demand concrete needs | Pros: Flexibility, reduced transportation costs; Cons: Limited batch size, potential for operator error. |
What Are the Characteristics of a Drum Mixer?
Drum mixers are one of the most common types used in construction. They feature a rotating drum that mixes the concrete as it turns, making them suitable for small to medium batches. Their simplicity and affordability make them a popular choice for smaller contractors or DIY projects. However, buyers should consider that while they are portable, the mixing quality can be inconsistent, particularly with larger volumes.
When Should You Use a Twin-Shaft Mixer?
Twin-shaft mixers are designed for high efficiency and output, employing two parallel shafts that rotate in opposite directions to ensure thorough mixing. They are particularly well-suited for large-scale construction projects, including the production of precast concrete. While they provide uniform consistency and high productivity, the initial investment is higher, and they may require more maintenance, which is crucial for B2B buyers to factor into their budget.
What Makes a Pan Mixer Versatile?
Pan mixers are characterized by their flat mixing pans and central mixing blades, making them versatile for various applications, particularly in concrete batching plants and block-making facilities. They excel in mixing dry materials and allow for quick batch changes. However, they may not perform as well with wet mixes and have limited capacity, which can be a drawback for larger operations.
Why Choose a Vertical Shaft Mixer for Heavy-Duty Applications?
Vertical shaft mixers are ideal for heavy-duty applications, especially those involving high-viscosity materials. Their design minimizes segregation and ensures a thorough mix, making them suitable for refractory materials and other specialized concrete mixes. While they offer significant advantages in mixing thick materials, they require more space and can consume more energy, which are important considerations for B2B buyers with specific operational constraints.
How Do Mobile Mixers Benefit Remote Construction Sites?
Mobile mixers are truck-mounted units that allow for on-demand concrete mixing at remote construction sites. Their portability and self-contained nature reduce transportation costs and provide flexibility in operations. However, they often have a limited batch size and may be prone to operator error. Buyers should evaluate the specific needs of their projects to determine if a mobile mixer aligns with their operational strategy.
Related Video: How to Mix Cement and Concrete with a Cement Mixer
Key Industrial Applications of cement mixer mixer
Industry/Sector | Specific Application of cement mixer mixer | Value/Benefit for the Business | Key Sourcing Considerations for this Application |
---|---|---|---|
Construction | Mixing concrete for building foundations | Ensures high-quality, uniform concrete | Durability, capacity, and energy efficiency of the mixer |
Road Infrastructure | Producing concrete for road pavements | Enhances durability and longevity of roads | Size, mobility, and maintenance support for remote areas |
Precast Concrete Production | Preparing concrete for precast elements | Streamlines production and reduces waste | Adaptability to various mix designs and ease of use |
Mining and Quarrying | Mixing cement for stabilizing soil and rock | Improves site safety and operational efficiency | Resistance to harsh environments and ease of transport |
Agriculture | Mixing soil amendments and fertilizers | Enhances crop yield and soil quality | Compatibility with various materials and ease of cleaning |
How is Cement Mixer Mixer Used in the Construction Industry?
In the construction sector, cement mixer mixers are crucial for mixing concrete used in building foundations, walls, and slabs. The mixers ensure a consistent and high-quality concrete mix, which is vital for structural integrity. International buyers in this sector must consider the mixer’s capacity to handle large volumes, energy efficiency, and durability, especially in regions with varying climates, such as Africa and South America, where equipment may face extreme conditions.
What Role Does a Cement Mixer Mixer Play in Road Infrastructure?
Cement mixer mixers are extensively used in producing concrete for road pavements. This application is critical as it enhances the durability and longevity of roads, reducing the frequency of repairs. Buyers should focus on sourcing mixers that are mobile and capable of mixing large batches to meet the demands of extensive road projects, particularly in developing regions in the Middle East and Africa where infrastructure development is booming.
How is Cement Mixer Mixer Utilized in Precast Concrete Production?
In the precast concrete industry, cement mixer mixers streamline the production of concrete elements such as beams, columns, and panels. By ensuring a uniform mix, these mixers help reduce waste and improve the overall efficiency of the production process. Buyers should seek mixers that can adapt to various mix designs and are easy to operate, which is particularly important in European markets where precision and compliance with standards are paramount.
What Applications Exist for Cement Mixer Mixer in Mining and Quarrying?
Cement mixer mixers are employed in mining and quarrying to mix cement with soil and rock for stabilization purposes. This application enhances safety and operational efficiency at mining sites. Buyers in this sector should consider mixers that are resistant to harsh environments, easy to transport, and capable of handling various material types, especially in remote areas of South America and Africa where accessibility is a challenge.
How Can Cement Mixer Mixer Benefit Agricultural Practices?
In agriculture, cement mixer mixers are used to mix soil amendments and fertilizers, improving soil quality and enhancing crop yields. This application is vital for sustainable farming practices. Buyers should prioritize mixers that are compatible with different materials and easy to clean, ensuring versatility in use. This is particularly important in Europe, where organic farming practices are gaining traction, necessitating equipment that can handle a variety of organic amendments.
Related Video: Cement Mixer Truck Pouring Concrete Pad
3 Common User Pain Points for ‘cement mixer mixer’ & Their Solutions
Scenario 1: Navigating Supply Chain Disruptions in Cement Mixer Mixer Procurement
The Problem:
For international B2B buyers, particularly in Africa and South America, sourcing cement mixer mixers can be fraught with challenges stemming from supply chain disruptions. This is especially true during periods of geopolitical instability or global pandemics when shipping delays and increased freight costs can significantly impact project timelines. Buyers often find themselves in a precarious position where their construction schedules are jeopardized due to delays in receiving essential equipment. The lack of reliable suppliers further complicates the situation, leading to increased stress and potential financial losses.
The Solution:
To mitigate supply chain risks, B2B buyers should diversify their supplier base by identifying multiple reliable manufacturers across different regions, such as Europe and the Middle East, that can provide cement mixer mixers. Establishing relationships with both local and international suppliers can ensure a steady flow of equipment even when one source is affected by disruptions. Additionally, buyers should consider leveraging technology such as supply chain management software that offers real-time tracking and alerts for shipments. This proactive approach allows buyers to adjust their procurement strategies dynamically, ensuring they remain on schedule and can react swiftly to unforeseen delays.
Scenario 2: Ensuring Compliance with Local Regulations for Cement Mixer Mixers
The Problem:
In many regions, especially in the Middle East and parts of Africa, regulations governing construction equipment can vary widely. B2B buyers may struggle to understand the specific compliance requirements for cement mixer mixers, which can lead to legal challenges, fines, or even project shutdowns. The complexity of navigating these regulatory landscapes can be overwhelming, particularly for companies unfamiliar with local laws or those operating across multiple jurisdictions.
The Solution:
To ensure compliance, buyers should engage with local experts or consultants who specialize in construction regulations. This can include hiring legal advisors familiar with the compliance landscape in their target markets. Moreover, buyers should conduct thorough research on local standards and regulations before finalizing their purchases. When selecting a cement mixer mixer, it is crucial to choose models that meet or exceed these regulations, which can often be verified through certification documents provided by manufacturers. Additionally, establishing a checklist of compliance requirements tailored to each region can streamline the procurement process and prevent costly mistakes.
Scenario 3: Managing Equipment Maintenance and Longevity for Cement Mixer Mixers
The Problem:
B2B buyers often face the challenge of ensuring the longevity and operational efficiency of their cement mixer mixers. In regions with harsher climates, such as extreme heat in the Middle East or humidity in South America, equipment can deteriorate faster than expected, leading to unexpected downtime and repair costs. This issue is compounded by a lack of access to qualified technicians or spare parts, making maintenance a significant pain point for buyers who rely heavily on consistent performance.
The Solution:
To enhance the lifespan of cement mixer mixers, buyers should invest in comprehensive maintenance training for their operators. This includes understanding the proper cleaning, lubrication, and storage techniques essential for equipment longevity. Additionally, establishing a regular maintenance schedule can help identify potential issues before they escalate into costly repairs. Buyers should also negotiate with suppliers for a warranty or service agreement that includes maintenance support and access to genuine spare parts. By fostering a relationship with a reliable service provider, buyers can ensure that their equipment remains operational and efficient, ultimately reducing downtime and extending the life of their investment.
Strategic Material Selection Guide for cement mixer mixer
When selecting materials for cement mixer mixers, international B2B buyers must consider a range of factors that influence performance, durability, and cost-effectiveness. Below, we analyze four common materials used in cement mixer mixers, focusing on their properties, advantages, disadvantages, and specific considerations for buyers from Africa, South America, the Middle East, and Europe.
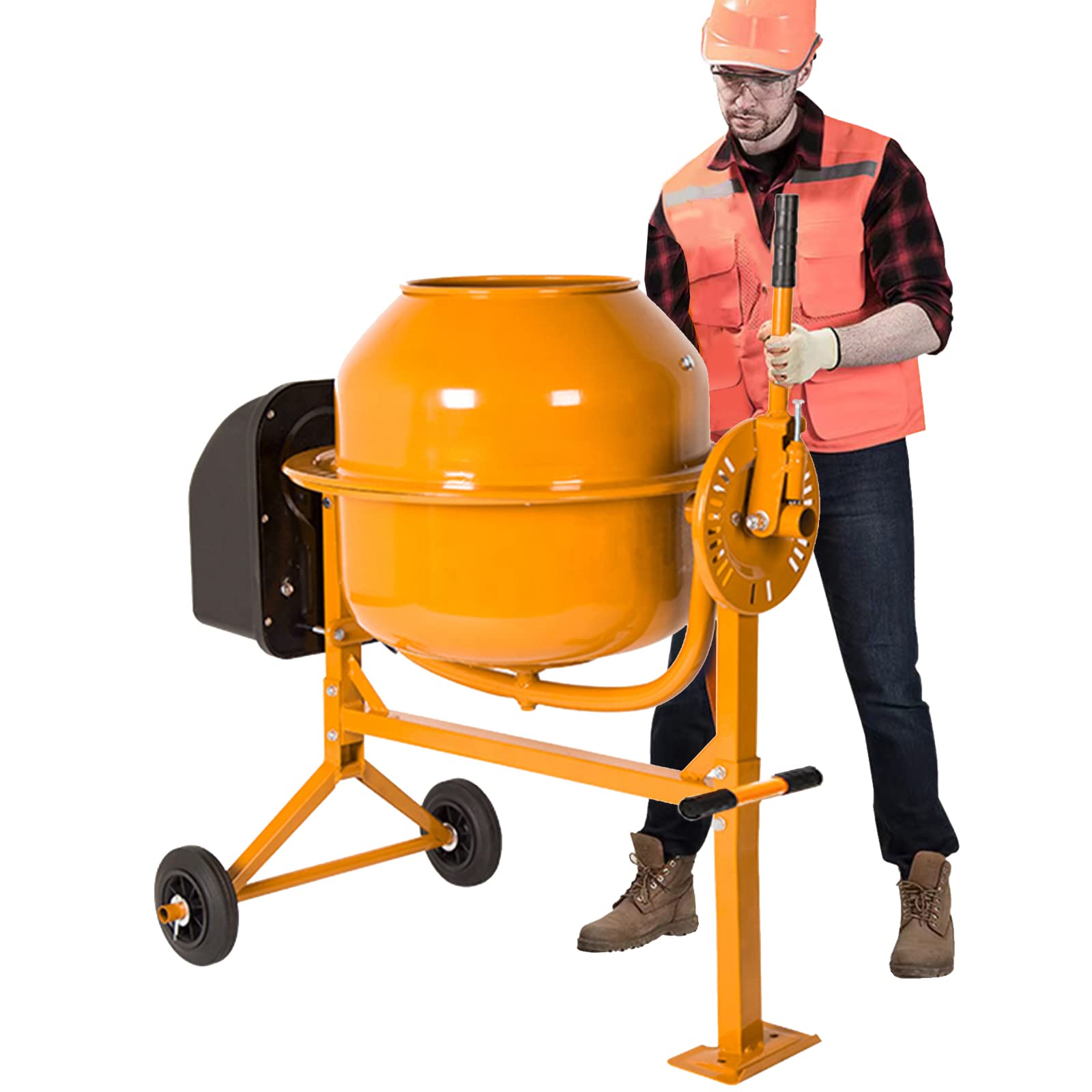
A stock image related to cement mixer mixer.
What are the Key Properties of Steel in Cement Mixer Mixers?
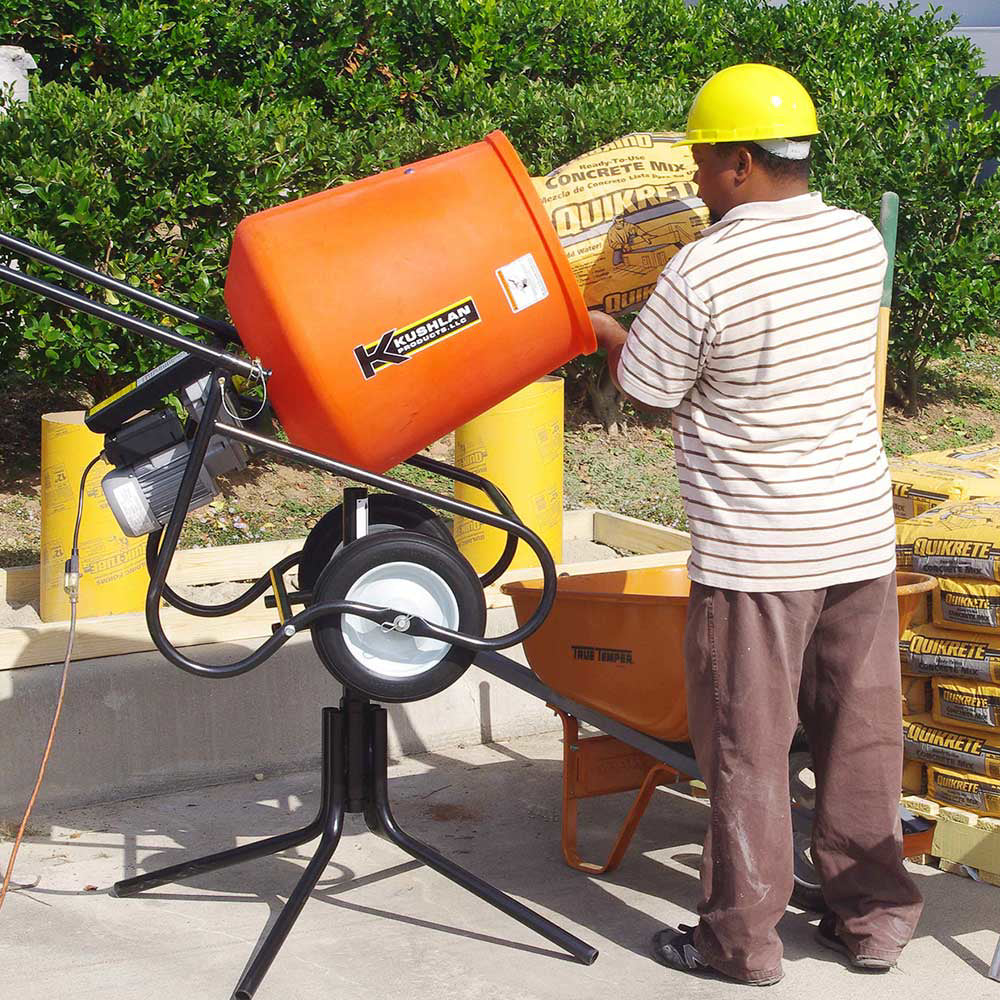
A stock image related to cement mixer mixer.
Steel is a widely used material in the construction of cement mixer mixers due to its high strength and durability. It typically exhibits excellent temperature and pressure ratings, making it suitable for heavy-duty applications. Steel’s corrosion resistance can be enhanced through galvanization or coating, which is crucial in environments with high moisture or exposure to aggressive chemicals.
Pros: Steel offers high structural integrity and can withstand significant wear and tear. It is relatively cost-effective and widely available, making it a popular choice for manufacturers.
Cons: While steel is strong, it can be prone to rust and corrosion if not properly treated. This limitation may require additional maintenance or protective coatings, which can increase overall costs.
Impact on Application: Steel is compatible with various media, including water and cement slurries. However, its susceptibility to corrosion can be a concern in humid environments, necessitating careful consideration of protective measures.
Considerations for International Buyers: Buyers should ensure compliance with international standards such as ASTM or DIN for steel quality. Additionally, understanding local sourcing options can impact costs and lead times.
How Does Aluminum Compare as a Material for Cement Mixer Mixers?
Aluminum is another viable option for cement mixer mixers, known for its lightweight properties and resistance to corrosion. It has a good temperature rating and can handle moderate pressure, making it suitable for certain applications.
Pros: The lightweight nature of aluminum makes it easier to handle and transport, reducing overall logistical costs. Its natural corrosion resistance minimizes maintenance needs over time.
Cons: Aluminum is generally less durable than steel and may not withstand the same level of stress. This can limit its use in heavy-duty applications, leading to potential performance issues.
Impact on Application: Aluminum is suitable for mixing lighter materials but may struggle with heavier cement mixes. Its compatibility with various media is generally good, but buyers should assess specific use cases.
Considerations for International Buyers: Buyers should be aware of the differences in aluminum grades and their compliance with international standards. Additionally, sourcing aluminum may be more expensive in certain regions compared to steel.
What are the Advantages of Using Composite Materials in Cement Mixer Mixers?
Composite materials, often a blend of plastic and fiberglass, are increasingly being used in cement mixer mixers. These materials offer unique properties, including high corrosion resistance and lightweight characteristics.
Pros: Composites are resistant to a wide range of chemicals, making them ideal for aggressive environments. They are also lightweight, which can enhance mobility and ease of installation.
Cons: The primary drawback of composites is their cost, which can be significantly higher than traditional materials like steel or aluminum. Additionally, their mechanical strength may not match that of metals, limiting their application in high-stress scenarios.
Impact on Application: Composites excel in applications where corrosion is a significant concern, such as in coastal or chemical processing environments. However, buyers must evaluate their suitability for specific mixing tasks.
Considerations for International Buyers: Compliance with local and international standards is essential. Buyers should also consider the availability of composite materials in their region, as this can impact lead times and costs.
Why is Stainless Steel a Preferred Material for Cement Mixer Mixers?
Stainless steel is renowned for its corrosion resistance and strength, making it a premium choice for cement mixer mixers. It offers excellent temperature and pressure ratings, suitable for various applications.
Pros: The durability and longevity of stainless steel reduce maintenance costs over time. Its resistance to rust and corrosion makes it ideal for harsh environments.
Cons: The primary disadvantage of stainless steel is its higher cost compared to other materials. This can be a significant factor for budget-conscious buyers.
Impact on Application: Stainless steel is compatible with all types of media, including abrasive cement mixes. Its robust nature ensures consistent performance across various applications.
Considerations for International Buyers: Buyers should prioritize sourcing stainless steel that meets international standards, such as ASTM or JIS. Understanding the local market for stainless steel can help in negotiating better prices.
Summary Table of Material Selection for Cement Mixer Mixers
Material | Typical Use Case for cement mixer mixer | Key Advantage | Key Disadvantage/Limitation | Relative Cost (Low/Med/High) |
---|---|---|---|---|
Steel | Heavy-duty applications | High strength and durability | Prone to rust without treatment | Medium |
Aluminum | Lightweight applications | Lightweight and corrosion-resistant | Less durable than steel | Medium |
Composite | Corrosive environments | Excellent chemical resistance | Higher cost and lower strength | High |
Stainless Steel | All-purpose applications | Corrosion-resistant and durable | Higher initial cost | High |
This guide aims to empower international B2B buyers with actionable insights into material selection for cement mixer mixers, considering performance, cost, and regional factors.
In-depth Look: Manufacturing Processes and Quality Assurance for cement mixer mixer
What Are the Main Manufacturing Processes for Cement Mixers?
Manufacturing cement mixers involves several critical stages that ensure the final product is both durable and efficient. Understanding these processes can help B2B buyers evaluate potential suppliers effectively.
Material Preparation: What Is Involved?
The first step in manufacturing a cement mixer is material preparation. This typically involves selecting high-quality raw materials such as steel, aluminum, and polymers. The quality of these materials directly influences the durability and performance of the mixer. Suppliers often perform a preliminary inspection of materials to ensure they meet industry standards before proceeding.
Once selected, the materials undergo various treatments, including cutting, bending, and surface treatment to enhance their properties. For instance, steel components may be galvanized to prevent rust and corrosion, which is particularly crucial for operations in humid climates like parts of Africa and South America.
How Is the Forming Process Executed?
The forming process involves shaping the raw materials into the desired components of the cement mixer. This can include:
- Casting: Used for large components such as the mixer drum and chassis, where molten metal is poured into molds.
- Machining: Precision tools are used to cut and shape components, ensuring they meet exact specifications.
- Welding: Critical parts are joined together, particularly in the frame and drum assembly, to provide structural integrity.
Advanced techniques such as Computer Numerical Control (CNC) machining are increasingly common, allowing for precise and repeatable production, which is essential for maintaining quality standards.
What Does the Assembly Process Entail?
During the assembly phase, the various components are brought together to form the finished cement mixer. This stage includes:
- Sub-assembly: Smaller components are first assembled into larger units.
- Final assembly: The sub-assemblies are then integrated into the complete mixer. This process often involves various types of fasteners and seals to ensure durability and prevent leaks.
Quality checks are integrated at this stage to catch any defects early on. For instance, a common practice is to test the mixer for leaks and structural integrity before moving on to the finishing touches.
How Is the Finishing Process Completed?
Finishing is the final stage of manufacturing, where the cement mixer is prepared for delivery. This includes:
- Surface treatment: Painting or powder coating protects the mixer from environmental factors, particularly important for buyers in regions with extreme weather conditions.
- Final inspection: A thorough quality control check is conducted to ensure all specifications are met, and the mixer operates as intended.
What Quality Assurance Measures Are Critical for Cement Mixers?
Quality assurance (QA) is vital to ensure that cement mixers are safe, reliable, and meet international standards. Here are key aspects of QA in the manufacturing of cement mixers.
Which International Standards Should B2B Buyers Consider?
B2B buyers should be familiar with various international standards that govern the quality of cement mixers:
- ISO 9001: This standard focuses on quality management systems and ensures that manufacturers consistently provide products that meet customer and regulatory requirements.
- CE Marking: Particularly important for buyers in Europe, this mark indicates that the product complies with EU safety, health, and environmental protection legislation.
- API Standards: For mixers used in oil and gas industries, compliance with American Petroleum Institute standards is often required.
Understanding these standards can help buyers assess a supplier’s commitment to quality.
What Are the Key QC Checkpoints in the Manufacturing Process?
Quality Control (QC) involves several checkpoints throughout the manufacturing process, including:
- Incoming Quality Control (IQC): Inspection of raw materials and components as they arrive at the manufacturing facility.
- In-Process Quality Control (IPQC): Ongoing checks during the manufacturing stages to ensure adherence to specifications.
- Final Quality Control (FQC): A comprehensive evaluation of the finished product before it is shipped to customers.
These checkpoints help ensure that any defects are identified and corrected before the product reaches the buyer.
What Common Testing Methods Are Used?
Several testing methods are employed to ensure that the cement mixers meet quality standards:
- Load Testing: Ensures that the mixer can handle the specified weight and pressure.
- Leak Testing: Checks for any potential leaks in the mixer drum and connections.
- Performance Testing: Evaluates the mixer’s operational efficiency under various conditions.
Buyers should inquire about these testing methods when evaluating suppliers.
How Can B2B Buyers Verify Supplier Quality Control?
Verification of a supplier’s quality control practices is crucial for B2B buyers looking to minimize risk. Here are some strategies:
- Supplier Audits: Conducting regular audits of suppliers can provide insight into their manufacturing processes and quality control measures.
- Requesting Quality Reports: Buyers should ask for documentation that details the QC processes used in production, including results from IQC, IPQC, and FQC.
- Third-Party Inspections: Engaging third-party inspection agencies can provide an unbiased evaluation of a supplier’s compliance with quality standards.
What Nuances Should International Buyers Be Aware Of?
International buyers, especially from regions like Africa, South America, the Middle East, and Europe, should be aware of specific nuances in quality control:
- Regulatory Differences: Each region may have different regulatory requirements, which can affect product compliance.
- Cultural Considerations: Understanding the local business culture can facilitate better communication and negotiations with suppliers.
- Logistical Challenges: Consideration of shipping and customs regulations is vital, as these can impact delivery timelines and costs.
By understanding these manufacturing processes and quality assurance measures, B2B buyers can make more informed decisions when selecting suppliers for cement mixers.
Practical Sourcing Guide: A Step-by-Step Checklist for ‘cement mixer mixer’
The procurement of a cement mixer is a significant investment for businesses engaged in construction, manufacturing, or other related industries. This practical sourcing guide provides a step-by-step checklist to help international B2B buyers navigate the complexities of sourcing a cement mixer. By following these steps, you can ensure that you make informed decisions and establish fruitful supplier relationships.
Step 1: Define Your Technical Specifications
Clearly outlining your technical requirements is crucial for successful procurement. Consider factors such as the mixer capacity, type (drum, pan, or twin-shaft), and any specific features like mobility or automation capabilities. This will help you narrow down suppliers who can meet your specific needs.
- Capacity Needs: Assess the volume of concrete you typically mix and choose a mixer that can handle that workload.
- Type of Mixer: Different projects may require different types of mixers. Understanding your project requirements will guide your choice.
Step 2: Research and Shortlist Potential Suppliers
Conduct thorough research to identify reputable suppliers in the market. Look for companies that specialize in cement mixers and have a strong presence in your target regions, such as Africa, South America, the Middle East, and Europe.
- Online Directories: Utilize platforms like Alibaba or Global Sources to find suppliers and read reviews.
- Trade Shows: Attend industry trade shows to meet suppliers face-to-face and see their products in action.
Step 3: Verify Supplier Certifications and Compliance
Before proceeding with any supplier, it’s essential to verify their certifications and compliance with industry standards. This step is particularly important in regions with strict safety regulations.
- ISO Certifications: Check if the supplier has relevant ISO certifications, which indicate adherence to quality management standards.
- Local Compliance: Ensure the supplier meets local regulations regarding construction equipment.
Step 4: Request Detailed Quotations
Once you have shortlisted suppliers, request detailed quotations that outline pricing, delivery times, and payment terms. A comprehensive quote will help you compare offers effectively.
- Itemized Costs: Look for transparency in pricing, including shipping costs and potential taxes.
- Payment Terms: Clarify payment options to avoid any future misunderstandings.
Step 5: Evaluate After-Sales Support and Warranty Policies
Understanding the after-sales support and warranty options provided by suppliers is critical. This step ensures you have access to necessary support post-purchase, which can save time and money in the long run.
- Technical Support: Inquire about the availability of technical assistance and training for your staff.
- Warranty Coverage: Assess the warranty terms and what they cover to protect your investment.
Step 6: Conduct a Site Visit or Request Video Demonstrations
If possible, arrange a site visit to the supplier’s facility or request video demonstrations of the cement mixer. This allows you to assess the quality of the equipment and the supplier’s manufacturing process.
- Quality Assurance: A site visit can help you verify the supplier’s production capabilities and quality control measures.
- Operational Understanding: Observing the mixer in action will give you insights into its performance and ease of use.
Step 7: Finalize the Contract and Payment Terms
Once you have completed your due diligence, finalize the contract with your chosen supplier. Ensure that all terms discussed are included in the contract to prevent future disputes.
- Contract Clarity: Make sure the contract clearly outlines the delivery schedule, payment terms, and responsibilities of both parties.
- Legal Review: Consider having a legal professional review the contract to ensure compliance with local laws and regulations.
By following this step-by-step checklist, B2B buyers can confidently navigate the procurement process for cement mixers, ensuring that they make informed decisions that align with their operational needs.
Comprehensive Cost and Pricing Analysis for cement mixer mixer Sourcing
What Are the Key Cost Components in Cement Mixer Mixer Sourcing?
When sourcing cement mixer mixers, understanding the cost structure is crucial for international B2B buyers. The primary cost components include:
-
Materials: The quality and type of materials used significantly affect the overall cost. High-grade steel and durable components increase the mixer’s longevity but may raise initial expenses.
-
Labor: Labor costs vary by region, influenced by local wage standards and the complexity of the manufacturing process. Skilled labor may be more expensive but ensures better quality.
-
Manufacturing Overhead: This includes costs related to utilities, equipment maintenance, and indirect labor. Efficient manufacturing processes can help reduce overhead costs.
-
Tooling: Custom tooling for specialized mixer designs can be a significant upfront investment. However, this cost can be amortized over larger production runs.
-
Quality Control (QC): Implementing rigorous QC processes adds to the cost but is essential for ensuring compliance with international standards, particularly for buyers in Europe and Australia.
-
Logistics: Shipping and handling fees can vary widely based on the origin of the product, destination, and shipping method. Understanding the logistics landscape is vital for accurate cost forecasting.
-
Margin: Suppliers typically add a margin to cover their costs and profit. This can vary based on market competition and supplier relationships.
How Do Price Influencers Affect Cement Mixer Mixer Costs?
Several factors influence the pricing of cement mixer mixers, making it essential for buyers to consider:
-
Volume/MOQ (Minimum Order Quantity): Larger orders often lead to lower per-unit costs due to economies of scale. Negotiating for bulk discounts can significantly reduce overall expenses.
-
Specifications and Customization: Custom features or specifications will increase costs. Buyers should clearly define their requirements to avoid unexpected price hikes.
-
Materials Used: The choice of materials impacts both the durability and price. Understanding the trade-offs between price and quality is crucial for long-term value.
-
Quality Certifications: Products that meet international quality standards may come at a premium. However, they can provide assurance of quality, which can be a significant factor for buyers in regulated markets.
-
Supplier Factors: The reputation and reliability of the supplier can influence price. Established suppliers may charge more but offer better service and quality assurance.
-
Incoterms: Understanding Incoterms (International Commercial Terms) is vital for determining the responsibilities of buyers and sellers regarding shipping, costs, and risks. This can greatly affect the total landed cost of the product.
What Are the Best Practices for Negotiating Cement Mixer Mixer Prices?
To effectively negotiate prices, international B2B buyers should consider these strategies:
-
Conduct Market Research: Understanding the market rates for cement mixer mixers can empower buyers during negotiations. Knowledge of competitor pricing can be a strong leverage point.
-
Focus on Total Cost of Ownership (TCO): Instead of just looking at the purchase price, consider the TCO, which includes maintenance, operational costs, and potential downtime. This perspective can justify a higher upfront investment for a more reliable product.
-
Build Relationships with Suppliers: Establishing a good rapport with suppliers can lead to better pricing, priority service, and favorable terms in future negotiations.
-
Be Clear on Requirements: Clearly articulating specifications and expectations can prevent misunderstandings and unexpected costs later in the process.
-
Leverage Payment Terms: Flexible payment options can sometimes be negotiated to ease cash flow concerns, allowing for better pricing agreements.
What Should Buyers Keep in Mind Regarding Indicative Prices?
It’s essential to note that prices for cement mixer mixers can fluctuate based on market conditions, raw material availability, and geopolitical factors. Therefore, buyers should view any indicative prices as starting points rather than fixed quotes. Engaging in direct discussions with suppliers and requesting detailed quotations based on specific needs will yield the most accurate and relevant pricing information.
Alternatives Analysis: Comparing cement mixer mixer With Other Solutions
When considering the procurement of a cement mixer, it’s essential to evaluate alternative solutions that may meet the specific needs of your construction projects. This analysis will provide a comparative overview of the cement mixer mixer against other viable options, helping international B2B buyers, particularly from Africa, South America, the Middle East, and Europe, make informed decisions.
Comparison Table of Cement Mixer Mixer and Alternatives
Comparison Aspect | Cement Mixer Mixer | Portable Concrete Mixer | Ready-Mix Concrete |
---|---|---|---|
Performance | High efficiency for small to medium jobs | Moderate, suitable for small jobs | High, consistent quality for large projects |
Cost | Moderate initial investment | Lower cost, but may require frequent replacements | Higher cost per cubic meter, but labor-efficient |
Ease of Implementation | Requires setup and training | Easy to set up and operate | Minimal setup, delivered ready to use |
Maintenance | Regular maintenance required for longevity | Low maintenance, but less durable | No maintenance needed; only scheduling required |
Best Use Case | Ideal for small to medium construction sites | Best for residential projects and DIY | Suited for large commercial projects requiring high volume |
What are the Advantages and Disadvantages of a Portable Concrete Mixer?
A Portable Concrete Mixer is a compact solution ideal for small-scale projects. Its main advantage lies in its affordability and ease of transport, making it suitable for residential jobs and small construction sites. However, it has limitations in terms of volume and mixing efficiency compared to a cement mixer mixer. The need for manual mixing can also lead to inconsistencies in the concrete quality, which may affect larger projects.
How Does Ready-Mix Concrete Compare?
Ready-Mix Concrete is a highly efficient solution for large construction projects. Delivered in a ready-to-use form, it eliminates the need for onsite mixing and labor costs associated with manual processes. The primary advantage is the consistent quality of the concrete, which is crucial for structural integrity. However, the costs can be significantly higher, especially for smaller projects where the volume may not justify the price. Additionally, scheduling delivery can pose challenges in remote areas.
Conclusion: How Can B2B Buyers Choose the Right Solution for Their Needs?
Selecting the appropriate solution for concrete mixing depends on various factors, including project size, budget, and specific requirements. For small to medium projects, a cement mixer mixer or a portable concrete mixer may provide the best balance of performance and cost. In contrast, for large-scale operations, ready-mix concrete ensures quality and efficiency, albeit at a higher price point. B2B buyers should carefully assess their project needs, considering both immediate requirements and long-term operational costs, to make an informed decision that aligns with their business objectives.
Essential Technical Properties and Trade Terminology for cement mixer mixer
What Are the Essential Technical Properties of Cement Mixer Mixers?
Understanding the technical specifications of cement mixer mixers is crucial for international B2B buyers, especially when ensuring the quality and durability of equipment. Here are several key properties to consider:
-
Material Grade
– Definition: Refers to the quality of materials used in the construction of the mixer, such as steel or high-grade plastic.
– Importance: High-grade materials enhance durability and resistance to wear and corrosion, ensuring longevity, which is especially vital in harsh working environments common in Africa and South America. -
Mixing Capacity
– Definition: The volume of concrete the mixer can produce in a single batch, typically measured in liters or cubic meters.
– Importance: Knowing the mixing capacity helps buyers determine if the mixer meets their project demands. For instance, larger capacities are beneficial for big construction projects in the Middle East where rapid construction is necessary. -
Power Rating
– Definition: The power consumed by the mixer, usually indicated in kilowatts (kW).
– Importance: A higher power rating often leads to more efficient mixing and faster operation. For B2B buyers in Europe, energy efficiency is increasingly important due to regulatory standards and operational cost considerations. -
Tolerance Levels
– Definition: The permissible limit of variation in dimensions or performance of the mixer.
– Importance: Tighter tolerance levels ensure consistent mixing quality and help in achieving desired concrete specifications. This is crucial for meeting regulatory standards in construction across various regions. -
Rotation Speed
– Definition: The speed at which the drum rotates, measured in revolutions per minute (RPM).
– Importance: Different projects require different mixing speeds to achieve the right consistency of the concrete. B2B buyers should consider this in relation to their specific applications.
What Are Common Trade Terms Associated with Cement Mixer Mixers?
Familiarity with industry jargon is essential for effective communication and negotiation in B2B transactions. Here are some common terms:
-
OEM (Original Equipment Manufacturer)
– Definition: A company that produces parts or equipment that may be marketed by another manufacturer.
– Importance: Understanding OEMs helps buyers identify reliable manufacturers who can provide high-quality mixers and spare parts. -
MOQ (Minimum Order Quantity)
– Definition: The smallest quantity of a product that a supplier is willing to sell.
– Importance: Knowing the MOQ is crucial for buyers to manage inventory effectively and avoid excess stock, particularly in markets like Africa where demand can fluctuate significantly. -
RFQ (Request for Quotation)
– Definition: A document issued by a buyer to request price quotes from suppliers for specific products.
– Importance: An RFQ helps buyers compare pricing and terms from different suppliers, facilitating better decision-making and cost management. -
Incoterms (International Commercial Terms)
– Definition: A set of predefined international rules that govern commercial transactions and shipping.
– Importance: Familiarity with Incoterms is vital for B2B buyers to understand their responsibilities in shipping, insurance, and tariffs, especially in cross-border transactions prevalent in Europe and the Middle East. -
Lead Time
– Definition: The amount of time between the initiation of a process and its completion, particularly in the context of manufacturing and delivery.
– Importance: Understanding lead times can help buyers plan their projects more effectively and manage cash flow, particularly important in fast-paced construction environments.
By grasping these essential technical properties and trade terminologies, international B2B buyers can make informed purchasing decisions, ensuring that they select the right cement mixer mixers for their specific needs.
Navigating Market Dynamics and Sourcing Trends in the cement mixer mixer Sector
What Are the Current Market Dynamics and Key Trends in the Cement Mixer Sector?
The cement mixer sector is experiencing a transformative phase, driven by several global factors that international B2B buyers must navigate. The rising demand for infrastructure development, particularly in emerging markets across Africa, South America, and the Middle East, is propelling growth. Governments in these regions are investing heavily in construction projects, which directly boosts the demand for cement mixers. Additionally, the global shift towards urbanization is creating a sustained need for efficient construction machinery.
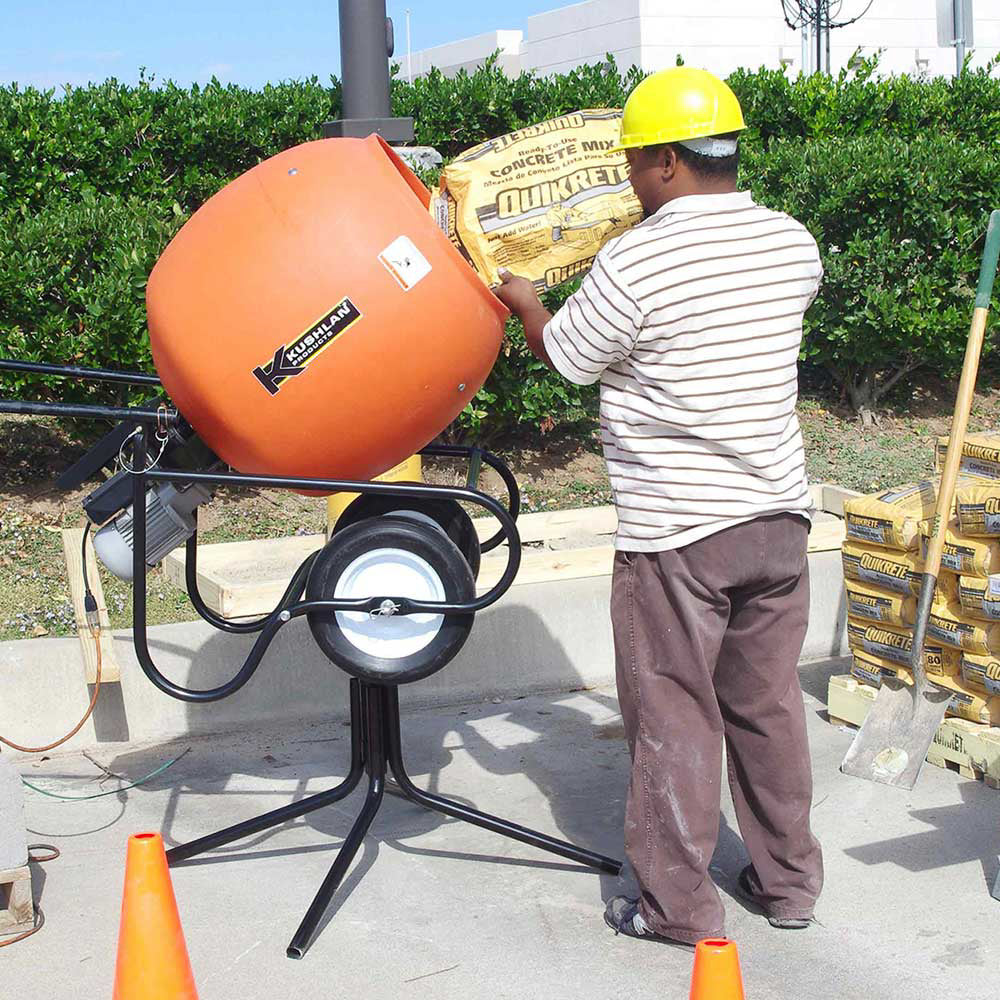
A stock image related to cement mixer mixer.
Emerging B2B technologies are reshaping sourcing trends, with automation and IoT (Internet of Things) taking center stage. Smart cement mixers equipped with sensors allow for real-time monitoring and predictive maintenance, enhancing operational efficiency. Furthermore, the integration of mobile applications for equipment tracking and remote management is becoming standard practice. Buyers are increasingly looking for suppliers who offer such innovative solutions to ensure they remain competitive in their projects.
The competitive landscape is also evolving, with a growing emphasis on product differentiation. Manufacturers are focusing on developing mixers that are not only efficient but also adaptable to various construction needs. This includes portable and compact models that cater to both large-scale projects and smaller construction sites. For B2B buyers, understanding these trends is crucial to make informed purchasing decisions and to align their sourcing strategies with the market’s direction.
How Is Sustainability Shaping Ethical Sourcing in the Cement Mixer Industry?
Sustainability is no longer just a trend; it has become a fundamental aspect of sourcing in the cement mixer sector. International B2B buyers are increasingly prioritizing suppliers who demonstrate a commitment to environmental stewardship. The cement industry is notorious for its environmental impact, and as such, there is a significant push towards reducing carbon footprints. Buyers should seek suppliers who utilize eco-friendly materials in their mixers, such as recycled components or those certified by recognized environmental standards.
Ethical sourcing practices also extend to labor conditions and supply chain transparency. Buyers are encouraged to collaborate with manufacturers who ensure fair labor practices and uphold human rights in their operations. Certifications such as ISO 14001 (Environmental Management) and Fair Trade can serve as indicators of a supplier’s commitment to sustainability and ethical practices. By prioritizing suppliers with strong sustainability credentials, B2B buyers not only enhance their corporate reputation but also contribute to a more sustainable construction industry.
What Is the Brief Evolution of the Cement Mixer Sector and Its Significance for B2B Buyers?
The evolution of the cement mixer sector has been marked by significant technological advancements and shifts in market demands. Initially, cement mixers were manual and labor-intensive, requiring substantial human effort for mixing and transportation. Over the decades, the introduction of motorized mixers revolutionized the industry, significantly enhancing efficiency and reducing labor costs.
In recent years, the focus has shifted towards automation and smart technology. The advent of computer-controlled mixers has enabled precise mixing ratios and reduced waste, aligning with modern construction practices that prioritize efficiency and sustainability. For B2B buyers, understanding this evolution is critical as it highlights the importance of investing in advanced machinery that can meet contemporary construction demands. As the sector continues to innovate, staying informed about historical trends can empower buyers to make strategic decisions that align with their long-term goals.
Frequently Asked Questions (FAQs) for B2B Buyers of cement mixer mixer
-
How do I determine the right capacity for my cement mixer?
Choosing the appropriate capacity for a cement mixer depends on the scale of your projects. For small to medium-sized construction tasks, a mixer with a capacity of 2 to 3 cubic meters is often sufficient. However, larger projects or commercial applications may require mixers with capacities ranging from 4 to 12 cubic meters. Evaluate your project requirements, frequency of use, and the volume of concrete needed to ensure efficiency and avoid over or under-utilization. -
What is the best type of cement mixer for construction projects?
The best type of cement mixer varies based on project requirements and site conditions. For high mobility, portable mixers are ideal, while stationary mixers are suited for large-scale operations. Drum mixers are common for their efficiency in mixing, while continuous mixers are excellent for ongoing operations. Assess your project scale, budget, and site constraints to determine the most suitable option. -
How can I verify the credibility of a cement mixer supplier?
To verify the credibility of a cement mixer supplier, consider checking their business licenses, certifications, and industry reputation. Look for reviews and testimonials from previous clients, as well as their experience in the market. Engaging in direct communication, requesting references, and visiting their facilities (if possible) can provide deeper insights into their reliability and product quality. -
What are the typical payment terms for international cement mixer purchases?
Payment terms for international purchases often include options such as advance payment, letter of credit, or payment upon delivery. It’s crucial to negotiate terms that provide security for both parties. Be aware of additional costs like shipping, customs duties, and insurance, which can affect the total price. Always ensure that the payment method is secure and verifiable to protect your investment. -
What is the minimum order quantity (MOQ) when sourcing cement mixers?
Minimum order quantities for cement mixers can vary widely among suppliers, typically ranging from one unit for smaller suppliers to several units for larger manufacturers. If you’re a first-time buyer or looking to test a supplier, inquire about their flexibility on MOQ. Some suppliers might allow smaller orders for specific models or during promotional periods, providing a low-risk entry point. -
How do I ensure quality assurance when importing cement mixers?
To ensure quality assurance when importing cement mixers, request detailed specifications, production samples, and certifications from your supplier. Consider hiring third-party inspection services to verify product quality before shipment. Establish a clear contract that includes quality standards and penalties for non-compliance, ensuring that the equipment meets your expectations upon arrival. -
What logistics considerations should I keep in mind for cement mixer imports?
When importing cement mixers, consider logistics factors such as shipping methods, lead times, and customs regulations specific to your region. Choose between sea or air freight based on your budget and urgency. Additionally, ensure that your supplier provides all necessary shipping documentation, including bills of lading and customs declarations, to facilitate smooth clearance upon arrival. -
Can cement mixers be customized for specific project requirements?
Yes, many suppliers offer customization options for cement mixers to meet specific project needs. Customizations may include modifications in size, mixing capacity, or additional features like automated controls or specific drum designs. Discuss your requirements with potential suppliers early in the negotiation process to understand the possibilities and any impact on pricing and delivery timelines.
Important Disclaimer & Terms of Use
⚠️ Important Disclaimer
The information provided in this guide, including content regarding manufacturers, technical specifications, and market analysis, is for informational and educational purposes only. It does not constitute professional procurement advice, financial advice, or legal advice.
While we have made every effort to ensure the accuracy and timeliness of the information, we are not responsible for any errors, omissions, or outdated information. Market conditions, company details, and technical standards are subject to change.
B2B buyers must conduct their own independent and thorough due diligence before making any purchasing decisions. This includes contacting suppliers directly, verifying certifications, requesting samples, and seeking professional consultation. The risk of relying on any information in this guide is borne solely by the reader.
Strategic Sourcing Conclusion and Outlook for cement mixer mixer
The strategic sourcing of cement mixers is pivotal for international B2B buyers aiming to optimize their procurement processes. By leveraging supplier relationships and conducting comprehensive market analysis, businesses can secure high-quality equipment that meets their specific operational needs. Engaging with local and global suppliers allows for cost-effective solutions while ensuring compliance with regional regulations, particularly in diverse markets across Africa, South America, the Middle East, and Europe.
How Can Strategic Sourcing Enhance Your Competitive Edge?
Utilizing strategic sourcing not only reduces costs but also enhances supply chain resilience. Buyers should focus on long-term partnerships that foster innovation and adaptability. This approach is crucial in a rapidly evolving construction industry, where the demand for efficiency and sustainability is ever-increasing.
What Should International Buyers Consider Moving Forward?
Looking ahead, international buyers must stay informed about emerging technologies and market trends that can influence their sourcing strategies. By prioritizing sustainability and efficiency, businesses can meet the growing demand for environmentally friendly practices while ensuring their operations remain competitive.
In conclusion, embracing a strategic sourcing mindset will empower international B2B buyers to make informed decisions, optimize their investments, and drive sustainable growth in the cement mixer sector. Now is the time to evaluate your sourcing strategies and align them with future market demands.