Cut Costs: The Ultimate Air Oil Separator Guide (2025)
Introduction: Navigating the Global Market for air oil separator
In today’s competitive landscape, sourcing high-quality air oil separators can be a daunting task for international B2B buyers. The challenge lies not only in identifying the right technology to optimize operations but also in navigating the diverse offerings available in the global market. This comprehensive guide will explore the various types of air oil separators, their applications across industries, and essential factors to consider when selecting a supplier.
We will delve into critical aspects such as supplier vetting processes, cost considerations, and best practices for integration into existing systems. By providing actionable insights and practical strategies, this guide empowers decision-makers in Africa, South America, the Middle East, and Europe—particularly in markets like Saudi Arabia and the UAE—to make informed purchasing decisions.
Understanding the nuances of air oil separators is vital for enhancing efficiency, reducing operational costs, and ensuring compliance with environmental regulations. With this resource, B2B buyers will gain a clear perspective on how to effectively source, evaluate, and implement air oil separators tailored to their specific needs, ultimately driving better outcomes for their organizations.
Understanding air oil separator Types and Variations
Type Name | Key Distinguishing Features | Primary B2B Applications | Brief Pros & Cons for Buyers |
---|---|---|---|
Coalescing Separator | Utilizes a coalescing filter to collect oil droplets | Manufacturing, Automotive, Marine | Pros: High efficiency in oil removal; Cons: Requires regular maintenance. |
Cyclonic Separator | Uses centrifugal force to separate oil from air | Power Generation, HVAC Systems | Pros: Low maintenance; Cons: Less effective for small particles. |
Membrane Separator | Employs a membrane barrier to filter oil | Chemical Processing, Food & Beverage | Pros: Compact design; Cons: Higher initial costs. |
Electrostatic Separator | Applies electrostatic charge for separation | Oil Refineries, Petrochemical Industries | Pros: Very high efficiency; Cons: Complex installation. |
Gravity Separator | Relies on gravity to separate oil from air | Wastewater Treatment, Oil Recovery | Pros: Simple design; Cons: Requires large footprint. |
What Are Coalescing Separators and Their Applications?
Coalescing separators are designed to efficiently remove oil droplets from air streams by using a filter that encourages smaller droplets to combine into larger ones. This type is particularly suited for industries such as manufacturing and automotive, where high levels of oil mist can be present. When purchasing, buyers should consider the separator’s maintenance needs, as regular filter changes are essential for optimal performance.
How Do Cyclonic Separators Work and Where Are They Used?
Cyclonic separators utilize centrifugal force to separate oil from air without the need for moving parts. This makes them ideal for applications in power generation and HVAC systems, where reliability and low maintenance are crucial. Buyers should evaluate the separator’s efficiency and the particle size it can handle, as cyclonic separators may struggle with very fine particles.
What Are the Benefits of Membrane Separators?
Membrane separators use a semi-permeable membrane to filter out oil from air, offering a compact solution for applications in chemical processing and food and beverage industries. Their space-saving design makes them attractive for facilities with limited space. However, buyers should weigh the higher initial investment against the long-term operational savings and efficiency benefits.
How Do Electrostatic Separators Operate?
Electrostatic separators leverage an electric charge to enhance the separation of oil from air, achieving very high efficiency levels. They are commonly used in oil refineries and petrochemical industries, where the demand for clean air is critical. Prospective buyers should consider the complexity of installation and the potential need for specialized maintenance services.
Why Choose Gravity Separators?
Gravity separators are the simplest form of air oil separation, relying solely on the force of gravity to separate oil from air. They are commonly employed in wastewater treatment and oil recovery applications. Buyers should note that while these separators are cost-effective and easy to operate, they require a larger physical footprint compared to more advanced technologies.
Related Video: How an Air Oil Separator Works and Why You Need One!
Key Industrial Applications of air oil separator
Industry/Sector | Specific Application of air oil separator | Value/Benefit for the Business | Key Sourcing Considerations for this Application |
---|---|---|---|
Manufacturing | Compressors in machining processes | Reduces oil carryover, improving efficiency and product quality | Durability, compatibility with existing systems, maintenance requirements |
Automotive | Engine oil separation in assembly lines | Enhances engine performance and lifespan, reducing downtime | Temperature tolerance, filtration efficiency, compliance with industry standards |
Oil & Gas | Separation in drilling and refining | Increases recovery rates and minimizes environmental impact | Corrosion resistance, capacity, and regulatory compliance |
Power Generation | Turbine lubrication systems | Ensures optimal operation, reducing wear and tear on equipment | Size, weight, energy efficiency, and supplier reliability |
Food & Beverage | Air compressor systems in production | Maintains product purity and safety, reducing contamination risk | FDA compliance, material specifications, and cleaning protocols |
How is Air Oil Separator Used in Manufacturing?
In the manufacturing sector, air oil separators are critical for compressors used in machining processes. These separators prevent oil from contaminating the compressed air, which is essential for maintaining product quality and operational efficiency. By significantly reducing oil carryover, businesses can enhance the performance of pneumatic tools and machinery, leading to lower operational costs and improved output. International buyers should consider the durability and compatibility of separators with existing systems, as well as the maintenance requirements to ensure long-term efficiency.
What Role Does Air Oil Separator Play in the Automotive Industry?
In the automotive industry, air oil separators are utilized in engine assembly lines to maintain optimal engine performance. They effectively separate oil from the air intake system, thus preventing oil-related issues that can lead to engine wear or failure. This application not only extends the lifespan of engines but also minimizes downtime for repairs. Buyers should focus on the temperature tolerance and filtration efficiency of the separators, ensuring they meet the stringent standards set by automotive regulations.
How is Air Oil Separator Essential for Oil & Gas Operations?
The oil and gas sector employs air oil separators during drilling and refining processes. These separators enhance recovery rates by ensuring that oil is effectively separated from the air and other gases, thus reducing environmental impact. As sustainability becomes increasingly important, sourcing separators with high corrosion resistance and compliance with regulatory standards is essential for international buyers, especially in regions such as the Middle East and Africa where environmental regulations are tightening.
What Benefits Does Air Oil Separator Provide in Power Generation?
In power generation, air oil separators are crucial for turbine lubrication systems. They ensure that lubricants remain clean and free from contaminants, which is vital for optimal turbine operation. This application helps in reducing wear and tear on equipment, thereby extending its operational lifespan and minimizing maintenance costs. Buyers should prioritize the size, weight, and energy efficiency of the separators, along with the reliability of the suppliers to ensure seamless integration into existing power generation systems.
How Does Air Oil Separator Contribute to the Food & Beverage Industry?
In the food and beverage sector, air oil separators are used in air compressor systems to maintain product purity and safety. By preventing oil contamination, these separators help ensure that the final products meet health and safety standards. This is particularly critical in regions like Europe and South America, where regulatory compliance is stringent. Buyers should ensure that the separators meet FDA compliance and material specifications, as well as have effective cleaning protocols to maintain hygiene in production processes.
3 Common User Pain Points for ‘air oil separator’ & Their Solutions
Scenario 1: Inconsistent Air Quality and Equipment Efficiency
The Problem:
Many industrial facilities in Africa and South America face challenges with air quality due to the inefficient operation of air oil separators. Inconsistent performance can lead to higher levels of oil contamination in the compressed air system, resulting in subpar air quality. This not only compromises the efficiency of pneumatic tools and machinery but can also lead to increased maintenance costs and unplanned downtime. For B2B buyers, understanding the root causes of these inefficiencies is crucial, especially in environments where optimal performance is expected to meet production targets.
The Solution:
To combat this issue, B2B buyers should prioritize sourcing high-quality air oil separators tailored to their specific operational conditions. It’s essential to consider separators that utilize advanced filtration technologies, such as coalescing filters, which can effectively remove oil aerosols and particles from compressed air. Additionally, implementing regular maintenance schedules, including timely replacement of filter elements, can greatly enhance the reliability of air oil separators. Buyers should also engage with suppliers who offer comprehensive technical support and training, ensuring that their staff understands the correct operation and maintenance procedures. By investing in durable, efficient separators and maintaining them properly, businesses can ensure a consistent air quality that supports equipment efficiency and minimizes costs.
Scenario 2: High Operating Costs Due to Ineffective Separator Systems
The Problem:
In the Middle East, businesses are often concerned about the rising operational costs associated with running inefficient air oil separator systems. These systems may consume excessive energy, leading to inflated utility bills, and may also necessitate frequent repairs or replacements due to premature failures. For B2B buyers, the challenge lies in balancing upfront costs with long-term savings, as opting for cheaper, less effective solutions can result in escalating expenses.
The Solution:
B2B buyers should conduct a thorough cost-benefit analysis when selecting air oil separators. Investing in energy-efficient models that meet or exceed industry standards can significantly reduce energy consumption and operational costs over time. Buyers should look for separators that feature low-pressure drop designs, which minimize the energy required to push air through the system. Additionally, it’s beneficial to partner with suppliers who offer lifetime warranties or performance guarantees, as this can provide peace of mind and reduce the risk of unexpected expenses. Regular performance audits can also help identify areas where efficiency can be improved, ultimately leading to substantial cost savings.
Scenario 3: Compliance and Environmental Regulations Challenges
The Problem:
European B2B buyers often face stringent regulations concerning air quality and environmental protection. Failure to comply with these regulations can result in hefty fines and damage to a company’s reputation. Air oil separators play a crucial role in ensuring that oil contamination in compressed air systems is kept within acceptable limits. However, many businesses struggle to find separators that meet these regulatory requirements, leading to a complex decision-making process.
The Solution:
To navigate compliance challenges effectively, B2B buyers must stay informed about local and international regulations related to air quality. Selecting air oil separators that are specifically designed to comply with these regulations is paramount. Buyers should work closely with manufacturers who provide detailed documentation on compliance certifications and performance metrics. Additionally, investing in separators that incorporate advanced monitoring technologies can offer real-time insights into system performance, helping to ensure ongoing compliance. Regular training for staff on environmental regulations and the importance of proper separator function can further bolster compliance efforts, ensuring that businesses maintain their operational integrity while minimizing environmental impact.
Strategic Material Selection Guide for air oil separator
When selecting materials for air oil separators, understanding the properties and applications of various materials is crucial for international B2B buyers. This guide analyzes four common materials used in the construction of air oil separators, providing insights into their performance, advantages, disadvantages, and considerations for buyers from regions such as Africa, South America, the Middle East, and Europe.
What Are the Key Properties of Aluminum in Air Oil Separators?
Aluminum is a popular choice for air oil separators due to its lightweight nature and excellent corrosion resistance. It typically has a temperature rating of up to 150°C and can withstand moderate pressure levels. Aluminum is also non-magnetic, which can be beneficial in certain applications where magnetic interference is a concern.
Pros: Aluminum’s lightweight characteristic facilitates easier installation and reduces overall system weight, which can be advantageous in mobile applications. It is also relatively cost-effective and easy to manufacture, allowing for complex shapes and designs.
Cons: While aluminum offers good corrosion resistance, it may not be suitable for highly corrosive environments without additional coatings. It can also be less durable than some other materials, particularly under high-impact conditions.
Impact on Application: Aluminum is compatible with various media, including oil and air, making it a versatile option for many air oil separator applications. However, buyers must ensure that the specific oil types used do not react adversely with aluminum.
How Does Stainless Steel Perform in Air Oil Separator Applications?
Stainless steel is renowned for its superior strength and corrosion resistance, making it ideal for harsh environments. It can handle high temperatures (up to 300°C) and pressures, which is essential for high-performance applications.
Pros: The durability of stainless steel translates to a longer lifespan for air oil separators, reducing replacement costs over time. Its resistance to corrosion and oxidation makes it suitable for use in marine and industrial applications.
Cons: The primary drawback of stainless steel is its higher cost compared to aluminum and plastic options. Additionally, the manufacturing process can be more complex, which may lead to longer lead times.
Impact on Application: Stainless steel is compatible with a wide range of oils and is often preferred in applications where hygiene and cleanliness are paramount, such as in food processing or pharmaceuticals.
What Are the Benefits of Using Polypropylene in Air Oil Separators?
Polypropylene is a thermoplastic polymer that offers excellent chemical resistance and is lightweight. It typically has a temperature rating of up to 80°C and is suitable for low-pressure applications.
Pros: Polypropylene is cost-effective and easy to mold into complex shapes, making it a popular choice for manufacturers. Its resistance to a wide range of chemicals ensures compatibility with various oil types.
Cons: The main limitation of polypropylene is its lower temperature and pressure ratings compared to metals. It may also be less durable in high-impact scenarios.
Impact on Application: Polypropylene is ideal for applications where cost is a primary concern, and the operating conditions are moderate. Buyers should be cautious about using polypropylene in high-temperature environments.
Why Consider Carbon Steel for Air Oil Separators?
Carbon steel is another common material used in air oil separators, particularly in industrial settings. It offers good strength and is typically rated for temperatures up to 200°C.
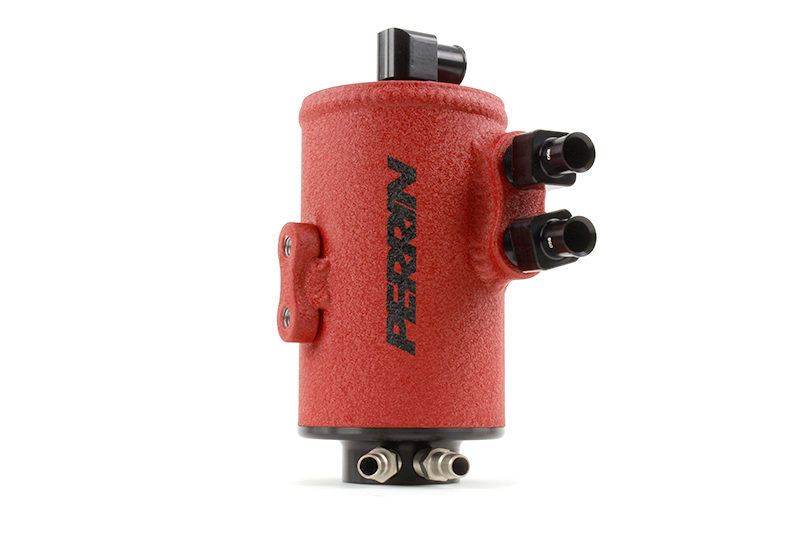
A stock image related to air oil separator.
Pros: Carbon steel is relatively inexpensive and widely available, making it an attractive option for large-scale applications. Its strength allows it to handle high-pressure scenarios effectively.
Cons: Carbon steel is prone to corrosion and may require protective coatings, which can increase maintenance costs. It is also heavier than aluminum and polypropylene, which could impact installation.
Impact on Application: Carbon steel is suitable for applications involving non-corrosive oils and can be used effectively in various industrial environments. Buyers should consider the need for protective measures to extend the lifespan of carbon steel separators.
Summary Table of Material Selection for Air Oil Separators
Material | Typical Use Case for Air Oil Separator | Key Advantage | Key Disadvantage/Limitation | Relative Cost (Low/Med/High) |
---|---|---|---|---|
Aluminum | Lightweight applications | Excellent corrosion resistance | Less durable under high impact | Low |
Stainless Steel | Harsh environments | Superior strength and longevity | Higher cost and complex manufacturing | High |
Polypropylene | Cost-sensitive applications | Cost-effective and chemically resistant | Lower temperature and pressure limits | Low |
Carbon Steel | Industrial settings | Inexpensive and strong | Prone to corrosion | Medium |
This guide provides a comprehensive overview of material options for air oil separators, helping international B2B buyers make informed decisions based on performance, cost, and application suitability.
In-depth Look: Manufacturing Processes and Quality Assurance for air oil separator
What Are the Key Stages in the Manufacturing Process of Air Oil Separators?
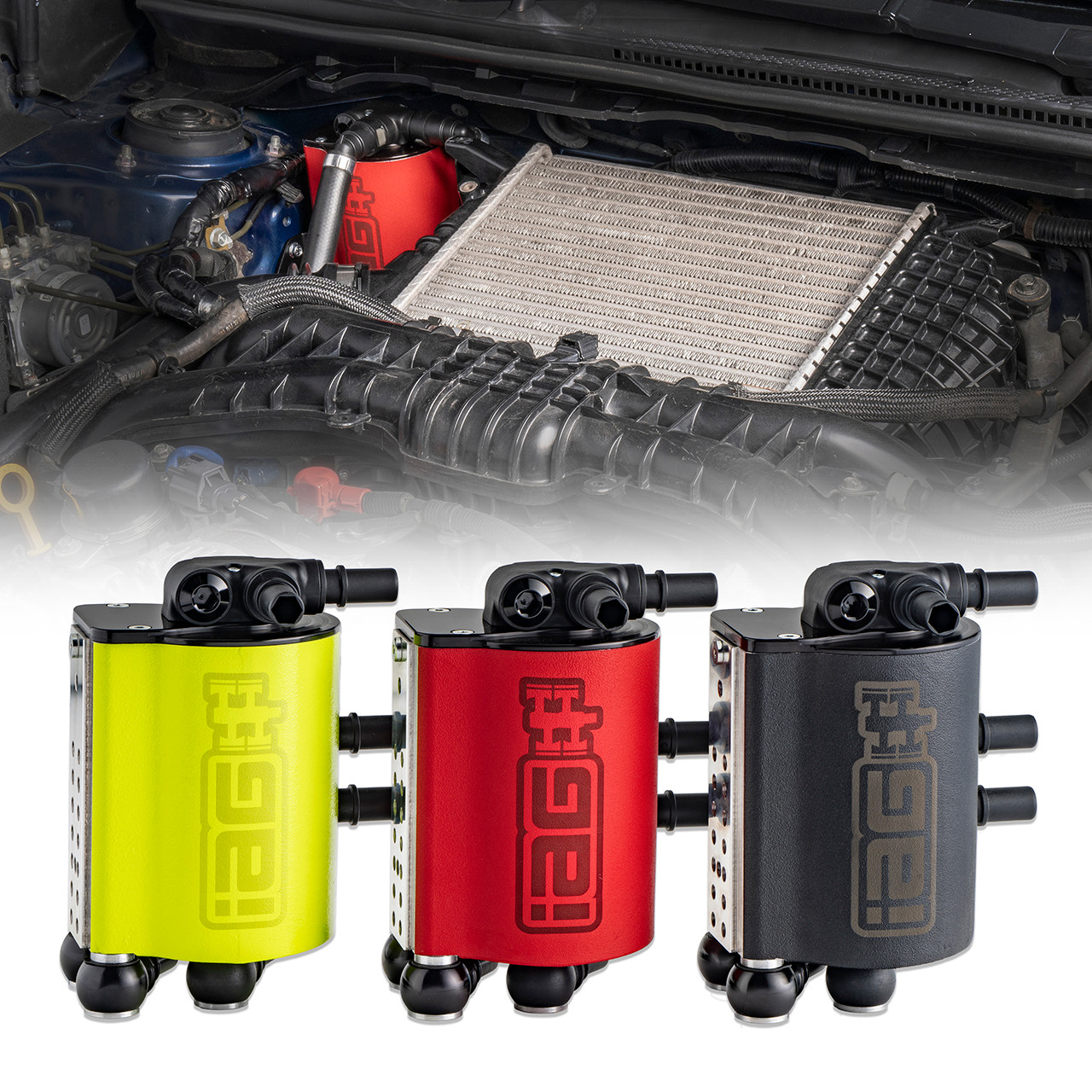
A stock image related to air oil separator.
The manufacturing process of air oil separators is critical to ensure their efficiency and reliability. This process can be broken down into four main stages: material preparation, forming, assembly, and finishing.
Material Preparation: What Materials Are Used?
The first step in manufacturing an air oil separator involves selecting appropriate materials. Common materials include aluminum, stainless steel, and high-grade plastics, which provide durability and resistance to corrosion. The material must also meet specific standards for chemical compatibility, especially when exposed to various oils and contaminants.
Once the materials are selected, they undergo rigorous testing for quality assurance. This includes checking for impurities, mechanical properties, and compliance with international standards.
Forming: How Are Air Oil Separators Shaped?
After material preparation, the forming stage begins. Techniques such as stamping, machining, and extrusion are commonly used to create the separator’s components.
- Stamping: This technique is often used for creating metal parts, where sheets of material are cut and shaped into specific forms.
- Machining: Involves removing material from a solid block to achieve the desired dimensions and surface finish. CNC (Computer Numerical Control) machining is frequently employed for its precision.
- Extrusion: This method is used for creating long components with consistent cross-sections, which is essential for certain separator designs.
Each of these techniques must adhere to strict tolerances to ensure that the final product performs as expected.
Assembly: How Are Components Brought Together?
The assembly stage is where all the components come together. This includes integrating filters, seals, and any electronic components that might be part of the separator.
During assembly, manufacturers often utilize automated systems to enhance precision and efficiency. Key assembly techniques include:
- Welding: For metal components, welding provides strong joints that can withstand high pressures.
- Adhesives: In cases where welding is not feasible, high-strength adhesives may be used to bond different materials.
- Mechanical Fastening: Bolts and screws are commonly employed to secure components.
Quality checks are performed at this stage to ensure each unit meets design specifications.
Finishing: What Final Touches Are Applied?
Finishing is the final stage of manufacturing, where the air oil separator is polished, coated, or painted to enhance durability and aesthetics. This stage may involve:
- Surface Treatment: Techniques such as anodizing or powder coating improve corrosion resistance.
- Inspection: Final inspection ensures that the product meets all functional and aesthetic requirements before packaging and shipping.
What Quality Assurance Measures Are Essential for Air Oil Separators?
Quality assurance is crucial in the manufacturing of air oil separators to ensure they operate effectively and meet industry standards.
Which International Standards Should B2B Buyers Consider?
Several international standards apply to air oil separators, including:
- ISO 9001: This standard focuses on quality management systems and is essential for manufacturers to demonstrate their commitment to quality.
- CE Marking: In Europe, this marking indicates that the product meets EU safety, health, and environmental requirements.
- API Standards: The American Petroleum Institute provides guidelines specific to oil and gas applications, ensuring that the separator is suitable for the intended environment.
B2B buyers should verify that their suppliers comply with these standards to ensure the reliability of the products.
What Are the Key QC Checkpoints in Manufacturing?
Quality control (QC) checkpoints are critical throughout the manufacturing process. Common checkpoints include:
- Incoming Quality Control (IQC): This involves inspecting raw materials upon receipt to ensure they meet specifications.
- In-Process Quality Control (IPQC): During manufacturing, regular checks are made to monitor the process and catch defects early.
- Final Quality Control (FQC): Before packaging, a comprehensive inspection is conducted to ensure that the finished product meets all design and quality specifications.
How Can B2B Buyers Verify Supplier QC Practices?
To ensure that suppliers maintain high QC standards, B2B buyers should consider the following actions:
- Conduct Audits: Regular audits of the supplier’s manufacturing facility can provide insights into their QC practices.
- Request Quality Reports: Suppliers should provide documentation of their QC processes, including test results and compliance certificates.
- Third-Party Inspections: Engaging independent inspection services can help validate the quality of the products before they are shipped.
What Testing Methods Are Commonly Used in Quality Control?
Various testing methods are employed to ensure that air oil separators perform effectively under different conditions:
- Pressure Testing: This method checks the ability of the separator to withstand operational pressures without leaking.
- Flow Rate Testing: Ensures that the separator can handle the required flow rates without compromising efficiency.
- Chemical Compatibility Testing: Verifies that materials used in the separator do not degrade when exposed to oils and other chemicals.
B2B buyers should inquire about the specific testing methods used by suppliers to ensure that their products will perform reliably in their intended applications.
How Do QC and Certification Nuances Affect International B2B Buyers?
For international buyers, understanding the nuances of QC and certification is essential. Different regions may have varying standards and regulations, which can affect the importation and acceptance of air oil separators.
- Regional Compliance: Buyers must ensure that products meet local regulations, which may require additional certifications beyond international standards.
- Documentation: Clear documentation is vital for customs clearance and compliance verification. Buyers should ensure that suppliers provide all necessary certifications and testing reports.
By being informed about manufacturing processes and quality assurance practices, B2B buyers can make better decisions when sourcing air oil separators, ensuring that they procure reliable and compliant products for their operations.
Practical Sourcing Guide: A Step-by-Step Checklist for ‘air oil separator’
Introduction
In the quest for efficient industrial operations, procuring the right air oil separator is essential for optimizing performance and ensuring environmental compliance. This step-by-step checklist is designed to guide international B2B buyers, particularly from Africa, South America, the Middle East, and Europe, through the sourcing process. By following these actionable steps, you can make informed decisions that align with your operational needs and budget.
Step 1: Define Your Technical Specifications
Before engaging suppliers, clarify the technical requirements for your air oil separator. This includes understanding the flow rate, pressure drop, and the type of oil to be separated.
- Flow Rate: Determine the volume of air that needs treatment to select a separator capable of handling your operational demands.
- Pressure Drop: A lower pressure drop can lead to energy savings, thus impacting your overall operating costs.
Step 2: Research Potential Suppliers
Conduct thorough research to identify reputable suppliers in the market. Utilize online platforms, industry directories, and trade fairs to compile a list of candidates.
- Supplier Reputation: Look for suppliers with a track record in your industry. Reviews and testimonials can provide insight into their reliability.
- Geographic Considerations: Consider suppliers that are strategically located to reduce shipping times and costs, especially when sourcing from regions like Europe or the Middle East.
Step 3: Evaluate Supplier Certifications
Verify that potential suppliers hold relevant certifications that guarantee product quality and compliance with industry standards.
- ISO Certification: This indicates adherence to international quality management standards, which is crucial for ensuring reliability.
- Environmental Certifications: Certifications such as ISO 14001 demonstrate a commitment to environmental management, which is increasingly important for regulatory compliance.
Step 4: Request Technical Proposals
Once you have shortlisted suppliers, request detailed technical proposals that outline their product offerings. This step is vital for comparing features and pricing.
- Specification Comparison: Analyze each proposal against your defined specifications to ensure compatibility.
- Customization Options: Inquire about the possibility of customizing the separator to meet specific operational needs, which can enhance performance.
Step 5: Assess After-Sales Support
The quality of after-sales support can significantly impact your operations. Assess the level of service offered by suppliers post-purchase.
- Warranty and Maintenance Services: Understand the warranty period and the availability of maintenance services to ensure long-term support.
- Technical Assistance: Check if the supplier provides technical support for installation and troubleshooting, which can minimize downtime.
Step 6: Negotiate Pricing and Payment Terms
Engage in negotiations to secure favorable pricing and payment terms. This step is essential for maintaining budgetary control.
- Volume Discounts: Ask about discounts for bulk purchases, which can lead to significant savings.
- Payment Flexibility: Explore options such as staggered payments or financing solutions that align with your cash flow.
Step 7: Finalize the Order and Confirm Delivery
After selecting the supplier, finalize your order by confirming the delivery schedule and logistics.
- Delivery Timeline: Ensure the supplier can meet your project timelines to avoid disruptions in operations.
- Shipping Arrangements: Clarify who is responsible for shipping costs and any potential customs duties, especially for international transactions.
By following this checklist, B2B buyers can effectively navigate the procurement process for air oil separators, ensuring they select a supplier that meets their technical and operational requirements while also providing value for money.
Comprehensive Cost and Pricing Analysis for air oil separator Sourcing
Understanding the cost structure and pricing dynamics of air oil separators is crucial for international B2B buyers, especially those from Africa, South America, the Middle East, and Europe, including regions like Saudi Arabia and the UAE. This section will break down the components of cost, factors influencing pricing, and provide strategic tips for effective procurement.
What Are the Key Components of Cost for Air Oil Separators?
-
Materials: The primary materials used in air oil separators include high-grade steel, aluminum, and various polymers. Prices for these materials can fluctuate based on global supply chains and commodity markets, influencing the final cost significantly.
-
Labor Costs: Labor costs vary by region. For instance, manufacturing in regions with lower labor costs can lead to reduced overall pricing, while high-wage areas may see increased costs. Additionally, skilled labor for assembly and quality control can add to the expenses.
-
Manufacturing Overhead: This includes expenses related to utilities, factory maintenance, and equipment depreciation. High overhead can result in higher pricing for the end product, particularly in developed markets.
-
Tooling: The initial investment in tooling, which is necessary for the production of air oil separators, can be substantial. This cost is often amortized over large production runs, meaning larger orders can yield lower per-unit costs.
-
Quality Control (QC): Rigorous QC processes are essential to ensure product reliability, particularly in industries where air oil separators are critical. The costs associated with testing and certification can impact overall pricing.
-
Logistics: Shipping costs, including freight, customs duties, and insurance, are significant, especially for international transactions. These costs can vary widely depending on the shipping method and distance.
-
Margin: Suppliers typically add a profit margin to cover their operational costs and provide a return on investment. Margins can vary based on the competitive landscape and the perceived value of the product.
What Influences Pricing for Air Oil Separators?
-
Volume and Minimum Order Quantity (MOQ): Larger orders often result in lower per-unit costs due to economies of scale. Understanding the supplier’s MOQ can help buyers negotiate better pricing.
-
Specifications and Customization: Custom designs and specifications can increase costs. Buyers should clearly communicate their requirements to avoid unexpected charges.
-
Material Choices: The choice of materials can significantly affect pricing. High-performance materials may incur higher costs, but they can also provide better longevity and efficiency.
-
Quality and Certifications: Products that meet specific industry standards or possess certifications (such as ISO) may come at a premium. However, these certifications often translate into reduced maintenance costs and improved reliability.
-
Supplier Factors: The reputation and reliability of suppliers can influence pricing. Established suppliers with a proven track record may charge higher prices but offer better service and quality assurance.
-
Incoterms: Understanding the Incoterms (International Commercial Terms) is vital as they define the responsibilities of buyers and sellers concerning shipping, insurance, and tariffs, which can impact total costs.
How Can Buyers Optimize Their Sourcing Strategy for Air Oil Separators?
-
Negotiate Effectively: Buyers should approach negotiations with a clear understanding of the cost structure and market prices. Leverage volume purchasing to negotiate better terms.
-
Focus on Total Cost of Ownership (TCO): Instead of solely considering the purchase price, evaluate the TCO, which includes maintenance, operation, and disposal costs. This approach can lead to more informed purchasing decisions.
-
Be Aware of Pricing Nuances: International buyers should account for currency fluctuations, import duties, and local taxes that can affect the final cost.
-
Consider Supplier Relationships: Building long-term relationships with suppliers can lead to better pricing and preferential treatment in times of high demand.
-
Stay Informed: Regularly monitor market trends and material costs to anticipate price changes. This knowledge can aid in timing purchases for optimal pricing.
Conclusion
By understanding the comprehensive cost structure and pricing dynamics of air oil separators, international B2B buyers can make informed decisions that enhance their procurement strategies. Careful consideration of the factors influencing costs and pricing, along with strategic negotiation and relationship management, can lead to significant savings and improved operational efficiency.
Alternatives Analysis: Comparing air oil separator With Other Solutions
Exploring Viable Alternatives to Air Oil Separators
When considering solutions for separating oil from air in various industrial applications, the air oil separator stands out due to its efficiency and reliability. However, there are alternative technologies and methods that may be more suitable depending on specific operational needs and constraints. Below, we compare the air oil separator against two viable alternatives: coalescing filters and centrifugal separators.
Comparison Aspect | Air Oil Separator | Coalescing Filter | Centrifugal Separator |
---|---|---|---|
Performance | High efficiency in oil removal (up to 99%) | Effective for small droplets, less effective for larger particles | Moderate efficiency, depends on flow rate and design |
Cost | Moderate initial investment, low operating costs | Lower initial cost but potentially higher long-term filter replacement costs | Higher initial investment, but low operational costs |
Ease of Implementation | Requires specific installation and calibration | Easy to install, minimal modifications needed | Installation may require significant space and alignment considerations |
Maintenance | Minimal maintenance; periodic filter replacement | Regular filter changes needed, can be labor-intensive | Requires infrequent maintenance; regular checks for efficiency |
Best Use Case | Ideal for pneumatic systems and compressors | Suitable for applications with low oil concentrations | Best for high-volume applications with larger oil droplets |
What Are the Benefits and Drawbacks of Coalescing Filters?
Coalescing filters operate by using a media that promotes the merging of small oil droplets into larger ones, which can then be easily removed. One of the main advantages of coalescing filters is their lower initial cost and relatively simple installation process, making them an attractive option for businesses looking to minimize upfront expenditures. However, they do require more frequent maintenance due to the need for regular filter changes, which can lead to increased labor costs over time. Additionally, their effectiveness diminishes with larger oil droplets, making them less suitable for high-viscosity applications.
How Do Centrifugal Separators Compare to Air Oil Separators?
Centrifugal separators utilize high-speed rotation to separate oil from air based on density differences. They are particularly effective for applications with larger oil droplets and can handle high volumes of air. While they have a higher initial investment compared to air oil separators, their low maintenance and operational costs make them an appealing long-term option. However, the complexity of installation and the need for precise alignment may pose challenges in certain industrial settings. Additionally, their efficiency can vary significantly based on the design and flow rates, which may lead to inconsistent performance.
Conclusion: Which Solution is Right for Your Business?
Choosing the right solution for oil separation involves a careful assessment of operational needs, budget constraints, and maintenance capabilities. Air oil separators provide high efficiency and low maintenance, making them a strong choice for many applications. Coalescing filters may be more suitable for businesses looking to minimize initial costs, while centrifugal separators excel in high-volume scenarios where larger droplets are present. B2B buyers should evaluate their specific requirements, including the nature of the fluids involved, the required efficiency levels, and the total cost of ownership, to make an informed decision that aligns with their operational goals.
Essential Technical Properties and Trade Terminology for air oil separator
What Are the Essential Technical Properties of Air Oil Separators?
When evaluating air oil separators, it’s crucial to understand the technical specifications that influence performance and suitability for various applications. Here are some key properties to consider:
1. Material Grade
The material grade of an air oil separator directly affects its durability and resistance to corrosion. Common materials include stainless steel and aluminum. Stainless steel offers excellent corrosion resistance, making it ideal for harsh environments, while aluminum is lighter and can be more cost-effective. Selecting the right material ensures longevity and reliability, reducing the need for frequent replacements.
2. Separation Efficiency
Separation efficiency refers to the percentage of oil that the separator can remove from the air stream. This is typically expressed as a percentage, with higher values indicating better performance. A separator with a high separation efficiency minimizes oil carryover, which can lead to operational issues and increased maintenance costs. For B2B buyers, understanding this specification helps in choosing a product that meets regulatory and operational standards.
3. Tolerance Levels
Tolerance levels define the acceptable limits for dimensions and performance characteristics of the air oil separator. Precise tolerances ensure that the separator fits properly within the system and operates effectively. Tighter tolerances may be required in high-performance applications, where even minor deviations can lead to inefficiencies. Knowledge of tolerance specifications is essential for ensuring compatibility with existing equipment.
4. Operating Temperature Range
The operating temperature range indicates the temperatures within which the air oil separator can function effectively. It is vital for ensuring that the separator performs optimally under varying environmental conditions. B2B buyers should consider the temperature conditions of their specific applications to select a separator that can handle the expected range, thereby preventing potential failures.
5. Flow Rate Capacity
Flow rate capacity measures the volume of air that can pass through the separator per unit of time, typically expressed in cubic feet per minute (CFM). A separator with a higher flow rate capacity can accommodate larger systems or processes without reducing efficiency. For businesses scaling operations, understanding the flow rate capacity is crucial for selecting the right equipment to match production needs.
Which Trade Terminology Should B2B Buyers Know When Purchasing Air Oil Separators?
Understanding industry terminology is essential for navigating B2B transactions effectively. Here are some common terms:
1. OEM (Original Equipment Manufacturer)
OEM refers to a company that produces parts or equipment that may be marketed by another manufacturer. For buyers, sourcing from reputable OEMs ensures quality and compatibility with existing systems, as these manufacturers adhere to industry standards.
2. MOQ (Minimum Order Quantity)
MOQ is the smallest quantity of a product that a supplier is willing to sell. Understanding MOQ is critical for budgeting and inventory management, particularly for international buyers who may face shipping and storage constraints.
3. RFQ (Request for Quotation)
An RFQ is a document that a buyer sends to suppliers to request pricing for specific products or services. By issuing an RFQ, buyers can compare prices and terms from multiple suppliers, ensuring they make informed purchasing decisions.
4. Incoterms (International Commercial Terms)
Incoterms are a set of rules that define the responsibilities of buyers and sellers in international transactions. Familiarity with these terms helps buyers understand shipping costs, risks, and delivery responsibilities, which can vary significantly across different regions, including Africa, South America, the Middle East, and Europe.
5. Lead Time
Lead time refers to the amount of time it takes from placing an order to receiving the product. Understanding lead times is essential for planning and ensuring that equipment is available when needed, especially in industries where downtime can lead to significant losses.
Conclusion
By grasping these essential technical properties and trade terminologies, international B2B buyers can make well-informed decisions when sourcing air oil separators. This knowledge not only enhances the purchasing process but also contributes to operational efficiency and cost-effectiveness in their respective industries.
Navigating Market Dynamics and Sourcing Trends in the air oil separator Sector
What Are the Current Market Dynamics and Key Trends in the Air Oil Separator Sector?
The air oil separator market is witnessing significant growth, driven by increasing industrialization and the need for efficient oil-water separation technologies. Key global drivers include stringent environmental regulations and a growing emphasis on reducing carbon footprints, particularly in regions like Europe, the Middle East, and parts of Africa and South America. International B2B buyers are increasingly seeking advanced air oil separators that enhance operational efficiency and comply with these regulations.
Emerging trends in B2B sourcing within this sector include the adoption of smart technologies and automation. Manufacturers are integrating IoT capabilities into air oil separators, allowing for real-time monitoring and predictive maintenance, which can significantly reduce operational downtime and maintenance costs. Additionally, sustainability is becoming a critical factor in purchasing decisions, as companies aim to align with green initiatives and corporate social responsibility goals.
For buyers in Africa, South America, and the Middle East, the shift towards localized sourcing is also evident. This trend helps mitigate supply chain risks and fosters economic growth within these regions. In Europe, the focus is on advanced filtration technologies that can handle diverse oil types while maintaining high separation efficiency. Understanding these dynamics will enable international buyers to make informed sourcing decisions that align with both market demands and regulatory requirements.
How Is Sustainability Influencing B2B Sourcing in the Air Oil Separator Sector?
Sustainability has emerged as a cornerstone of modern B2B sourcing strategies, particularly in the air oil separator market. The environmental impact of manufacturing and disposing of these systems has prompted buyers to seek solutions that not only perform efficiently but also minimize ecological footprints. This shift is largely driven by increased consumer awareness and regulatory pressures aimed at reducing industrial waste and emissions.
Ethical sourcing is gaining traction as companies prioritize suppliers who demonstrate commitment to sustainable practices. This includes using recyclable materials, reducing energy consumption during production, and ensuring fair labor practices throughout the supply chain. Certifications such as ISO 14001 (Environmental Management Systems) and Green Seal are becoming essential for suppliers to secure contracts with environmentally-conscious buyers.
Moreover, the use of ‘green’ materials in the production of air oil separators—such as biodegradable lubricants and non-toxic coatings—can significantly enhance product appeal. B2B buyers are encouraged to assess their suppliers’ sustainability credentials and consider the lifecycle impact of the products they source. This holistic approach not only supports environmental goals but also boosts brand reputation and customer loyalty in an increasingly eco-conscious market.
What Is the Historical Context of the Air Oil Separator Market?
The evolution of air oil separators can be traced back to the early 20th century when industrial processes began to recognize the need for efficient separation of oil from air and water. Initially, these systems were rudimentary, primarily consisting of simple mechanical filters that struggled with oil emulsification and varying operational conditions.
As industries grew and environmental regulations tightened, the demand for more sophisticated solutions surged. By the late 20th century, technological advancements led to the development of centrifugal and coalescing separators, which provided improved separation efficiencies and reliability. Today, the market features advanced models equipped with digital monitoring capabilities, reflecting a significant leap in both functionality and design.
This historical context underscores the importance of innovation in the air oil separator sector, as manufacturers continuously adapt to meet evolving industrial needs and environmental standards. Understanding this evolution helps B2B buyers appreciate the technological advancements available and make informed decisions when sourcing air oil separators.
Frequently Asked Questions (FAQs) for B2B Buyers of air oil separator
-
How do I solve issues with air oil separator efficiency?
To enhance the efficiency of an air oil separator, regularly check and maintain the unit, including replacing filters and ensuring proper drainage. Evaluate the operating conditions to confirm they align with the manufacturer’s specifications. If efficiency remains low, consider upgrading to a more advanced model or consulting with the supplier for optimization techniques tailored to your specific application. -
What is the best air oil separator for my industrial application?
The ideal air oil separator depends on your industry and specific needs. For heavy-duty applications, consider separators designed for high flow rates and robust filtration capabilities. Evaluate factors such as operating temperature, pressure drop, and compatibility with existing equipment. Consulting with suppliers who understand your industry can provide valuable insights into the best options available. -
How can I ensure the quality of air oil separators from international suppliers?
To ensure quality, conduct thorough supplier vetting. Check for certifications such as ISO 9001 and review customer testimonials. Request samples or product specifications before placing large orders. Establish clear quality assurance protocols, including inspection upon receipt and regular performance evaluations to ensure the separators meet your operational standards. -
What are the typical minimum order quantities (MOQ) for air oil separators?
Minimum order quantities for air oil separators can vary significantly by supplier and product type, typically ranging from 10 to 100 units. It’s essential to discuss your requirements directly with suppliers to negotiate terms that fit your needs, especially if you are a smaller business or entering a new market. -
What payment terms should I expect when sourcing air oil separators internationally?
Payment terms can vary widely but often include options like 30% upfront and 70% upon delivery or net 30 days post-invoice. It’s advisable to negotiate terms that suit your cash flow, and consider using secure payment methods like letters of credit for larger transactions to mitigate risk. -
How can I customize air oil separators for my specific needs?
Customization options typically include size, filtration efficiency, and materials used in construction. Discuss your requirements with potential suppliers, as many manufacturers offer tailored solutions. Provide detailed specifications regarding your application to ensure the customizations meet operational demands. -
What logistics considerations should I keep in mind when importing air oil separators?
When importing, consider shipping methods, transit times, and potential customs duties. Work with logistics partners experienced in your region to ensure smooth transport and compliance with local regulations. It’s also wise to factor in lead times for manufacturing and delivery to avoid operational disruptions. -
What are the common maintenance practices for air oil separators?
Regular maintenance practices include inspecting and replacing filters, checking for leaks, and ensuring proper drainage. Develop a maintenance schedule based on the manufacturer’s recommendations and your operational environment. Documenting maintenance activities can help track performance and identify areas for improvement.
Important Disclaimer & Terms of Use
⚠️ Important Disclaimer
The information provided in this guide, including content regarding manufacturers, technical specifications, and market analysis, is for informational and educational purposes only. It does not constitute professional procurement advice, financial advice, or legal advice.
While we have made every effort to ensure the accuracy and timeliness of the information, we are not responsible for any errors, omissions, or outdated information. Market conditions, company details, and technical standards are subject to change.
B2B buyers must conduct their own independent and thorough due diligence before making any purchasing decisions. This includes contacting suppliers directly, verifying certifications, requesting samples, and seeking professional consultation. The risk of relying on any information in this guide is borne solely by the reader.
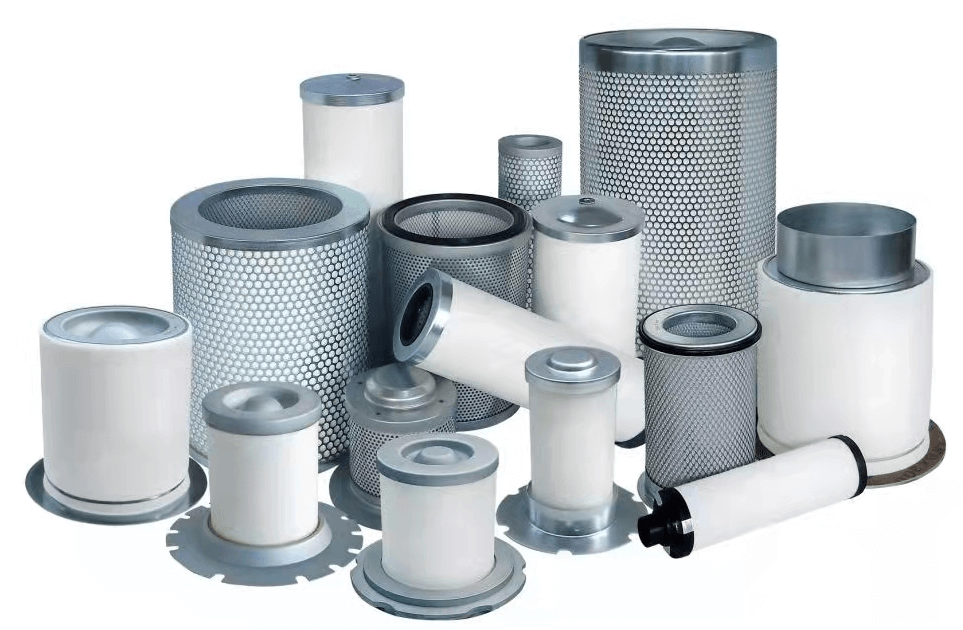
A stock image related to air oil separator.
Strategic Sourcing Conclusion and Outlook for air oil separator
As international B2B buyers, particularly from Africa, South America, the Middle East, and Europe, understanding the strategic sourcing of air oil separators is critical for optimizing operational efficiency and reducing costs. The key takeaways from this guide highlight the importance of selecting high-quality components that not only meet regulatory standards but also enhance the longevity and performance of your machinery. By leveraging strategic sourcing, companies can ensure they are making informed purchasing decisions that align with their operational goals.
Investing in reliable air oil separators translates to improved equipment reliability, reduced maintenance costs, and enhanced environmental compliance. For buyers in regions like Saudi Arabia and the UAE, where industrial growth is rapid, focusing on quality sourcing can significantly impact your competitive edge in the market.
Looking ahead, the demand for advanced air oil separator technologies is set to grow, propelled by increasing industrialization and environmental regulations. We encourage international B2B buyers to actively engage with suppliers, explore innovative solutions, and build partnerships that foster sustainable growth. Now is the time to align your sourcing strategies with industry advancements to ensure your operations remain ahead of the curve.