Cut Costs with Cutter Machine Cloth: The Ultimate Guide (2025)
Introduction: Navigating the Global Market for cutter machine cloth
Navigating the complexities of sourcing cutter machine cloth can be a daunting challenge for international B2B buyers, especially in diverse regions such as Africa, South America, the Middle East, and Europe. The fabric’s performance, durability, and cost-effectiveness are critical factors that can significantly impact production efficiency and product quality. This guide offers a comprehensive overview of the global market for cutter machine cloth, covering various types, applications, and the nuances of supplier vetting.
As an international buyer, understanding the specific requirements of your industry—be it textile manufacturing, automotive, or upholstery—will empower you to make informed purchasing decisions. The guide delves into essential aspects such as evaluating supplier credibility, comparing pricing structures, and recognizing quality indicators that ensure you choose the right material for your needs.
Moreover, it highlights regional considerations that may affect your sourcing strategy, including trade regulations and local market trends. By equipping you with actionable insights and best practices, this guide aims to streamline your procurement process and help you navigate the global landscape confidently. Whether you are seeking to optimize production costs or enhance product quality, the knowledge contained herein is designed to support your strategic sourcing efforts effectively.
Understanding cutter machine cloth Types and Variations
Type Name | Key Distinguishing Features | Primary B2B Applications | Brief Pros & Cons for Buyers |
---|---|---|---|
Cotton Cutter Cloth | Soft texture, high absorbency, biodegradable | Apparel manufacturing, upholstery, crafts | Pros: Cost-effective, versatile; Cons: Less durable than synthetic options. |
Polyester Cutter Cloth | High tensile strength, water-resistant, durable | Industrial applications, automotive, textiles | Pros: Long-lasting, resistant to wear; Cons: Less breathable than natural fibers. |
Canvas Cutter Cloth | Heavyweight, rugged, thick weave | Outdoor gear, bags, protective covers | Pros: Extremely durable, weather-resistant; Cons: Can be bulky and rigid. |
Nylon Cutter Cloth | Lightweight, strong, abrasion-resistant | Fashion, sportswear, outdoor equipment | Pros: Lightweight, high strength-to-weight ratio; Cons: Can be expensive compared to cotton. |
Silk Cutter Cloth | Smooth, luxurious feel, lightweight | High-end fashion, accessories, interior design | Pros: Elegant appearance, soft texture; Cons: High maintenance, costlier than other options. |
What are the characteristics of Cotton Cutter Cloth and its suitability for B2B buyers?
Cotton cutter cloth is characterized by its soft texture and high absorbency, making it an ideal choice for a variety of applications such as apparel manufacturing and upholstery. As a biodegradable material, it appeals to eco-conscious businesses. B2B buyers should consider its cost-effectiveness and versatility, especially for products that require comfort. However, its durability is less than that of synthetic options, which may be a concern for high-traffic applications.
How does Polyester Cutter Cloth stand out for industrial applications?
Polyester cutter cloth is known for its high tensile strength and water-resistant properties, making it suitable for demanding industrial applications. It is commonly used in automotive and textile industries where durability is paramount. Buyers should appreciate its long-lasting nature and resistance to wear, which can lead to lower replacement costs over time. However, its reduced breathability compared to natural fibers may limit its use in certain apparel applications.
What makes Canvas Cutter Cloth a go-to choice for outdoor products?
Canvas cutter cloth is distinguished by its heavyweight and rugged structure, making it an excellent choice for outdoor gear, bags, and protective covers. Its durability and weather-resistant properties appeal to businesses that require robust materials for outdoor use. While its strength is a significant advantage, the bulkiness and rigidity can be a drawback for applications requiring flexibility. Buyers should assess the balance between durability and ease of use based on their specific needs.
Why consider Nylon Cutter Cloth for fashion and outdoor equipment?
Nylon cutter cloth is lightweight yet strong, offering abrasion resistance that is particularly beneficial in fashion and outdoor equipment. Its high strength-to-weight ratio makes it an appealing option for businesses looking to minimize material weight without sacrificing durability. However, buyers should be aware that nylon can be more expensive than cotton, which may affect budget considerations. The application context will dictate whether the investment is justified.
What are the benefits and drawbacks of using Silk Cutter Cloth in high-end markets?
Silk cutter cloth is recognized for its smooth, luxurious feel and lightweight nature, making it a popular choice in high-end fashion and accessories. It delivers an elegant appearance that can enhance product value in the luxury market. However, B2B buyers should consider the high maintenance requirements and cost associated with silk, which may not align with all business models. Its suitability is primarily for niche markets that can support premium pricing.
Related Video: 2024 Best Laser Cutting Machine for Fabric, Textile and Garment
Key Industrial Applications of cutter machine cloth
Industry/Sector | Specific Application of cutter machine cloth | Value/Benefit for the Business | Key Sourcing Considerations for this Application |
---|---|---|---|
Textile Manufacturing | Fabric cutting for garments and upholstery | Increases efficiency and precision in cutting processes | Quality of cloth, compatibility with machinery, cost-effectiveness |
Automotive Industry | Cutting of interior textiles for vehicles | Enhances quality and durability of vehicle interiors | Compliance with safety standards, durability of material, supplier reliability |
Furniture Production | Upholstery cutting for furniture | Reduces waste and improves design accuracy | Availability of various fabric types, lead times, and bulk pricing |
Home Décor | Cutting curtains and drapes | Facilitates customization and faster production | Color and pattern options, material quality, and shipping logistics |
Fashion Design | Prototype cutting for clothing collections | Speeds up the design process and reduces errors | Fabric type, supplier reputation, and responsiveness to orders |
How is Cutter Machine Cloth Used in Textile Manufacturing?
In the textile manufacturing sector, cutter machine cloth is essential for the efficient cutting of fabrics used in garments and upholstery. It provides the necessary durability and precision to handle various materials, which is crucial for maintaining high production standards. For international B2B buyers, particularly those in Africa and South America, sourcing high-quality cutter machine cloth can lead to reduced fabric waste and improved cutting accuracy, ultimately enhancing overall production efficiency.
What Role Does Cutter Machine Cloth Play in the Automotive Industry?
The automotive industry utilizes cutter machine cloth for cutting interior textiles, such as seat covers and headliners. This application is vital as it ensures that the materials not only fit perfectly but also meet safety and durability standards. B2B buyers from the Middle East and Europe need to consider the compliance of cutter machine cloth with automotive standards, ensuring it withstands wear and tear while providing aesthetic appeal.
How is Cutter Machine Cloth Applied in Furniture Production?
In furniture production, cutter machine cloth is used to cut upholstery materials for chairs, sofas, and other furniture items. This application significantly reduces waste and enhances the accuracy of designs, allowing for more complex patterns and styles. International buyers, especially from Europe, should focus on the availability of diverse fabric types and the ability of suppliers to meet bulk orders without compromising quality.
What Benefits Does Cutter Machine Cloth Offer for Home Décor?
Cutter machine cloth is also employed in the home décor sector for cutting fabrics used in curtains and drapes. This allows for customization, as buyers can select specific designs and materials to match their interior themes. For buyers in Africa and South America, ensuring that the sourced cutter machine cloth offers a variety of color and pattern options, along with efficient shipping logistics, is crucial for timely project completion.
How Does Cutter Machine Cloth Assist Fashion Designers?
For fashion designers, cutter machine cloth is integral for prototyping clothing collections. It allows designers to quickly create patterns and samples, speeding up the overall design process while reducing potential errors. B2B buyers in the fashion industry, particularly from Australia and Indonesia, should prioritize sourcing cloth that is versatile and compatible with various fabric types to facilitate innovative designs and rapid prototyping.
Related Video: Use of the Fly Cutter on the Milling Machine
3 Common User Pain Points for ‘cutter machine cloth’ & Their Solutions
Scenario 1: Sourcing Quality Cutter Machine Cloth for Different Fabrics
The Problem:
Many B2B buyers struggle with sourcing cutter machine cloth that is suitable for various fabric types, especially when working across diverse markets like Africa and Europe. The challenge lies in understanding the specifications required for different textiles, which can result in suboptimal cutting performance, fabric damage, or increased waste. This issue is compounded by the lack of standardized quality across suppliers, leading to inconsistent results and dissatisfied customers.
The Solution:
To effectively address this pain point, buyers should engage in thorough supplier vetting. Start by creating a checklist of specifications based on the types of fabrics you frequently work with. Key factors to consider include the cloth’s thickness, durability, and compatibility with specific cutting machines. Prioritize suppliers who can provide detailed technical sheets and samples for testing before making bulk orders. Additionally, consider suppliers who offer customized solutions, allowing you to specify the exact requirements for your operations. Establishing a trial phase with selected suppliers can also help in assessing the performance of the cutter machine cloth on actual projects, minimizing the risk of poor-quality purchases.
Scenario 2: Managing Inventory Levels of Cutter Machine Cloth
The Problem:
International B2B buyers often face challenges in managing their inventory of cutter machine cloth, particularly in fluctuating market conditions. Over-ordering can lead to excess stock, while under-ordering can halt production lines, causing delays and financial losses. This becomes especially problematic in regions with inconsistent shipping times, such as parts of South America and Africa, where lead times can vary significantly.
The Solution:
Implementing an inventory management system that incorporates predictive analytics can help mitigate this issue. By analyzing historical usage patterns and current market trends, businesses can better forecast their cloth requirements. Additionally, establish relationships with multiple suppliers to create a buffer system—this way, if one supplier has extended lead times, another can provide the necessary materials without disruption. Regular audits of inventory levels and usage rates will also assist in adjusting orders proactively. Leveraging technology for real-time tracking of inventory can provide insights into usage trends, enabling more informed purchasing decisions.
Scenario 3: Ensuring Compliance with International Standards
The Problem:
Compliance with international standards for cutter machine cloth is a significant concern for B2B buyers, especially when exporting goods to different countries. Each region may have varying regulations regarding the materials used, affecting the entire supply chain. Non-compliance can lead to costly fines, product recalls, and damage to reputation, particularly for companies operating in Europe and the Middle East.
The Solution:
To navigate compliance challenges, buyers should conduct a comprehensive review of the regulatory requirements for the regions they operate in. This includes understanding the specific standards for materials, safety regulations, and environmental impacts associated with cutter machine cloth. Partnering with suppliers who have a proven track record of compliance can streamline this process. Additionally, consider investing in compliance training for your procurement team to keep them updated on the latest regulations. Regularly reviewing supplier certifications and requesting documentation can also provide peace of mind that the materials sourced meet the necessary international standards, thus minimizing the risk of compliance-related issues.
Strategic Material Selection Guide for cutter machine cloth
What Are the Key Properties of Common Materials for Cutter Machine Cloth?
When selecting materials for cutter machine cloth, it is essential to understand the properties that directly influence performance. Here, we analyze four common materials used in this application: polyester, nylon, cotton, and aramid fibers. Each material has unique characteristics that can impact durability, cost, and suitability for specific applications.
How Does Polyester Perform as a Cutter Machine Cloth Material?
Polyester is a synthetic material known for its durability and resistance to shrinking and stretching. It can withstand moderate temperatures and has good abrasion resistance, making it suitable for various cutting applications. Its low moisture absorption also helps maintain dimensional stability under varying conditions.
Pros: Polyester is cost-effective and widely available, making it a popular choice for many manufacturers. It is also relatively easy to work with, which reduces manufacturing complexity.
Cons: While polyester offers decent durability, it may not perform well under extreme temperatures or harsh chemical exposure, limiting its use in specialized applications.
Impact on Application: Polyester is compatible with a variety of media, including paper, textiles, and some plastics. However, it may not be suitable for cutting materials that generate high heat or require high precision.
What Advantages Does Nylon Offer for Cutter Machine Cloth?
Nylon is another synthetic option that excels in strength and flexibility. It has a high melting point and excellent resistance to abrasion, making it ideal for high-performance cutting tasks. Nylon’s elasticity allows it to maintain its shape under stress, which is beneficial for applications requiring precision.
Pros: The high durability and resistance to wear make nylon a preferred choice for heavy-duty applications. Its ability to withstand high temperatures also enhances its versatility.
Cons: Nylon can be more expensive than polyester and may require more complex manufacturing processes. Additionally, it has a higher moisture absorption rate, which can affect its performance in humid environments.
Impact on Application: Nylon is particularly effective for cutting tougher materials, such as leather and rubber, due to its strength. However, international buyers should be aware of its limitations regarding moisture sensitivity.
Why Choose Cotton for Cutter Machine Cloth?
Cotton is a natural fiber known for its softness and breathability. While it may not be as durable as synthetic options, it is often chosen for applications requiring a softer touch or less friction.
Pros: Cotton is biodegradable and environmentally friendly, appealing to companies focused on sustainable practices. It is also relatively inexpensive and easy to source.
Cons: Cotton has lower abrasion resistance and can degrade more quickly than synthetic materials, making it less suitable for heavy-duty applications.
Impact on Application: Cotton is ideal for cutting softer materials or applications requiring a gentle touch, such as in the garment industry. However, its performance may be compromised in high-stress environments.
What Are the Benefits of Using Aramid Fibers in Cutter Machine Cloth?
Aramid fibers, such as Kevlar, are known for their exceptional strength-to-weight ratio and heat resistance. They are often used in high-performance applications where durability and safety are paramount.
Pros: Aramid fibers offer outstanding resistance to abrasion and cutting, making them ideal for use in protective gear and high-stress cutting environments.
Cons: The cost of aramid fibers is significantly higher than other materials, which may not be feasible for all budgets. Additionally, their manufacturing process can be complex.
Impact on Application: Aramid fibers are suitable for cutting applications that involve high temperatures or hazardous materials. International buyers should ensure compliance with safety standards relevant to their region.
Summary Table of Material Properties for Cutter Machine Cloth
Material | Typical Use Case for cutter machine cloth | Key Advantage | Key Disadvantage/Limitation | Relative Cost (Low/Med/High) |
---|---|---|---|---|
Polyester | General cutting applications | Cost-effective and widely available | Limited performance in extreme conditions | Low |
Nylon | Heavy-duty cutting tasks | High durability and temperature resistance | Higher cost and moisture sensitivity | Medium |
Cotton | Soft material cutting | Biodegradable and environmentally friendly | Lower durability and abrasion resistance | Low |
Aramid Fibers | High-performance cutting | Exceptional strength and heat resistance | High cost and complex manufacturing | High |
This guide aims to equip international B2B buyers with the necessary insights to make informed decisions regarding the selection of cutter machine cloth materials, considering both performance and compliance with regional standards.
In-depth Look: Manufacturing Processes and Quality Assurance for cutter machine cloth
What Are the Key Manufacturing Processes for Cutter Machine Cloth?
Understanding the manufacturing process of cutter machine cloth is crucial for international B2B buyers looking to ensure quality and reliability in their supply chains. The production typically involves several stages: material preparation, forming, assembly, and finishing.
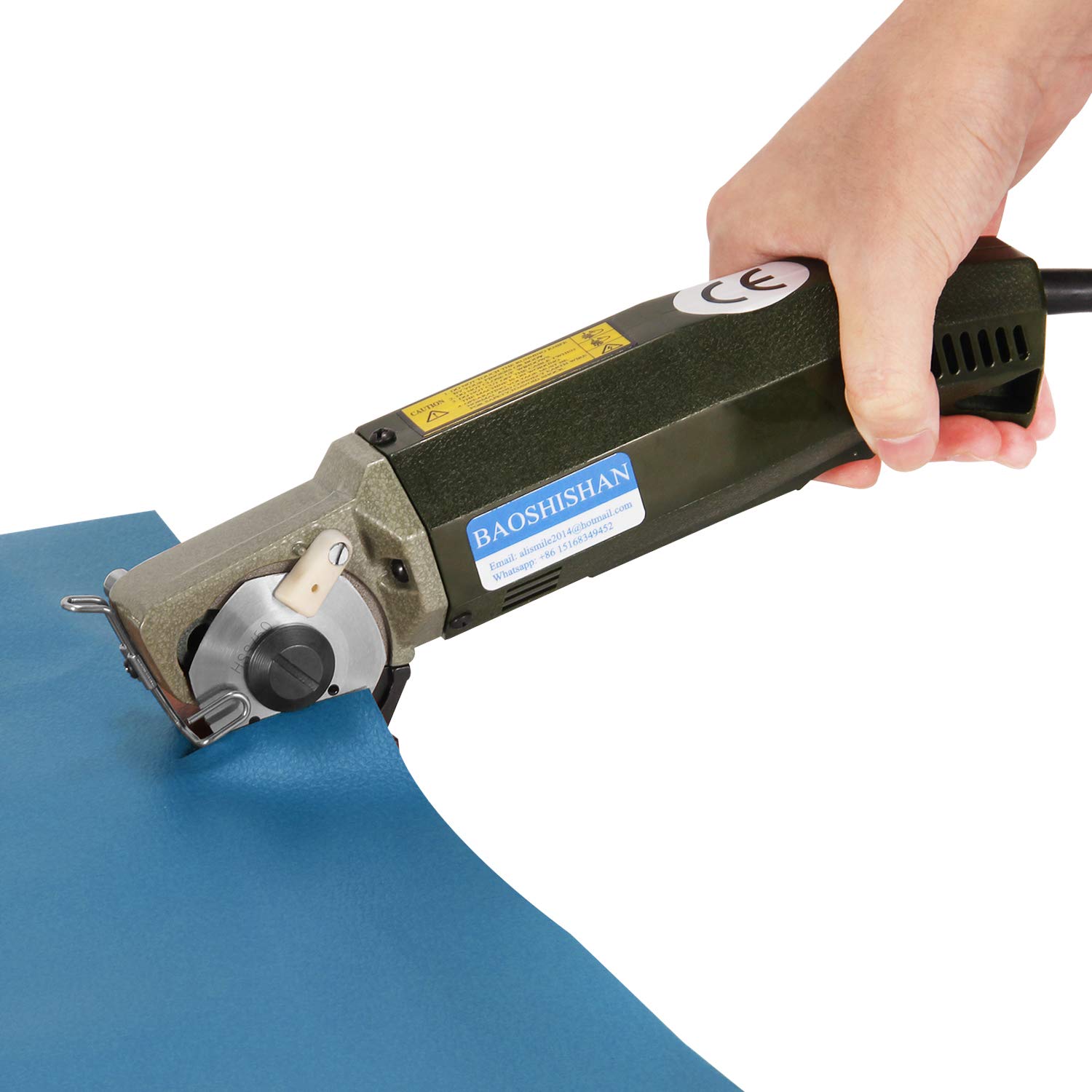
A stock image related to cutter machine cloth.
How Is Material Prepared in the Production of Cutter Machine Cloth?
The first step in the manufacturing process is material preparation, where the primary materials—such as high-quality synthetic fibers or natural textiles—are sourced and inspected. Buyers should verify that suppliers use materials that meet international standards for durability and performance. This phase may include:
- Sourcing: Suppliers should provide documentation on the origin of materials, ensuring they comply with local and international regulations.
- Inspection: Incoming materials undergo quality control checks (IQC) to ensure they meet specified standards, such as tensile strength and resistance to wear.
What Techniques Are Used in Forming Cutter Machine Cloth?
Once materials are prepared, the next step is forming, which involves converting raw materials into fabric through various techniques. Common methods include:
- Weaving or Knitting: Depending on the desired properties of the cloth, either weaving or knitting techniques are employed. Weaving typically provides greater strength and durability, while knitting offers flexibility and comfort.
- Coating: Some cutter machine cloths may undergo a coating process to enhance properties like water resistance or grip, which is essential for specific applications.
This stage is critical for establishing the physical properties of the cloth, impacting its performance in industrial applications.
What Is the Assembly Process for Cutter Machine Cloth?
The assembly stage involves cutting the fabric into specified dimensions and integrating any additional components, such as backing materials or reinforcement layers.
- Cutting: Precision cutting tools are utilized to ensure accuracy in dimensions, which is vital for proper machine integration.
- Sewing or Bonding: Depending on the design, pieces may be sewn together or bonded using adhesives or heat, enhancing the durability of the final product.
Buyers should pay attention to the assembly techniques used, as they can significantly affect the final product’s quality and usability.
How Is Finishing Completed for Cutter Machine Cloth?
Finishing processes are crucial for enhancing the final appearance and performance characteristics of the cutter machine cloth. This stage may involve:
- Dyeing: If color is a requirement, the cloth may undergo dyeing processes. Buyers should confirm that dyes used are environmentally friendly and compliant with safety regulations.
- Treatment: Additional treatments may be applied to improve properties like fire resistance or anti-static capabilities.
The finishing stage is the final opportunity to ensure the product meets the specific needs of the end user.
What Quality Assurance Measures Should Be in Place?
Quality assurance (QA) is a vital aspect of the manufacturing process for cutter machine cloth, ensuring that products meet both industry standards and buyer specifications. Here are key elements of QA to consider:
Which International Standards Are Relevant for Cutter Machine Cloth?
Buyers should be familiar with relevant international standards, such as:
- ISO 9001: This standard focuses on quality management systems and is essential for suppliers aiming to enhance customer satisfaction through effective processes.
- CE Marking: Particularly relevant for products sold in Europe, CE marking indicates compliance with health, safety, and environmental protection standards.
- API Standards: For specific applications in industries like oil and gas, API standards ensure that the cloth meets rigorous performance criteria.
Understanding these standards can help buyers assess supplier credibility and product reliability.
What Are the Critical QC Checkpoints in the Manufacturing Process?
Quality control checkpoints are integral to maintaining standards throughout the manufacturing process. Key checkpoints include:
- Incoming Quality Control (IQC): Inspection of raw materials upon arrival to ensure they meet specifications.
- In-Process Quality Control (IPQC): Ongoing checks during production to identify defects early.
- Final Quality Control (FQC): Comprehensive inspection of the finished product before shipment, ensuring it meets all specifications.
These checkpoints help in minimizing defects and ensuring the final product’s quality.
How Can B2B Buyers Verify Supplier Quality Control?
B2B buyers must take proactive steps to verify the quality control processes of their suppliers. Here are actionable strategies:
- Conduct Audits: Regular audits of supplier facilities can provide insights into their manufacturing practices and adherence to quality standards.
- Request Quality Reports: Suppliers should provide detailed reports on quality control tests conducted, including results and methodologies.
- Engage Third-Party Inspectors: Utilizing independent inspection services can offer an unbiased assessment of the supplier’s quality control processes.
These actions help mitigate risks associated with sourcing materials from international suppliers, particularly in regions like Africa, South America, the Middle East, and Europe.
What Are the Nuances of Quality Control for International B2B Buyers?
International B2B buyers should be aware of specific nuances in quality control when dealing with suppliers from different regions.
- Cultural Differences: Understanding local manufacturing practices and cultural attitudes towards quality can influence supplier relationships.
- Regulatory Compliance: Ensure that suppliers comply with both local regulations and international standards, as discrepancies can lead to significant issues.
- Communication: Maintaining clear and consistent communication regarding quality expectations can help bridge gaps and build stronger partnerships.
By considering these factors, buyers can enhance their procurement strategies and ensure they receive high-quality cutter machine cloth tailored to their specific needs.
Practical Sourcing Guide: A Step-by-Step Checklist for ‘cutter machine cloth’
In the competitive landscape of B2B sourcing, particularly for cutter machine cloth, establishing a systematic approach is vital for achieving optimal procurement outcomes. This guide provides a practical checklist to assist international buyers from Africa, South America, the Middle East, and Europe in making informed decisions when sourcing cutter machine cloth.
Step 1: Define Your Technical Specifications
Clearly outline the technical requirements for the cutter machine cloth you intend to purchase. This includes material type, thickness, durability, and any specific performance characteristics required for your applications.
– Why It Matters: Accurate specifications help ensure that you receive products that meet your operational needs, reducing the risk of costly reorders or production delays.
Step 2: Conduct Market Research
Investigate the market to identify potential suppliers. Utilize online resources, industry directories, and trade shows to gather information on companies that specialize in cutter machine cloth.
– What to Look For: Assess supplier reputation, product variety, and geographical presence, focusing on those with a strong track record in your target region.
Step 3: Evaluate Potential Suppliers
Before committing, it’s crucial to vet suppliers thoroughly. Request company profiles, case studies, and references from buyers in a similar industry or region.
– Key Actions:
– Analyze their production capacity and lead times.
– Check for certifications that demonstrate compliance with international quality standards, such as ISO 9001.
Step 4: Request Samples for Testing
Always ask for samples of the cutter machine cloth before finalizing your order. This allows you to evaluate the material’s quality and suitability for your specific applications.
– Why This Is Important: Testing samples can prevent future issues related to product performance and ensure that the cloth meets your expectations.
Step 5: Negotiate Pricing and Terms
Once you have selected a few potential suppliers, initiate negotiations on pricing, payment terms, and delivery schedules. Transparency in these discussions can lead to better deals and long-term partnerships.
– Considerations:
– Discuss bulk order discounts if applicable.
– Ensure clarity on shipping costs and import duties, especially for international transactions.
Step 6: Verify Supplier Certifications
Ensure that your selected suppliers hold relevant certifications that guarantee their products meet international standards. This is particularly crucial for buyers in regulated industries.
– What to Check: Look for certifications related to quality management, environmental standards, and safety protocols. This adds an extra layer of assurance regarding product integrity.
Step 7: Establish Communication Channels
Set up clear communication channels with your chosen suppliers. Regular updates on order status, shipping, and any potential issues are essential for maintaining a smooth procurement process.
– Best Practices: Use a project management tool or a dedicated communication platform to keep all stakeholders informed and accountable throughout the sourcing process.
By following this practical checklist, B2B buyers can streamline their sourcing of cutter machine cloth, ensuring they make informed decisions that align with their operational needs and business goals.
Comprehensive Cost and Pricing Analysis for cutter machine cloth Sourcing
What are the Key Cost Components in Cutter Machine Cloth Sourcing?
When sourcing cutter machine cloth, understanding the cost structure is essential for effective budgeting and decision-making. The primary cost components include:
-
Materials: The type of fabric and its quality significantly influence the overall cost. High-performance materials, such as specialized synthetic fibers, tend to be more expensive but offer enhanced durability and efficiency.
-
Labor: Labor costs can vary widely based on geographic location and the complexity of the manufacturing process. Countries with lower labor costs may offer attractive pricing, but it is crucial to assess the quality of workmanship to avoid long-term issues.
-
Manufacturing Overhead: This encompasses all indirect costs associated with production, including utilities, equipment maintenance, and factory rent. Efficient manufacturing practices can help mitigate these costs.
-
Tooling: Depending on the specific design and features of the cutter machine cloth, tooling costs may be incurred. Custom tooling can increase initial costs but can lead to long-term savings through improved production efficiency.
-
Quality Control (QC): Implementing a robust QC process ensures that the materials meet required standards. While this adds to the upfront costs, it reduces the risk of defects and returns, making it a worthwhile investment.
-
Logistics: Shipping and handling costs should not be overlooked. Factors such as distance, mode of transport, and the chosen Incoterms can significantly impact the final price.
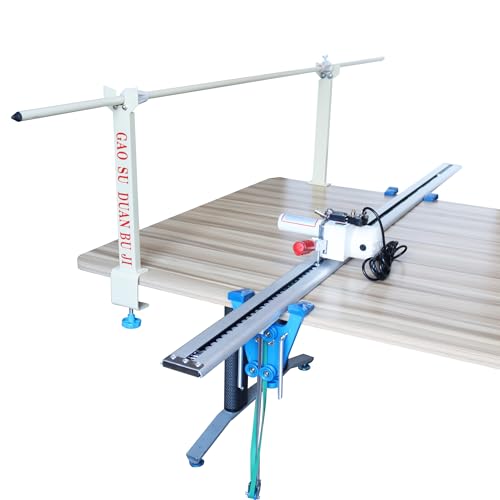
A stock image related to cutter machine cloth.
- Margin: Suppliers typically add a margin to cover their costs and profit. Understanding the market rate for these margins can help buyers negotiate better deals.
What Influences Pricing for Cutter Machine Cloth?
Several factors influence the pricing of cutter machine cloth, particularly in an international B2B context:
-
Volume and Minimum Order Quantity (MOQ): Suppliers often provide tiered pricing based on order volume. Higher quantities usually lead to lower per-unit costs. It’s advisable to negotiate MOQs to optimize pricing.
-
Specifications and Customization: Customized products may incur additional costs due to unique requirements in design or material. Clearly defining specifications upfront can prevent unexpected expenses later.
-
Material Quality and Certifications: Higher quality materials and certifications (such as ISO or specific industry standards) can increase costs but may enhance product performance and marketability.
-
Supplier Factors: The supplier’s reputation, location, and production capacity play a critical role in pricing. Established suppliers with a track record of quality may command higher prices but offer peace of mind regarding reliability.
-
Incoterms: Understanding Incoterms is vital for managing logistics costs. Options like FOB (Free on Board) or CIF (Cost, Insurance, and Freight) can affect the total landed cost of goods.
What are Effective Buyer Tips for Cost-Efficiency in Cutter Machine Cloth Sourcing?
International B2B buyers should consider the following strategies to enhance cost-efficiency when sourcing cutter machine cloth:
-
Negotiation Tactics: Engage suppliers in open discussions about pricing and terms. Leverage competitive quotes from multiple suppliers to negotiate better deals without compromising quality.
-
Total Cost of Ownership (TCO): Evaluate the TCO rather than just the purchase price. This includes factoring in shipping, handling, and potential maintenance costs. A lower initial cost might result in higher long-term expenses.
-
Pricing Nuances for International Buyers: Be aware of currency fluctuations and local tariffs, which can impact overall pricing. Establishing contracts in stable currencies or considering forward contracts can mitigate risks.
-
Market Research: Stay informed about market trends and pricing benchmarks. Understanding the competitive landscape can empower buyers to make informed decisions and negotiate effectively.
-
Supplier Relationship Management: Building long-term relationships with suppliers can lead to better pricing, priority service, and improved communication. Consider strategic partnerships that can yield mutual benefits over time.
Disclaimer on Indicative Prices
It is essential to note that prices for cutter machine cloth can vary widely based on the factors discussed above. Buyers should conduct thorough research and obtain multiple quotes to ensure competitive pricing tailored to their specific needs.
Alternatives Analysis: Comparing cutter machine cloth With Other Solutions
Understanding Alternative Solutions to Cutter Machine Cloth
In the realm of fabric cutting and textile processing, the choice of material can significantly influence operational efficiency, cost-effectiveness, and overall output quality. As B2B buyers evaluate their options, it is crucial to consider not only cutter machine cloth but also viable alternatives that may better suit specific production needs. Below, we will compare cutter machine cloth against two prominent alternatives: Laser Cutting Technology and Rotary Cutting Systems.
Comparison Aspect | Cutter Machine Cloth | Laser Cutting Technology | Rotary Cutting Systems |
---|---|---|---|
Performance | High precision and durability | Exceptional accuracy, intricate designs | Good for bulk cutting, moderate accuracy |
Cost | Moderate initial investment | High initial setup costs | Lower initial costs, but operational costs can add up |
Ease of Implementation | Simple setup and operation | Requires skilled personnel, more complex setup | User-friendly, easy to integrate |
Maintenance | Regular cleaning required | Low maintenance but costly repairs | Moderate maintenance; blades need regular replacement |
Best Use Case | Ideal for diverse fabric types | Best for intricate designs and patterns | Best for large-scale, high-volume cutting |
What Are the Advantages and Disadvantages of Laser Cutting Technology?
Laser Cutting Technology offers significant advantages in terms of precision and the ability to cut complex designs without physical contact with the material. This technology employs a focused laser beam to melt or vaporize the fabric, leading to clean edges and minimal fraying. However, the initial setup costs for laser cutting machines can be prohibitively high for smaller operations. Additionally, this method requires skilled personnel for operation and maintenance, which may increase overall operational costs in the long run.
Why Consider Rotary Cutting Systems Over Cutter Machine Cloth?
Rotary Cutting Systems utilize circular blades that spin to cut fabric, making them particularly effective for high-volume production runs. They are user-friendly and can be easily integrated into existing workflows, which is attractive for companies looking to streamline their operations. However, while they are generally less expensive to purchase than laser cutters, the ongoing costs associated with blade replacements can accumulate. Moreover, rotary systems may not achieve the same level of precision as cutter machine cloth, especially for intricate patterns.
How to Choose the Right Solution for Your Business Needs?
When selecting the appropriate cutting solution, B2B buyers should evaluate their specific operational requirements, budget constraints, and desired output quality. If precision and intricate designs are paramount, investing in laser cutting technology may be justified despite higher upfront costs. Conversely, for businesses focused on high-volume production with moderate accuracy, rotary cutting systems can offer an effective balance of cost and functionality. Cutter machine cloth remains a strong contender for its versatility across various fabric types and ease of use, making it a reliable choice for many textile operations.
In conclusion, understanding the strengths and weaknesses of each alternative enables buyers to make informed decisions tailored to their specific needs, ensuring optimal production efficiency and cost management.
Essential Technical Properties and Trade Terminology for cutter machine cloth
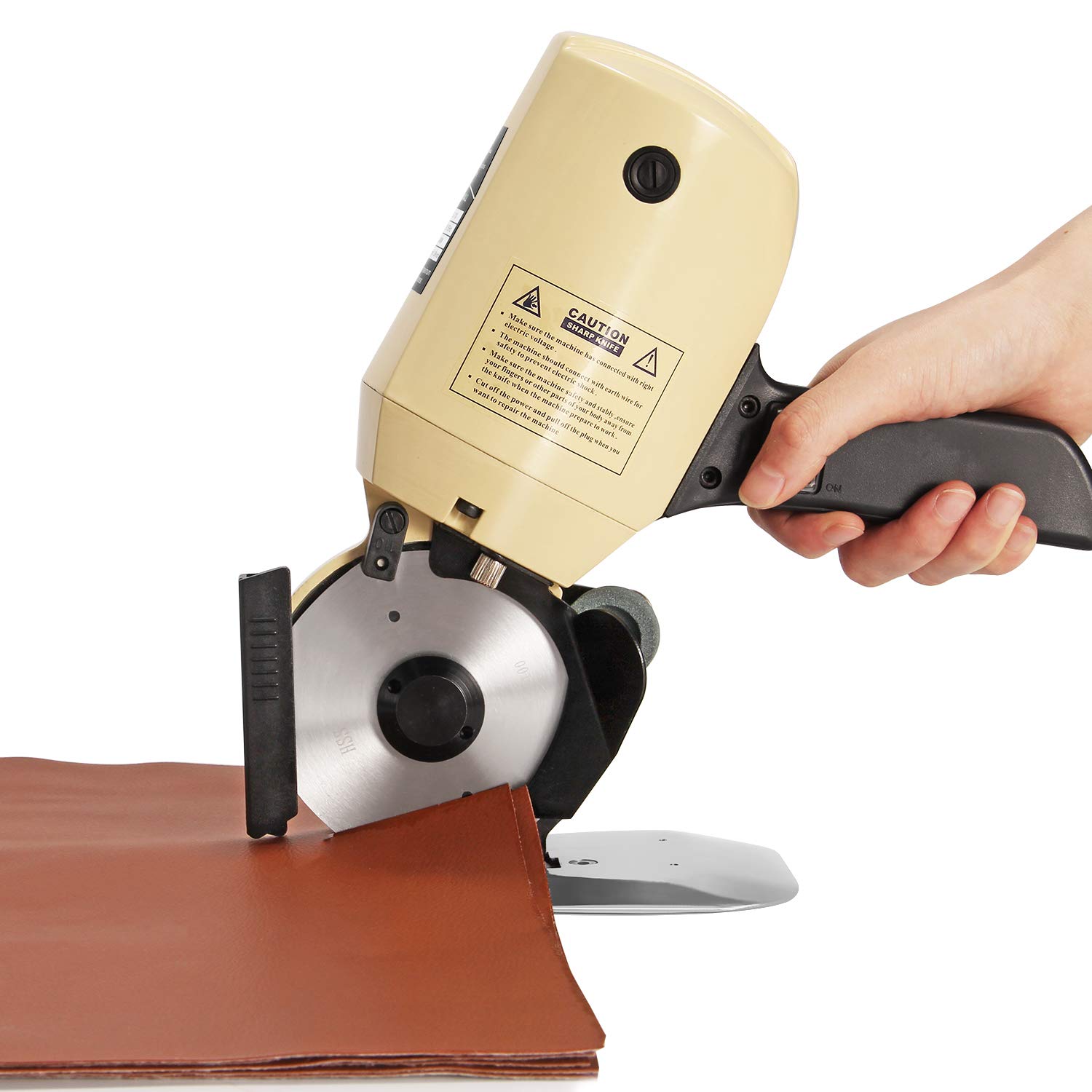
A stock image related to cutter machine cloth.
What Are the Key Technical Properties of Cutter Machine Cloth?
Cutter machine cloth is essential for various industries, particularly in manufacturing and textile production. Understanding its technical properties can significantly influence purchasing decisions and operational efficiency. Here are some critical specifications to consider:
-
Material Grade
– The material grade of cutter machine cloth typically refers to the quality and type of fabric used, such as cotton, polyester, or specialized synthetic blends. Higher-grade materials often offer better durability and performance. For B2B buyers, selecting the appropriate material grade is vital as it directly impacts the lifespan of the cloth and the overall production quality. -
Tolerance Levels
– Tolerance levels define the acceptable variations in size and dimensions of the cutter machine cloth. These specifications are crucial for ensuring that the cloth fits the machinery accurately and operates without issues. Inaccurate tolerances can lead to production delays and increased costs, making it essential for buyers to verify these measurements before purchase. -
Weight and Density
– The weight (measured in grams per square meter, or GSM) and density of the cloth are significant indicators of its strength and suitability for specific applications. Heavier and denser fabrics typically provide more durability, making them suitable for high-intensity operations. B2B buyers should assess these properties to ensure the cloth meets the demands of their production processes. -
Abrasion Resistance
– This property measures how well the cloth can withstand wear and tear from cutting tools and machinery. High abrasion resistance is essential for maintaining the integrity of the cloth over time, especially in high-volume manufacturing environments. Buyers in industries such as textiles or automotive should prioritize this feature to minimize replacement costs. -
Chemical Resistance
– Depending on the operational environment, the cutter machine cloth may need to resist various chemicals and solvents. Chemical resistance is vital for ensuring that the cloth does not degrade when exposed to harsh substances, maintaining its functionality and safety. B2B buyers must evaluate this property based on their specific industrial needs.
What Are Common Trade Terminologies Associated with Cutter Machine Cloth?
Familiarizing oneself with industry jargon is crucial for effective communication and negotiation in B2B transactions. Here are some common trade terms relevant to cutter machine cloth:
-
OEM (Original Equipment Manufacturer)
– This term refers to companies that produce components or products that are sold under another company’s brand. In the context of cutter machine cloth, understanding OEM relationships can help buyers source high-quality materials tailored to their specific machinery. -
MOQ (Minimum Order Quantity)
– MOQ is the smallest quantity of product that a supplier is willing to sell. This term is crucial for B2B buyers as it affects inventory management and cost efficiency. Knowing the MOQ helps in planning purchases and negotiating better terms with suppliers. -
RFQ (Request for Quotation)
– An RFQ is a document sent to suppliers to invite them to bid on specific products or services. B2B buyers should prepare detailed RFQs to ensure they receive accurate quotes that include all necessary specifications and terms. -
Incoterms (International Commercial Terms)
– These are standardized trade terms that define the responsibilities of buyers and sellers in international transactions. Understanding Incoterms is essential for managing shipping, insurance, and liability, which can vary significantly based on the agreed terms. -
Lead Time
– Lead time refers to the amount of time from placing an order to receiving the product. This term is crucial for B2B buyers to understand, as it impacts production schedules and inventory management. Buyers should discuss lead times with suppliers to ensure timely deliveries. -
Certification Standards
– Certification standards, such as ISO or ASTM, indicate that the cutter machine cloth meets specific quality and safety benchmarks. Buyers should seek suppliers who adhere to these standards to ensure they are purchasing reliable and compliant materials.
By understanding these essential technical properties and trade terminologies, international B2B buyers can make informed decisions when sourcing cutter machine cloth, ultimately leading to enhanced operational efficiency and cost savings.
Navigating Market Dynamics and Sourcing Trends in the cutter machine cloth Sector
What are the Current Market Dynamics and Sourcing Trends in the Cutter Machine Cloth Sector?
The cutter machine cloth sector is experiencing significant growth, driven by several global factors. The increasing demand for precision in manufacturing processes, especially in the textile and apparel industries, is pushing for advanced cutter machine technologies. Automation and digitization are among the leading trends, with companies adopting smart technologies to enhance efficiency and reduce labor costs. This shift is particularly pronounced in regions like Africa and South America, where manufacturers are looking to modernize their operations to compete globally.
Emerging technologies such as Industry 4.0 and the Internet of Things (IoT) are transforming sourcing strategies. International B2B buyers are increasingly seeking suppliers that can provide integrated solutions, including software and hardware, that enable real-time monitoring and data analytics. Furthermore, the integration of AI in cutter machines is becoming a game-changer, allowing for better predictive maintenance and minimizing downtime.
Market dynamics also reflect a growing interest in local sourcing, particularly in the Middle East and Europe. Buyers are looking for suppliers who can offer shorter lead times and greater flexibility in production. This trend is reshaping supply chains, encouraging partnerships with local manufacturers, which also helps mitigate risks associated with global logistics disruptions.
How Does Sustainability Impact Sourcing in the Cutter Machine Cloth Sector?
Sustainability has emerged as a crucial consideration for international B2B buyers in the cutter machine cloth sector. The environmental impact of traditional manufacturing practices has prompted a shift towards more sustainable methods. Buyers are increasingly prioritizing suppliers who demonstrate a commitment to reducing their carbon footprint and using eco-friendly materials.
Ethical sourcing is becoming a non-negotiable aspect of supplier selection. Buyers are demanding transparency in supply chains, ensuring that materials used in cutter machines are sourced responsibly. Certifications such as Global Organic Textile Standard (GOTS) and OEKO-TEX are gaining importance, as they provide assurance of environmentally friendly and socially responsible practices.
Moreover, the use of recycled materials in manufacturing cutter machine cloth is on the rise. Not only does this contribute to waste reduction, but it also appeals to consumers who are increasingly conscious of sustainability. B2B buyers should actively seek partnerships with suppliers who are investing in green technologies and sustainable practices, as this aligns with global trends towards responsible consumption.
How Has the Cutter Machine Cloth Sector Evolved Over Time?
The cutter machine cloth sector has evolved significantly over the decades, transitioning from manual cutting techniques to highly automated solutions. Initially, the focus was primarily on mechanical efficiency, but advancements in technology have shifted the emphasis towards precision and versatility. The introduction of computer-aided design (CAD) systems in the 1980s marked a pivotal moment, allowing for intricate designs and more efficient material usage.
In recent years, the sector has seen an increased integration of digital technologies, enabling features such as automated fabric spreading and cutting that dramatically reduce waste. This evolution reflects the broader trends in manufacturing, where digital transformation is reshaping how businesses operate. As the market continues to evolve, international B2B buyers must stay informed of technological advancements and adapt their sourcing strategies to leverage these innovations effectively.
Frequently Asked Questions (FAQs) for B2B Buyers of cutter machine cloth
-
How do I choose the right cutter machine cloth for my business needs?
When selecting cutter machine cloth, consider the specific materials you will be cutting and the machine type you are using. Assess the cloth’s durability, thickness, and compatibility with your cutting equipment. Additionally, evaluate the cloth’s resistance to fraying and wear over time. It’s beneficial to request samples from suppliers to test the cloth’s performance in your operational environment before making a bulk purchase. -
What factors should I consider when sourcing cutter machine cloth internationally?
When sourcing cutter machine cloth internationally, consider supplier reliability, quality certifications, and shipping logistics. Investigate the supplier’s production capabilities and adherence to international quality standards. It’s essential to understand the import regulations in your country, including tariffs and duties. Establish clear communication regarding timelines and payment terms to avoid potential delays or misunderstandings. -
How can I ensure the quality of cutter machine cloth from international suppliers?
To ensure quality, vet potential suppliers by requesting product certifications and references from previous customers. Implement quality assurance measures such as third-party inspections before shipment. Establish a clear quality control process that includes specifications on fabric weight, thickness, and tensile strength. Regular audits of the supplier’s production facilities can also help maintain quality standards. -
What is the minimum order quantity (MOQ) for cutter machine cloth?
Minimum order quantities for cutter machine cloth can vary widely among suppliers. Typically, MOQs range from 50 to several hundred meters, depending on the supplier’s production capacity and the type of fabric. Discuss your needs with potential suppliers to negotiate MOQs that align with your business requirements while ensuring cost-effectiveness. -
What payment terms should I expect when buying cutter machine cloth internationally?
Payment terms can differ based on supplier policies and your negotiation outcomes. Common terms include 30% upfront payment with the balance due upon delivery or a letter of credit. It’s crucial to clarify these terms before finalizing orders to avoid cash flow issues. Consider using secure payment methods that offer buyer protection, especially when dealing with new suppliers. -
How can I customize cutter machine cloth to meet my specific requirements?
Customization options for cutter machine cloth often include fabric weight, color, and specific dimensions. Many suppliers offer bespoke services, but it’s essential to communicate your needs clearly and early in the negotiation process. Request samples of customized options to assess their suitability for your cutting needs. Be prepared for potential minimum order requirements for custom products. -
What are the common shipping options for cutter machine cloth, and how do I choose the right one?
Shipping options for cutter machine cloth typically include air freight, sea freight, and express courier services. The choice depends on your budget, urgency, and destination. Air freight is faster but more expensive, suitable for smaller, high-value orders. Sea freight is cost-effective for larger volumes but takes longer. Assess your timeline and budget to select the most appropriate shipping method. -
What are the best practices for managing logistics when importing cutter machine cloth?
Effective logistics management involves planning your supply chain from the supplier to your location. Ensure you have a reliable freight forwarder who can handle customs clearance and documentation. Track shipments closely to anticipate delays and maintain clear communication with your supplier. Consider setting up a local warehouse if you frequently import to streamline operations and reduce lead times.
Important Disclaimer & Terms of Use
⚠️ Important Disclaimer
The information provided in this guide, including content regarding manufacturers, technical specifications, and market analysis, is for informational and educational purposes only. It does not constitute professional procurement advice, financial advice, or legal advice.
While we have made every effort to ensure the accuracy and timeliness of the information, we are not responsible for any errors, omissions, or outdated information. Market conditions, company details, and technical standards are subject to change.
B2B buyers must conduct their own independent and thorough due diligence before making any purchasing decisions. This includes contacting suppliers directly, verifying certifications, requesting samples, and seeking professional consultation. The risk of relying on any information in this guide is borne solely by the reader.
Strategic Sourcing Conclusion and Outlook for cutter machine cloth
As international B2B buyers navigate the complexities of sourcing cutter machine cloth, the strategic sourcing process remains paramount. By understanding regional market dynamics, identifying reliable suppliers, and establishing strong negotiation tactics, businesses can secure high-quality materials that enhance production efficiency. Key takeaways include the importance of assessing supplier capabilities, fostering relationships for long-term collaboration, and leveraging technology to streamline procurement processes.
How Can Strategic Sourcing Enhance Your Competitive Advantage?
Investing in strategic sourcing not only reduces costs but also improves product quality and delivery timelines, which are critical factors in maintaining a competitive edge in diverse markets such as Africa, South America, the Middle East, and Europe. As demand for innovative cutting solutions continues to grow, aligning with suppliers who are committed to sustainability and innovation will be essential.
What’s Next for International B2B Buyers?
Looking ahead, international buyers should prioritize building adaptable sourcing strategies that can respond to fluctuating market conditions. Engaging in industry forums and trade events can offer valuable insights into emerging trends and new technologies. By embracing a proactive sourcing approach, businesses can navigate future challenges and seize new opportunities in the cutter machine cloth market. Start exploring your strategic sourcing options today to ensure your business remains at the forefront of the industry.