Cut Costs with Plastic Chair Chairs: The Ultimate Buying Guide (2025)
Introduction: Navigating the Global Market for plastic chair chairs
In today’s competitive landscape, sourcing high-quality plastic chair chairs that meet both aesthetic and functional requirements can be a daunting challenge for international B2B buyers. Whether you are searching for ergonomic seating solutions for office environments or durable outdoor chairs for hospitality venues, the decision-making process is often complicated by varying material qualities, supplier reliability, and fluctuating costs. This comprehensive guide is designed to empower decision-makers in Africa, South America, the Middle East, and Europe—regions where the demand for versatile and sustainable seating options is rapidly growing.
Throughout this guide, we will delve into the different types of plastic used in chair manufacturing, exploring their unique properties and applications. From understanding the nuances of materials like polypropylene and polyethylene to evaluating supplier vetting processes, our aim is to equip you with the knowledge necessary for making informed purchasing decisions. Additionally, we will analyze cost factors, market trends, and environmental considerations, ensuring that you can choose products that align with both your budget and sustainability goals.
By the end of this guide, international B2B buyers will be better positioned to navigate the complexities of the global market for plastic chair chairs, fostering confidence in their procurement choices and ultimately enhancing their business operations.
Understanding plastic chair chairs Types and Variations
Type Name | Key Distinguishing Features | Primary B2B Applications | Brief Pros & Cons for Buyers |
---|---|---|---|
Stackable Chairs | Lightweight, space-saving, easy to transport | Event venues, offices, schools | Pros: Cost-effective, versatile; Cons: May lack durability compared to heavier models. |
Reclining Chairs | Adjustable backrest, ergonomic design | Waiting areas, lounges, healthcare | Pros: Comfort-focused, enhances user experience; Cons: Higher cost, requires more space. |
Outdoor Chairs | UV-resistant, weatherproof materials | Patios, gardens, outdoor events | Pros: Durable against elements, easy to clean; Cons: Limited color options, can fade over time. |
Folding Chairs | Compact, portable, quick setup | Trade shows, conferences, picnics | Pros: Highly portable, easy storage; Cons: Less stability, may not be suitable for heavy use. |
Designer Chairs | Unique aesthetics, premium materials | High-end offices, luxury settings | Pros: Enhances brand image, durable; Cons: Higher price point, may require longer lead times. |
What Are Stackable Chairs and Their B2B Benefits?
Stackable chairs are designed for efficiency, allowing multiple units to be stacked on top of each other for easy storage and transport. They are ideal for businesses that require flexible seating arrangements, such as event venues, schools, and offices. When purchasing stackable chairs, consider the weight capacity, material quality, and comfort level, as these factors will affect both usability and longevity in high-traffic environments.
How Do Reclining Chairs Enhance Business Spaces?
Reclining chairs are perfect for spaces that prioritize comfort, such as waiting areas in healthcare facilities or lounges in corporate offices. Their ergonomic design supports relaxation, which can improve customer satisfaction and employee well-being. When selecting reclining chairs, assess the adjustability features and overall durability, as these elements are crucial for maintaining a professional environment while catering to comfort.
Why Choose Outdoor Chairs for Business Settings?
Outdoor chairs are constructed from UV-resistant and weatherproof materials, making them suitable for patios, gardens, and outdoor events. They are designed to withstand various environmental conditions, ensuring longevity and ease of maintenance. B2B buyers should consider the chair’s weight, ease of cleaning, and aesthetic appeal to ensure they fit seamlessly into outdoor settings while providing comfort to users.
What Are the Advantages of Folding Chairs in B2B Applications?
Folding chairs are known for their portability and ease of setup, making them ideal for trade shows, conferences, and outdoor picnics. Their compact design allows for efficient storage, which is a significant advantage for businesses with limited space. When selecting folding chairs, it’s essential to evaluate their stability and comfort, as these factors will impact user experience during extended use.
How Do Designer Chairs Impact Brand Perception?
Designer chairs offer a unique aesthetic and are often made from premium materials, making them suitable for high-end offices and luxury settings. They not only enhance the visual appeal of a space but also contribute to a positive brand image. However, B2B buyers should be mindful of the higher price point and lead times associated with these chairs, ensuring that the investment aligns with their overall branding strategy and budget.
Related Video: SEE HOW I TURNED A PLASTIC CHAIR INTO A THRONE CHAIR | DIY CHAIR ON A BUDGET!
Key Industrial Applications of plastic chair chairs
Industry/Sector | Specific Application of Plastic Chair Chairs | Value/Benefit for the Business | Key Sourcing Considerations for this Application |
---|---|---|---|
Hospitality | Restaurant and Café Seating | Durable, easy to clean, and weather-resistant. | Ensure UV resistance and weight capacity specifications. |
Education | Classroom and Lecture Hall Furniture | Lightweight, stackable for flexible space usage. | Check for compliance with safety standards and ergonomic design. |
Events and Exhibitions | Temporary Event Seating | Cost-effective for large gatherings and easy transport. | Consider foldability and portability for quick setup. |
Healthcare | Patient Waiting Area Seating | Comfortable and hygienic options for patients. | Look for antimicrobial properties and easy-to-sanitize materials. |
Outdoor Recreation | Park and Recreational Area Seating | Weather-resistant and low maintenance. | Focus on durability against the elements and aesthetic appeal. |
How are Plastic Chair Chairs Used in Hospitality Settings?
In the hospitality industry, plastic chair chairs are essential for restaurants and cafés, where they provide durable and easy-to-clean seating options. These chairs can withstand the wear and tear of high traffic, making them ideal for busy dining environments. International buyers should ensure that the chairs are UV resistant to prevent fading and are designed to support various weight capacities, catering to diverse customer needs.
What is the Role of Plastic Chair Chairs in Educational Institutions?
In educational settings, plastic chair chairs are commonly used in classrooms and lecture halls due to their lightweight and stackable design. This flexibility allows institutions to reconfigure spaces easily for different activities, maximizing usability. Buyers from Africa, South America, and Europe should prioritize chairs that comply with safety standards and offer ergonomic designs to enhance student comfort during long periods of sitting.
How Do Plastic Chair Chairs Benefit Events and Exhibitions?
For events and exhibitions, plastic chair chairs are a go-to solution for temporary seating needs. Their cost-effectiveness allows organizers to accommodate large crowds without overspending. Additionally, the ease of transport and setup makes them ideal for quick arrangements. International buyers should consider the foldability and portability of these chairs to streamline event logistics, ensuring they can be set up and taken down efficiently.
Why are Plastic Chair Chairs Important in Healthcare Environments?
In healthcare settings, patient waiting areas require seating that is both comfortable and hygienic. Plastic chair chairs designed for this sector often feature antimicrobial properties, making them easier to clean and maintain. For B2B buyers in the healthcare industry, sourcing chairs that meet these hygiene standards is critical, as is ensuring they are comfortable enough to enhance the patient experience during their wait.
How are Plastic Chair Chairs Utilized in Outdoor Recreation Areas?
Plastic chair chairs are increasingly popular in parks and recreational areas, where their weather-resistant properties make them suitable for outdoor use. These chairs require minimal maintenance and can withstand various environmental conditions, making them ideal for public spaces. Buyers should focus on sourcing chairs that not only resist fading and deterioration from sunlight and rain but also complement the aesthetic of the outdoor environment, enhancing the overall visitor experience.
Related Video: How Furniture is Made from Recycled Plastic | Made Here | Popular Mechanics
3 Common User Pain Points for ‘plastic chair chairs’ & Their Solutions
Scenario 1: Navigating Quality Assurance in Sourcing Plastic Chairs
The Problem: B2B buyers often face challenges in ensuring the quality and durability of plastic chairs, especially when sourcing from international suppliers. In regions like Africa and South America, where local manufacturers may have varying standards, buyers worry about the longevity and safety of their products. Poor-quality chairs can lead to high replacement costs and customer dissatisfaction, affecting their bottom line and brand reputation.
The Solution: To overcome this issue, buyers should implement a stringent supplier vetting process. Begin by requesting samples from multiple manufacturers to assess material quality and durability firsthand. Pay particular attention to the type of plastic used, such as High-Density Polyethylene (HDPE) or Polypropylene (PP), which are known for their strength and resistance to wear. Additionally, consider suppliers who provide certifications or test reports confirming the chairs meet international safety and quality standards. Establishing a clear communication channel with suppliers can also aid in understanding the production processes and quality control measures they employ.
Scenario 2: Addressing Environmental Concerns with Plastic Chair Chairs
The Problem: In today’s eco-conscious market, B2B buyers are increasingly scrutinizing the environmental impact of the products they source. Plastic chairs, often associated with pollution and waste, can pose a dilemma for businesses aiming to maintain sustainable practices. Buyers from Europe, for instance, face pressure from consumers to adopt more environmentally friendly solutions, which can complicate their purchasing decisions.
The Solution: To navigate these environmental concerns, buyers should prioritize sourcing chairs made from recyclable or biodegradable materials. Look for manufacturers who use recycled plastics or sustainable production methods, such as eco-friendly additives that enhance the recyclability of the chairs. Additionally, inquire about the manufacturer’s recycling program or take-back schemes, which can help mitigate waste. Educating customers about the sustainability features of the plastic chairs can also enhance brand loyalty and marketability. Buyers can even consider engaging with suppliers who are transparent about their environmental impact and commit to continuous improvement in sustainability practices.
Scenario 3: Ensuring Comfort and Ergonomics in Plastic Chair Design
The Problem: Another common pain point for B2B buyers is the comfort level of plastic chairs, particularly in settings where they will be used for extended periods, such as offices or event venues. Chairs that are uncomfortable can lead to decreased productivity and negative experiences for end-users. This is especially crucial for buyers in the Middle East and Europe, where ergonomic standards are highly valued.
The Solution: Buyers should conduct thorough research on ergonomic designs and prioritize chairs that have been tested for comfort. Look for features such as contoured seating, adequate back support, and adjustable components. Request detailed specifications and user feedback from the supplier to gauge comfort levels. Additionally, consider conducting user trials with your target audience to gather firsthand insights into comfort and usability. Providing a range of chair options that cater to different ergonomic needs can also enhance customer satisfaction and retention. By focusing on comfort alongside aesthetics and functionality, buyers can ensure they select plastic chairs that not only meet practical needs but also contribute positively to user experience.
Strategic Material Selection Guide for plastic chair chairs
What Are the Key Properties of Common Materials Used in Plastic Chair Chairs?
When selecting materials for plastic chair chairs, it is essential to understand the properties of various plastics to ensure optimal performance and durability. The most commonly used materials include Polypropylene (PP), High-Density Polyethylene (HDPE), Polyvinyl Chloride (PVC), and Polystyrene (PS). Each material has unique characteristics that can significantly impact the final product’s quality and suitability for specific applications.
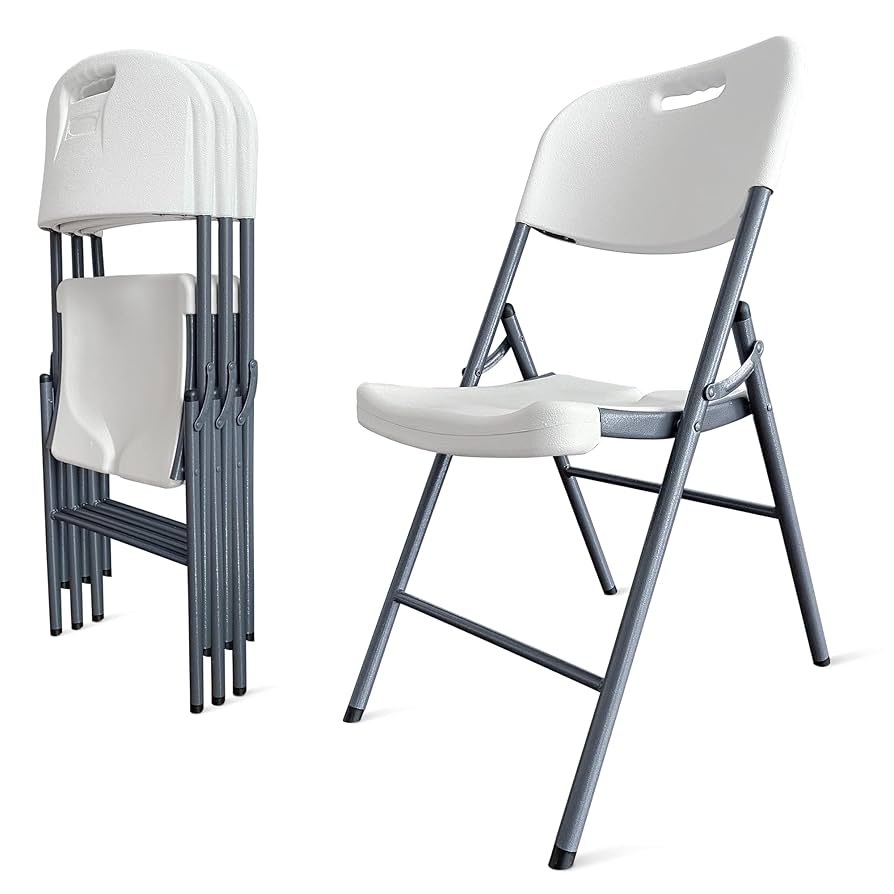
A stock image related to plastic chair chairs.
How Does Polypropylene (PP) Perform in Plastic Chair Chairs?
Polypropylene is known for its excellent fatigue resistance, making it ideal for applications requiring repeated bending, such as chair hinges. It has a high melting point of around 160°C, which allows it to withstand heat without deforming. Furthermore, PP is resistant to many chemicals, making it suitable for various environments.
Pros: PP is lightweight, durable, and easy to mold, allowing for complex designs. It is also recyclable, which aligns with sustainability goals.
Cons: While it is resistant to impact, it can become brittle at lower temperatures. Additionally, its color can fade over time when exposed to UV light.
Impact on Application: PP’s chemical resistance and high-temperature tolerance make it ideal for outdoor chairs or environments where exposure to various substances is common.
Considerations for International Buyers: Buyers in regions like Africa and South America should ensure compliance with local recycling regulations and standards such as ASTM D638 for tensile properties.
What Are the Benefits of Using High-Density Polyethylene (HDPE)?
HDPE is recognized for its strength and resistance to impact, making it a popular choice for plastic chair chairs. It can withstand temperatures up to 120°C and is resistant to various chemicals, including acids and bases.
Pros: HDPE is one of the easiest plastics to recycle and is highly durable, making it suitable for both indoor and outdoor use. Its resistance to moisture prevents mold and mildew growth.
Cons: While HDPE is strong, it can be susceptible to stress cracking under certain conditions. Its surface can also be prone to scratching.
Impact on Application: HDPE’s durability and moisture resistance make it an excellent choice for chairs used in humid environments or outdoor settings.
Considerations for International Buyers: Compliance with recycling standards is crucial, especially in Europe, where regulations are stringent. Buyers should also be aware of local manufacturing capabilities to ensure quality.
Why Is Polyvinyl Chloride (PVC) Less Preferred for Plastic Chair Chairs?
PVC is versatile and can be rigid or flexible, but its use in chair manufacturing is often debated due to environmental concerns. It is resistant to moisture and has good mechanical properties.
Pros: PVC is cost-effective and can be easily processed into various shapes and forms. It is also resistant to fire and weathering.
Cons: PVC is not easily recyclable and can release harmful chemicals during production and disposal. Its rigidity can limit design flexibility.
Impact on Application: While PVC can be used in chair frames, its environmental impact makes it less favorable for sustainable product lines.
Considerations for International Buyers: Buyers should evaluate local regulations regarding PVC use and disposal, especially in regions with strict environmental laws.
What Are the Drawbacks of Using Polystyrene (PS) in Plastic Chair Chairs?
Polystyrene is lightweight and inexpensive, making it a common choice for disposable items. However, its application in durable products like chairs is limited due to its fragility.
Pros: PS is easy to mold and can be produced at a low cost, making it suitable for mass production.
Cons: It is highly flammable and can leach harmful chemicals, especially when heated. Its low impact resistance makes it unsuitable for long-term use.
Impact on Application: PS is generally not recommended for chairs intended for regular use due to its fragility and environmental concerns.
Considerations for International Buyers: Buyers should be cautious about using PS, especially in markets with growing environmental awareness, as it may face regulatory scrutiny.
Summary Table of Material Selection for Plastic Chair Chairs
Material | Typical Use Case for Plastic Chair Chairs | Key Advantage | Key Disadvantage/Limitation | Relative Cost (Low/Med/High) |
---|---|---|---|---|
Polypropylene (PP) | Outdoor and indoor chairs | Excellent fatigue resistance and recyclability | Can become brittle at low temperatures | Medium |
High-Density Polyethylene (HDPE) | Durable outdoor chairs | Moisture resistance and easy recyclability | Susceptible to stress cracking | Medium |
Polyvinyl Chloride (PVC) | Rigid chair frames | Cost-effective and versatile | Not easily recyclable and environmental concerns | Low |
Polystyrene (PS) | Disposable or low-cost chairs | Lightweight and low production cost | Highly flammable and fragile | Low |
This strategic material selection guide provides international B2B buyers with a comprehensive overview of the materials available for plastic chair chairs, allowing them to make informed decisions based on performance, cost, and environmental impact.
In-depth Look: Manufacturing Processes and Quality Assurance for plastic chair chairs
What Are the Key Stages in the Manufacturing Process of Plastic Chair Chairs?
The manufacturing process for plastic chair chairs involves several key stages, each essential for ensuring the final product meets both quality and durability standards. Understanding these stages can help B2B buyers make informed decisions regarding their suppliers.
Material Preparation: How Are Raw Materials Selected and Processed?
The first step in the manufacturing process is the selection and preparation of raw materials. Typically, high-density polyethylene (HDPE) or polypropylene (PP) is chosen for its strength, flexibility, and recyclability. Suppliers must ensure that the plastics used are free from contaminants, which can affect the quality of the final product.
Once selected, the raw materials undergo a drying process to remove any moisture. This is critical as moisture can lead to defects during the molding process. The materials are then compounded with additives to enhance properties like UV resistance, color, and impact strength, ensuring the chairs can withstand various environmental conditions.
What Forming Techniques Are Used to Create Plastic Chair Chairs?
Forming is a crucial stage where the prepared materials are shaped into chair components. The primary techniques include:
-
Injection Molding: This is the most common method for producing plastic chairs. In this process, molten plastic is injected into a mold under high pressure, allowing for complex shapes and designs. This technique is efficient for mass production, providing consistent quality and reducing waste.
-
Blow Molding: Used for hollow chair designs, blow molding involves inflating a heated plastic tube within a mold to form the chair’s body. This method is beneficial for creating lightweight structures.
-
Thermoforming: In this method, plastic sheets are heated until pliable and then formed over molds. This technique is suitable for producing larger chair components and is often used for custom designs.
How Are Plastic Chair Components Assembled?
After the forming process, the various components of the chair, such as the seat, backrest, and legs, are assembled. This can be done manually or using automated systems, depending on the scale of production. The assembly process may involve welding, mechanical fastening, or using adhesives, ensuring that each component fits securely to enhance the chair’s structural integrity.
What Finishing Techniques Are Applied to Enhance Plastic Chair Chairs?
Finishing processes are essential for enhancing the aesthetic appeal and functionality of plastic chairs. Common finishing techniques include:
-
Surface Treatment: This involves applying coatings to improve UV resistance, scratch resistance, and overall durability.
-
Coloring: While some manufacturers use colored plastics, others may apply paint or other finishes to achieve desired aesthetics.
-
Quality Control Checks: Throughout the manufacturing process, quality control checks are integrated to ensure that each chair meets design specifications and performance standards.
What International Quality Standards Should B2B Buyers Be Aware Of?
Quality assurance is vital in manufacturing plastic chair chairs, and compliance with international standards is critical for B2B buyers. Key standards include:
-
ISO 9001: This standard outlines criteria for a quality management system, ensuring that manufacturers consistently meet customer and regulatory requirements.
-
CE Marking: Particularly relevant for European buyers, CE marking indicates that the product complies with EU safety, health, and environmental requirements.
-
API Standards: For chairs used in specialized environments (like healthcare), adherence to specific API standards may be necessary.
What Are the Key Quality Control Checkpoints in the Manufacturing Process?
Quality Control (QC) is integrated at various stages of the manufacturing process, often categorized into three checkpoints:
-
Incoming Quality Control (IQC): This step involves inspecting raw materials and components as they arrive at the manufacturing facility. Ensuring that materials meet specified standards is crucial for preventing defects in the final product.
-
In-Process Quality Control (IPQC): During the manufacturing process, regular checks are conducted to monitor the quality of products at various stages. This may include dimensional checks, visual inspections, and functional tests to ensure compliance with design specifications.
-
Final Quality Control (FQC): At the end of the production line, final inspections are performed. This includes checking for defects, verifying dimensions, and conducting performance tests. Chairs that pass these checks are approved for packaging and shipment.
How Can B2B Buyers Verify Supplier Quality Control Practices?
For international B2B buyers, especially in regions like Africa, South America, the Middle East, and Europe, verifying a supplier’s quality control practices is essential. Here are some actionable steps:
-
Conduct Audits: Regular audits of potential suppliers can provide insights into their manufacturing processes and quality management systems.
-
Request Quality Assurance Reports: Suppliers should be able to provide documentation demonstrating compliance with international standards and their internal QC procedures.
-
Engage Third-Party Inspectors: Utilizing third-party inspection services can provide an unbiased assessment of the manufacturer’s quality control practices and the quality of the products being produced.
What Are the Nuances of Quality Control for International B2B Buyers?
Navigating quality control nuances is crucial for international B2B buyers. Differences in regional regulations and standards can affect product compliance. For instance:
-
Regional Compliance: Buyers from Europe may prioritize CE marking, while those from Africa may need to consider local standards that may not align with international norms.
-
Cultural Considerations: Understanding the cultural context of suppliers can influence communication and expectations regarding quality. Building strong relationships with suppliers can lead to improved quality outcomes.
-
Sustainability Practices: Increasingly, buyers are looking for suppliers who adhere to sustainable practices. This includes using recyclable materials and minimizing waste during production. Ensure that potential suppliers can demonstrate their commitment to sustainability through certifications or practices.
Conclusion
Understanding the manufacturing processes and quality assurance measures for plastic chair chairs is crucial for B2B buyers. By focusing on the key stages of manufacturing, being aware of international quality standards, and verifying supplier QC practices, buyers can make informed decisions that ensure they procure high-quality products that meet their needs. This knowledge not only aids in selecting reliable suppliers but also helps in building long-term partnerships that can drive business success.
Practical Sourcing Guide: A Step-by-Step Checklist for ‘plastic chair chairs’
In this practical sourcing guide, we aim to equip international B2B buyers—particularly from Africa, South America, the Middle East, and Europe—with a comprehensive checklist for procuring plastic chair chairs. By following these steps, you can ensure a successful purchasing process that meets both your quality and sustainability requirements.
Step 1: Define Your Technical Specifications
Clearly articulating your technical specifications is vital to ensure that the plastic chair chairs meet your operational needs. Consider factors such as size, weight capacity, design, and intended use.
– Materials: Specify the type of plastic (e.g., HDPE, PP) to ensure durability and recyclability.
– Comfort Features: Include considerations for ergonomics if the chairs are intended for long-term use.
Step 2: Research Sustainable Materials and Practices
As environmental concerns continue to grow, sourcing chairs made from sustainable materials is increasingly important. Investigate suppliers that utilize eco-friendly plastics or recycled materials.
– Certifications: Look for products with certifications such as ISO 14001 (Environmental Management) to ensure adherence to sustainability practices.
– Life Cycle Analysis: Request information on the product’s life cycle to understand its environmental impact from production to disposal.
Step 3: Evaluate Potential Suppliers
Before finalizing a purchase, conduct thorough due diligence on potential suppliers. Request detailed company profiles, case studies, and references from other B2B buyers.
– Quality Assurance: Inquire about their quality control processes to ensure that the chairs meet international standards.
– Experience: Choose suppliers with a proven track record in your industry or region for added assurance.
Step 4: Request Samples for Testing
To verify quality and comfort, always request samples before making a bulk order. This step allows you to assess the product firsthand.
– Durability Tests: Check how the chair holds up under stress and various conditions.
– Comfort Assessment: Evaluate the ergonomic features and overall comfort for your intended audience.
Step 5: Verify Compliance with International Standards
Ensure that the plastic chair chairs comply with relevant international safety and quality standards. This is particularly crucial for markets in Europe and the Middle East, where regulations can be stringent.
– Standards to Look For: Familiarize yourself with standards such as EN 16139 (Furniture – Strength, durability, and safety) for European markets.
– Documentation: Request documentation that certifies compliance with these standards from your supplier.
Step 6: Negotiate Terms and Conditions
Once you have selected a supplier, it’s time to negotiate the terms of your purchase. This includes pricing, payment terms, and delivery schedules.
– Bulk Discounts: Inquire about discounts for larger orders to optimize your budget.
– Lead Times: Discuss expected lead times for production and delivery to ensure they align with your project timelines.
Step 7: Establish a Clear Communication Plan
Effective communication is key to a successful sourcing process. Establish a clear communication plan with your supplier to address any concerns or changes promptly.
– Point of Contact: Designate a single point of contact for consistency.
– Regular Updates: Schedule regular check-ins to monitor progress and resolve any issues that may arise during production.
By following this step-by-step checklist, B2B buyers can confidently navigate the procurement process for plastic chair chairs, ensuring they make informed decisions that align with their business needs and sustainability goals.
Comprehensive Cost and Pricing Analysis for plastic chair chairs Sourcing
What Are the Key Cost Components in Sourcing Plastic Chair Chairs?
When sourcing plastic chair chairs, understanding the cost structure is crucial for effective budgeting and negotiation. The primary cost components include:
-
Materials: The type of plastic used significantly influences the cost. Common plastics such as Polypropylene (PP) and High-Density Polyethylene (HDPE) are popular due to their durability and cost-effectiveness. Specialty materials may increase costs but can enhance product longevity and sustainability.
-
Labor: Labor costs can vary widely based on geographical location. For instance, countries in Africa and South America may offer lower labor costs compared to European nations. It’s important to factor in local wage rates and the skill level required for production.
-
Manufacturing Overhead: This includes costs related to factory operations such as utilities, equipment maintenance, and administrative expenses. Efficient production processes can help minimize these overheads.
-
Tooling: The initial investment in molds and machinery for producing plastic chairs can be substantial. However, this cost is often amortized over high production volumes, making it crucial to assess minimum order quantities (MOQs).
-
Quality Control (QC): Implementing robust QC processes ensures that the products meet specified standards, which can incur additional costs. However, investing in quality can reduce returns and enhance customer satisfaction in the long run.
-
Logistics: Shipping costs can vary greatly depending on the distance and transportation methods used. International buyers should be aware of tariffs, import duties, and insurance costs that may impact the total landed cost.
-
Margin: Suppliers typically add a profit margin to cover their risks and expenses. Understanding the competitive landscape can help buyers negotiate better pricing.
How Do Price Influencers Impact the Sourcing of Plastic Chair Chairs?
Several factors influence the pricing of plastic chair chairs:
-
Volume/MOQ: Higher order volumes often lead to lower per-unit costs. Suppliers are more willing to negotiate discounts for bulk purchases, which can be particularly advantageous for large-scale projects.
-
Specifications and Customization: Custom designs or specific performance criteria can increase costs. It’s essential to balance the need for customization with budget constraints.
-
Materials and Quality Certifications: The choice of materials and the presence of certifications (e.g., ISO, environmental standards) can significantly affect pricing. Premium materials and certified products typically command higher prices but can offer better durability and sustainability.
-
Supplier Factors: The reputation and reliability of suppliers can impact pricing. Established suppliers may offer better quality and service but at a premium. Conducting thorough due diligence can yield long-term partnerships.
-
Incoterms: Understanding Incoterms (International Commercial Terms) is crucial for international transactions. They define the responsibilities of buyers and sellers regarding shipping, insurance, and tariffs, which can influence total costs.
What Buyer Tips Can Enhance Cost Efficiency in Plastic Chair Chair Sourcing?
For international B2B buyers, particularly from Africa, South America, the Middle East, and Europe, several strategies can optimize sourcing:
-
Negotiate Effectively: Leverage competitive quotes from multiple suppliers to negotiate better terms. Building strong relationships with suppliers can also lead to favorable pricing and terms over time.
-
Consider Total Cost of Ownership (TCO): Look beyond initial purchase prices. Assess long-term costs including maintenance, durability, and disposal. Investing in higher-quality products may yield savings over time.
-
Be Mindful of Pricing Nuances: Different regions have varying pricing structures influenced by local economic conditions, currency fluctuations, and supply chain dynamics. Being aware of these factors can enhance negotiation strategies.
-
Conduct Market Research: Regularly review market trends and pricing benchmarks to stay informed. Understanding the competitive landscape can help buyers make informed decisions and identify the best sourcing opportunities.
Disclaimer on Indicative Prices
Prices for plastic chair chairs can vary widely based on multiple factors, including material choice, supplier location, and order volume. It is advisable to obtain specific quotes based on your unique requirements to ensure accurate budgeting and planning.
Alternatives Analysis: Comparing plastic chair chairs With Other Solutions
Understanding Alternatives to Plastic Chair Chairs for B2B Buyers
In the evolving landscape of furniture solutions, international B2B buyers face a multitude of choices when considering alternatives to plastic chair chairs. While plastic chairs offer benefits such as affordability and versatility, it is essential to evaluate other materials and technologies that can fulfill similar requirements. This comparison will focus on two viable alternatives: metal chairs and wooden chairs.
Comparison Table of Plastic Chair Chairs and Alternatives
Comparison Aspect | Plastic Chair Chairs | Metal Chairs | Wooden Chairs |
---|---|---|---|
Performance | Durable, lightweight | Highly durable, stable | Strong, aesthetically pleasing |
Cost | Low to moderate | Moderate to high | Moderate to high |
Ease of Implementation | Easy to manufacture and customize | Requires more complex manufacturing | More labor-intensive to produce |
Maintenance | Minimal maintenance, resistant to weather | Requires occasional polishing | Requires regular maintenance (polishing, sealing) |
Best Use Case | Outdoor events, casual settings | Office environments, industrial use | Restaurants, upscale venues |
Pros and Cons of Alternative Solutions
What Are the Advantages and Disadvantages of Metal Chairs?
Metal chairs are known for their strength and stability, making them ideal for high-traffic environments. They are often stackable, saving space in storage and during transport. However, the initial cost can be higher compared to plastic chairs, and they may require additional maintenance to keep them looking polished and rust-free. In environments with extreme temperatures, metal chairs can become uncomfortable without cushions, which may lead to additional investment in accessories.
How Do Wooden Chairs Compare to Plastic Chair Chairs?
Wooden chairs offer a timeless aesthetic and can elevate the ambiance of any setting, particularly in restaurants or high-end venues. They are typically stronger and more durable than plastic chairs, but they come with a higher price tag and require regular maintenance to preserve their finish and structural integrity. Wooden chairs may not be suitable for outdoor use unless treated specifically for weather resistance, which can further increase costs and complexity.
How Should B2B Buyers Choose the Right Solution?
When selecting between plastic chair chairs and their alternatives, B2B buyers should consider several factors specific to their needs. Assessing the intended use, budget constraints, and desired aesthetic is crucial. For example, if the chairs will be used in a casual outdoor setting, plastic chairs may be the most practical choice due to their cost-effectiveness and low maintenance. Conversely, if the chairs are intended for a high-end restaurant, investing in wooden chairs may yield better long-term value despite the higher initial costs. Ultimately, aligning the choice with the brand’s image and operational needs will guide buyers to the right decision.
Essential Technical Properties and Trade Terminology for plastic chair chairs
What Are the Key Technical Properties of Plastic Chair Chairs?
When sourcing plastic chair chairs, understanding their technical properties is essential for making informed purchasing decisions. Here are some critical specifications to consider:
1. Material Grade: Which Plastics Are Best for Durability?
The material grade refers to the specific type of plastic used in manufacturing the chairs. Common grades include Polypropylene (PP) and High-Density Polyethylene (HDPE). These materials are known for their durability, resistance to impact, and weather resistance, making them suitable for both indoor and outdoor use. Choosing the right material grade ensures that the chairs can withstand various environmental conditions, which is particularly important for businesses operating in diverse climates, such as those in Africa or South America.
2. Weight Capacity: How Much Load Can the Chair Support?
The weight capacity indicates the maximum load a chair can bear safely. This specification is crucial for B2B buyers, especially in sectors like hospitality and events, where chairs must accommodate varying body weights. A chair designed for a higher weight capacity will be more versatile and suitable for a wider audience, reducing the risk of damage and increasing customer satisfaction.
3. Tolerance: What Level of Precision Is Required in Manufacturing?
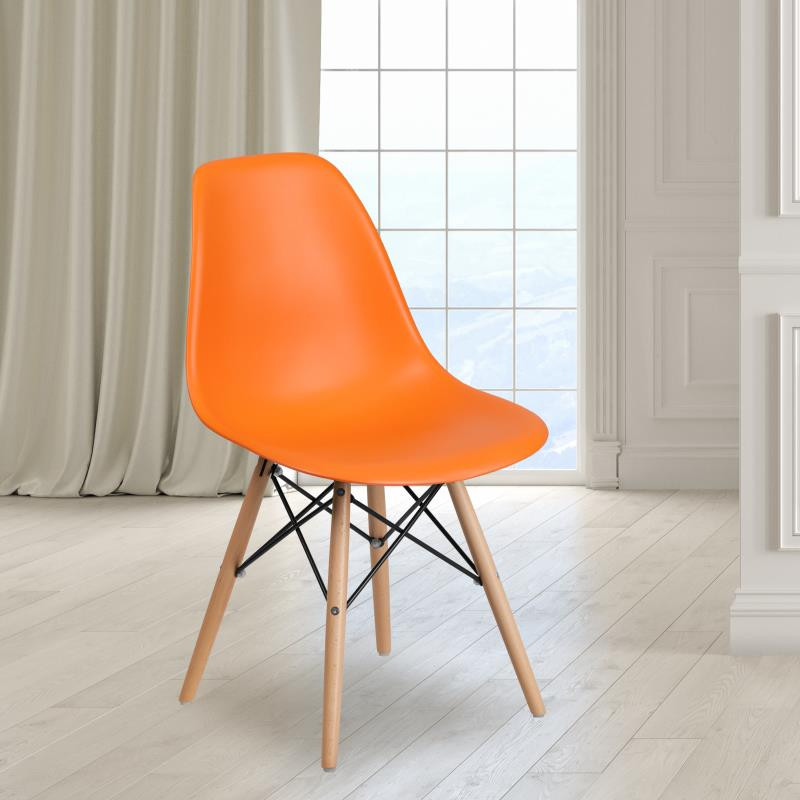
A stock image related to plastic chair chairs.
Tolerance refers to the allowable deviation from specified dimensions during the manufacturing process. For plastic chair chairs, maintaining tight tolerances is vital for ensuring a consistent fit and finish. This is particularly important for large orders where uniformity is key. A manufacturer with strict tolerance controls will likely produce higher-quality products that meet exact specifications, minimizing returns and dissatisfaction.
4. UV Resistance: How Well Do Chairs Hold Up Under Sun Exposure?
UV resistance indicates how well the material can withstand degradation due to sunlight exposure. Chairs used outdoors, especially in sunny regions of Africa and South America, should have high UV resistance to prevent fading and brittleness over time. This property not only extends the life of the chairs but also enhances the aesthetic appeal, maintaining their visual integrity longer.
5. Recyclability: Is the Material Environmentally Friendly?
Recyclability is an increasingly important factor for B2B buyers, particularly in Europe, where environmental regulations are strict. Chairs made from recyclable materials like PET or HDPE can reduce waste and appeal to eco-conscious consumers. Understanding the recyclability of the plastic used can also influence procurement strategies and corporate sustainability goals.
What Are Common Trade Terms Relevant to Plastic Chair Chairs?
Familiarity with industry jargon is essential for navigating the B2B landscape effectively. Here are some common terms you should know:
1. OEM (Original Equipment Manufacturer): Who Is Producing Your Chairs?
OEM refers to companies that produce products that are marketed under another brand’s name. In the context of plastic chair chairs, an OEM may manufacture chairs for a retailer, allowing businesses to focus on branding while relying on the expertise of specialized manufacturers.
2. MOQ (Minimum Order Quantity): What Is the Least You Can Order?
MOQ is the smallest number of units a supplier is willing to sell. This term is crucial for budgeting and inventory management. Understanding the MOQ can help businesses assess whether a supplier meets their purchasing needs, especially for startups or small enterprises looking to manage costs effectively.
3. RFQ (Request for Quotation): How Do You Get Pricing Information?
An RFQ is a document issued by a buyer to request pricing and terms from suppliers. When looking for plastic chair chairs, sending an RFQ can help you gather competitive pricing, assess potential suppliers, and make informed purchasing decisions.
4. Incoterms: What Shipping Terms Should You Know?
Incoterms (International Commercial Terms) define the responsibilities of buyers and sellers in international transactions. Understanding these terms is crucial for international B2B buyers as they outline shipping costs, risks, and insurance obligations, allowing for smoother cross-border transactions.
5. Lead Time: How Long Will It Take to Receive Your Order?
Lead time is the period between placing an order and receiving the goods. Knowing the lead time helps businesses plan inventory and manage customer expectations. Short lead times can be a significant competitive advantage, especially in fast-paced markets.
By grasping these essential technical properties and trade terms, international B2B buyers can make more informed decisions when sourcing plastic chair chairs, ultimately enhancing their purchasing strategy and operational efficiency.
Navigating Market Dynamics and Sourcing Trends in the plastic chair chairs Sector
What Are the Current Market Dynamics and Key Trends in the Plastic Chair Chairs Sector?
The global plastic chair chairs market is experiencing significant growth, driven by urbanization, increasing disposable incomes, and a rising demand for affordable, lightweight furniture. In regions like Africa and South America, where rapid urbanization is common, the need for versatile seating solutions in both residential and commercial sectors is surging. Additionally, the Middle East and Europe are witnessing a trend towards multifunctional furniture that caters to both aesthetic and practical needs, aligning with contemporary design trends.
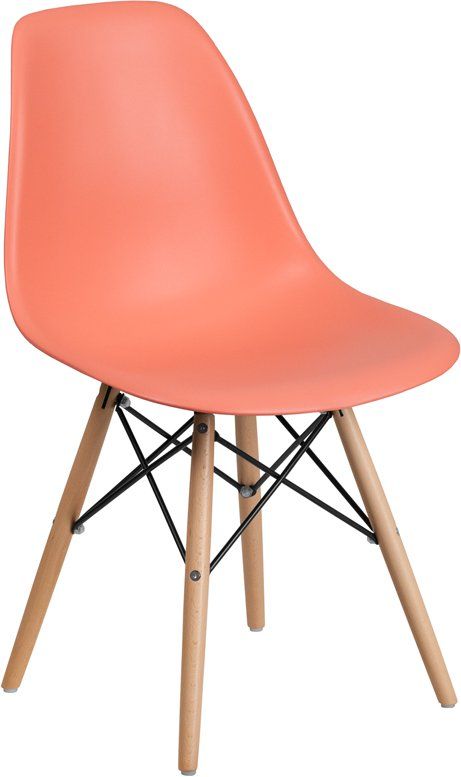
A stock image related to plastic chair chairs.
Emerging B2B technology plays a crucial role in sourcing trends. Digital platforms are increasingly being used for procurement processes, allowing buyers to compare suppliers and products more efficiently. Innovations in manufacturing, such as 3D printing and automation, are reducing lead times and costs, making it easier for international buyers to obtain customized solutions that meet their specific needs. Furthermore, leveraging data analytics enables businesses to forecast demand accurately, which helps in optimizing inventory levels and reducing waste.
Sustainability is becoming a pivotal factor in purchasing decisions. Buyers are now more inclined to source from manufacturers that demonstrate a commitment to eco-friendly practices, including the use of recycled materials and sustainable production methods. As the market evolves, understanding these dynamics will be essential for international B2B buyers to remain competitive and responsive to changing consumer preferences.
How Is Sustainability Influencing Sourcing in the Plastic Chair Chairs Sector?
The environmental impact of plastic production and waste management is a growing concern for businesses and consumers alike. International B2B buyers are increasingly prioritizing sustainability in their sourcing strategies, looking for partners who demonstrate ethical practices and environmental responsibility. This shift is particularly pronounced in regions such as Europe, where stringent regulations regarding plastic use and waste management are in place.
Ethical supply chains are now a key consideration for buyers seeking to minimize their environmental footprint. Manufacturers that utilize sustainable materials, such as recycled polyethylene (rPET) or bio-based plastics, are gaining a competitive edge. Green certifications, such as the Forest Stewardship Council (FSC) or Global Recycled Standard (GRS), can enhance a company’s reputation and appeal to environmentally conscious buyers.
Moreover, the focus on circular economy principles is reshaping the market. Companies that incorporate designs for disassembly and recycling into their products are not only reducing waste but also appealing to a growing segment of consumers who prioritize sustainability. By aligning sourcing strategies with these principles, international B2B buyers can foster long-term relationships with suppliers and contribute to a more sustainable future.
What Is the Evolution of the Plastic Chair Chairs Market?
The plastic chair chairs market has evolved significantly since its inception. Initially, the focus was primarily on functionality and affordability. However, as consumer preferences have shifted towards design, comfort, and sustainability, manufacturers have adapted their offerings accordingly. In the early days, materials like polyvinyl chloride (PVC) dominated, but concerns over environmental impact have led to a gradual transition towards more sustainable alternatives, such as high-density polyethylene (HDPE) and polypropylene (PP).
The introduction of advanced manufacturing techniques has also transformed the sector. Innovations such as injection molding and blow molding have enabled the production of complex designs and improved durability. Additionally, the rise of e-commerce platforms has revolutionized distribution channels, making it easier for international buyers to access a wider range of products and suppliers.
As the market continues to mature, ongoing advancements in materials science and technology will likely drive further changes. This evolution presents an exciting opportunity for B2B buyers to engage with suppliers who are committed to innovation and sustainability, ensuring that their sourcing practices align with future market demands.
Frequently Asked Questions (FAQs) for B2B Buyers of plastic chair chairs
-
How do I ensure the quality of plastic chair chairs before purchasing?
To guarantee quality, it is essential to conduct thorough supplier vetting. Request samples to inspect the material, durability, and design. Check for certifications like ISO 9001, which indicates a commitment to quality management. Additionally, consider third-party quality assurance inspections before shipment, especially for bulk orders. Engaging in trade shows or industry expos can also help you assess the quality of different suppliers’ products firsthand. -
What is the best material for plastic chair chairs in different climates?
High-Density Polyethylene (HDPE) is an excellent choice for outdoor plastic chairs due to its resistance to impact and UV light. For indoor use, Polypropylene (PP) offers durability and high-temperature resistance, making it suitable for various environments. Additionally, consider the environmental impact; opting for recycled materials can enhance your brand’s sustainability profile, particularly important for buyers in Europe and other eco-conscious markets. -
What are the typical minimum order quantities (MOQs) for plastic chair chairs?
MOQs can vary widely depending on the supplier and the type of plastic chair. Generally, international manufacturers may set MOQs between 100 to 1,000 units. It’s advisable to negotiate MOQs based on your needs, especially if you’re a new buyer or testing the market in regions like Africa or South America. Some suppliers may offer flexibility for first-time buyers or smaller businesses, so don’t hesitate to ask. -
How can I customize plastic chair chairs for my brand?
Customization options often include color, design, and branding elements such as logos. Most manufacturers will require a minimum order quantity for customized products, so be prepared for that. When approaching suppliers, clearly communicate your design requirements and ask for prototypes to ensure that the final product meets your expectations. Engaging with suppliers who specialize in custom designs can also yield better results. -
What payment terms should I negotiate when sourcing plastic chair chairs?
Standard payment terms typically include a 30% deposit upfront with the balance due before shipment. However, depending on your relationship with the supplier, you may negotiate more favorable terms such as net 30 or net 60 days. It’s crucial to clarify these terms before finalizing any contract to avoid misunderstandings. Additionally, consider using secure payment methods such as letters of credit or escrow services for added protection. -
How do I handle logistics and shipping for international orders of plastic chair chairs?
When sourcing internationally, it’s vital to understand the logistics involved. Choose a reliable freight forwarder experienced in handling furniture shipments, as they can help navigate customs regulations and shipping costs. Factor in delivery times, which can vary depending on the origin and destination. Always confirm shipping terms (Incoterms) with your supplier to clarify responsibilities for shipping costs, insurance, and risk of loss. -
What regulations should I be aware of when importing plastic chair chairs?
Each country has its own regulations regarding the importation of plastic products. In Europe, for instance, compliance with REACH (Registration, Evaluation, Authorisation, and Restriction of Chemicals) is mandatory. In Africa and South America, specific import tariffs and safety standards may apply. Always consult with a local customs broker to ensure compliance with all regulations and avoid costly delays at the border. -
What are the environmental considerations when sourcing plastic chair chairs?
Sustainability is increasingly important for B2B buyers. Look for suppliers who use recycled plastics or those who have eco-friendly production processes. Certifications like the Global Recycled Standard (GRS) can guide you in making environmentally conscious choices. Additionally, consider the end-of-life options for the chairs, such as recyclability, to enhance your brand’s commitment to sustainability, which is especially valued in markets like Europe and North America.
Important Disclaimer & Terms of Use
⚠️ Important Disclaimer
The information provided in this guide, including content regarding manufacturers, technical specifications, and market analysis, is for informational and educational purposes only. It does not constitute professional procurement advice, financial advice, or legal advice.
While we have made every effort to ensure the accuracy and timeliness of the information, we are not responsible for any errors, omissions, or outdated information. Market conditions, company details, and technical standards are subject to change.
B2B buyers must conduct their own independent and thorough due diligence before making any purchasing decisions. This includes contacting suppliers directly, verifying certifications, requesting samples, and seeking professional consultation. The risk of relying on any information in this guide is borne solely by the reader.
Strategic Sourcing Conclusion and Outlook for plastic chair chairs
In the evolving landscape of international B2B sourcing, especially for plastic chair chairs, strategic sourcing emerges as a critical factor for success. By understanding the diverse types of plastics—such as PET, HDPE, and polypropylene—buyers can make informed decisions that align with both quality and sustainability. The importance of selecting materials that are recyclable and environmentally friendly cannot be overstated, as this not only enhances brand reputation but also meets the growing demand for sustainable products across global markets.
What are the benefits of strategic sourcing for plastic chair chairs? By engaging in strategic sourcing, international buyers can leverage competitive pricing, ensure consistent supply, and foster long-term relationships with suppliers. This approach is particularly beneficial for businesses in regions like Africa, South America, the Middle East, and Europe, where market dynamics can differ significantly.
Looking ahead, the call to action for B2B buyers is clear: prioritize strategic sourcing to not only enhance your product offerings but also contribute positively to environmental sustainability. As the market continues to evolve, staying ahead of trends and embracing innovative sourcing practices will be essential for future growth and success in the plastic chair chairs sector.