Cut Costs with Rolling Machines for Tobacco: A Complete Guide (2025)
Introduction: Navigating the Global Market for rolling machines for tobacco
In the dynamic landscape of the global tobacco industry, sourcing reliable rolling machines for tobacco production is a pivotal challenge that many international B2B buyers face. With the increasing demand for high-quality tobacco products, understanding the intricacies of machine specifications, production capacity, and technological advancements is essential. This guide provides a comprehensive overview of the various types of rolling machines available, their specific applications, and the critical factors to consider when selecting the right equipment for your business needs.
From manual to fully automated solutions, rolling machines come in diverse configurations tailored to different production scales and product types. Buyers will gain insights into the latest innovations in tobacco rolling technology, alongside practical advice on supplier vetting processes, ensuring that you choose reputable manufacturers that align with your operational goals. Moreover, understanding the cost implications associated with these machines, including maintenance and operational efficiency, is crucial for maximizing your return on investment.
This guide is designed specifically for international B2B buyers from Africa, South America, the Middle East, and Europe, offering actionable insights that empower informed purchasing decisions. By equipping you with the knowledge to navigate this complex market, you can enhance your procurement strategies, ultimately leading to a more competitive edge in the global tobacco sector.
Understanding rolling machines for tobacco Types and Variations
Type Name | Key Distinguishing Features | Primary B2B Applications | Brief Pros & Cons for Buyers |
---|---|---|---|
Manual Rolling Machines | Operated by hand; portable; low initial cost | Small-scale producers; local markets | Pros: Affordable; easy to use. Cons: Slower production; labor-intensive. |
Semi-Automatic Rolling Machines | Combines manual input with automated functions; higher output | Medium-scale operations; specialty shops | Pros: Increased efficiency; moderate cost. Cons: Requires training; maintenance needed. |
Fully Automatic Rolling Machines | High-speed production; minimal labor input; advanced technology | Large-scale manufacturers; export markets | Pros: High efficiency; consistent quality. Cons: High initial investment; complex setup. |
Electric Rolling Machines | Powered by electricity; quick setup; user-friendly | Convenience stores; vending machine suppliers | Pros: Fast production; consistent rolls. Cons: Dependence on power supply; higher operational costs. |
Rolling Machine Accessories | Includes parts like molds, trays, and feeders; enhances machine capability | Customization for all types of machines | Pros: Improves efficiency; tailored solutions. Cons: Additional costs; compatibility issues. |
What are the characteristics of Manual Rolling Machines?
Manual rolling machines are characterized by their simplicity and portability. Typically operated by hand, these machines are ideal for small-scale producers and local markets in regions like Africa and South America, where the initial investment is a critical factor. Buyers should consider the labor intensity and slower production rates, which may affect output in high-demand scenarios. However, their affordability makes them an attractive option for startups and small businesses looking to enter the tobacco market without significant financial risk.
How do Semi-Automatic Rolling Machines enhance production?
Semi-automatic rolling machines blend manual input with automated features, which significantly boosts production efficiency. They are suitable for medium-scale operations and specialty shops that require a balance between speed and quality. When purchasing, B2B buyers should evaluate the training requirements for staff, as well as the maintenance needs, which can impact overall operational costs. These machines provide a practical solution for businesses looking to scale without the complexities of fully automated systems.
Why are Fully Automatic Rolling Machines preferred by large manufacturers?
Fully automatic rolling machines are designed for high-speed production with minimal labor input. They are ideal for large-scale manufacturers and export markets, where consistent quality and high output are paramount. Buyers should weigh the high initial investment against the long-term benefits of efficiency and reduced labor costs. Additionally, the complexity of setup and maintenance might require specialized training, making it essential for businesses to assess their operational capabilities before committing to such a purchase.
What advantages do Electric Rolling Machines offer?
Electric rolling machines provide quick setup and user-friendly operation, making them a convenient choice for convenience stores and vending machine suppliers. Their powered functionality allows for rapid production, ensuring consistent quality in each roll. However, B2B buyers must consider the dependency on a reliable power supply and the potential for higher operational costs. This type of machine is particularly beneficial for businesses that prioritize speed and uniformity in their products.
How can Rolling Machine Accessories improve efficiency?
Rolling machine accessories, including molds, trays, and feeders, enhance the capability of all types of rolling machines. These accessories allow for customization, enabling businesses to tailor their production processes to meet specific demands. B2B buyers should factor in the additional costs associated with these accessories and ensure compatibility with existing machines. While they represent an upfront investment, the potential for improved efficiency and output can justify the expense, especially for businesses aiming for scalability.
Related Video: The Best Cigarette Rolling Machines of 2025 | RYO Tobacco
Key Industrial Applications of rolling machines for tobacco
Industry/Sector | Specific Application of Rolling Machines for Tobacco | Value/Benefit for the Business | Key Sourcing Considerations for this Application |
---|---|---|---|
Tobacco Manufacturing | Production of Cigarettes and Rolling Tobacco | Increased production efficiency and consistency | Compliance with local regulations, machine capacity, and technology |
Small-Scale Tobacco Farms | Manual Rolling for Local Markets | Cost-effective production for niche markets | Durability, ease of use, and availability of parts |
Export and Import Trading Firms | Packaging and Distribution of Tobacco Products | Enhanced product presentation and shelf life | Customization options, logistics compatibility, and certifications |
Tobacco Product Retailers | In-Store Rolling Machines for Customers | Improved customer experience and engagement | Space requirements, maintenance support, and power needs |
Research and Development Facilities | Testing New Tobacco Blends and Rolling Techniques | Innovation in product offerings | Precision capabilities, versatility, and data collection features |
How Are Rolling Machines for Tobacco Used in Tobacco Manufacturing?
In large-scale tobacco manufacturing, rolling machines are crucial for producing cigarettes and rolling tobacco. These machines automate the rolling process, ensuring high-speed production with consistent quality. This efficiency helps manufacturers meet high demand while minimizing labor costs. International buyers must consider compliance with local regulations regarding tobacco production, as well as the machine’s capacity to handle various tobacco blends and the technology used to ensure product quality.
What Role Do Rolling Machines Play in Small-Scale Tobacco Farms?
For small-scale tobacco farms, rolling machines serve as a cost-effective solution for producing products tailored for local markets. These machines allow farmers to roll their tobacco manually, offering flexibility in production while maintaining quality. Buyers from regions like Africa and South America should focus on the durability and ease of use of these machines, as well as the availability of replacement parts to ensure long-term viability and support for their operations.
How Are Rolling Machines Beneficial for Export and Import Trading Firms?
Export and import trading firms utilize rolling machines primarily for packaging and distribution of tobacco products. These machines enhance product presentation, ensuring that items are attractively rolled and packaged for international markets. This not only improves shelf life but also appeals to consumers. B2B buyers should consider customization options that cater to specific market demands, alongside logistics compatibility to facilitate smooth transportation of goods across borders.
How Do Retailers Use Rolling Machines to Enhance Customer Experience?
Tobacco product retailers are increasingly incorporating rolling machines in-store to allow customers to roll their own products. This interactive experience not only engages customers but also caters to the growing trend of personalized tobacco products. Retailers must consider space requirements for these machines, as well as maintenance support and the power needs to ensure they operate smoothly in a high-traffic environment.
Why Are Rolling Machines Important for Research and Development in Tobacco?
Research and development facilities leverage rolling machines to test new tobacco blends and rolling techniques. These machines provide precise control over the rolling process, enabling researchers to experiment with different tobacco types and formulations. B2B buyers in this sector should prioritize machines with precision capabilities and versatility, along with features that facilitate data collection for analyzing the performance of new products.
Related Video: Electric Cigarette Machine Easy Automatic Tobacco Rolling Machine
3 Common User Pain Points for ‘rolling machines for tobacco’ & Their Solutions
Scenario 1: Difficulty in Achieving Consistent Quality in Tobacco Rolling
The Problem: One of the most significant challenges faced by B2B buyers of rolling machines for tobacco is achieving consistent quality in the final product. Many manufacturers struggle with variations in density, moisture content, and the cut of the tobacco leaves. This inconsistency can lead to customer dissatisfaction and increased returns, damaging business reputation and profitability. Buyers often find themselves grappling with machines that either over-compress or under-compress the tobacco, resulting in uneven rolls that affect the smoking experience.
The Solution: To overcome this issue, it is crucial to invest in rolling machines equipped with advanced technology that offers adjustable compression settings. Look for machines that allow for precise control over the rolling process, ensuring uniform density and moisture retention. Additionally, consider sourcing machines with integrated moisture sensors that can automatically adjust the rolling parameters based on the tobacco’s moisture content. Before purchasing, request samples of different machine settings to evaluate the output quality. Collaborating with suppliers who provide training on machine calibration can also enhance consistency in production.
Scenario 2: High Maintenance Costs and Downtime
The Problem: High maintenance costs and unexpected downtime can cripple production schedules, especially for companies in regions where access to replacement parts and service technicians is limited. B2B buyers often face the frustration of dealing with machines that require frequent repairs or have complex maintenance protocols that are hard to follow. This not only affects output but also strains budgets, especially for smaller enterprises or those in emerging markets in Africa or South America.
The Solution: To mitigate these challenges, it is advisable to conduct thorough research before selecting a rolling machine. Focus on models known for their durability and ease of maintenance. Opt for machines that come with comprehensive service packages, including extended warranties and readily available spare parts. Suppliers who offer online support and maintenance training can significantly reduce downtime. Additionally, implementing a preventive maintenance schedule can help identify potential issues before they escalate into costly repairs. Keeping a stock of essential spare parts on hand can further ensure that production is not interrupted.
Scenario 3: Compliance with Regional Regulations and Quality Standards
The Problem: B2B buyers in the tobacco industry often face the challenge of ensuring their rolling machines comply with various regional regulations and quality standards. This is particularly pertinent for buyers from Europe and the Middle East, where regulations can be stringent regarding product safety and environmental impact. Navigating these regulations can be daunting, leading to potential legal issues and financial penalties if not adhered to.
The Solution: To address this pain point, buyers should prioritize sourcing rolling machines that are certified to meet international and local standards. Before making a purchase, verify that the machines have been tested and certified by recognized regulatory bodies. Engaging with suppliers who have a track record of compliance can help streamline this process. Additionally, staying informed about changing regulations in your target market is crucial. This can be achieved through industry associations or regulatory bodies. Investing in machines that offer eco-friendly features, such as reduced energy consumption or recyclable materials, can also position your business favorably in the eyes of regulators and consumers alike.
Strategic Material Selection Guide for rolling machines for tobacco
When selecting materials for rolling machines used in the tobacco industry, international B2B buyers must consider various factors that influence performance, durability, and compliance with industry standards. Below, we analyze four common materials used in the construction of these machines, focusing on their properties, advantages, disadvantages, and specific considerations for buyers from regions such as Africa, South America, the Middle East, and Europe.
What Are the Key Properties of Stainless Steel in Rolling Machines for Tobacco?
Stainless steel is a popular choice for rolling machines due to its excellent corrosion resistance and high-temperature tolerance. It typically has a temperature rating of up to 800°C and can withstand high-pressure environments. Its non-reactive nature makes it suitable for processing tobacco, ensuring that the flavor and quality remain intact.
Pros: Stainless steel is highly durable and requires minimal maintenance. It is also relatively easy to clean, which is crucial for hygiene in tobacco processing.
Cons: The primary drawback is its cost, as stainless steel can be more expensive than other materials. Additionally, the manufacturing process can be complex, requiring specialized equipment.
Impact on Application: Stainless steel’s compatibility with various media makes it ideal for rolling machines that handle different tobacco blends.
Considerations for Buyers: Buyers should ensure compliance with international standards such as ASTM and DIN, particularly regarding food safety and material certifications.
How Does Aluminum Compare for Use in Tobacco Rolling Machines?
Aluminum is another material frequently used in rolling machines due to its lightweight properties and good thermal conductivity. It typically has a lower temperature tolerance than stainless steel, around 400°C, but is still adequate for many tobacco processing applications.
Pros: Aluminum is less expensive than stainless steel and easier to machine, which can reduce manufacturing complexity and lead times.
Cons: Its lower strength and susceptibility to corrosion can be significant drawbacks, especially in humid environments common in many tobacco-producing regions.
Impact on Application: Aluminum is suitable for machines that require frequent mobility or where weight is a concern. However, care must be taken with moisture exposure to prevent degradation.
Considerations for Buyers: Buyers in humid climates should assess the need for protective coatings to enhance corrosion resistance and ensure compliance with local regulations regarding material safety.
What Advantages Does Carbon Steel Offer in Tobacco Rolling Machines?
Carbon steel is known for its high strength and durability, making it suitable for heavy-duty rolling machines. It can handle high-pressure applications and has a temperature rating similar to stainless steel.
Pros: The cost-effectiveness of carbon steel is a major advantage, as it is generally cheaper than stainless steel and aluminum. Its strength makes it ideal for heavy-duty applications.
Cons: However, carbon steel is prone to rust and corrosion if not properly coated or maintained, which can impact the quality of the tobacco being processed.
Impact on Application: Carbon steel is best suited for machines that operate in dry environments where moisture is minimal.
Considerations for Buyers: Buyers must consider the need for protective coatings and regular maintenance to prevent rust, particularly in humid regions like parts of Africa and South America.
Why Is Polymer Material Becoming Popular in Tobacco Rolling Machines?
Polymers, particularly high-performance plastics, are increasingly being used in rolling machines due to their lightweight and corrosion-resistant properties. They can withstand temperatures up to 200°C, making them suitable for specific applications.
Pros: The primary advantage of polymers is their resistance to corrosion and ease of cleaning, which is essential for maintaining hygiene in tobacco processing.
Cons: However, their lower temperature tolerance and strength compared to metals can limit their use in high-stress applications.
Impact on Application: Polymers can be ideal for components that require frequent cleaning or where weight reduction is beneficial.
Considerations for Buyers: Buyers should verify the specific polymer grades used and ensure they meet relevant industry standards, especially in regions with stringent regulations.
Summary Table of Material Selection for Rolling Machines
Material | Typical Use Case for rolling machines for tobacco | Key Advantage | Key Disadvantage/Limitation | Relative Cost (Low/Med/High) |
---|---|---|---|---|
Stainless Steel | High-end, durable machines | Excellent corrosion resistance | Higher cost and complex manufacturing | High |
Aluminum | Lightweight, portable machines | Cost-effective and easy to machine | Susceptible to corrosion | Medium |
Carbon Steel | Heavy-duty applications | High strength and durability | Prone to rust without proper coating | Low |
Polymer | Components requiring frequent cleaning | Corrosion-resistant and lightweight | Lower temperature tolerance | Medium |
This guide aims to provide international B2B buyers with actionable insights into the strategic selection of materials for rolling machines in the tobacco industry, ensuring informed decisions that align with operational needs and compliance requirements.
In-depth Look: Manufacturing Processes and Quality Assurance for rolling machines for tobacco
What Are the Key Stages in the Manufacturing Process of Rolling Machines for Tobacco?
The manufacturing process of rolling machines for tobacco involves several critical stages, each designed to ensure high-quality output and efficiency. These stages typically include material preparation, forming, assembly, and finishing.
Material Preparation: What Materials Are Used?
The first step in the manufacturing process is the selection and preparation of materials. Manufacturers commonly use high-grade metals such as stainless steel for durability and resistance to corrosion. Additionally, components made from high-density plastics may be used for non-critical parts to reduce weight and cost. The materials undergo rigorous testing to ensure they meet industry specifications before they enter the production line.
Forming: How Are Components Shaped?
During the forming stage, raw materials are shaped into the components required for the rolling machines. Techniques such as CNC machining, stamping, and injection molding are often employed. CNC machining allows for precise dimensions and tolerances, which is vital for the mechanical components that must fit together seamlessly. Stamping is typically used for flat components, while injection molding is ideal for producing complex shapes in plastic parts.
Assembly: What Are the Best Practices?
Assembly is a crucial phase where all the formed components are brought together. This process often utilizes automated assembly lines to enhance efficiency and reduce labor costs. Manual assembly may still be necessary for intricate parts or when quality assurance requires a more hands-on approach. During this stage, manufacturers typically employ techniques such as lean manufacturing to minimize waste and optimize production flow.
Finishing: How Is Quality Enhanced?
The finishing stage focuses on enhancing the product’s aesthetics and functionality. Processes such as polishing, painting, or applying protective coatings are common. This not only improves the machine’s appearance but also its resistance to wear and tear. Attention to detail in this phase is critical, as it can significantly impact the machine’s longevity and operational efficiency.
What Quality Assurance Standards Are Relevant to Rolling Machines for Tobacco?
Quality assurance is a vital aspect of the manufacturing process, ensuring that the rolling machines meet the necessary performance and safety standards. International standards such as ISO 9001 play a crucial role in this regard. This standard outlines requirements for a quality management system, helping manufacturers consistently provide products that meet customer and regulatory requirements.
What Industry-Specific Certifications Should Buyers Look For?
In addition to ISO 9001, industry-specific certifications like CE marking in Europe and API standards in certain regions can be critical indicators of quality. CE marking signifies that the product complies with European safety standards, while API standards are essential for ensuring that machinery meets the rigorous demands of the oil and gas sector, should they overlap with tobacco processing.
How Are Quality Control Checkpoints Implemented?
Quality control (QC) is implemented at various checkpoints throughout the manufacturing process. These checkpoints typically include:
-
Incoming Quality Control (IQC): This stage involves inspecting raw materials before they enter the manufacturing process to ensure they meet the required specifications.
-
In-Process Quality Control (IPQC): During the manufacturing stages, periodic checks are conducted to monitor the quality of components being produced. This ensures that any deviations from quality standards are caught early.
-
Final Quality Control (FQC): Once the machines are fully assembled, a comprehensive inspection is performed to ensure that all components function correctly and meet the specified standards.
What Common Testing Methods Are Used in Quality Control?
Various testing methods are employed to ensure the quality of rolling machines for tobacco. These may include:
-
Functional Testing: Verifying that all machine functions operate as intended under normal operating conditions.
-
Durability Testing: Subjecting machines to stress tests to ensure they can withstand regular use over time without failure.
-
Safety Testing: Ensuring that the machines meet all safety requirements to protect operators and reduce liability.
How Can B2B Buyers Verify Supplier Quality Control?
For international B2B buyers, verifying the quality control processes of suppliers is critical to ensuring a reliable partnership. Here are some actionable steps:
-
Conduct Supplier Audits: Regular audits can provide insights into the supplier’s manufacturing processes and quality control measures. This can be done by the buyer or through third-party auditing services.
-
Request Quality Assurance Reports: Suppliers should be able to provide documentation detailing their quality control processes, including results from IQC, IPQC, and FQC.
-
Engage Third-Party Inspection Services: Independent inspectors can assess the machinery and manufacturing practices to ensure compliance with international standards.
What Are the QC and Certification Nuances for International B2B Buyers?
For buyers in Africa, South America, the Middle East, and Europe, understanding the nuances of quality control and certification is essential. Each region may have different regulatory requirements, and it’s important to ensure that the suppliers comply with these regulations. For instance, while CE marking is mandatory in Europe, certain countries in Africa may have different certifications that are equally important.
Furthermore, buyers should consider the logistical aspects of sourcing machinery internationally. This includes understanding import regulations, tariffs, and potential delays in the supply chain that could affect the delivery and installation of machinery.
Conclusion: How to Ensure Quality in Your Purchase of Rolling Machines for Tobacco
When investing in rolling machines for tobacco, international B2B buyers should prioritize understanding the manufacturing processes and quality assurance measures in place. By focusing on certified suppliers, conducting thorough audits, and ensuring compliance with international standards, buyers can minimize risks and ensure the longevity and efficiency of their machinery. Understanding these processes not only aids in making informed purchasing decisions but also fosters long-term partnerships that can lead to competitive advantages in the market.
Practical Sourcing Guide: A Step-by-Step Checklist for ‘rolling machines for tobacco’
This guide serves as a practical checklist for B2B buyers in the tobacco industry looking to procure rolling machines. By following these steps, you can ensure a streamlined sourcing process that meets your operational needs and enhances your production capabilities.
Step 1: Define Your Technical Specifications
Understanding your specific requirements is the first critical step in sourcing rolling machines. Determine the type of tobacco products you will be rolling, the expected production volume, and the desired level of automation.
- Machine Capacity: Assess how many units you need to produce per hour.
- Type of Rolling: Decide whether you need manual, semi-automatic, or fully automatic machines.
Step 2: Research Market Trends and Innovations
Staying informed about the latest industry trends and technologies is essential for making a sound investment. Explore emerging technologies that improve efficiency and reduce waste.
- Sustainable Practices: Consider machines that incorporate eco-friendly processes.
- New Features: Look for innovations like enhanced precision and reduced downtime.
Step 3: Evaluate Potential Suppliers
Before committing to a supplier, conduct thorough evaluations. Request detailed company profiles, including their history, customer testimonials, and case studies relevant to your industry.
- Industry Experience: Choose suppliers with proven expertise in manufacturing rolling machines for tobacco.
- Client References: Seek feedback from other businesses in your region to gauge reliability.
Step 4: Verify Supplier Certifications and Compliance
Ensure that your chosen suppliers adhere to international quality standards. This is particularly important for B2B transactions involving machinery that affects production quality.
- ISO Certifications: Check if the supplier has relevant ISO certifications that guarantee quality management.
- Regulatory Compliance: Confirm that their machines comply with regional regulations, particularly in your target markets.
Step 5: Request Samples and Demonstrations
Before finalizing your order, it’s prudent to request samples or product demonstrations. This allows you to evaluate the machine’s performance firsthand.
- Testing: Assess the machine’s ease of use, speed, and output quality.
- Adaptability: Ensure the machine can handle different types of tobacco and rolling specifications.
Step 6: Negotiate Terms and Conditions
Once you’ve identified a suitable supplier, focus on negotiating the best terms and conditions. This includes pricing, payment terms, warranties, and after-sales support.
- Warranty Provisions: Ensure that the warranty covers parts and labor for a reasonable period.
- Payment Flexibility: Look for options that allow for installment payments to ease cash flow.
Step 7: Plan for Logistics and After-Sales Support
Finally, consider the logistics of shipping and installation, as well as ongoing support. A reliable supplier should provide comprehensive after-sales service, including training for your staff.
- Shipping Arrangements: Clarify who bears the shipping costs and how long delivery will take.
- Technical Support: Ensure that the supplier offers robust technical support to resolve any operational issues post-installation.
By following this structured checklist, B2B buyers can make informed decisions when sourcing rolling machines for tobacco, ensuring they select the best equipment to meet their production needs effectively.
Comprehensive Cost and Pricing Analysis for rolling machines for tobacco Sourcing
What Are the Key Cost Components for Rolling Machines for Tobacco?
Understanding the cost structure associated with rolling machines for tobacco is essential for international B2B buyers. The primary cost components include:
-
Materials: The choice of materials directly impacts the cost. High-quality steel and specialized components can elevate prices. Consider suppliers that offer a balance between durability and cost-effectiveness.
-
Labor: Labor costs vary significantly based on the manufacturing location. Countries with lower labor costs, such as those in Southeast Asia, might provide more competitive pricing, but ensure that labor standards meet your quality requirements.
-
Manufacturing Overhead: This includes expenses related to utilities, factory maintenance, and indirect labor. Higher overhead can lead to increased prices, so it’s crucial to evaluate suppliers’ operational efficiency.
-
Tooling: Initial tooling costs for custom machines can be substantial. If you require bespoke specifications, inquire about how these costs will affect your overall price.
-
Quality Control (QC): Implementing strict QC measures ensures product reliability but can add to the cost. Opt for suppliers who are certified to international quality standards, as this can mitigate future operational risks.
-
Logistics: Shipping and handling costs vary based on the distance and mode of transport. Be mindful of potential tariffs and customs duties, which can significantly affect your total expenditure.
-
Margin: Supplier profit margins can fluctuate based on their market positioning and production capabilities. Always assess whether the margin aligns with the value provided.
How Do Price Influencers Affect the Cost of Rolling Machines?
Several factors influence the pricing of rolling machines for tobacco:
-
Volume/MOQ (Minimum Order Quantity): Bulk purchasing often leads to discounts. Negotiate terms that allow for flexibility in order quantities without significantly increasing unit costs.
-
Specifications and Customization: Customized machines tailored to specific production needs can incur higher costs. Clearly define your requirements to avoid unexpected charges.
-
Materials and Quality Certifications: Premium materials and certifications (e.g., ISO) can increase the price but may lead to long-term savings due to improved machine longevity and performance.
-
Supplier Factors: The supplier’s reputation, experience, and reliability play a crucial role. Established suppliers may charge more but offer better support and warranty options.
-
Incoterms: Understanding the terms of shipping (e.g., FOB, CIF) can influence overall costs. Choose terms that best align with your logistics strategy to control expenses.
What Buyer Tips Can Enhance Cost-Efficiency?
International buyers should consider the following actionable tips to enhance cost-efficiency when sourcing rolling machines for tobacco:
-
Negotiate Wisely: Build relationships with suppliers and engage in open discussions regarding pricing. Highlight your long-term purchasing potential to secure better rates.
-
Assess Total Cost of Ownership (TCO): Beyond the initial purchase price, consider maintenance, operational costs, and potential downtime. A machine with a higher upfront cost may prove more economical over its lifecycle.
-
Stay Informed About Pricing Nuances: Prices can fluctuate based on market demand, currency exchange rates, and geopolitical factors, especially in regions like Africa, South America, and the Middle East. Stay updated on these trends to make informed purchasing decisions.
-
Utilize Local Expertise: In regions like Europe, leveraging local agents or consultants familiar with the market can provide valuable insights and facilitate negotiations.
Disclaimer on Indicative Prices
While this analysis provides a framework for understanding costs and pricing in the tobacco rolling machine market, actual prices can vary widely based on specific supplier capabilities, market conditions, and individual buyer requirements. Always request detailed quotes from multiple suppliers to compare and assess value effectively.
Alternatives Analysis: Comparing rolling machines for tobacco With Other Solutions
In the competitive landscape of tobacco production, selecting the right equipment is crucial for optimizing efficiency and product quality. While rolling machines for tobacco are a popular choice, there are alternative solutions that may better suit specific operational needs. Understanding these alternatives can help international B2B buyers make informed decisions based on performance, cost, and ease of implementation.
Comparison Table of Rolling Machines for Tobacco and Alternative Solutions
Comparison Aspect | Rolling Machines For Tobacco | Hand Rolling Techniques | Automated Packing Solutions |
---|---|---|---|
Performance | High efficiency and consistency in production. | Variable performance; relies on skill level. | Extremely efficient; minimizes human error. |
Cost | Higher initial investment; long-term savings possible. | Low initial cost; ongoing labor costs can add up. | Moderate to high cost; ROI depends on volume. |
Ease of Implementation | Requires training for operators; setup can be complex. | Simple to implement; no special training needed. | Requires significant setup and training. |
Maintenance | Regular maintenance needed; parts may require replacement. | Minimal maintenance; skill degradation over time. | Requires specialized maintenance; can be costly. |
Best Use Case | High-volume production with consistent quality demands. | Small-scale or artisanal production. | Large-scale operations with a focus on efficiency. |
What Are the Pros and Cons of Hand Rolling Techniques?
Hand rolling techniques, while traditional, offer a unique approach to tobacco production. One of the primary advantages is the low initial cost; businesses can start producing with minimal investment in equipment. Additionally, this method allows for a level of craftsmanship that may appeal to niche markets seeking artisanal products. However, the variability in performance is a significant drawback. The quality and consistency of the final product can fluctuate based on the skill of the roller, which may not meet the standards required for larger operations. Furthermore, as demand increases, relying solely on hand rolling can become labor-intensive and less efficient.
How Do Automated Packing Solutions Compare?
Automated packing solutions represent a cutting-edge alternative that enhances operational efficiency in large-scale tobacco production. These systems are designed to minimize human error and maximize speed, which is particularly beneficial in high-demand scenarios. The moderate to high cost of these solutions is often justified by the return on investment (ROI) seen in increased output and reduced labor costs. However, the initial setup can be complex and may require specialized training for operators. Maintenance can also be a concern, as automated systems often need specific care that can lead to higher long-term costs.
Conclusion: How Can B2B Buyers Choose the Right Tobacco Rolling Solution?
When determining the best solution for tobacco rolling, B2B buyers must evaluate their specific operational needs, production volume, and budget constraints. Rolling machines for tobacco offer high efficiency and consistency, making them ideal for large-scale operations. However, for businesses focused on artisanal products or those with lower production demands, hand rolling may be more suitable. Automated packing solutions can provide significant advantages in speed and accuracy but come with higher costs and maintenance considerations. By carefully assessing these factors, buyers can select the most appropriate solution that aligns with their business objectives and market demands.
Essential Technical Properties and Trade Terminology for rolling machines for tobacco
What Are the Key Technical Properties of Rolling Machines for Tobacco?
When selecting rolling machines for tobacco, understanding their technical properties is crucial for ensuring optimal performance and durability. Here are several essential specifications that international B2B buyers should consider:
1. Material Grade
The material grade of a rolling machine significantly influences its longevity and resistance to wear. Common materials include stainless steel, which offers corrosion resistance, and high-carbon steel, known for its strength. Buyers should assess the material grade to ensure it meets the specific demands of their production environment, especially in humid or high-temperature regions typical in Africa and South America.
2. Tolerance Levels
Tolerance refers to the permissible limits of variation in a physical dimension. For rolling machines, tighter tolerances can lead to better product consistency and quality. This specification is vital for manufacturers aiming to meet stringent regulatory standards or seeking to maintain brand reputation in competitive markets. Understanding tolerance levels can also impact maintenance costs and machine lifespan.
3. Production Capacity
The production capacity, often measured in units per hour, indicates how much tobacco the machine can process in a given timeframe. This specification is particularly important for businesses with fluctuating demand or those looking to scale operations. Evaluating production capacity allows buyers to align machinery with their operational goals, ensuring efficiency without over-investing in equipment.
4. Power Consumption
Energy efficiency is a growing concern for manufacturers worldwide. Understanding the power consumption of rolling machines can significantly affect operational costs. Machines that require less energy can lead to substantial savings over time, making it essential for B2B buyers to consider this property in relation to their overall production budget.
5. Machine Dimensions
The physical dimensions of the rolling machine, including its footprint and height, play a critical role in space management within production facilities. International buyers should evaluate their available space and ensure that the chosen machine fits seamlessly into their production line, especially in facilities with limited space.
What Are Common Trade Terms Related to Rolling Machines for Tobacco?
Navigating the procurement process for rolling machines involves understanding key trade terminology. Here are several essential terms that B2B buyers should be familiar with:
1. OEM (Original Equipment Manufacturer)
OEM refers to a company that produces parts or equipment that may be marketed by another manufacturer. In the context of rolling machines, buyers may seek OEM partnerships to ensure they receive quality machinery that meets industry standards. Understanding OEM relationships can help buyers make informed decisions about sourcing and reliability.
2. MOQ (Minimum Order Quantity)
MOQ is the smallest quantity of a product that a supplier is willing to sell. For rolling machines, understanding the MOQ is essential for budgeting and inventory management. Buyers should negotiate MOQs to ensure they can meet production needs without overcommitting resources.
3. RFQ (Request for Quotation)
An RFQ is a document sent to suppliers to invite them to bid on specific products or services. For rolling machines, issuing an RFQ allows buyers to compare pricing, specifications, and terms from multiple vendors, ensuring they make a cost-effective and informed choice.
4. Incoterms (International Commercial Terms)
Incoterms are internationally recognized rules that define the responsibilities of buyers and sellers in international transactions. Familiarity with Incoterms is crucial for B2B buyers as they outline aspects such as shipping, insurance, and risk transfer. Understanding these terms helps buyers manage logistics and costs effectively.
5. Lead Time
Lead time refers to the time taken from placing an order to receiving the product. In the context of rolling machines, understanding lead times can impact production schedules and cash flow management. Buyers should factor lead times into their planning to avoid disruptions in their manufacturing processes.
By grasping these essential technical properties and trade terms, international B2B buyers can make informed decisions when procuring rolling machines for tobacco, ultimately enhancing their operational efficiency and competitiveness in the global market.
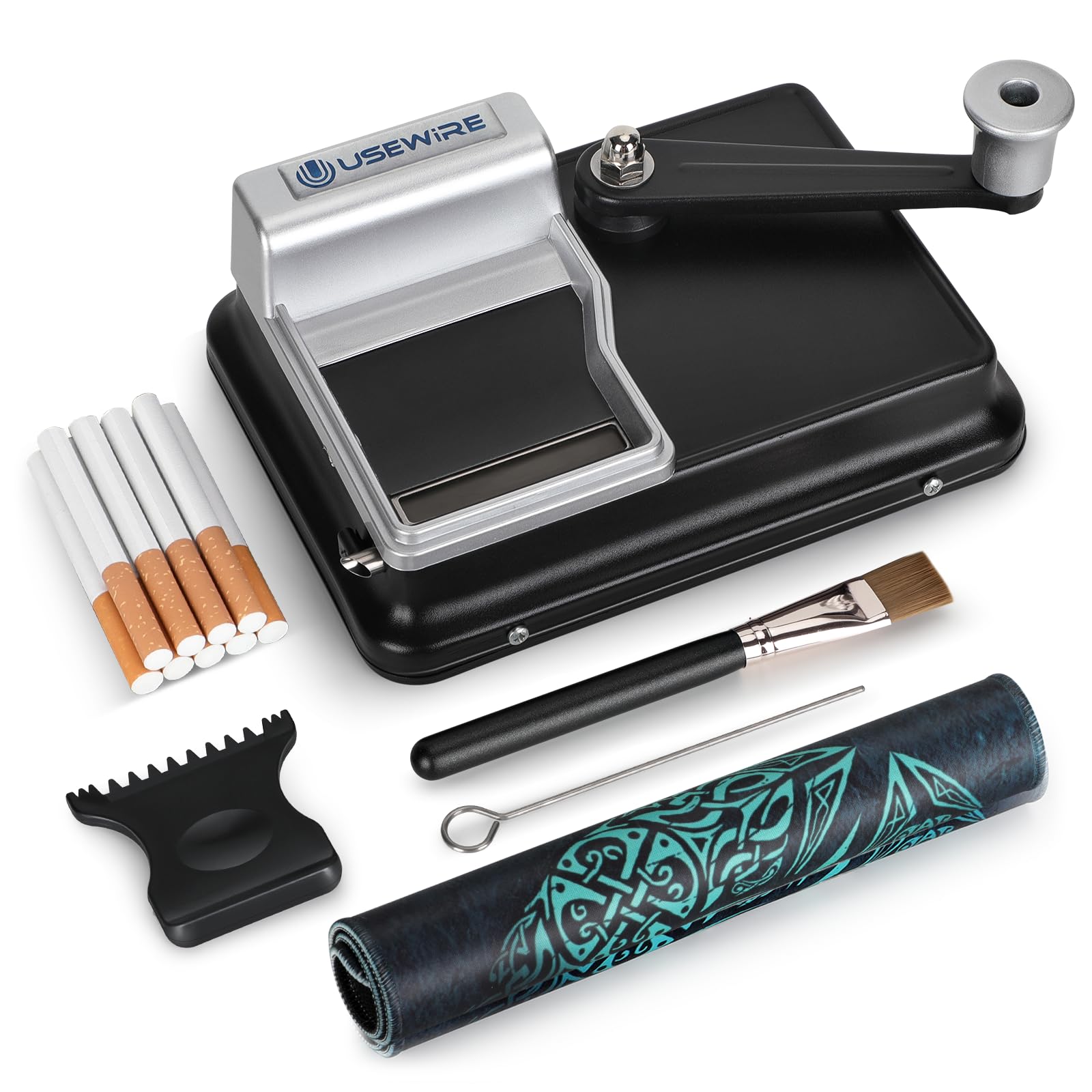
A stock image related to rolling machines for tobacco.
Navigating Market Dynamics and Sourcing Trends in the rolling machines for tobacco Sector
What Are the Current Market Dynamics for Rolling Machines in the Tobacco Sector?
The global market for rolling machines used in the tobacco industry is experiencing significant transformation driven by several factors. One of the primary drivers is the increasing demand for custom and high-quality tobacco products, particularly in emerging markets across Africa, South America, the Middle East, and Europe. The rise of local brands and artisanal tobacco products is prompting manufacturers to invest in advanced rolling technologies that enhance efficiency and product quality. Additionally, innovations in automation and smart manufacturing technologies are reshaping sourcing strategies, allowing companies to optimize production processes and reduce operational costs.
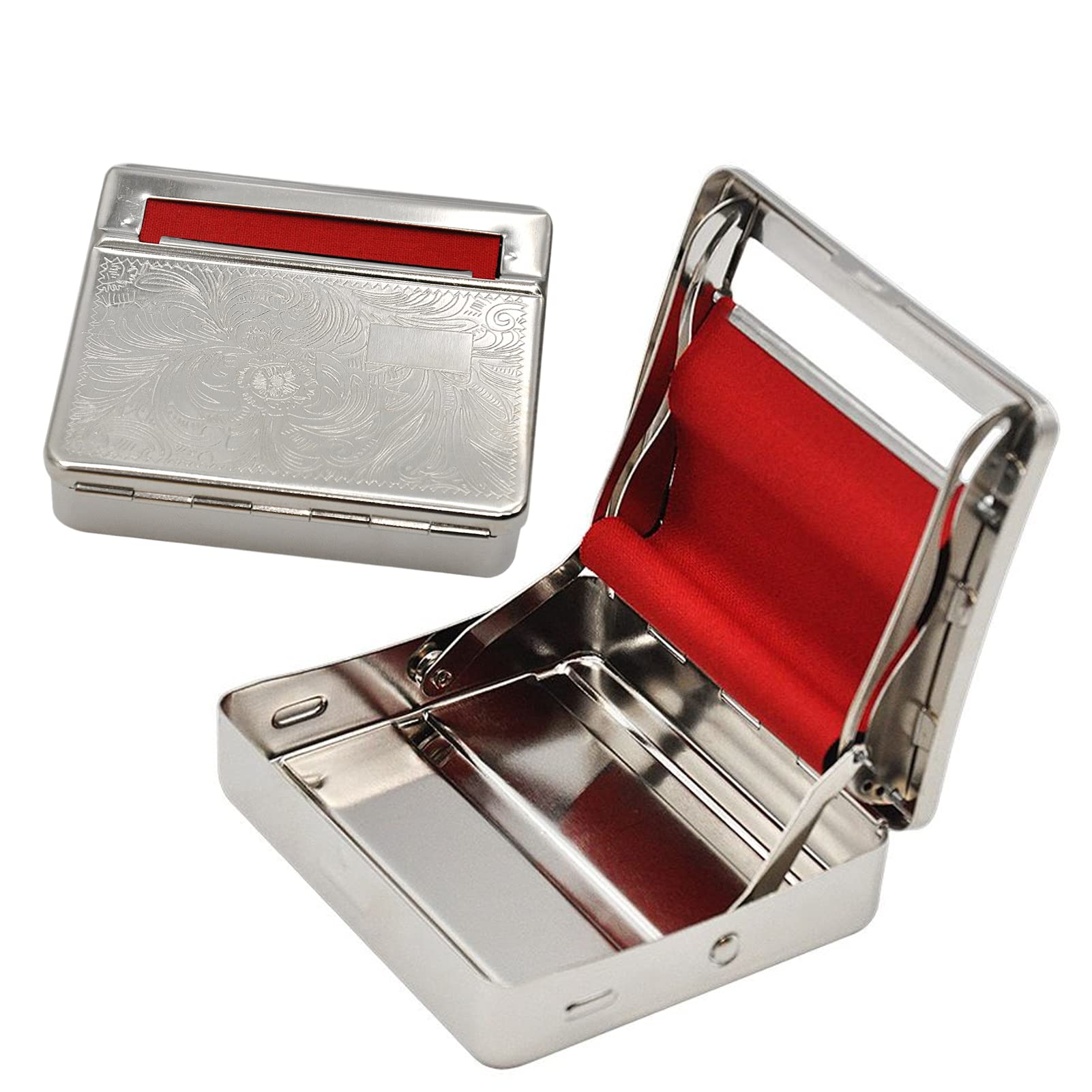
A stock image related to rolling machines for tobacco.
International B2B buyers are also witnessing a shift towards digitization and e-commerce platforms that facilitate easier sourcing of rolling machines. These platforms enable buyers to compare specifications, prices, and supplier ratings in real-time, thus enhancing decision-making capabilities. Notably, sustainability has become a pivotal concern, with buyers increasingly favoring suppliers that adopt eco-friendly practices and materials in their production processes. As a result, companies are urged to stay abreast of these trends to ensure they align their sourcing strategies with market demands.
How Is Sustainability Influencing the Sourcing of Rolling Machines for Tobacco?
The environmental impact of tobacco production, including the use of rolling machines, is under scrutiny, making sustainability a key consideration for B2B buyers. The industry is witnessing a push towards ethical sourcing and sustainable practices to reduce carbon footprints and waste. Buyers are encouraged to seek suppliers that prioritize eco-friendly materials and manufacturing processes, such as those using renewable energy sources or recyclable components in their rolling machines.
Certifications like ISO 14001 (Environmental Management) and adherence to the Global Reporting Initiative (GRI) standards are increasingly becoming prerequisites for suppliers aiming to establish credibility in the market. Furthermore, the adoption of ‘green’ certifications not only aligns with global sustainability goals but also appeals to a growing segment of environmentally conscious consumers. By partnering with manufacturers that emphasize sustainability, B2B buyers can enhance their brand reputation and meet the rising consumer demand for ethical products.
What Is the Historical Context Behind Rolling Machines in the Tobacco Sector?
The evolution of rolling machines for tobacco can be traced back to the late 19th century when manual rolling techniques were predominant. Initially, these machines were designed to enhance productivity and reduce labor costs. Over the decades, technological advancements led to the development of semi-automated and fully automated machines, which significantly increased efficiency and consistency in production.
In recent years, the focus has shifted from merely improving output to incorporating advanced technologies such as artificial intelligence and machine learning. These innovations allow for greater precision in rolling, reducing waste and improving product quality. As the market continues to evolve, understanding this historical context is essential for B2B buyers looking to invest in the latest rolling machine technologies that meet current industry standards and consumer expectations.
Frequently Asked Questions (FAQs) for B2B Buyers of rolling machines for tobacco
-
How do I choose the right rolling machine for my tobacco production needs?
Selecting the right rolling machine involves assessing your production volume, the type of tobacco products you plan to produce, and the level of automation required. Consider machines that offer adjustable settings for different tobacco blends and rolling styles. It’s also crucial to evaluate the machine’s durability, ease of maintenance, and availability of spare parts. Engaging with suppliers who provide demonstrations or trial periods can help you make a more informed decision. -
What is the best rolling machine for small-scale tobacco manufacturers?
For small-scale manufacturers, a manual or semi-automatic rolling machine is often ideal. These machines are typically more affordable and require less initial investment, making them suitable for limited budgets. Look for machines that are compact, easy to operate, and designed for versatility, allowing you to produce various tobacco products without significant downtime or complex setup processes. -
What should I consider when vetting suppliers of rolling machines for tobacco?
When vetting suppliers, prioritize their experience in the tobacco machinery sector, customer reviews, and after-sales support. Check for certifications that demonstrate compliance with international quality standards. Additionally, assess their manufacturing capabilities, lead times, and responsiveness to inquiries. Establishing a direct line of communication with potential suppliers can also provide insights into their reliability and transparency. -
What are the common minimum order quantities (MOQ) for rolling machines?
Minimum order quantities can vary significantly by supplier and region. Typically, MOQs for rolling machines range from one unit for custom or specialized machines to several units for standard models. It’s essential to discuss your specific needs with suppliers, as some may be flexible with MOQs, especially for first-time buyers. Consider negotiating terms that allow for smaller initial orders while ensuring you have a stable supply for future needs.
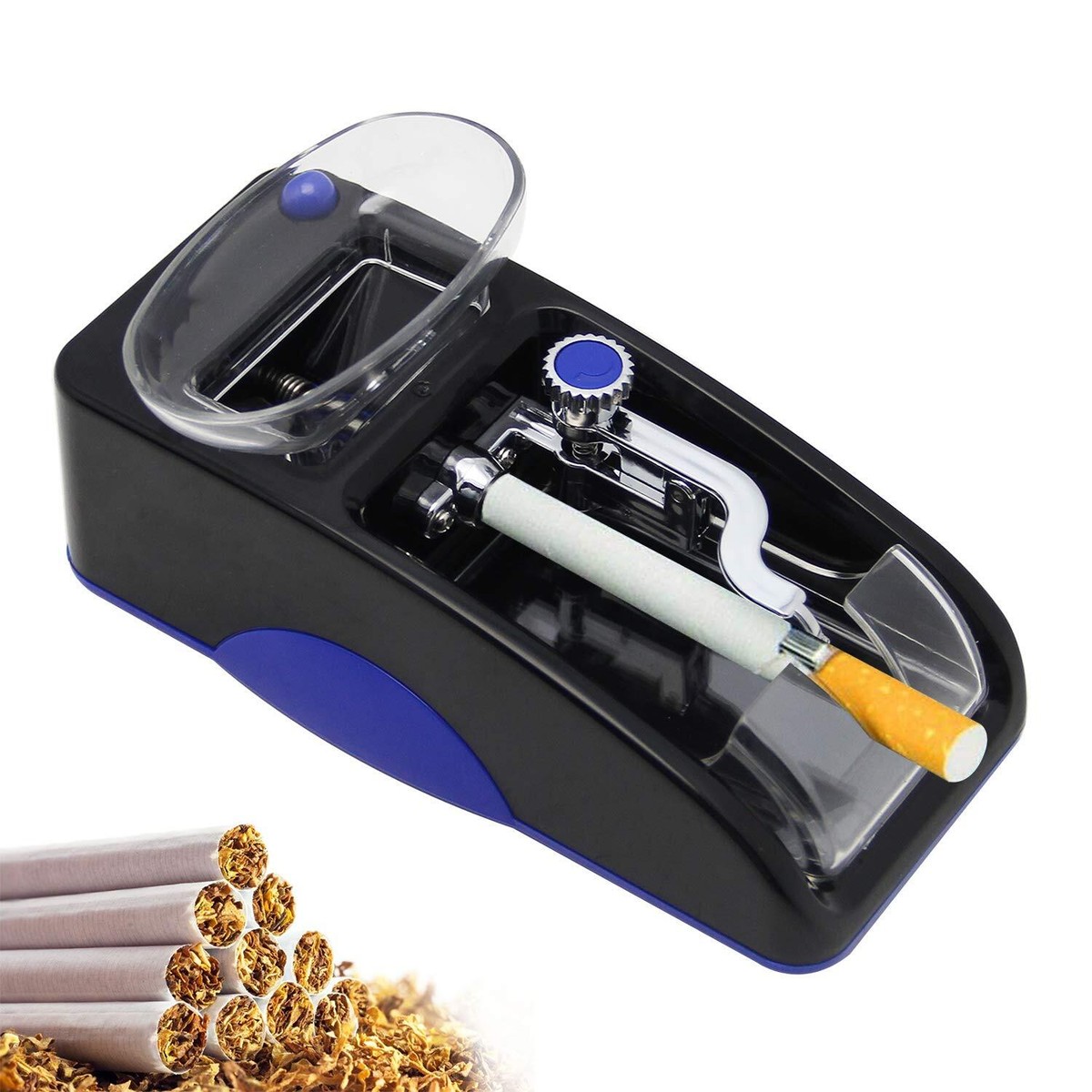
A stock image related to rolling machines for tobacco.
-
What payment terms should I expect when purchasing rolling machines internationally?
Payment terms can vary widely, but common practices include partial payment upfront (30-50%) with the balance due upon shipment or delivery. Some suppliers may offer financing options or installment plans for larger orders. Always clarify payment methods accepted, such as bank transfers, letters of credit, or escrow services, to ensure secure transactions. Be cautious of suppliers requiring full payment in advance, especially if they have limited market presence. -
How can I ensure quality assurance for rolling machines sourced internationally?
To ensure quality assurance, request detailed specifications and certifications from suppliers, such as ISO 9001. Conducting factory visits or audits can provide firsthand insights into their manufacturing processes. Additionally, consider third-party quality inspection services that can verify product standards before shipment. Establishing a clear return policy in case of defects is also crucial for mitigating risks associated with international sourcing. -
What logistics considerations should I be aware of when importing rolling machines?
Logistics considerations include understanding shipping methods, costs, and delivery timelines. Be aware of customs duties and import regulations specific to your country, as they can affect overall expenses. It’s advisable to partner with a reliable freight forwarder experienced in handling machinery shipments to navigate logistics complexities. Ensure that the supplier provides all necessary documentation for customs clearance, including invoices and certificates of origin. -
How can I customize a rolling machine to meet my specific production requirements?
Many manufacturers offer customization options for rolling machines, allowing you to tailor features such as size, speed, and operational capabilities. When discussing customization, provide detailed specifications and production goals to the supplier. This may include adjustments for different tobacco types or integration with existing production lines. Be prepared for potential lead time extensions and additional costs associated with custom features.
Important Disclaimer & Terms of Use
⚠️ Important Disclaimer
The information provided in this guide, including content regarding manufacturers, technical specifications, and market analysis, is for informational and educational purposes only. It does not constitute professional procurement advice, financial advice, or legal advice.
While we have made every effort to ensure the accuracy and timeliness of the information, we are not responsible for any errors, omissions, or outdated information. Market conditions, company details, and technical standards are subject to change.
B2B buyers must conduct their own independent and thorough due diligence before making any purchasing decisions. This includes contacting suppliers directly, verifying certifications, requesting samples, and seeking professional consultation. The risk of relying on any information in this guide is borne solely by the reader.
Strategic Sourcing Conclusion and Outlook for rolling machines for tobacco
In conclusion, effective strategic sourcing of rolling machines for tobacco is essential for international B2B buyers aiming to enhance operational efficiency and product quality. By prioritizing suppliers that offer advanced technology and customization options, businesses can not only reduce costs but also improve production capabilities. Understanding regional market dynamics, particularly in Africa, South America, the Middle East, and Europe, allows buyers to make informed decisions that align with local regulations and consumer preferences.
What are the key factors influencing your sourcing decisions for rolling machines? Collaborating with reputable manufacturers who have a track record of reliability and customer support can mitigate risks and ensure a smoother procurement process. Furthermore, leveraging trade shows and industry networks can open doors to innovative solutions and partnerships.
As the market for tobacco products continues to evolve, staying abreast of technological advancements and regulatory changes will be crucial. Engage with suppliers who are committed to sustainability and innovation, as these factors will play a significant role in future-proofing your operations. Embrace the opportunities that strategic sourcing presents, and take the next step towards optimizing your production processes and staying competitive in a dynamic global market.