Discover Cost-Effective Recycling Equipment for Sale (2025)
Introduction: Navigating the Global Market for recycling equipment for sale
Navigating the complexities of sourcing recycling equipment for sale can be a daunting challenge for international B2B buyers, especially in rapidly developing markets across Africa, South America, the Middle East, and Europe. As environmental regulations tighten and sustainability becomes a priority, businesses are increasingly tasked with finding reliable and efficient recycling solutions. This guide serves as a comprehensive resource, covering various types of recycling equipment, their applications, and essential factors to consider when making purchasing decisions.
From waste shredders and balers to sorting systems and compactors, understanding the diverse options available is crucial. We delve into the intricacies of supplier vetting, ensuring that you engage with reputable manufacturers and distributors who meet international standards. Additionally, we analyze cost implications, helping you navigate budget constraints while maximizing the return on investment.
This guide empowers B2B buyers by providing actionable insights tailored to their unique needs. Whether you’re in Colombia looking to enhance your recycling capabilities or in the Middle East seeking sustainable waste management solutions, our expertise will equip you with the knowledge to make informed decisions. By understanding the global market landscape, you can effectively source the right recycling equipment that aligns with your operational goals and environmental commitments.
Understanding recycling equipment for sale Types and Variations
Type Name | Key Distinguishing Features | Primary B2B Applications | Brief Pros & Cons for Buyers |
---|---|---|---|
Shredders | High-capacity machines for reducing waste size | E-waste, plastics, and metal recycling | Pros: Efficient size reduction; Cons: May require regular maintenance. |
Balers | Compresses recyclables into bales for easy transport | Paper, cardboard, and plastics | Pros: Maximizes storage space; Cons: Initial investment can be high. |
Granulators | Used for grinding plastics into small particles | Plastic recycling | Pros: Produces uniform particles; Cons: Limited to specific materials. |
Sorting Systems | Automated systems for sorting materials based on type | Mixed recyclables | Pros: Increases efficiency; Cons: High upfront costs and complexity. |
Compact Crushers | Reduces the size of construction and demolition waste | C&D debris recycling | Pros: Versatile for various materials; Cons: Requires space and power. |
What Are the Characteristics of Shredders in Recycling Equipment?
Shredders are essential in the recycling process, particularly for materials like e-waste, plastics, and metals. They work by cutting down large items into smaller, manageable pieces, making it easier to handle and process waste. When considering a shredder, buyers should evaluate its capacity, power requirements, and the types of materials it can handle. Regular maintenance is a key consideration, as wear and tear can affect performance.
How Do Balers Enhance Recycling Efficiency?
Balers are pivotal for organizations that deal with large volumes of recyclable materials, such as paper, cardboard, and plastics. These machines compress materials into compact bales, optimizing storage and reducing transportation costs. Buyers should look for balers that fit their volume needs and consider the cost versus potential savings on transport. While the initial investment can be substantial, the long-term benefits in efficiency and space-saving can be significant.
What Are the Benefits of Using Granulators for Plastic Recycling?
Granulators are specialized machines designed to grind plastic waste into uniform particles, facilitating further processing. They are particularly suitable for businesses focusing on plastic recycling, as they can handle a variety of plastic types. Key purchasing considerations include the granulator’s output size, energy consumption, and compatibility with existing systems. While they offer consistent particle sizes, granulators may be limited to specific materials, which can affect their versatility.
Why Are Sorting Systems Essential for Effective Recycling?
Sorting systems play a crucial role in recycling operations by automatically sorting mixed recyclables into their respective categories. This increases efficiency and reduces labor costs. When purchasing sorting systems, businesses should assess the technology used, accuracy rates, and the types of materials that can be sorted. Although the initial investment may be high, the long-term operational efficiency can justify the cost, especially for larger operations.
How Do Compact Crushers Facilitate Construction Waste Recycling?
Compact crushers are designed to reduce the size of construction and demolition (C&D) waste, making them valuable for recycling operations focused on building materials. These machines can process various materials, including concrete, bricks, and asphalt. Buyers should consider the crusher’s capacity, power requirements, and mobility. While they offer versatility, compact crushers require adequate space and power supply, which can be a constraint for some operations.
Related Video: Waste Plastic Recycling Machine | How to recycle PP, PE into plastic pellets and granules?
Key Industrial Applications of recycling equipment for sale
Industry/Sector | Specific Application of Recycling Equipment for Sale | Value/Benefit for the Business | Key Sourcing Considerations for this Application |
---|---|---|---|
Construction and Demolition | Concrete Recycling Equipment | Reduces landfill costs and generates reusable aggregate | Equipment durability, transportability, and processing capacity |
Electronics Manufacturing | E-Waste Recycling Solutions | Extracts valuable materials and mitigates environmental impact | Compliance with local regulations, recovery rates, and efficiency |
Automotive Industry | Scrap Metal Recycling Machinery | Maximizes profit from scrap and reduces raw material costs | Machinery compatibility with existing systems and maintenance support |
Plastics Industry | Plastic Waste Granulators | Enhances recycling rates and reduces raw material dependency | Processing capacity, versatility for different plastic types |
Food and Beverage Processing | Organic Waste Composting Equipment | Converts waste into compost, reducing disposal costs | Capacity for waste volume, energy efficiency, and ease of operation |
How is Recycling Equipment Used in the Construction and Demolition Sector?
Recycling equipment, particularly concrete crushers and screeners, is essential in the construction and demolition sector. These machines process waste concrete into reusable aggregate, significantly reducing landfill costs and promoting sustainable building practices. For international buyers, especially in developing regions like Africa and South America, equipment that is durable and easy to transport can be crucial due to varying infrastructure conditions.
What are the Applications of E-Waste Recycling Solutions in Electronics Manufacturing?
E-waste recycling solutions enable electronics manufacturers to recover valuable metals and components from discarded devices. This not only reduces environmental harm but also provides a sustainable supply of materials for production. Buyers from the Middle East and Europe must consider compliance with local environmental regulations and the efficiency of recovery rates to maximize profitability.
How Does Scrap Metal Recycling Machinery Benefit the Automotive Industry?
In the automotive industry, scrap metal recycling machinery allows businesses to efficiently process end-of-life vehicles, extracting valuable metals like aluminum and steel. This process maximizes profit margins by turning waste into revenue while reducing the need for new raw materials. When sourcing equipment, automotive companies should prioritize machinery that integrates well with existing operations and offers robust maintenance support.
What Role Do Plastic Waste Granulators Play in the Plastics Industry?
Plastic waste granulators are pivotal in the plastics industry, allowing manufacturers to recycle post-consumer waste into reusable materials. This not only enhances recycling rates but also decreases reliance on virgin plastics, supporting sustainability initiatives. B2B buyers, particularly in Europe, should focus on granulators that can handle various plastic types and possess sufficient processing capacity to meet production demands.
How Can Organic Waste Composting Equipment Transform Food and Beverage Processing?
Organic waste composting equipment is increasingly vital in the food and beverage sector, where it converts organic waste into compost, thus minimizing disposal costs and environmental impact. This equipment is particularly beneficial for businesses looking to enhance their sustainability profile. Buyers should evaluate equipment based on its capacity to handle waste volume, energy efficiency, and operational simplicity to ensure a seamless integration into their processes.
Related Video: Magnetic Separators and Eddy Current Separators in action for the Recycling Industry
3 Common User Pain Points for ‘recycling equipment for sale’ & Their Solutions
Scenario 1: Navigating Regulatory Compliance for Recycling Equipment
The Problem:
International B2B buyers, especially in regions like Africa and South America, often face challenges in ensuring that the recycling equipment they purchase complies with local regulations. Many countries have specific standards regarding emissions, noise levels, and waste management practices. Failure to comply can lead to hefty fines and operational delays, which can significantly impact profitability. Buyers may feel overwhelmed by the complexity of regulations that vary not only from country to country but also within regions.
The Solution:
To effectively navigate regulatory compliance, buyers should start by conducting thorough research on local regulations regarding recycling equipment. Engaging with local industry associations or consulting with legal experts can provide invaluable insights into compliance requirements. When sourcing recycling equipment for sale, buyers should prioritize suppliers who can demonstrate compliance with these regulations, such as providing certification documents and detailed technical specifications.
Additionally, consider investing in equipment that offers adaptability to future regulatory changes. This could mean opting for modular systems that can be upgraded or modified without complete replacement. Lastly, maintaining open communication with equipment suppliers can help buyers stay informed about any changes in legislation, ensuring they can adapt their operations proactively.
Scenario 2: Assessing Equipment Quality and Reliability in Recycling Machinery
The Problem:
B2B buyers often struggle with the challenge of assessing the quality and reliability of recycling equipment. This is particularly critical for companies in developing markets, where lower-quality machinery can lead to frequent breakdowns, increased maintenance costs, and ultimately reduced productivity. Buyers may find it difficult to distinguish between high-quality equipment and subpar alternatives, especially when evaluating options from international suppliers.
The Solution:
To ensure the quality and reliability of recycling equipment, buyers should implement a structured evaluation process. Start by reviewing the equipment’s specifications and performance metrics in detail. Request performance data from the supplier, including case studies or testimonials from existing users, particularly those in similar industries or regions.
Conducting site visits to existing installations can also provide firsthand insights into the equipment’s performance and reliability. If possible, arrange for a demonstration of the machinery to assess its operational capabilities directly. Furthermore, consider partnering with suppliers that offer comprehensive warranties and after-sales support. This not only secures the investment but also ensures ongoing assistance, which is critical in maintaining operational efficiency.
Scenario 3: Understanding Total Cost of Ownership for Recycling Equipment
The Problem:
A common pain point for B2B buyers is the lack of clarity regarding the total cost of ownership (TCO) of recycling equipment. While initial purchase price is a significant factor, many buyers overlook long-term costs such as maintenance, energy consumption, and potential downtime. This can lead to budget overruns and unexpected expenses, particularly in markets where operational budgets are tightly constrained.
The Solution:
To gain a clearer understanding of the TCO, buyers should engage in a comprehensive cost analysis before making a purchasing decision. This involves not just evaluating the purchase price but also estimating the ongoing costs associated with energy consumption, maintenance, and potential repairs over the equipment’s lifespan.
Buyers should request detailed operating cost estimates from suppliers, including energy efficiency ratings and maintenance schedules. It’s also beneficial to ask for a breakdown of parts and service costs to understand what future expenses might look like. Additionally, consider the potential return on investment (ROI) by calculating how the equipment can improve efficiency and reduce waste over time. By taking a holistic approach to cost assessment, buyers can make more informed decisions that align with their financial goals and operational needs.
Strategic Material Selection Guide for recycling equipment for sale
What Are the Key Materials Used in Recycling Equipment?
When selecting recycling equipment, the choice of materials is critical to ensure durability, efficiency, and compliance with international standards. Here, we analyze four common materials used in recycling equipment, focusing on their properties, advantages, disadvantages, and considerations for international B2B buyers.
How Does Steel Perform in Recycling Equipment?
Key Properties:
Steel is renowned for its high tensile strength and durability. It can withstand high temperatures and pressures, making it suitable for heavy-duty applications. Additionally, steel exhibits good corrosion resistance, especially when treated with coatings.
Pros & Cons:
The primary advantage of steel is its robustness, which translates to a longer lifespan for equipment. However, it can be heavier than other materials, potentially increasing shipping costs. Manufacturing complexity can also be higher due to the need for specialized welding and fabrication processes.
Impact on Application:
Steel is compatible with various media, including metals and plastics, making it versatile for different recycling processes.
Considerations for International Buyers:
Buyers from regions like Africa and South America should ensure compliance with local standards (e.g., ASTM, DIN) when sourcing steel equipment. Additionally, they should consider the availability of local suppliers to reduce lead times.
What Role Does Aluminum Play in Recycling Equipment?
Key Properties:
Aluminum is lightweight and possesses excellent corrosion resistance. It has a lower melting point than steel, which can be advantageous in certain recycling processes.
Pros & Cons:
The lightweight nature of aluminum reduces transportation costs, and its resistance to corrosion ensures longevity. However, aluminum is less durable than steel, which may limit its use in high-stress applications. The cost of aluminum can also be higher, depending on market fluctuations.
Impact on Application:
Aluminum is particularly effective in applications involving the recycling of lightweight materials, such as beverage containers.
Considerations for International Buyers:
Buyers must be aware of the varying standards for aluminum recycling equipment across regions. Compliance with international standards is crucial, especially in Europe, where regulations are stringent.
How Does Plastic Contribute to Recycling Equipment Design?
Key Properties:
Plastics, such as polyethylene and polypropylene, are lightweight and resistant to corrosion. They can be molded into complex shapes, allowing for innovative designs in recycling equipment.
Pros & Cons:
The main advantage of plastic is its versatility and lower cost compared to metals. However, plastics may not withstand high temperatures or heavy loads, limiting their application in certain environments.
Impact on Application:
Plastic components are ideal for equipment designed to handle softer materials, such as paper and textiles.
Considerations for International Buyers:
B2B buyers should consider the environmental impact of plastic materials and ensure compliance with recycling regulations in their respective countries, particularly in Europe, where eco-design principles are emphasized.
What Advantages Does Stainless Steel Offer for Recycling Equipment?
Key Properties:
Stainless steel combines the strength of steel with enhanced corrosion resistance. It can withstand extreme temperatures and is often used in applications requiring hygiene, such as food waste recycling.
Pros & Cons:
The primary advantage of stainless steel is its durability and resistance to rust, making it suitable for long-term use. However, it is more expensive than regular steel and can be challenging to work with due to its hardness.
Impact on Application:
Stainless steel is particularly effective in recycling processes involving organic materials, where hygiene is paramount.
Considerations for International Buyers:
When sourcing stainless steel equipment, buyers should verify compliance with international standards and certifications, as these can vary significantly between regions.
Summary Table of Material Selection for Recycling Equipment
Material | Typical Use Case for recycling equipment for sale | Key Advantage | Key Disadvantage/Limitation | Relative Cost (Low/Med/High) |
---|---|---|---|---|
Steel | Heavy-duty machinery for metal recycling | High durability | Heavier, higher shipping costs | Medium |
Aluminum | Lightweight applications like beverage containers | Lightweight, corrosion-resistant | Less durable, higher cost | High |
Plastic | Equipment for soft materials like paper | Versatile, lower cost | Limited temperature resistance | Low |
Stainless Steel | Organic waste recycling equipment | Excellent corrosion resistance | More expensive, harder to work with | High |
This strategic guide on material selection will help international B2B buyers make informed decisions when sourcing recycling equipment, ensuring they consider performance, cost, and compliance with local regulations.
In-depth Look: Manufacturing Processes and Quality Assurance for recycling equipment for sale
What Are the Main Manufacturing Processes for Recycling Equipment?
Manufacturing recycling equipment involves several critical stages that ensure the equipment meets functionality and durability standards. The primary stages include material preparation, forming, assembly, and finishing.
How Is Material Prepared for Recycling Equipment Manufacturing?
The first step in the manufacturing process is material preparation. This phase involves selecting the appropriate raw materials, such as high-quality steel, aluminum, and plastics. Suppliers often conduct thorough material inspections to ensure compliance with standards.
Once the materials are selected, they undergo processes such as cutting, machining, and surface treatment. This ensures that the raw materials are suitable for subsequent forming processes. For instance, steel plates may be cut into specific dimensions before being shaped into components.
What Techniques Are Used for Forming Recycling Equipment?
The forming process involves transforming raw materials into usable parts through various techniques, including stamping, welding, and extrusion.
-
Stamping: This technique is used to create complex shapes and components by applying high pressure. It is common for parts like frames and casings.
-
Welding: Essential for assembling different parts, welding ensures that components are securely joined. Different welding methods, such as MIG and TIG, are used based on the material type and thickness.
-
Extrusion: This method is used to produce continuous profiles, such as tubes and channels, which are often used in conveyor systems or shredders.
Each technique must be executed with precision to ensure the structural integrity and performance of the recycling equipment.
How Is Recycling Equipment Assembled and Finished?
After forming, the next stage is assembly. This involves the systematic joining of various components to create the final product. Assembly lines are often used, and workers are trained to ensure that each piece fits correctly and functions as intended.
Finishing processes, such as painting and coating, enhance the equipment’s durability and resistance to corrosion. This is particularly important for recycling equipment, which often operates in harsh environments. Surface treatments may include powder coating or galvanization to provide long-lasting protection.
What Quality Assurance Standards Should B2B Buyers Consider?
Quality assurance is crucial in the manufacturing of recycling equipment. Buyers should be aware of several international standards that guarantee the quality and safety of the equipment.
How Do ISO and Other Certifications Impact Quality Assurance?
ISO 9001 is a widely recognized standard that outlines requirements for a quality management system (QMS). Manufacturers that are ISO 9001 certified have demonstrated their ability to consistently provide products that meet customer and regulatory requirements.
Additionally, specific certifications such as CE marking (for compliance with European safety standards) and API (American Petroleum Institute) certifications for specific industrial applications are also essential. These certifications indicate that the equipment adheres to stringent safety and performance standards.
What Are the Key QC Checkpoints in Recycling Equipment Manufacturing?
Quality control (QC) processes are integral to ensuring that recycling equipment meets required specifications. Key QC checkpoints include:
-
Incoming Quality Control (IQC): This is the initial inspection of raw materials upon delivery. Suppliers must verify that materials meet specified standards before they are used in manufacturing.
-
In-Process Quality Control (IPQC): During manufacturing, random inspections are conducted to ensure that each stage of production adheres to quality standards. This includes monitoring forming techniques, assembly accuracy, and surface treatments.
-
Final Quality Control (FQC): Before equipment is shipped, a final inspection is performed to verify that the finished product meets all specifications and standards. Functional testing may also be conducted to ensure operational efficiency.
What Testing Methods Are Commonly Used in Recycling Equipment Manufacturing?
B2B buyers should understand the common testing methods employed during the QC process. These methods may include:
-
Functional Testing: This assesses whether the equipment operates as intended. For example, shredders may be tested for their ability to process specific materials efficiently.
-
Load Testing: This evaluates the equipment’s performance under maximum load conditions to ensure durability and reliability.
-
Non-Destructive Testing (NDT): Techniques like ultrasonic and magnetic particle testing are used to identify defects without damaging the components.
How Can International B2B Buyers Verify Supplier Quality Control?
International buyers, particularly from regions like Africa, South America, the Middle East, and Europe, must take proactive steps to verify supplier QC practices.
What Are Effective Verification Methods for B2B Buyers?
-
Supplier Audits: Conducting on-site audits allows buyers to evaluate the manufacturing processes and quality control measures firsthand. This can help identify potential issues before purchasing.
-
Quality Reports: Requesting detailed quality assurance reports from suppliers can provide insights into their QC processes, including testing results and compliance with standards.
-
Third-Party Inspections: Engaging third-party inspection services can provide an unbiased assessment of the equipment’s quality and compliance with international standards.
What Nuances Should International B2B Buyers Be Aware Of?
Understanding the nuances of QC and certification processes is vital for international buyers. Different regions may have varying regulatory requirements. For instance, equipment sold in Europe must comply with CE standards, while products exported to other regions may need to meet local regulations.
Buyers should also be aware of potential language barriers and cultural differences that may affect communication with suppliers. Establishing clear expectations regarding quality standards and certifications at the outset can help mitigate misunderstandings.
By focusing on these manufacturing processes and quality assurance practices, B2B buyers can make informed decisions when sourcing recycling equipment, ensuring they receive products that meet their operational needs and industry standards.
Practical Sourcing Guide: A Step-by-Step Checklist for ‘recycling equipment for sale’
In the evolving landscape of waste management, sourcing recycling equipment effectively is crucial for businesses aiming to enhance their sustainability efforts. This guide provides a step-by-step checklist tailored for international B2B buyers, especially those from Africa, South America, the Middle East, and Europe, looking to procure recycling equipment.
Step 1: Define Your Technical Specifications
Before initiating the procurement process, clearly outline the technical specifications of the recycling equipment you need. This includes understanding the types of materials you will process, the expected volume, and the technology required for efficient operation.
– Key considerations:
– What types of recyclable materials will you handle? (e.g., plastics, metals, e-waste)
– What is your processing capacity requirement (tonnage per hour)?
Step 2: Research Market Trends and Innovations
Stay informed about the latest trends and technological advancements in recycling equipment. This knowledge will help you make informed decisions and choose equipment that meets current industry standards.
– Research sources:
– Industry reports and publications.
– Online forums and trade shows focused on waste management and recycling technologies.
Step 3: Identify and Verify Potential Suppliers
It’s essential to compile a list of potential suppliers who specialize in recycling equipment. Vet these suppliers thoroughly to ensure they meet your requirements.
– Verification steps:
– Check for certifications such as ISO standards or other relevant industry accreditations.
– Request references from previous clients to assess their reliability and service quality.
Step 4: Evaluate Supplier Capabilities and Experience
Assess the capabilities and experience of the shortlisted suppliers. This includes their manufacturing processes, technological expertise, and previous projects.
– Considerations:
– How long has the supplier been in the recycling equipment industry?
– Do they have experience with businesses similar to yours in terms of size and sector?
Step 5: Request Quotes and Compare Offerings
Once you have a shortlist of potential suppliers, request detailed quotations that include pricing, delivery timelines, and warranty terms. Comparing these quotes will help you understand the market rates and value propositions.
– What to look for:
– Are there any hidden costs associated with installation or maintenance?
– What are the payment terms, and do they offer financing options?
Step 6: Assess After-Sales Support and Maintenance Services
After-sales support is crucial for the long-term operation of your recycling equipment. Evaluate the level of service the supplier offers post-purchase.
– Key questions:
– What are the maintenance schedules, and how quickly can they respond to service requests?
– Do they provide training for your staff on equipment operation and safety?
Step 7: Finalize the Contract and Terms of Purchase
Once you have selected a supplier, ensure that all terms and conditions are clearly outlined in a formal contract. This should cover delivery schedules, payment terms, and warranties.
– Important elements:
– Ensure there are clauses for penalties in case of delays or substandard equipment delivery.
– Confirm the warranty period and the process for addressing defects.
By following these steps, B2B buyers can effectively navigate the procurement process for recycling equipment, ensuring they select the right partner to support their sustainability goals.
Comprehensive Cost and Pricing Analysis for recycling equipment for sale Sourcing
What Are the Key Cost Components in Recycling Equipment Pricing?
When considering the purchase of recycling equipment, it is essential to understand the various cost components that contribute to the overall pricing structure. The main components include:
-
Materials: The quality and type of materials used in manufacturing recycling equipment directly influence the cost. Higher-grade materials typically result in better durability and performance, but they also increase the initial purchase price.
-
Labor: Labor costs can vary significantly depending on the region and the complexity of the manufacturing process. In regions with higher labor costs, such as parts of Europe, the overall equipment price may reflect this.
-
Manufacturing Overhead: This includes costs related to factory operations, utilities, and administrative expenses. Efficient manufacturing practices can help keep these costs down, ultimately affecting the price of the equipment.
-
Tooling: The initial investment in tooling for specialized equipment can be substantial. Customization often requires unique tooling, which can further increase costs.
-
Quality Control (QC): Rigorous QC processes ensure that the equipment meets safety and performance standards. The costs associated with QC are often factored into the final price.
-
Logistics: Transportation and shipping costs are significant, especially for international buyers. These costs can vary based on distance, shipping method, and any tariffs or taxes imposed.
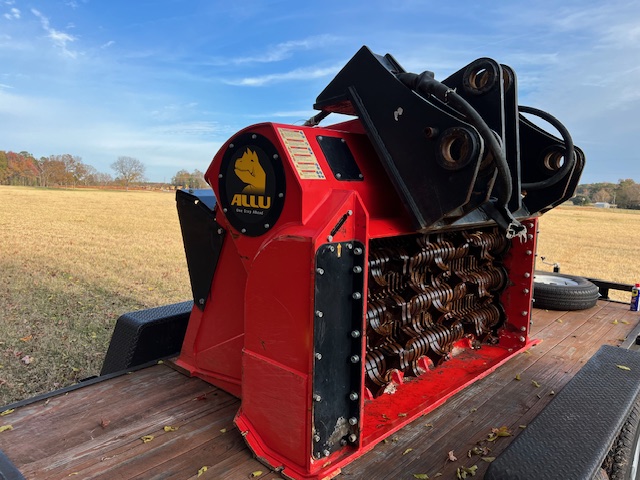
A stock image related to recycling equipment for sale.
- Margin: Suppliers typically add a profit margin to cover their costs and ensure profitability. This margin can vary widely based on market conditions and competition.
How Do Price Influencers Affect Recycling Equipment Sourcing?
Several factors can influence the pricing of recycling equipment, making it crucial for buyers to understand these variables:
-
Volume/MOQ (Minimum Order Quantity): Purchasing in larger quantities often results in discounted pricing. Suppliers are more willing to negotiate when they receive larger orders.
-
Specifications and Customization: Customizing equipment to meet specific operational needs can significantly increase costs. Buyers should weigh the benefits of customization against the added expense.
-
Materials and Quality Certifications: Equipment made from premium materials and possessing quality certifications (like ISO standards) typically comes at a higher price but offers better long-term reliability.
-
Supplier Factors: The reputation and reliability of the supplier play a crucial role in pricing. Established suppliers may charge more due to their proven track record and customer service.
-
Incoterms: Understanding the shipping terms outlined in Incoterms can affect the total cost. Terms like FOB (Free on Board) or CIF (Cost, Insurance, and Freight) can lead to different pricing scenarios depending on the buyer’s location.
What Are the Best Buyer Tips for Negotiating Recycling Equipment Prices?
International B2B buyers, particularly from regions such as Africa, South America, the Middle East, and Europe, should consider the following strategies to enhance cost-efficiency:
-
Negotiate Wisely: Leverage your purchasing power, especially if ordering in bulk. Don’t hesitate to request discounts or improved payment terms.
-
Evaluate Total Cost of Ownership (TCO): Look beyond the initial purchase price. Consider maintenance, operational efficiency, and potential resale value to assess the true cost of ownership.
-
Understand Pricing Nuances: Be aware of how currency fluctuations and regional economic conditions can impact pricing. For instance, a favorable exchange rate can make sourcing equipment from Europe more cost-effective for South American buyers.
-
Conduct Market Research: Compare quotes from multiple suppliers and analyze their offerings. This helps identify the best value for your specific needs.
Disclaimer for Indicative Prices
Prices for recycling equipment can vary significantly based on the factors mentioned above. The provided insights are intended for guidance only, and buyers should conduct thorough research and negotiations to obtain the most accurate and competitive pricing.
Alternatives Analysis: Comparing recycling equipment for sale With Other Solutions
When considering recycling equipment for sale, it is crucial for international B2B buyers to evaluate various alternatives that can achieve similar waste management goals. This analysis will compare traditional recycling equipment with two notable alternatives: waste-to-energy (WtE) systems and composting technologies. Each option has unique benefits and challenges that can impact a buyer’s decision based on their operational needs, budget, and sustainability goals.
Comparison Aspect | Recycling Equipment For Sale | Waste-to-Energy Systems | Composting Technologies |
---|---|---|---|
Performance | High efficiency in separating and processing recyclable materials. | Converts waste into energy, reducing landfill use significantly. | Effective for organic waste, producing valuable compost. |
Cost | Initial investment can be high; ongoing operational costs vary. | High initial setup cost, but potential for energy revenue. | Low cost for setup; ongoing material cost savings. |
Ease of Implementation | Requires training and setup time; integration with existing systems needed. | Complex installation; regulatory hurdles may exist. | Relatively easy to implement with proper training. |
Maintenance | Regular maintenance required; parts may need frequent replacement. | Moderate maintenance; requires specialized knowledge. | Minimal maintenance; requires regular monitoring of conditions. |
Best Use Case | Best for facilities generating significant recyclables. | Ideal for regions with high waste generation and energy needs. | Best for organic waste management in agricultural settings. |
What are the Advantages and Disadvantages of Waste-to-Energy Systems?
Waste-to-energy (WtE) systems convert non-recyclable waste materials into usable forms of energy, such as electricity or heat. The primary advantage of WtE systems is their ability to reduce the volume of waste sent to landfills while simultaneously generating energy, making them particularly suitable for areas with high waste generation. However, the initial investment for WtE technology can be substantial, and the regulatory landscape may pose challenges for implementation. Furthermore, environmental concerns regarding emissions and the quality of energy produced can deter some buyers.
How Do Composting Technologies Compare for Organic Waste?
Composting technologies focus on the biological decomposition of organic waste to produce nutrient-rich compost. One of the key advantages of composting is its low operational cost and minimal environmental impact. It is particularly beneficial for agricultural businesses looking to recycle organic matter into useful soil amendments. However, composting is best suited for organic waste only and may not be effective for other waste types. Additionally, buyers must consider the space and time required for proper composting, as it is a slower process compared to mechanical recycling methods.
Conclusion: How Should B2B Buyers Choose the Right Recycling Solution?
When selecting between recycling equipment for sale and its alternatives, B2B buyers must assess their specific operational needs, budget constraints, and sustainability goals. Companies focused on processing a diverse range of recyclable materials may find traditional recycling equipment to be the best fit. On the other hand, organizations dealing with substantial organic waste might benefit more from composting technologies, while those in energy-intensive regions could consider waste-to-energy systems. Ultimately, a thorough analysis of each option’s performance, cost-effectiveness, and operational requirements will guide buyers in making informed decisions that align with their waste management strategies.
Essential Technical Properties and Trade Terminology for recycling equipment for sale
What Are the Key Technical Properties of Recycling Equipment for Sale?
Understanding the technical properties of recycling equipment is crucial for international B2B buyers. Here are some essential specifications:
1. Material Grade
Material grade refers to the quality and type of materials used in the construction of the recycling equipment. Equipment made from high-grade materials, such as stainless steel or heavy-duty polymers, ensures durability and longevity. For buyers in regions like Africa and South America, where equipment may face harsher operating conditions, selecting high-grade materials can significantly reduce maintenance costs and downtime.
2. Capacity and Throughput
Capacity indicates the amount of waste the equipment can process within a specific timeframe, often measured in tons per hour. Throughput is the actual quantity of material processed after accounting for downtime and inefficiencies. Understanding these metrics is critical for buyers to ensure the equipment meets their operational demands, especially in regions with high waste generation like urban centers in Europe.
3. Tolerance Levels
Tolerance levels specify the allowable variations in dimensions and performance of the equipment. High tolerance levels imply precision in operation, which can lead to more efficient recycling processes. For B2B buyers, especially those in manufacturing sectors, understanding tolerance levels is vital to ensure compatibility with existing systems and to maintain product quality.
4. Energy Efficiency Ratings
Energy efficiency ratings indicate how much energy the equipment consumes relative to its output. Higher energy efficiency translates to lower operational costs and a reduced carbon footprint, aligning with global sustainability goals. Buyers from the Middle East, where energy costs can be significant, should prioritize equipment with favorable energy ratings to optimize their investments.
5. Safety Features
Safety features encompass mechanisms designed to protect operators and the environment during the recycling process. These can include emergency shut-off systems, guards, and sensors. For international buyers, understanding safety standards specific to their country can help in compliance with regulations and in safeguarding personnel.
What Are Common Trade Terms Used in Recycling Equipment Transactions?
Familiarity with industry terminology is essential for effective negotiation and procurement processes. Below are some commonly used terms:
1. OEM (Original Equipment Manufacturer)
OEM refers to companies that produce parts and equipment that may be marketed by another manufacturer. For B2B buyers, sourcing from reputable OEMs can ensure quality and reliability, which is especially important in the recycling industry where equipment performance directly impacts operational efficiency.
2. MOQ (Minimum Order Quantity)
MOQ is the smallest quantity of a product that a supplier is willing to sell. Understanding MOQ is vital for international buyers who may be looking to minimize inventory costs or test new equipment. This term is particularly relevant for buyers in South America, where market fluctuations can impact demand.
3. RFQ (Request for Quotation)
An RFQ is a document that solicits price offers from suppliers for specific products or services. For B2B buyers, issuing an RFQ is a strategic way to compare offers and negotiate better deals, ensuring they get the best value for their investment.
4. Incoterms (International Commercial Terms)
Incoterms are a series of pre-defined commercial terms published by the International Chamber of Commerce (ICC) relating to international commercial law. They clarify the responsibilities of buyers and sellers regarding shipping, insurance, and tariffs. Understanding Incoterms is crucial for international transactions, particularly for buyers in Europe and Africa, as they can significantly affect total landed costs.
5. Lead Time
Lead time refers to the amount of time it takes from placing an order to receiving the equipment. This term is essential for B2B buyers to plan their operations effectively, especially in regions where timely waste processing is critical to public health and environmental sustainability.
By grasping these technical properties and trade terminologies, international B2B buyers can make informed decisions when acquiring recycling equipment, ultimately enhancing their operational efficiency and sustainability efforts.
Navigating Market Dynamics and Sourcing Trends in the recycling equipment for sale Sector
What Are the Key Market Dynamics and Trends in the Recycling Equipment Sector?
The recycling equipment market is experiencing significant growth, driven by increasing global awareness of environmental issues and stringent regulations aimed at reducing landfill waste. The European Union, for example, has established ambitious targets for waste reduction, which influences equipment demand across Europe and beyond. Additionally, emerging economies in Africa and South America are recognizing the importance of recycling to manage urban waste effectively, prompting investments in advanced recycling technologies.
International B2B buyers should note several key trends shaping the market. Firstly, automation and smart technology are gaining traction, with equipment increasingly integrated with IoT capabilities to enhance operational efficiency and data analytics. This trend is evident in machinery that can monitor performance in real-time, thereby optimizing maintenance schedules and reducing downtime. Furthermore, there is a noticeable shift towards modular and scalable equipment solutions, allowing businesses to adapt their recycling capabilities in response to fluctuating waste streams and market demands.
Sourcing strategies are also evolving. Buyers are increasingly looking for suppliers that offer comprehensive service packages, including installation, maintenance, and training, which can significantly reduce the total cost of ownership. Additionally, partnerships with local suppliers are becoming vital for navigating logistics and regulatory compliance, particularly in regions like Africa and South America, where infrastructure can vary greatly.
How Can Sustainability and Ethical Sourcing Impact B2B Buying Decisions in Recycling Equipment?
Sustainability has become a cornerstone of modern B2B purchasing decisions, particularly in the recycling equipment sector. International buyers are increasingly prioritizing environmentally friendly solutions that minimize their carbon footprint and comply with local and international regulations. This shift is not merely a trend but a necessity, as businesses face pressure from consumers and governments to demonstrate their commitment to sustainable practices.
Ethical sourcing is equally critical. B2B buyers should ensure that their suppliers adhere to transparent supply chain practices, which can include the use of recycled materials in the manufacturing of equipment and responsible labor practices. Certifications such as ISO 14001 (Environmental Management) and ISO 45001 (Occupational Health and Safety) are indicators of a supplier’s commitment to sustainability and ethical practices. By choosing certified suppliers, businesses can reduce their environmental impact and enhance their reputation in the marketplace.
Moreover, the adoption of “green” certifications for recycling equipment can not only improve operational efficiency but also serve as a unique selling proposition in competitive markets. For example, equipment that has been certified as energy-efficient can lead to significant cost savings over its lifespan, making it an attractive investment for B2B buyers looking to balance initial costs with long-term operational savings.
What Is the Historical Context of Recycling Equipment Development?
The evolution of recycling equipment can be traced back to the early 20th century when the first mechanized recycling processes were developed. Initially, the focus was primarily on metal recycling, driven by the economic necessity of resource conservation during and after World War II. As environmental awareness grew in the 1970s and 1980s, particularly with the rise of the environmental movement, the scope of recycling expanded to include paper, plastics, and electronic waste.
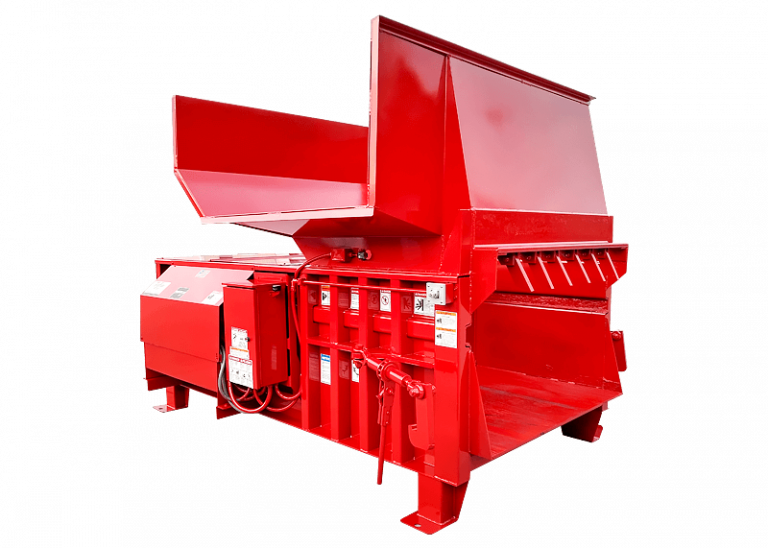
A stock image related to recycling equipment for sale.
Technological advancements have significantly influenced the recycling equipment landscape, leading to the development of more efficient and effective machines capable of handling a diverse array of materials. The introduction of automation and digital technologies in recent years has further transformed the industry, allowing for greater precision and efficiency in recycling operations. This historical context underscores the ongoing innovation within the sector, making it imperative for international B2B buyers to stay informed about the latest developments and trends in recycling equipment.
Frequently Asked Questions (FAQs) for B2B Buyers of recycling equipment for sale
-
How do I choose the right recycling equipment for my business needs?
Choosing the right recycling equipment involves assessing your specific recycling goals, the types of materials you plan to process, and your operational capacity. Start by evaluating the volume of waste generated and the material composition. Research different equipment options, such as balers, shredders, or granulators, that align with your needs. It’s also crucial to consider the equipment’s efficiency, maintenance requirements, and compatibility with existing systems. Consulting with industry experts and suppliers can provide valuable insights tailored to your operational context. -
What are the key factors to consider when vetting suppliers of recycling equipment?
When vetting suppliers, prioritize their industry experience, reputation, and customer reviews. Investigate their manufacturing processes, quality certifications, and after-sales support. Request references from previous clients to gauge reliability and service levels. Ensure they comply with international standards, particularly if you are importing equipment. Additionally, consider their flexibility in meeting your customization requests and their ability to provide spare parts and maintenance services. -
What are the minimum order quantities (MOQ) for recycling equipment purchases?
Minimum order quantities can vary significantly based on the supplier and the type of equipment. Some suppliers may offer flexible MOQs for smaller businesses, while others may require bulk purchases for cost-effectiveness. It’s essential to discuss your specific needs with potential suppliers to negotiate favorable terms. If your order is below the MOQ, consider teaming up with other businesses to meet the requirement or explore suppliers that specialize in small-scale equipment sales. -
What payment terms should I expect when purchasing recycling equipment internationally?
Payment terms can vary by supplier and region, but common options include upfront payments, payment on delivery, or installment plans. For international transactions, consider using secure payment methods like letters of credit or escrow services to mitigate risks. Ensure you clarify the currency, payment schedule, and any additional fees related to shipping or customs. Establishing clear terms in your contract can help prevent misunderstandings and protect your investment.
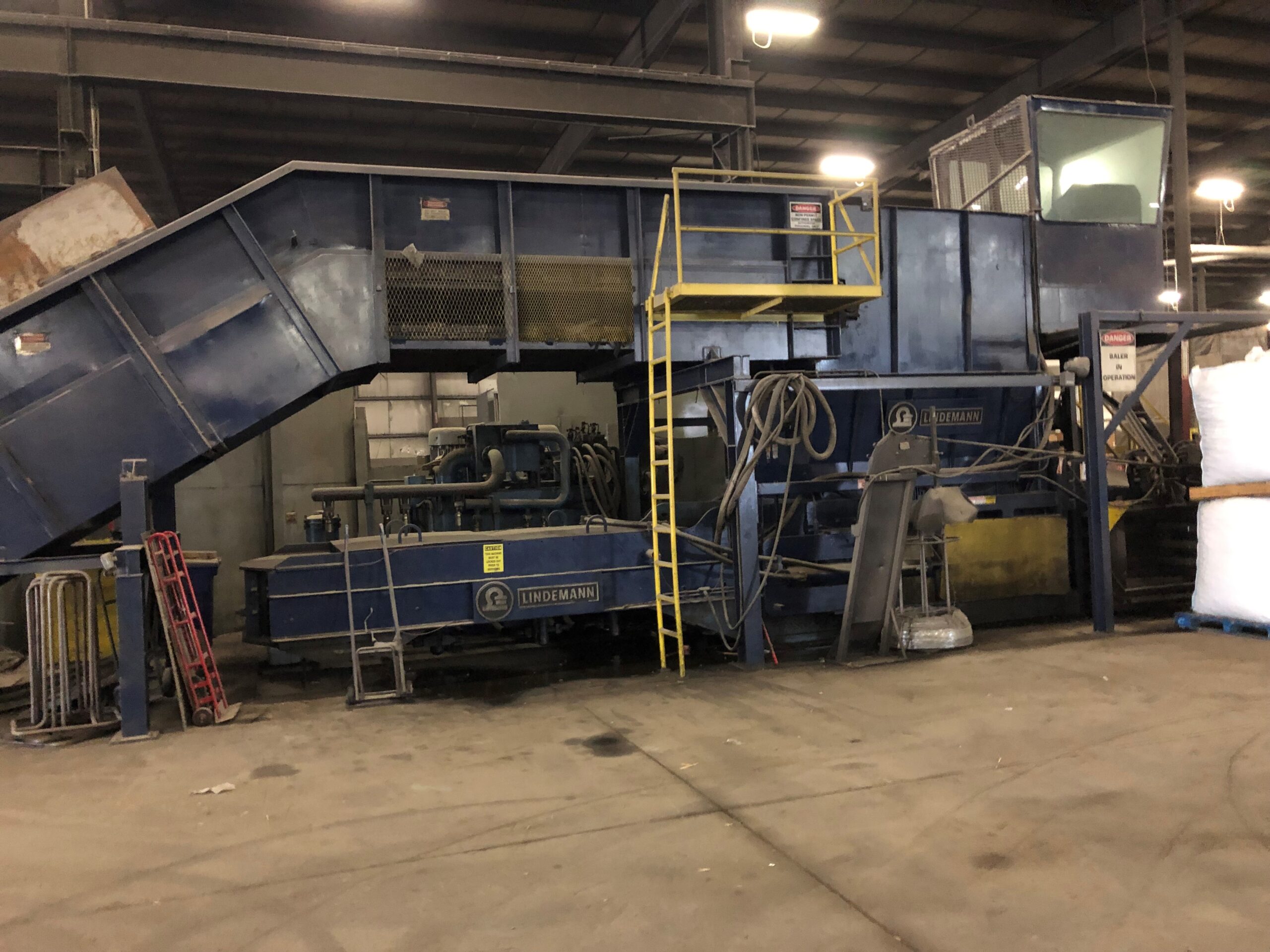
A stock image related to recycling equipment for sale.
-
How can I ensure the quality of recycling equipment before making a purchase?
To ensure quality, request detailed specifications, certifications, and compliance documents from suppliers. It may also be beneficial to visit the manufacturing facility if feasible or to request product samples. Engage third-party inspection services to assess the equipment before shipment, particularly for large purchases. Additionally, inquire about warranties, maintenance support, and the availability of replacement parts, as these factors contribute to long-term equipment reliability. -
What are the logistics considerations for importing recycling equipment?
Logistics for importing recycling equipment include understanding shipping methods, customs regulations, and potential tariffs. Collaborate with freight forwarders experienced in handling industrial equipment to navigate these complexities. Ensure all necessary documentation, including invoices, packing lists, and certificates of origin, is prepared in advance. Factor in lead times for production and shipping, as well as any potential delays at customs, to ensure timely equipment arrival. -
What customization options are available for recycling equipment?
Many suppliers offer customization options to cater to specific processing needs, such as varying sizes, capacities, and additional features like automated controls or specialized shredding capabilities. Discuss your requirements with the supplier to understand what modifications are possible. Customization can enhance efficiency and adaptability, but it may also impact lead times and costs, so it’s crucial to balance your needs with budget constraints. -
How do I assess the return on investment (ROI) for recycling equipment?
To assess ROI, calculate the total cost of ownership, including purchase price, maintenance, and operational costs. Estimate the potential revenue generated from recycled materials and the savings from waste disposal costs. Consider factors such as increased efficiency, reduced labor costs, and environmental benefits, which can also contribute to long-term savings. Performing a break-even analysis can help you determine how long it will take to recoup your investment based on projected performance and savings.
Important Disclaimer & Terms of Use
⚠️ Important Disclaimer
The information provided in this guide, including content regarding manufacturers, technical specifications, and market analysis, is for informational and educational purposes only. It does not constitute professional procurement advice, financial advice, or legal advice.
While we have made every effort to ensure the accuracy and timeliness of the information, we are not responsible for any errors, omissions, or outdated information. Market conditions, company details, and technical standards are subject to change.
B2B buyers must conduct their own independent and thorough due diligence before making any purchasing decisions. This includes contacting suppliers directly, verifying certifications, requesting samples, and seeking professional consultation. The risk of relying on any information in this guide is borne solely by the reader.
Strategic Sourcing Conclusion and Outlook for recycling equipment for sale
The journey toward effective recycling practices is undeniably intertwined with strategic sourcing of recycling equipment. For international B2B buyers in regions like Africa, South America, the Middle East, and Europe, understanding the nuances of sourcing the right machinery is crucial. Key takeaways emphasize the importance of aligning equipment capabilities with local waste management needs and regulatory frameworks. Buyers should prioritize suppliers who not only provide robust machinery but also offer technical support and training, ensuring a smooth integration into existing operations.
How can B2B buyers leverage strategic sourcing for competitive advantage? By investing in high-quality recycling equipment that enhances operational efficiency and reduces waste management costs, businesses can significantly improve their sustainability profiles. This not only meets regulatory demands but also appeals to environmentally conscious consumers.
As we look to the future, the recycling equipment market is poised for innovation, driven by technological advancements and increasing global emphasis on sustainability. International buyers are encouraged to stay informed about emerging trends and collaborate with suppliers that share a commitment to environmental stewardship. The time to act is now; seize the opportunity to enhance your recycling capabilities and contribute to a greener planet.