Discover the Benefits of Using Spider Gag in Your Business (2025)
Introduction: Navigating the Global Market for spider gag
Navigating the complexities of the global market for spider gags can be daunting for international B2B buyers, especially when it comes to sourcing reliable and high-quality products. Understanding the nuances of this unique equipment, often used in various industries, is crucial for making informed purchasing decisions. This guide serves as a comprehensive resource that explores the different types of spider gags, their applications across various sectors, and the best practices for supplier vetting.
International buyers from regions such as Africa, South America, the Middle East, and Europe, including countries like Spain and Nigeria, face distinct challenges in ensuring they procure the right products at competitive prices. By addressing cost considerations, supplier reliability, and product specifications, this guide empowers B2B buyers to navigate these challenges effectively.
In addition to providing insights into the market landscape, we will also discuss the latest trends in spider gag technology and how they can impact operational efficiency. With actionable strategies and expert recommendations, this resource aims to enhance your procurement strategy, ensuring that you not only meet your business needs but also drive value within your organization. Whether you are a seasoned buyer or new to the market, this guide will equip you with the knowledge needed to make strategic, informed decisions.
Understanding spider gag Types and Variations
Type Name | Key Distinguishing Features | Primary B2B Applications | Brief Pros & Cons for Buyers |
---|---|---|---|
Traditional Spider Gag | Standard design with a single mouthpiece and adjustable straps | Veterinary practices, equestrian sports | Pros: Versatile for various horse sizes; Cons: May require frequent adjustments for comfort. |
Double Jointed Spider Gag | Features a double-jointed mouthpiece for increased flexibility | Training and competition in equestrian events | Pros: Reduces tongue pressure; Cons: May be challenging for inexperienced handlers. |
Ported Spider Gag | Incorporates a port in the mouthpiece to alleviate pressure on the tongue | Used in advanced riding and performance disciplines | Pros: Offers better control and comfort; Cons: Higher cost and requires proper fitting. |
Rubberized Spider Gag | Made with a rubber mouthpiece for softer contact | Therapeutic riding and sensitive horses | Pros: Gentle on the horse’s mouth; Cons: Less durable than metal options. |
Adjustable Spider Gag | Allows customization of the gag’s height and pressure | Various equestrian disciplines, particularly for training | Pros: Tailored fit for individual horses; Cons: Complexity in adjustment can confuse some users. |
What are the Characteristics of Traditional Spider Gags?
Traditional spider gags are characterized by their straightforward design, featuring a single mouthpiece and adjustable straps. These gags are widely used in both veterinary practices and equestrian sports, making them a versatile choice for various horse sizes. Buyers should consider that while traditional spider gags are adaptable, they may require frequent adjustments to ensure the horse’s comfort during use.
How Does a Double Jointed Spider Gag Benefit Equestrians?
Double jointed spider gags feature a unique double-jointed mouthpiece that offers increased flexibility, which can be particularly beneficial during training and competition in equestrian events. This design helps reduce tongue pressure, making it a suitable option for horses that may be sensitive in the mouth. However, buyers should be aware that using this type of gag may pose challenges for inexperienced handlers who are not familiar with its operation.
Why Choose a Ported Spider Gag for Advanced Riding?
Ported spider gags include a port in the mouthpiece, which alleviates pressure on the horse’s tongue, making them ideal for advanced riding and performance disciplines. This design allows for better control and comfort, which can be advantageous during high-stakes competitions. However, buyers should note that ported spider gags come at a higher cost and require precise fitting to ensure effectiveness and comfort for the horse.
What Advantages Do Rubberized Spider Gags Offer?
Rubberized spider gags are crafted with a soft rubber mouthpiece, providing a gentler contact for horses, which is particularly useful in therapeutic riding settings or for sensitive horses. While they offer a kinder approach, buyers should consider that rubberized gags may be less durable compared to their metal counterparts, potentially leading to more frequent replacements.
How Can Adjustable Spider Gags Enhance Training?
Adjustable spider gags allow for customization of the gag’s height and pressure, making them suitable for various equestrian disciplines, particularly during training. This tailored fit can significantly enhance the horse’s performance and comfort. However, the complexity involved in adjusting these gags can sometimes confuse users, so buyers should ensure they are well-informed about the adjustment mechanisms for optimal use.
Related Video: The Genius Behind Bach’s Goldberg Variations: CANONS
Key Industrial Applications of spider gag
Industry/Sector | Specific Application of spider gag | Value/Benefit for the Business | Key Sourcing Considerations for this Application |
---|---|---|---|
Oil & Gas | Wellhead control during drilling operations | Enhances safety and efficiency in drilling | Compliance with international safety standards; durability in extreme conditions |
Construction | Temporary support during concrete curing | Reduces risk of structural failure | Material strength and load-bearing capacity; regional availability |
Mining | Load stabilization for heavy machinery | Increases operational efficiency and safety | Compatibility with existing equipment; sourcing from reliable manufacturers |
Marine | Tension control for mooring systems | Improves vessel stability and safety at port | Corrosion resistance; compliance with maritime regulations |
Industrial Equipment | Lifting and rigging applications | Enhances operational safety and productivity | Weight specifications; certification for lifting equipment |
How is ‘spider gag’ Used in the Oil & Gas Sector?
In the oil and gas industry, spider gags are essential for wellhead control during drilling operations. They provide a secure grip on various components, ensuring stability and safety while drilling deep into the earth. This application significantly reduces the risk of accidents and enhances operational efficiency. For international buyers, especially in regions like Africa and the Middle East, sourcing spider gags requires a focus on compliance with international safety standards, as well as durability to withstand extreme conditions often encountered in drilling environments.
What Role Does ‘spider gag’ Play in Construction?
In construction, spider gags are utilized as temporary supports during concrete curing processes. They help stabilize forms and prevent structural failure, which can lead to costly delays and safety hazards. By ensuring that the concrete sets properly, businesses can maintain project timelines and budgets. Buyers in Europe and South America should prioritize sourcing spider gags that meet material strength specifications and are readily available in their regions to avoid project disruptions.
How is ‘spider gag’ Applied in Mining Operations?
Spider gags find significant applications in the mining sector, particularly for load stabilization of heavy machinery. They ensure that equipment remains secure during operation, which is crucial for maintaining efficiency and safety in harsh mining environments. For international buyers, it is vital to consider compatibility with existing equipment and to source from reliable manufacturers that can guarantee the quality and durability of the spider gags used in mining operations.
Why is ‘spider gag’ Important for Marine Applications?
In marine applications, spider gags are used for tension control in mooring systems. They play a critical role in enhancing vessel stability and safety while docked or in transit. This application is particularly important for companies operating in busy ports in Africa and Europe, where the risk of accidents can be high. Buyers should ensure that the spider gags are corrosion-resistant and compliant with maritime regulations to ensure longevity and reliability in marine environments.
How Does ‘spider gag’ Enhance Industrial Equipment Operations?
Spider gags are also crucial in various lifting and rigging applications across industrial sectors. They enhance operational safety and productivity by securely holding loads during lifting operations. For B2B buyers, particularly in South America, it is essential to verify weight specifications and ensure that the spider gags are certified for lifting equipment to meet safety regulations and operational standards.
Related Video: Uses and Gratifications Theory – UGT
3 Common User Pain Points for ‘spider gag’ & Their Solutions
Scenario 1: Difficulty in Sourcing Quality Spider Gags for Industrial Applications
The Problem: B2B buyers, particularly in manufacturing and construction sectors, often struggle to find suppliers who provide high-quality spider gags that meet safety and durability standards. This can lead to project delays and increased costs due to the need for frequent replacements or failures during critical operations. Buyers may also face challenges in verifying the credibility of suppliers, especially when sourcing from international markets in regions like Africa and South America, where quality assurance practices may vary significantly.
The Solution: To overcome sourcing difficulties, B2B buyers should prioritize establishing relationships with reputable suppliers who specialize in spider gags. Conduct thorough research by checking supplier certifications and customer reviews. Utilizing platforms like Alibaba or industry-specific trade shows can be beneficial for identifying trusted manufacturers. Additionally, consider requesting samples before making bulk purchases to assess the product quality firsthand. Engaging in direct communication with suppliers regarding their manufacturing processes and quality control measures can also provide insights into their reliability.
Scenario 2: Inadequate Understanding of Spider Gag Specifications and Applications
The Problem: Many B2B buyers lack a comprehensive understanding of the specifications and appropriate applications for spider gags, leading to the procurement of unsuitable products. This knowledge gap can result in using spider gags that do not meet the specific requirements of their operations, potentially leading to safety hazards and operational inefficiencies. For instance, a construction company in Spain may mistakenly order a spider gag intended for light-duty applications for a heavy-load scenario, compromising worker safety.
The Solution: Buyers should invest time in educating themselves about the various types of spider gags and their specifications, such as load capacity, material composition, and design features. Engaging with industry experts through webinars, workshops, or training sessions can provide valuable insights into the correct usage of spider gags. Additionally, creating a checklist of project requirements before purchasing can help ensure that the selected spider gag aligns with operational needs. Collaborating with engineers or safety consultants can further enhance the decision-making process by ensuring that the chosen products meet both safety and performance standards.
Scenario 3: Challenges in Maintenance and Proper Use of Spider Gags
The Problem: Once acquired, many B2B buyers face challenges in the maintenance and proper use of spider gags, which can lead to premature wear and failure. A lack of training on how to properly install, use, and maintain spider gags can result in accidents and costly downtime. For example, a company in Nigeria might experience significant project delays because their team misused spider gags, leading to equipment damage and worker injuries.
The Solution: To mitigate these challenges, companies should implement comprehensive training programs focused on the proper use and maintenance of spider gags. This training should cover installation techniques, regular inspection protocols, and best practices for maintenance. Providing easy-to-follow manuals and visual aids can enhance the learning experience for employees. Additionally, establishing a routine maintenance schedule can help extend the lifespan of spider gags and ensure safe operations. Companies may also consider partnering with suppliers who offer training and support services to reinforce best practices in the workplace.
Strategic Material Selection Guide for spider gag
When selecting materials for spider gags, it is essential to consider various factors that influence performance, durability, and compatibility with specific applications. Below, we analyze four common materials used in the manufacture of spider gags, focusing on their properties, advantages, disadvantages, and considerations for international buyers.
What are the Key Properties of Stainless Steel for Spider Gags?
Stainless Steel is a popular choice for spider gags due to its excellent strength and corrosion resistance. It typically has a temperature rating of up to 800°F (427°C) and can withstand high pressures, making it suitable for demanding environments. The most common grades used include 304 and 316, with 316 offering superior corrosion resistance, especially in saline or acidic environments.
Pros: Stainless steel is durable and has a long lifespan, making it a cost-effective option in the long run. It is also easy to clean and maintain, which is crucial in industries requiring hygiene.
Cons: The initial cost of stainless steel can be high, and it may require specialized manufacturing processes, which can increase lead times.
Impact on Application: Stainless steel spider gags are ideal for applications involving water, oils, and chemicals, but they may not be suitable for environments with extreme pH levels.
Considerations for International Buyers: Compliance with ASTM standards is essential for buyers in Europe and the Middle East. Buyers should also consider local regulations regarding corrosion resistance, especially in coastal regions.
How Does Aluminum Compare as a Material for Spider Gags?
Aluminum is another material option for spider gags, known for its lightweight properties and resistance to corrosion. It typically has a temperature rating of around 400°F (204°C) and is less effective under high-pressure conditions compared to stainless steel.
Pros: The lightweight nature of aluminum makes it easier to handle and install, which can reduce labor costs. It is also more affordable than stainless steel.
Cons: While aluminum is corrosion-resistant, it is not as durable as stainless steel, particularly in high-stress applications. It may also deform under high pressure.
Impact on Application: Aluminum spider gags are suitable for less demanding environments, such as those involving air or low-pressure fluids.
Considerations for International Buyers: Buyers should ensure that aluminum used meets local standards, such as DIN or JIS, particularly in the automotive and aerospace industries where weight is a critical factor.
Why Choose Plastic for Spider Gags?
Plastic, particularly high-density polyethylene (HDPE) or polypropylene, is used in specific applications where chemical resistance and lightweight properties are paramount. These materials can withstand temperatures up to 180°F (82°C) and are generally not suitable for high-pressure applications.
Pros: Plastic spider gags are highly resistant to a wide range of chemicals, making them ideal for corrosive environments. They are also very lightweight and cost-effective.
Cons: The main drawback is their limited temperature and pressure ratings, which restricts their use in demanding applications. They may also be less durable than metal options.
Impact on Application: Plastic spider gags are best suited for chemical processing, wastewater treatment, and other environments where metal corrosion is a concern.
Considerations for International Buyers: Compliance with environmental regulations is crucial, especially in regions with strict plastic waste management policies. Buyers should also check for certifications regarding chemical resistance.
What are the Benefits of Using Carbon Steel in Spider Gags?
Carbon Steel is a cost-effective option for spider gags, particularly in applications requiring strength and durability. It typically has a temperature rating of up to 500°F (260°C) and can handle high pressures effectively.
Pros: Carbon steel is strong and relatively inexpensive, making it a popular choice for many industrial applications.
Cons: Its susceptibility to corrosion means that it often requires protective coatings or galvanization, which can add to the overall cost and manufacturing complexity.
Impact on Application: Carbon steel spider gags are suitable for applications where exposure to moisture is limited or where protective coatings can be effectively applied.
Considerations for International Buyers: It is essential to ensure that carbon steel products comply with local standards and regulations, particularly in regions with high humidity or corrosive environments.
Summary Table of Material Selection for Spider Gags
Material | Typical Use Case for spider gag | Key Advantage | Key Disadvantage/Limitation | Relative Cost (Low/Med/High) |
---|---|---|---|---|
Stainless Steel | High-pressure applications, chemical processing | Excellent durability and corrosion resistance | Higher initial cost and manufacturing complexity | High |
Aluminum | Low-pressure applications, lightweight needs | Lightweight and cost-effective | Limited durability under high stress | Medium |
Plastic | Chemical processing, wastewater treatment | Highly resistant to chemicals | Limited temperature and pressure ratings | Low |
Carbon Steel | General industrial applications | Cost-effective and strong | Susceptible to corrosion without coatings | Medium |
This analysis provides international B2B buyers with actionable insights into material selection for spider gags, ensuring they make informed decisions based on their specific application needs and regional compliance requirements.
In-depth Look: Manufacturing Processes and Quality Assurance for spider gag
What Are the Main Stages of Manufacturing Spider Gags?
The manufacturing process for spider gags involves several critical stages to ensure quality and functionality. Understanding these stages can help international B2B buyers make informed decisions when sourcing these products.
Material Preparation: What Materials Are Used for Spider Gags?
The first step in the manufacturing process is material selection. Spider gags are typically made from high-strength stainless steel or aluminum alloys, which offer durability and corrosion resistance. The choice of material impacts the performance and longevity of the product, especially in harsh environments commonly found in industries like oil and gas, agriculture, and construction.
Once the material is selected, it undergoes preparation, which may include cutting, machining, and surface treatment to enhance durability. This stage is crucial as it sets the foundation for the subsequent manufacturing processes.
How Are Spider Gags Formed?
Following material preparation, the forming process takes place. This can involve techniques such as:
- Stamping: High-pressure machines shape the raw materials into the desired form. This method is efficient for mass production.
- Casting: Molten metal is poured into molds to create complex shapes. This is beneficial for producing intricate designs that may be difficult to achieve through stamping.
- Forging: Materials are heated and then shaped under high pressure. This process increases the strength of the material and is particularly useful for high-stress applications.
Each of these methods has its advantages, and the choice depends on the specific design requirements and production volume.
What Is Involved in the Assembly of Spider Gags?
After forming, the next stage is assembly. This involves combining various components, such as the gag body, hinges, and locking mechanisms. Assembly can be done manually or through automated processes, depending on the production scale.
Quality control during assembly is essential. Each component must fit precisely to ensure the spider gag operates correctly. Misalignment can lead to operational failures, making this stage critical for maintaining product integrity.
How Is the Finishing of Spider Gags Conducted?
The finishing process enhances the aesthetic and functional properties of the spider gags. This may include:
- Polishing: To achieve a smooth surface finish that reduces friction and improves appearance.
- Coating: Applying protective coatings to prevent corrosion and wear, especially for products used in outdoor or industrial settings.
- Inspection: Final inspections are conducted to ensure that each product meets the required specifications and standards.
What Quality Assurance Standards Should B2B Buyers Consider?
Quality assurance is a vital aspect of the manufacturing process for spider gags. International buyers should be aware of relevant standards that ensure product reliability and safety.
Which International Standards Are Applicable?
ISO 9001 is one of the most recognized quality management standards globally. It ensures that manufacturers adhere to consistent quality practices throughout their production processes. Additionally, industry-specific certifications such as CE marking (for products sold within the European Economic Area) and API standards (for oil and gas equipment) are crucial.
These certifications indicate that the products meet rigorous safety and performance criteria, making them essential for buyers looking for high-quality spider gags.
What Are the Key Quality Control Checkpoints?
Quality control in the manufacturing of spider gags typically involves several checkpoints:
- Incoming Quality Control (IQC): Inspection of raw materials before production begins. Ensuring materials meet specified standards is critical for product quality.
- In-Process Quality Control (IPQC): Continuous monitoring during the manufacturing process. This includes checks at each stage of production to identify any defects early.
- Final Quality Control (FQC): A thorough inspection of the finished products before they are shipped. This stage ensures that all products comply with design specifications and quality standards.
How Can B2B Buyers Verify Supplier Quality Control?
Verifying a supplier’s quality control processes is essential for international B2B buyers. Here are some actionable steps to consider:
What Audit Processes Should Buyers Implement?
Conducting supplier audits can provide insights into their manufacturing processes and quality control practices. Buyers should request documentation of quality procedures, certifications, and previous audit reports. An on-site audit can also be beneficial, allowing buyers to assess the manufacturing environment and practices firsthand.
How to Review Quality Control Reports?
Buyers should ask for regular quality control reports from suppliers. These reports should detail inspection results, defect rates, and corrective actions taken. A supplier that is transparent about their quality metrics is more likely to maintain high standards.
Should Buyers Consider Third-Party Inspections?
Engaging third-party inspection services can provide an unbiased assessment of product quality. These inspectors can conduct random checks at various stages of the manufacturing process, ensuring that the products meet specified requirements. This is particularly important for buyers from regions like Africa and South America, where local regulations may differ from international standards.
What Are the Nuances of Quality Control for International Buyers?
International B2B buyers must navigate various challenges related to quality control. Cultural differences, regulatory requirements, and varying standards can complicate the sourcing process.
How to Navigate Regulatory Challenges?
Buyers should familiarize themselves with the regulatory requirements in their target markets. This may involve understanding local certifications and compliance standards. Engaging with local experts or consultants can help streamline this process.
What Should Buyers Know About Communication with Suppliers?
Effective communication is key to ensuring quality. Buyers should establish clear expectations regarding quality standards, inspection processes, and timelines. Regular updates from suppliers can help mitigate risks associated with quality issues.
By understanding the manufacturing processes and quality assurance practices for spider gags, international B2B buyers can make informed decisions that enhance their procurement strategies. This knowledge is essential for ensuring product reliability and achieving long-term business success.
Practical Sourcing Guide: A Step-by-Step Checklist for ‘spider gag’
In the competitive landscape of international B2B procurement, sourcing a reliable and high-quality spider gag requires a structured approach. This checklist serves as a practical guide for buyers from diverse regions such as Africa, South America, the Middle East, and Europe. By following these steps, you can ensure a successful sourcing experience.
Step 1: Define Your Technical Specifications
Clearly outline the technical requirements of the spider gag you need. This includes dimensions, material specifications, and load capacity. A well-defined specification helps suppliers understand your needs, reducing the chances of miscommunication and ensuring that the products meet your operational standards.
Step 2: Research Potential Suppliers
Conduct thorough research to identify potential suppliers. Utilize online directories, trade shows, and industry forums to gather a list of manufacturers and distributors. Look for companies with a proven track record in producing spider gags, particularly those that cater to your region’s specific standards and regulations.
Step 3: Evaluate Supplier Certifications
Ensure that the suppliers you consider hold relevant certifications and adhere to international quality standards. Certifications such as ISO 9001 or specific industry-related certifications indicate a commitment to quality and safety. This step is crucial for mitigating risks associated with product quality and compliance.
Step 4: Request Samples for Evaluation
Before making a bulk purchase, request samples of the spider gags to evaluate their quality firsthand. Inspect the samples for craftsmanship, material integrity, and functionality. This practical evaluation allows you to verify that the products align with your specifications and operational requirements.
Step 5: Compare Pricing and Payment Terms
Gather detailed quotations from multiple suppliers and compare their pricing structures. Look beyond the base price; consider shipping costs, payment terms, and any potential hidden fees. Understanding the total cost of ownership will help you make a more informed decision and maintain budget control.
Step 6: Check References and Reviews
Reach out to previous clients or request case studies from the suppliers you’re considering. Customer feedback can provide insights into the supplier’s reliability, product performance, and service quality. This step is vital for establishing trust and confidence in your chosen supplier.
Step 7: Establish Clear Communication Channels
Set up effective communication channels with your chosen supplier to facilitate ongoing dialogue. Discuss timelines, delivery schedules, and any potential issues that may arise during the procurement process. Clear communication is essential for ensuring that both parties are aligned and can quickly address any concerns.
By adhering to this structured sourcing checklist, B2B buyers can effectively navigate the complexities of procuring spider gags, ensuring that they partner with reliable suppliers who meet their specific needs. This proactive approach not only enhances procurement efficiency but also fosters long-term business relationships.
Comprehensive Cost and Pricing Analysis for spider gag Sourcing
What are the Key Cost Components in Spider Gag Manufacturing?
When sourcing spider gags, international B2B buyers should consider several critical cost components that contribute to the overall pricing structure. The primary factors include:
-
Materials: The type and quality of materials used in the production of spider gags significantly impact costs. High-grade stainless steel or specialized alloys can increase material costs but may offer better durability and performance.
-
Labor: Labor costs vary by region and can be influenced by the skill level required for manufacturing. For instance, countries with lower wage standards may offer cost advantages, but buyers should consider the trade-off in terms of quality and craftsmanship.
-
Manufacturing Overhead: This includes utilities, rent, and equipment maintenance that contribute to the cost of production. Understanding the local economic conditions can help buyers gauge the overhead costs associated with their suppliers.
-
Tooling: The initial investment in tooling and molds can be significant, especially for custom designs. Buyers should inquire about tooling costs and whether they will be amortized over large orders.
-
Quality Control (QC): Implementing stringent quality control processes adds to the cost but is essential for ensuring product reliability. Buyers should seek suppliers who maintain high QC standards, as this can prevent future costs related to returns or replacements.
-
Logistics: Transportation and shipping costs can fluctuate based on the delivery location and chosen Incoterms. Understanding the logistics involved in sourcing spider gags is crucial for accurately estimating total costs.
-
Margin: Suppliers will include a profit margin in their pricing. It is vital for buyers to understand the typical margins in their industry to negotiate effectively.
How Do Price Influencers Affect Spider Gag Sourcing?
Several factors influence the pricing of spider gags, and understanding these can help buyers negotiate better deals:
-
Volume and Minimum Order Quantity (MOQ): Larger orders often lead to reduced unit costs due to economies of scale. Buyers should assess their needs and aim for larger purchases if feasible.
-
Specifications and Customization: Custom designs or specific certifications can increase costs. Buyers should clearly define their requirements to avoid unexpected pricing changes.
-
Materials and Quality Certifications: The grade of materials and any relevant certifications (e.g., ISO, CE) can affect pricing. Buyers should weigh the importance of quality against cost, especially in regions where safety standards are critical.
-
Supplier Factors: The supplier’s reputation, reliability, and location can influence pricing. Established suppliers may charge more but offer better service and quality assurance.
-
Incoterms: Understanding shipping terms is essential. Different Incoterms can affect the total landed cost, so buyers should choose terms that minimize risk and maximize cost efficiency.
What Are the Best Negotiation Tips for International B2B Buyers?
When negotiating prices for spider gags, buyers should consider the following strategies to achieve cost efficiency:
-
Research and Benchmarking: Conduct thorough market research to understand prevailing prices and identify potential suppliers. Knowledge of competitor pricing can bolster negotiation positions.
-
Build Relationships: Establishing a rapport with suppliers can lead to better terms and pricing. Long-term relationships often yield greater flexibility and potential discounts.
-
Total Cost of Ownership (TCO): Evaluate the TCO rather than just the initial purchase price. Consider factors like maintenance, longevity, and potential warranty claims to make informed decisions.
-
Be Transparent: Sharing purchasing intentions and forecasts can help suppliers plan better and potentially lead to lower costs for buyers.
-
Understand Cultural Nuances: Different regions may have varying negotiation styles. Being culturally aware can enhance communication and strengthen business relationships.
Final Thoughts on Sourcing Spider Gags
While the prices for spider gags can vary widely based on several factors, it is crucial for international buyers to engage in thorough research and strategic negotiation. Understanding the cost structure, price influencers, and effective negotiation techniques will empower buyers to make informed decisions and achieve favorable outcomes. Always remember that the prices provided by suppliers are indicative and may fluctuate based on market conditions and specific requirements.
Alternatives Analysis: Comparing spider gag With Other Solutions
When evaluating solutions for specific applications, it’s crucial for international B2B buyers to consider various alternatives that can meet their operational needs. This section will compare the ‘spider gag’ with two viable alternatives, enabling buyers to make informed decisions.
Comparison Aspect | ‘Spider Gag’ | Alternative 1: ‘Bite Block’ | Alternative 2: ‘Traditional Gag’ |
---|---|---|---|
Performance | High stability and control | Moderate stability | Good for basic control |
Cost | Moderate initial investment | Lower upfront costs | Variable, depending on materials |
Ease of Implementation | Requires specialized training | Easy to use | Straightforward installation |
Maintenance | Low maintenance needs | Moderate maintenance | High maintenance over time |
Best Use Case | Ideal for advanced applications | Suitable for basic use | Effective for temporary solutions |
How Does ‘Bite Block’ Compare to Spider Gag?
The ‘Bite Block’ is a device designed to restrict the movement of the jaw without as much complexity as the spider gag. It offers moderate stability, making it a viable option for less demanding applications. One of its significant advantages is its lower upfront costs, which can appeal to buyers with budget constraints. However, the ease of use and implementation makes it accessible for teams without specialized training. On the downside, it may require moderate maintenance over time to ensure its effectiveness, which could lead to additional costs.
What Are the Benefits of Using a Traditional Gag?
Traditional gags are straightforward devices that have been used for many years. They are effective for temporary solutions where immediate control is necessary. The installation process is typically simple, making them suitable for quick applications. However, their performance can be limited compared to more advanced solutions like the spider gag. Maintenance needs are higher, as traditional gags often wear out faster and require replacement or repairs. While they may be cost-effective initially, long-term use can lead to increased expenses.
Conclusion: How to Choose the Right Solution for Your Needs?
When selecting the right solution, B2B buyers should carefully assess their specific operational requirements. Considerations should include the complexity of the application, budget constraints, and the level of training available within the team. If high performance and stability are critical, the spider gag may be the best choice despite its moderate costs. Alternatively, for more straightforward or temporary needs, the bite block or traditional gag could provide adequate solutions at a lower investment. Understanding these alternatives will enable buyers from diverse regions, including Africa, South America, the Middle East, and Europe, to make strategic decisions that align with their operational goals.
Essential Technical Properties and Trade Terminology for spider gag
What Are the Key Technical Properties of Spider Gag?
When procuring spider gags for various applications, understanding the essential technical properties is crucial for making informed decisions. Here are several critical specifications to consider:
-
Material Grade
Spider gags are typically made from stainless steel or high-grade aluminum. The material grade impacts the gag’s strength, durability, and resistance to corrosion. For B2B buyers, selecting the right material ensures longevity and performance under various environmental conditions, particularly in industries such as oil and gas or marine applications. -
Load Capacity
This refers to the maximum weight the spider gag can safely handle. Load capacity is vital for applications where heavy loads are common, such as in construction or heavy machinery. Buyers must assess the load requirements of their specific applications to choose a spider gag that meets safety and operational standards. -
Tolerance Levels
Tolerance indicates the permissible limit of variation in dimensions. In the context of spider gags, precise tolerances are crucial for ensuring compatibility with other equipment and for maintaining safety standards. B2B buyers should prioritize products that meet or exceed industry tolerance specifications to avoid operational failures. -
Size and Configuration
Spider gags come in various sizes and configurations, which can influence their application and effectiveness. Understanding the specific size requirements is essential for compatibility with existing systems. Buyers should consult with manufacturers to determine the best fit for their operational needs. -
Surface Finish
The surface finish can affect the performance and longevity of spider gags. A higher-quality finish can enhance corrosion resistance and reduce friction, leading to better performance in dynamic applications. B2B buyers should consider the environmental conditions where the spider gag will be used when evaluating surface finishes.
What Are Common Trade Terms Associated with Spider Gags?
Understanding industry jargon is essential for effective communication and negotiation in B2B transactions. Here are some common terms related to spider gags:
-
OEM (Original Equipment Manufacturer)
This term refers to companies that produce parts or equipment that may be marketed by another manufacturer. In the context of spider gags, buyers often deal directly with OEMs for custom specifications and bulk orders. Understanding OEMs can help buyers ensure they are getting quality products tailored to their needs. -
MOQ (Minimum Order Quantity)
MOQ represents the smallest number of units a supplier is willing to sell. For B2B buyers, knowing the MOQ is crucial for budgeting and inventory management. It can also impact the overall cost-effectiveness of sourcing spider gags, particularly for smaller businesses. -
RFQ (Request for Quotation)
An RFQ is a document sent to suppliers requesting price and availability information for specific products. In the procurement of spider gags, submitting an RFQ allows buyers to compare pricing, terms, and delivery times from different suppliers, facilitating better decision-making. -
Incoterms (International Commercial Terms)
These are a set of international rules that define the responsibilities of buyers and sellers in international transactions. Understanding Incoterms is essential for B2B buyers to clarify shipping costs, insurance responsibilities, and delivery timelines when importing spider gags from international suppliers. -
Lead Time
Lead time refers to the period between placing an order and receiving the goods. For businesses relying on spider gags for ongoing projects, understanding lead times is crucial for planning and avoiding delays. Buyers should factor in lead times when negotiating with suppliers to ensure timely delivery.
By familiarizing themselves with these technical properties and trade terms, B2B buyers can enhance their procurement strategies, ensuring they select the right products for their specific applications while fostering effective supplier relationships.
Navigating Market Dynamics and Sourcing Trends in the spider gag Sector
What are the Current Market Dynamics and Key Trends in the Spider Gag Sector?
The spider gag market is witnessing significant growth driven by various global factors, including the increasing demand for innovative equestrian products and the rise of animal welfare awareness. International B2B buyers, particularly those from Africa, South America, the Middle East, and Europe, are becoming more discerning, seeking products that not only enhance performance but also prioritize the well-being of the animal. The emergence of digital platforms has revolutionized sourcing trends, enabling buyers to access a broader range of suppliers and compare products efficiently.
In terms of technology, the integration of advanced materials such as synthetic fibers and biocompatible substances is shaping the spider gag landscape. These materials offer improved durability and comfort, appealing to modern buyers. Additionally, the trend towards customization is gaining momentum, with manufacturers providing tailored solutions to meet specific client needs, thereby enhancing customer satisfaction and loyalty.
The market dynamics are also influenced by economic factors, such as fluctuating commodity prices and supply chain disruptions, particularly in the context of global events. Buyers must remain agile, adapting their sourcing strategies to mitigate risks associated with these fluctuations. Developing relationships with local suppliers can also provide a competitive edge, ensuring a more stable supply chain while fostering community engagement.
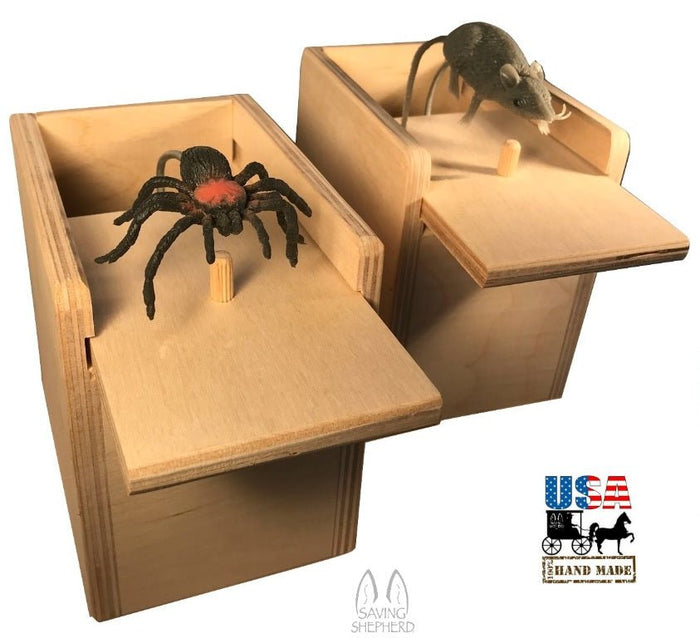
A stock image related to spider gag.
How Can Sustainability and Ethical Sourcing Impact B2B Buyers in the Spider Gag Sector?
Sustainability is becoming a crucial consideration for B2B buyers in the spider gag sector, reflecting a broader shift towards environmentally responsible practices. The environmental impact of production methods and material choices is under scrutiny, with buyers increasingly favoring suppliers who demonstrate a commitment to reducing their carbon footprint. This includes utilizing renewable resources and implementing waste reduction strategies.
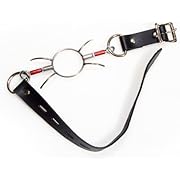
A stock image related to spider gag.
Ethical sourcing is equally important, as consumers and businesses alike prioritize transparency in supply chains. Buyers should seek suppliers that adhere to ethical standards, such as fair labor practices and humane treatment of animals. Certifications such as Global Organic Textile Standard (GOTS) and Fair Trade can serve as indicators of a supplier’s commitment to ethical practices.
Incorporating ‘green’ materials, such as recycled or biodegradable components, can not only enhance the sustainability profile of a product but also resonate with environmentally conscious consumers. This alignment with sustainability and ethical sourcing not only meets regulatory requirements but can also serve as a strong marketing tool, enhancing brand reputation and customer loyalty.
What is the Brief Evolution and History of the Spider Gag?
The spider gag has evolved significantly since its inception, primarily as a tool for horse training and control. Initially designed for specific equestrian disciplines, its usage has expanded to various riding styles, reflecting a growing understanding of horse behavior and welfare.
Over the decades, innovations in design and materials have transformed the spider gag into a more effective and humane option for riders. This evolution is marked by a shift from traditional materials to modern synthetics, which offer enhanced durability and comfort for the horse. As a result, the spider gag has become a staple in the inventory of equestrian suppliers worldwide, appealing to a diverse range of buyers looking for effective, ethical solutions for horse management.
In summary, the spider gag sector is not just about functionality but also about aligning with market trends that prioritize sustainability and ethical practices, offering a compelling proposition for B2B buyers across various regions.
Frequently Asked Questions (FAQs) for B2B Buyers of spider gag
-
How do I choose the right spider gag for my business needs?
When selecting a spider gag, consider the specific requirements of your application, including the type of livestock and the intended use (e.g., training, competition, or veterinary care). Evaluate factors such as material durability, size options, and comfort for the animal. Engaging with suppliers who offer customization options can also ensure you get a product tailored to your needs. Always seek samples or product demonstrations to assess quality before making a bulk purchase. -
What is the best material for a spider gag in livestock management?
The best material for a spider gag typically includes durable and non-toxic options like stainless steel, rubber, or silicone. Stainless steel provides strength and longevity, while rubber and silicone can enhance comfort for the animal. Consider the specific environment in which the gag will be used, as materials need to withstand various conditions without degrading. Always verify that materials comply with local regulations and standards for animal welfare. -
How can I verify the credibility of spider gag suppliers?
To vet suppliers, start by researching their reputation through online reviews and testimonials from other B2B buyers. Request references and check their compliance with international standards, such as ISO certifications. Additionally, consider visiting their manufacturing facilities if possible. Engaging in trade shows or industry conferences can also provide insights into a supplier’s reliability and product quality. -
What are the typical minimum order quantities (MOQs) for spider gags?
Minimum order quantities for spider gags can vary significantly depending on the supplier and customization options. Generally, MOQs can range from 50 to 200 units. It’s essential to discuss your needs directly with suppliers to negotiate terms that fit your purchasing strategy. Some suppliers may offer flexibility for first-time buyers or allow smaller test orders to evaluate product quality. -
What payment terms should I expect when sourcing spider gags internationally?
Payment terms for international transactions can vary widely, but common practices include upfront payments, letters of credit, or payment upon delivery. Discussing terms in advance is crucial to avoid misunderstandings. Additionally, consider using secure payment methods that offer buyer protection, especially for large orders. Ensure that you understand the currency exchange implications and any associated fees. -
How can I ensure quality assurance for spider gags purchased abroad?
To ensure quality assurance, establish clear specifications with your supplier before production begins. Request samples to evaluate the product firsthand. Consider third-party quality inspections to assess the goods before shipment. Additionally, inquire about the supplier’s quality control processes and certifications, which can provide further assurance of their commitment to maintaining high standards. -
What logistics considerations should I keep in mind when importing spider gags?
When importing spider gags, consider shipping methods, customs regulations, and potential tariffs. Choose a logistics partner experienced in handling agricultural equipment to streamline the process. Ensure that all documentation is accurate and complies with both exporting and importing countries’ regulations. Additionally, plan for lead times, as international shipping can introduce delays that may affect your supply chain. -
Are there specific regulations for importing spider gags into African or South American markets?
Yes, importing spider gags into African or South American markets may be subject to specific regulations regarding animal welfare and safety standards. It is crucial to familiarize yourself with local laws and import restrictions. Consulting with a local customs broker can provide valuable insights into necessary documentation and compliance requirements, helping to avoid delays or penalties during the import process.
Important Disclaimer & Terms of Use
⚠️ Important Disclaimer
The information provided in this guide, including content regarding manufacturers, technical specifications, and market analysis, is for informational and educational purposes only. It does not constitute professional procurement advice, financial advice, or legal advice.
While we have made every effort to ensure the accuracy and timeliness of the information, we are not responsible for any errors, omissions, or outdated information. Market conditions, company details, and technical standards are subject to change.
B2B buyers must conduct their own independent and thorough due diligence before making any purchasing decisions. This includes contacting suppliers directly, verifying certifications, requesting samples, and seeking professional consultation. The risk of relying on any information in this guide is borne solely by the reader.
Strategic Sourcing Conclusion and Outlook for spider gag
What Are the Key Takeaways for B2B Buyers of Spider Gags?
In conclusion, the strategic sourcing of spider gags offers significant advantages for international B2B buyers. Understanding the unique specifications and applications of spider gags is crucial to make informed purchasing decisions. By leveraging supplier networks and market intelligence, businesses can optimize their procurement processes, ensuring they acquire high-quality products at competitive prices.
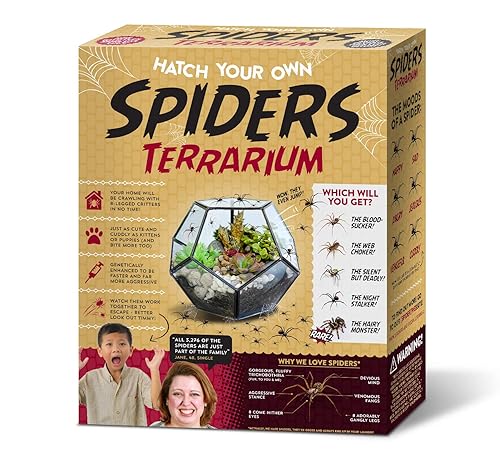
A stock image related to spider gag.
Why Is Strategic Sourcing Essential in the Global Market?
Strategic sourcing not only enhances supply chain efficiency but also mitigates risks associated with fluctuating market dynamics, especially in regions like Africa, South America, the Middle East, and Europe. Buyers should prioritize partnerships with reliable manufacturers and suppliers who can provide consistent quality and support, which is vital in maintaining operational integrity.
How Can B2B Buyers Prepare for Future Trends in Spider Gag Sourcing?
Looking ahead, the demand for spider gags is expected to grow, driven by advancements in industrial applications and increased safety regulations. B2B buyers should stay proactive by investing in technology and data analytics to forecast trends and adapt to market shifts. Engaging with local suppliers can also enhance responsiveness and reduce lead times, ultimately leading to a more resilient supply chain.
In a rapidly evolving marketplace, now is the time for buyers from diverse regions to refine their sourcing strategies and embrace innovation. By doing so, they position themselves favorably for the opportunities that lie ahead in the spider gag sector.