Discover the Best Blunt Roller: A Complete Buying Guide (2025)
Introduction: Navigating the Global Market for blunt roller
Navigating the global market for blunt rollers presents a unique challenge for international B2B buyers seeking to optimize their production processes. With a growing demand for efficient and reliable blunt rollers, particularly in regions like Africa, South America, the Middle East, and Europe, sourcing the right equipment is crucial. This guide offers a comprehensive overview of blunt rollers, covering various types, applications, and the critical aspects of supplier vetting. By delving into cost considerations and performance metrics, this resource equips buyers with the insights needed to make informed purchasing decisions.
Understanding the nuances of blunt rollers can significantly impact operational efficiency and product quality. Whether you’re in Kenya looking for robust rollers suited for local manufacturing conditions or in Spain seeking advanced technology to enhance production capabilities, the information presented here is tailored to meet diverse regional needs. This guide empowers B2B buyers by providing actionable insights into selecting the right blunt rollers that align with their business objectives. By addressing key challenges and offering expert recommendations, we aim to facilitate smarter sourcing decisions that drive success in the competitive landscape of global trade.
Understanding blunt roller Types and Variations
Type Name | Key Distinguishing Features | Primary B2B Applications | Brief Pros & Cons for Buyers |
---|---|---|---|
Standard Blunt Roller | Flat, wide surface for even distribution of weight | Construction, landscaping | Pros: Versatile, suitable for various surfaces. Cons: May require heavier machinery for operation. |
Hydraulic Blunt Roller | Equipped with hydraulic systems for adjustable pressure | Road construction, paving | Pros: Enhanced control over compaction. Cons: Higher maintenance costs due to hydraulic systems. |
Vibratory Blunt Roller | Incorporates vibration technology for increased efficiency | Heavy-duty compaction projects | Pros: Faster compaction rates. Cons: Can be more expensive than standard rollers. |
Pneumatic Blunt Roller | Utilizes air-filled tires for flexibility and better traction | Asphalt paving, road maintenance | Pros: Reduces surface damage, adaptable to uneven terrain. Cons: Limited effectiveness on very soft soils. |
Mini Blunt Roller | Compact size for tight spaces and small projects | Urban construction, landscaping | Pros: Maneuverable, ideal for limited access areas. Cons: Limited compaction depth compared to larger models. |
What are the characteristics of a Standard Blunt Roller?
The Standard Blunt Roller is characterized by its flat and wide surface, allowing for an even distribution of weight across the material being compacted. This type is commonly used in construction and landscaping projects where a solid foundation is necessary. Buyers should consider the operational requirements, as this roller may need heavier machinery for efficient use, but it offers versatility across various surfaces.
How does a Hydraulic Blunt Roller enhance compaction?
Hydraulic Blunt Rollers are designed with hydraulic systems that allow operators to adjust the pressure exerted during compaction. This feature is particularly beneficial in road construction and paving, where precise control over compaction is critical. While these rollers provide enhanced performance, buyers should be aware of the higher maintenance costs associated with hydraulic systems.
What advantages do Vibratory Blunt Rollers offer?
Vibratory Blunt Rollers utilize vibration technology to increase compaction efficiency, making them ideal for heavy-duty projects. They are particularly effective in achieving faster compaction rates, which can significantly reduce project timelines. However, potential buyers should weigh the higher initial investment against the operational benefits, as these rollers can be more costly than standard models.
In what scenarios is a Pneumatic Blunt Roller most effective?
Pneumatic Blunt Rollers feature air-filled tires that provide flexibility and better traction on various surfaces, making them suitable for asphalt paving and road maintenance. Their design minimizes surface damage and allows for effective operation on uneven terrain. Nonetheless, buyers should consider their limitations, as these rollers may not perform well on very soft soils.
Why choose a Mini Blunt Roller for specific projects?
Mini Blunt Rollers are compact and designed for maneuverability, making them ideal for urban construction and landscaping projects with limited access. Their small size allows for effective compaction in tight spaces, but they have a limited compaction depth compared to larger models. Buyers looking for equipment that can operate in confined areas should consider this option while being mindful of its limitations in larger applications.
Related Video: Snoop Dogg’s Blunt Roller Reveals How She Got The Greatest $50K Job On Earth
Key Industrial Applications of blunt roller
Industry/Sector | Specific Application of blunt roller | Value/Benefit for the Business | Key Sourcing Considerations for this Application |
---|---|---|---|
Construction | Asphalt compaction during road construction | Ensures a smooth and durable road surface | Look for durability, weight capacity, and compatibility with existing machinery. |
Agriculture | Soil preparation for planting crops | Prepares soil effectively for optimal crop yield | Evaluate roller size, weight, and ease of transport for various terrains. |
Manufacturing | Surface finishing in manufacturing processes | Enhances product quality and consistency | Consider the roller material, size, and precision for specific manufacturing needs. |
Mining | Compacting material for better excavation efficiency | Increases productivity and reduces operational costs | Assess the roller’s ability to handle different material types and environmental conditions. |
Landscaping | Creating level surfaces for landscaping projects | Improves aesthetics and functionality of outdoor spaces | Focus on the roller’s maneuverability and compatibility with various landscape designs. |
How is the blunt roller used in construction for asphalt compaction?
In the construction industry, blunt rollers are essential for asphalt compaction during road construction projects. Their heavy weight and broad surface area allow for effective compression of asphalt layers, resulting in a smooth and durable road surface. This is critical for ensuring longevity and safety in transportation infrastructure. Buyers in this sector, particularly from regions like Africa and the Middle East, should prioritize sourcing rollers that are robust, have high weight capacities, and can operate efficiently in varying weather conditions.
What role does the blunt roller play in agriculture for soil preparation?
In agriculture, blunt rollers are used to prepare soil for planting crops by breaking up clumps and leveling the ground. This process is vital for ensuring optimal seed-to-soil contact, which can significantly enhance crop yields. For international B2B buyers, especially in South America where agricultural output is crucial, it is important to consider the roller’s size and weight. These factors influence the ease of transport across different terrains, as well as the roller’s effectiveness in various soil types.
How does blunt roller enhance manufacturing processes?
Within the manufacturing sector, blunt rollers are utilized for surface finishing, where they help achieve a uniform and polished product finish. This application is critical in industries like automotive and electronics, where product quality is paramount. Buyers should look for rollers that are made from durable materials and provide precise control over the finishing process. Sourcing considerations should include the roller’s size and the specific manufacturing requirements to ensure compatibility and efficiency.
In what ways does blunt roller improve efficiency in mining?
In mining operations, blunt rollers are employed to compact materials, facilitating better excavation and reducing the time needed for site preparation. This application is particularly beneficial in regions with challenging terrain, as effective compaction can lead to increased productivity and lower operational costs. Buyers in this sector should assess the roller’s ability to handle various material types and its performance under different environmental conditions, ensuring it meets the demands of the mining operation.
How is blunt roller utilized in landscaping for creating level surfaces?
Blunt rollers are also valuable in landscaping projects, where they are used to create level surfaces for gardens, parks, and recreational areas. This application enhances the aesthetic appeal and functionality of outdoor spaces, making them more accessible and enjoyable. For buyers focused on landscaping in Europe, it is crucial to consider the roller’s maneuverability and how well it can adapt to diverse landscape designs. Ensuring that the roller is easy to transport and operate in various settings can significantly impact project efficiency and success.
Related Video: Types of bearings and its applications
3 Common User Pain Points for ‘blunt roller’ & Their Solutions
Scenario 1: Difficulty in Achieving Consistent Roll Quality
The Problem: Many B2B buyers in the blunt roller market face the challenge of inconsistent roll quality, which can lead to product waste and dissatisfied customers. This inconsistency often arises from variations in raw materials or the manufacturing process, resulting in poorly rolled blunts that compromise the user experience. For businesses, this not only affects customer loyalty but also increases operational costs due to wasted materials and the need for rework.
The Solution: To overcome this issue, B2B buyers should prioritize sourcing blunt rollers from manufacturers that implement stringent quality control measures throughout the production process. Look for suppliers that utilize advanced technology for uniform material distribution and precise rolling mechanisms. It’s beneficial to request samples and conduct trials before committing to large orders, ensuring the product meets your specifications. Additionally, investing in training for staff on how to use the blunt roller correctly can significantly enhance the consistency of the final product. Creating a feedback loop where operators can report issues back to the manufacturer can also help in refining the roller’s design or the rolling technique used.
Scenario 2: High Maintenance and Repair Costs
The Problem: Another common pain point for B2B buyers is the high maintenance and repair costs associated with blunt rollers. Frequent breakdowns can lead to production downtime, which is particularly detrimental in fast-paced environments where timely product delivery is crucial. Buyers often find themselves spending more on repairs than anticipated, impacting their overall profitability and operational efficiency.
The Solution: To mitigate maintenance costs, it is essential for buyers to choose blunt rollers designed with durability in mind. Look for models that use high-quality materials and have a reputation for reliability. Suppliers that offer extended warranties or maintenance plans can provide additional security against unforeseen expenses. Buyers should also consider investing in routine maintenance training for their staff, ensuring they understand how to care for the equipment properly and identify potential issues before they escalate. Establishing a relationship with a reliable technician or service provider for regular check-ups can also extend the lifespan of the blunt rollers, reducing long-term costs.
Scenario 3: Limited Customization Options
The Problem: B2B buyers often encounter limitations in customization options for blunt rollers, which can hinder their ability to meet specific customer demands or adapt to market trends. When suppliers do not offer versatile or customizable products, buyers may struggle to differentiate their offerings in a competitive market, potentially losing business to more adaptable competitors.
The Solution: To address this challenge, buyers should seek out suppliers who provide customizable blunt roller solutions. Engage in discussions with manufacturers about your specific requirements, including size, design, and functionality. Some manufacturers might offer modular designs that allow for easy upgrades or modifications based on changing needs. Additionally, forming partnerships with suppliers that prioritize innovation can provide access to new technologies and designs that enhance product offerings. Participating in industry trade shows or forums can also help buyers discover emerging trends and customization options that align with their business goals, allowing them to stay competitive in the market.
Strategic Material Selection Guide for blunt roller
When selecting materials for blunt rollers, it is crucial to consider various factors that influence performance, durability, and cost-effectiveness. Below, we analyze four common materials used in the manufacturing of blunt rollers, highlighting their properties, advantages, disadvantages, and specific considerations for international B2B buyers.
What are the Key Properties of Rubber for Blunt Rollers?
Rubber is a popular choice for blunt rollers due to its excellent flexibility and resilience. It can withstand a wide range of temperatures and pressures, making it suitable for various applications. Rubber also exhibits good abrasion resistance, which is essential for maintaining the integrity of the roller over time.
Pros and Cons of Rubber:
– Pros: High durability, excellent grip, and resistance to wear and tear.
– Cons: Can degrade under UV exposure and extreme temperatures, leading to a shorter lifespan in harsh environments.
Impact on Application:
Rubber is compatible with a variety of media, including oils and chemicals, making it versatile for different industries. However, its performance may be compromised in extreme conditions, which is a consideration for buyers in regions with high UV exposure or temperature fluctuations.
Considerations for International Buyers:
Buyers from Africa, South America, the Middle East, and Europe should ensure compliance with local standards such as ASTM or DIN. Additionally, they should consider the availability of rubber grades suitable for their specific environmental conditions.
How Does Steel Compare as a Material for Blunt Rollers?
Steel is known for its strength and durability, making it an excellent choice for blunt rollers that require high load-bearing capacity. It typically has a high temperature and pressure rating, which allows it to perform well under demanding conditions.
Pros and Cons of Steel:
– Pros: Exceptional strength, longevity, and resistance to deformation.
– Cons: Heavier than other materials, which may impact the overall weight of the equipment. It can also be prone to corrosion if not properly treated.
Impact on Application:
Steel’s compatibility with heavy-duty applications makes it ideal for industrial settings. However, in corrosive environments, such as those found in coastal regions, additional protective coatings may be necessary.
Considerations for International Buyers:
Buyers should be aware of the need for corrosion-resistant treatments, particularly in humid or marine environments. Compliance with international standards for steel grades is also essential for ensuring product reliability.
What are the Benefits of Using Polyurethane for Blunt Rollers?
Polyurethane is increasingly being used for blunt rollers due to its excellent abrasion resistance and flexibility. It can handle a wide range of temperatures and pressures, making it suitable for various applications.
Pros and Cons of Polyurethane:
– Pros: High resilience, excellent wear resistance, and good chemical compatibility.
– Cons: Generally more expensive than rubber and may require specific processing techniques during manufacturing.
Impact on Application:
Polyurethane’s compatibility with different media, including solvents and oils, makes it a versatile choice. Its durability ensures a long service life, even in demanding conditions.
Considerations for International Buyers:
International buyers should consider the availability of polyurethane materials that meet local compliance standards. The cost implications of sourcing high-quality polyurethane should also be factored into the purchasing decision.
Why is Aluminum a Suitable Material for Blunt Rollers?
Aluminum is lightweight and resistant to corrosion, making it an attractive option for blunt rollers used in various applications. Its low density allows for easier handling and installation.
Pros and Cons of Aluminum:
– Pros: Lightweight, excellent corrosion resistance, and good thermal conductivity.
– Cons: Lower load-bearing capacity compared to steel and can be more expensive.
Impact on Application:
Aluminum is suitable for applications where weight reduction is crucial, such as in portable equipment. However, its load-bearing limitations may restrict its use in heavy-duty applications.
Considerations for International Buyers:
Buyers should ensure that the aluminum grades used comply with relevant international standards. Additionally, the cost of aluminum may vary significantly depending on market conditions, which is an important consideration for budget-conscious buyers.
Material | Typical Use Case for blunt roller | Key Advantage | Key Disadvantage/Limitation | Relative Cost (Low/Med/High) |
---|---|---|---|---|
Rubber | General-purpose applications | High durability and flexibility | Degrades under UV exposure | Medium |
Steel | Heavy-duty industrial applications | Exceptional strength and longevity | Prone to corrosion | Medium |
Polyurethane | Versatile applications | Excellent abrasion resistance | Higher cost than rubber | High |
Aluminum | Lightweight equipment | Corrosion resistance | Lower load-bearing capacity | Medium to High |
This strategic material selection guide provides international B2B buyers with insights into the properties, advantages, and limitations of each material, facilitating informed decision-making tailored to their specific needs and regional considerations.
In-depth Look: Manufacturing Processes and Quality Assurance for blunt roller
What Are the Main Stages of Manufacturing a Blunt Roller?
The manufacturing process of a blunt roller involves several key stages that ensure the final product meets industry standards and buyer expectations. Understanding these stages is crucial for international B2B buyers looking to source high-quality blunt rollers.
Material Preparation: What Materials Are Used in Blunt Roller Manufacturing?
The first step in manufacturing a blunt roller is material preparation. Typically, blunt rollers are made from durable materials such as stainless steel, aluminum, or high-grade plastics. These materials are selected for their strength, resistance to wear, and ability to withstand various environmental conditions.
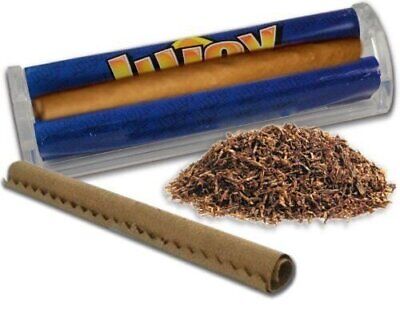
A stock image related to blunt roller.
Before production begins, raw materials undergo quality checks to verify their compliance with international standards. This includes assessing the chemical composition and mechanical properties. Buyers should inquire about the sourcing of these materials, as local suppliers might offer cost advantages and shorter lead times.
Forming: How Are Blunt Rollers Shaped and Molded?
Once the materials are prepared, the next stage is forming. This can involve techniques such as machining, stamping, or molding. For instance, a typical method for creating the body of a blunt roller is CNC machining, which allows for precision shaping and detailing.
In the case of molded blunt rollers, the plastic or rubber components are shaped using injection molding techniques, ensuring consistent quality across batches. Buyers should consider suppliers that utilize advanced forming technologies, as this often translates to better product consistency and lower manufacturing defects.
Assembly: What Does the Assembly Process Involve?
The assembly stage involves bringing together all components of the blunt roller. This includes attaching the roller body to the handle and any additional features such as grips or safety mechanisms. Quality control during assembly is critical; each unit should be checked for proper fit and functionality.
Many manufacturers employ automated assembly lines to improve efficiency and reduce human error. For international buyers, it’s important to understand the assembly processes used by suppliers, as this can impact both the cost and quality of the final product.
Finishing: How Is the Final Product Treated for Quality?
Finishing processes enhance the appearance and durability of blunt rollers. This may include surface treatments such as anodizing for metal components or applying protective coatings to prevent corrosion and wear.
Additionally, polishing and painting are common finishing steps that not only improve aesthetics but also add to the roller’s functionality. Buyers should ask about the finishing techniques employed by suppliers to ensure that the products meet their specific requirements for durability and appearance.
What Quality Assurance Standards Are Relevant for Blunt Rollers?
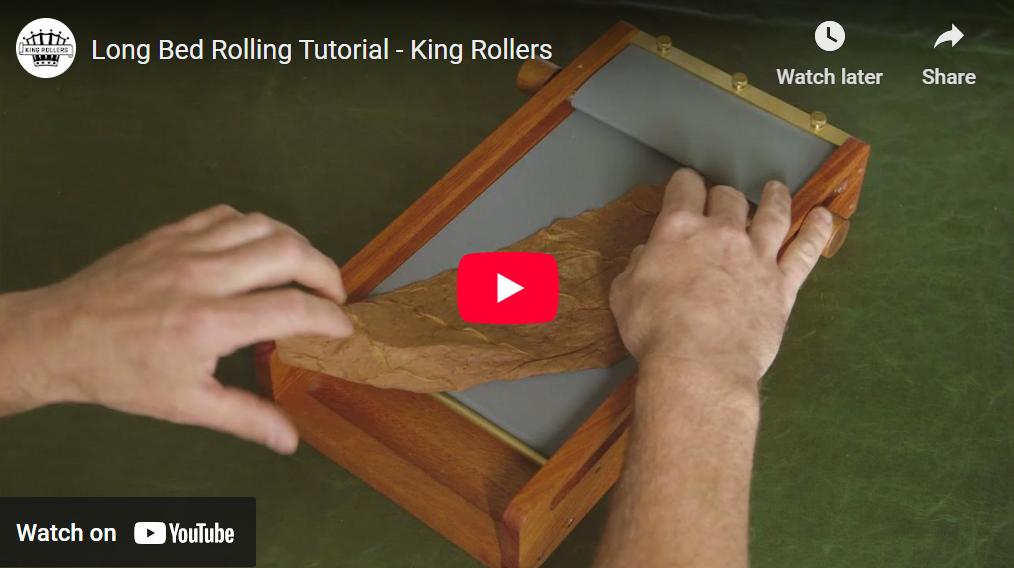
A stock image related to blunt roller.
Quality assurance is critical in the manufacturing of blunt rollers, particularly for international B2B transactions. Understanding the relevant standards can help buyers ensure they are sourcing from reputable manufacturers.
Which International Standards Should Buyers Look For?
ISO 9001 is a widely recognized quality management standard that outlines the criteria for establishing an effective quality management system. Manufacturers that are ISO 9001 certified demonstrate their commitment to quality and customer satisfaction.
Additionally, industry-specific certifications such as CE (Conformité Européenne) and API (American Petroleum Institute) may also apply, depending on the intended use of the blunt roller. Buyers should verify that suppliers hold the necessary certifications relevant to their markets.
What Are the Key Quality Control Checkpoints During Manufacturing?
Quality control checkpoints are essential to ensuring that the manufacturing process adheres to set standards. Key checkpoints include:
- Incoming Quality Control (IQC): This involves inspecting raw materials upon arrival to ensure they meet specified criteria.
- In-Process Quality Control (IPQC): This occurs at various stages of production, checking for defects or deviations from standards.
- Final Quality Control (FQC): The final inspection is conducted before the product is packaged and shipped, ensuring that it meets all specifications.
B2B buyers should inquire about the specific quality control processes used by suppliers to ensure that they are receiving a high-quality product.
How Can B2B Buyers Verify Supplier Quality Control?
International B2B buyers must adopt strategies to verify the quality control processes of their suppliers. Here are some actionable insights:
What Should Buyers Consider During Supplier Audits?
Conducting supplier audits is an effective way to assess a manufacturer’s quality control practices. Buyers should look for audits that include:
- Assessment of manufacturing processes and equipment.
- Review of quality management documentation.
- Verification of compliance with international standards.
Buyers can either perform these audits themselves or hire third-party inspection services to ensure an objective assessment.
How Can Buyers Utilize Quality Reports and Third-Party Inspections?
Requesting quality reports from suppliers can provide insight into their manufacturing processes and quality control measures. These reports should detail inspection results, defects found, and corrective actions taken.
Third-party inspections can also be beneficial. Engaging an independent inspection agency to evaluate the products prior to shipment can offer peace of mind regarding quality and compliance with specifications.
What Nuances Should Buyers Be Aware of When Sourcing Internationally?
Sourcing blunt rollers internationally, particularly from regions such as Africa, South America, the Middle East, and Europe, presents unique challenges. Buyers should be aware of:
- Cultural Differences: Understanding regional business practices can facilitate smoother negotiations and partnerships.
- Regulatory Compliance: Different regions may have varying regulations regarding product safety and quality standards.
- Logistics and Shipping Considerations: International shipping can introduce delays and additional costs, so buyers should plan accordingly.
By considering these factors, B2B buyers can make informed decisions and ensure they are sourcing high-quality blunt rollers that meet their operational needs.
Practical Sourcing Guide: A Step-by-Step Checklist for ‘blunt roller’
When sourcing a blunt roller, particularly for international B2B transactions, it is essential to follow a structured approach to ensure quality, compliance, and value. This checklist will guide you through the necessary steps to effectively procure a blunt roller that meets your specifications and business needs.
Step 1: Define Your Technical Specifications
Start by clearly outlining the technical specifications you require for the blunt roller. This includes dimensions, materials, and any specific features that are essential for your operations. A well-defined specification not only helps in communicating your needs to potential suppliers but also aids in comparing different products objectively.
- Considerations:
- What is the intended use of the blunt roller? (e.g., commercial production, personal use)
- Are there specific regulations or standards the product must meet in your region?
Step 2: Conduct Market Research
Investigate the market to identify potential suppliers who specialize in manufacturing blunt rollers. Utilize online resources, industry trade shows, and professional networks to gather a list of potential candidates. Understanding market trends can also provide insights into pricing and product availability.
- Action Items:
- Review supplier websites and product catalogs.
- Check for industry reviews or testimonials regarding the suppliers.
Step 3: Evaluate Potential Suppliers
Before committing to a supplier, conduct a thorough evaluation. Request company profiles, product samples, and references from other businesses in similar industries. This process is crucial to ensure that the supplier can deliver quality products consistently.
- Key Questions:
- What is the supplier’s experience in the industry?
- Can they provide case studies or references from satisfied customers?
Step 4: Verify Supplier Certifications and Compliance
Ensure that the suppliers you are considering have the necessary certifications and comply with international quality standards. This step is particularly important when sourcing products across borders, as regulations may vary significantly.
- Important Certifications:
- ISO 9001 for quality management.
- Any specific industry-related certifications that may apply.
Step 5: Request Detailed Quotations
Once you have shortlisted potential suppliers, request detailed quotations. This should include pricing, lead times, payment terms, and shipping costs. A comprehensive quotation will allow you to perform a detailed cost analysis and determine the overall value of each offer.
- Comparison Factors:
- Are there bulk discounts available?
- What are the terms for after-sales support or warranty?
Step 6: Assess Logistics and Shipping Options
Consider the logistics involved in importing the blunt rollers. Assess shipping options, delivery times, and any potential customs duties that may apply. A smooth logistics process is crucial for timely operations.
- Logistics Checklist:
- What shipping methods are available (air, sea, etc.)?
- Who will handle customs clearance, and what documentation will be required?
Step 7: Finalize the Agreement
After selecting the supplier that best meets your criteria, finalize the agreement. Ensure that all terms are clearly outlined in a formal contract, including quality expectations, delivery schedules, and payment terms. A well-documented agreement protects both parties and sets clear expectations.
- Key Elements to Include:
- Penalties for late delivery or non-compliance.
- Procedures for handling defects or quality issues.
Following this checklist will streamline your sourcing process for blunt rollers, ensuring you make informed decisions that align with your business objectives.
Comprehensive Cost and Pricing Analysis for blunt roller Sourcing
What Are the Key Cost Components in Blunt Roller Sourcing?
When sourcing blunt rollers, understanding the cost structure is essential for effective budgeting and negotiation. The primary cost components include:
-
Materials: The choice of materials greatly influences the overall cost. High-quality metals or specialized polymers used in manufacturing blunt rollers can increase the price but also enhance durability and performance.
-
Labor: Labor costs vary by region, impacting the total cost. In countries with higher labor costs, such as parts of Europe, expect to pay more compared to regions like South America or Africa, where labor might be less expensive.
-
Manufacturing Overhead: This includes costs associated with utilities, rent, and equipment maintenance. Factories operating in regions with higher operational costs will reflect this in their pricing.
-
Tooling: Initial tooling costs can be significant, especially for custom designs. These costs are typically amortized over the production volume, making them a critical factor in per-unit pricing.
-
Quality Control (QC): Implementing rigorous QC processes ensures the product meets industry standards. However, it adds to the overall cost. Buyers should weigh the importance of quality certifications when considering price.
-
Logistics: Transportation and shipping costs can vary based on distance, shipping method, and Incoterms. International buyers should be aware of these factors, as they can significantly affect the final price.
-
Margin: Suppliers will include a profit margin in their pricing. Understanding the typical margins in the industry can help buyers gauge if they are receiving a fair price.
How Do Price Influencers Affect Blunt Roller Costs?
Several factors can influence the pricing of blunt rollers, particularly for international buyers:
-
Volume and Minimum Order Quantity (MOQ): Larger orders often lead to discounts due to economies of scale. Buyers should consider their purchasing strategy to optimize costs.
-
Specifications and Customization: Custom designs or specific material requirements can increase costs. It is vital to clearly communicate specifications to avoid unexpected price hikes.
-
Material Quality and Certifications: Higher quality materials or compliance with specific industry standards can increase the cost. However, investing in quality can reduce maintenance and replacement costs over time.
-
Supplier Factors: The reputation and reliability of the supplier can influence pricing. Established suppliers may charge a premium but often provide better service and quality assurance.
-
Incoterms: Understanding Incoterms is crucial for international buyers. They dictate the responsibilities of buyers and sellers regarding shipping, insurance, and tariffs, which can impact overall costs.
What Are the Best Buyer Tips for Cost-Efficient Blunt Roller Sourcing?
International B2B buyers should consider the following tips to enhance cost-efficiency in blunt roller sourcing:
-
Negotiation Strategies: Leverage your purchasing volume to negotiate better terms. Establishing long-term relationships with suppliers can also lead to better pricing and service.
-
Total Cost of Ownership (TCO): Look beyond the initial purchase price. Consider maintenance, potential downtime, and replacement costs to understand the true value of your investment.
-
Pricing Nuances for International Buyers: Be aware of currency fluctuations and tariffs that may impact pricing. Ensure that your pricing agreements account for these variables to avoid budget overruns.
-
Supplier Audits: Conducting audits or assessments of potential suppliers can provide insights into their operational efficiencies and cost structures, allowing for more informed purchasing decisions.
-
Research and Benchmarking: Regularly research market prices and trends. This will help you understand the competitive landscape and ensure that you are making informed purchasing decisions.
Disclaimer on Indicative Prices
The prices for blunt rollers can vary widely based on the factors discussed above. It is advisable for buyers to obtain multiple quotes and conduct thorough market research to ensure they are getting competitive pricing tailored to their specific needs.
Alternatives Analysis: Comparing blunt roller With Other Solutions
In the world of manufacturing and production, choosing the right tool or method is critical for efficiency and cost-effectiveness. The blunt roller is a popular solution for various applications, particularly in the processing and handling of materials. However, several alternatives can also achieve similar results, each with its unique advantages and disadvantages. This section compares the blunt roller with two viable alternatives: the conventional roller and the squeegee system.
Comparison Table
Comparison Aspect | Blunt Roller | Conventional Roller | Squeegee System |
---|---|---|---|
Performance | Effective for bulk material handling; minimizes damage | High efficiency; versatile across different materials | Excellent for liquid and semi-liquid materials; highly effective in cleaning |
Cost | Moderate initial investment; lower operational costs | Lower upfront cost; higher maintenance costs | Generally low cost; requires frequent replacement of squeegees |
Ease of Implementation | Requires training for optimal use | Easy to implement; minimal training needed | Simple setup; no specialized training required |
Maintenance | Low maintenance; durable | Moderate maintenance; parts may wear out | High maintenance; squeegees need regular replacement |
Best Use Case | Ideal for materials that require gentle handling | Suitable for a wide range of materials in various settings | Best for cleaning and application of liquids |
Detailed Breakdown of Alternatives
What are the advantages and disadvantages of the Conventional Roller?
The conventional roller is a widely used alternative that excels in handling various materials efficiently. Its design allows for quick and effective movement, making it versatile across different production lines. The initial cost is generally lower than that of a blunt roller, but it may incur higher maintenance costs due to wear and tear on the rollers. This makes it less suitable for environments where durability and long-term cost savings are priorities.
How does the Squeegee System compare to a Blunt Roller?
The squeegee system is particularly effective for applications involving liquids or semi-liquids, such as in cleaning processes or applying coatings. Its simplicity and low cost make it an attractive option for businesses looking to minimize upfront investments. However, the need for frequent replacement of squeegees can lead to higher operational costs over time. Additionally, the squeegee system may not be effective for solid materials, limiting its application compared to the blunt roller.
Conclusion: How can B2B buyers choose the right solution for their needs?
When selecting the appropriate solution for their operations, B2B buyers should consider their specific requirements, including the types of materials they handle, their budget, and the operational environment. The blunt roller is ideal for applications requiring gentle handling and durability, while the conventional roller offers versatility at a lower upfront cost. The squeegee system is best suited for liquid applications but may not be the most cost-effective in the long run due to maintenance needs. By carefully evaluating these factors, buyers can make informed decisions that align with their operational goals and budgetary constraints.
Essential Technical Properties and Trade Terminology for blunt roller
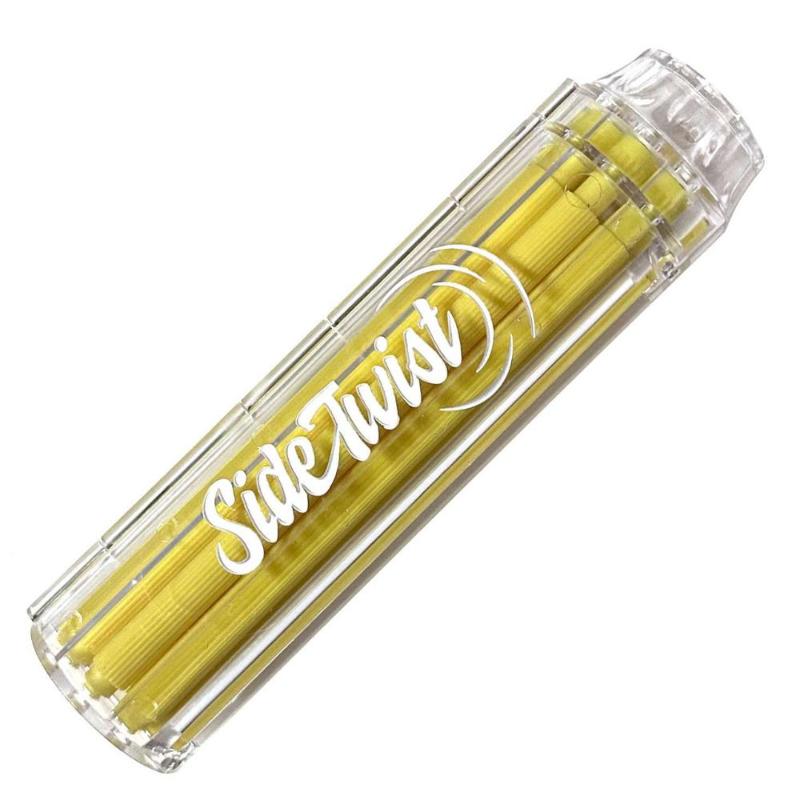
A stock image related to blunt roller.
What are the Key Technical Properties of a Blunt Roller?
When evaluating blunt rollers for industrial applications, understanding their technical specifications is crucial for ensuring optimal performance and longevity. Here are some essential properties to consider:
1. Material Grade
The material grade of a blunt roller significantly impacts its durability and performance. Common materials include high-carbon steel, stainless steel, and specialized alloys. Each material has distinct properties: high-carbon steel offers strength, while stainless steel provides corrosion resistance. Selecting the right material is vital for applications exposed to harsh environments, as it affects the overall life cycle of the roller.
2. Tolerance Levels
Tolerance refers to the allowable deviation in dimensions of the blunt roller. Precise tolerances are critical in applications requiring exact fit and alignment, such as in manufacturing processes. A tolerance of ±0.01 mm is often necessary for high-precision equipment, ensuring consistent performance and reducing wear over time. Understanding the required tolerances helps buyers avoid costly production errors.
3. Load Capacity
The load capacity of a blunt roller indicates the maximum weight it can support without deforming or failing. This property is essential for applications involving heavy materials or continuous operation. Load capacities can vary widely, with some rollers supporting up to several tons. Buyers must assess their specific needs to select a roller that meets or exceeds the required load specifications.
4. Surface Finish
The surface finish of a blunt roller affects its friction, wear resistance, and overall operational efficiency. Common finishes include polished, anodized, or coated surfaces. A smoother surface can reduce friction, enhancing performance in high-speed applications. Buyers should consider the operating conditions and environmental factors when selecting the appropriate surface finish.
5. Dimensions and Design
The dimensions and design of a blunt roller determine its compatibility with existing machinery. Important dimensions include diameter, width, and overall length. Custom designs may also be necessary for specific applications. Understanding the required dimensions ensures seamless integration into production lines, minimizing downtime during installation.
6. Operating Temperature Range
The operating temperature range indicates the environments in which the blunt roller can function effectively. Some rollers are designed for extreme conditions, while others may only operate within a moderate range. Knowing the temperature requirements helps buyers select rollers that will maintain performance under varying operational conditions.
What Common Trade Terms Should B2B Buyers Know When Purchasing Blunt Rollers?
Familiarizing oneself with industry terminology can streamline the purchasing process and enhance communication with suppliers. Here are some key terms related to blunt rollers:
1. OEM (Original Equipment Manufacturer)
OEM refers to companies that produce parts that are used in another company’s end product. In the context of blunt rollers, buyers often seek OEMs to ensure compatibility and reliability with existing machinery. Understanding OEM relationships is crucial for maintaining quality standards.
2. MOQ (Minimum Order Quantity)
MOQ is the smallest number of units that a supplier is willing to sell. Knowing the MOQ helps buyers plan their procurement strategies and manage inventory effectively. For blunt rollers, MOQs can vary based on material and customization requirements.
3. RFQ (Request for Quotation)
An RFQ is a formal document sent to suppliers to request pricing and terms for specific products. When sourcing blunt rollers, an RFQ can clarify specifications, quantities, and delivery timelines. This process helps buyers make informed decisions and compare offers from multiple suppliers.
4. Incoterms (International Commercial Terms)
Incoterms are a set of international rules that define the responsibilities of buyers and sellers in global trade. Understanding these terms is crucial for international transactions involving blunt rollers, as they dictate shipping costs, risk transfer, and delivery responsibilities.
5. Lead Time
Lead time refers to the amount of time it takes from placing an order until the product is delivered. For blunt rollers, lead times can affect production schedules. Buyers should inquire about lead times to avoid disruptions in their operations.
6. Customization
Customization involves modifying standard products to meet specific buyer requirements. Many manufacturers offer tailored blunt rollers to accommodate unique applications. Understanding customization options enables buyers to obtain products that precisely fit their operational needs.
By grasping these technical properties and trade terms, international B2B buyers can make informed purchasing decisions regarding blunt rollers, ensuring they meet their operational demands effectively.
Navigating Market Dynamics and Sourcing Trends in the blunt roller Sector
What Are the Current Market Dynamics and Key Trends Affecting the Blunt Roller Sector?
The blunt roller market is experiencing significant growth, driven by increasing consumer demand for cannabis-related products across various regions. In Africa, South America, the Middle East, and Europe, regulatory changes and the gradual acceptance of cannabis use for medicinal and recreational purposes are propelling market expansion. International B2B buyers should note that technological advancements in production processes are enhancing efficiency and reducing costs, making sourcing more appealing.
Emerging trends such as automation in manufacturing and the use of artificial intelligence for quality control are reshaping the landscape. Buyers should also pay attention to the shift towards online platforms for sourcing blunt rollers, which facilitates a more streamlined procurement process. In addition, the rise of e-commerce is allowing manufacturers to reach broader markets, providing international buyers with a wider range of options.
Furthermore, sustainability is becoming a crucial consideration. As environmental awareness grows, suppliers are increasingly adopting eco-friendly practices, which influences purchasing decisions. For international B2B buyers, understanding these dynamics is vital to making informed sourcing decisions that align with market expectations.
How Is Sustainability Impacting the Sourcing of Blunt Rollers?
The environmental impact of the blunt roller industry is an essential factor for international B2B buyers to consider. The sourcing of raw materials, such as paper and tobacco, can significantly affect the carbon footprint of production. Buyers should prioritize suppliers who demonstrate a commitment to sustainability through the use of recycled materials and environmentally friendly production processes.
Ethical sourcing is becoming increasingly relevant, with consumers demanding transparency in supply chains. International buyers should seek partners who adhere to ethical practices, such as fair labor conditions and responsible harvesting methods. Certifications like Forest Stewardship Council (FSC) and other green certifications can serve as indicators of a supplier’s commitment to sustainability.
In addition, the trend towards using organic materials for blunt rollers not only meets consumer demand but also reduces the overall environmental impact. B2B buyers from regions such as Kenya and Spain should actively engage with suppliers who prioritize eco-friendly materials and practices, as this can enhance brand reputation and customer loyalty in a competitive market.
What Is the Brief History of Blunt Rollers in the B2B Context?
The evolution of blunt rollers can be traced back to the early 1990s when cannabis enthusiasts began using cigar wraps to create blunts. Initially, these products were handmade, leading to variability in quality and availability. However, as the cannabis market expanded, manufacturers recognized the opportunity to standardize production, leading to the introduction of pre-rolled blunt rollers.
Over the years, innovation in materials and design has transformed the blunt roller sector. The introduction of flavored wraps and organic options has catered to diverse consumer preferences, making blunt rollers a staple in the cannabis market. For B2B buyers, understanding this evolution is crucial for identifying reliable suppliers and anticipating future trends in product offerings. As the market continues to mature, staying informed about historical context can aid in strategic sourcing decisions.
Frequently Asked Questions (FAQs) for B2B Buyers of blunt roller
1. How do I choose the right blunt roller for my business needs?
When selecting a blunt roller, consider factors such as the scale of your operations, the materials you plan to use, and the desired output speed. Look for rollers with adjustable settings for different sizes and types of blunt wraps. Additionally, assess the machine’s build quality and ease of maintenance to ensure longevity and reliability. Reading customer reviews and seeking recommendations from industry peers can also help in making an informed decision tailored to your specific business requirements.
2. What are the typical minimum order quantities (MOQs) for blunt rollers?
MOQs for blunt rollers can vary significantly based on the supplier and the type of machine. Many manufacturers may set MOQs between 1 to 10 units for standard models, while custom or specialized machines may require larger orders. It’s advisable to negotiate these terms directly with suppliers to ensure they align with your budget and production needs, especially if you’re a small business or startup.
3. What payment terms should I expect when sourcing blunt rollers internationally?
Payment terms for international purchases of blunt rollers typically include options such as a 30% deposit with the order and the balance before shipment, or net 30/60 days after delivery. However, terms can vary depending on the supplier’s policies and your relationship with them. It’s essential to clarify these terms upfront, and consider using secure payment methods like letters of credit or escrow services to mitigate risks associated with international transactions.
4. How can I ensure quality assurance (QA) when sourcing blunt rollers?
To ensure quality assurance, request detailed specifications and certifications from the manufacturer. Conduct factory audits if possible, or consider hiring third-party inspection services to verify product quality before shipment. Additionally, ask for samples or trial runs to evaluate the machine’s performance. Establishing a clear communication channel with your supplier will also facilitate ongoing quality checks throughout the production process.
5. What customization options are available for blunt rollers?
Most manufacturers offer customization options, including size, color, material, and specific features tailored to your production needs. Discuss your requirements with the supplier to see if they can accommodate unique specifications, such as integration with existing production lines or additional functionality. Keep in mind that customizations may impact lead times and pricing, so factor these into your planning.
6. How do I vet suppliers for blunt rollers in international markets?
Vetting suppliers involves researching their reputation, experience, and customer feedback. Use platforms like Alibaba or Global Sources to find verified suppliers and read reviews. Request references and conduct background checks to assess reliability. It’s also beneficial to visit trade shows or industry events to connect directly with potential suppliers and evaluate their products firsthand.
7. What are the logistics considerations when importing blunt rollers?
Logistics play a crucial role in importing blunt rollers. Consider shipping methods (air vs. sea), customs duties, and lead times. Ensure that your supplier provides necessary documentation for customs clearance, such as invoices and packing lists. Additionally, engage with a freight forwarder who understands the regulations in your region, especially for buyers in Africa or South America, to streamline the import process and avoid delays.
8. How do I handle after-sales support and maintenance for blunt rollers?
After-sales support is vital for the longevity of your blunt rollers. Confirm that the supplier offers a warranty and accessible customer service for troubleshooting and repairs. Establish a maintenance schedule to ensure regular upkeep, and inquire about the availability of spare parts. Building a good relationship with the supplier can also facilitate quicker support and access to resources in case of operational issues.
Important Disclaimer & Terms of Use
⚠️ Important Disclaimer
The information provided in this guide, including content regarding manufacturers, technical specifications, and market analysis, is for informational and educational purposes only. It does not constitute professional procurement advice, financial advice, or legal advice.
While we have made every effort to ensure the accuracy and timeliness of the information, we are not responsible for any errors, omissions, or outdated information. Market conditions, company details, and technical standards are subject to change.
B2B buyers must conduct their own independent and thorough due diligence before making any purchasing decisions. This includes contacting suppliers directly, verifying certifications, requesting samples, and seeking professional consultation. The risk of relying on any information in this guide is borne solely by the reader.
Strategic Sourcing Conclusion and Outlook for blunt roller
Why Is Strategic Sourcing Important for Blunt Roller Procurement?
In the competitive landscape of blunt roller procurement, strategic sourcing is essential for international B2B buyers aiming to optimize their supply chains. By leveraging data analytics and market intelligence, businesses can identify reliable suppliers, negotiate favorable terms, and ensure product quality. This approach not only reduces costs but also mitigates risks associated with supply chain disruptions, particularly in emerging markets across Africa, South America, the Middle East, and Europe.
How Can B2B Buyers Leverage Global Sourcing Trends?
Understanding global sourcing trends allows buyers to capitalize on innovations and cost efficiencies. For instance, buyers in Kenya and Spain can explore partnerships with manufacturers that utilize advanced production technologies. Furthermore, engaging with suppliers who prioritize sustainability can enhance brand reputation and meet the increasing demand for eco-friendly products.
What’s Next for International B2B Buyers?
As the market continues to evolve, staying informed about trends and best practices in strategic sourcing will be crucial. Buyers should consider establishing long-term relationships with suppliers and investing in technology that streamlines procurement processes. By doing so, they can enhance their competitive edge and ensure a resilient supply chain.
In conclusion, embracing strategic sourcing not only fosters growth but also positions your business for future success. Take proactive steps today to explore the vast opportunities in the global market for blunt rollers, ensuring you remain ahead of the curve.