Discover the Key Benefits of Appearance of Filter Paper (2025)
Introduction: Navigating the Global Market for appearance of filter paper
Navigating the complexities of the global market for filter paper can be a daunting task for international B2B buyers, particularly those hailing from diverse regions such as Africa, South America, the Middle East, and Europe. The appearance of filter paper is not merely a matter of aesthetics; it plays a critical role in the quality and efficacy of filtration processes across various industries. Understanding the nuances of sourcing high-quality filter paper that meets specific application requirements is essential for maintaining operational efficiency and product integrity.
This comprehensive guide delves into the multifaceted world of filter paper, covering everything from the different types available—such as qualitative and quantitative filter papers—to their diverse applications in laboratories, pharmaceuticals, and food industries. Additionally, we will explore essential factors in supplier vetting, ensuring that you partner with reputable manufacturers who can provide consistent quality and reliable service. Cost considerations will also be examined, helping you to balance budget constraints with quality demands.
Arming yourself with the insights provided in this guide will empower you to make informed purchasing decisions, mitigating risks and enhancing your procurement strategies. Whether you are looking to optimize your supply chain or simply seeking reliable sources for filter paper, this resource aims to equip you with the knowledge needed to navigate the global market effectively.
Understanding appearance of filter paper Types and Variations
Type Name | Key Distinguishing Features | Primary B2B Applications | Brief Pros & Cons for Buyers |
---|---|---|---|
Qualitative Filter Paper | Thick, high-absorbency, often used for analysis | Environmental testing, food & beverage | Pros: High retention; Cons: Limited flow rate |
Quantitative Filter Paper | Uniform thickness, low ash content | Laboratory analysis, pharmaceuticals | Pros: High precision; Cons: Higher cost |
Glass Microfiber Filter | High dirt-holding capacity, fast flow rates | Air and water filtration | Pros: Efficient; Cons: Less durable |
Membrane Filter Paper | Porous structure, available in various pore sizes | Microbiology, biotechnology | Pros: Versatile; Cons: Requires careful handling |
Specialty Filter Paper | Customizable for specific applications | Chemical processing, oil filtration | Pros: Tailored solutions; Cons: Longer lead times |
What Are the Characteristics of Qualitative Filter Paper?
Qualitative filter paper is characterized by its thickness and high absorbency, making it ideal for various analytical procedures. This type is commonly used in environmental testing and the food and beverage industry, where retaining fine particles is crucial. When considering a purchase, B2B buyers should evaluate the filter paper’s retention capabilities and flow rate, as a thicker paper might slow down filtration but provide better particle retention.
How Does Quantitative Filter Paper Differ in Use?
Quantitative filter paper is designed with uniform thickness and low ash content, making it suitable for precise laboratory analyses, especially in pharmaceuticals. This type guarantees high precision in measurements and results, which is vital for quality control processes. Buyers should assess the cost versus the accuracy required for their applications, as this type tends to be pricier but offers significant benefits in reliability.
What Advantages Do Glass Microfiber Filters Offer?
Glass microfiber filters are known for their high dirt-holding capacity and fast flow rates, making them excellent choices for air and water filtration applications. These filters can efficiently capture particulate matter while allowing for quick processing. However, buyers should be aware of their durability; while they are efficient, they may not withstand harsh chemical environments as well as other types.
In What Situations Should Membrane Filter Paper Be Used?
Membrane filter paper features a porous structure with various pore sizes, making it suitable for microbiological applications and biotechnology. Its versatility allows it to filter out bacteria and other microorganisms effectively. B2B buyers need to consider the specific pore size required for their applications, as well as the handling requirements, as membrane filters can be delicate and require careful use.
Why Choose Specialty Filter Paper for Specific Applications?
Specialty filter paper can be customized for specific applications, such as chemical processing and oil filtration. This type allows B2B buyers to tailor their filtration solutions to meet unique operational needs. However, the customization process may lead to longer lead times, so it’s essential for buyers to plan accordingly and assess their timelines against production requirements.
Related Video: Gravity filtration and folding a fluted filter paper
Key Industrial Applications of appearance of filter paper
Industry/Sector | Specific Application of Appearance of Filter Paper | Value/Benefit for the Business | Key Sourcing Considerations for this Application |
---|---|---|---|
Pharmaceuticals | Quality Control in Drug Manufacturing | Ensures purity and compliance with health standards | Certifications, material quality, and batch traceability |
Food and Beverage | Filtration in Beverage Production | Enhances product safety and quality | Food-grade certifications and chemical compatibility |
Environmental Testing | Air and Water Quality Monitoring | Supports regulatory compliance and public health | Material durability, filtration efficiency, and environmental certifications |
Laboratory Research | Sample Preparation and Analysis | Improves accuracy and reliability of results | Purity levels, particle retention, and compatibility with solvents |
Textile and Material Testing | Fiber Content Analysis | Ensures product quality and material specifications | Specific filtration ratings, size, and durability for testing procedures |
How is Filter Paper Used in Pharmaceuticals?
In the pharmaceutical industry, the appearance of filter paper is crucial for quality control during drug manufacturing. It is employed to filter out impurities from raw materials, ensuring that the final product meets stringent health and safety standards. For international B2B buyers, it is essential to source filter paper that has the necessary certifications and traceability to ensure compliance with local and international regulations. Buyers should prioritize suppliers who can provide detailed documentation about the material quality and batch history.
How Does Filter Paper Enhance Food and Beverage Safety?
In the food and beverage sector, filter paper plays a vital role in the filtration processes used during production. It is used to remove particulate matter from liquids, thereby enhancing product safety and quality. International B2B buyers in this sector should seek filter paper that is certified for food contact and compatible with various chemicals used in processing. Ensuring that the filter paper meets local food safety regulations is imperative for maintaining consumer trust and product integrity.
What Role Does Filter Paper Play in Environmental Testing?
Filter paper is essential in environmental testing, particularly for air and water quality monitoring. It is utilized to capture particulates and contaminants, supporting compliance with environmental regulations and protecting public health. For B2B buyers in Africa, South America, the Middle East, and Europe, sourcing durable filter paper with high filtration efficiency is critical. Buyers should also consider the environmental certifications of the filter paper to align with sustainability goals.
How is Filter Paper Important for Laboratory Research?
In laboratory settings, the appearance of filter paper is significant for sample preparation and analysis. It is used to separate solids from liquids, which is essential for accurate testing and research outcomes. B2B buyers in this field must focus on the purity levels and particle retention capabilities of the filter paper. Compatibility with various solvents and chemicals is also a key consideration to ensure reliable results in diverse research applications.
Why is Filter Paper Used in Textile and Material Testing?
The textile industry relies on filter paper for fiber content analysis, which is crucial for maintaining quality standards. It helps in determining the composition of materials, ensuring that products meet specified requirements. For B2B buyers, sourcing filter paper with specific filtration ratings and durability is vital for accurate testing procedures. Understanding the testing protocols and requirements of the end product will guide buyers in selecting the right type of filter paper for their applications.
3 Common User Pain Points for ‘appearance of filter paper’ & Their Solutions
Scenario 1: Inconsistent Quality of Filter Paper Affects Results
The Problem: For international B2B buyers, particularly those in sectors like pharmaceuticals and food processing, the appearance and quality of filter paper can significantly influence the final product. Many buyers encounter the challenge of receiving filter paper that varies in color, thickness, or surface texture from batch to batch. This inconsistency can lead to unreliable filtration results, affecting product quality and leading to potential compliance issues with industry regulations. For buyers in Africa or South America, where supply chains can be complex, these inconsistencies can become particularly problematic, causing delays and additional costs.
The Solution: To mitigate quality inconsistencies, buyers should prioritize sourcing filter paper from reputable manufacturers with established quality control processes. Request documentation detailing the manufacturing standards and certifications (like ISO or FDA compliance) of the filter paper. Additionally, conducting a pre-shipment inspection can help verify the quality of the product before it arrives. Buyers should also consider establishing a long-term relationship with a single supplier to ensure consistent product quality. Implementing a regular feedback loop with the supplier regarding product performance can lead to improved consistency over time.
Scenario 2: Difficulty in Selecting the Right Type of Filter Paper
The Problem: B2B buyers often find themselves overwhelmed by the wide variety of filter paper types available in the market, each designed for specific applications. This confusion is especially pronounced among buyers from the Middle East and Europe, where technical specifications can be intricate. Choosing the wrong type can lead to suboptimal filtration results, wasted resources, and financial losses. For instance, using filter paper that is too coarse for a fine filtration process can compromise the purity of the final product.
The Solution: To select the appropriate type of filter paper, buyers should first assess their specific filtration needs, including the particle size to be filtered, the volume of liquid, and the chemical compatibility of the paper. Consulting with filter paper manufacturers or industry experts can provide valuable insights into which products will best meet their needs. Buyers should also consider utilizing samples or trial orders to test different types of filter paper in their specific applications before making a bulk purchase. This proactive approach not only ensures the right choice but also minimizes the risk of future complications.
Scenario 3: Environmental Concerns Related to Filter Paper Disposal
The Problem: With increasing global focus on sustainability, B2B buyers, especially those in Europe and South America, are increasingly concerned about the environmental impact of their operations, including the disposal of filter paper. Many types of filter paper are not biodegradable and can contribute to landfill waste, raising ethical concerns among companies striving for eco-friendly practices. This can also lead to potential reputational damage and compliance issues with local regulations regarding waste management.
The Solution: To address environmental concerns, buyers should consider sourcing biodegradable or recyclable filter paper options. Engaging with suppliers who specialize in eco-friendly products can help ensure that the filter paper used aligns with sustainability goals. Additionally, companies can implement an efficient waste management strategy that includes recycling and proper disposal methods for used filter paper. Buyers should also communicate their sustainability requirements to suppliers, encouraging them to develop innovative solutions that meet these needs. By prioritizing environmentally responsible products and practices, companies can enhance their brand reputation while contributing positively to environmental conservation efforts.
Strategic Material Selection Guide for appearance of filter paper
When selecting materials for the appearance of filter paper, international B2B buyers must consider several factors that impact performance, compatibility, and cost. Below is an analysis of four common materials used in filter paper production, focusing on their properties, advantages, disadvantages, and specific considerations for buyers from diverse regions such as Africa, South America, the Middle East, and Europe.
What Are the Key Properties of Cotton Filter Paper?
Cotton filter paper is known for its excellent absorbency and filtration capabilities. It can withstand moderate temperatures and pressures, making it suitable for various laboratory applications. Cotton’s natural fibers provide a high level of porosity, allowing for effective separation of solids from liquids.
Pros & Cons: The primary advantage of cotton filter paper is its high absorbency, which is beneficial in applications requiring liquid retention. However, it can be more expensive than synthetic options, and its durability may be lower under extreme conditions.
Impact on Application: Cotton filter paper is particularly compatible with aqueous solutions, making it ideal for laboratory settings in pharmaceuticals and food industries.
Considerations for International Buyers: Buyers should ensure compliance with local regulations regarding natural fibers, as some regions may have specific standards for sourcing and processing.
How Does Synthetic Filter Paper Compare in Performance?
Synthetic filter paper, often made from polyester or nylon, offers superior chemical resistance and durability compared to natural fibers. These materials can handle higher temperatures and pressures, making them suitable for demanding industrial applications.
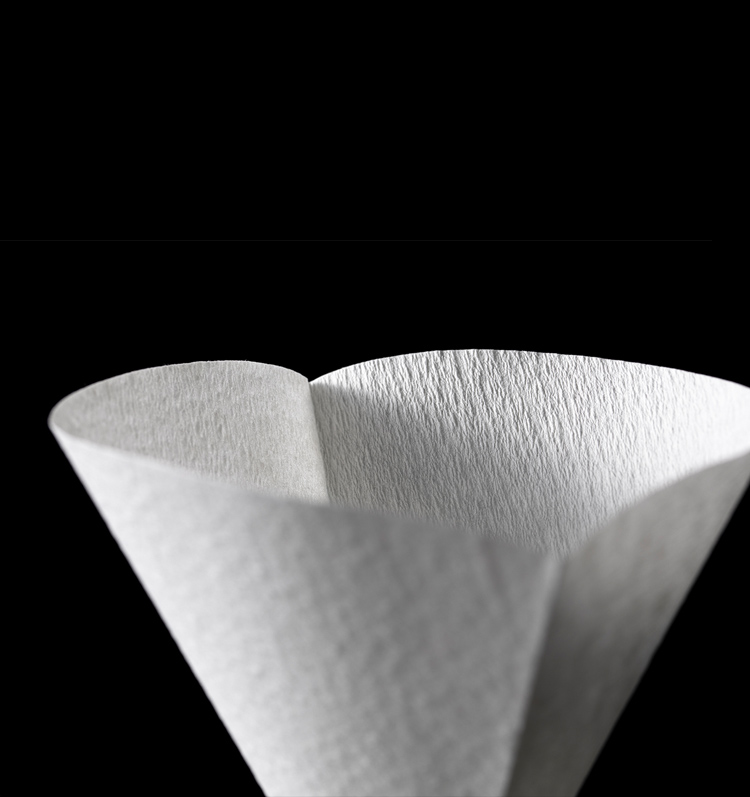
A stock image related to appearance of filter paper.
Pros & Cons: The key advantage of synthetic filter paper is its robustness and longevity, which can lead to lower replacement costs over time. However, the initial investment is typically higher, and some buyers may prefer natural materials for sustainability reasons.
Impact on Application: Synthetic filter paper is ideal for aggressive solvents and chemicals, making it a preferred choice in the chemical and petrochemical industries.
Considerations for International Buyers: Buyers should verify compliance with international standards such as ASTM or DIN, particularly when dealing with hazardous materials.
What Are the Benefits of Glass Fiber Filter Paper?
Glass fiber filter paper is renowned for its high flow rate and excellent particle retention capabilities. It can operate effectively at elevated temperatures and is resistant to most chemicals, making it suitable for a wide range of applications.
Pros & Cons: The primary advantage of glass fiber filter paper is its efficiency in filtering fine particles, which is crucial in analytical laboratories. However, it can be brittle and may not be suitable for all handling conditions.
Impact on Application: This type of filter paper is particularly effective in environmental testing and industrial applications where high filtration efficiency is required.
Considerations for International Buyers: Buyers should be aware of the potential for glass fibers to pose health risks and ensure that products meet safety standards in their respective regions.
Why Choose Cellulose Filter Paper for General Use?
Cellulose filter paper is one of the most commonly used materials due to its balance of performance and cost. It offers good filtration efficiency and is compatible with a variety of solvents and liquids.
Pros & Cons: The main advantage of cellulose filter paper is its affordability and availability, making it suitable for general laboratory use. However, it may not perform as well as synthetic options under extreme conditions.
Impact on Application: Cellulose filter paper is widely used in laboratories for routine filtration tasks, including in the food and beverage industry.
Considerations for International Buyers: Buyers should check for compliance with specific industry standards and certifications, especially in regions with stringent food safety regulations.
Summary Table of Materials for Filter Paper
Material | Typical Use Case for appearance of filter paper | Key Advantage | Key Disadvantage/Limitation | Relative Cost (Low/Med/High) |
---|---|---|---|---|
Cotton | Laboratory filtration of aqueous solutions | High absorbency | Higher cost, lower durability | Medium |
Synthetic | Chemical and petrochemical industries | Superior chemical resistance | Higher initial investment | High |
Glass Fiber | Environmental testing and industrial applications | High flow rate and particle retention | Brittle, handling risks | Medium |
Cellulose | General laboratory use | Affordable and widely available | Lower performance under extreme conditions | Low |
By understanding these materials and their implications, B2B buyers can make informed decisions that align with their specific needs and regional compliance requirements.
In-depth Look: Manufacturing Processes and Quality Assurance for appearance of filter paper
What Are the Key Stages in the Manufacturing Process of Filter Paper?
The manufacturing of filter paper involves several critical stages that ensure high quality and performance, particularly important for B2B buyers who demand consistency. The typical stages include:
-
Material Preparation: The primary materials for filter paper are cellulose fibers, which are often derived from wood pulp. These fibers are processed to create a slurry. The quality of the raw materials significantly impacts the final product, so buyers should prioritize suppliers who source high-grade cellulose.
-
Forming: During this stage, the slurry is evenly distributed onto a moving wire mesh. The water is drained away, leaving a mat of cellulose fibers. The forming process must ensure that the fibers are evenly spread to achieve uniform thickness and porosity, which are vital for filtration efficiency.
-
Pressing: The wet mat is subjected to pressure to remove excess water and compact the fibers. This step is crucial for enhancing the strength and durability of the filter paper.
-
Drying: The pressed paper is then dried in large drying machines. The drying process affects the final appearance, including color and texture, which can be critical for buyers who require specific aesthetic qualities.
-
Finishing: After drying, the filter paper may undergo additional treatments, such as coating or calendaring, to improve its filtration characteristics and appearance. This stage is particularly relevant for applications requiring specific surface properties.
-
Cutting and Packaging: Finally, the filter paper is cut into sheets or rolls and packaged for shipment. Proper packaging ensures that the product remains uncontaminated and undamaged during transport.
How Is Quality Assurance Maintained Throughout the Manufacturing Process?
Quality assurance (QA) is a crucial aspect of the manufacturing process that ensures filter paper meets international standards and customer specifications.
-
International Standards: Many manufacturers adhere to ISO 9001, which outlines criteria for a quality management system. Compliance with this standard assures buyers of consistent quality and continuous improvement practices. Additional certifications, such as CE marking for products sold in Europe or API for pharmaceutical applications, may also be relevant depending on the intended use of the filter paper.
-
Quality Control Checkpoints:
– Incoming Quality Control (IQC): This involves inspecting raw materials upon arrival to ensure they meet specified standards. Buyers should inquire about the sourcing and testing of materials used in production.
– In-Process Quality Control (IPQC): Throughout the manufacturing stages, regular checks are conducted to monitor parameters like weight, thickness, and porosity. This ensures any deviations from specifications can be addressed immediately.
– Final Quality Control (FQC): Before shipment, the finished product undergoes a comprehensive inspection to verify that it meets all quality standards and customer requirements.
What Common Testing Methods Are Used to Ensure Quality in Filter Paper?
To verify the quality of filter paper, several testing methods are commonly employed:
- Gravimetric Analysis: This method assesses the weight and thickness of the filter paper, ensuring it aligns with specifications.
- Filtration Efficiency Tests: These tests determine how effectively the filter paper removes particulates from fluids, a key performance metric.
- Burst Strength Testing: This evaluates the paper’s resistance to pressure, important for applications where the filter paper will encounter varying flow rates.
- Visual Inspection: A thorough visual examination for defects such as discoloration or uneven texture is often conducted, particularly for products where appearance is crucial.
How Can B2B Buyers Verify Supplier Quality Control?
For international B2B buyers, particularly those in Africa, South America, the Middle East, and Europe, verifying supplier quality control is paramount. Here are actionable steps:
-
Supplier Audits: Conducting regular audits of potential suppliers can provide insights into their manufacturing processes and quality management systems. This can include visits to their facilities or reviewing their audit reports.
-
Requesting Quality Reports: Buyers should ask for detailed QC reports that outline the results of the various tests performed on the filter paper. This documentation should include data on filtration efficiency, strength, and compliance with international standards.
-
Third-Party Inspections: Engaging third-party inspection agencies can provide an unbiased assessment of the supplier’s quality control measures. These inspections can be particularly valuable for buyers who are unable to visit manufacturing sites in person.
-
Certification Verification: Ensure that suppliers possess relevant certifications and that these are current. Certifications should be verified through official channels to avoid any discrepancies.
What Are the Nuances of Quality Control and Certification for International B2B Buyers?
Understanding the nuances of quality control and certification can be particularly important for B2B buyers in diverse markets. Here are some considerations:
-
Regional Standards Variability: Different regions may have varying standards for filter paper quality. For example, European standards may differ significantly from those in Africa or South America. Buyers should ensure that suppliers can meet the specific regulatory requirements of their target market.
-
Documentation and Traceability: Ensuring that all quality control processes are documented and traceable is crucial. This not only aids in compliance but also builds trust between suppliers and buyers.
-
Cultural Sensitivity in Communication: When dealing with suppliers from different regions, being culturally sensitive in communication can foster better relationships and clearer understanding of quality expectations.
-
Market-Specific Requirements: Some industries may have unique requirements for filter paper, such as food-grade certifications or pharmaceutical-grade specifications. Buyers should communicate these requirements clearly to suppliers to ensure compliance.
By focusing on these aspects of manufacturing processes and quality assurance, B2B buyers can make informed decisions when sourcing filter paper, ultimately leading to enhanced operational efficiency and product reliability.
Practical Sourcing Guide: A Step-by-Step Checklist for ‘appearance of filter paper’
Introduction
Sourcing filter paper with the appropriate appearance is critical for various industrial applications, including pharmaceuticals, food processing, and environmental testing. This guide provides an actionable checklist for B2B buyers, particularly from Africa, South America, the Middle East, and Europe, to ensure they make informed purchasing decisions. By following these steps, you can confidently procure filter paper that meets your specific quality and performance standards.
Step 1: Define Your Technical Specifications
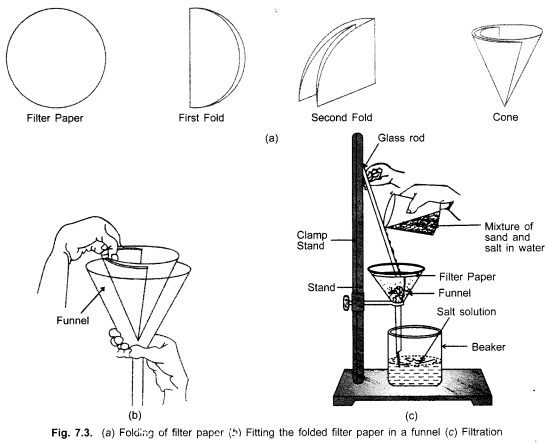
A stock image related to appearance of filter paper.
Before initiating the procurement process, clearly outline the technical specifications required for your filter paper. Consider factors such as pore size, thickness, and material composition, which will directly impact filtration efficiency and compatibility with your processes.
- Pore Size: Identify the filtration needs based on the application; smaller pores are suitable for fine particles.
- Material Composition: Determine whether you need cellulose-based or synthetic filter paper based on chemical resistance requirements.
Step 2: Research Market Trends and Standards
Understanding current market trends and compliance standards can guide your sourcing strategy effectively. Different regions may have specific certifications and quality benchmarks that filter paper must meet.
- Regulatory Compliance: Check if the paper adheres to ISO or ASTM standards relevant to your industry.
- Sustainability Trends: Consider the increasing demand for eco-friendly products and whether suppliers offer sustainable options.
Step 3: Evaluate Potential Suppliers
Conduct a thorough evaluation of potential suppliers to ensure they can meet your requirements. This includes assessing their manufacturing capabilities, quality control processes, and past performance.
- Company Profiles: Request detailed company profiles to understand their experience and expertise in producing filter paper.
- References and Case Studies: Ask for testimonials from other businesses in similar industries to gauge reliability and quality.
Step 4: Request Samples for Quality Assessment
Before making a bulk purchase, always request samples of the filter paper. Testing these samples in your specific applications will help you verify their performance and appearance.
- Physical Inspection: Examine the samples for any inconsistencies in appearance, such as color uniformity and texture.
- Performance Testing: Conduct filtration tests to ensure the paper meets your operational standards.
Step 5: Negotiate Pricing and Terms
Once you have selected a supplier and verified the quality of the filter paper, enter into negotiations regarding pricing and delivery terms.
- Volume Discounts: Inquire about pricing structures based on order volume to maximize cost efficiency.
- Delivery Schedules: Confirm lead times and shipping logistics to ensure timely delivery aligned with your production schedules.
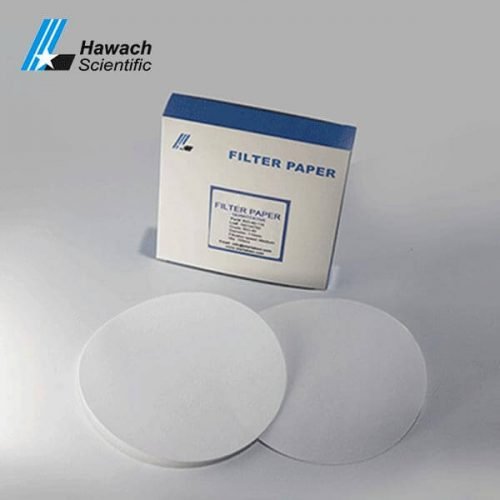
A stock image related to appearance of filter paper.
Step 6: Verify Supplier Certifications
Before finalizing your order, confirm that the supplier holds relevant certifications, such as ISO 9001 for quality management systems. This ensures that they adhere to industry standards and regulations.
- Quality Assurance: Certifications indicate a commitment to quality and can reduce the risk of receiving subpar products.
- Transparency: A certified supplier is more likely to provide transparent documentation regarding their products and processes.
Step 7: Establish a Communication Plan
After selecting a supplier, set up a clear communication plan for ongoing support and issue resolution. Effective communication helps in maintaining a strong partnership and addressing any potential concerns proactively.
- Regular Updates: Schedule periodic check-ins to discuss order status and any changes in requirements.
- Feedback Mechanism: Establish a channel for providing feedback on product performance to facilitate continuous improvement.
By following this checklist, B2B buyers can ensure they procure filter paper that not only meets their technical requirements but also aligns with their operational goals, thus enhancing overall efficiency and product quality.
Comprehensive Cost and Pricing Analysis for appearance of filter paper Sourcing
What Are the Key Cost Components in Filter Paper Sourcing?
When sourcing filter paper, understanding the cost structure is essential for international B2B buyers. The primary cost components include:
-
Materials: The quality and type of raw materials used in producing filter paper significantly influence costs. High-grade cellulose or specialized synthetic materials may incur higher prices but offer better performance.
-
Labor: Labor costs vary by region and can impact the overall price. In areas with higher wages, such as parts of Europe, labor costs might be a larger portion of the total price compared to regions with lower labor costs.
-
Manufacturing Overhead: This includes expenses related to facility maintenance, utilities, and equipment depreciation. Efficient manufacturing processes can help minimize these costs.
-
Tooling: Custom tooling for specific filter paper designs can lead to significant upfront costs. However, investing in the right tooling can lead to cost savings in the long run by increasing production efficiency.
-
Quality Control (QC): Implementing rigorous QC processes is essential to ensure product consistency and compliance with international standards. This can add to the cost but is vital for maintaining quality.
-
Logistics: Transportation and storage costs can vary widely depending on the supplier’s location and the destination market. Understanding logistics expenses is crucial, especially for buyers in regions with less developed infrastructure.
-
Margin: Suppliers will typically add a margin to cover their risks and ensure profitability. This margin can be influenced by market demand and competition.
How Do Price Influencers Affect Filter Paper Costs?
Several factors can influence the pricing of filter paper, particularly for international buyers:
-
Volume and Minimum Order Quantity (MOQ): Higher order volumes often lead to discounts. Negotiating MOQs can be beneficial for buyers looking to optimize costs.
-
Specifications and Customization: Customized filter paper with specific dimensions or properties typically incurs higher costs. Buyers should assess whether customization is necessary for their applications.
-
Materials and Quality Certifications: The choice of materials and the presence of quality certifications (like ISO or FDA compliance) can significantly affect pricing. High-quality materials may lead to higher initial costs but can offer better longevity and performance.
-
Supplier Factors: Reputation, reliability, and financial stability of suppliers can also influence pricing. Established suppliers may charge more due to their proven track record.
-
Incoterms: The agreed terms of delivery (Incoterms) play a crucial role in determining the final price. Buyers should clarify whether costs include shipping, insurance, and tariffs to avoid unexpected expenses.
What Tips Can Help Buyers Optimize Costs in Filter Paper Sourcing?
To achieve cost-efficiency in filter paper sourcing, international buyers should consider the following strategies:
-
Negotiation Techniques: Establishing strong relationships with suppliers can lead to better negotiation outcomes. Understanding market trends and being prepared with competitive quotes can strengthen your position.
-
Total Cost of Ownership (TCO): Beyond the purchase price, consider the total cost of ownership, which includes maintenance, disposal, and potential performance-related costs. A lower initial price may not always yield the best value.
-
Market Research: Conduct thorough market research to compare prices and quality across different suppliers. This helps in identifying fair pricing and establishing benchmarks.
-
Regional Considerations: Buyers from Africa, South America, the Middle East, and Europe should be aware of regional variations in pricing and supply chain dynamics. Understanding local market conditions can provide leverage in negotiations.
-
Evaluate Supplier Partnerships: Building long-term partnerships with suppliers can lead to more favorable pricing and consistent quality. Consider suppliers who can offer both competitive prices and reliable service.
Are Indicative Prices Reliable for B2B Buyers?
While indicative prices can provide a general understanding of market trends, they should be approached with caution. Prices can fluctuate based on numerous factors, including raw material costs, geopolitical developments, and currency fluctuations. Always request detailed quotes tailored to specific requirements to ensure accuracy in budgeting and planning.
Alternatives Analysis: Comparing appearance of filter paper With Other Solutions
Introduction: Exploring Alternatives to Filter Paper
When it comes to filtration in laboratory and industrial settings, the appearance of filter paper is often the go-to solution for many. However, international B2B buyers should consider alternative solutions that may better meet their specific requirements. Different methods can offer varying levels of performance, cost-effectiveness, and ease of use. This section evaluates the appearance of filter paper against two viable alternatives: membrane filters and cartridge filters, providing insights for buyers from Africa, South America, the Middle East, and Europe.
Comparison Table: Evaluating Filter Paper and Alternatives
Comparison Aspect | Appearance Of Filter Paper | Membrane Filters | Cartridge Filters |
---|---|---|---|
Performance | Good for general filtration, limited in particle retention | High precision, can filter very fine particles | Moderate to high efficiency, suitable for bulk filtration |
Cost | Generally low-cost | Higher initial investment, but long-lasting | Moderate to high cost, depending on material and brand |
Ease of Implementation | Simple to use, minimal setup required | Requires specific equipment and calibration | Requires installation, but often user-friendly |
Maintenance | Disposable, no maintenance required | Regular cleaning and replacement needed | Regular replacement, but less frequent than filter paper |
Best Use Case | Routine laboratory filtration | High-stakes applications needing sterile conditions | Industrial processes requiring high-volume filtration |
Detailed Breakdown of Alternatives
What are Membrane Filters and Their Benefits?
Membrane filters are thin layers of material that can filter particles at the micro or nano scale. They are particularly effective in applications requiring sterile filtration, such as in pharmaceuticals and food production. The precision of membrane filters allows for the removal of bacteria and other contaminants, making them ideal for high-stakes environments. However, they come with a higher initial cost and require specific equipment for implementation and maintenance. Regular cleaning and careful handling are essential to maintain performance, which may increase operational complexity.
How Do Cartridge Filters Compare?
Cartridge filters are cylindrical filters designed for high-volume applications. They offer moderate to high efficiency and are often used in industrial processes, such as water treatment and oil filtration. One of the key advantages of cartridge filters is their longevity; they typically need to be replaced less frequently than filter paper, which can result in cost savings over time. However, the initial investment can be moderate to high, depending on the materials used. While installation is generally straightforward, it may require some technical knowledge, which could be a barrier for some users.
Conclusion: Choosing the Right Filtration Solution
Selecting the right filtration solution depends on a variety of factors, including the specific application, budget constraints, and ease of use. While the appearance of filter paper is a reliable and cost-effective option for many routine tasks, alternatives like membrane and cartridge filters offer distinct advantages for specialized needs. B2B buyers should assess their operational requirements, performance expectations, and maintenance capabilities before making a decision. By understanding the strengths and weaknesses of each filtration method, businesses can make informed choices that enhance efficiency and productivity in their processes.
Essential Technical Properties and Trade Terminology for appearance of filter paper
What Are the Key Technical Properties of Filter Paper Appearance?
When selecting filter paper for various applications, understanding its technical properties is essential. Here are several critical specifications that international B2B buyers should consider:
1. Material Grade
Material grade refers to the quality and composition of the filter paper. Common materials include cellulose, glass fiber, and synthetic polymers. The choice of material affects the filter’s strength, porosity, and chemical compatibility. For instance, cellulose filter paper is widely used for general laboratory filtration, while glass fiber is preferred for high-temperature applications. Buyers must select the appropriate material grade to ensure optimal performance in their specific use cases.
2. Basis Weight
Basis weight is defined as the weight of the filter paper per unit area, typically measured in grams per square meter (gsm). This property is crucial because it influences the paper’s thickness, strength, and filtration efficiency. Higher basis weight often indicates more robust paper, which can handle larger volumes of liquids without tearing. Buyers should assess the required basis weight based on their filtration needs to avoid costly operational issues.
3. Pore Size
Pore size determines the size of particles that can be effectively filtered. It is measured in micrometers (µm) and is critical for applications requiring specific filtration precision. For example, a pore size of 0.45 µm is standard for microbiological analysis, while larger pore sizes may suffice for less demanding tasks. Understanding the required pore size helps buyers choose the right filter paper, ensuring quality results in their processes.
4. Flow Rate
Flow rate indicates how quickly a liquid can pass through the filter paper, often expressed in milliliters per minute (mL/min). This property is particularly important for processes where time efficiency is crucial. A higher flow rate can speed up operations, but it might compromise the filtration quality. Buyers should balance flow rate with the required filtration effectiveness to optimize their workflow.
5. Chemical Resistance
Chemical resistance refers to the filter paper’s ability to withstand exposure to various solvents and chemicals without degrading. This property is essential for industries such as pharmaceuticals and chemical manufacturing, where specific chemicals are used in processes. Buyers should verify chemical compatibility to ensure that the filter paper will perform reliably under their operational conditions.
What Trade Terminology Should B2B Buyers Know for Filter Paper?
Familiarity with industry jargon can significantly enhance communication and negotiation processes. Here are key terms that buyers should understand:
1. OEM (Original Equipment Manufacturer)
OEM refers to companies that produce parts or equipment that may be marketed by another manufacturer. In the context of filter paper, an OEM may supply filter media for a specific brand of laboratory equipment. Understanding OEM relationships can help buyers identify reliable sources and ensure product compatibility.
2. MOQ (Minimum Order Quantity)
MOQ is the smallest quantity of a product that a supplier is willing to sell. This term is crucial for B2B buyers, as it directly impacts inventory levels and cash flow. Understanding MOQs helps buyers plan their purchases effectively, ensuring they meet supply needs without overcommitting resources.
3. RFQ (Request for Quotation)
An RFQ is a document sent to suppliers to solicit price quotes for specific products or services. For filter paper, an RFQ can detail specifications such as material grade, basis weight, and quantity. Crafting a comprehensive RFQ enables buyers to receive accurate quotes, facilitating better decision-making.
4. Incoterms (International Commercial Terms)
Incoterms are standardized trade terms that define the responsibilities of buyers and sellers in international transactions. They specify who is responsible for shipping, insurance, and tariffs. Familiarity with Incoterms helps B2B buyers understand shipping logistics and avoid unexpected costs when importing filter paper from different regions.
5. Lead Time
Lead time refers to the amount of time it takes from placing an order to receiving the product. Understanding lead times is essential for inventory management and production planning. Buyers should always inquire about lead times to ensure timely delivery of filter paper, especially in industries with strict deadlines.
By grasping these essential properties and trade terms, international B2B buyers can make informed decisions when sourcing filter paper, ensuring they choose products that meet their specific needs and operational requirements.
Navigating Market Dynamics and Sourcing Trends in the appearance of filter paper Sector
What Are the Current Market Dynamics and Key Trends in the Appearance of Filter Paper Sector?
The appearance of filter paper market is currently shaped by several global drivers that influence sourcing decisions for B2B buyers across Africa, South America, the Middle East, and Europe. A major trend is the increasing demand for high-quality filtration solutions, particularly in industries such as pharmaceuticals, food and beverage, and environmental testing. This demand is fueled by stricter regulatory standards and a growing awareness of product quality among consumers.
Emerging technologies, such as advanced filtration methods and innovative material compositions, are also transforming the landscape. B2B buyers are increasingly looking for suppliers that offer customized solutions tailored to specific applications, which can enhance operational efficiency and reduce costs. The rise of e-commerce platforms and digital marketplaces is making it easier for international buyers to connect with suppliers, facilitating quicker decision-making processes.
Additionally, geopolitical factors and trade regulations are becoming significant considerations. Buyers need to remain aware of tariffs, import restrictions, and local market conditions that may affect sourcing strategies. As companies aim to diversify their supply chains to mitigate risks, sourcing from emerging markets in Africa and South America is gaining traction, creating opportunities for competitive pricing and unique product offerings.
How Can Sustainability and Ethical Sourcing Be Integrated into B2B Practices?
Sustainability has become a critical concern in the appearance of filter paper sector. The environmental impact of production processes, from raw material sourcing to waste management, is under scrutiny. B2B buyers are increasingly prioritizing suppliers that demonstrate a commitment to sustainable practices. This includes using renewable resources, reducing water and energy consumption during production, and minimizing waste.
Ethical sourcing is equally important. Buyers are encouraged to verify that their suppliers adhere to fair labor practices and maintain transparency throughout their supply chains. Certifications such as FSC (Forest Stewardship Council) and ISO 14001 can serve as indicators of a supplier’s commitment to sustainability and ethical sourcing. By choosing suppliers with these certifications, international buyers not only enhance their corporate responsibility but also align with the growing consumer demand for environmentally friendly products.
Moreover, integrating sustainability into sourcing strategies can lead to cost savings in the long run. For instance, adopting eco-friendly materials may reduce energy costs and improve brand loyalty among environmentally-conscious consumers. In this context, B2B buyers should actively engage with suppliers to explore sustainable alternatives that do not compromise on quality.
What is the Brief Evolution of the Appearance of Filter Paper Sector?
The appearance of filter paper has evolved significantly over the past century, transitioning from basic filtration solutions to sophisticated products designed for specialized applications. Initially, filter paper was primarily used in laboratories for simple filtration tasks. However, advancements in technology and materials have led to the development of high-performance filter papers that cater to diverse industries, including pharmaceuticals, food processing, and environmental monitoring.
In recent decades, the sector has seen a shift towards more sustainable practices, reflecting broader societal changes in consumer behavior and regulatory requirements. This evolution has prompted manufacturers to innovate continuously, focusing on enhancing the quality and functionality of filter paper products. Today, B2B buyers benefit from a wide array of options that meet stringent quality standards while aligning with sustainability goals, marking a significant progression in the industry’s landscape.
Frequently Asked Questions (FAQs) for B2B Buyers of appearance of filter paper
-
How do I choose the right type of filter paper for my application?
Choosing the right filter paper depends on various factors, including the type of material being filtered, the desired particle retention rate, and the chemical compatibility with the substances involved. For instance, if you’re filtering fine particulates, look for filter paper with a lower pore size. Additionally, consider the thickness and flow rate; thicker papers may provide better strength but slower filtration. Collaborating with suppliers who can offer samples and technical data sheets can help you make an informed decision tailored to your specific needs. -
What are the key characteristics of high-quality filter paper?
High-quality filter paper should possess consistent thickness, uniform pore size, and high tensile strength. Look for papers that are chemically resistant to the substances you will be filtering, ensuring no contaminants leach into your samples. Additionally, evaluate the retention rate and flow rate, as these will impact your filtration efficiency. Supplier certifications, such as ISO standards, can also indicate the quality and reliability of the product. -
Can filter paper be customized to meet specific requirements?
Yes, many manufacturers offer customization options for filter paper. This can include specific dimensions, pore sizes, and even special coatings for chemical resistance. When sourcing, communicate your requirements clearly to suppliers and request samples of customized products. This will help ensure that the filter paper meets your precise application needs while also maintaining quality standards. -
What is the minimum order quantity (MOQ) for filter paper?
The MOQ for filter paper can vary significantly by supplier and the specific type of filter paper you require. Typically, manufacturers may set an MOQ ranging from a few hundred to several thousand sheets. It’s essential to discuss your needs with potential suppliers, especially if you’re a smaller business or just starting. Some suppliers may be willing to accommodate lower MOQs, particularly if you are open to accepting alternative options or product lines. -
What payment terms should I expect when sourcing filter paper internationally?
Payment terms can differ widely based on the supplier’s policies and your negotiation skills. Common terms include advance payment, net 30, or letters of credit for larger orders. International buyers should be cautious and consider escrow services or payment protection plans to mitigate risks. Establishing a solid relationship with suppliers can also lead to more favorable payment terms over time. -
How do I assess the reliability of a filter paper supplier?
To assess a supplier’s reliability, start by researching their reputation through online reviews, industry forums, and trade references. Request documentation of certifications and quality assurance processes to ensure they meet international standards. Additionally, consider visiting their production facilities if feasible, or request a third-party audit. Building a relationship with suppliers through communication can also provide insights into their reliability and customer service. -
What logistics considerations should I keep in mind when importing filter paper?
When importing filter paper, consider shipping costs, customs duties, and lead times. Ensure that the supplier can handle export logistics and provide necessary documentation for customs clearance. Evaluate the shipping methods available, as air freight may be faster but more expensive compared to sea freight. Additionally, plan for potential delays in delivery and factor that into your production schedule to avoid disruptions. -
How can I ensure quality assurance for imported filter paper?
To ensure quality assurance for imported filter paper, establish clear quality standards with your supplier before placing an order. Request samples for testing before full-scale production, and consider third-party inspections during manufacturing. Additionally, keep an open line of communication with your supplier to address any quality concerns promptly. Implementing a quality control process upon receipt of goods will help maintain product consistency and reliability in your operations.
Important Disclaimer & Terms of Use
⚠️ Important Disclaimer
The information provided in this guide, including content regarding manufacturers, technical specifications, and market analysis, is for informational and educational purposes only. It does not constitute professional procurement advice, financial advice, or legal advice.
While we have made every effort to ensure the accuracy and timeliness of the information, we are not responsible for any errors, omissions, or outdated information. Market conditions, company details, and technical standards are subject to change.
B2B buyers must conduct their own independent and thorough due diligence before making any purchasing decisions. This includes contacting suppliers directly, verifying certifications, requesting samples, and seeking professional consultation. The risk of relying on any information in this guide is borne solely by the reader.
Strategic Sourcing Conclusion and Outlook for appearance of filter paper
In navigating the complexities of sourcing filter paper, international B2B buyers must prioritize strategic sourcing to optimize their procurement processes. The quality, consistency, and performance of filter paper can significantly impact operational efficiency, particularly in sectors like pharmaceuticals, food and beverage, and environmental testing. By establishing strong relationships with reputable suppliers and focusing on transparent supply chains, buyers can ensure they receive high-quality products that meet their specific requirements.
How Can Buyers Leverage Strategic Sourcing for Competitive Advantage?
Understanding market trends and regional variations is crucial for buyers in Africa, South America, the Middle East, and Europe. Engaging in detailed market analysis can reveal potential supply challenges and opportunities for cost savings. Furthermore, fostering collaborations with local suppliers can enhance product availability and reduce lead times, ultimately driving greater value for businesses.
What Is the Future Outlook for Filter Paper Sourcing?
As industries evolve, the demand for innovative filter paper solutions is expected to rise. Buyers should remain proactive in exploring new technologies and sustainable practices within the filter paper market. By doing so, they can not only meet regulatory standards but also appeal to environmentally conscious consumers.
In conclusion, embracing strategic sourcing will empower international B2B buyers to navigate the evolving landscape of filter paper procurement successfully. Start evaluating your sourcing strategies today to unlock new opportunities and ensure your business stays ahead in this competitive market.