Enhance Efficiency: The Ultimate Tablet Cutting Device Guide (2025)
Introduction: Navigating the Global Market for tablet cutting device
In today’s rapidly evolving pharmaceutical landscape, sourcing a reliable tablet cutting device can pose significant challenges for B2B buyers, particularly in emerging markets across Africa, South America, the Middle East, and Europe. The need for precision and efficiency in tablet production is paramount, as businesses strive to meet increasing consumer demands while ensuring compliance with stringent regulatory standards. This guide aims to provide international buyers with a comprehensive overview of tablet cutting devices, exploring various types, applications, and the crucial aspects of supplier vetting.
As you navigate this global market, you will find insights into cost considerations, technological advancements, and best practices that empower informed purchasing decisions. Whether you are a pharmaceutical manufacturer in Colombia seeking to enhance production efficiency or a distributor in Spain looking to diversify your equipment portfolio, understanding the nuances of tablet cutting devices will enable you to make strategic choices that align with your operational goals.
By leveraging the information contained within this guide, you will be better equipped to select the right tablet cutting device that meets your specific needs, ultimately driving productivity and ensuring the quality of your pharmaceutical products.
Understanding tablet cutting device Types and Variations
Type Name | Key Distinguishing Features | Primary B2B Applications | Brief Pros & Cons for Buyers |
---|---|---|---|
Manual Tablet Cutter | Hand-operated, portable, simple design | Small pharmacies, clinics | Pros: Low cost, easy to use. Cons: Labor-intensive, less precise. |
Electric Tablet Cutter | Automated cutting, adjustable settings for different tablet sizes | Large-scale manufacturers, research labs | Pros: High precision, efficient for bulk cutting. Cons: Higher initial investment, requires maintenance. |
Tablet Splitter | Designed specifically for splitting tablets into smaller doses | Hospitals, long-term care facilities | Pros: Accurate dosing, improves medication adherence. Cons: Limited to specific tablet types. |
Multi-functional Tablet Cutter | Combines cutting, crushing, and splitting functionalities | Compounding pharmacies, specialty pharmacies | Pros: Versatile, saves space and time. Cons: More complex operation, higher price point. |
Pill Press and Cutter | Integrates tablet pressing with cutting capabilities | Pharmaceutical manufacturing | Pros: Streamlined production, consistent tablet quality. Cons: Requires significant investment, complex setup. |
What Are the Characteristics of Manual Tablet Cutters?
Manual tablet cutters are simple, hand-operated devices that allow users to cut tablets into smaller pieces. They are typically portable and designed for ease of use, making them suitable for small pharmacies and clinics where space and budget may be limited. B2B buyers should consider the labor intensity of these devices, as they rely on manual operation, which can affect efficiency. However, their low cost and straightforward design can be advantageous for smaller operations.
How Do Electric Tablet Cutters Enhance Efficiency?
Electric tablet cutters are automated machines that offer adjustable settings for cutting various tablet sizes. They are ideal for large-scale manufacturers and research labs where high precision and efficiency are critical. The primary purchasing considerations for B2B buyers include the initial investment and ongoing maintenance costs. While the automation can significantly reduce labor costs and increase production rates, buyers must ensure they have the technical support and resources to maintain these machines.
Why Choose a Tablet Splitter for Medication Management?
Tablet splitters are specialized devices designed to accurately split tablets into smaller doses, making them particularly useful in hospitals and long-term care facilities. They enhance medication adherence by allowing for precise dosing tailored to patient needs. When considering a tablet splitter, B2B buyers should evaluate the compatibility of the device with various tablet types and the potential for improving patient outcomes through better medication management.
What Makes Multi-functional Tablet Cutters Valuable?
Multi-functional tablet cutters combine cutting, crushing, and splitting capabilities into one device, making them ideal for compounding and specialty pharmacies. These machines save space and time, providing versatility in handling different dosage forms. Buyers should weigh the benefits of having a single device that performs multiple functions against the complexity of operation and higher price point. This option is particularly attractive for pharmacies looking to optimize their workflow.
How Do Pill Press and Cutters Streamline Production?
Pill press and cutters are integrated machines that facilitate both tablet pressing and cutting, making them essential for pharmaceutical manufacturing. These devices ensure consistent tablet quality and streamline production processes. B2B buyers should consider the significant investment required for such equipment, as well as the complexity of setup and operation. However, for large manufacturers, the efficiency gains and quality assurance they provide can justify the costs involved.
Related Video: LOKLiK Crafter Cutting Machine: Setup and Demo in English
Key Industrial Applications of tablet cutting device
Industry/Sector | Specific Application of tablet cutting device | Value/Benefit for the Business | Key Sourcing Considerations for this Application |
---|---|---|---|
Pharmaceutical | Precise dosage division of tablets | Ensures accurate medication delivery, reducing waste and errors | Compliance with health regulations, machine precision, and maintenance |
Nutraceuticals | Customizing supplement sizes for specific markets | Meets diverse consumer needs, enhancing market reach | Material compatibility, scalability, and ease of operation |
Food and Beverage | Portioning functional food tablets | Improves product consistency and consumer satisfaction | Food safety standards, ease of cleaning, and operational efficiency |
Veterinary Medicine | Cutting tablets for animal health products | Tailors dosages for various animal sizes, improving treatment efficacy | Regulatory compliance, training for operators, and durability |
Research and Development | Preparing tablets for clinical trials | Facilitates accurate testing and data collection | Customization capabilities, speed of production, and quality control |
How is the Tablet Cutting Device Used in the Pharmaceutical Industry?
In the pharmaceutical sector, a tablet cutting device is essential for ensuring precise dosage division of tablets. By enabling the splitting of standard tablets into smaller, more manageable doses, manufacturers can cater to patients with varying dosage requirements. This application not only reduces medication waste but also minimizes the risk of overdosage, which is critical in maintaining patient safety. International buyers, especially from regions like Africa and South America, should prioritize sourcing devices that comply with strict health regulations and offer high precision to meet their specific needs.
What Role Does the Tablet Cutting Device Play in Nutraceuticals?
In the nutraceutical industry, tablet cutting devices are utilized to customize supplement sizes tailored for specific markets. This flexibility allows companies to meet diverse consumer preferences and regulatory requirements across different regions. For instance, a buyer in Colombia might need smaller tablet sizes for local consumers who prefer easier-to-swallow options. When sourcing these devices, businesses must consider material compatibility with various supplements, scalability for production, and ease of operation to ensure efficiency and compliance with health standards.
How Does the Tablet Cutting Device Benefit the Food and Beverage Sector?
The food and beverage industry employs tablet cutting devices for portioning functional food tablets, which are increasingly popular among health-conscious consumers. This application ensures product consistency and enhances consumer satisfaction by providing uniform sizes. International buyers, particularly in Europe, should focus on sourcing equipment that adheres to food safety standards and is easy to clean, as hygiene is paramount in food production. Additionally, operational efficiency is crucial to maintaining competitive pricing and meeting consumer demand.
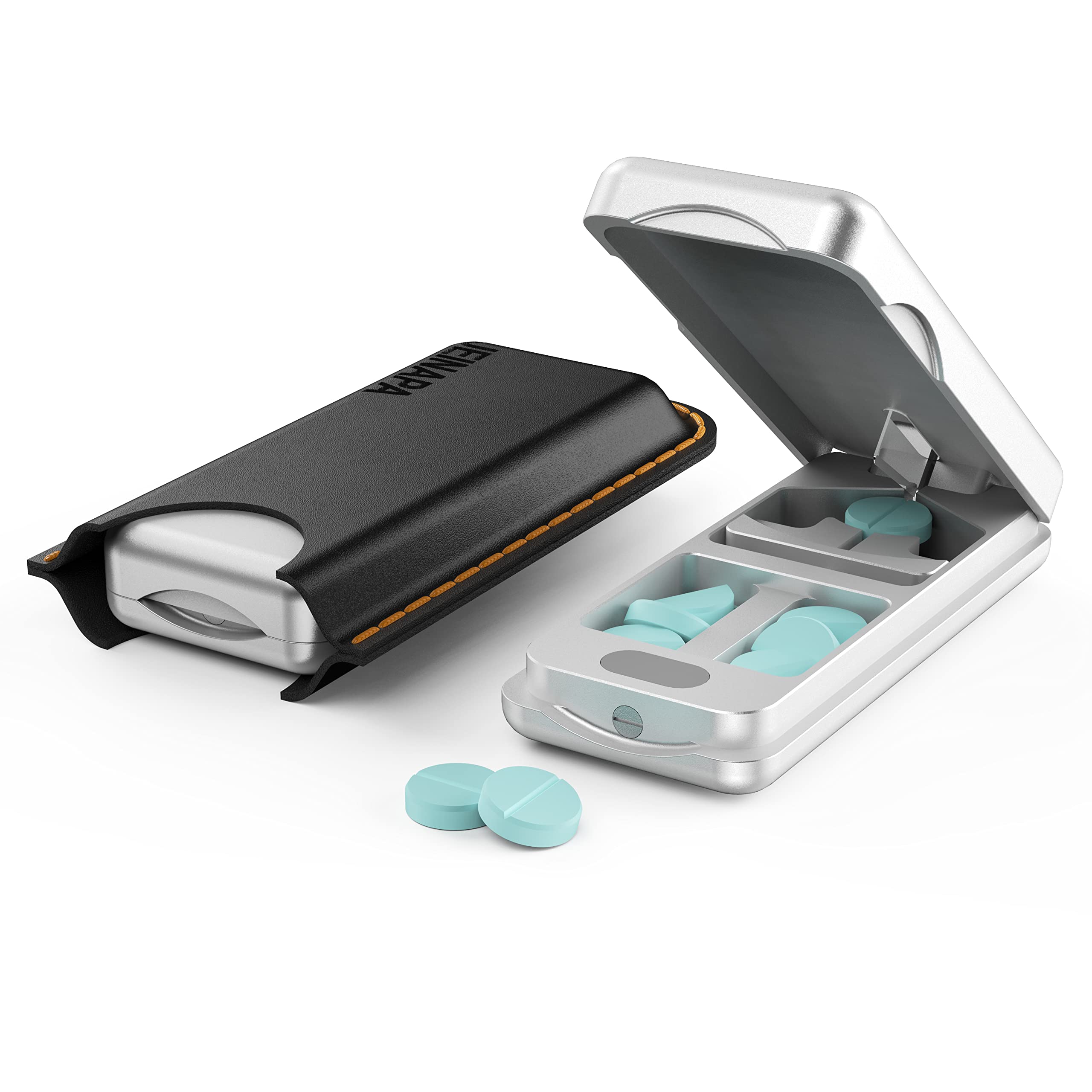
A stock image related to tablet cutting device.
How is the Tablet Cutting Device Used in Veterinary Medicine?
In veterinary medicine, tablet cutting devices are instrumental in tailoring dosages for animal health products. These devices allow veterinarians to adjust medication sizes according to different animal species and sizes, thereby improving treatment efficacy. Buyers from the Middle East should ensure that the devices they source comply with regulatory standards specific to veterinary products, and that operators are adequately trained to use the equipment safely and effectively.
Why is the Tablet Cutting Device Important for Research and Development?
In research and development, particularly in the pharmaceutical field, tablet cutting devices facilitate the preparation of tablets for clinical trials. By allowing researchers to create precise dosages for testing, these devices play a crucial role in data collection and analysis. For international buyers, especially those in Europe, it’s essential to consider the customization capabilities of the equipment, the speed of production, and stringent quality control measures to ensure reliable results in their studies.
Related Video: Prima Power Platino Fiber with 4kw Laser Cutting Demonstration
3 Common User Pain Points for ‘tablet cutting device’ & Their Solutions
Scenario 1: Difficulty in Achieving Consistent Tablet Sizes
The Problem: One of the most significant challenges B2B buyers face when using tablet cutting devices is achieving uniformity in tablet sizes. Inconsistent tablet sizes can lead to dosage errors, affecting product efficacy and regulatory compliance. This is particularly critical for pharmaceutical companies that must adhere to strict quality control standards. When tablets are cut unevenly, it can result in a loss of trust from customers and potential legal issues.
The Solution: To overcome this challenge, buyers should invest in advanced tablet cutting devices that feature precision cutting technology. Look for devices equipped with laser-guided systems or high-resolution imaging that ensures each tablet is cut to the exact specifications. Furthermore, implementing regular calibration and maintenance schedules for the cutting devices will help maintain their accuracy over time. Training staff on proper loading and operation techniques can also significantly reduce human error, ensuring that every cut is consistent. Establishing a quality control protocol that includes random sampling of tablet sizes can also help identify any inconsistencies early in the process.
Scenario 2: Inefficiency in Production Speed
The Problem: Another common pain point is the inefficiency in production speed when using tablet cutting devices. Slow cutting processes can lead to production bottlenecks, delaying product availability and increasing operational costs. This is especially detrimental in competitive markets where speed to market can determine success.
The Solution: To address inefficiencies, buyers should consider upgrading to high-capacity tablet cutting devices that can handle larger volumes without compromising on quality. Choosing devices with automated feeding systems can streamline the process, allowing for continuous operation and reducing downtime. Additionally, integrating the cutting device with existing production systems can enhance workflow efficiency. Implementing real-time monitoring systems can also help identify any slowdowns in the process, enabling quick adjustments. Training operators on best practices for loading and operating the machines can further optimize production speed.
Scenario 3: High Maintenance and Operating Costs
The Problem: Many B2B buyers encounter high maintenance and operational costs associated with tablet cutting devices. Frequent breakdowns, coupled with the costs of replacement parts and repairs, can significantly erode profit margins. This issue is compounded in regions with limited access to specialized service technicians, making timely repairs difficult and expensive.
The Solution: To mitigate these costs, buyers should prioritize purchasing tablet cutting devices from reputable manufacturers known for their reliability and lower total cost of ownership. Investing in devices with robust warranties and service agreements can also provide peace of mind and reduce unexpected expenses. Additionally, implementing a proactive maintenance schedule can prevent breakdowns before they occur. Training staff to perform basic maintenance tasks can also help minimize downtime and repair costs. Lastly, consider exploring options for leasing equipment, which can provide access to the latest technology without the burden of ownership costs.
Strategic Material Selection Guide for tablet cutting device
When selecting materials for tablet cutting devices, international B2B buyers must consider various factors that influence performance, cost, and compliance with industry standards. Below is an analysis of four common materials used in tablet cutting devices, focusing on their properties, advantages, disadvantages, and implications for buyers, particularly from regions such as Africa, South America, the Middle East, and Europe.
What Are the Key Properties of Stainless Steel in Tablet Cutting Devices?
Stainless steel is widely regarded for its excellent corrosion resistance, durability, and ability to withstand high temperatures and pressures. These properties make it suitable for environments where hygiene and longevity are critical, such as pharmaceutical manufacturing.
Pros and Cons:
– Pros: High durability, resistance to corrosion, easy to clean, and compliant with food and drug safety standards.
– Cons: Higher initial cost compared to other materials and can be complex to machine, which may increase manufacturing lead times.
Impact on Application:
Stainless steel is compatible with various media, including aggressive cleaning agents, making it ideal for environments requiring stringent hygiene practices.
Considerations for International Buyers:
Buyers should ensure compliance with ASTM and DIN standards, particularly in regions like Europe, where regulatory frameworks are stringent. Additionally, sourcing from local suppliers can mitigate import costs and lead times.
Why Is Plastic a Popular Choice for Tablet Cutting Devices?
Plastic, particularly high-performance polymers like polycarbonate or polypropylene, is increasingly used in tablet cutting devices due to its lightweight nature and versatility.
Pros and Cons:
– Pros: Lower cost, lightweight, and good chemical resistance.
– Cons: Generally less durable than metals, can warp under high temperatures, and may not withstand high-pressure applications.
Impact on Application:
Plastics can be suitable for applications where weight reduction is essential, but they may not be ideal for high-stress environments.
Considerations for International Buyers:
Buyers should verify that the chosen plastic complies with relevant safety and regulatory standards, especially in the pharmaceutical sector, where material safety is paramount.
How Does Aluminum Compare as a Material for Tablet Cutting Devices?
Aluminum is another popular choice due to its favorable strength-to-weight ratio and good corrosion resistance.
Pros and Cons:
– Pros: Lightweight, relatively low cost, and good machinability.
– Cons: Less durable than stainless steel and can be susceptible to corrosion in certain environments.
Impact on Application:
Aluminum is suitable for applications where weight is a concern, but its corrosion resistance may limit its use in more aggressive environments.
Considerations for International Buyers:
Buyers should be aware of the specific grades of aluminum that meet industry standards, such as JIS or ASTM, and consider local sourcing to reduce costs.
What Role Does Glass-Filled Nylon Play in Tablet Cutting Devices?
Glass-filled nylon is a composite material that combines nylon with glass fibers to enhance its mechanical properties.
Pros and Cons:
– Pros: High strength, good wear resistance, and excellent dimensional stability.
– Cons: Higher cost than standard nylon and can be more challenging to process.
Impact on Application:
This material is particularly effective in applications requiring high strength and durability, making it suitable for components subjected to wear.
Considerations for International Buyers:
Buyers should ensure that the glass-filled nylon used complies with industry standards, and they should consider the implications of sourcing such specialized materials, particularly in regions with less access to advanced composites.
Summary Table of Material Selection for Tablet Cutting Devices
Material | Typical Use Case for tablet cutting device | Key Advantage | Key Disadvantage/Limitation | Relative Cost (Low/Med/High) |
---|---|---|---|---|
Stainless Steel | Pharmaceutical manufacturing equipment | Excellent corrosion resistance and durability | Higher initial cost and complex machining | High |
Plastic | Lightweight tablet cutting devices | Low cost and lightweight | Less durable and can warp under heat | Low |
Aluminum | General tablet cutting applications | Lightweight and good machinability | Susceptible to corrosion in aggressive media | Medium |
Glass-Filled Nylon | High-wear tablet cutting components | High strength and wear resistance | Higher cost and processing challenges | Medium |
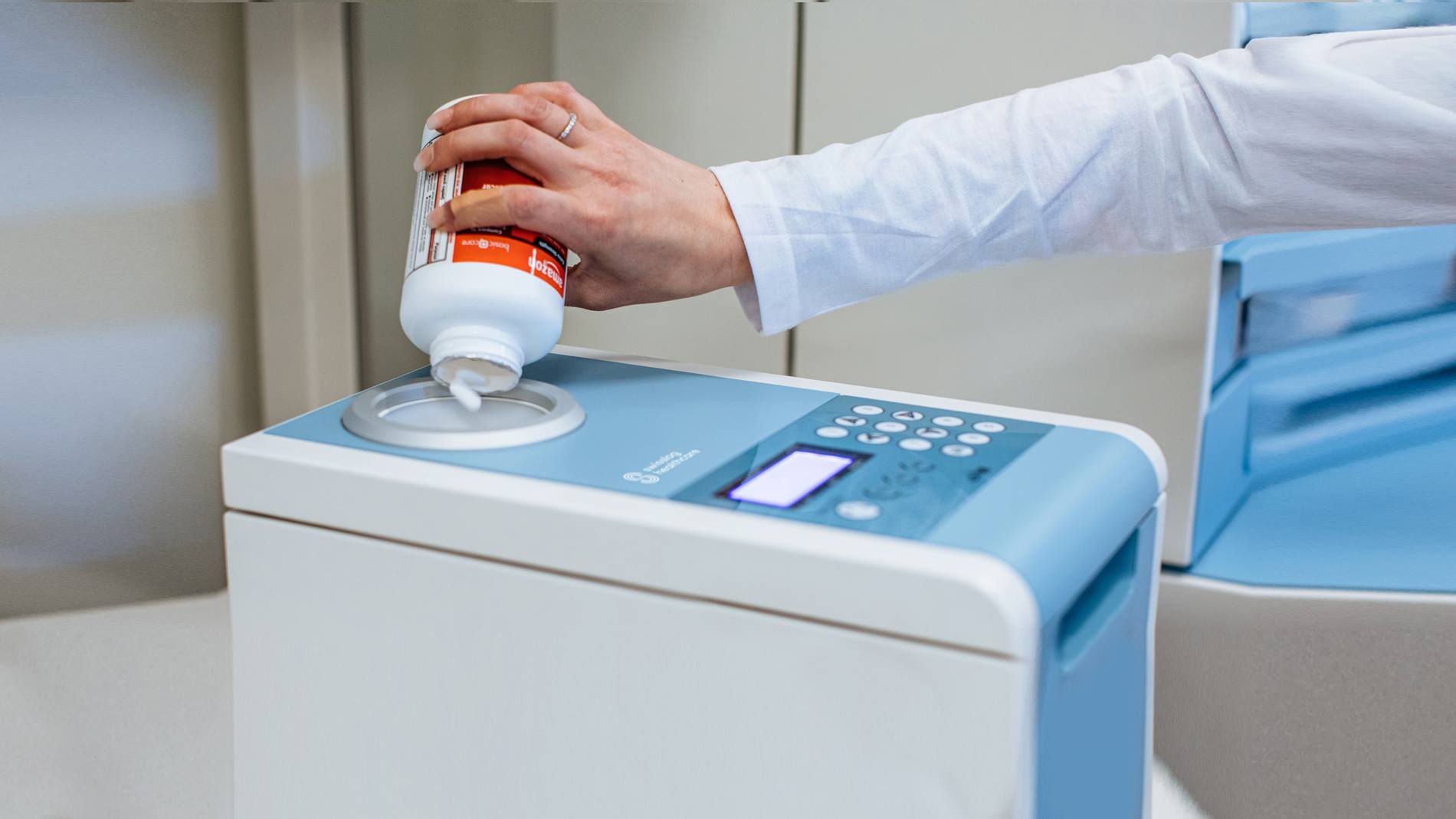
A stock image related to tablet cutting device.
This guide provides a comprehensive overview of material selection for tablet cutting devices, helping international B2B buyers make informed decisions based on performance, cost, and compliance with standards relevant to their specific regions.
In-depth Look: Manufacturing Processes and Quality Assurance for tablet cutting device
What Are the Main Stages of Manufacturing a Tablet Cutting Device?
The manufacturing process for tablet cutting devices involves several critical stages, each designed to ensure precision and quality. Understanding these stages is essential for B2B buyers looking to procure reliable equipment.
1. Material Preparation: How Are Raw Materials Selected and Processed?
The first step in manufacturing a tablet cutting device is the selection and preparation of raw materials. Manufacturers typically use high-grade stainless steel or medical-grade plastics for the cutting blades and housing components. The materials are sourced from certified suppliers who meet international quality standards.
Once selected, the materials undergo rigorous inspections to ensure they meet specifications for durability and safety. This may include testing for tensile strength, corrosion resistance, and biocompatibility, especially if the device will be used in medical settings.
2. Forming: What Techniques Are Used to Shape the Device Components?
The forming stage employs various techniques to shape the components of the tablet cutting device. Common methods include:
-
CNC Machining: Computer Numerical Control (CNC) machines are utilized to precisely cut and shape metal and plastic parts. This method ensures high accuracy and repeatability, which is crucial for maintaining the device’s performance.
-
Injection Molding: For plastic components, injection molding is often used. This process allows for the mass production of uniform parts, which can significantly reduce manufacturing costs and time.
-
Stamping: Metal parts may be produced using stamping techniques, where sheets of metal are cut and formed into desired shapes under high pressure.
How Is Assembly Conducted in Tablet Cutting Device Manufacturing?
The assembly stage is where individual components come together to form the final product. This stage typically involves:
-
Component Integration: All parts, including the cutting mechanism, housing, and safety features, are assembled. This requires skilled technicians who ensure that each piece fits correctly and functions as intended.
-
Quality Checks: During assembly, manufacturers perform in-line inspections to catch any defects early in the process. This helps to minimize waste and rework later in production.
What Finishing Techniques Are Applied to Ensure Quality?
The finishing stage focuses on enhancing the device’s appearance and performance. Key techniques include:
-
Surface Treatment: Components may undergo treatments such as anodizing or powder coating to improve corrosion resistance and aesthetics.
-
Polishing: Cutting surfaces are polished to achieve a sharp edge, which is crucial for effective tablet cutting.
-
Final Assembly: After finishing, the device undergoes final assembly, where it is tested for operational functionality.
What International Standards Are Relevant for Quality Assurance?
Quality assurance is critical in the manufacturing of tablet cutting devices, particularly for international buyers. Key standards include:
-
ISO 9001: This standard outlines the requirements for a quality management system (QMS). Manufacturers must demonstrate their ability to consistently provide products that meet customer and regulatory requirements.
-
CE Marking: For devices sold in Europe, CE marking indicates compliance with health, safety, and environmental protection standards. This certification is essential for market access in the EU.
-
API Standards: The Active Pharmaceutical Ingredients (API) standards are particularly relevant for devices used in pharmaceutical manufacturing. Compliance ensures that equipment meets the necessary safety and efficacy requirements.
What Are the Quality Control Checkpoints in Tablet Cutting Device Manufacturing?
Quality control (QC) is integral throughout the manufacturing process. Major checkpoints include:
-
Incoming Quality Control (IQC): At this stage, raw materials are inspected upon arrival to ensure they meet specifications before processing begins.
-
In-Process Quality Control (IPQC): During manufacturing, periodic checks are conducted to monitor compliance with operational standards. This includes testing the accuracy of CNC machining and the integrity of assembled components.
-
Final Quality Control (FQC): Once the device is fully assembled, it undergoes final testing to verify performance and safety. This may include functionality tests, durability assessments, and compliance checks with relevant standards.
How Can B2B Buyers Verify Supplier Quality Control?
For B2B buyers, particularly from regions such as Africa, South America, the Middle East, and Europe, verifying the quality control processes of suppliers is vital. Here are effective strategies:
-
Conducting Audits: Buyers should perform on-site audits of potential suppliers. This allows for firsthand assessment of manufacturing practices, quality control measures, and compliance with international standards.
-
Requesting Quality Reports: Suppliers should provide documentation that details their quality control processes, including inspection results and compliance certificates. This transparency is crucial for building trust.
-
Engaging Third-Party Inspectors: Utilizing third-party inspection services can provide an unbiased assessment of the supplier’s quality control practices. These inspectors can evaluate compliance with both international and industry-specific standards.
What Are the Nuances of Quality Control for International B2B Buyers?
International B2B buyers must navigate various nuances when it comes to quality control:
-
Cultural Differences in Quality Standards: Different regions may have varying expectations regarding quality and safety standards. Buyers should familiarize themselves with local regulations and industry practices to ensure compliance.
-
Language Barriers: Communication challenges can lead to misunderstandings regarding quality requirements. Buyers should consider working with suppliers that have multilingual capabilities or hiring local representatives.
-
Logistical Considerations: Importing equipment from different regions may involve additional quality checks upon arrival. Understanding local customs regulations and inspection requirements can prevent delays and ensure compliance.
Conclusion: Ensuring Quality in Tablet Cutting Device Procurement
By understanding the manufacturing processes, quality assurance standards, and verification methods, B2B buyers can make informed decisions when procuring tablet cutting devices. Ensuring that suppliers adhere to international quality standards not only protects buyers’ investments but also enhances the reliability and safety of the devices used in their operations.
Practical Sourcing Guide: A Step-by-Step Checklist for ‘tablet cutting device’
Introduction
Sourcing a tablet cutting device is a critical step for businesses in the pharmaceutical and nutraceutical industries, where precision and efficiency are paramount. This guide provides a practical, step-by-step checklist for international B2B buyers, particularly those from Africa, South America, the Middle East, and Europe. By following these steps, you can ensure that you select the right equipment to meet your operational needs and regulatory standards.
1. Define Your Technical Specifications
Before you begin sourcing, clearly define the technical specifications required for your tablet cutting device. Consider factors such as the size and type of tablets you will be cutting, desired output capacity, and any specific cutting features necessary for your production process. Having a detailed specification will help you communicate effectively with potential suppliers.
- Output Capacity: Determine the number of tablets you need to cut per hour.
- Tablet Size: Specify the dimensions of the tablets to ensure compatibility with the cutting device.
2. Research Potential Suppliers
Conduct thorough research to identify potential suppliers of tablet cutting devices. Look for companies with a solid reputation in the industry, positive customer reviews, and a proven track record of delivering high-quality equipment.
- Online Directories: Utilize platforms like Alibaba, ThomasNet, or industry-specific directories to compile a list of suppliers.
- Trade Shows: Attend industry trade shows to meet suppliers and see their products firsthand.
3. Evaluate Supplier Certifications
Verify that your shortlisted suppliers have the necessary certifications and comply with industry standards. This includes ISO certifications, CE marking, and any local regulatory approvals specific to your region.
- Quality Assurance: Certifications ensure that the equipment meets international quality standards.
- Regulatory Compliance: Compliance with local regulations is crucial for operational legality.
4. Request Detailed Quotations
Once you have a shortlist of suppliers, request detailed quotations that include pricing, shipping costs, and lead times. Ensure that the quotation covers all aspects of the device, including any additional components or services that may be necessary.
- Breakdown of Costs: A clear breakdown will help you compare offers effectively.
- Lead Times: Understanding delivery timelines is essential for planning your production schedule.
5. Assess After-Sales Support and Warranty
Evaluate the after-sales support offered by potential suppliers. This includes warranty terms, availability of spare parts, and the responsiveness of customer service. Reliable support can significantly impact the longevity and efficiency of your equipment.
- Warranty Length: A longer warranty period often indicates confidence in the product’s durability.
- Technical Support: Ensure that technical support is readily available in case of operational issues.
6. Conduct a Final Supplier Review
Before making a final decision, conduct a comprehensive review of your chosen supplier. This should include checking references from other businesses that have purchased similar devices. A well-informed decision will minimize risks and ensure that you are investing in a quality product.
- Client Testimonials: Seek feedback from clients in similar industries or regions to gauge satisfaction levels.
- Site Visits: If feasible, visiting the supplier’s facility can provide insight into their operations and quality control processes.
7. Finalize the Purchase Agreement
Once you have selected a supplier, finalize the purchase agreement, ensuring that all terms and conditions are clearly outlined. This should include payment terms, delivery schedules, and any penalties for non-compliance.
- Clear Terms: Clearly defined terms will help prevent misunderstandings and disputes.
- Payment Security: Consider using escrow services or letters of credit for added security in the transaction.
By following this step-by-step checklist, B2B buyers can effectively navigate the procurement process for a tablet cutting device, ensuring a successful investment that meets their operational needs.
Comprehensive Cost and Pricing Analysis for tablet cutting device Sourcing
What are the Key Cost Components for Sourcing a Tablet Cutting Device?
When sourcing a tablet cutting device, understanding the cost structure is critical for international B2B buyers. The main cost components include:
-
Materials: The quality and type of materials used in the device significantly influence costs. High-grade steel or specialized alloys may be more expensive but enhance durability and performance.
-
Labor: Labor costs vary by region. In countries with higher labor costs, such as those in Europe, the manufacturing expenses will be higher compared to regions in Africa or South America where labor may be cheaper.
-
Manufacturing Overhead: This includes indirect costs associated with production, such as utilities, rent, and equipment maintenance. Efficient manufacturing processes can help reduce these overhead costs.
-
Tooling: Custom tooling for specific designs can be a significant upfront cost. Understanding the tooling requirements early on can help in negotiating better terms with suppliers.
-
Quality Control (QC): Implementing rigorous QC processes ensures that the devices meet industry standards. However, these processes add to the overall cost, so it’s essential to balance quality and expenditure.
-
Logistics: Shipping and handling costs are crucial, especially for international buyers. Factors such as distance, shipping method, and customs duties can substantially affect the total costs.
-
Margin: Suppliers typically include a profit margin in their pricing. Understanding the expected margins can provide insight into pricing negotiation strategies.
How Do Price Influencers Impact the Cost of Tablet Cutting Devices?
Several factors can influence the pricing of tablet cutting devices, which international buyers must consider:
-
Volume/MOQ: The minimum order quantity (MOQ) affects pricing significantly. Higher volumes often lead to lower per-unit costs due to economies of scale.
-
Specifications and Customization: Customizing devices to meet specific needs can lead to increased costs. Buyers should evaluate whether standard models can meet their requirements to avoid unnecessary expenses.
-
Materials: As mentioned earlier, the choice of materials can affect pricing. Sustainable or specialized materials may incur higher costs but can provide long-term benefits.
-
Quality and Certifications: Devices that meet international certifications may come at a premium. However, investing in certified products can enhance reliability and reduce long-term risks.
-
Supplier Factors: The reputation and reliability of the supplier can influence costs. Established suppliers with a track record of quality may charge more, but they often provide better service and warranty options.
-
Incoterms: Understanding the Incoterms used in the contract is essential. Terms like FOB (Free on Board) or CIF (Cost, Insurance, and Freight) can affect the overall landed cost of the device.
What Are Essential Buyer Tips for Negotiating Tablet Cutting Device Prices?
For international B2B buyers, especially from Africa, South America, the Middle East, and Europe, here are actionable tips for effective negotiation and cost management:
-
Negotiate Early and Often: Establishing a good rapport with suppliers can lead to better pricing. Don’t hesitate to negotiate terms, especially on volume discounts or payment terms.
-
Focus on Cost-Efficiency: Look beyond the initial price. Consider the Total Cost of Ownership (TCO), which includes maintenance, operation, and potential downtime costs.
-
Understand Pricing Nuances: Pricing can vary significantly between regions due to labor and material costs. Be aware of these differences to make informed decisions.
-
Request Detailed Quotes: Always ask for itemized quotes to understand where costs are coming from. This transparency can help in negotiations and identifying areas for potential savings.
-
Leverage Local Knowledge: Engaging local agents or consultants can provide valuable insights into the market, helping to navigate cultural nuances and improve negotiation outcomes.
Disclaimer on Indicative Prices
Prices for tablet cutting devices can fluctuate based on market conditions, changes in material costs, and supplier pricing strategies. It is essential for buyers to conduct thorough research and obtain multiple quotes to ensure they are getting the best value for their investment.
Alternatives Analysis: Comparing tablet cutting device With Other Solutions
When exploring solutions for tablet cutting in the pharmaceutical and nutraceutical industries, it’s crucial to consider various alternatives alongside the tablet cutting device. Each option presents unique advantages and challenges that can significantly impact operational efficiency, cost-effectiveness, and product quality. Below is a comparison of the tablet cutting device against two viable alternatives: manual tablet splitting and automated capsule filling systems.
Comparison Aspect | Tablet Cutting Device | Manual Tablet Splitting | Automated Capsule Filling Systems |
---|---|---|---|
Performance | High precision and speed for cutting tablets into desired dosages. | Limited precision; relies on operator skill and can lead to inconsistent results. | High throughput; can fill and seal capsules quickly and accurately. |
Cost | Moderate initial investment with low long-term operating costs. | Low initial cost, but higher labor costs and inefficiencies. | High initial investment; however, cost savings in labor and time can be significant. |
Ease of Implementation | Requires training for optimal operation; setup can be complex. | Simple to implement with minimal training needed. | Complex installation process; requires skilled personnel for setup and maintenance. |
Maintenance | Regular maintenance needed for optimal performance; parts may need replacement. | Minimal maintenance required; however, can lead to wear and tear on manual tools. | Requires regular maintenance and calibration; downtime can be costly. |
Best Use Case | Ideal for high-volume production with precise dosage requirements. | Suitable for small-scale operations or pharmacies with low volume. | Best for large-scale production of capsules where speed and efficiency are paramount. |
What Are the Advantages and Disadvantages of Manual Tablet Splitting?
Manual tablet splitting is a straightforward approach where operators use handheld tools to divide tablets into smaller doses.
Pros:
– Cost-Effective: The initial investment is low, making it accessible for small businesses or pharmacies.
– Flexibility: Operators can adjust the splitting process based on specific tablet characteristics.
Cons:
– Inconsistency: The quality and accuracy of splits can vary significantly based on the operator’s skill level.
– Labor-Intensive: This method requires more time and labor, which can lead to inefficiencies, especially in high-demand situations.
How Do Automated Capsule Filling Systems Compare?
Automated capsule filling systems are designed to efficiently fill capsules with powders or granules, offering high-speed production capabilities.
Pros:
– Efficiency: These systems can produce large quantities of filled capsules in a short time, which is ideal for high-volume manufacturers.
– Precision: Automated systems ensure accurate dosage and consistent quality across all capsules.
Cons:
– High Initial Investment: The cost of purchasing and installing automated systems can be prohibitive for smaller businesses.
– Complexity: Requires skilled personnel for operation and maintenance, which can add to operational costs.
How Can B2B Buyers Choose the Right Solution?
When selecting the most appropriate solution for tablet cutting or capsule filling, B2B buyers should assess their specific operational needs, volume requirements, and budget constraints. For businesses with high production needs and a focus on precision, a tablet cutting device may offer the best balance of performance and cost-efficiency. Conversely, smaller operations may find manual splitting sufficient for their needs, while larger manufacturers may benefit from the speed and efficiency of automated systems. Evaluating these factors will help ensure that the chosen solution aligns with both current and future business objectives.
Essential Technical Properties and Trade Terminology for tablet cutting device
What Are the Essential Technical Properties of a Tablet Cutting Device?
When selecting a tablet cutting device, understanding its technical properties is crucial for B2B buyers, particularly in industries such as pharmaceuticals and nutraceuticals. Here are some key specifications to consider:
1. Material Grade
The material used in the construction of the tablet cutting device significantly affects its durability and performance. Stainless steel is commonly preferred due to its corrosion resistance and ease of cleaning, which is vital for maintaining hygiene standards in pharmaceutical environments. Buyers should ensure that the device meets industry standards, such as FDA regulations, to guarantee safety and reliability.
2. Tolerance Levels
Tolerance refers to the allowable deviation in the dimensions of the device components. In tablet cutting, precise tolerances are critical to ensure uniformity in tablet size and shape, which directly impacts dosage accuracy. A tolerance of ±0.1 mm is typically acceptable in high-quality devices. Understanding tolerance levels helps buyers assess the reliability of the equipment and the quality of the final product.
3. Cutting Speed
The cutting speed of a tablet cutting device, measured in tablets per minute (TPM), determines its efficiency and productivity. A higher cutting speed means that more tablets can be processed in a shorter time, enhancing production capacity. Buyers should evaluate their production needs and select a device that balances speed with the quality of the cut to avoid wastage.
4. Blade Material and Design
The blade material and design influence the cutting efficiency and longevity of the tablet cutting device. High-speed steel (HSS) and carbide blades are commonly used for their durability and sharpness. A well-designed blade can reduce friction and heat, ensuring cleaner cuts and extending the lifespan of the device. Buyers should inquire about blade specifications and replacement costs to gauge long-term operational expenses.
5. Safety Features
Safety features such as emergency stop buttons, blade guards, and automatic shut-off mechanisms are essential in tablet cutting devices. These features protect operators and minimize the risk of accidents. Buyers should prioritize devices that comply with safety standards and provide adequate training for operators to ensure a safe working environment.
What Common Trade Terms Should B2B Buyers Know When Purchasing Tablet Cutting Devices?
Understanding trade terminology can streamline the procurement process and enhance communication between buyers and suppliers. Here are some essential terms:
1. OEM (Original Equipment Manufacturer)
OEM refers to a company that produces parts or equipment that may be marketed by another manufacturer. In the context of tablet cutting devices, buyers may work with OEMs to customize machinery according to specific production needs. Understanding OEM relationships helps buyers negotiate better pricing and specifications.
2. MOQ (Minimum Order Quantity)
MOQ is the smallest quantity of a product that a supplier is willing to sell. For tablet cutting devices, MOQs can vary significantly based on the manufacturer and the complexity of the equipment. Buyers should be aware of MOQs to manage inventory effectively and optimize purchasing costs.
3. RFQ (Request for Quotation)
An RFQ is a document that solicits price quotes from suppliers for specific products or services. When considering a tablet cutting device, submitting an RFQ can help buyers obtain competitive pricing and terms from multiple suppliers. It’s a crucial step in the procurement process to ensure the best deal.
4. Incoterms (International Commercial Terms)
Incoterms are internationally recognized rules that define the responsibilities of buyers and sellers regarding shipping, insurance, and tariffs. Familiarity with Incoterms is essential for international buyers to understand their obligations and costs associated with importing tablet cutting devices.
5. CE Marking
CE marking indicates that a product complies with EU safety, health, and environmental protection standards. For buyers in Europe, ensuring that a tablet cutting device has CE marking is vital for compliance and marketability within the EU.
By understanding these technical properties and trade terms, B2B buyers can make informed decisions when purchasing tablet cutting devices, ultimately leading to improved operational efficiency and product quality.
Navigating Market Dynamics and Sourcing Trends in the tablet cutting device Sector
What Are the Key Market Dynamics and Trends in the Tablet Cutting Device Sector?
The tablet cutting device market is witnessing significant transformation driven by several global factors. The increasing demand for precision in pharmaceutical manufacturing and the growing prevalence of chronic diseases are key drivers propelling the market forward. As international B2B buyers from regions like Africa, South America, the Middle East, and Europe (notably Colombia and Spain) navigate this landscape, they should focus on emerging technologies such as automation and AI integration in tablet cutting processes. These innovations enhance efficiency, reduce waste, and improve product consistency, all of which are critical for maintaining competitive advantage in a fast-evolving market.
Additionally, the rise of e-commerce and digital procurement platforms is reshaping how international buyers source tablet cutting devices. These platforms facilitate easier access to suppliers across the globe, offering a wider array of products and competitive pricing. Furthermore, as regulatory frameworks around pharmaceutical manufacturing tighten, buyers must consider equipment that meets stringent compliance standards. This shift necessitates a deeper understanding of suppliers’ certifications and capabilities, ensuring that sourced equipment adheres to local and international regulations.
How Can International Buyers Address Sustainability and Ethical Sourcing in the Tablet Cutting Device Sector?
Sustainability is becoming increasingly crucial in the sourcing of tablet cutting devices. The environmental impact of manufacturing processes, including energy consumption and waste generation, is a growing concern for B2B buyers. As a result, the demand for suppliers who prioritize sustainable practices is on the rise. Buyers should look for manufacturers that utilize eco-friendly materials and processes, as well as those who have obtained ‘green’ certifications such as ISO 14001. These certifications signal a commitment to reducing environmental footprints and can enhance a company’s reputation in the eyes of environmentally conscious consumers.
Moreover, ethical sourcing is gaining traction as businesses recognize the importance of transparency in their supply chains. For international buyers, ensuring that suppliers adhere to ethical labor practices is paramount. This includes verifying that materials used in tablet cutting devices are sourced responsibly and that workers are treated fairly. Engaging with suppliers who prioritize ethical practices not only mitigates risk but can also lead to long-term partnerships that support corporate social responsibility initiatives.
What Is the Brief Evolution of the Tablet Cutting Device Market?
The tablet cutting device sector has evolved significantly over the past few decades, reflecting broader advancements in pharmaceutical manufacturing technology. Initially, tablet cutting was a manual process, often leading to inconsistencies in dosage and product quality. However, with the advent of automated cutting devices in the late 20th century, precision and efficiency dramatically improved. These innovations allowed for higher production rates and the ability to manufacture complex tablet shapes tailored to specific therapeutic needs.
Today, the market continues to advance with the integration of smart technologies, such as IoT-enabled devices that provide real-time monitoring and data analytics. This evolution not only enhances operational efficiency but also allows for better compliance with regulatory requirements. As the market progresses, international B2B buyers must stay informed about these advancements to make strategic sourcing decisions that align with their operational goals and regulatory obligations.
Frequently Asked Questions (FAQs) for B2B Buyers of tablet cutting device
-
How do I ensure the quality of a tablet cutting device before purchasing?
To ensure the quality of a tablet cutting device, start by requesting samples from potential suppliers. Evaluate the device’s performance, durability, and ease of use during a trial period. Additionally, verify certifications such as ISO or CE standards to confirm compliance with international quality norms. Engaging third-party quality assurance services can also provide independent assessments, ensuring the device meets your specifications and industry standards. -
What are the key features to consider when selecting a tablet cutting device?
When selecting a tablet cutting device, consider its cutting precision, speed, and capacity. Look for features such as adjustable cutting thickness, compatibility with various tablet sizes, and ease of maintenance. Additionally, assess the device’s safety features, user interface, and the availability of technical support from the manufacturer. Customization options for specific production needs can also be a critical factor. -
What is the average lead time for international shipping of tablet cutting devices?
The average lead time for international shipping of tablet cutting devices varies based on the origin and destination countries. Typically, shipping can take anywhere from 2 to 6 weeks, depending on factors such as customs clearance, shipping method (air or sea), and supplier processing times. To avoid delays, it’s advisable to confirm lead times with suppliers and consider potential disruptions in logistics networks, especially during peak seasons. -
How can I vet suppliers for tablet cutting devices effectively?
To vet suppliers effectively, conduct thorough research on their reputation and track record in the industry. Check for online reviews, request references from previous clients, and verify their business licenses and certifications. Additionally, consider visiting their manufacturing facility if possible or using virtual tours. Engaging with a local sourcing agent can also facilitate the vetting process and help establish trust.
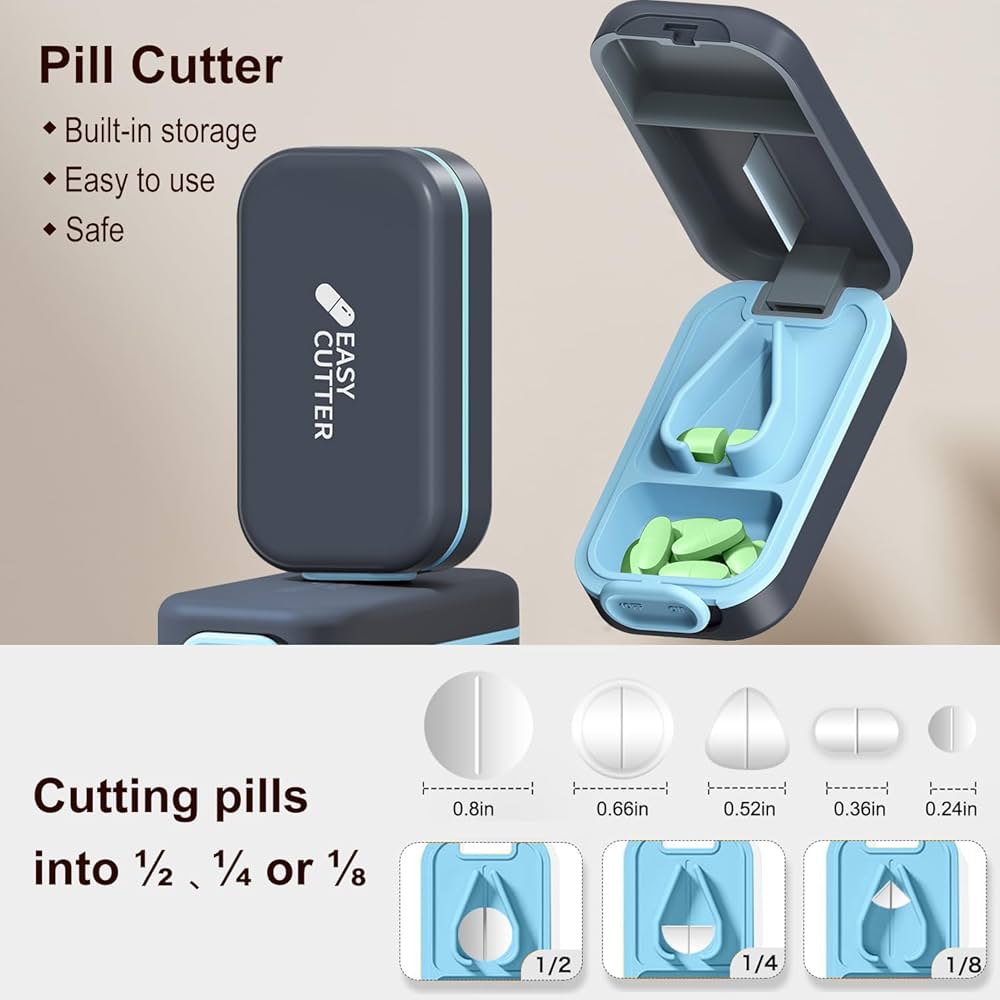
A stock image related to tablet cutting device.
-
What payment terms should I negotiate with suppliers of tablet cutting devices?
When negotiating payment terms, aim for flexibility that suits your cash flow. Common terms include a deposit (typically 30-50%) upfront, with the balance paid upon delivery or after inspection. Consider using secure payment methods such as letters of credit or escrow services to mitigate risks. Additionally, discussing volume discounts or payment milestones based on production stages can enhance your negotiation position. -
Are there customization options available for tablet cutting devices?
Many manufacturers offer customization options for tablet cutting devices to meet specific production requirements. Customizations can include modifications to cutting size, speed, and additional features such as automated feeding systems. It is essential to discuss your unique needs with the supplier during the initial stages of negotiation to ensure they can accommodate your specifications without significant lead time delays. -
What logistics considerations should I keep in mind when sourcing tablet cutting devices?
When sourcing tablet cutting devices, consider the logistics of transporting heavy machinery, including shipping costs, insurance, and customs duties. Ensure that your supplier has a reliable logistics partner for smooth transportation. Additionally, factor in the location of your facility and potential tariffs, especially when importing from different regions, which can significantly impact overall costs and delivery timelines. -
How do I handle warranty and after-sales service for tablet cutting devices?
Before finalizing your purchase, clarify the warranty terms and after-sales service offered by the supplier. A standard warranty should cover parts and labor for a specified period, typically 12 to 24 months. Inquire about the availability of spare parts and support services, such as training for your staff and technical assistance in case of malfunction. Establishing clear communication channels for after-sales support can enhance your operational efficiency and minimize downtime.
Important Disclaimer & Terms of Use
⚠️ Important Disclaimer
The information provided in this guide, including content regarding manufacturers, technical specifications, and market analysis, is for informational and educational purposes only. It does not constitute professional procurement advice, financial advice, or legal advice.
While we have made every effort to ensure the accuracy and timeliness of the information, we are not responsible for any errors, omissions, or outdated information. Market conditions, company details, and technical standards are subject to change.
B2B buyers must conduct their own independent and thorough due diligence before making any purchasing decisions. This includes contacting suppliers directly, verifying certifications, requesting samples, and seeking professional consultation. The risk of relying on any information in this guide is borne solely by the reader.
Strategic Sourcing Conclusion and Outlook for tablet cutting device
In conclusion, the strategic sourcing of tablet cutting devices presents a unique opportunity for international B2B buyers, particularly those operating in Africa, South America, the Middle East, and Europe. By leveraging advanced technologies and optimizing supply chains, businesses can enhance production efficiency and reduce operational costs. It is crucial for buyers to engage with suppliers who offer robust quality assurance and innovative solutions tailored to the specific needs of their markets.
How Can Strategic Sourcing Enhance Your Competitive Edge?
Investing in strategic sourcing not only streamlines procurement processes but also fosters long-term partnerships with suppliers, which is essential in today’s rapidly evolving marketplace. Buyers should prioritize suppliers who demonstrate a commitment to sustainability and compliance with international regulations, ensuring that their sourcing practices align with global standards.
What’s Next for International B2B Buyers?
As the demand for efficient and precise tablet cutting devices grows, now is the time for buyers to reevaluate their sourcing strategies. Explore new partnerships, invest in technology, and stay informed about industry trends to maintain a competitive edge. By taking proactive steps today, businesses can position themselves for success in the dynamic global landscape. Engage with your suppliers and explore innovative solutions that will propel your business forward.