Enhance Quality with Dough Moulding Compound: A Complete Guide (2025)
Introduction: Navigating the Global Market for dough moulding compound
In the ever-evolving landscape of manufacturing and industrial processes, sourcing high-quality dough moulding compounds can be a daunting task for international B2B buyers. Whether you are operating in Africa, South America, the Middle East, or Europe, understanding the nuances of this specialized material is crucial for ensuring product quality and operational efficiency. This guide provides a comprehensive overview of dough moulding compounds, including their various types, applications across different industries, and critical insights into supplier vetting.
International buyers will find actionable strategies for assessing costs, negotiating terms, and establishing long-term partnerships with reliable suppliers. By addressing common challenges such as quality assurance, regulatory compliance, and supply chain logistics, this guide empowers businesses to make informed purchasing decisions. It equips you with the knowledge to navigate the complexities of the global market, ensuring you find the right products to meet your specific needs.
As we delve deeper into the intricacies of dough moulding compounds, you’ll discover valuable insights tailored for diverse markets, including Vietnam and Spain. Understanding these aspects not only enhances your procurement strategy but also fosters sustainable business growth in a competitive environment. Let’s embark on this journey to streamline your sourcing process and elevate your operational capabilities in the global market.
Understanding dough moulding compound Types and Variations
Type Name | Key Distinguishing Features | Primary B2B Applications | Brief Pros & Cons for Buyers |
---|---|---|---|
Thermosetting Dough Moulding Compound | Cures through heat, providing high durability and heat resistance | Automotive parts, electrical insulators | Pros: Excellent thermal stability; Cons: Limited reusability |
Thermoplastic Dough Moulding Compound | Can be remolded upon heating, offering flexibility in design | Consumer goods, packaging materials | Pros: Recyclable; Cons: Lower heat resistance compared to thermosetting types |
Filled Dough Moulding Compound | Contains fillers to enhance properties like strength and cost-efficiency | Construction materials, industrial applications | Pros: Cost-effective; Cons: May reduce overall material flexibility |
High-Performance Dough Moulding Compound | Engineered for extreme conditions, such as high temperatures or corrosive environments | Aerospace, military, and specialized industrial applications | Pros: Superior performance; Cons: Higher cost and limited availability |
Color-Enhanced Dough Moulding Compound | Incorporates pigments for aesthetic finishes without additional coatings | Consumer electronics, decorative items | Pros: Immediate aesthetic appeal; Cons: Color stability may vary under UV exposure |
What Are the Characteristics of Thermosetting Dough Moulding Compound?
Thermosetting dough moulding compounds are characterized by their ability to cure into a hard, inflexible structure when exposed to heat. This type of compound is particularly suitable for applications requiring high durability and thermal resistance, making it ideal for automotive parts and electrical insulators. When purchasing, buyers should consider the specific heat resistance and mechanical properties required for their applications, as well as the potential for limited reusability.
How Do Thermoplastic Dough Moulding Compounds Differ?
Thermoplastic dough moulding compounds can be reshaped upon heating, allowing for greater design flexibility. This variation is commonly used in consumer goods and packaging materials, where the ability to recycle and remold is advantageous. B2B buyers should assess the intended use to determine whether the lower heat resistance of thermoplastics aligns with their product requirements, especially in environments where heat exposure is a concern.
What Are the Benefits of Filled Dough Moulding Compounds?
Filled dough moulding compounds incorporate various fillers to enhance properties such as strength and cost-efficiency. These compounds are widely used in construction materials and industrial applications due to their affordability and improved performance. Buyers should weigh the cost benefits against potential reductions in flexibility and other mechanical properties, ensuring that the chosen material meets the necessary performance standards.
Why Choose High-Performance Dough Moulding Compounds?
High-performance dough moulding compounds are specifically engineered for extreme conditions, making them suitable for aerospace, military, and specialized industrial applications. They offer superior thermal stability and resistance to harsh environments. However, buyers should consider the higher costs associated with these materials and evaluate their availability in the market, ensuring that their investment aligns with the operational demands of their projects.
How Can Color-Enhanced Dough Moulding Compounds Add Value?
Color-enhanced dough moulding compounds include pigments that provide aesthetic finishes without the need for additional coatings. This characteristic is particularly beneficial for consumer electronics and decorative items, where visual appeal is crucial. When selecting color-enhanced options, buyers should be mindful of color stability under UV exposure and other environmental factors, as these can impact the long-term appearance and durability of the final product.
Related Video: Sheet Moulding Compound
Key Industrial Applications of dough moulding compound
Industry/Sector | Specific Application of Dough Moulding Compound | Value/Benefit for the Business | Key Sourcing Considerations for this Application |
---|---|---|---|
Automotive Manufacturing | Production of automotive components such as housings and panels | High durability, lightweight, and corrosion resistance | Compliance with automotive standards; quality certifications |
Electrical & Electronics | Moulding of insulative parts and housings for electrical devices | Enhanced electrical insulation and safety | Material compatibility with electrical components; fire retardancy certifications |
Construction & Infrastructure | Creation of decorative and functional architectural elements | Aesthetic appeal combined with structural integrity | Local sourcing for cost efficiency; resistance to environmental factors |
Consumer Goods | Manufacturing of durable consumer product casings | Improved product longevity and market competitiveness | Customization options; scalability of production |
Industrial Equipment | Moulding of parts for machinery and tools | Increased operational efficiency and reduced maintenance | Technical specifications; sourcing of raw materials with consistent quality |
How is Dough Moulding Compound Used in Automotive Manufacturing?
In the automotive sector, dough moulding compound (DMC) is extensively utilized for producing components such as housings, panels, and other structural elements. The lightweight yet durable properties of DMC help in reducing the overall vehicle weight, which can lead to improved fuel efficiency. For international buyers, especially in regions like Africa and South America, it is crucial to ensure that the sourced DMC meets stringent automotive standards and regulations, which often vary from country to country. Additionally, quality certifications are essential to maintain the integrity and safety of automotive products.
What Role Does Dough Moulding Compound Play in Electrical & Electronics?
DMC is particularly valuable in the electrical and electronics industry for moulding insulative parts and housings for various devices. Its excellent electrical insulation properties ensure safety and functionality in devices ranging from household appliances to industrial machinery. For B2B buyers in Europe and the Middle East, sourcing DMC that complies with international safety and fire retardancy standards is vital. This ensures that the end products not only perform well but also adhere to regulatory requirements, minimizing risks associated with electrical failures.
How is Dough Moulding Compound Applied in Construction & Infrastructure?
In the construction industry, DMC is used to create both decorative and functional architectural elements, such as facades and structural panels. The compound’s versatility allows for intricate designs while maintaining structural integrity, making it a popular choice for modern buildings. Buyers from regions like Africa and South America should consider local sourcing to reduce transportation costs and ensure timely delivery. Additionally, understanding the material’s resistance to environmental factors such as moisture and UV exposure is essential for long-term durability.
What are the Benefits of Dough Moulding Compound in Consumer Goods?
DMC is widely used in the manufacturing of durable casings for consumer products, enhancing their longevity and aesthetic appeal. This leads to increased market competitiveness as consumers tend to prefer products that combine functionality with design. For international B2B buyers, particularly in Europe, customization options in moulding can provide a significant advantage, allowing businesses to tailor products to specific consumer demands. Scalability in production is another critical factor, enabling suppliers to meet varying order sizes efficiently.
How is Dough Moulding Compound Utilized in Industrial Equipment?
In the industrial sector, DMC is essential for moulding parts used in machinery and tools. The material’s robustness contributes to increased operational efficiency and a reduction in maintenance costs, making it a preferred choice for manufacturers. Buyers should focus on the technical specifications of the DMC to ensure compatibility with their machinery requirements. Moreover, sourcing high-quality raw materials is crucial to maintain consistent production standards and minimize defects, which can lead to costly downtimes.
3 Common User Pain Points for ‘dough moulding compound’ & Their Solutions
Scenario 1: Quality Inconsistency in Dough Moulding Compound
The Problem:
B2B buyers often face significant challenges with the quality inconsistency of dough moulding compounds sourced from different suppliers. For manufacturers in Africa and South America, fluctuating product quality can lead to production delays, increased waste, and ultimately, dissatisfaction among end customers. This inconsistency might arise from varying raw material quality, production techniques, or even inadequate quality control measures employed by suppliers.
The Solution:
To tackle this issue, international buyers should prioritize establishing long-term partnerships with reputable suppliers who have a proven track record of quality assurance. It is essential to conduct thorough due diligence, including requesting product samples and quality certification documents. Implementing a robust supplier evaluation process that assesses not only the product but also the supplier’s operational standards can mitigate risks. Furthermore, collaborating with suppliers to define specific quality parameters and conducting regular audits can ensure that the dough moulding compound meets the required specifications consistently. Buyers can also consider forming a quality assurance agreement that outlines the expected standards, penalties for non-compliance, and incentives for maintaining high-quality production.
Scenario 2: Difficulty in Matching Specific Application Requirements
The Problem:
Another common pain point is the challenge of finding a dough moulding compound that meets specific application requirements for various industries, such as automotive, electrical, or consumer goods. Buyers often struggle to navigate the technical specifications, such as curing times, flexibility, and thermal stability, leading to mismatches in application and performance.
The Solution:
To overcome this challenge, buyers should invest time in understanding the unique requirements of their applications. This involves collaborating closely with their engineering or R&D teams to outline precise criteria for the dough moulding compound. Additionally, engaging with suppliers early in the product development process can provide insights into available formulations that best suit their needs. Buyers should also utilize detailed technical datasheets and product guides provided by manufacturers, which can aid in making informed decisions. Participating in industry conferences and trade shows can also expose buyers to innovative products and allow for direct discussions with suppliers about specific application needs.
Scenario 3: High Costs Associated with Dough Moulding Compound
The Problem:
Cost control is a pressing issue for many B2B buyers, especially in regions like the Middle East and Europe, where operational costs can be high. Buyers often find themselves paying premium prices for dough moulding compounds without understanding the underlying factors that contribute to these costs, which can severely impact their bottom line.
The Solution:
To manage costs effectively, buyers should adopt a strategic sourcing approach. This involves not only comparing prices but also evaluating the total cost of ownership (TCO), which includes factors like transportation, storage, and waste associated with the dough moulding compound. Establishing relationships with multiple suppliers can provide leverage in negotiations, enabling buyers to secure more favorable pricing terms. Additionally, buyers should explore bulk purchasing options or long-term contracts that can lower unit costs. Leveraging technology, such as procurement software, can also streamline the purchasing process and provide valuable analytics to identify the most cost-effective suppliers and materials. Engaging in continuous market research to stay informed about industry trends and pricing fluctuations can further empower buyers to make timely and cost-efficient decisions.
Strategic Material Selection Guide for dough moulding compound
What Are the Key Materials for Dough Moulding Compound?
Selecting the right material for dough moulding compounds is crucial for ensuring optimal performance, durability, and cost-effectiveness in various applications. Below is an analysis of four common materials used in dough moulding compounds, focusing on their key properties, advantages, disadvantages, and specific considerations for international B2B buyers.
How Does Epoxy Resin Perform in Dough Moulding Compounds?
Key Properties: Epoxy resins are known for their excellent adhesion, chemical resistance, and thermal stability. They can withstand high temperatures (up to 150°C) and pressures, making them suitable for various industrial applications.
Pros & Cons: The primary advantage of epoxy resin is its strong mechanical properties, which enhance the durability of the final product. However, the manufacturing complexity can be high due to the need for precise mixing ratios and curing processes. Additionally, epoxy can be more expensive compared to other materials.
Impact on Application: Epoxy resins are compatible with a wide range of media, including oils and solvents, making them ideal for applications in automotive and aerospace sectors.
Considerations for International Buyers: Buyers from regions like Africa and South America should be aware of local regulations regarding chemical safety and environmental impact. Compliance with standards such as ASTM D638 (tensile properties) is essential.
What Are the Benefits of Polyurethane in Dough Moulding Compounds?
Key Properties: Polyurethane (PU) materials exhibit excellent flexibility, abrasion resistance, and can operate effectively in a wide temperature range (-40°C to 80°C).
Pros & Cons: The flexibility of PU makes it suitable for applications requiring impact resistance. However, it may not perform well under extreme chemical exposure, limiting its use in certain environments. The cost of PU is generally moderate, making it a balanced choice for many applications.
Impact on Application: PU is particularly effective in applications requiring cushioning or shock absorption, such as in automotive interiors.
Considerations for International Buyers: European buyers should ensure compliance with REACH regulations concerning chemical substances. Understanding local market preferences for flexibility and durability can guide material selection.
How Does Thermoplastic Elastomer Compare for Dough Moulding Compounds?
Key Properties: Thermoplastic elastomers (TPE) combine the properties of rubber and plastic, offering good elasticity and resistance to UV light and ozone.
Pros & Cons: TPEs are easy to process and recycle, which can reduce manufacturing waste. However, they may have lower thermal stability compared to other materials, which can be a limiting factor in high-temperature applications. Their relative cost is generally low to medium.
Impact on Application: TPEs are suitable for applications requiring soft-touch surfaces, such as consumer products and medical devices.
Considerations for International Buyers: Buyers in the Middle East may need to consider the material’s performance in high-temperature environments and ensure compliance with local safety standards.
What Role Does Phenolic Resin Play in Dough Moulding Compounds?
Key Properties: Phenolic resins are known for their high heat resistance (up to 200°C) and excellent dimensional stability, making them suitable for high-performance applications.
Pros & Cons: The primary advantage of phenolic resin is its durability and resistance to chemicals and heat. However, the manufacturing process can be complex, and the material is often more expensive than alternatives.
Impact on Application: Phenolic resin is ideal for applications requiring high strength and thermal stability, such as in electrical components and automotive parts.
Considerations for International Buyers: Buyers from Europe should ensure that their products meet the stringent EU regulations regarding emissions and safety. Knowledge of local standards like DIN 16945 can aid in compliance.
Summary Table of Material Selection for Dough Moulding Compound
Material | Typical Use Case for Dough Moulding Compound | Key Advantage | Key Disadvantage/Limitation | Relative Cost (Low/Med/High) |
---|---|---|---|---|
Epoxy Resin | Aerospace and automotive components | Excellent adhesion and durability | High manufacturing complexity | High |
Polyurethane | Automotive interiors | Good flexibility and abrasion resistance | Limited chemical resistance | Med |
Thermoplastic Elastomer | Consumer products and medical devices | Easy processing and recycling | Lower thermal stability | Low/Med |
Phenolic Resin | Electrical components and automotive parts | High heat resistance | Complex manufacturing process | High |
This guide aims to provide international B2B buyers with actionable insights into the strategic selection of materials for dough moulding compounds, ensuring that they can make informed decisions that align with their specific operational needs and compliance requirements.
In-depth Look: Manufacturing Processes and Quality Assurance for dough moulding compound
What Are the Main Stages of Manufacturing Dough Moulding Compound?
The manufacturing process of dough moulding compound (DMC) involves several critical stages, each essential for achieving the desired quality and performance of the final product. Understanding these stages helps B2B buyers assess potential suppliers and ensure they meet required specifications.
1. Material Preparation
The initial stage of DMC production focuses on the careful selection and preparation of raw materials. The primary components typically include unsaturated polyester resin, fillers, and additives. Each ingredient is meticulously weighed and mixed to ensure uniformity and proper chemical reactions during curing.
Key Techniques:
– Batch Mixing: Raw materials are combined in precise proportions using specialized mixers, which can vary in size depending on production scale.
– Quality Control of Inputs: Incoming materials undergo rigorous testing to verify compliance with industry standards, ensuring they are free from impurities that could affect the final product.
2. Forming
Once the material is prepared, the next step is forming the DMC into the desired shapes. This is typically achieved through processes such as compression moulding or injection moulding.
Key Techniques:
– Compression Moulding: A pre-measured amount of DMC is placed in a heated mould, where pressure is applied to shape it. This method is favored for its ability to produce complex shapes with minimal waste.
– Injection Moulding: DMC is heated until it becomes pliable and then injected into a mould. This technique allows for high-volume production and precision in detail.
3. Assembly
In some applications, multiple components may need to be assembled post-forming. This assembly process can involve additional curing or bonding techniques to ensure structural integrity.
Key Techniques:
– Adhesive Bonding: High-strength adhesives are used to attach different DMC parts, enhancing durability and performance.
– Mechanical Fastening: Components may also be assembled using mechanical fasteners, which require precise engineering to maintain product integrity.
4. Finishing
The final stage involves surface treatments and finishing touches that enhance the aesthetic and functional properties of the DMC products.
Key Techniques:
– Surface Coatings: A variety of coatings can be applied for added protection against environmental factors or to improve appearance.
– Quality Inspection: Each finished product undergoes a final quality check to ensure compliance with specifications before packaging and shipping.
How Is Quality Assurance Implemented in Dough Moulding Compound Production?
Quality assurance (QA) is paramount in the manufacturing of DMC, ensuring that products meet both international standards and specific customer requirements. The QA process is structured around several key elements.
Relevant International Standards for DMC
B2B buyers should be familiar with the international standards that govern the manufacturing of DMC. Compliance with these standards not only assures product quality but also facilitates smoother trade across borders.
- ISO 9001: This globally recognized standard outlines the criteria for a quality management system (QMS). Manufacturers certified under ISO 9001 demonstrate their ability to consistently provide products that meet customer and regulatory requirements.
- CE Marking: For suppliers in Europe, CE marking indicates compliance with health, safety, and environmental protection standards. This is particularly important for products used in construction and automotive applications.
- API Standards: For DMC used in the oil and gas industry, adherence to American Petroleum Institute (API) standards is crucial, ensuring that materials can withstand harsh operational conditions.
What Are the QC Checkpoints in DMC Manufacturing?
Quality control checkpoints are critical for ensuring that each stage of the manufacturing process adheres to established standards.
- Incoming Quality Control (IQC): This initial checkpoint assesses the quality of raw materials before they enter the production process. Materials that do not meet specifications are rejected or reprocessed.
- In-Process Quality Control (IPQC): During production, samples are taken at various stages to monitor quality and consistency. This real-time feedback allows for immediate corrective actions if deviations are detected.
- Final Quality Control (FQC): After the finishing stage, a comprehensive inspection is conducted to verify that the final products meet all specifications and standards before they are packaged and shipped.
What Testing Methods Are Commonly Used for Dough Moulding Compound?
Several testing methods are employed to evaluate the performance and quality of DMC products, ensuring they meet the necessary standards for their intended applications.
- Mechanical Testing: This includes tensile strength, impact resistance, and flexural strength tests, which assess how the material will perform under stress.
- Thermal Testing: Evaluating heat resistance and thermal conductivity is vital for applications exposed to high temperatures.
- Chemical Resistance Testing: DMC products must be tested for their resistance to various chemicals, especially if used in industrial applications.
How Can B2B Buyers Verify Supplier Quality Control?
For international buyers, especially those from Africa, South America, the Middle East, and Europe, verifying a supplier’s quality control practices is essential to mitigate risks.
- Supplier Audits: Conducting regular audits of suppliers allows buyers to assess compliance with quality standards and operational practices.
- Requesting Quality Reports: Buyers should request detailed QC reports that outline testing results, manufacturing processes, and any corrective actions taken for non-conformities.
- Third-Party Inspections: Engaging third-party inspection services can provide an unbiased evaluation of a supplier’s quality control measures, ensuring compliance with international standards.
What Are the Quality Control and Certification Nuances for International B2B Buyers?
Navigating the quality control landscape can be complex for international buyers, particularly when sourcing DMC from different regions.
- Understanding Local Standards: Different countries may have specific regulations or standards that affect the manufacturing and certification of DMC. Buyers should familiarize themselves with these to avoid compliance issues.
- Cultural Considerations: Building strong relationships with suppliers often requires understanding cultural nuances, which can impact communication and quality assurance practices.
- Documentation and Traceability: Ensure that suppliers maintain thorough documentation of their quality control processes, allowing for traceability of materials and compliance verification.
By understanding these manufacturing processes and quality assurance practices, international B2B buyers can make informed decisions when sourcing dough moulding compounds, ensuring they receive high-quality products that meet their operational needs.
Practical Sourcing Guide: A Step-by-Step Checklist for ‘dough moulding compound’
In the realm of sourcing dough moulding compounds, a structured approach is essential for B2B buyers, especially from diverse regions like Africa, South America, the Middle East, and Europe. This checklist aims to guide you through the critical steps necessary to ensure a successful procurement process, helping you find quality products that meet your business needs.
Step 1: Define Your Technical Specifications
Begin by outlining the specific requirements for the dough moulding compound you need. This includes details such as viscosity, curing time, and compatibility with existing production processes.
– Why it’s important: Clear specifications help suppliers understand your needs and ensure that the products offered are suitable for your applications.
– What to look for: Engage with your engineering or production team to finalize these specifications.
Step 2: Conduct Market Research
Explore the current market trends and suppliers of dough moulding compounds. Utilize industry reports, trade publications, and online resources to gather insights on potential suppliers.
– Why it’s important: Understanding the market landscape enables you to identify reputable suppliers and evaluate their offerings effectively.
– What to look for: Focus on suppliers with a strong track record in quality, reliability, and customer service.
Step 3: Evaluate Potential Suppliers
Before making a commitment, thoroughly vet potential suppliers. Request detailed company profiles, case studies, and references from other businesses in your sector.
– Why it’s important: A comprehensive evaluation minimizes risks associated with supplier reliability and product quality.
– What to look for: Look for suppliers who have experience in your industry and can provide testimonials from satisfied clients.
Step 4: Request Samples and Test Products
Once you have shortlisted suppliers, request samples of the dough moulding compound for testing. Assess the samples against your specifications to ensure they meet your requirements.
– Why it’s important: Testing samples allows you to verify product performance and compatibility with your processes before making a large purchase.
– What to look for: Check for consistency in quality, ease of handling, and compliance with safety standards.
Step 5: Verify Supplier Certifications
Ensure that potential suppliers possess the necessary certifications and quality assurance processes in place, such as ISO certifications or industry-specific standards.
– Why it’s important: Certifications indicate that a supplier adheres to recognized quality and safety standards, which is critical for maintaining product integrity.
– What to look for: Request documentation and check for any industry-specific certifications relevant to your region or sector.
Step 6: Negotiate Terms and Conditions
Discuss pricing, payment terms, lead times, and delivery conditions with your chosen supplier. Ensure all terms are clearly defined to prevent misunderstandings later.
– Why it’s important: Clear negotiations help establish a mutual understanding and set expectations for both parties.
– What to look for: Be attentive to hidden costs and ensure that the supplier is transparent about all charges.
Step 7: Establish a Communication Plan
After selecting a supplier, set up a communication plan to maintain consistent dialogue. This should include regular updates on order status, potential issues, and feedback on product performance.
– Why it’s important: Effective communication fosters a strong supplier relationship and enables quick resolution of any problems that arise.
– What to look for: Determine preferred communication channels and frequency of updates that work for both parties.
By following this checklist, B2B buyers can streamline their sourcing process for dough moulding compounds, ensuring they partner with suppliers who meet their quality standards and business needs.
Comprehensive Cost and Pricing Analysis for dough moulding compound Sourcing
What Are the Key Cost Components in Dough Moulding Compound Sourcing?
When sourcing dough moulding compounds, understanding the cost structure is essential for B2B buyers to make informed decisions. The primary cost components include:
-
Materials: The choice of raw materials directly influences the cost. Common materials used in dough moulding compounds include polymers, fillers, and additives. Prices fluctuate based on market conditions and availability, so it’s crucial to stay updated on material costs.
-
Labor: Labor costs vary significantly depending on the manufacturing location. Regions with higher labor costs, such as parts of Europe, may lead to increased overall pricing. Conversely, sourcing from regions with lower labor costs, like some areas in Africa and South America, can offer savings.
-
Manufacturing Overhead: This includes utilities, equipment maintenance, and facility costs. Efficient production processes can help reduce these overheads, impacting the final pricing of the compound.
-
Tooling: The costs associated with creating molds and tools for production can be substantial, especially for custom specifications. Investing in high-quality tooling can lead to better product quality and longevity.
-
Quality Control (QC): Implementing rigorous QC measures ensures the final product meets required standards but adds to the overall cost. Buyers should evaluate the QC processes of potential suppliers to balance quality and cost.
-
Logistics: Shipping and handling costs can vary widely based on the location of the supplier and the buyer. Incoterms play a critical role in determining who bears these costs, affecting the total price.
-
Margin: Suppliers typically add a margin to cover their costs and profits. Understanding a supplier’s pricing strategy can provide leverage during negotiations.
How Do Price Influencers Affect Dough Moulding Compound Pricing?
Several factors can influence the pricing of dough moulding compounds, including:
-
Volume/MOQ: Minimum order quantities (MOQs) often dictate pricing; larger orders generally yield lower unit costs. Buyers should assess their demand to negotiate better pricing.
-
Specifications and Customization: Tailored compounds or unique specifications can significantly increase costs. Buyers should clarify their needs upfront to avoid unexpected price hikes.
-
Material Quality and Certifications: Higher quality materials and certifications (such as ISO or ASTM) typically come at a premium. Buyers must weigh the benefits of enhanced quality against the additional costs.
-
Supplier Factors: The reputation and reliability of the supplier can affect pricing. Established suppliers might command higher prices due to their experience and quality assurance, while new entrants may offer lower prices to gain market share.
-
Incoterms: Understanding shipping terms can drastically impact costs. For example, an Ex-Works (EXW) arrangement means the buyer is responsible for all shipping costs, which can be more expensive than a Delivered Duty Paid (DDP) agreement.
What Are Effective Buyer Tips for Sourcing Dough Moulding Compounds?
To navigate the complexities of pricing and sourcing dough moulding compounds effectively, consider these actionable tips:
-
Negotiate Strategically: Use your understanding of cost components to negotiate better terms. Highlight your potential for larger orders or long-term partnerships to secure more favorable pricing.
-
Evaluate Total Cost of Ownership (TCO): Look beyond the initial price. Consider factors like logistics, quality, and the longevity of the product to determine the true cost over time.
-
Research Pricing Nuances for International Markets: Buyers from regions such as Africa, South America, the Middle East, and Europe should be aware of regional pricing variations. Currency fluctuations, tariffs, and local market conditions can all impact pricing.
-
Request Samples: Before committing to a large order, request samples to evaluate quality. This can help in making informed decisions and ensuring the product meets your specifications.
-
Stay Informed on Market Trends: Regularly monitor market conditions and material prices to anticipate changes that could affect sourcing costs. Being proactive can help you negotiate better deals.
Disclaimer on Indicative Prices
Prices for dough moulding compounds can fluctuate based on various factors, including market demand, material availability, and supplier pricing strategies. It is advisable for buyers to obtain quotes directly from suppliers to get the most accurate and current pricing information.
Alternatives Analysis: Comparing dough moulding compound With Other Solutions
When evaluating materials for manufacturing applications, it is crucial to consider various alternatives to dough moulding compound (DMC). Each alternative presents unique benefits and challenges that can significantly impact production efficiency, costs, and end product quality. Below, we explore two viable alternatives to DMC: thermoplastic elastomers (TPE) and epoxy resins.
Comparison Table of Dough Moulding Compound and Alternatives
Comparison Aspect | Dough Moulding Compound | Thermoplastic Elastomers (TPE) | Epoxy Resins |
---|---|---|---|
Performance | High thermal stability, excellent electrical insulation | Flexible, good impact resistance | Strong adhesion, chemical resistance |
Cost | Moderate to high | Generally lower than DMC | Typically high |
Ease of Implementation | Requires specialized moulding equipment | Easier to process, can be injection moulded | Needs precise mixing and curing time |
Maintenance | Low maintenance | Moderate maintenance required | Low maintenance once cured |
Best Use Case | Automotive, electrical components | Consumer goods, seals, gaskets | Aerospace, construction |
What Are the Advantages and Disadvantages of Thermoplastic Elastomers (TPE)?
Thermoplastic elastomers (TPE) are a versatile alternative that combines the properties of rubber with the recyclability of plastics. TPEs are relatively easy to process, often allowing for injection moulding, which can reduce production times and costs. Their flexibility and impact resistance make them suitable for applications in consumer products, seals, and gaskets.
However, TPEs may not offer the same thermal stability or electrical insulation properties as DMC, which can be a significant drawback in industries requiring stringent performance metrics, such as automotive or electronics. Buyers should consider the specific requirements of their applications before opting for TPEs over DMC.
How Do Epoxy Resins Compare to Dough Moulding Compound?
Epoxy resins are known for their excellent adhesion and chemical resistance, making them ideal for applications in aerospace and construction. They can be tailored for specific requirements through various formulations, allowing for high-performance applications. Once cured, epoxy resins exhibit low maintenance needs, which is beneficial for long-term projects.
On the downside, the initial costs of epoxy resins can be higher than DMC, and their processing often requires precise mixing and curing times, which can complicate production schedules. For manufacturers focused on durability and strong bonding, epoxy resins may be a superior choice, but they might not be as versatile as DMC in certain applications.
How Can B2B Buyers Choose the Right Solution for Their Needs?
Selecting the appropriate material for manufacturing processes hinges on understanding specific application requirements, performance expectations, and budget constraints. B2B buyers should assess their production capabilities, the environmental conditions the final product will face, and any regulatory standards that must be met. Conducting a thorough cost-benefit analysis, including long-term maintenance and performance metrics, will empower buyers to make informed decisions that align with their operational goals.
Ultimately, whether opting for dough moulding compound, thermoplastic elastomers, or epoxy resins, the choice should be driven by a comprehensive understanding of each material’s characteristics and the specific needs of the application.
Essential Technical Properties and Trade Terminology for dough moulding compound
What Are the Key Technical Properties of Dough Moulding Compound?
Dough moulding compounds (DMC) are essential in various manufacturing processes, particularly in producing electrical components and automotive parts. Understanding their technical properties is crucial for international B2B buyers to ensure they select the right materials for their applications. Below are some critical specifications to consider:
-
Material Grade
The material grade of DMC refers to the specific formulation and composition of the compound. Different grades have varying mechanical, thermal, and electrical properties, affecting their performance in applications. B2B buyers should assess the required grade based on the end-use of the product, as this can influence durability and compliance with industry standards. -
Tensile Strength
This property measures the compound’s ability to withstand tension without failing. High tensile strength is essential for applications that experience mechanical stress. Buyers should consider this specification to ensure that the DMC can handle operational loads and minimize the risk of product failure. -
Thermal Stability
Thermal stability indicates how well a DMC can maintain its properties under heat exposure. A compound with high thermal stability is less likely to deform or degrade when subjected to elevated temperatures. For applications in automotive or electrical environments, thermal stability is a critical factor that can affect performance and longevity. -
Cure Time
This property specifies the duration required for the compound to fully harden after being processed. Shorter cure times can enhance production efficiency, making it a vital consideration for manufacturers looking to optimize their operations. Understanding cure times helps B2B buyers plan their production schedules and meet delivery deadlines. -
Viscosity
Viscosity is a measure of a fluid’s resistance to flow. In the context of DMC, it affects how easily the compound can be molded and shaped during manufacturing. Buyers should ensure that the viscosity aligns with their processing methods to achieve the desired product specifications.
What Are Common Trade Terms in the Dough Moulding Compound Industry?
Navigating the world of B2B purchasing requires familiarity with industry jargon. Below are several common terms that buyers should understand:
-
OEM (Original Equipment Manufacturer)
An OEM is a company that produces parts or equipment that may be marketed by another manufacturer. In the context of DMC, OEMs often require specific formulations or grades for their components, making it essential for buyers to understand their needs. -
MOQ (Minimum Order Quantity)
MOQ refers to the smallest quantity of a product that a supplier is willing to sell. This term is crucial for B2B buyers to consider when negotiating orders, as it can affect inventory management and overall costs. -
RFQ (Request for Quotation)
An RFQ is a document that a buyer sends to suppliers to solicit price quotes for specific products or services. This process allows buyers to compare offers and make informed purchasing decisions based on quality, price, and delivery terms. -
Incoterms (International Commercial Terms)
Incoterms are a set of predefined commercial terms published by the International Chamber of Commerce, outlining the responsibilities of buyers and sellers in international transactions. Understanding Incoterms is vital for B2B buyers to clarify shipping responsibilities, risk management, and cost allocation. -
Lead Time
Lead time refers to the time taken from placing an order to receiving the goods. This term is critical for buyers to manage their supply chain effectively, ensuring that production schedules align with material availability.
By understanding these technical properties and trade terms, international B2B buyers from regions like Africa, South America, the Middle East, and Europe can make informed decisions when sourcing dough moulding compounds, ultimately enhancing their operational efficiency and product quality.
Navigating Market Dynamics and Sourcing Trends in the dough moulding compound Sector
What are the Current Market Dynamics and Key Trends in the Dough Moulding Compound Sector?
The dough moulding compound (DMC) market is experiencing significant growth driven by several global factors. The increasing demand for lightweight, durable materials in various applications such as automotive, electrical, and consumer goods is a key driver. Technological advancements in manufacturing processes, like enhanced resin formulations and automated production techniques, are also shaping market dynamics. International B2B buyers from regions like Africa, South America, the Middle East, and Europe must stay attuned to these developments to capitalize on emerging opportunities.
One of the most notable trends is the shift towards digitalization and automation in supply chain management. B2B buyers are increasingly utilizing advanced analytics and IoT (Internet of Things) technologies to enhance decision-making processes and improve operational efficiencies. Additionally, the rise of e-commerce platforms is facilitating easier access to suppliers and products, enabling buyers to source DMC materials more conveniently and cost-effectively.
Moreover, sustainability considerations are becoming paramount, influencing sourcing strategies. Buyers are looking for suppliers who can demonstrate responsible sourcing practices, which include reducing carbon footprints and waste. Understanding these trends is essential for businesses aiming to maintain competitiveness in the DMC sector.
How Does Sustainability Impact Sourcing in the Dough Moulding Compound Sector?
Sustainability is a critical factor in the sourcing of dough moulding compounds, as environmental impact becomes a focal point for international B2B buyers. The production of DMC often involves the use of petrochemical-based materials, which can lead to significant ecological concerns, including greenhouse gas emissions and waste generation. As a result, buyers are increasingly prioritizing suppliers who adopt sustainable practices and offer eco-friendly alternatives.
Ethical sourcing is equally important, as companies are held accountable for their supply chain’s social and environmental footprint. Buyers should seek suppliers that comply with international sustainability standards and can provide certifications that verify the environmental impact of their products. Certifications such as ISO 14001 for environmental management or specific ‘green’ certifications for materials are indicators of a supplier’s commitment to sustainability.
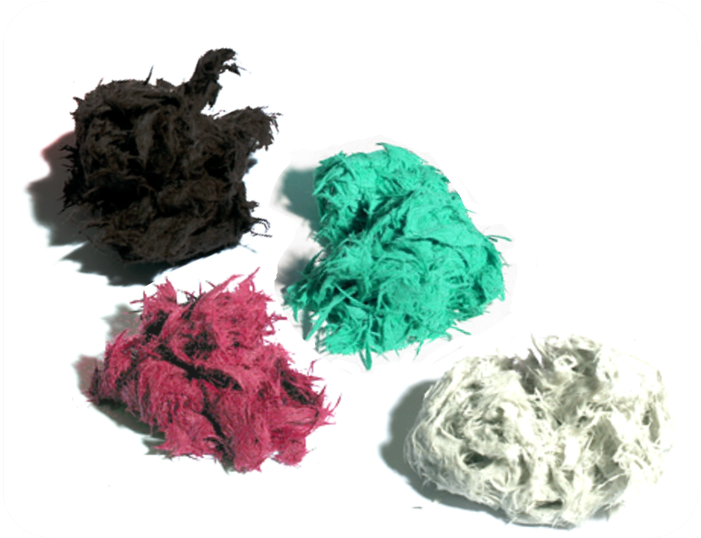
A stock image related to dough moulding compound.
The demand for bio-based or recycled materials in the DMC sector is also rising, with companies exploring options to integrate these materials into their production processes. By prioritizing sustainable sourcing, B2B buyers not only enhance their brand reputation but also align with consumer expectations for environmentally responsible products.
What is the Evolution of the Dough Moulding Compound Sector?
The dough moulding compound sector has evolved significantly over the decades, transitioning from traditional manufacturing methods to advanced composite technologies. Initially, DMCs were primarily used in the electrical and automotive industries due to their excellent insulating properties and mechanical strength. However, the introduction of innovative formulations and production techniques has broadened the application scope of DMCs.
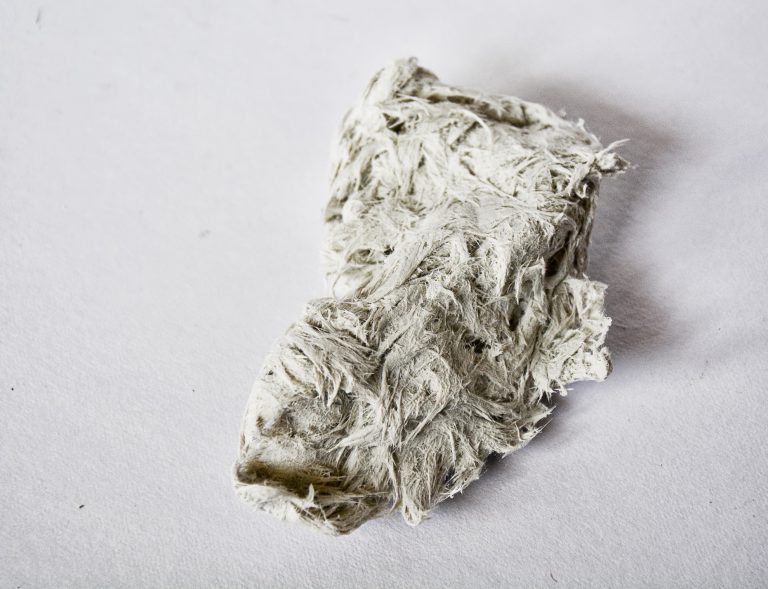
A stock image related to dough moulding compound.
In recent years, the sector has seen a surge in demand driven by the growth of the automotive and consumer goods industries, particularly in emerging markets. As the focus shifts towards lightweight materials and sustainable practices, the DMC sector is poised for further evolution, integrating advanced materials science with eco-friendly practices to meet the needs of a dynamic marketplace. International B2B buyers must remain informed of these historical trends to better understand current market offerings and future potential.
Frequently Asked Questions (FAQs) for B2B Buyers of dough moulding compound
-
How do I choose the right dough moulding compound for my manufacturing needs?
Selecting the appropriate dough moulding compound hinges on your specific application requirements. Factors such as the intended use, desired properties (like flexibility, hardness, and thermal resistance), and compatibility with existing production processes should guide your choice. It’s advisable to consult with suppliers who can provide samples for testing. Additionally, consider the climatic conditions in your region, as this may affect the compound’s performance, especially in places with extreme temperatures like parts of Africa or the Middle East. -
What are the common applications of dough moulding compounds in various industries?
Dough moulding compounds are widely used in industries such as automotive, electrical, and consumer goods. They are ideal for producing components like insulators, housings, and decorative parts due to their excellent moldability and durability. Understanding your industry’s specific requirements can help you select a compound that meets regulatory standards and performance expectations, particularly in diverse markets across South America and Europe. -
What minimum order quantities (MOQ) should I expect when sourcing dough moulding compounds?
MOQs for dough moulding compounds can vary significantly based on the supplier and the specific formulation required. Typically, you may encounter MOQs ranging from 100 kg to several tons. For international buyers, especially from Africa and South America, negotiating MOQs can be possible, particularly if you demonstrate long-term purchasing potential. Always clarify these terms upfront to avoid unexpected costs or logistical challenges. -
What payment terms are commonly offered by suppliers of dough moulding compounds?
Payment terms for sourcing dough moulding compounds can vary widely by supplier and region. Common arrangements include net 30 or net 60 terms, requiring full payment upfront, or a deposit followed by the balance upon delivery. For international transactions, consider using secure payment methods such as letters of credit or escrow services to safeguard your investment. It’s crucial to establish clear payment expectations during the negotiation phase to facilitate smooth transactions. -
How can I ensure quality assurance when sourcing dough moulding compounds?
To ensure quality assurance, request detailed specifications and certifications from your suppliers. This should include compliance with international standards such as ISO or ASTM, as well as data sheets that outline mechanical and thermal properties. Conducting factory audits or requesting third-party testing can also enhance your confidence in the product’s quality. Building a solid relationship with your supplier can further ensure consistent quality over time. -
What logistical considerations should I keep in mind when importing dough moulding compounds?
When importing dough moulding compounds, consider factors such as shipping methods, customs regulations, and lead times. Verify that the supplier can manage logistics efficiently, including handling documentation for customs clearance. Depending on your location in Africa, South America, or Europe, shipping times can vary significantly, so plan your inventory accordingly. Working with a freight forwarder experienced in your region can help streamline the process. -
How can I vet suppliers of dough moulding compounds effectively?
Vetting suppliers requires a multi-faceted approach. Start by researching their market reputation through reviews and testimonials. Request references from other clients, especially those in similar industries. Evaluate their production capabilities and quality control processes through site visits or virtual tours. Additionally, ensure they comply with relevant certifications and standards. This thorough vetting process is essential for securing reliable partnerships, particularly in diverse markets across the Middle East and Europe. -
Can dough moulding compounds be customized for specific applications?
Yes, many suppliers offer customization options for dough moulding compounds to meet specific application needs. This may include adjusting the compound’s hardness, color, or thermal resistance based on your requirements. When discussing customization, be clear about your specifications and the intended application. Collaborating closely with your supplier during the development phase can lead to a tailored solution that enhances your product’s performance in the competitive international market.
Important Disclaimer & Terms of Use
⚠️ Important Disclaimer
The information provided in this guide, including content regarding manufacturers, technical specifications, and market analysis, is for informational and educational purposes only. It does not constitute professional procurement advice, financial advice, or legal advice.
While we have made every effort to ensure the accuracy and timeliness of the information, we are not responsible for any errors, omissions, or outdated information. Market conditions, company details, and technical standards are subject to change.
B2B buyers must conduct their own independent and thorough due diligence before making any purchasing decisions. This includes contacting suppliers directly, verifying certifications, requesting samples, and seeking professional consultation. The risk of relying on any information in this guide is borne solely by the reader.
Strategic Sourcing Conclusion and Outlook for dough moulding compound
What Are the Key Takeaways for B2B Buyers in the Dough Moulding Compound Market?
As the demand for dough moulding compounds continues to grow across diverse regions, international B2B buyers must prioritize strategic sourcing to ensure quality, cost-effectiveness, and timely delivery. Understanding local market dynamics in Africa, South America, the Middle East, and Europe is crucial. Buyers should seek suppliers that not only meet specifications but also demonstrate reliability and innovation in their production processes.
How Can Strategic Sourcing Enhance Your Supply Chain?
By leveraging strategic sourcing, businesses can optimize their supply chains, reduce operational risks, and foster long-term partnerships with suppliers. This approach facilitates access to new technologies and materials, enabling companies to remain competitive in an evolving marketplace. Additionally, establishing robust communication channels with suppliers can lead to improved transparency and responsiveness.
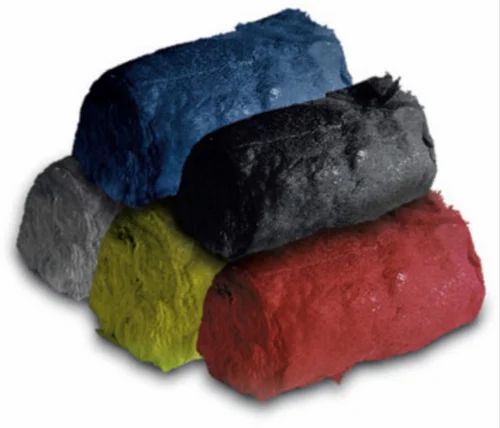
A stock image related to dough moulding compound.
What Should B2B Buyers Do Next?
Looking ahead, B2B buyers are encouraged to stay informed about industry trends and innovations in dough moulding compounds. Engaging in trade shows, webinars, and industry forums can provide valuable insights and networking opportunities. By taking proactive steps towards strategic sourcing, international buyers can position themselves for success in a global market that is increasingly focused on sustainability and efficiency. Embrace these opportunities to enhance your sourcing strategy and drive growth in your business.