How Often to Change Brake Fluid: The Complete Guide (2025)
Introduction: Navigating the Global Market for how often to change brake fluid
In today’s competitive automotive industry, understanding how often to change brake fluid is crucial for maintaining vehicle safety and performance. For international B2B buyers, particularly those sourcing parts and services from regions like Africa, South America, the Middle East, and Europe, determining the optimal frequency for brake fluid replacement can pose significant challenges. Factors such as environmental conditions, vehicle usage patterns, and compliance with local regulations can affect fluid degradation, ultimately impacting vehicle safety and operational costs.
This comprehensive guide aims to equip B2B buyers with the knowledge needed to make informed decisions regarding brake fluid maintenance. We will delve into various types of brake fluids available in the market, their applications across different vehicle types, and the implications of each choice. Additionally, we will explore supplier vetting processes, cost considerations, and best practices for procurement.
By addressing these critical aspects, this guide empowers international buyers to navigate the complexities of brake fluid sourcing confidently. It not only highlights the importance of regular maintenance but also provides actionable insights to enhance the purchasing process. With a focus on quality and reliability, you can ensure that your fleet operates safely and efficiently, regardless of your geographical location.
Understanding how often to change brake fluid Types and Variations
Type Name | Key Distinguishing Features | Primary B2B Applications | Brief Pros & Cons for Buyers |
---|---|---|---|
Standard Maintenance | Recommended every 2 years or 24,000 miles | Fleet vehicles, logistics companies | Pros: Predictable schedule, easier budgeting. Cons: May lead to unnecessary changes if usage is low. |
Usage-Based Change | Based on specific vehicle usage and conditions | Construction, mining, agriculture | Pros: Tailored maintenance, cost-effective. Cons: Requires monitoring and data analysis. |
Manufacturer Guidelines | Adheres to specific vehicle manufacturer’s advice | Automotive dealerships, repair shops | Pros: Ensures compliance, maintains warranty. Cons: Potentially conservative intervals. |
Climate-Sensitive Change | Adjusts intervals based on regional climate factors | Transport companies in extreme climates | Pros: Optimizes performance, enhances safety. Cons: Requires knowledge of local conditions. |
Performance Upgrades | Shorter intervals for high-performance vehicles | Racing teams, luxury car services | Pros: Enhances braking efficiency, ensures safety. Cons: Higher costs associated with frequent changes. |
What are the Characteristics of Standard Maintenance for Brake Fluid Changes?
Standard maintenance typically recommends changing brake fluid every two years or after 24,000 miles, whichever comes first. This interval is designed to ensure that the fluid remains effective in maintaining brake performance. It is particularly relevant for fleet vehicles and logistics companies that operate under similar conditions, allowing for predictable budgeting and scheduling. However, this approach can lead to unnecessary changes for vehicles that are not frequently used, which may impact overall maintenance costs.
How Does Usage-Based Change Impact Brake Fluid Maintenance?
Usage-based change strategies dictate that brake fluid replacement should be based on the vehicle’s specific usage patterns and environmental conditions. This approach is ideal for industries such as construction, mining, and agriculture, where vehicles may be subjected to harsher conditions. While this method can be more cost-effective, it requires monitoring and data analysis to determine the optimal change intervals, which can be a challenge for businesses without dedicated maintenance teams.
Why Are Manufacturer Guidelines Important for Brake Fluid Changes?
Following manufacturer guidelines for brake fluid changes is crucial for automotive dealerships and repair shops to maintain compliance and protect warranties. These guidelines often recommend specific intervals based on extensive testing and are designed to ensure optimal vehicle performance. While adhering to these recommendations can be beneficial, they may sometimes lead to more conservative intervals that do not account for the actual usage patterns of the vehicle.
How Do Climate Factors Influence Brake Fluid Change Frequency?
Climate-sensitive change strategies adjust the frequency of brake fluid changes based on regional climate factors. For transport companies operating in extreme climates, such as high heat or severe cold, this approach can optimize vehicle performance and enhance safety. However, it requires a thorough understanding of local environmental conditions and their effects on brake fluid, which can complicate maintenance planning.
What Are the Benefits and Drawbacks of Performance Upgrades for Brake Fluid?
Performance upgrades necessitate shorter intervals for brake fluid changes, particularly for high-performance vehicles used in racing or luxury services. This approach ensures enhanced braking efficiency and safety, which is critical in high-stakes environments. However, the downside includes higher costs associated with frequent changes, which may not be feasible for all businesses. Companies must weigh the benefits of improved performance against the increased maintenance expenses.
Key Industrial Applications of how often to change brake fluid
Industry/Sector | Specific Application of how often to change brake fluid | Value/Benefit for the Business | Key Sourcing Considerations for this Application |
---|---|---|---|
Automotive Manufacturing | Regular maintenance schedules for fleet vehicles | Enhances vehicle safety and reduces accident risk | Ensure compatibility with various vehicle models and types |
Public Transportation | Compliance with safety regulations for buses and trains | Minimizes downtime and increases passenger safety | Source fluids that meet international safety standards |
Construction Equipment Rental | Maintenance protocols for heavy machinery | Reduces equipment failure and prolongs machinery lifespan | Consider bulk purchasing options for cost efficiency |
Logistics and Transportation | Brake fluid checks as part of routine vehicle inspections | Improves reliability of delivery fleets | Look for suppliers with rapid delivery capabilities |
Oil and Gas Industry | Safety checks for vehicles used in hazardous environments | Ensures operational safety and compliance with industry regulations | Source fluids that are resistant to extreme conditions |
How is ‘how often to change brake fluid’ applied in the automotive manufacturing sector?
In the automotive manufacturing sector, regular maintenance schedules for fleet vehicles are crucial. Businesses must adhere to recommended intervals for changing brake fluid, which typically ranges from every one to two years, depending on the vehicle type and usage. This practice not only enhances vehicle safety but also reduces the risk of accidents caused by brake failure. For international buyers, understanding regional regulations and vehicle specifications is essential to ensure compliance and safety.
What are the implications for public transportation in relation to brake fluid maintenance?
For public transportation systems, compliance with safety regulations is paramount. Buses and trains require stringent maintenance protocols, including regular checks of brake fluid levels. This practice minimizes downtime and increases passenger safety, directly impacting public perception and operational efficiency. Buyers in this sector should seek suppliers that provide products meeting international safety standards to ensure reliability across diverse fleet types.
How does brake fluid maintenance affect construction equipment rental businesses?
In the construction equipment rental industry, implementing robust maintenance protocols for heavy machinery is vital. Regularly changing brake fluid helps reduce equipment failure rates and prolongs machinery lifespan, thereby enhancing profitability. Buyers should consider sourcing brake fluid in bulk to achieve cost efficiency while ensuring that the fluid is compatible with a wide range of equipment to meet diverse client needs.
Why is brake fluid inspection critical for logistics and transportation?
In logistics and transportation, brake fluid checks are integral to routine vehicle inspections. Ensuring that brake fluid is changed at appropriate intervals improves the reliability of delivery fleets, which is essential for maintaining schedules and customer satisfaction. International B2B buyers should prioritize suppliers who offer rapid delivery capabilities, allowing for timely replenishment and minimizing operational disruptions.
What safety considerations are there for the oil and gas industry regarding brake fluid?
In the oil and gas industry, vehicles operating in hazardous environments require meticulous safety checks, including the maintenance of brake fluid. Regular changes help ensure operational safety and compliance with industry regulations, which can be particularly stringent. Buyers must source brake fluids that are resistant to extreme conditions, ensuring that their vehicles remain operational and safe in demanding environments.
Related Video: How To & How Often to Replace Brake Fluid // COMPLETE Guide Step-by-Step
3 Common User Pain Points for ‘how often to change brake fluid’ & Their Solutions
Scenario 1: Understanding Brake Fluid Change Intervals in Diverse Climatic Conditions
The Problem: For international B2B buyers, particularly those operating fleets in regions with varying climates such as Africa and the Middle East, determining the optimal frequency for changing brake fluid can be challenging. Different environments can lead to accelerated fluid degradation, affecting performance and safety. For instance, high temperatures can cause brake fluid to absorb moisture more quickly, while humid conditions can lead to corrosion in braking systems. Buyers may struggle to find standardized guidelines that apply universally to their diverse operational landscapes, risking vehicle reliability and safety.
The Solution: To effectively manage brake fluid maintenance across different climates, B2B buyers should implement a tailored maintenance schedule based on local conditions. Begin by conducting a comprehensive assessment of the environmental factors affecting each fleet location. Collaborate with brake fluid manufacturers to obtain specifications that detail how their products perform under specific climatic conditions. Regularly monitor brake fluid condition using moisture test strips and replace the fluid as needed—generally every 1-2 years in humid environments or more frequently in extreme heat. Establishing a localized maintenance protocol not only enhances vehicle safety but also extends the life of braking systems, reducing long-term costs.
Scenario 2: Balancing Cost and Quality of Brake Fluid
The Problem: B2B buyers often face the dilemma of balancing cost versus quality when purchasing brake fluid. Cheaper options may promise short-term savings but can lead to long-term issues such as reduced braking efficiency and increased repair costs. In markets like South America, where budget constraints are common, decision-makers may feel pressured to opt for lower-cost alternatives without fully understanding the implications on vehicle safety and performance.
The Solution: To navigate this challenge, B2B buyers should adopt a value-based purchasing approach rather than solely focusing on initial costs. Conduct thorough research on brake fluid options, comparing performance specifications, industry certifications, and manufacturer reputations. Develop a cost-benefit analysis that includes potential long-term savings from reduced maintenance and repair needs when using high-quality brake fluid. Additionally, consider establishing partnerships with reputable suppliers who can provide consistent quality and offer bulk purchasing discounts. Investing in premium brake fluid will lead to enhanced performance, safety, and ultimately lower total costs over the lifespan of the vehicles.
Scenario 3: Lack of Knowledge on Brake Fluid Specifications and Standards
The Problem: In many regions, including parts of Europe and Africa, there is often a lack of awareness regarding the specifications and standards for brake fluid. Buyers may inadvertently purchase incompatible fluids that do not meet the requirements of their vehicles, leading to suboptimal performance and potential safety hazards. This knowledge gap can result in increased liability and maintenance costs for businesses, particularly those managing multiple vehicle types.
The Solution: To address this issue, B2B buyers should prioritize education on brake fluid specifications such as DOT ratings and compatibility with vehicle types. Organize training sessions for maintenance teams that cover the importance of selecting the correct fluid and the implications of using substandard products. Create a centralized database of vehicle specifications and recommended brake fluid types for easy reference during procurement. Additionally, collaborate with automotive associations or industry experts to stay updated on best practices and regulatory changes regarding brake fluid standards. By enhancing their understanding, businesses can make informed decisions that prioritize safety and operational efficiency.
Strategic Material Selection Guide for how often to change brake fluid
What Are the Key Materials for Brake Fluid and How Often Should They Be Changed?
When considering the selection of materials for brake fluid, it’s essential to understand the properties and performance characteristics of various types. Brake fluids are typically classified into categories based on their chemical composition, which influences their performance, compatibility, and maintenance requirements. Below, we analyze four common brake fluid materials: DOT 3, DOT 4, DOT 5, and mineral oil-based fluids.
How Does DOT 3 Brake Fluid Perform in Terms of Change Frequency?
Key Properties:
DOT 3 brake fluid is glycol-based and has a boiling point of around 205°C (401°F). It is hygroscopic, meaning it absorbs moisture over time, which can lead to a decrease in performance.
Pros & Cons:
The primary advantage of DOT 3 is its cost-effectiveness and wide availability, making it a popular choice for many vehicles. However, its susceptibility to moisture absorption can lead to corrosion of brake components and a need for more frequent changes, typically every 1-2 years.
Impact on Application:
Due to its hygroscopic nature, DOT 3 is suitable for vehicles operating under moderate conditions but may not perform well in high-performance applications.
Considerations for International Buyers:
In regions like Africa and South America, where climatic conditions can vary significantly, the choice of DOT 3 should be accompanied by regular checks and maintenance. Compliance with local automotive standards is crucial, and buyers should ensure that they are sourcing products that meet ASTM or DIN standards.
What Are the Benefits of Using DOT 4 Brake Fluid?
Key Properties:
DOT 4 brake fluid has a higher boiling point (around 230°C or 446°F) compared to DOT 3, making it suitable for more demanding applications. It is also hygroscopic.
Pros & Cons:
The key advantage of DOT 4 is its enhanced performance in high-temperature conditions, which reduces the risk of vapor lock. However, it is more expensive than DOT 3 and still requires regular changes, ideally every 2 years.
Impact on Application:
DOT 4 is compatible with ABS systems and is often used in mid-range and performance vehicles, providing better safety margins.
Considerations for International Buyers:
European buyers, particularly in countries like France and the UK, should ensure that their brake fluid meets the required specifications. Compliance with EU regulations and standards is essential, and buyers should be aware of the potential for counterfeit products in the market.
Why Choose DOT 5 Brake Fluid for Specialized Applications?
Key Properties:
DOT 5 is silicone-based and non-hygroscopic, which means it does not absorb moisture. Its boiling point is around 260°C (500°F).
Pros & Cons:
The primary advantage of DOT 5 is its excellent stability and resistance to moisture, which results in longer intervals between changes, typically every 3-5 years. However, it is not compatible with glycol-based fluids, which can complicate maintenance.
Impact on Application:
DOT 5 is ideal for classic cars and vehicles that may be stored for long periods, as it prevents corrosion and maintains performance.
Considerations for International Buyers:
Buyers in the Middle East and Europe should be cautious about the compatibility of DOT 5 with existing brake systems. Ensuring compliance with local automotive standards is vital, and buyers should verify the product’s authenticity to avoid issues with performance.
What Are the Advantages of Mineral Oil-Based Brake Fluids?
Key Properties:
Mineral oil-based fluids are derived from refined petroleum and offer a high boiling point and excellent lubricating properties.
Pros & Cons:
These fluids are known for their longevity and stability, making them suitable for long-term use. However, they can be more expensive and may not be compatible with all brake systems.
Impact on Application:
Mineral oil-based fluids are often used in specialized applications, such as in bicycles and some automotive systems, where their unique properties can be fully leveraged.
Considerations for International Buyers:
In regions with varying climate conditions, such as Africa and South America, buyers should ensure that the mineral oil-based fluids they choose comply with local standards and regulations. Understanding the specific application requirements is crucial for optimal performance.
Summary Table of Brake Fluid Materials
Material | Typical Use Case for how often to change brake fluid | Key Advantage | Key Disadvantage/Limitation | Relative Cost (Low/Med/High) |
---|---|---|---|---|
DOT 3 | Standard vehicles, moderate conditions | Cost-effective | Absorbs moisture, needs frequent changes | Low |
DOT 4 | Mid-range and performance vehicles | Higher boiling point | More expensive, still hygroscopic | Medium |
DOT 5 | Classic cars, long-term storage | Non-hygroscopic, longer intervals | Not compatible with glycol fluids | High |
Mineral Oil-Based | Specialized applications (e.g., bicycles) | Excellent stability | Compatibility issues with some systems | Medium |
This guide provides an overview of the key materials used in brake fluids, highlighting their properties, advantages, and considerations for international B2B buyers. Understanding these factors is critical for making informed purchasing decisions that align with specific application requirements and regional standards.
In-depth Look: Manufacturing Processes and Quality Assurance for how often to change brake fluid
What Are the Main Stages of Brake Fluid Manufacturing Processes?
Understanding the manufacturing processes of brake fluid is crucial for B2B buyers, particularly those sourcing from diverse regions such as Africa, South America, the Middle East, and Europe. The production of brake fluid involves several key stages that ensure the final product meets performance and safety standards.
-
Material Preparation: The first step in brake fluid manufacturing involves the careful selection and preparation of raw materials. Brake fluids are typically formulated from glycol ethers or silicone-based compounds. Suppliers must ensure that these materials are free from contaminants and meet specified chemical properties to guarantee optimal performance.
-
Forming: In this stage, the raw materials are blended under controlled conditions. The formulation process requires precise control over temperature and mixing times to achieve the desired viscosity and boiling point. Advanced mixing techniques, such as high-shear mixing, are often employed to ensure uniformity in the final product.
-
Assembly: Once the fluid is formed, it is transferred to storage tanks or directly into packaging. During this phase, stringent hygiene and cleanliness protocols must be followed to prevent contamination. Packaging must also protect the fluid from exposure to air and moisture, which can degrade its quality.
-
Finishing: The final stage involves quality checks and labeling. Brake fluid must be packaged in containers that meet international safety standards to prevent leakage and ensure easy handling. Labels should provide essential information, including the fluid’s specifications and recommended usage guidelines.
What Are the Key Quality Assurance Standards for Brake Fluid?
Quality assurance (QA) is critical in brake fluid manufacturing, as any compromise can lead to safety hazards. B2B buyers must be aware of international and industry-specific standards that govern the quality of brake fluids.
-
International Standards: ISO 9001 is the most recognized quality management standard globally. Manufacturers that comply with ISO 9001 demonstrate their commitment to quality and customer satisfaction. This certification is crucial for B2B buyers who want assurance that their suppliers adhere to best practices in manufacturing.
-
Industry-Specific Standards: In addition to ISO, brake fluids must often comply with specific standards such as the European Union’s CE marking, which indicates conformity with health, safety, and environmental protection standards. The American Petroleum Institute (API) also sets guidelines for brake fluid performance, particularly for those sourced from North America.
How Are Quality Control Checkpoints Implemented in Brake Fluid Production?
Quality control (QC) is integral to the brake fluid manufacturing process. B2B buyers should understand the various QC checkpoints and testing methods employed by manufacturers to ensure product reliability.
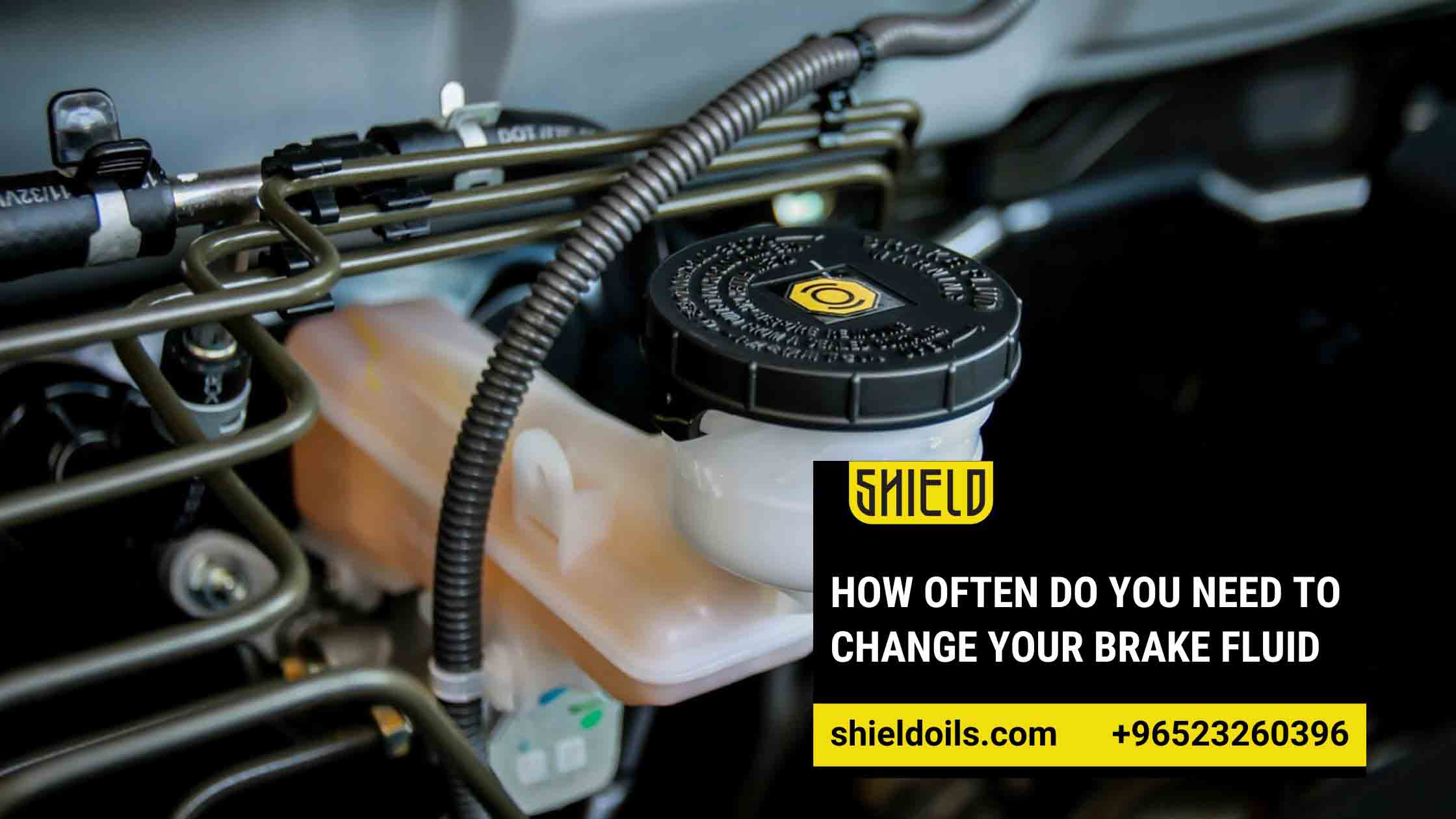
A stock image related to how often to change brake fluid.
-
Incoming Quality Control (IQC): This checkpoint involves testing raw materials upon arrival at the manufacturing facility. Suppliers must conduct chemical and physical tests to ensure that incoming materials meet predefined specifications.
-
In-Process Quality Control (IPQC): Throughout the manufacturing process, IPQC checks are performed to monitor variables such as temperature, pressure, and viscosity. This continuous monitoring helps identify any deviations from the desired specifications and allows for immediate corrective actions.
-
Final Quality Control (FQC): Before the brake fluid is packaged, a final round of quality checks is conducted. This includes testing for boiling point, viscosity, and pH levels, ensuring that the final product meets all relevant standards.
What Common Testing Methods Are Used to Ensure Brake Fluid Quality?
To maintain high-quality standards, manufacturers employ several testing methods throughout the production process:
-
Viscosity Testing: This test measures the fluid’s resistance to flow, which is critical for brake performance. A viscometer is typically used to assess this property.
-
Boiling Point Testing: Brake fluid must have a high boiling point to prevent vapor lock during operation. This is usually measured using a boiling point apparatus.
-
pH Testing: The acidity or alkalinity of brake fluid can significantly affect its performance. pH meters are employed to ensure that the fluid remains within the acceptable range.
How Can B2B Buyers Verify Supplier Quality Control Processes?
Verifying the quality control processes of suppliers is essential for B2B buyers looking to source brake fluid. Here are several strategies to ensure the reliability of suppliers:
-
Conduct Audits: Regular audits of suppliers can help verify their compliance with quality standards. Buyers should develop a checklist based on relevant certifications and industry standards.
-
Request Quality Assurance Reports: Suppliers should be able to provide documentation demonstrating their adherence to quality standards, including test results and compliance certificates.
-
Engage Third-Party Inspectors: Utilizing third-party inspection services can provide an unbiased assessment of a supplier’s manufacturing practices. These inspections can identify potential issues that may not be apparent through standard audits.
What Are the Quality Control Nuances for International B2B Buyers?
International B2B buyers face unique challenges when sourcing brake fluid. Understanding these nuances can help buyers make informed decisions.
-
Regional Standards Compliance: Different regions may have varying regulations regarding brake fluid quality. Buyers must ensure that their suppliers comply with local and international standards relevant to their target market.
-
Cultural Considerations: Communication styles and business practices vary across regions. Buyers should be aware of these differences when negotiating contracts and discussing quality expectations with suppliers.
-
Logistical Challenges: Importing brake fluid can pose logistical challenges, including transportation conditions that affect product quality. Buyers should work closely with suppliers to ensure that products are transported under optimal conditions.
By understanding these manufacturing processes and quality assurance measures, B2B buyers can make informed decisions when sourcing brake fluid from international suppliers. This knowledge not only fosters trust but also enhances the overall safety and performance of the products they provide.
Practical Sourcing Guide: A Step-by-Step Checklist for ‘how often to change brake fluid’
Introduction: Why is a Brake Fluid Change Schedule Essential for B2B Buyers?
Understanding how often to change brake fluid is critical for maintaining vehicle safety and performance, especially in commercial fleets. This guide will help B2B buyers establish a systematic approach to sourcing brake fluid and related services, ensuring that their vehicles remain compliant with safety regulations and operationally efficient. By following this checklist, buyers from Africa, South America, the Middle East, and Europe can make informed decisions that optimize their procurement processes.
Step 1: Assess Your Fleet’s Needs
Before you can determine how often to change brake fluid, you need to evaluate your fleet’s specific requirements. Consider factors such as vehicle type, usage patterns, and environmental conditions.
- Vehicle Type: Different vehicles may have unique brake fluid requirements.
- Usage Patterns: High-frequency usage may necessitate more frequent fluid changes.
Step 2: Define Your Technical Specifications
Establish clear technical specifications for the brake fluid you need. This will help in sourcing products that meet industry standards and your operational needs.
- Fluid Type: Identify whether you need DOT 3, DOT 4, or DOT 5.1 brake fluid.
- Compatibility: Ensure that the fluid is compatible with your vehicles’ braking systems to prevent corrosion or failure.
Step 3: Evaluate Potential Suppliers
Before committing, it’s crucial to vet suppliers thoroughly. Request company profiles, case studies, and references from buyers in a similar industry or region.
- Supplier Reputation: Look for suppliers with a proven track record in brake fluid quality.
- Certifications: Verify that the suppliers’ products meet international safety and quality standards.
Step 4: Request Samples for Testing
Always ask for product samples before making a bulk purchase. Testing the brake fluid will allow you to assess its performance and compatibility with your vehicles.
- Performance Tests: Conduct tests to evaluate boiling point, viscosity, and moisture absorption.
- Compliance Checks: Ensure the samples meet your defined technical specifications.
Step 5: Establish a Maintenance Schedule
Work with your service team to create a maintenance schedule that outlines when to change brake fluid. This proactive approach can extend the lifespan of your braking systems.
- Frequency Guidelines: Depending on usage, a common recommendation is to change brake fluid every 1-2 years.
- Documentation: Keep detailed records of all maintenance activities for compliance and future reference.
Step 6: Negotiate Terms and Conditions
Once you have selected a supplier, negotiate terms and conditions that reflect your purchasing needs. This includes pricing, delivery schedules, and return policies.
- Volume Discounts: Inquire about discounts for bulk purchases.
- Warranty and Returns: Understand the warranty and return policies in case the product does not meet your expectations.
Step 7: Monitor and Review Supplier Performance
After procurement, continuously monitor the supplier’s performance to ensure they meet your expectations. Conduct regular reviews to adapt to any changes in your operational needs.
- Feedback Mechanism: Establish a feedback loop to report any issues with the brake fluid.
- Supplier Audits: Schedule periodic audits to ensure ongoing compliance with quality standards.
By following these steps, B2B buyers can streamline their procurement of brake fluid, ensuring safety and efficiency in their operations.
Comprehensive Cost and Pricing Analysis for how often to change brake fluid Sourcing
What Are the Key Cost Components in Brake Fluid Sourcing?
When considering the sourcing of brake fluid, international B2B buyers must understand the various cost components involved. Key components include:
-
Materials: The primary cost driver is the quality of the brake fluid itself. The composition, whether it’s glycol-based or mineral oil-based, significantly affects pricing. Higher-quality fluids that meet stringent international standards often come at a premium.
-
Labor: Labor costs vary by region. In emerging markets like Africa and South America, labor may be less expensive, but this could compromise quality if not managed properly. Conversely, European manufacturers may have higher labor costs but often provide superior quality assurance.
-
Manufacturing Overhead: This includes fixed costs associated with production facilities, utilities, and machinery. Manufacturers in Europe might face higher overhead due to stricter regulations and environmental compliance, impacting the overall pricing structure.
-
Tooling and Equipment: The setup costs for producing specialized brake fluids can be substantial. Custom formulations may require unique equipment, thus raising initial investment costs, which can affect pricing in the long run.
-
Quality Control (QC): Rigorous QC processes ensure that the brake fluid meets safety and performance standards. This aspect can add to the cost but is essential for reliability, especially in markets that prioritize safety.
-
Logistics: Shipping costs can be significant, particularly for international transactions. Factors such as distance, mode of transport, and customs duties all influence the final pricing.
-
Margin: Suppliers will add a margin to cover risks, unexpected costs, and profit. Understanding the average margins in your region can help in negotiation.
What Influences the Price of Brake Fluid in the B2B Market?
Several factors can influence the price of brake fluid in the B2B market, especially for international buyers:
-
Volume and Minimum Order Quantity (MOQ): Larger orders typically lead to lower per-unit costs. Buyers should negotiate MOQs that align with their inventory and usage rates.
-
Specifications and Customization: Custom formulations or fluids meeting specific regional standards may incur higher costs. Buyers should assess whether they need customized solutions or if standard products suffice.
-
Material Quality and Certifications: Brake fluids that meet international certifications (e.g., DOT, ISO) will generally command higher prices. Buyers should weigh the importance of certifications against potential cost savings from lower-quality options.
-
Supplier Factors: The reputation and reliability of the supplier can significantly affect pricing. Established suppliers with a track record of quality may charge more but can reduce risks associated with product failure.
-
Incoterms: Understanding the Incoterms used in contracts can affect total costs. For instance, DDP (Delivered Duty Paid) terms may include additional charges that should be considered in the overall cost analysis.
What Negotiation Tips Should International Buyers Consider?
When engaging in negotiations for brake fluid sourcing, international buyers should keep the following tips in mind:
-
Research and Benchmarking: Understand market prices and compare multiple suppliers. This knowledge will empower you during negotiations.
-
Focus on Total Cost of Ownership (TCO): Evaluate not just the purchase price but also the long-term costs associated with quality, reliability, and potential failure. A lower upfront price might lead to higher maintenance costs if the fluid does not perform adequately.
-
Build Relationships: Establishing strong relationships with suppliers can lead to better pricing and terms over time. Trust can result in favorable negotiations, including discounts for repeat business.
-
Leverage Economic Trends: Keep an eye on economic conditions and currency fluctuations that may impact pricing. Timing your orders can yield significant savings.
-
Consider Regional Differences: Be aware of the specific market dynamics in Africa, South America, the Middle East, and Europe. Tailoring your approach based on regional insights can enhance negotiation outcomes.
Disclaimer on Pricing
Prices for brake fluid can vary widely based on factors discussed above. The information provided is indicative and should be verified with suppliers to obtain accurate quotes tailored to your specific needs.
Alternatives Analysis: Comparing how often to change brake fluid With Other Solutions
Understanding Alternatives to Changing Brake Fluid
When it comes to maintaining the safety and performance of vehicles, understanding how often to change brake fluid is crucial. However, there are alternative solutions that can achieve similar results in ensuring braking efficiency and safety. This section explores viable alternatives to the traditional brake fluid change, helping international B2B buyers make informed decisions based on their unique operational contexts.
Comparison Table of Brake Fluid Change Alternatives
Comparison Aspect | How Often To Change Brake Fluid | Brake Fluid Testing Equipment | Brake Fluid Condition Monitoring Systems |
---|---|---|---|
Performance | Essential for safety; prevents brake failure | Provides immediate assessment; less frequent changes possible | Continuous monitoring; predictive maintenance |
Cost | Relatively low cost for periodic changes | Initial investment high; potential savings over time | Higher upfront costs; long-term savings through fewer breakdowns |
Ease of Implementation | Simple; requires standard maintenance procedures | Requires technician training and calibration | Installation may be complex; requires integration with existing systems |
Maintenance | Regular checks needed; low maintenance | Periodic calibration and maintenance required | Minimal; automated alerts reduce manual checks |
Best Use Case | Standard vehicles in routine use | Fleet operations needing frequent checks | High-use environments where predictive maintenance is beneficial |
Pros and Cons of Brake Fluid Testing Equipment
Brake fluid testing equipment provides an alternative to changing brake fluid by assessing its condition regularly. This method can identify when fluid degradation occurs, allowing for more precise maintenance scheduling. Pros include the ability to extend the interval between changes, potentially reducing overall costs. However, the cons involve the initial investment in equipment and the necessity for technician training to ensure accurate results. For businesses with high vehicle utilization, this method can be particularly advantageous as it minimizes downtime and enhances safety.
Exploring Brake Fluid Condition Monitoring Systems
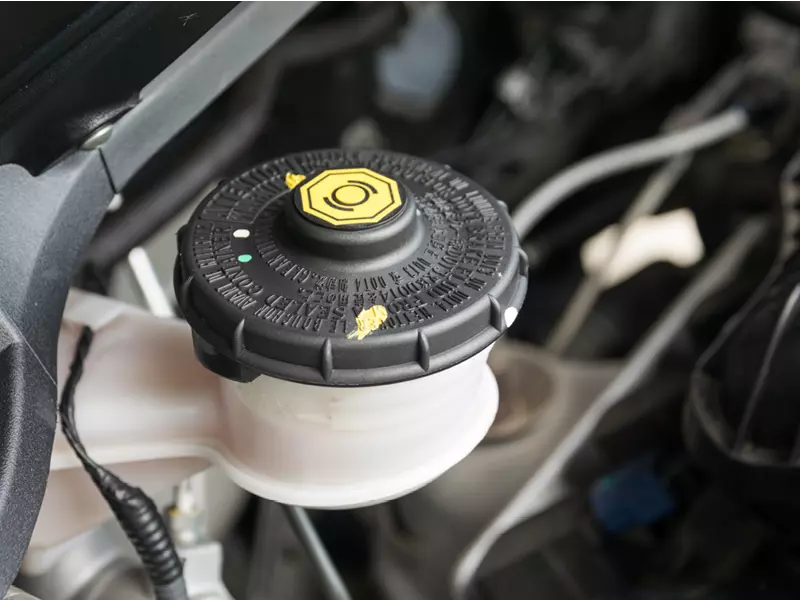
A stock image related to how often to change brake fluid.
Another alternative is the implementation of brake fluid condition monitoring systems. These systems continuously track the quality of brake fluid and provide real-time data on its condition. The primary advantage of this technology is its predictive capability, allowing businesses to perform maintenance before issues arise. However, the disadvantages include higher upfront costs and the complexity of installation. This solution is best suited for fleets or high-use environments where the potential for brake fluid degradation is significant, as it ensures optimal performance and safety.
How Should B2B Buyers Choose the Right Solution?
When considering how often to change brake fluid or alternative solutions, B2B buyers should evaluate their specific operational needs, budget constraints, and maintenance capabilities. For companies operating in high-demand environments, investing in testing equipment or monitoring systems may yield long-term savings and enhance safety. In contrast, businesses with standard usage patterns might find periodic changes to be the most cost-effective and straightforward approach. Ultimately, the choice should align with the organization’s operational strategy, ensuring safety and efficiency are maintained without incurring unnecessary costs.
Essential Technical Properties and Trade Terminology for how often to change brake fluid
What Are the Key Technical Properties Related to Brake Fluid Changes?
Understanding the essential technical properties of brake fluid is crucial for B2B buyers involved in automotive maintenance and manufacturing. The following specifications are vital for ensuring optimal brake performance and safety.
1. Boiling Point
The boiling point of brake fluid is a critical property that determines its performance under high-temperature conditions. Brake fluid absorbs moisture over time, which lowers its boiling point and can lead to brake failure. It is categorized into DOT grades (e.g., DOT 3, DOT 4, DOT 5.1), with higher grades having higher boiling points. For international buyers, selecting the right grade based on environmental conditions is essential.
2. Viscosity
Viscosity measures the fluid’s resistance to flow at various temperatures. Brake fluid must maintain optimal viscosity to ensure effective hydraulic pressure transfer in braking systems. Different climates can affect fluid performance; thus, understanding viscosity ratings helps buyers choose fluids suitable for specific regional conditions, such as those experienced in Africa or South America.
3. Chemical Composition
Brake fluids are typically glycol-based or silicone-based. Glycol-based fluids are hygroscopic, meaning they absorb moisture, while silicone-based fluids do not. The choice of chemical composition affects the fluid’s lifespan and maintenance schedule. B2B buyers should consider compatibility with vehicle systems and regional regulations when selecting brake fluid types.
4. pH Level
The pH level of brake fluid is an indicator of its acidity or alkalinity. An optimal pH level ensures the fluid does not corrode internal components of the braking system. Regular testing of brake fluid pH is recommended, especially for fleets operating in harsh environments. Buyers should prioritize fluids with stable pH levels to ensure system longevity.
5. Compatibility with Materials
Brake fluid must be compatible with various materials used in braking systems, including rubber seals and metal components. Incompatibility can lead to seal degradation and system failures. B2B buyers should verify that the brake fluid meets OEM specifications for compatibility, especially when sourcing from international suppliers.
What Are Common Trade Terms Related to Brake Fluid Procurement?
Familiarity with industry terminology can facilitate smoother transactions and enhance communication between B2B buyers and suppliers.
1. OEM (Original Equipment Manufacturer)
OEM refers to companies that produce parts or fluids to be used in the manufacturing of vehicles. Understanding OEM standards is crucial for B2B buyers, as it ensures that the brake fluid meets the specifications required for particular vehicle models.
2. MOQ (Minimum Order Quantity)
MOQ is the smallest quantity of a product that a supplier is willing to sell. Knowing the MOQ is essential for B2B buyers to manage inventory effectively and negotiate terms that align with their operational needs. This is particularly relevant for businesses in regions with varying demand levels.
3. RFQ (Request for Quotation)
An RFQ is a document sent to suppliers requesting pricing for specific quantities and specifications of products. For international buyers, preparing a comprehensive RFQ ensures clarity and helps suppliers provide accurate quotes, facilitating better negotiation outcomes.
4. Incoterms (International Commercial Terms)
Incoterms are a set of predefined international rules that clarify the responsibilities of buyers and sellers in global trade. Understanding Incoterms helps B2B buyers navigate shipping logistics, risk management, and cost calculations when sourcing brake fluid internationally.
5. Lifecycle Cost
Lifecycle cost refers to the total cost of owning and operating a product over its lifespan, including purchase price, maintenance, and disposal. B2B buyers should evaluate the lifecycle cost of brake fluid, considering factors such as frequency of changes and potential system failures, to make informed purchasing decisions.
By grasping these technical properties and trade terms, international B2B buyers can make more informed decisions regarding brake fluid procurement, ensuring safety, compliance, and operational efficiency in their automotive operations.
Navigating Market Dynamics and Sourcing Trends in the how often to change brake fluid Sector
What are the Current Market Dynamics in the Brake Fluid Sector?
The global brake fluid market is witnessing significant shifts driven by advancements in automotive technology and increasing safety regulations. As vehicles become more sophisticated, the demand for high-quality brake fluids that enhance performance and safety is rising. International B2B buyers, particularly from Africa, South America, the Middle East, and Europe, should be aware of these dynamics as they navigate sourcing strategies. The rise of electric vehicles (EVs) also presents an emerging trend; manufacturers are innovating brake fluids compatible with EV braking systems, which often require different formulations.
Additionally, the growing emphasis on preventive maintenance is influencing how often brake fluid should be changed. Industry standards suggest a replacement every two years or 24,000 miles, but this can vary based on vehicle type and usage. Buyers should consider sourcing suppliers that offer clear guidance on these intervals and provide products that meet or exceed industry standards. Furthermore, the integration of digital technologies, such as IoT sensors in vehicles, is leading to a more data-driven approach in maintenance schedules, allowing for tailored sourcing solutions.
How is Sustainability Influencing Brake Fluid Sourcing Decisions?
Sustainability has become a critical factor for B2B buyers in the brake fluid sector. The environmental impact of brake fluid production and disposal is gaining attention, prompting companies to seek eco-friendly alternatives. Buyers should prioritize suppliers that adhere to sustainable practices, such as utilizing biodegradable materials and minimizing waste in their production processes.
Ethical sourcing is equally important, with a focus on ensuring that raw materials are obtained responsibly. Certifications such as ISO 14001 for environmental management systems can serve as indicators of a supplier’s commitment to sustainability. Additionally, products with green certifications not only reflect a company’s ethical stance but can also enhance brand reputation in the marketplace. For international buyers, aligning sourcing strategies with sustainability goals not only meets regulatory demands but also appeals to a growing segment of environmentally-conscious consumers.
What is the Historical Context of Brake Fluid Development?
The evolution of brake fluid has been closely tied to advancements in automotive technology. Initially, brake fluids were primarily glycol-based, which offered acceptable performance but lacked stability over time. Over the years, manufacturers have developed synthetic brake fluids that provide improved boiling points and moisture resistance, significantly enhancing safety.
In the late 20th century, the introduction of new standards and regulations, particularly in Europe and North America, led to further innovation in brake fluid formulations. These developments have resulted in a broader array of products available in the market today, allowing B2B buyers to choose from options that best suit their specific vehicle types and operational needs. Understanding this historical context can provide insights into current sourcing trends and the importance of product quality in the brake fluid sector.
Frequently Asked Questions (FAQs) for B2B Buyers of how often to change brake fluid
-
How often should brake fluid be changed for optimal vehicle performance?
Regular maintenance is crucial for vehicle safety and performance. It is generally recommended to change brake fluid every 1 to 2 years, or approximately every 20,000 to 45,000 kilometers, depending on the vehicle type and usage conditions. For businesses operating fleets or in regions with extreme weather, more frequent changes may be necessary. Monitoring moisture content in the brake fluid can also provide insights into when it needs to be replaced, as high moisture levels can lead to reduced braking efficiency. -
What are the signs that brake fluid needs to be changed?
Key indicators that brake fluid requires changing include a spongy brake pedal, decreased braking responsiveness, and a change in the fluid’s color from clear to a darker hue. Additionally, if your brake warning light activates, it may signal low brake fluid levels or contamination. Regular inspections and testing of brake fluid quality can help prevent potential brake system failures, ensuring safety for drivers and reducing liability for businesses. -
How can I assess the quality of brake fluid before purchasing?
To assess brake fluid quality, consider conducting a moisture content test, which can indicate how much water has entered the fluid, affecting its boiling point. Look for certifications from recognized organizations, which ensure the fluid meets industry standards. Requesting samples for testing before committing to a bulk purchase can also help ensure you’re sourcing high-quality products that comply with safety regulations in your region. -
What are the implications of using low-quality brake fluid?
Using low-quality brake fluid can compromise vehicle safety, leading to brake failure and increased repair costs. Poor-quality fluid may have a lower boiling point, which can cause vapor lock in high-performance situations. For B2B buyers, sourcing from reputable suppliers with proven track records is essential to ensure compliance with safety standards and to protect your investment in fleet vehicles. -
How can I find reliable suppliers for brake fluid in international markets?
To find reliable suppliers, start by researching manufacturers with a strong reputation in the brake fluid market. Utilize trade platforms and industry-specific trade shows to connect with potential suppliers. Verify their certifications, quality assurance processes, and customer reviews. Building relationships with suppliers through direct communication can also help assess their reliability and responsiveness to your needs. -
What are the typical minimum order quantities (MOQ) for brake fluid?
Minimum order quantities (MOQ) for brake fluid can vary significantly between suppliers and regions. Generally, MOQs range from 500 liters to several thousand liters, depending on the manufacturer and your specific needs. When negotiating with suppliers, consider discussing flexible MOQs, especially if your company is smaller or just starting. This can help mitigate risk while ensuring you have adequate stock to meet demand. -
What payment terms should I consider when sourcing brake fluid internationally?
When sourcing brake fluid, payment terms can vary by supplier and region. Common terms include advance payment, letters of credit, or net 30/60/90 days. It’s crucial to negotiate terms that align with your cash flow and financial strategy. Additionally, consider the implications of currency fluctuations and transaction fees in international trade, and explore options such as escrow services for larger orders to mitigate risks. -
What logistics considerations should I keep in mind when importing brake fluid?
Logistics for importing brake fluid include understanding shipping regulations, customs duties, and the specific handling requirements for hazardous materials. Ensure that your suppliers provide appropriate documentation for transportation and compliance with local laws. Partnering with a logistics company experienced in hazardous goods can streamline the process, ensuring timely delivery and reducing the risk of delays due to regulatory issues.
Important Disclaimer & Terms of Use
⚠️ Important Disclaimer
The information provided in this guide, including content regarding manufacturers, technical specifications, and market analysis, is for informational and educational purposes only. It does not constitute professional procurement advice, financial advice, or legal advice.
While we have made every effort to ensure the accuracy and timeliness of the information, we are not responsible for any errors, omissions, or outdated information. Market conditions, company details, and technical standards are subject to change.
B2B buyers must conduct their own independent and thorough due diligence before making any purchasing decisions. This includes contacting suppliers directly, verifying certifications, requesting samples, and seeking professional consultation. The risk of relying on any information in this guide is borne solely by the reader.
Strategic Sourcing Conclusion and Outlook for how often to change brake fluid
In the realm of strategic sourcing, understanding how often to change brake fluid is not merely a matter of maintenance; it is a critical component of ensuring operational safety and efficiency. For international B2B buyers, particularly in regions like Africa, South America, the Middle East, and Europe, implementing a proactive approach to brake fluid management can significantly reduce the risk of vehicle malfunctions and enhance overall fleet reliability.
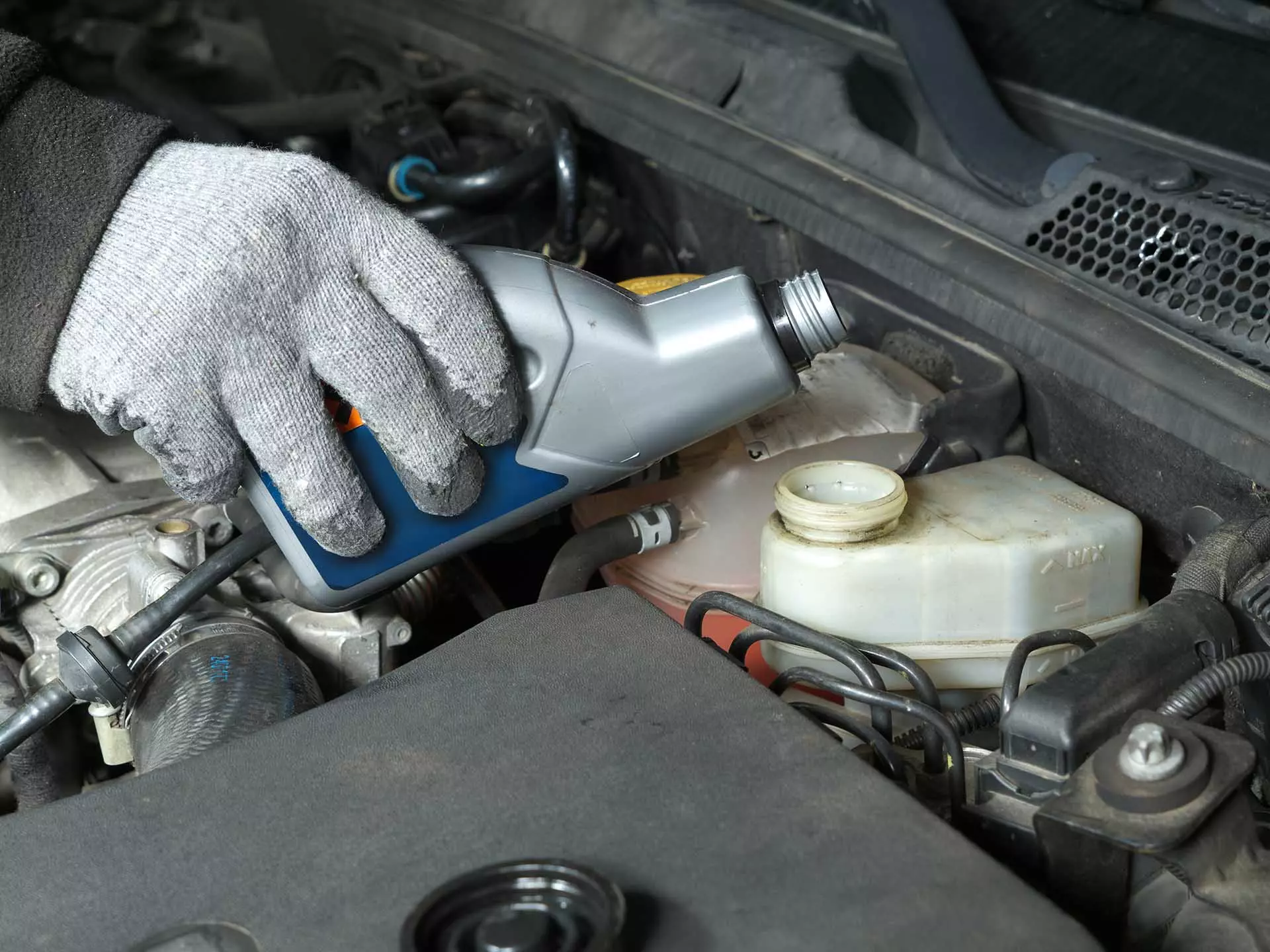
A stock image related to how often to change brake fluid.
Regularly scheduled brake fluid changes—typically every 1-2 years or according to the manufacturer’s guidelines—should be integrated into your procurement strategy. This ensures that your fleet operates at peak performance, minimizing downtime and maintenance costs. Furthermore, sourcing high-quality brake fluid from reputable suppliers can lead to better performance and increased safety for your vehicles.
As you consider your strategic sourcing decisions, prioritize relationships with suppliers who understand the unique demands of your geographic market. By fostering these partnerships, you can stay informed about best practices and innovations in brake fluid technology.
Looking ahead, embrace the opportunity to enhance your fleet’s safety and efficiency through informed sourcing decisions. Commit to regular assessments of your brake fluid management practices, and position your business for long-term success in a competitive marketplace.