Maximize Efficiency: The Ultimate Tool Pouch Guide (2025)
Introduction: Navigating the Global Market for tool pouch
In today’s competitive landscape, sourcing the right tool pouch is crucial for businesses looking to optimize efficiency and organization in their operations. International B2B buyers face the challenge of selecting tool pouches that not only meet industry standards but also cater to specific applications, whether in construction, manufacturing, or service sectors. This comprehensive guide delves into various types of tool pouches, their applications, and essential factors to consider when sourcing, including supplier vetting and cost analysis.
Understanding the diversity of tool pouch options available in the market is vital for making informed purchasing decisions. From heavy-duty pouches designed for rugged environments to lightweight, ergonomic models suitable for everyday use, this guide provides insights that help buyers select the best fit for their needs. Additionally, we will explore the importance of assessing suppliers, ensuring quality, and managing costs effectively.
This guide is specifically tailored for international B2B buyers from regions such as Africa, South America, the Middle East, and Europe, including countries like Egypt and the UK. By equipping you with the knowledge to navigate the global market for tool pouches, we empower you to make strategic decisions that enhance productivity and drive business success.
Understanding tool pouch Types and Variations
Type Name | Key Distinguishing Features | Primary B2B Applications | Brief Pros & Cons for Buyers |
---|---|---|---|
Waist Tool Pouch | Attaches to a belt, compact, easy access to tools | Construction, electrical work | Pros: Lightweight, hands-free access. Cons: Limited storage space. |
Tool Roll | Foldable, organized pockets, portable | Automotive, woodworking | Pros: Versatile, easy to transport. Cons: Requires time to roll/unroll. |
Multi-Pocket Pouch | Multiple compartments, various sizes available | HVAC, plumbing | Pros: High organization, accommodates many tools. Cons: Can be bulky. |
Suspender Pouch | Suspended from shoulders, distributes weight evenly | Heavy-duty construction, masonry | Pros: Reduces strain, increased carrying capacity. Cons: May require adjustment for comfort. |
Electrician’s Pouch | Specialized pockets for tools like wire strippers, testers | Electrical contracting | Pros: Tailored for specific tools, enhances efficiency. Cons: Limited to electrical tools. |
What are the characteristics of a Waist Tool Pouch?
Waist tool pouches are designed for easy attachment to a belt, providing immediate access to essential tools without the need for bulky bags. They typically feature a few pockets that can hold hand tools, fasteners, or other small items. Ideal for construction and electrical work, these pouches enhance mobility and allow workers to keep their hands free. B2B buyers should consider the weight and size of the pouch to ensure it meets their specific needs while maintaining comfort throughout the workday.
How does a Tool Roll differ from other types?
Tool rolls are portable storage solutions that allow users to organize their tools in a compact, foldable format. They often feature various pockets and compartments that can accommodate different tools, making them suitable for industries like automotive and woodworking. The key advantage of a tool roll is its versatility and ease of transport. However, B2B buyers should consider the time it takes to roll and unroll the pouch, which may be a drawback in fast-paced work environments.
Why choose a Multi-Pocket Pouch for your team?
Multi-pocket pouches provide extensive organization with multiple compartments designed to hold a variety of tools and equipment. This type of pouch is particularly beneficial in industries such as HVAC and plumbing, where technicians often carry numerous tools. While they offer high organization, B2B buyers should be aware that multi-pocket pouches can be bulkier, potentially hindering mobility. Ensuring that the pouch is lightweight yet spacious enough for the required tools is essential for optimal functionality.
What advantages does a Suspender Pouch offer?
Suspender pouches are designed to be worn over the shoulders, distributing the weight of tools evenly and reducing strain on the lower back. This makes them particularly useful in heavy-duty construction and masonry work, where carrying substantial tools is common. While they enhance carrying capacity and comfort, B2B buyers should consider the need for adjustments to fit different body types and personal preferences, ensuring a secure and comfortable fit during use.
What features make an Electrician’s Pouch essential?
Electrician’s pouches are specifically tailored to accommodate the tools used by electrical contractors, such as wire strippers, testers, and other specialized equipment. These pouches often include dedicated pockets for quick access to essential tools, enhancing efficiency on the job. However, they may be limited in versatility, as they are designed primarily for electrical work. B2B buyers should evaluate whether their team requires specialized tools or if a more general-purpose pouch would suffice for their operations.
Related Video: Handyman’s Tool Bag TOUR! Best Bag EVER!?
Key Industrial Applications of tool pouch
Industry/Sector | Specific Application of Tool Pouch | Value/Benefit for the Business | Key Sourcing Considerations for this Application |
---|---|---|---|
Construction | On-site tool organization | Increases efficiency and reduces time spent searching for tools | Durability, weather resistance, and size options |
Automotive Repair | Mobile tool storage for technicians | Enhances mobility and quick access to tools during repairs | Lightweight materials and ergonomic design |
Electrical Installation | Compact storage for electrical tools | Improves safety and organization on job sites | Insulation properties and compatibility with tools |
Landscaping | Tool management for gardening equipment | Streamlines workflow and reduces tool loss | Resistance to outdoor elements and easy cleaning |
Manufacturing | Storage for assembly line tools | Optimizes production efficiency and minimizes downtime | Customization options and bulk ordering capabilities |
How Can Tool Pouches Enhance Efficiency in the Construction Industry?
In the construction sector, tool pouches are essential for on-site tool organization. They allow workers to keep essential tools within reach, significantly reducing the time wasted searching for items. For international buyers, especially in regions like Africa and South America, sourcing durable and weather-resistant pouches is crucial due to the varied environmental conditions. Buyers should consider the size options available to match their specific tool sets.
What Benefits Do Tool Pouches Provide to Automotive Repair Technicians?
Automotive repair technicians benefit greatly from mobile tool storage solutions like tool pouches. These pouches enhance mobility, allowing technicians to carry necessary tools directly to the vehicle they are working on. This increases efficiency and reduces the time spent moving back and forth to a toolbox. Buyers in the Middle East should prioritize lightweight materials and ergonomic designs to ensure comfort during long hours of use.
How Do Tool Pouches Improve Safety in Electrical Installations?
In the electrical installation industry, tool pouches are invaluable for storing electrical tools securely. They help improve safety by keeping tools organized and easily accessible, minimizing the risk of accidents caused by misplaced tools. Buyers in Europe, particularly in the UK, should look for pouches with insulation properties to ensure safe handling of electrical equipment, as well as compatibility with various tools.
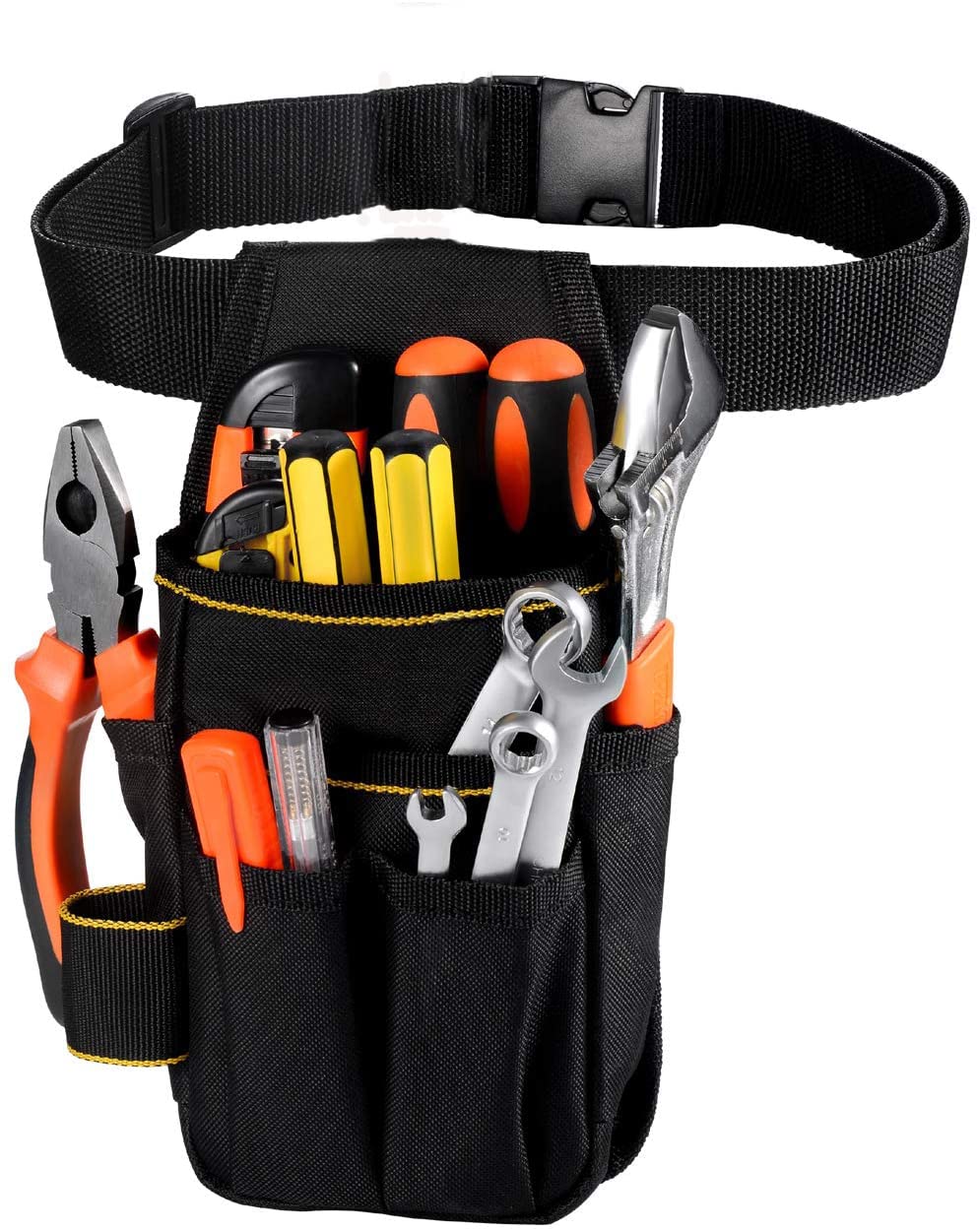
A stock image related to tool pouch.
Why Are Tool Pouches Important for Landscaping Professionals?
Landscaping professionals utilize tool pouches for effective management of gardening equipment. These pouches streamline workflow by allowing workers to carry multiple tools at once, reducing the time spent looking for items or making trips back to the shed. Buyers in Africa should consider sourcing pouches that are resistant to outdoor elements and easy to clean, as these features enhance longevity and usability in diverse climates.
How Can Tool Pouches Optimize Production in Manufacturing?
In manufacturing, tool pouches serve as essential storage solutions for assembly line tools. They help optimize production efficiency by minimizing downtime caused by searching for tools, thereby speeding up the assembly process. When sourcing tool pouches, businesses should consider customization options that allow for branding and bulk ordering capabilities to meet their specific production needs efficiently.
Related Video: CLEVER things to do with an Oscillating Multi-Tool!
3 Common User Pain Points for ‘tool pouch’ & Their Solutions
Scenario 1: The Dilemma of Durability in Extreme Conditions
The Problem: B2B buyers in sectors such as construction or maintenance often face the challenge of sourcing tool pouches that can withstand harsh environments. For instance, a contractor in Egypt may need a tool pouch that can endure high temperatures and dust without degrading. Similarly, buyers in South America might be looking for pouches that resist moisture in humid conditions. The inadequacy of typical tool pouches leads to frequent replacements, which not only incurs additional costs but also disrupts workflows.
The Solution: To address durability concerns, B2B buyers should prioritize sourcing tool pouches made from high-quality, weather-resistant materials such as ballistic nylon or heavy-duty polyester. When evaluating suppliers, request samples to test their performance in relevant environmental conditions. Additionally, consider pouches with reinforced stitching and heavy-duty zippers, which significantly enhance longevity. It’s also advisable to invest in pouches with modular designs that allow for the attachment of additional pockets or tools, thus increasing functionality while maintaining robustness. Establishing partnerships with manufacturers who specialize in custom solutions can also lead to tailored products that meet specific industry needs.
Scenario 2: Inadequate Organization Leading to Inefficiency
The Problem: Many B2B buyers discover that standard tool pouches lack adequate organizational features, leading to inefficiencies on job sites. For example, a buyer in the UK may find that their team spends too much time searching for the right tool amidst a cluttered pouch, resulting in wasted labor hours and decreased productivity. This issue is exacerbated when multiple team members share the same pouch, as different preferences for tool organization can lead to further disarray.
The Solution: To combat disorganization, look for tool pouches that offer customizable storage solutions, such as multiple compartments, elastic loops, and tool holders. When selecting a pouch, assess the layout and consider how tools will be used on-site. Opt for pouches with clear labeling or color-coded sections to facilitate quick access. Providing training to employees on effective organization practices can also significantly improve efficiency. Lastly, consider investing in digital inventory management tools that can help track tools and materials, ensuring that each team member knows where to find and return tools at the end of the day.
Scenario 3: The Struggle with Comfort and Accessibility
The Problem: Comfort and accessibility are critical pain points for B2B buyers purchasing tool pouches for their workforce. Workers who spend long hours on their feet, such as electricians or plumbers, often report discomfort from poorly designed pouches that can lead to fatigue or injury. Furthermore, pouches that are difficult to access can slow down work processes, affecting overall productivity.
The Solution: To enhance comfort and accessibility, seek out tool pouches designed with ergonomic features, such as padded belts or adjustable straps that distribute weight evenly across the body. Look for pouches that allow for easy access to frequently used tools, such as those with quick-release mechanisms or magnetic closures. Conduct trials with different designs to find which options your team prefers; employee feedback can provide invaluable insights. Additionally, regular training sessions on how to properly wear and adjust pouches can ensure that workers are using them in the most comfortable and efficient manner possible. By prioritizing ergonomics, you can foster a healthier and more productive work environment.
Strategic Material Selection Guide for tool pouch
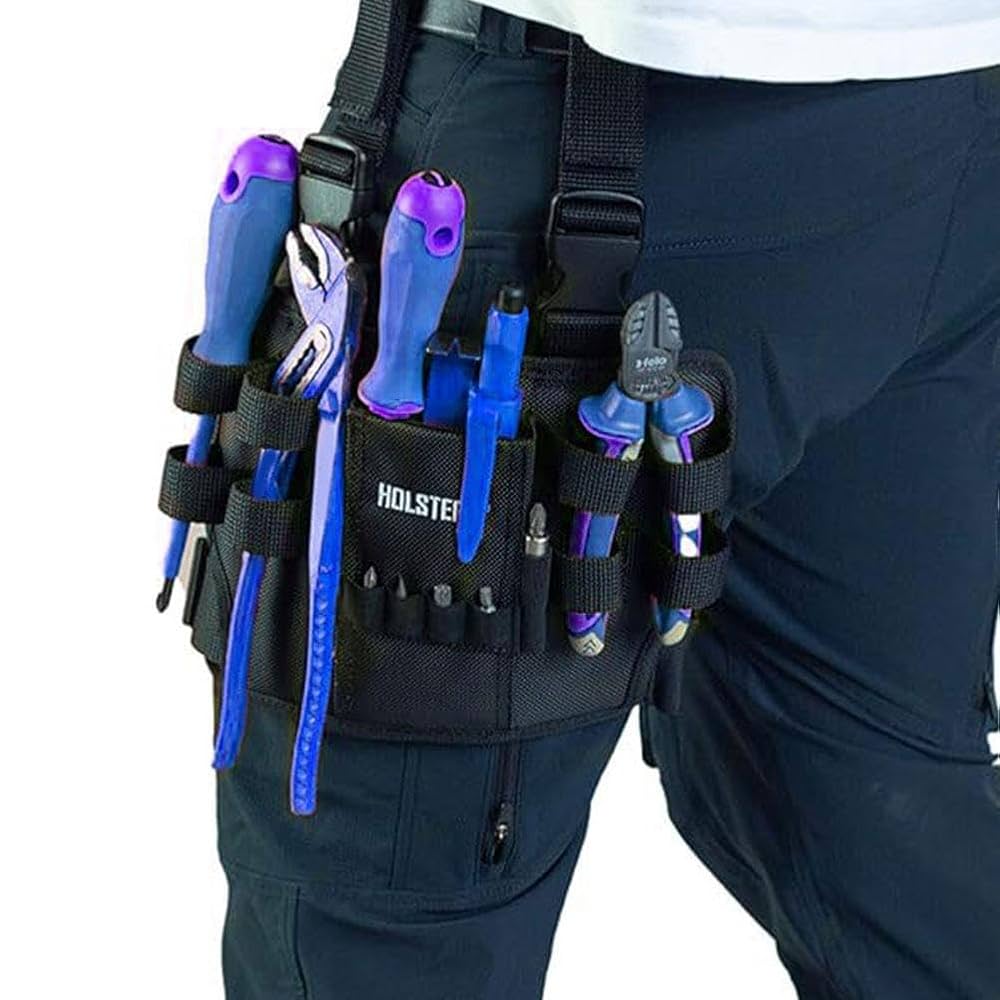
A stock image related to tool pouch.
When selecting materials for tool pouches, international B2B buyers must consider various factors, including durability, cost, and specific application needs. Below is an analysis of four common materials used in tool pouch manufacturing, focusing on their properties, advantages, disadvantages, and considerations for buyers from Africa, South America, the Middle East, and Europe.
What Are the Key Properties of Canvas for Tool Pouches?
Canvas is a popular choice for tool pouches due to its robust nature. Typically made from cotton or a blend of cotton and synthetic fibers, canvas offers excellent durability and resistance to wear and tear. Its temperature rating is generally suitable for moderate environments, while its breathability helps prevent moisture build-up.
Pros: Canvas is relatively inexpensive and easy to manufacture, making it a cost-effective option for bulk purchases. It is also lightweight and can be treated for water resistance.
Cons: While durable, canvas may not withstand extreme temperatures or heavy moisture exposure without additional treatments. Over time, it can fade and lose its structural integrity if not cared for properly.
Impact on Application: Canvas is suitable for general tool storage and light to moderate use. However, it may not be ideal for environments with high humidity or exposure to harsh chemicals.
Considerations for International Buyers: Buyers should ensure that the canvas meets local standards for durability and safety. In regions like Europe, compliance with REACH regulations is essential, while buyers in Africa and South America may prioritize cost and availability.
How Does Nylon Compare as a Material for Tool Pouches?
Nylon is another widely used material for tool pouches, known for its high strength-to-weight ratio. It is resistant to abrasion and has good chemical resistance, making it suitable for various environments, including those with exposure to oils and solvents.
Pros: Nylon is highly durable and can withstand heavy use without tearing. It is also lightweight and can be easily dyed, allowing for a variety of color options.
Cons: The primary drawback of nylon is its cost, which is generally higher than canvas. Additionally, it can be less breathable, leading to moisture retention if not designed with ventilation in mind.
Impact on Application: Nylon tool pouches are ideal for heavy-duty applications and environments where exposure to chemicals is common. They are also suitable for outdoor use due to their resistance to water and UV light.
Considerations for International Buyers: Buyers should check for compliance with ASTM standards, particularly regarding tensile strength and chemical resistance. Buyers in the Middle East may also seek materials that can withstand high temperatures.
What Are the Benefits and Drawbacks of Leather for Tool Pouches?
Leather is a classic material for tool pouches, known for its durability and aesthetic appeal. It offers excellent resistance to wear and tear, as well as natural water resistance.
Pros: Leather tool pouches are incredibly durable and can last for years with proper care. They also provide a professional appearance, making them suitable for high-end markets.
Cons: The main disadvantages of leather are its higher cost and the need for regular maintenance to prevent drying and cracking. It is also heavier than synthetic materials.
Impact on Application: Leather is suitable for professional environments where aesthetics and durability are paramount. However, it may not be the best choice for environments with high moisture or exposure to chemicals.
Considerations for International Buyers: Buyers should consider sourcing leather that meets ethical standards, such as those outlined by the Leather Working Group. Regulations regarding animal welfare may also vary by region, impacting sourcing decisions.
Why Is Polyester a Viable Option for Tool Pouches?
Polyester is a synthetic material that offers a good balance of strength and flexibility. It is resistant to shrinking, stretching, and wrinkling, making it a low-maintenance option.
Pros: Polyester is generally less expensive than nylon and leather while still providing decent durability. It is also resistant to mildew and fading, making it suitable for outdoor use.
Cons: While polyester is durable, it may not have the same strength as nylon and can be prone to tearing under extreme conditions. It is also less breathable than natural fibers.
Impact on Application: Polyester tool pouches are suitable for general-purpose use and outdoor applications where moisture resistance is important. They are not recommended for heavy-duty applications requiring high tensile strength.
Considerations for International Buyers: Buyers should ensure that polyester products comply with local environmental regulations, especially regarding manufacturing processes. In Europe, adherence to EU Ecolabel standards may be beneficial.
Summary Table of Material Properties for Tool Pouches
Material | Typical Use Case for Tool Pouch | Key Advantage | Key Disadvantage/Limitation | Relative Cost (Low/Med/High) |
---|---|---|---|---|
Canvas | General tool storage | Cost-effective and lightweight | Limited moisture resistance | Low |
Nylon | Heavy-duty applications | High durability and chemical resistance | Higher cost and less breathable | High |
Leather | Professional environments | Long-lasting and aesthetically pleasing | Expensive and requires maintenance | High |
Polyester | General-purpose and outdoor use | Affordable and mildew-resistant | Less durable than nylon | Medium |
This analysis provides international B2B buyers with essential insights into material selection for tool pouches, enabling informed purchasing decisions that align with their specific needs and regional standards.
In-depth Look: Manufacturing Processes and Quality Assurance for tool pouch
What Are the Key Stages in the Manufacturing Process of Tool Pouches?
The manufacturing process of tool pouches involves several critical stages to ensure quality and functionality. Understanding these stages can help B2B buyers make informed decisions about their suppliers.
Material Preparation: Selecting the Right Materials
The first step in manufacturing tool pouches is material preparation. Common materials include durable fabrics like nylon, polyester, and canvas, which are chosen for their strength and resistance to wear and tear. Additionally, buyers should consider materials that offer water resistance or enhanced durability based on the intended use of the tool pouch.
- Material Testing: Before production begins, materials undergo testing for tensile strength, abrasion resistance, and water repellency. This ensures that the selected materials meet industry standards and customer expectations.
How Is the Forming Process Executed for Tool Pouches?
Once the materials are prepared, the next phase is forming. This involves cutting the fabric into the necessary shapes and sizes for the tool pouch.
Cutting Techniques: Precision Matters
- Die Cutting: This technique uses sharp dies to cut multiple layers of fabric simultaneously, ensuring uniformity and precision.
- Laser Cutting: An advanced method that provides clean edges and can cut intricate designs, often preferred for custom tool pouches.
What Assembly Techniques Are Used in Tool Pouch Manufacturing?
After cutting, the assembly process begins. This stage is crucial as it brings together all components of the tool pouch.
Sewing and Assembly Methods
- Sewing: Reinforced stitching is essential for durability. Double-stitching and bar tacking at stress points are common practices to enhance the longevity of the pouch.
- Attachment of Accessories: Features such as pockets, straps, and zippers are added during this phase. Quality control during assembly ensures that these components function correctly and meet design specifications.
What Finishing Processes Are Important for Tool Pouches?
Finishing involves the final touches that enhance the appearance and functionality of the tool pouch.
Quality Finishing Techniques
- Waterproofing Treatments: Applying coatings or laminates to enhance water resistance.
- Quality Checks: Ensuring that the final product meets specifications in terms of appearance, functionality, and durability.
How Is Quality Assurance Implemented in Tool Pouch Manufacturing?
Quality assurance (QA) is vital in the manufacturing of tool pouches to ensure that products meet both international and industry-specific standards.
What International Standards Should B2B Buyers Look For?
ISO 9001 is a globally recognized standard for quality management systems. Compliance with ISO 9001 indicates that a manufacturer has processes in place to ensure consistent quality. For tool pouches, additional certifications may include:
- CE Marking: Indicates conformity with European health, safety, and environmental protection standards.
- API Certification: Relevant for tool pouches used in oil and gas industries, ensuring they meet specific safety and quality requirements.
What QC Checkpoints Are Critical for Tool Pouch Production?
Implementing quality control (QC) checkpoints throughout the manufacturing process is essential.
Key QC Checkpoints
- Incoming Quality Control (IQC): Materials are inspected upon arrival to ensure they meet specified standards.
- In-Process Quality Control (IPQC): Continuous checks during the manufacturing process to identify defects early.
- Final Quality Control (FQC): Comprehensive inspections of the finished product before shipping. This may include testing for functionality, appearance, and adherence to specifications.
Which Common Testing Methods Are Used for Tool Pouches?
Testing is an integral part of the quality assurance process. B2B buyers should understand the common testing methods applied to tool pouches:
- Tensile Strength Testing: Measures the maximum load the fabric can withstand before breaking.
- Water Resistance Testing: Evaluates how well the pouch can resist water penetration.
- Abrasion Resistance Testing: Assesses the durability of the material against wear and tear.
How Can B2B Buyers Verify Supplier Quality Control?
B2B buyers need to ensure that their suppliers maintain high-quality standards. Here are some ways to verify supplier QC:
Conducting Supplier Audits
- On-Site Audits: Visiting the manufacturing facility allows buyers to assess the production processes, QC practices, and overall operation.
- Requesting Quality Reports: Suppliers should provide documentation of their quality control processes, including results from IQC, IPQC, and FQC tests.
Utilizing Third-Party Inspections
Engaging third-party inspection services can provide an unbiased assessment of the manufacturing quality. These services can conduct random inspections and provide detailed reports on compliance with international standards.
What Are the Nuances of QC and Certification for International B2B Buyers?
International buyers, particularly from Africa, South America, the Middle East, and Europe, should consider specific nuances in QC and certifications:
- Understanding Local Standards: Familiarity with local regulations and standards is crucial for compliance and market acceptance.
- Customs and Import Regulations: Buyers must ensure that the tool pouches meet the import regulations of their respective countries, which may vary significantly.
- Cultural Considerations: Recognizing cultural preferences in design and functionality can enhance product acceptance in diverse markets.
By comprehensively understanding the manufacturing processes and quality assurance practices, B2B buyers can make informed decisions, ensuring they source high-quality tool pouches that meet their specific needs.
Practical Sourcing Guide: A Step-by-Step Checklist for ‘tool pouch’
The following is a comprehensive sourcing guide for B2B buyers interested in procuring tool pouches. This checklist will help you navigate the essential steps to ensure you select the best suppliers and products for your business needs.
Step 1: Define Your Technical Specifications
Start by clearly outlining the technical specifications for the tool pouches you require. Consider factors such as material durability, size, weight capacity, and specific features like pockets or tool retention systems. Having a detailed specification will streamline your search and ensure that suppliers understand your exact requirements.
Step 2: Research Market Trends and Needs
Understanding current market trends is crucial in sourcing tool pouches. Analyze what types of pouches are in demand in your target regions, such as Africa, South America, the Middle East, and Europe. Look for trends related to material preferences (e.g., eco-friendly materials) or design innovations that could provide your company with a competitive edge.
Step 3: Evaluate Potential Suppliers
Before committing, it’s crucial to vet suppliers thoroughly. Request company profiles, case studies, and references from buyers in a similar industry or region. Pay attention to their production capabilities, quality control processes, and customer service reputation to ensure they can meet your requirements.
- Supplier Certifications: Verify if the suppliers have relevant certifications (ISO, CE, etc.) to ensure quality and compliance with international standards.
- Production Capacity: Assess their production capacity to ensure they can handle your order volume and delivery timelines.
Step 4: Request Samples for Quality Assessment
Once you have shortlisted potential suppliers, request samples of their tool pouches. This step is vital to evaluate the quality, craftsmanship, and suitability of the product for your specific needs. Inspect the samples for durability, comfort, and functionality, ensuring they align with your specifications.
Step 5: Negotiate Pricing and Terms
After evaluating samples, engage in negotiations regarding pricing and terms. Be transparent about your budget while seeking the best value for quality. Ensure to discuss payment terms, minimum order quantities, and lead times to avoid any future misunderstandings.
- Bulk Discounts: Inquire about discounts for larger orders, which can significantly reduce costs.
- Payment Flexibility: Consider negotiating payment plans that align with your cash flow needs.
Step 6: Assess Logistics and Supply Chain Management
Logistics play a crucial role in sourcing tool pouches. Evaluate the supplier’s logistics capabilities, including shipping methods, lead times, and delivery reliability. Understanding the supply chain will help you anticipate potential delays and manage inventory effectively.
Step 7: Establish a Quality Control Process
Before finalizing your order, set up a quality control process to monitor the production and delivery of the tool pouches. Specify the quality standards that need to be met and consider conducting factory audits if necessary. This proactive approach will help ensure that the final products meet your expectations and reduce the risk of defects.
By following this detailed checklist, B2B buyers can effectively source tool pouches that meet their specific needs while fostering strong supplier relationships, ultimately contributing to their business success.
Comprehensive Cost and Pricing Analysis for tool pouch Sourcing
What Are the Key Cost Components in Tool Pouch Sourcing?
When sourcing tool pouches, understanding the cost structure is crucial for international B2B buyers. The primary cost components include:
-
Materials: The type of fabric (e.g., nylon, leather, polyester) significantly influences the cost. Durable, high-quality materials often come at a premium but can enhance product longevity and performance.
-
Labor: Labor costs vary by region and can be affected by local wage standards and working conditions. For example, sourcing from countries with lower labor costs may reduce overall expenses, but it’s essential to consider the impact on quality.
-
Manufacturing Overhead: This includes costs related to factory operation, such as utilities, equipment maintenance, and administrative expenses. Efficient production processes can help minimize these overhead costs.
-
Tooling: Initial tooling costs can be significant, especially for custom designs. Buyers should factor in these one-time expenses when evaluating total costs.
-
Quality Control (QC): Ensuring product quality often requires investment in QC processes, which may include inspections, testing, and certifications. This is critical for maintaining standards, particularly in industries with strict compliance requirements.
-
Logistics: Shipping and handling costs can vary based on the distance, shipping method, and Incoterms used. Understanding the logistics landscape is vital for accurate pricing.
-
Margin: Suppliers typically add a margin to cover their risks and expenses. Negotiating this margin can lead to better pricing outcomes for buyers.
How Do Price Influencers Affect Tool Pouch Costs?
Several factors can influence the pricing of tool pouches, including:
-
Volume and Minimum Order Quantity (MOQ): Larger orders often lead to lower per-unit costs due to economies of scale. Buyers should negotiate MOQs that align with their needs to optimize pricing.
-
Specifications and Customization: Custom designs or specific features can increase costs. Buyers should assess whether the added benefits justify the additional expenditure.
-
Materials and Quality Certifications: The choice of materials and the presence of quality certifications (such as ISO standards) can significantly impact pricing. Higher quality often correlates with higher costs.
-
Supplier Factors: Supplier reputation, reliability, and production capabilities can affect pricing. Established suppliers may charge more but offer enhanced quality and service.
-
Incoterms: The chosen Incoterms (International Commercial Terms) dictate responsibilities for shipping and logistics, impacting overall costs. Understanding these terms can help buyers avoid unexpected expenses.
What Are the Best Negotiation Strategies for Tool Pouch Pricing?
For international B2B buyers, particularly from regions like Africa, South America, the Middle East, and Europe, effective negotiation strategies are essential:
-
Conduct Thorough Market Research: Understand the prevailing market rates for tool pouches in your target region. This knowledge empowers you during negotiations.
-
Build Long-term Relationships: Establishing a strong rapport with suppliers can lead to better pricing and terms over time. Loyalty often results in more favorable negotiations.
-
Evaluate Total Cost of Ownership (TCO): Consider all costs associated with the tool pouch, including maintenance, logistics, and potential quality issues. This holistic view can help justify higher upfront costs for better quality.
-
Leverage Volume Discounts: If your business can commit to larger orders, use this leverage to negotiate better prices or terms.
-
Be Transparent About Your Needs: Clearly communicate your requirements and constraints. This transparency can lead to more tailored solutions that fit your budget.
What Should Buyers Keep in Mind Regarding Pricing Nuances?
International buyers should be aware of specific pricing nuances:
-
Currency Fluctuations: Exchange rate variations can impact costs. Consider hedging strategies to mitigate risks associated with currency volatility.
-
Import Duties and Taxes: Understand the import regulations and associated costs in your country. This knowledge is crucial to calculate the total landed cost accurately.
-
Cultural Differences in Negotiation: Different cultures have varying negotiation styles. Familiarize yourself with these to ensure effective communication and successful outcomes.
-
Disclaimer on Indicative Prices: Prices can fluctuate based on market conditions, supplier changes, and other factors. Always seek updated quotes to ensure accuracy in budgeting.
By understanding these cost components, price influencers, and negotiation strategies, international B2B buyers can make informed sourcing decisions for tool pouches, enhancing their overall procurement efficiency.
Alternatives Analysis: Comparing tool pouch With Other Solutions
When considering the best solution for organizing and carrying tools, it is essential to evaluate various options available in the market. While tool pouches are a popular choice for many professionals, there are alternative solutions that may better suit specific needs or preferences. This analysis will compare tool pouches with two viable alternatives: tool belts and tool bags, focusing on key aspects that matter to B2B buyers.
Comparison Table of Tool Pouch and Alternatives
Comparison Aspect | Tool Pouch | Tool Belt | Tool Bag |
---|---|---|---|
Performance | Good for quick access | Excellent for mobility | High capacity for storage |
Cost | Moderate | Moderate to high | Low to moderate |
Ease of Implementation | Easy to use | Requires adjustment | Simple, ready to use |
Maintenance | Low maintenance | Moderate (wear and tear) | Low (cleaning required) |
Best Use Case | Handyman, electricians | Construction, plumbing | General trades, large tools |
What Are the Advantages and Disadvantages of Using a Tool Belt?
Tool belts offer a unique advantage in terms of mobility, making them an ideal choice for professionals who need to move around frequently on job sites. They allow for quick access to tools without needing to set down a bag or pouch. However, tool belts can sometimes be cumbersome and require adjustments to fit properly, which may take time and effort. Additionally, they can become uncomfortable during long periods of use, especially if heavily loaded.
How Does a Tool Bag Compare to a Tool Pouch?
Tool bags are versatile and provide ample storage space, making them suitable for carrying a wide range of tools. Their larger capacity allows for the organization of multiple tools, which is beneficial for general tradespeople or those who require various equipment on-site. However, tool bags can be less convenient for quick access since they often require unzipping or opening to retrieve tools. They are generally more affordable, which can be a significant factor for budget-conscious businesses, but they may not offer the same level of organization as tool pouches.
Conclusion: How to Choose the Right Solution for Your Needs?
When selecting the right tool-carrying solution, B2B buyers should assess their specific requirements, including the type of tools they use, the nature of their work, and their budget. Tool pouches excel in providing quick access and organization for a limited number of tools, making them ideal for electricians or handymen. On the other hand, tool belts are perfect for those who prioritize mobility and efficiency on job sites, while tool bags are best for individuals needing a comprehensive storage solution for various tools. Evaluating these factors will help buyers make an informed decision that best meets their operational needs.
Essential Technical Properties and Trade Terminology for tool pouch
What are the Key Technical Properties of Tool Pouches?
Understanding the technical specifications of tool pouches is crucial for B2B buyers, especially when sourcing products that meet specific operational needs. Here are some essential technical properties to consider:
1. What Material Grades are Commonly Used in Tool Pouches?
Tool pouches are typically made from durable materials such as Nylon, Polyester, or Leather. Each material offers distinct advantages:
- Nylon: Known for its strength and lightweight properties, nylon is resistant to abrasion and water, making it ideal for rugged use in various environments.
- Polyester: This material is UV resistant and offers good durability. It is often used for pouches that require less weight but still need to withstand everyday wear and tear.
- Leather: While heavier and more expensive, leather provides a classic look and exceptional durability, often used in high-end or specialized tool pouches.
Selecting the appropriate material is vital as it impacts the pouch’s longevity, weight, and suitability for specific tasks.
2. How Important is Load Capacity in Tool Pouches?
Load capacity refers to the maximum weight a tool pouch can safely carry without compromising its integrity. This is typically measured in kilograms or pounds. Understanding load capacity is essential for buyers to ensure that the pouch can hold the required tools and accessories without risk of tearing or failure during use. In industries where safety is paramount, such as construction or manufacturing, adhering to load capacity specifications can prevent accidents and equipment loss.
3. What Tolerances Should Be Considered When Sourcing Tool Pouches?
Tolerance in the context of tool pouches refers to the acceptable variations in size and dimensions during manufacturing. Tight tolerances are critical for ensuring that the tools fit properly within the pouch without excessive movement, which can lead to damage or inefficiency. Buyers should inquire about the tolerances applicable to the pouches they are considering, as this will affect both usability and safety.
What Trade Terms are Essential for B2B Buyers of Tool Pouches?
Familiarizing oneself with industry-specific terminology is crucial for effective communication and negotiation in B2B transactions. Here are some key terms:
4. What Does OEM Mean in the Context of Tool Pouches?
OEM (Original Equipment Manufacturer) refers to companies that produce parts or products that are then marketed by another company. When sourcing tool pouches, buyers often work with OEMs to ensure that the pouches meet their specific requirements and branding needs. Understanding OEM relationships can help buyers negotiate better terms and ensure product quality.
5. What is MOQ and Why is it Important?
MOQ (Minimum Order Quantity) is the smallest amount of a product that a supplier is willing to sell. This term is vital for budget planning and inventory management. Buyers should understand the MOQ when sourcing tool pouches, as it can significantly impact initial investments and stock levels. Negotiating a lower MOQ can be beneficial for small businesses or startups.
6. How Does RFQ Influence the Buying Process?
RFQ (Request for Quotation) is a document sent to suppliers requesting pricing and other terms for a specific quantity of products. For tool pouches, an RFQ allows buyers to compare prices, quality, and terms from multiple suppliers. This process is essential for ensuring that buyers get the best deal and understand market rates.
7. What are Incoterms and Their Relevance to Tool Pouch Purchases?
Incoterms (International Commercial Terms) are a set of predefined international rules that clarify the responsibilities of buyers and sellers regarding shipping, insurance, and tariffs. Familiarity with Incoterms helps B2B buyers navigate international transactions more effectively, ensuring that they understand who is responsible for costs and risks at various stages of the shipping process. This knowledge is particularly relevant for buyers in Africa, South America, the Middle East, and Europe, as it can impact overall project costs and timelines.
By understanding these technical properties and trade terminology, international B2B buyers can make informed decisions when sourcing tool pouches, ensuring they select the right products for their needs.
Navigating Market Dynamics and Sourcing Trends in the tool pouch Sector
What Are the Key Trends Influencing the Global Tool Pouch Market?
The global tool pouch market is experiencing notable growth, driven by several key factors. The increasing demand for organized storage solutions in both industrial and domestic settings is pushing B2B buyers to seek high-quality, durable tool pouches. Furthermore, the rise of DIY culture, particularly in regions like Europe and North America, is catalyzing demand for tool pouches that cater to hobbyists and professionals alike.
Emerging technologies are also shaping sourcing trends. The integration of e-commerce platforms facilitates easier procurement for international buyers, enabling them to access a wider variety of tool pouches from different manufacturers. In particular, buyers from Africa, South America, and the Middle East are increasingly leveraging online marketplaces to find suppliers that meet their specific needs, such as customization options and bulk purchasing discounts.
Additionally, the trend towards digitalization in supply chain management is influencing how businesses source tool pouches. Companies are adopting data analytics to forecast demand, optimize inventory levels, and streamline logistics. This trend is crucial for B2B buyers looking to maintain competitive pricing and ensure timely delivery in a rapidly evolving market.
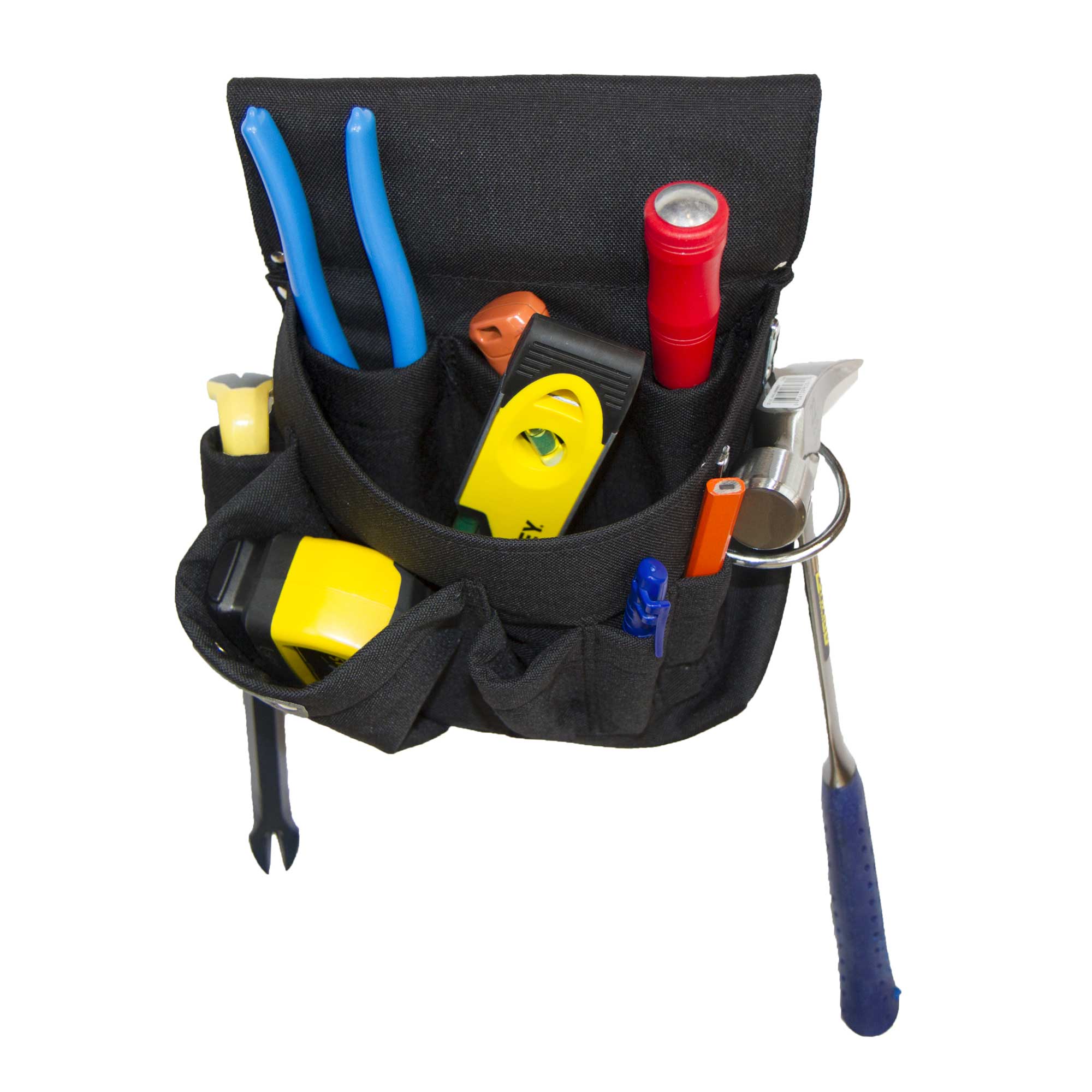
A stock image related to tool pouch.
How Is Sustainability Impacting Tool Pouch Sourcing Decisions?
As global awareness of environmental issues rises, sustainability is becoming a significant factor in the sourcing of tool pouches. B2B buyers are increasingly prioritizing suppliers that adhere to ethical sourcing practices, reflecting a commitment to reduce environmental impact. This shift is particularly evident in Europe, where regulatory frameworks are pushing companies to adopt sustainable practices.
One of the key aspects of sustainable sourcing is the use of eco-friendly materials. Buyers are showing interest in tool pouches made from recycled or sustainably sourced materials, which not only reduce carbon footprints but also appeal to environmentally conscious consumers. Certifications such as Global Recycle Standard (GRS) and OEKO-TEX® are becoming essential criteria for B2B buyers when assessing potential suppliers.
Moreover, transparency in the supply chain is gaining importance. Buyers are looking for suppliers who can provide clear documentation about the sourcing of raw materials and the manufacturing process. This trend is not only about compliance but also about building brand reputation and customer trust in increasingly competitive markets.
What Is the Historical Context of Tool Pouch Development?
The tool pouch has evolved significantly over the years, transitioning from simple fabric designs to sophisticated, multifunctional products. Originally designed for tradespeople to carry essential tools, modern tool pouches now offer features such as ergonomic designs, weather-resistant materials, and modular components for increased functionality.
This evolution reflects broader trends in the manufacturing and construction industries, where efficiency and organization are paramount. As work environments become more demanding, the tool pouch has adapted to meet the needs of professionals across various sectors, reinforcing its relevance in today’s B2B marketplace.
Understanding these historical developments can provide valuable context for international buyers, particularly when assessing product quality and supplier capabilities. Recognizing the advancements in design and materials can help buyers make informed decisions about which tool pouches best suit their operational needs and align with their sustainability goals.
Frequently Asked Questions (FAQs) for B2B Buyers of tool pouch
-
How do I choose the right tool pouch for my business needs?
Selecting the right tool pouch involves assessing the specific tools you need to carry and the working conditions. Consider factors such as size, material durability, and organizational features. For example, if you operate in wet environments, opt for waterproof materials. Additionally, evaluate whether you require customized compartments for specific tools, as tailored solutions can enhance efficiency and organization. -
What are the advantages of using a tool pouch in various industries?
Tool pouches provide easy access to tools, improving efficiency and productivity across various sectors such as construction, maintenance, and landscaping. They enhance organization, allowing workers to carry essential tools without the bulk of a toolbox. In industries where mobility is key, tool pouches offer a lightweight solution that keeps tools at hand, reducing downtime during tasks. -
What customization options are available for tool pouches?
Customization options for tool pouches include size adjustments, color choices, branding with logos, and the addition of specific pockets or compartments tailored to your tools. Some suppliers also offer personalized features like padded backs for comfort or reinforced stitching for durability. Discuss your requirements with manufacturers to explore the best options for your specific needs. -
How do I vet suppliers for tool pouches in international markets?
To vet suppliers, start by researching their reputation through reviews and testimonials from previous clients. Request samples to assess product quality and ensure they meet your specifications. Additionally, verify their manufacturing capabilities and compliance with international standards. Establish direct communication to gauge responsiveness and willingness to accommodate your requirements. -
What is the typical minimum order quantity (MOQ) for tool pouches?
Minimum order quantities (MOQs) for tool pouches can vary significantly depending on the supplier and the level of customization required. Generally, MOQs range from 50 to 500 units. When sourcing, inquire about the MOQ for standard designs versus customized options, as some suppliers may have lower MOQs for bulk orders or stock items. -
What payment terms should I expect when purchasing tool pouches internationally?
Payment terms can vary based on the supplier and your relationship with them. Common arrangements include a 30% upfront deposit with the balance due upon delivery, or net 30 to 60 days after receipt of goods. Always clarify payment methods accepted (e.g., wire transfer, credit card) and consider using an escrow service for added security in international transactions. -
What quality assurance measures should I consider when sourcing tool pouches?
When sourcing tool pouches, ensure that suppliers implement rigorous quality assurance (QA) measures. Ask about their inspection processes, certifications (such as ISO), and if they conduct third-party quality checks. Request documentation on material sourcing and production processes to ensure compliance with safety and quality standards, especially if you plan to sell these products in regulated markets. -
How can logistics impact my tool pouch sourcing process?
Logistics play a crucial role in sourcing tool pouches, affecting delivery times and costs. Assess the supplier’s shipping methods, lead times, and reliability. Consider potential customs duties and taxes when importing, especially in regions with strict regulations. Building a relationship with a logistics partner can help streamline the process, ensuring timely delivery and minimizing disruptions in your supply chain.
Important Disclaimer & Terms of Use
⚠️ Important Disclaimer
The information provided in this guide, including content regarding manufacturers, technical specifications, and market analysis, is for informational and educational purposes only. It does not constitute professional procurement advice, financial advice, or legal advice.
While we have made every effort to ensure the accuracy and timeliness of the information, we are not responsible for any errors, omissions, or outdated information. Market conditions, company details, and technical standards are subject to change.
B2B buyers must conduct their own independent and thorough due diligence before making any purchasing decisions. This includes contacting suppliers directly, verifying certifications, requesting samples, and seeking professional consultation. The risk of relying on any information in this guide is borne solely by the reader.
Strategic Sourcing Conclusion and Outlook for tool pouch
In today’s competitive landscape, strategic sourcing for tool pouches offers significant advantages for international B2B buyers. By understanding market trends and leveraging supplier relationships, businesses can optimize their procurement processes, ensuring high-quality products at competitive prices. Buyers from Africa, South America, the Middle East, and Europe should prioritize sourcing strategies that emphasize sustainability and innovation, aligning with global standards and consumer expectations.
How Can International B2B Buyers Optimize Their Sourcing Strategies?
Implementing a thorough evaluation of suppliers, focusing on their production capabilities and adherence to quality standards, can further enhance purchasing decisions. Additionally, fostering partnerships with local suppliers can lead to reduced lead times and improved communication, particularly in regions like Egypt and the UK, where logistical considerations are paramount.
What Does the Future Hold for Tool Pouch Procurement?
As the demand for versatile and durable tool pouches continues to rise, international buyers are encouraged to stay ahead of industry trends. Engaging in proactive sourcing strategies will not only enhance supply chain resilience but also position companies for success in a rapidly evolving market. Now is the time to explore innovative sourcing solutions that can lead to long-term growth and sustainability in your operations.