Replace Cabin Air Filter: How Often Should You Do It? (2025)
Introduction: Navigating the Global Market for how often to replace cabin air filter
Navigating the global market for cabin air filters presents a significant challenge for international B2B buyers, particularly in regions like Africa, South America, the Middle East, and Europe. Understanding how often to replace cabin air filters is not just a maintenance issue; it directly impacts vehicle performance, air quality, and ultimately, customer satisfaction. With a variety of factors influencing the lifespan of these filters—such as environmental conditions, vehicle type, and usage patterns—B2B buyers must be equipped with comprehensive knowledge to make informed decisions.
This guide aims to demystify the complexities surrounding cabin air filter replacement, offering insights into different types of filters available in the market, their specific applications, and the implications of timely replacements. Buyers will learn about effective supplier vetting processes, enabling them to identify reputable manufacturers and distributors who meet their quality and pricing standards. Additionally, we will explore cost considerations that affect procurement strategies, providing a framework for budgeting and financial planning.
By leveraging the actionable insights and data presented in this guide, international B2B buyers can enhance their purchasing strategies, ensuring they not only comply with industry standards but also improve operational efficiency. Whether you are sourcing for a fleet in Mexico or managing a workshop in Poland, this comprehensive resource will empower you to navigate the global market with confidence, leading to better outcomes for your business and customers alike.
Understanding how often to replace cabin air filter Types and Variations
Type Name | Key Distinguishing Features | Primary B2B Applications | Brief Pros & Cons for Buyers |
---|---|---|---|
Standard Replacement Filter | Basic filtration, typically made of paper or synthetic material. | General automotive maintenance shops | Pros: Cost-effective; Cons: Limited filtration efficiency. |
HEPA Filter | High-Efficiency Particulate Air filter; captures smaller particles. | Luxury vehicle maintenance, hospitals | Pros: Superior air quality; Cons: Higher cost. |
Activated Carbon Filter | Contains activated carbon to absorb odors and gases. | Fleet management, public transport | Pros: Reduces odors; Cons: Needs more frequent replacement. |
Electrostatic Filter | Uses an electrostatic charge to attract and trap particles. | Industrial vehicles, construction sites | Pros: Enhanced filtration; Cons: Requires specific cleaning methods. |
Cabin Filter with UV Light | Incorporates UV light to kill bacteria and mold. | Healthcare vehicles, high-end vehicles | Pros: Sanitary air quality; Cons: Complex installation. |
What are the characteristics and suitability of Standard Replacement Filters?
Standard replacement filters are the most commonly used type, designed to provide basic filtration of airborne particles. Typically made from paper or synthetic materials, they are suitable for most vehicles in regions with moderate air quality concerns. B2B buyers should consider these filters for general automotive maintenance shops, where cost-effectiveness is a priority. However, their limited filtration efficiency may not meet the needs of businesses operating in highly polluted environments.
How do HEPA Filters enhance air quality for B2B applications?
HEPA (High-Efficiency Particulate Air) filters are engineered to capture at least 99.97% of particles as small as 0.3 microns, making them ideal for luxury vehicles and environments where air quality is paramount, such as hospitals. For B2B buyers, investing in HEPA filters ensures superior air quality for clients and employees, particularly in regions with high pollution levels. However, the higher initial cost may require justification in terms of long-term health benefits and customer satisfaction.
What benefits do Activated Carbon Filters provide for fleet management?
Activated carbon filters are specifically designed to absorb odors and harmful gases, making them an excellent choice for fleet management and public transport systems. Their ability to improve passenger comfort and air quality can enhance the overall experience. However, B2B buyers must be aware that these filters may require more frequent replacements due to their absorption capacity, impacting long-term operational costs.
Why choose Electrostatic Filters for industrial vehicles?
Electrostatic filters utilize an electrostatic charge to attract and trap particles, offering enhanced filtration capabilities. They are particularly suitable for industrial vehicles and construction sites, where dust and particulate matter are prevalent. B2B buyers should consider the need for specific cleaning methods to maintain these filters, as improper maintenance can reduce their effectiveness. The investment in electrostatic filters can lead to better air quality and equipment longevity.
What advantages do Cabin Filters with UV Light provide in healthcare applications?
Cabin filters that incorporate UV light technology are designed to kill bacteria and mold, making them ideal for healthcare vehicles and high-end automobiles. These filters provide a significant advantage in maintaining sanitary air quality, especially in environments where hygiene is critical. However, B2B buyers should note that the installation of UV light systems can be more complex and may involve higher maintenance costs. The health benefits often outweigh these costs, making them a valuable option for businesses in sensitive sectors.
Related Video: How to Replace Cabin Air Filter 2011-2018 Ram 1500
Key Industrial Applications of how often to replace cabin air filter
Industry/Sector | Specific Application of how often to replace cabin air filter | Value/Benefit for the Business | Key Sourcing Considerations for this Application |
---|---|---|---|
Automotive Manufacturing | Routine maintenance schedules for fleet vehicles | Improved air quality and employee health | Quality certifications, compatibility with various models |
Public Transportation | Regular replacement for buses and trains | Enhanced passenger comfort and safety | Bulk purchasing agreements, local suppliers |
Construction | Maintenance of construction machinery and vehicles | Reduced equipment downtime and improved efficiency | Availability of filters that withstand harsh environments |
Agriculture | Air filtration in farm vehicles and equipment | Protection against dust and allergens for operators | Durability in extreme conditions, ease of installation |
Logistics and Delivery | Ensuring air quality in delivery trucks | Better driver health and reduced fatigue | Sourcing from manufacturers with global reach |
How is ‘how often to replace cabin air filter’ used in Automotive Manufacturing?
In the automotive manufacturing sector, the frequency of cabin air filter replacement is critical for maintaining the air quality within fleet vehicles. Regular maintenance schedules should be established to ensure filters are replaced at intervals recommended by manufacturers, typically every 12,000 to 15,000 miles. This practice not only enhances the health and comfort of drivers and passengers but also prevents potential HVAC system issues. For international buyers, understanding local regulations regarding vehicle emissions and air quality can influence sourcing decisions for compliant filters.
What are the implications of cabin air filter maintenance in Public Transportation?
For public transportation systems, such as buses and trains, the cabin air filter plays a vital role in passenger comfort and safety. Regular replacement is necessary to mitigate the buildup of pollutants and allergens, which can lead to health complaints among passengers. Operators should follow a strict replacement schedule, ideally every 6 to 12 months, depending on usage and environmental conditions. B2B buyers in this sector should consider sourcing filters that are specifically designed for high-traffic vehicles to ensure longevity and efficiency.
How does cabin air filter replacement affect Construction?
In the construction industry, maintaining the air quality in machinery and vehicles is essential due to the dusty and often hazardous environments. Cabin air filters should be replaced regularly, ideally every 3 to 6 months, to prevent the entry of harmful particulates that can affect operator health and equipment performance. Buyers should prioritize filters that are robust enough to handle extreme conditions and are easy to install, minimizing downtime. This can significantly enhance the overall efficiency of construction operations.
Why is cabin air filter maintenance critical in Agriculture?
In agricultural settings, the air quality within farm vehicles and equipment is crucial for protecting operators from dust and allergens. Regular replacement of cabin air filters is recommended every 12 months or based on usage patterns. This practice not only safeguards the health of the operators but also ensures that machinery runs optimally. Buyers in this sector should look for filters that offer high filtration efficiency and can withstand the rigors of outdoor environments, making them suitable for diverse agricultural applications.
What benefits does proper cabin air filter maintenance bring to Logistics and Delivery?
In the logistics and delivery sector, the cabin air filter’s role in ensuring air quality is vital for driver health and performance. Filters should be replaced every 10,000 to 15,000 miles to maintain optimal air quality, which can reduce driver fatigue and improve focus. For international B2B buyers, it’s important to consider suppliers that can provide filters compatible with a wide range of vehicle models and offer reliable logistics to ensure timely replacements, thus enhancing operational efficiency.
Related Video: How to Replace the Cabin Air Filter on a 2019-2024 Chevy Silverado
3 Common User Pain Points for ‘how often to replace cabin air filter’ & Their Solutions
Scenario 1: Navigating Replacement Intervals in Diverse Markets
The Problem: B2B buyers in regions like Africa and South America often face inconsistencies in the recommended replacement intervals for cabin air filters due to varying environmental conditions and vehicle usage. This can lead to confusion regarding how frequently filters should be replaced, especially for fleets operating in dusty or polluted areas. Buyers may struggle to balance the need for air quality improvements with cost-effectiveness, risking either over-replacement, which inflates operational costs, or under-replacement, which could compromise vehicle performance and passenger safety.
The Solution: To effectively manage replacement intervals, B2B buyers should implement a data-driven maintenance schedule based on specific environmental factors and vehicle usage patterns. Conducting an initial assessment of air quality in your operational areas can provide a baseline. For example, if vehicles are predominantly used in urban environments with high pollution levels, consider a more frequent replacement cycle, such as every 10,000 kilometers. Conversely, in less polluted regions, extending the interval to 15,000-20,000 kilometers may be viable. Establish partnerships with reliable suppliers who can provide high-quality filters and support tailored maintenance plans that align with these assessments.
Scenario 2: Understanding Quality vs. Cost in Cabin Air Filters
The Problem: International buyers, particularly in Europe and the Middle East, often grapple with the dilemma of choosing between low-cost filters and higher-quality options. While budget constraints may push them towards cheaper alternatives, these filters may not effectively capture pollutants, leading to a decline in air quality within the vehicle. This scenario presents a classic trade-off between immediate savings and long-term vehicle health, which can be particularly troublesome for companies managing large fleets.
The Solution: To navigate this challenge, B2B buyers should prioritize total cost of ownership rather than just initial purchase price. Conduct a cost-benefit analysis comparing the lifespan and efficiency of low-cost filters versus premium options. Engage with suppliers who can provide detailed product specifications, including filtration efficiency ratings and expected longevity. Furthermore, consider bulk purchasing agreements that allow for better pricing on high-quality filters, thus reducing overall costs while ensuring superior air quality and vehicle performance. This strategic approach not only enhances the well-being of passengers but also improves the longevity of the HVAC system in the vehicles.
Scenario 3: Educating Staff on Maintenance Best Practices
The Problem: A common pain point for B2B buyers across all regions is the lack of understanding among staff about the importance of cabin air filter maintenance. Often, employees may not recognize the signs of a clogged filter or the recommended schedules for replacements. This gap in knowledge can lead to inconsistent maintenance practices, resulting in operational inefficiencies and increased health risks for passengers.
The Solution: Implement a comprehensive training program focused on the importance of cabin air filter maintenance. This should include educational materials that detail how to identify signs of filter clogging, such as reduced airflow or unpleasant odors. Consider using visual aids and hands-on workshops to demonstrate how to check and replace filters correctly. Additionally, integrate a digital tracking system that reminds staff of replacement schedules based on vehicle mileage or time intervals. By fostering a culture of awareness and responsibility around air quality, companies can ensure that their fleets operate at peak efficiency, ultimately enhancing passenger comfort and safety.
Strategic Material Selection Guide for how often to replace cabin air filter
What Are the Common Materials Used in Cabin Air Filters?
When selecting materials for cabin air filters, it’s essential to consider their properties, advantages, and limitations. This analysis focuses on three common materials: activated carbon, HEPA (High-Efficiency Particulate Air), and synthetic fibers. Each material has unique characteristics that can significantly impact performance, durability, and overall cost-effectiveness for international B2B buyers.
How Does Activated Carbon Perform in Cabin Air Filters?
Activated carbon is widely recognized for its exceptional adsorption properties, making it ideal for filtering out odors and harmful gases. Key properties include a high surface area that enhances its ability to capture volatile organic compounds (VOCs) and other pollutants.
Pros: Activated carbon filters are effective in improving air quality by removing unpleasant smells and harmful particles. They are relatively lightweight and easy to manufacture, which can lower production costs.
Cons: However, activated carbon filters may have a shorter lifespan compared to other materials, requiring more frequent replacements. They also may not effectively filter out smaller particulate matter, which can be a concern for specific applications.
Considerations for International Buyers: Buyers should ensure compliance with local air quality standards, such as those set by the European Union or local regulations in African and South American countries. Understanding the specific environmental conditions in regions like the Middle East can also guide material selection.
What Are the Benefits of HEPA Filters for Cabin Air Quality?
HEPA filters are renowned for their ability to capture at least 99.97% of particles that are 0.3 microns in diameter. This makes them an excellent choice for applications requiring high air quality standards.
Pros: The primary advantage of HEPA filters is their efficiency in trapping allergens, dust, and other fine particles. They are durable and can last longer than activated carbon filters, reducing the frequency of replacements.
Cons: The manufacturing complexity of HEPA filters can lead to higher production costs. Additionally, their density can restrict airflow, which may affect vehicle performance if not properly designed.
Considerations for International Buyers: Compliance with international standards such as ASTM and DIN is crucial. Buyers in Europe, for instance, may prioritize HEPA filters for their stringent air quality regulations, while buyers in regions with less stringent standards may not require such high-performance materials.
How Do Synthetic Fibers Compare for Cabin Air Filter Applications?
Synthetic fibers, such as polyester and polypropylene, are commonly used in cabin air filters due to their versatility and effectiveness in capturing particulate matter.
Pros: These materials are durable, lightweight, and resistant to moisture and mold, making them suitable for various climates. Their manufacturing process is generally straightforward, which can lead to lower costs.
Cons: While synthetic fibers are effective at filtering larger particles, they may not perform as well against gases and odors compared to activated carbon. Additionally, their environmental impact can be a concern, especially in regions focused on sustainability.
Considerations for International Buyers: Buyers should consider local regulations regarding the use of synthetic materials and their recyclability. In Europe, for instance, there is a growing emphasis on sustainable materials, which may influence purchasing decisions.
Summary Table of Material Selection for Cabin Air Filters
Material | Typical Use Case for how often to replace cabin air filter | Key Advantage | Key Disadvantage/Limitation | Relative Cost (Low/Med/High) |
---|---|---|---|---|
Activated Carbon | Ideal for odor removal and gas filtration | Excellent adsorption properties for VOCs and odors | Shorter lifespan, less effective for fine particles | Medium |
HEPA | Best for high air quality requirements | Captures 99.97% of particles, durable | Higher production costs, potential airflow issues | High |
Synthetic Fibers | Versatile use in various climates | Durable, lightweight, moisture-resistant | Less effective against gases and odors | Low |
In conclusion, the selection of materials for cabin air filters requires careful consideration of their properties, advantages, and limitations. International B2B buyers must also account for local compliance standards and market preferences, particularly in diverse regions like Africa, South America, the Middle East, and Europe. Understanding these factors will aid in making informed purchasing decisions that align with both performance and cost-effectiveness.
In-depth Look: Manufacturing Processes and Quality Assurance for how often to replace cabin air filter
What Are the Key Manufacturing Processes for Cabin Air Filters?
The manufacturing of cabin air filters involves several essential stages that ensure the final product meets quality and performance standards. Understanding these processes can help international B2B buyers make informed decisions regarding sourcing.
Material Preparation: What Materials Are Used?
The manufacturing process begins with material preparation, where raw materials such as synthetic fibers, activated carbon, and non-woven fabrics are sourced. These materials are chosen for their filtration efficiency and ability to absorb pollutants. For buyers, it’s crucial to verify the origin and quality of these materials, as they directly influence the filter’s performance.
How Are Cabin Air Filters Formed?
Once the materials are prepared, they undergo a forming process. This typically involves cutting and shaping the materials into the required filter dimensions. Techniques such as pleating are often used to increase the surface area, enhancing the filter’s ability to capture contaminants. For B2B buyers, understanding these techniques can help assess the effectiveness of the filter design and its potential longevity.
What Does the Assembly Process Involve?
The assembly stage involves combining the formed materials into a complete filter unit. This may include inserting support frames, applying adhesive, and ensuring proper sealing to prevent air bypass. Buyers should inquire about the assembly methods used, as automated versus manual assembly can affect the consistency and quality of the final product.
What Finishing Techniques Are Commonly Used?
Finishing techniques, such as coating or additional treatments, are applied to enhance the filter’s properties, such as moisture resistance or additional filtration capabilities. These processes can significantly impact the filter’s overall performance and lifespan. B2B buyers should look for suppliers who utilize advanced finishing techniques to ensure superior product quality.
What Quality Assurance Standards Should B2B Buyers Consider?
Quality assurance is paramount in the manufacturing of cabin air filters, and various international standards guide these practices. Understanding these can help buyers ensure they are purchasing reliable products.
Which International Standards Are Relevant?
Many manufacturers adhere to ISO 9001, a standard that focuses on quality management systems. Compliance with this standard indicates that the manufacturer has established processes to ensure consistent quality. Additionally, industry-specific certifications like CE (Conformité Européenne) for Europe and API (American Petroleum Institute) standards may also apply, depending on the intended use of the filters.
What Are the Quality Control Checkpoints?
Quality control (QC) involves several checkpoints throughout the manufacturing process. These include:
- Incoming Quality Control (IQC): This stage assesses the quality of raw materials before production.
- In-Process Quality Control (IPQC): Ongoing checks during manufacturing ensure that processes remain within specified limits.
- Final Quality Control (FQC): The final product undergoes comprehensive testing to verify performance and compliance with specifications.
For B2B buyers, understanding these checkpoints can help in evaluating supplier reliability.
How Can B2B Buyers Verify Supplier Quality Control?
To ensure that suppliers maintain high-quality standards, B2B buyers should consider implementing the following verification methods:
What Role Do Audits Play in Quality Verification?
Conducting regular audits of suppliers can provide insights into their quality management systems and adherence to international standards. Audits can be performed in-house or by third-party organizations to ensure objectivity. This process allows buyers to identify potential issues before they affect product quality.
Why Are Quality Reports Important?
Requesting detailed quality reports from suppliers can offer transparency regarding their QC processes. These reports should include data on material sourcing, manufacturing processes, and testing outcomes. Buyers should look for consistency in these reports to gauge supplier reliability.
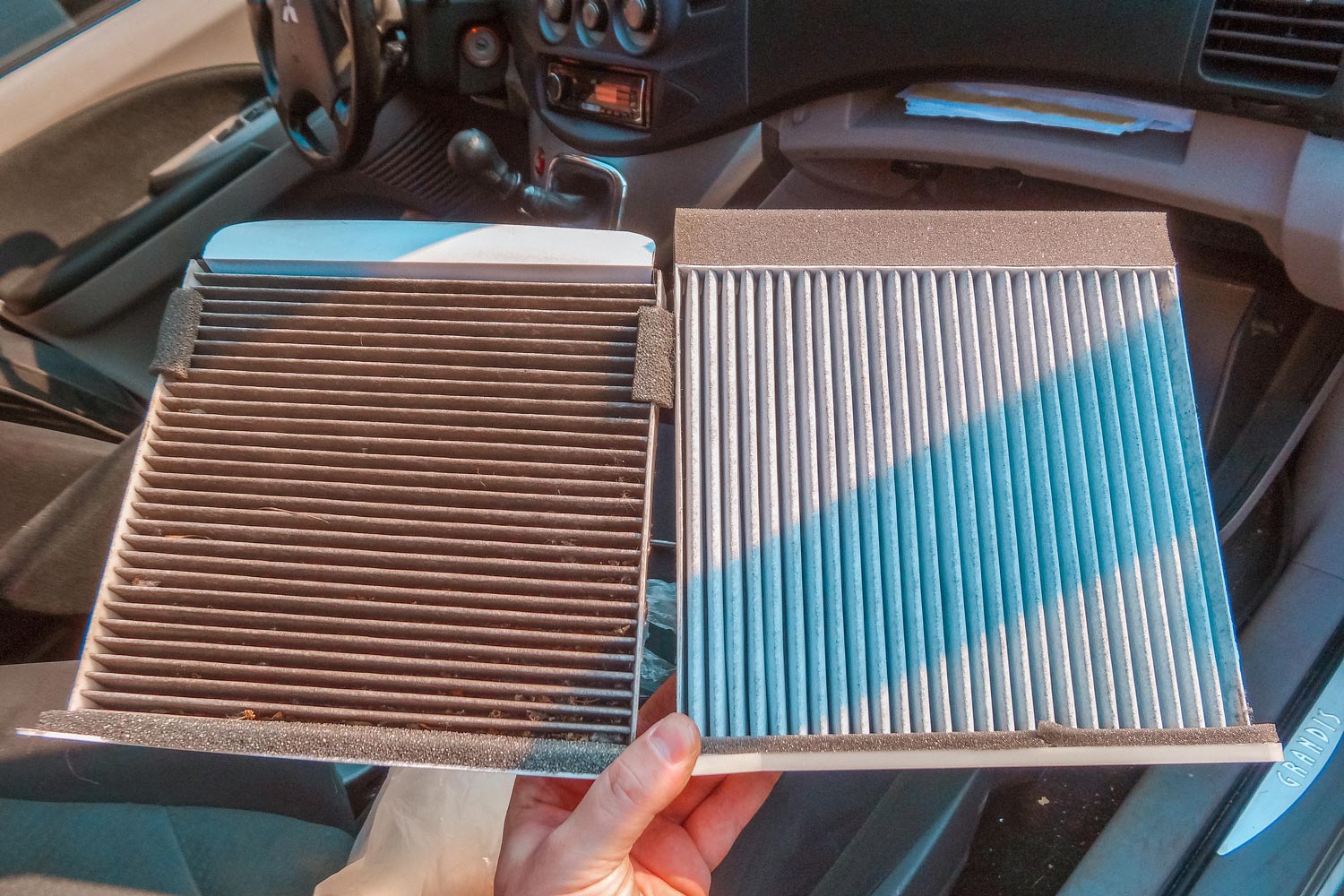
A stock image related to how often to replace cabin air filter.
How Can Third-Party Inspections Enhance Trust?
Engaging third-party inspection agencies can further validate a supplier’s quality assurance practices. These inspections can provide an impartial assessment of the manufacturing processes and the final product. For buyers in Africa, South America, the Middle East, and Europe, partnering with reputable inspection agencies can mitigate risks associated with sourcing.
What Are the Common Testing Methods for Cabin Air Filters?
Testing methods are critical in ensuring that cabin air filters meet performance standards. Understanding these methods can help buyers evaluate the effectiveness of the filters they are considering.
Which Tests Are Essential for Performance Verification?
Common testing methods for cabin air filters include:
- Particle Filtration Efficiency Tests: Measure the filter’s ability to capture particles of various sizes.
- Dust Holding Capacity Tests: Assess how much dust the filter can hold before requiring replacement.
- Airflow Resistance Tests: Evaluate how the filter affects airflow, which is crucial for vehicle performance.
Buyers should inquire about the specific tests conducted by suppliers and the results, as these metrics directly impact filter performance.
What Are the Quality Control Nuances for International B2B Buyers?
International B2B buyers face unique challenges when sourcing cabin air filters, particularly regarding quality control nuances.
How Do Regional Standards Affect Quality Assurance?
Different regions may have varying quality standards and regulations. For instance, filters sold in Europe must comply with CE marking requirements, while those in the Middle East may need to adhere to local standards. Buyers should be aware of these differences and ensure that suppliers can meet the necessary certifications for their specific market.
Why Is Supplier Communication Critical?
Effective communication with suppliers is crucial to ensure that all quality standards are understood and met. B2B buyers should establish clear expectations regarding quality control processes, testing methods, and compliance with international standards. This proactive approach can significantly reduce the risk of receiving subpar products.
Conclusion: How Can B2B Buyers Ensure Quality in Cabin Air Filters?
In summary, understanding the manufacturing processes and quality assurance practices for cabin air filters is essential for B2B buyers. By focusing on material preparation, forming, assembly, and finishing processes, as well as adhering to international quality standards, buyers can make informed decisions. Implementing rigorous quality verification methods, including audits, quality reports, and third-party inspections, will further enhance the reliability of their sourcing decisions.
Practical Sourcing Guide: A Step-by-Step Checklist for ‘how often to replace cabin air filter’
This guide aims to equip international B2B buyers with a practical checklist for sourcing information on how often to replace cabin air filters. Understanding the replacement frequency is crucial for maintaining air quality in vehicles, which can impact health, comfort, and even operational efficiency. Here’s a structured approach to ensure you make informed decisions when sourcing this critical information.
Step 1: Identify Your Vehicle Requirements
Understanding the specific requirements for your fleet or individual vehicles is essential. Different makes and models have varying recommendations for cabin air filter replacement. Consult manufacturer guidelines and maintenance manuals to determine the ideal replacement interval, which typically ranges from 15,000 to 30,000 kilometers.
Step 2: Research Industry Standards and Practices
Investigate common practices and standards within your industry or region. This knowledge can help you benchmark against competitors and ensure compliance with local regulations. For instance, European regulations may differ from those in Africa or South America, influencing how often filters should be replaced.
Step 3: Engage with Reliable Suppliers
Building relationships with reputable suppliers is vital. Seek suppliers who specialize in automotive parts and have a proven track record in your region. Ask for certifications, such as ISO standards, and ensure they provide filters that meet or exceed OEM specifications.
Step 4: Evaluate Product Quality and Performance
Not all cabin air filters are created equal. Look for filters that offer superior filtration efficiency and durability. Consider factors like:
– Material: High-efficiency particulate air (HEPA) filters can capture finer particles.
– Longevity: Some filters are designed for longer use, which can reduce replacement frequency.
Step 5: Request Samples for Testing
Before making bulk purchases, request samples from potential suppliers. Conduct performance tests to assess how well the filters perform under your operational conditions. This step can help you avoid costly mistakes and ensure you are sourcing high-quality products.
Step 6: Establish a Replacement Schedule
Once you have determined the optimal replacement frequency, create a maintenance schedule. Document this schedule and communicate it to your maintenance team to ensure timely replacements. This proactive approach can prevent issues related to air quality and enhance overall vehicle performance.
Step 7: Monitor and Adjust Based on Feedback
After implementing your replacement schedule, continuously monitor the performance of the cabin air filters. Collect feedback from drivers and maintenance personnel regarding air quality and filter efficiency. Be prepared to adjust your sourcing strategy or replacement intervals based on this feedback to ensure optimal results.
By following this checklist, B2B buyers can ensure they are well-informed about how often to replace cabin air filters, leading to improved air quality, enhanced vehicle performance, and ultimately, greater satisfaction for both drivers and clients.
Comprehensive Cost and Pricing Analysis for how often to replace cabin air filter Sourcing
What Are the Key Cost Components for Cabin Air Filter Sourcing?
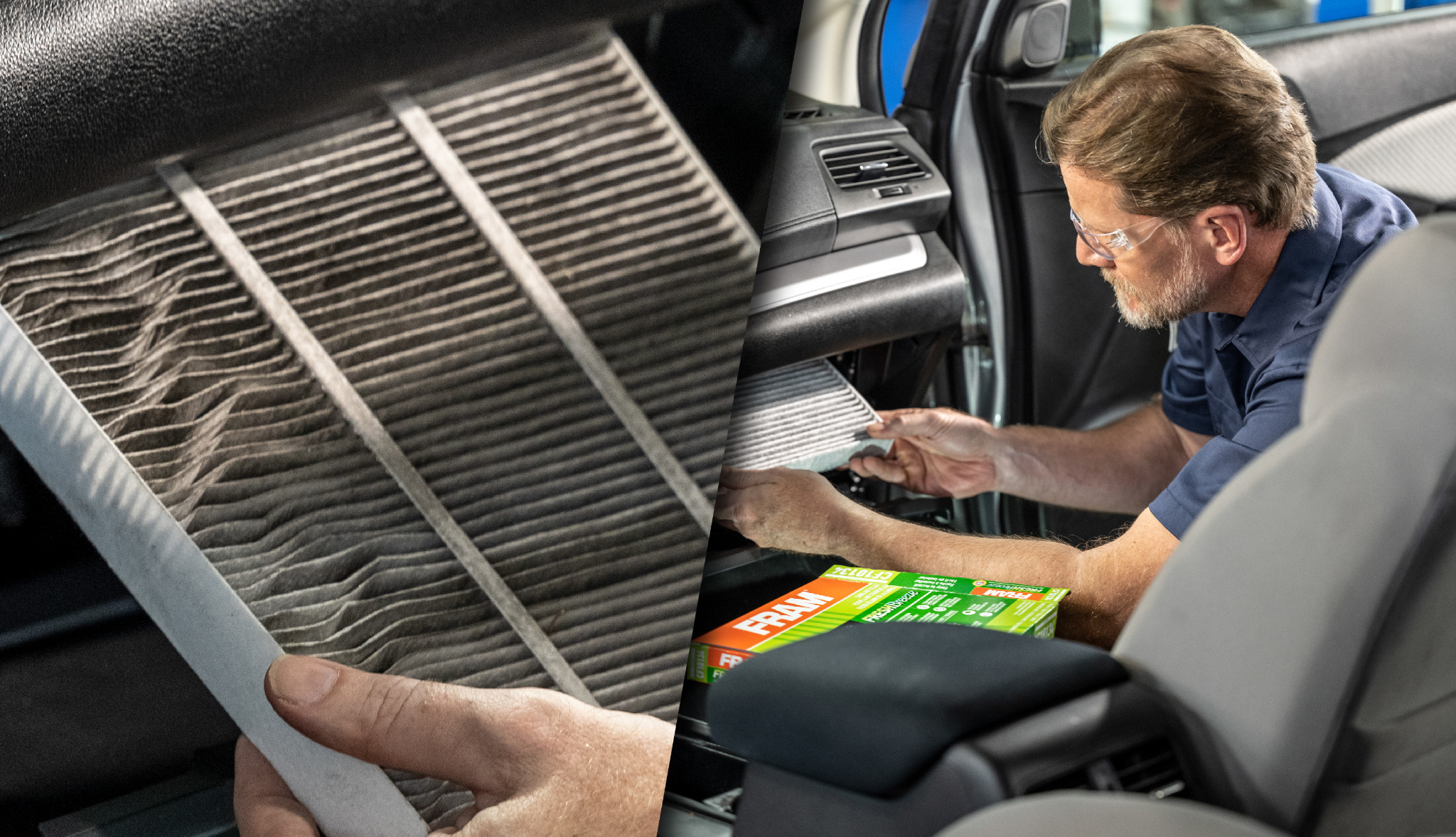
A stock image related to how often to replace cabin air filter.
When assessing the cost structure for sourcing cabin air filters, several components come into play. Understanding these elements can help B2B buyers optimize their procurement strategies.
-
Materials: The primary cost driver is the quality of materials used in manufacturing cabin air filters. Common materials include activated carbon, synthetic fibers, and cellulose. Premium materials often lead to higher filtration efficiency, which can justify increased costs.
-
Labor: Labor costs vary significantly depending on the region. In regions such as Africa or South America, labor costs might be lower, which can reduce overall production expenses. However, suppliers in Europe may have higher labor costs, affecting pricing strategies.
-
Manufacturing Overhead: This includes costs associated with utilities, facility maintenance, and administrative expenses. B2B buyers should inquire about how a supplier allocates these costs to ensure transparency in pricing.
-
Tooling: The initial investment in specialized tooling can be substantial, especially for custom or high-spec filters. Buyers need to consider whether the tooling costs are amortized over a larger production run, which can impact unit pricing.
-
Quality Control (QC): Implementing rigorous QC measures adds to the overall cost but is crucial for ensuring product reliability. Suppliers that adhere to international quality standards may charge a premium, which can be worthwhile for long-term partnerships.
-
Logistics: Transportation costs can vary based on the geographic location of suppliers. For international buyers, understanding Incoterms is essential to determine who bears the cost of logistics and risk during shipment.
-
Margin: Supplier profit margins can fluctuate based on market demand and competition. Buyers should benchmark prices to ensure they are not overpaying.
What Influences Pricing for Cabin Air Filters?
Several factors can influence the pricing of cabin air filters, particularly in an international context:
-
Volume/MOQ: Suppliers often provide tiered pricing based on the Minimum Order Quantity (MOQ). Higher order volumes typically yield better pricing, allowing buyers to negotiate favorable terms.
-
Specifications and Customization: Custom filters designed for specific vehicle models or unique environmental conditions can incur additional costs. Buyers should evaluate whether the added investment aligns with their operational needs.
-
Materials and Quality Certifications: Filters that meet international quality certifications (such as ISO or OEM standards) may command higher prices. Buyers must weigh the cost against the expected performance benefits.
-
Supplier Factors: The reputation and reliability of a supplier can significantly impact pricing. Established suppliers with a proven track record may charge more due to their reliability and quality assurance processes.
-
Incoterms: Understanding Incoterms is vital for international transactions. These terms define the responsibilities of buyers and sellers regarding shipping, insurance, and tariffs, all of which can affect the overall cost.
What Are the Best Buyer Tips for Cost-Efficiency?
To maximize cost-efficiency in sourcing cabin air filters, international B2B buyers should consider the following strategies:
-
Negotiate Terms: Effective negotiation can lead to significant savings. Engage in discussions about pricing, payment terms, and delivery schedules to find mutually beneficial arrangements.
-
Assess Total Cost of Ownership (TCO): Beyond the initial purchase price, consider the TCO, which includes maintenance, efficiency, and replacement frequency. A higher upfront cost may lead to lower TCO if the filter has a longer lifespan and better performance.
-
Pricing Nuances for International Buyers: Understand the currency fluctuations and economic conditions in the supplier’s region. This knowledge can inform your negotiation strategy and help in budgeting.
-
Evaluate Supplier Performance: Regularly assess supplier performance in terms of quality, delivery times, and responsiveness. Building strong relationships with reliable suppliers can lead to better pricing and service over time.
Disclaimer on Indicative Prices
Prices for cabin air filters can vary widely based on the factors discussed above. It is advisable for buyers to conduct thorough market research and obtain quotes from multiple suppliers to ensure competitive pricing.
Alternatives Analysis: Comparing how often to replace cabin air filter With Other Solutions
Exploring Alternatives: How Does Replacing Cabin Air Filters Compare to Other Solutions?
When considering the maintenance of vehicle air quality, the frequency of replacing cabin air filters is a critical factor. However, B2B buyers should also evaluate alternative solutions that can achieve similar outcomes. This analysis compares the standard practice of replacing cabin air filters with two notable alternatives: using high-efficiency particulate air (HEPA) filters and implementing air purification systems.
Comparison Table of Cabin Air Filter Replacement and Alternatives
Comparison Aspect | How Often To Replace Cabin Air Filter | HEPA Filters | Air Purification Systems |
---|---|---|---|
Performance | Reduces allergens and pollutants. | Higher filtration efficiency. | Eliminates a broader range of contaminants. |
Cost | Moderate cost for filters and labor. | Higher initial cost, lower long-term maintenance. | High upfront investment, ongoing operational costs. |
Ease of Implementation | Simple, often DIY. | Requires specific fitting. | Professional installation recommended. |
Maintenance | Every 12,000 to 15,000 miles. | Less frequent, depending on usage. | Regular filter replacements and cleaning needed. |
Best Use Case | Regular vehicle use in urban areas. | Ideal for high dust or allergen environments. | Best for confined spaces with high contamination levels. |
What Are HEPA Filters and How Do They Compare?
HEPA filters offer a more advanced filtration solution compared to standard cabin air filters. They can capture particles as small as 0.3 microns with a minimum efficiency of 99.97%. This makes them particularly effective for environments where allergens and fine particulate matter are a concern.
Pros:
– Superior filtration capability.
– Longer lifespan compared to standard filters.
Cons:
– Higher initial cost and may require specific installation.
– Not always compatible with every vehicle model, necessitating additional research before purchase.
How Do Air Purification Systems Work and What Are Their Benefits?
Air purification systems go beyond the cabin air filter by actively removing pollutants from the air through various technologies, such as activated carbon filters and UV light. These systems are particularly useful in environments with high pollution levels or for individuals with severe allergies.
Pros:
– Comprehensive air quality improvement.
– Can improve overall vehicle hygiene.
Cons:
– Significant upfront investment and ongoing operational costs.
– Installation often requires professional assistance, which can add to the overall expense.
How Should B2B Buyers Decide on the Right Solution?
When selecting the right solution for maintaining vehicle air quality, B2B buyers should consider their specific operational environment and the types of contaminants they are most likely to encounter. For companies operating in urban settings with moderate pollution levels, maintaining a regular cabin air filter replacement schedule may suffice. However, those in industries with higher exposure to allergens or particulates may find HEPA filters or air purification systems to be more beneficial in the long run.
Ultimately, the choice between these options will depend on a careful evaluation of costs, performance needs, and ease of implementation tailored to the unique requirements of the business and its fleet.
Essential Technical Properties and Trade Terminology for how often to replace cabin air filter
What Are the Key Technical Properties of Cabin Air Filters?
When considering the replacement of cabin air filters, understanding the technical specifications is crucial for B2B buyers. Here are essential properties that influence performance and longevity:
1. Material Grade
The material of the cabin air filter significantly impacts its filtration efficiency. Common materials include activated carbon, HEPA (High-Efficiency Particulate Air), and synthetic fibers. Filters made from high-grade materials typically offer better pollutant capture, enhancing air quality within vehicles. Buyers should prioritize filters that meet specific industry standards to ensure optimal performance.
2. Filtration Efficiency
This property indicates the filter’s ability to trap particles of various sizes, measured as a percentage. A higher filtration efficiency means that the filter can remove more dust, pollen, and other airborne contaminants. For B2B buyers, selecting filters with a minimum efficiency reporting value (MERV) rating of 8 or higher is advisable, as this ensures superior air quality for end users.
3. Dust Holding Capacity
This measures how much dust and debris a filter can hold before it needs replacing. Filters with high dust holding capacity can last longer, reducing the frequency of replacements and maintenance costs. B2B purchasers should evaluate this capacity to minimize downtime and ensure continuous operation in various environments.
4. Operating Temperature Range
Cabin air filters must withstand various temperature extremes without degrading. Filters should ideally operate effectively within a range of -20°C to 50°C (-4°F to 122°F). Understanding this range is essential for buyers in regions with diverse climates, as it affects the longevity and performance of the filter.
5. Filter Size and Configuration
Filters come in various sizes and configurations, tailored to fit specific vehicle models. Accurate sizing is crucial to ensure proper airflow and filtration efficiency. B2B buyers should have access to detailed specifications for each filter type to prevent compatibility issues.
What Are Common Trade Terms Related to Cabin Air Filter Replacement?
Familiarizing yourself with industry jargon is vital for effective communication and decision-making in the B2B sector. Here are common trade terms relevant to cabin air filter procurement:
1. OEM (Original Equipment Manufacturer)
OEM filters are produced by the same manufacturer that supplies the vehicle maker. These filters often provide a perfect fit and performance. For B2B buyers, opting for OEM parts can ensure compliance with warranty conditions and maintain vehicle performance.
2. MOQ (Minimum Order Quantity)
MOQ refers to the smallest quantity of a product that a supplier is willing to sell. Understanding MOQ is essential for B2B buyers to manage inventory and cost-effectiveness. Suppliers may set MOQs based on production costs, which can affect pricing strategies.
3. RFQ (Request for Quotation)
An RFQ is a formal document sent to suppliers to solicit pricing and terms for specific products. For B2B buyers, issuing an RFQ can help gather competitive pricing, ensuring that they make informed purchasing decisions.
4. Incoterms (International Commercial Terms)
These are standardized trade terms used in international shipping to define the responsibilities of buyers and sellers. Understanding Incoterms is crucial for B2B transactions, as they clarify costs, risks, and logistics involved in the delivery of cabin air filters.
5. Lead Time
Lead time refers to the period from placing an order to receiving the goods. For B2B buyers, understanding lead times is critical for inventory planning and ensuring that replacement filters are available when needed, thus avoiding operational disruptions.
In summary, being well-versed in the technical properties and trade terminology surrounding cabin air filters is essential for international B2B buyers. This knowledge not only aids in making informed purchasing decisions but also helps in fostering strong supplier relationships and optimizing supply chain management.
Navigating Market Dynamics and Sourcing Trends in the how often to replace cabin air filter Sector
What Are the Key Trends Influencing the Cabin Air Filter Replacement Market?
The global cabin air filter market is currently experiencing dynamic shifts driven by increasing consumer awareness regarding air quality and vehicle maintenance. B2B buyers from regions like Africa, South America, the Middle East, and Europe are noticing a rising demand for efficient filtration solutions as urbanization and industrial activities contribute to air pollution. Technological advancements, such as the development of high-efficiency particulate air (HEPA) filters and activated carbon options, are becoming essential in meeting regulatory standards and consumer expectations.
Emerging trends also indicate a movement towards digital platforms for sourcing cabin air filters. E-commerce and online marketplaces provide international buyers with access to a broader range of suppliers and products, facilitating price comparisons and enhancing procurement efficiency. In addition, the integration of IoT technology in automotive systems allows for real-time monitoring of air quality, prompting timely replacement of filters and creating new opportunities for suppliers to offer value-added services.
How Can Sustainability and Ethical Sourcing Impact the Cabin Air Filter Industry?
As global focus shifts towards sustainability, ethical sourcing is becoming a critical factor for B2B buyers in the cabin air filter sector. The environmental impact of manufacturing processes and materials used in filters is under scrutiny, leading companies to seek eco-friendly alternatives. Suppliers are increasingly adopting sustainable practices, such as utilizing biodegradable materials and minimizing waste during production.
B2B buyers should prioritize suppliers who possess ‘green’ certifications, such as ISO 14001 or those using recycled materials in their products. These certifications not only validate the supplier’s commitment to sustainability but also align with the growing consumer demand for environmentally responsible products. Additionally, transparent supply chains are becoming a necessity, as businesses face pressure to demonstrate ethical sourcing practices and comply with international regulations.
What Is the Historical Context of Cabin Air Filter Replacement?
The concept of cabin air filtration emerged in the automotive industry during the 1980s, primarily in response to growing concerns about air quality within vehicles. Initially, cabin air filters were basic in design, focusing mainly on dust and pollen filtration. However, with advancements in automotive technology and increasing awareness of air pollution’s health effects, the need for more sophisticated filtration systems became apparent.
Over the years, manufacturers have evolved cabin air filters to include features that combat a broader range of contaminants, including smoke, odors, and harmful gases. This evolution has enabled B2B buyers to access a variety of filter types tailored to specific environmental challenges, reflecting the changing dynamics of consumer preferences and regulatory requirements. As the market continues to evolve, understanding these historical trends can provide valuable insights for informed sourcing decisions.
Frequently Asked Questions (FAQs) for B2B Buyers of how often to replace cabin air filter
-
How often should I replace the cabin air filter in my fleet vehicles?
The frequency of cabin air filter replacement can vary based on factors such as vehicle type, usage conditions, and manufacturer recommendations. As a general guideline, it is advisable to replace cabin air filters every 12,000 to 15,000 miles or annually for standard operating conditions. However, in regions with high dust levels or urban environments, more frequent changes may be necessary. Monitoring air quality and vehicle performance can help determine the optimal replacement schedule. -
What are the signs that indicate a cabin air filter needs replacement?
Common signs that your cabin air filter may need replacement include reduced airflow from the HVAC system, unpleasant odors inside the vehicle, and increased dust accumulation on the dashboard. If passengers notice allergy symptoms or respiratory discomfort during travel, it may also indicate poor air filtration. Regular inspections can help identify these issues early and ensure a comfortable environment for drivers and passengers alike. -
How can I ensure the quality of cabin air filters from suppliers?
To ensure quality, source cabin air filters from reputable suppliers who adhere to international quality standards such as ISO certifications. Request samples to evaluate filter performance and construction before placing bulk orders. Additionally, consider suppliers that provide detailed specifications, including filtration efficiency ratings and compatibility with your fleet vehicles. Establishing a quality assurance process can help maintain standards over time. -
What customization options are available for cabin air filters?
Many suppliers offer customization options for cabin air filters, including size, material, and filtration technology. Depending on your fleet’s specific needs, you may request filters that use activated carbon for odor removal or HEPA filters for enhanced allergen filtration. Discussing customization capabilities with potential suppliers can help you identify the best solutions tailored to your operational requirements. -
What are the minimum order quantities (MOQs) for cabin air filters?
Minimum order quantities (MOQs) for cabin air filters can vary significantly among suppliers. Generally, MOQs may range from 50 to several hundred units, depending on the manufacturer’s production capabilities and inventory policies. When negotiating with suppliers, inquire about flexibility in MOQs, especially if you are testing new products or entering a new market. This can help manage cash flow and reduce excess inventory risks. -
What payment terms should I negotiate with cabin air filter suppliers?
Payment terms can greatly impact your cash flow and overall purchasing strategy. Common terms include net 30, net 60, or even payment upon delivery. It’s advisable to negotiate terms that align with your financial capabilities and the supplier’s policies. Consider leveraging early payment discounts or exploring financing options if bulk purchases are necessary. Establishing clear payment terms upfront can prevent misunderstandings later in the transaction process. -
How can I assess the reliability of cabin air filter suppliers in different regions?
To assess supplier reliability, conduct thorough background checks, including evaluating customer reviews, industry certifications, and years in business. Engaging in trade shows or industry conferences can provide opportunities for direct communication and relationship building. Additionally, consider reaching out to other businesses in your region to gather firsthand experiences. Establishing a robust vetting process will help mitigate risks associated with supplier selection. -
What logistics considerations should I be aware of when sourcing cabin air filters internationally?
International logistics can pose challenges, including customs regulations, shipping costs, and lead times. When sourcing cabin air filters, ensure that the supplier has experience with international shipping and can navigate customs effectively. Discuss shipping options and costs upfront, and consider the impact of logistics on your inventory management. Additionally, plan for potential delays by maintaining a buffer stock to avoid disruptions in your operations.
Important Disclaimer & Terms of Use
⚠️ Important Disclaimer
The information provided in this guide, including content regarding manufacturers, technical specifications, and market analysis, is for informational and educational purposes only. It does not constitute professional procurement advice, financial advice, or legal advice.
While we have made every effort to ensure the accuracy and timeliness of the information, we are not responsible for any errors, omissions, or outdated information. Market conditions, company details, and technical standards are subject to change.
B2B buyers must conduct their own independent and thorough due diligence before making any purchasing decisions. This includes contacting suppliers directly, verifying certifications, requesting samples, and seeking professional consultation. The risk of relying on any information in this guide is borne solely by the reader.
Strategic Sourcing Conclusion and Outlook for how often to replace cabin air filter
In conclusion, understanding the frequency of cabin air filter replacement is essential for maintaining vehicle performance and ensuring passenger comfort. For B2B buyers, particularly in diverse markets across Africa, South America, the Middle East, and Europe, strategic sourcing of high-quality filters can enhance operational efficiency and customer satisfaction. Regularly replacing cabin air filters—typically every 12,000 to 15,000 miles—can prevent costly repairs and extend the lifespan of HVAC systems, making it a critical component of vehicle maintenance.
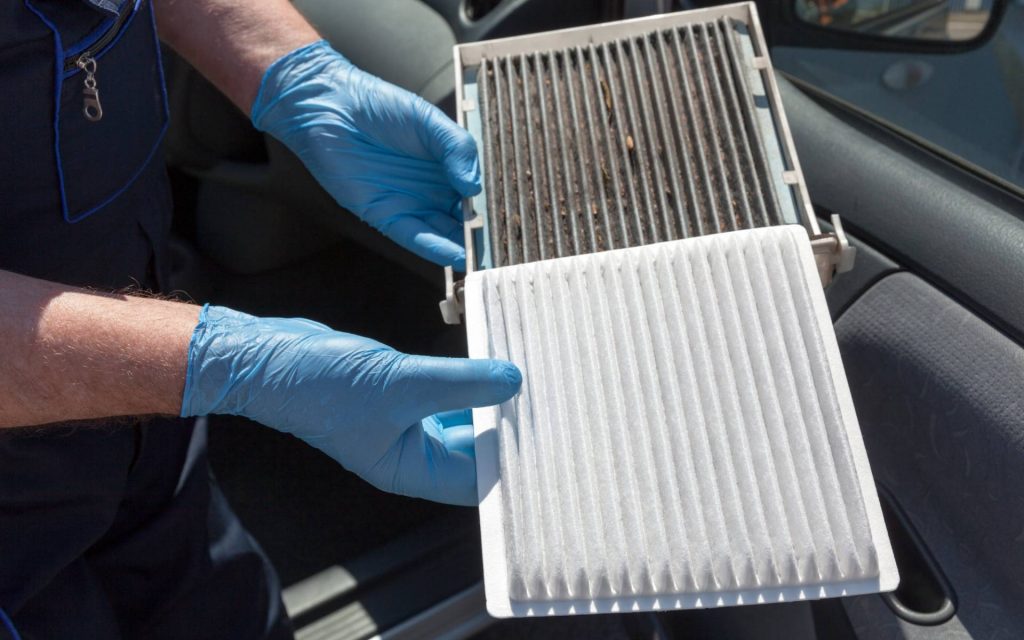
A stock image related to how often to replace cabin air filter.
What are the benefits of strategic sourcing for cabin air filters? By establishing reliable supplier relationships, businesses can secure competitive pricing and ensure consistent product quality. This not only streamlines inventory management but also enhances supply chain resilience in the face of global market fluctuations.
As we look ahead, it is imperative for international B2B buyers to prioritize the procurement of cabin air filters that meet regional standards and environmental regulations. Engaging with suppliers who understand local market dynamics can provide a significant competitive edge. Invest in strategic sourcing today to optimize your vehicle maintenance processes and drive long-term business success.