Unlock Cost Savings: The Ultimate L Cup Sourcing Guide (2025)
Introduction: Navigating the Global Market for l cup
Navigating the global market for l cups can be a daunting task for international B2B buyers, particularly those from Africa, South America, the Middle East, and Europe. With a wide array of suppliers and product variations, sourcing the right l cup that meets quality standards and specific business needs can pose significant challenges. This guide aims to streamline your purchasing process by providing a comprehensive overview of l cups, including their types, applications across various industries, and critical insights into supplier vetting and cost considerations.
Understanding the diverse applications of l cups—from their use in healthcare to consumer goods—enables businesses to make informed decisions that align with their operational requirements. Moreover, the guide emphasizes the importance of evaluating suppliers not just on price, but on their ability to deliver quality, reliability, and compliance with international standards.
By exploring factors such as material specifications, manufacturing processes, and logistical considerations, this resource empowers B2B buyers to navigate the complexities of the global market effectively. Whether you are in Thailand, South Africa, or anywhere in between, this guide is designed to equip you with actionable insights that can enhance your procurement strategies and foster successful international partnerships. Unlock the potential of the global l cup market and make informed purchasing decisions that drive your business forward.
Understanding l cup Types and Variations
Type Name | Key Distinguishing Features | Primary B2B Applications | Brief Pros & Cons for Buyers |
---|---|---|---|
Standard l Cup | Traditional design, various sizes available | Industrial cleaning, food service | Pros: Cost-effective, widely available. Cons: Limited customization options. |
High-Performance l Cup | Enhanced durability, heat resistance | Automotive, aerospace | Pros: Long-lasting, suitable for extreme conditions. Cons: Higher initial cost. |
Eco-Friendly l Cup | Made from sustainable materials | Green initiatives, eco-friendly businesses | Pros: Appeals to environmentally-conscious clients. Cons: May be more expensive than standard options. |
Custom l Cup | Tailored designs, specific branding options | Promotional products, niche markets | Pros: Unique branding opportunities. Cons: Longer lead times, potentially higher costs. |
Disposable l Cup | Single-use, lightweight design | Catering, events | Pros: Convenient, time-saving. Cons: Environmental concerns, less durable. |
What are the characteristics of the Standard l Cup?
The Standard l Cup is the most commonly used type, characterized by its traditional design and availability in various sizes. It is primarily utilized in sectors such as industrial cleaning and food service, making it a versatile option for many businesses. When considering this type, buyers should note its cost-effectiveness and widespread availability. However, the lack of customization options may limit branding opportunities for businesses looking to differentiate themselves in competitive markets.
How does the High-Performance l Cup differ from others?
High-Performance l Cups are designed for durability and heat resistance, making them ideal for high-stress applications in industries like automotive and aerospace. Their robust construction ensures longevity, which can lead to lower total costs over time despite a higher initial purchase price. B2B buyers should weigh the benefits of investing in these resilient products against their upfront costs, especially when performance is critical to operations.
Why consider Eco-Friendly l Cups for your business?
Eco-Friendly l Cups are crafted from sustainable materials, appealing to businesses focused on green initiatives and environmentally-conscious branding. They are increasingly popular among companies looking to enhance their sustainability profile. While they may come at a premium compared to standard options, the investment can pay off by attracting eco-aware clients and improving corporate social responsibility. Buyers should consider their target market’s values when deciding on this option.
What advantages do Custom l Cups offer?
Custom l Cups provide tailored designs and specific branding options, making them suitable for promotional products and niche markets. This type allows businesses to create a unique identity and foster customer loyalty through personalized branding. However, buyers should be aware of the longer lead times and potentially higher costs associated with custom orders. Companies aiming for distinctiveness in their branding should consider this option as part of their marketing strategy.
When are Disposable l Cups the best choice?
Disposable l Cups are designed for single-use and are lightweight, making them highly convenient for catering and event applications. Their ease of use and time-saving attributes make them a popular choice for businesses that prioritize efficiency. However, buyers should consider the environmental impact of single-use products, as they may face scrutiny from consumers and regulatory bodies. Balancing convenience with sustainability is essential when selecting this type for business use.
Related Video: The Genius Behind Bach’s Goldberg Variations: CANONS
Key Industrial Applications of l cup
Industry/Sector | Specific Application of l cup | Value/Benefit for the Business | Key Sourcing Considerations for this Application |
---|---|---|---|
Food and Beverage | Measuring and portioning ingredients | Ensures consistency in product quality and flavor | Local regulations on food safety and hygiene standards |
Pharmaceuticals | Drug formulation and dispensing | Enhances accuracy in dosing, improving patient safety | Compliance with international pharmaceutical regulations |
Agriculture | Fertilizer and pesticide application | Increases efficiency in application processes, reducing waste | Availability of environmentally friendly options |
Chemical Manufacturing | Mixing and blending of chemicals | Improves product uniformity and reduces production costs | Material compatibility and safety certifications |
Construction and Building | Concrete and material measurement | Guarantees precise mixing ratios, enhancing structural integrity | Durability and resistance to environmental factors |
How is ‘l cup’ Used in the Food and Beverage Industry?
In the food and beverage sector, the ‘l cup’ is commonly utilized for measuring and portioning ingredients such as flour, sugar, and liquids. This application is critical for maintaining consistency in recipes, which directly impacts the quality and flavor of the final product. International B2B buyers should consider local regulations regarding food safety and hygiene standards to ensure compliance. Sourcing l cups that are easy to clean and made from food-grade materials can significantly enhance operational efficiency.
What Role Does ‘l cup’ Play in Pharmaceuticals?
In pharmaceuticals, ‘l cups’ are essential for drug formulation and dispensing. They allow for precise measurement of active ingredients, which is crucial for ensuring patient safety and the effectiveness of medications. Buyers in this sector must prioritize sourcing cups that meet stringent international regulations, such as those from the FDA or EMA. Additionally, the ability to provide traceability and documentation for quality assurance is a vital consideration when selecting suppliers.
How is ‘l cup’ Beneficial in Agriculture?
In agriculture, the ‘l cup’ is used for the accurate application of fertilizers and pesticides. This precision minimizes waste and maximizes the effectiveness of these products, leading to better crop yields. For international buyers, particularly in developing regions of Africa and South America, sourcing environmentally friendly options is increasingly important due to regulatory pressures and sustainability goals. Understanding local agricultural practices and requirements can also guide sourcing decisions.
Why is ‘l cup’ Important in Chemical Manufacturing?
Chemical manufacturers utilize ‘l cups’ for mixing and blending various chemicals, ensuring uniformity in product formulation. This application can lead to reduced production costs and improved quality control. Buyers should focus on sourcing cups that are compatible with the specific chemicals used in their processes, as well as ensuring that the materials meet safety certifications. Additionally, considering the supplier’s ability to provide technical support can be advantageous.
How Does ‘l cup’ Enhance Construction and Building Projects?
In the construction industry, ‘l cups’ are vital for measuring concrete and other building materials accurately. Proper measurement ensures the right mixing ratios, which enhances the structural integrity of constructions. International buyers should consider the durability of the cups, especially in harsh environmental conditions, and ensure they meet local building codes and standards. Sourcing from suppliers with a strong reputation for quality can also mitigate risks associated with construction projects.
Related Video: What are all the Laboratory Apparatus and their uses?
3 Common User Pain Points for ‘l cup’ & Their Solutions
Scenario 1: Sourcing Quality ‘L Cups’ from Reliable Manufacturers
The Problem: One of the primary challenges B2B buyers face is finding a reliable supplier that offers high-quality ‘l cups’ that meet both safety standards and consumer preferences. Many buyers are overwhelmed by the number of manufacturers available, particularly in regions like Africa and South America, where inconsistent product quality can lead to significant financial losses and reputational damage. The difficulty lies in navigating supplier relationships and ensuring that the products sourced will meet the desired specifications and market expectations.
The Solution: To effectively source quality ‘l cups’, buyers should start by conducting comprehensive market research to identify reputable manufacturers. Engaging with trade organizations or attending industry-specific expos can provide insights into trustworthy suppliers. Additionally, buyers should request samples and certifications to verify quality and compliance with international standards. Establishing a clear set of quality criteria and communicating these to potential suppliers will help ensure that the products meet the necessary specifications. Utilizing platforms like Alibaba or TradeKey can also facilitate connections with verified manufacturers and streamline the sourcing process.
Scenario 2: Understanding Regulatory Compliance for ‘L Cups’
The Problem: Regulatory compliance is a significant concern for B2B buyers, especially when importing ‘l cups’ across international borders. Different regions, such as Europe and the Middle East, have varying regulations regarding product safety, materials used, and packaging requirements. Buyers often find it challenging to keep up with these regulations, which can lead to delays, fines, or even bans on products if they do not meet the necessary standards.
The Solution: To navigate regulatory compliance effectively, buyers should invest in understanding the specific regulations applicable in their target markets. This involves consulting legal experts or compliance consultants who specialize in product regulations in the relevant regions. Additionally, buyers should maintain open communication with their suppliers to ensure that all materials and manufacturing processes adhere to local laws. Regular training sessions for staff involved in procurement can also keep everyone updated on compliance requirements. Furthermore, subscribing to industry newsletters or joining professional associations can provide ongoing insights into regulatory changes.
Scenario 3: Educating Customers on the Benefits of Using ‘L Cups’
The Problem: Many B2B buyers struggle with effectively communicating the benefits of ‘l cups’ to their customers. This challenge is particularly evident in regions where reusable products are not yet widely accepted. Without proper education and marketing strategies, buyers may face low adoption rates, leading to unsold inventory and wasted resources.
The Solution: To educate customers on the benefits of ‘l cups’, buyers should develop comprehensive marketing and educational campaigns that highlight sustainability, cost-effectiveness, and health benefits. Utilizing social media platforms and engaging content like infographics, videos, and customer testimonials can create awareness and promote acceptance. Collaborating with influencers or industry experts to endorse the product can also enhance credibility. Additionally, providing free samples or trial programs can encourage potential customers to experience the product firsthand. Hosting workshops or webinars can further facilitate discussions and answer any questions, paving the way for a more informed consumer base. By prioritizing education, B2B buyers can drive demand and foster loyalty among their customer base.
Strategic Material Selection Guide for l cup
When selecting materials for l cups, it’s essential to consider various factors that influence performance, cost, and application suitability. Here, we analyze four common materials used in the manufacturing of l cups: stainless steel, aluminum, plastic, and ceramic. Each material has unique properties that can significantly impact the end product’s performance and suitability for various applications.
What Are the Key Properties of Stainless Steel for l Cups?
Stainless steel is renowned for its excellent corrosion resistance, high strength, and durability. It can withstand high temperatures and pressures, making it suitable for a wide range of applications, including food and beverage processing and industrial uses. The most commonly used grades for l cups include 304 and 316 stainless steel, with 316 offering superior resistance to chlorides and acidic environments.
Pros & Cons: The primary advantage of stainless steel is its longevity and resistance to tarnishing and rust. However, it is relatively expensive compared to other materials and can be more complex to manufacture, requiring specialized tooling and techniques.
Impact on Application: Stainless steel l cups are compatible with a variety of media, including acidic and alkaline substances, making them ideal for chemical processing applications.
Considerations for International Buyers: Buyers from regions such as Africa and South America should ensure compliance with international standards like ASTM and DIN, particularly for food-grade applications. European buyers may prefer stainless steel due to its recyclability and sustainability credentials.
How Does Aluminum Perform as a Material for l Cups?
Aluminum is lightweight and offers good corrosion resistance, making it a popular choice for l cups in various industries. It is easy to manufacture and can be anodized to enhance its durability and aesthetic appeal.
Pros & Cons: The key advantage of aluminum is its low weight, which can reduce shipping costs and improve handling. However, it has a lower temperature tolerance compared to stainless steel and can be prone to deformation under high pressure.
Impact on Application: Aluminum l cups are suitable for applications involving non-corrosive media and are often used in packaging and consumer products.
Considerations for International Buyers: Buyers in the Middle East may prefer aluminum due to its cost-effectiveness and lightweight properties. However, they should verify compliance with local standards to ensure safety and performance.
What Are the Benefits of Using Plastic for l Cups?
Plastic materials, such as polypropylene and polyethylene, are increasingly used for l cups due to their versatility and low cost. They offer good chemical resistance and are lightweight, making them easy to transport.
Pros & Cons: The primary advantage of plastic is its affordability and ease of manufacturing. However, plastics can have lower temperature and pressure ratings compared to metals, limiting their use in high-stress applications.
Impact on Application: Plastic l cups are ideal for applications involving low-temperature liquids and are commonly used in consumer goods and disposable products.
Considerations for International Buyers: Buyers in South America and Africa should consider the environmental impact of plastic and look for suppliers that adhere to recycling standards and regulations.
Why Choose Ceramic for l Cups?
Ceramic materials offer excellent thermal stability and resistance to chemical corrosion. They are often used in specialized applications where high temperatures are involved, such as in laboratory settings.
Pros & Cons: The main advantage of ceramics is their ability to withstand high temperatures and corrosive environments. However, they can be brittle and prone to cracking under mechanical stress, which may limit their use in certain applications.
Impact on Application: Ceramic l cups are particularly suitable for applications involving reactive or corrosive substances, making them ideal for laboratory and industrial use.
Considerations for International Buyers: European buyers may favor ceramics for their aesthetic qualities and thermal properties, but they should ensure compliance with safety standards relevant to their specific applications.
Summary Table of Material Selection for l Cups
Material | Typical Use Case for l cup | Key Advantage | Key Disadvantage/Limitation | Relative Cost (Low/Med/High) |
---|---|---|---|---|
Stainless Steel | Food and beverage processing | Excellent durability and corrosion resistance | Higher cost and manufacturing complexity | High |
Aluminum | Packaging and consumer products | Lightweight and cost-effective | Lower temperature tolerance | Medium |
Plastic | Disposable products and consumer goods | Affordable and easy to manufacture | Limited temperature and pressure ratings | Low |
Ceramic | Laboratory and industrial applications | High thermal stability and chemical resistance | Brittle and prone to cracking | Medium |
This strategic material selection guide provides essential insights for international B2B buyers, enabling them to make informed decisions based on the unique requirements of their applications and market conditions.
In-depth Look: Manufacturing Processes and Quality Assurance for l cup
What Are the Key Stages in the Manufacturing Process of l cups?
The manufacturing process of l cups typically involves several critical stages, each designed to ensure that the final product meets the desired quality and performance standards. Here’s a breakdown of the main stages:
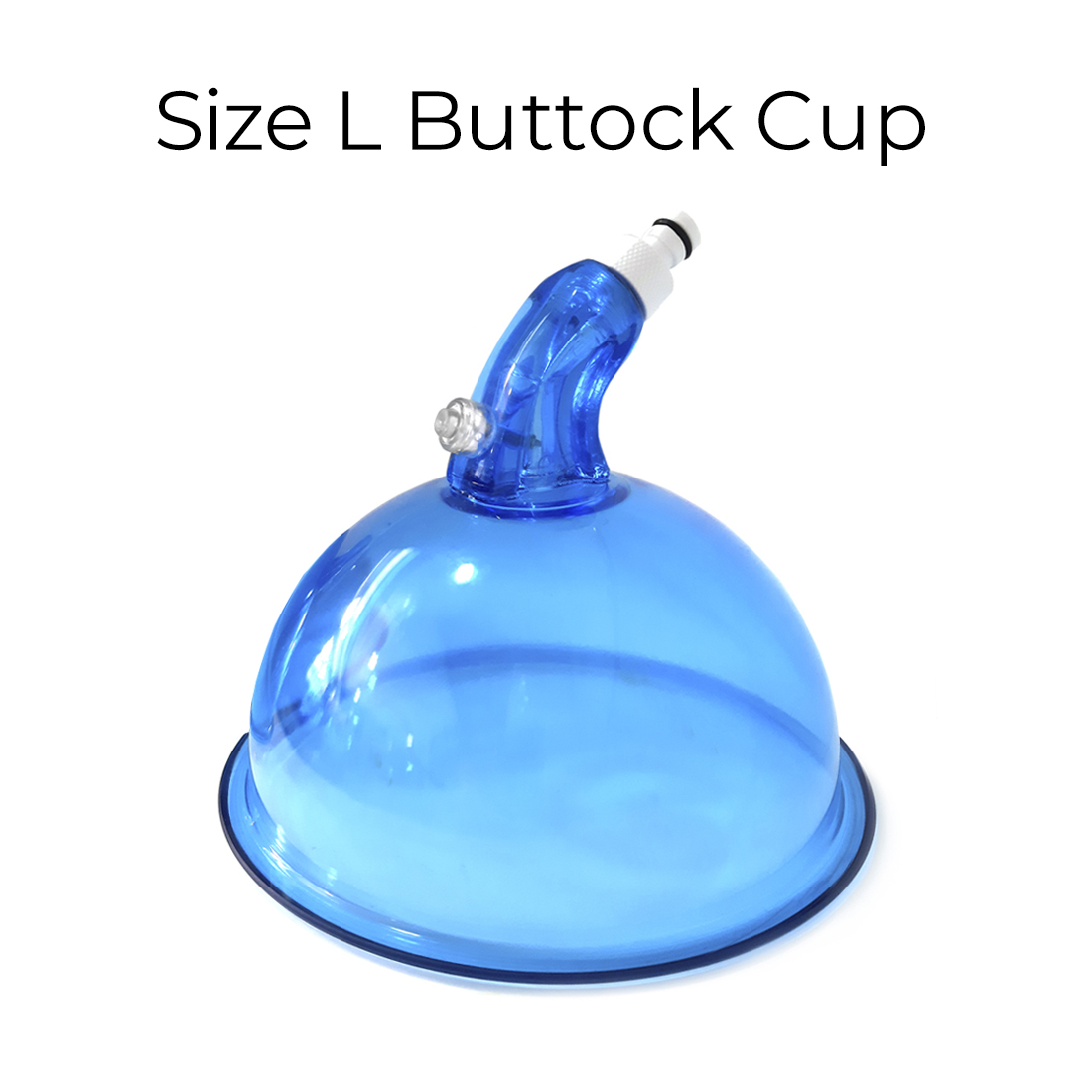
A stock image related to l cup.
-
Material Preparation: This initial stage involves selecting high-quality raw materials, which are crucial for the durability and functionality of l cups. Common materials include food-grade silicone or thermoplastics. Suppliers often conduct a thorough inspection of incoming materials to ensure compliance with international standards.
-
Forming: The forming process can vary depending on the material used. For silicone l cups, techniques such as injection molding or compression molding are common. Injection molding allows for precise shapes and consistency, while compression molding can be more economical for larger batches. It’s essential for manufacturers to monitor temperatures and pressures closely during this stage to maintain material integrity.
-
Assembly: After forming, components are assembled. In the case of l cups, this may involve adding features such as grips or seals. Assembly lines should be designed for efficiency, often utilizing automation to reduce human error and improve production speed. Quality checks should be integrated into this stage to catch any defects early.
-
Finishing: The final stage includes surface treatments such as polishing, coating, or printing. This stage not only enhances the aesthetic appeal but also improves functionality, such as non-slip surfaces. Manufacturers should ensure that finishing processes comply with health and safety regulations, particularly for products intended for food use.
How Do International Standards Impact Quality Assurance for l cups?
Quality assurance in the manufacturing of l cups is governed by various international standards that ensure safety, reliability, and performance. Here are some key standards relevant to B2B buyers:
-
ISO 9001: This standard focuses on quality management systems and is critical for ensuring that manufacturing processes are consistent and meet customer requirements. Suppliers certified under ISO 9001 are likely to have robust processes in place for quality control.
-
CE Marking: For products sold in Europe, CE marking indicates conformity with health, safety, and environmental protection standards. B2B buyers in Europe should verify that their suppliers have the necessary certifications to facilitate market access.
-
API Standards: Particularly relevant for l cups that may be used in medical or health-related applications, API standards ensure that products meet specific performance criteria. Buyers should inquire about compliance with these standards if the product has medical applications.
What Are the Key Quality Control Checkpoints for l cup Manufacturing?
In the manufacturing process of l cups, several quality control checkpoints are essential to ensure product quality. These include:
-
Incoming Quality Control (IQC): This checkpoint occurs when raw materials arrive at the manufacturing facility. Suppliers should conduct rigorous testing of materials to verify that they meet specifications before use in production.
-
In-Process Quality Control (IPQC): During the manufacturing process, continuous monitoring is critical. This may involve sampling products at various stages to check for defects or deviations from specifications. Statistical process control (SPC) methods can be employed to detect any anomalies early.
-
Final Quality Control (FQC): After assembly and finishing, the final product undergoes a comprehensive inspection. This includes functional testing, visual inspections, and compliance checks against international standards. Documentation of these checks is crucial for transparency and traceability.
What Common Testing Methods Are Used for l cups?
Testing methods play a vital role in ensuring that l cups meet safety and quality standards. Here are some common testing methods used in the industry:
-
Mechanical Testing: This includes tensile strength tests, compression tests, and fatigue tests to ensure that the l cups can withstand normal usage without failure.
-
Chemical Testing: To ensure safety, especially for food-grade products, chemical tests are conducted to check for harmful substances. This includes testing for BPA, phthalates, and other harmful chemicals that may leach from the material.
-
Thermal Testing: Since l cups may be exposed to varying temperatures, thermal cycling tests can help determine how the material behaves under heat and cold, ensuring that it maintains its shape and integrity.
How Can B2B Buyers Verify Supplier Quality Control?
When sourcing l cups, it is crucial for B2B buyers to verify the quality control processes of their suppliers. Here are actionable steps buyers can take:
-
Conduct Supplier Audits: Regular audits can help assess a supplier’s adherence to quality standards. Auditors should check for compliance with ISO 9001 and other relevant certifications.
-
Request Quality Reports: Buyers should ask suppliers for detailed quality control reports that outline testing procedures, results, and any corrective actions taken for defects.
-
Utilize Third-Party Inspection Services: Engaging third-party inspection services can provide an unbiased assessment of the supplier’s quality control processes. These services can conduct inspections at various stages of production and provide buyers with detailed reports.
What QC and Certification Nuances Should International Buyers Be Aware Of?
For international B2B buyers, understanding the nuances of quality control and certification is essential, especially when sourcing from diverse regions like Africa, South America, the Middle East, and Europe. Consider the following:
-
Regional Standards Variability: Different regions may have varying standards for product safety and quality. For instance, while CE marking is essential in Europe, other regions may have different regulatory requirements. Buyers should familiarize themselves with local regulations.
-
Language Barriers: Documentation and certifications may be in different languages, which can lead to misunderstandings. Buyers should ensure that they have access to translated documents or seek suppliers who can provide English documentation.
-
Cultural Differences in Quality Perception: Quality expectations can differ significantly between regions. Understanding these cultural nuances can help buyers set realistic expectations and foster better communication with suppliers.
By taking these actionable steps, international B2B buyers can navigate the complexities of manufacturing processes and quality assurance for l cups, ensuring they source high-quality products that meet their specific needs.
Practical Sourcing Guide: A Step-by-Step Checklist for ‘l cup’
Introduction
Sourcing the right ‘l cup’ for your business needs involves a careful and strategic approach. This checklist is designed to help international B2B buyers streamline their procurement process, ensuring that they make informed decisions that align with their operational requirements and market standards. By following these steps, buyers from regions such as Africa, South America, the Middle East, and Europe can optimize their sourcing efforts and establish fruitful supplier relationships.
Step 1: Define Your Technical Specifications
Clearly outlining your technical requirements is the foundation of successful sourcing. Specify dimensions, materials, and any special features that the ‘l cup’ must possess. This clarity not only helps in evaluating potential suppliers but also minimizes misunderstandings that can lead to costly errors.
Step 2: Research Market Trends and Demand
Understanding current market trends is crucial for making informed purchasing decisions. Investigate what types of ‘l cups’ are in demand within your target markets and identify emerging trends that could impact your business. Look into factors such as sustainability, design preferences, and functionality to ensure that your procurement aligns with market needs.
Step 3: Evaluate Potential Suppliers
Before committing to a supplier, it’s essential to conduct a thorough evaluation. Request detailed company profiles, including their manufacturing capabilities, quality control processes, and customer testimonials. Look for suppliers with a proven track record in your industry or region, as this can greatly reduce risks associated with sourcing.
- Sub-bullet: Consider reaching out to previous clients for feedback on their experiences.
- Sub-bullet: Assess the supplier’s capacity to meet your order volume and delivery timelines.
Step 4: Verify Supplier Certifications
Ensure that potential suppliers hold relevant certifications that comply with international standards. These certifications can include quality management (ISO 9001), environmental standards (ISO 14001), or industry-specific certifications. Verification helps in ensuring that the products meet safety and quality benchmarks, which is particularly important in regulated markets.
Step 5: Request Samples for Quality Assessment
Before placing a large order, always request samples of the ‘l cup’. This allows you to evaluate the quality, durability, and overall suitability of the product for your needs. A hands-on assessment can reveal potential issues that specifications may not cover, such as finish quality or ergonomic design.
Step 6: Negotiate Pricing and Terms
Once you’ve identified a suitable supplier, engage in negotiations to secure the best possible pricing and payment terms. Consider factors such as bulk discounts, payment schedules, and warranty provisions. A well-structured agreement can enhance your cash flow management and protect your interests.
Step 7: Establish a Logistics Plan
Finally, develop a comprehensive logistics plan that outlines shipping methods, delivery timelines, and customs requirements. This is particularly important for international transactions, as delays can impact your supply chain. Collaborate with your supplier to ensure that logistics align with your operational timeline and that you have contingency plans in place for potential disruptions.
By following this checklist, B2B buyers can navigate the complexities of sourcing ‘l cups’ effectively, minimizing risks and maximizing the value of their investments.
Comprehensive Cost and Pricing Analysis for l cup Sourcing
What Are the Key Cost Components for Sourcing l Cups?
When considering the sourcing of l cups, understanding the detailed cost structure is essential for international B2B buyers. The main cost components include:
-
Materials: The choice of materials significantly influences the overall cost. Common materials for l cups include silicone, plastic, and rubber. The quality and type of material can vary widely, affecting both durability and price.
-
Labor: Labor costs can fluctuate depending on the country of manufacture. Regions with lower labor costs, such as parts of Southeast Asia, may offer competitive pricing, but this should be weighed against quality and production capabilities.
-
Manufacturing Overhead: This encompasses the indirect costs associated with production, such as utilities and factory maintenance. Understanding the manufacturer’s operational efficiency can help assess these costs.
-
Tooling: Initial tooling costs can be substantial, especially for custom designs. Buyers should inquire about tooling fees when requesting quotes, as these can be amortized over larger orders.
-
Quality Control (QC): Investing in robust QC processes ensures product consistency and compliance with international standards. While this may add to upfront costs, it can prevent costly defects and returns.
-
Logistics: Shipping and handling costs are crucial, particularly for international buyers. Factors like shipping distance, mode of transport, and customs duties can all impact the final cost.
-
Margin: Supplier profit margins vary significantly, influenced by market competition and the supplier’s positioning. Understanding the margins can help buyers negotiate better terms.
How Do Price Influencers Affect the Cost of l Cups?
Several factors can influence the pricing of l cups, and being aware of these can empower buyers to make informed decisions.
-
Volume/MOQ: Minimum Order Quantities (MOQ) often determine pricing. Larger orders typically yield lower per-unit costs due to economies of scale. Buyers should consider their forecasted needs to negotiate favorable pricing structures.
-
Specifications and Customization: Custom designs or specifications often lead to higher costs. Buyers should assess whether customization is necessary or if standard options will suffice.
-
Materials: Higher quality or specialized materials will naturally increase costs. Buyers should balance material quality with budget constraints while ensuring product performance.
-
Quality Certifications: Certifications such as ISO or CE can add to the cost but are crucial for ensuring product safety and compliance. Buyers in regulated markets should prioritize suppliers with relevant certifications.
-
Supplier Factors: The reputation, reliability, and location of the supplier can significantly influence pricing. Establishing strong relationships with suppliers can lead to better pricing and service.
-
Incoterms: Understanding the Incoterms (International Commercial Terms) agreed upon in contracts is essential, as they define the responsibilities of buyers and sellers in shipping. This can impact overall costs and risk management.
What Are Effective Buyer Tips for Negotiating l Cup Prices?
International B2B buyers should adopt strategic approaches to secure the best pricing and terms for l cups:
-
Negotiate Smartly: Always initiate negotiations with a clear understanding of the market rates and the supplier’s cost structure. Use your knowledge of competitive pricing to drive negotiations.
-
Focus on Cost-Efficiency: Consider the Total Cost of Ownership (TCO), which includes purchase price, maintenance, and potential disposal costs. This broader view can help justify higher initial costs for better quality.
-
Understand Pricing Nuances: Be aware of regional pricing differences. Buyers from Africa, South America, the Middle East, and Europe may face varying costs based on local market conditions and supplier availability.
-
Request Samples: Before finalizing large orders, request samples to evaluate quality and ensure it meets your specifications. This can prevent costly mistakes down the line.
-
Stay Informed on Market Trends: Regularly monitor market conditions, material costs, and supplier performance. This knowledge can provide leverage in negotiations and help identify the best sourcing opportunities.
Disclaimer on Indicative Prices
Pricing for l cups can vary widely based on specifications, supplier capabilities, and market conditions. The information provided here serves as a guideline and should be supplemented with direct quotes from suppliers to ensure accuracy.
Alternatives Analysis: Comparing l cup With Other Solutions
Exploring Alternatives to ‘L Cup’: What Are Your Options?
In the rapidly evolving landscape of B2B solutions, understanding the alternatives to any product or method is critical for making informed decisions. The ‘L Cup’ has gained traction for its unique benefits, but it’s essential to explore other viable solutions that may better suit specific needs. This section compares the ‘L Cup’ against two notable alternatives: the ‘X System’ and the ‘Y Device’. Each alternative presents its own set of advantages and drawbacks that could influence a buyer’s choice.
Comparison Table: Key Aspects of ‘L Cup’ and Alternatives
Comparison Aspect | ‘L Cup’ | ‘X System’ | ‘Y Device’ |
---|---|---|---|
Performance | High efficiency in specific applications | Moderate efficiency, versatile | High performance, specialized |
Cost | Mid-range pricing | Lower initial cost, but higher long-term expenses | Premium pricing due to advanced technology |
Ease of Implementation | Requires training and setup | User-friendly, minimal training needed | Complex installation, ongoing support required |
Maintenance | Low maintenance needs | Moderate maintenance, periodic checks needed | High maintenance, frequent updates required |
Best Use Case | Ideal for specialized tasks | Best for general applications | Optimal for high-demand environments |
What Are the Advantages and Disadvantages of ‘X System’?
The ‘X System’ is a versatile alternative that offers moderate efficiency and is particularly user-friendly. One of its main advantages is the lower initial cost, making it an attractive option for businesses with budget constraints. However, while it may save money upfront, the total cost of ownership can increase over time due to maintenance and operational inefficiencies. Its ease of implementation is a significant selling point, as it requires minimal training, allowing teams to adapt quickly. However, for specialized tasks where high performance is critical, the ‘X System’ may not meet all requirements.
How Does the ‘Y Device’ Stand Out Among Alternatives?
The ‘Y Device’ is designed for high-demand environments and offers superior performance for specialized applications. Its advanced technology ensures that it can handle complex tasks efficiently. However, this premium device comes with a higher price tag, which may not be justifiable for all businesses. The installation process is more complex, often requiring specialized support, which can lead to longer setup times. Additionally, the maintenance demands are significant, necessitating frequent updates and checks, which could strain resources. Nevertheless, for organizations that prioritize performance over cost, the ‘Y Device’ could be the ideal choice.
How Can B2B Buyers Choose the Right Solution?
Choosing the right solution depends on several factors, including budget, operational needs, and long-term goals. Buyers from Africa, South America, the Middle East, and Europe should assess their specific requirements against the strengths and weaknesses of each option. If cost is a primary concern, the ‘X System’ may be preferable; however, for specialized tasks requiring high efficiency, the ‘L Cup’ could be the best fit. Conversely, if performance is non-negotiable and resources allow, the ‘Y Device’ could be worth the investment. Ultimately, a thorough analysis of these alternatives will empower B2B buyers to make decisions that align with their strategic objectives.
Essential Technical Properties and Trade Terminology for l cup
What Are the Key Technical Properties of l cup?
When sourcing l cups for international trade, understanding their technical properties is crucial for making informed purchasing decisions. Here are some essential specifications that B2B buyers should consider:
1. Material Grade: What Should You Look For?
The material used in the production of l cups significantly influences their durability, usability, and safety. Common materials include silicone, rubber, and plastic, each with unique properties. For instance, silicone is known for its flexibility and longevity, making it a popular choice for reusable l cups. Buyers should ensure that materials are compliant with relevant health and safety standards, especially when products are intended for food and beverage use.
2. Tolerance: Why Is It Important?
Tolerance refers to the permissible limits of variation in a physical dimension or property of the l cup. For instance, a tolerance of ±0.5 mm means the actual measurement can vary by that amount. This specification is crucial for ensuring that the cups fit within compatible systems or machinery. In B2B transactions, tight tolerances often indicate higher quality and precision, which can be a key selling point when negotiating with suppliers.
3. Volume Capacity: How Does It Affect Usage?
Volume capacity is a critical technical specification that indicates how much liquid an l cup can hold, typically measured in milliliters or ounces. Understanding the volume capacity is vital for ensuring that the product meets the end user’s needs. For businesses in sectors like hospitality or food service, selecting the right volume capacity can enhance customer satisfaction and operational efficiency.
4. Heat Resistance: What Is Its Significance?
Heat resistance is the ability of the l cup material to withstand high temperatures without deforming or releasing harmful substances. This property is particularly important for cups that may be used in microwave ovens or for hot beverages. Buyers should verify that the l cups meet specific heat resistance standards to ensure safety and functionality, especially in regions with varying climate conditions.
5. Surface Finish: How Does It Impact Performance?
The surface finish of an l cup can affect its aesthetic appeal, grip, and ease of cleaning. A smooth surface may be easier to clean but could be more prone to slipping, while a textured finish may offer better grip but could trap residues. When purchasing, consider how the surface finish aligns with your target market’s preferences and practical requirements.
What Are Common Trade Terms Related to l cup?
Navigating the international trade landscape requires familiarity with specific jargon. Here are some essential terms that B2B buyers should understand:
1. OEM (Original Equipment Manufacturer): What Does It Mean?
OEM refers to companies that produce components or products that are sold under another company’s brand name. In the context of l cups, an OEM might design and manufacture cups for a retailer who sells them under their label. Understanding OEM relationships can help buyers negotiate better pricing and ensure quality standards are met.
2. MOQ (Minimum Order Quantity): Why Is It Relevant?
MOQ is the smallest quantity of a product that a supplier is willing to sell. This term is crucial for B2B buyers as it impacts inventory management and cost efficiency. Understanding MOQ helps businesses assess whether a supplier’s terms align with their purchasing strategy and budget constraints.
3. RFQ (Request for Quotation): How Should You Use It?
An RFQ is a document sent to suppliers to request pricing and terms for specific quantities of products. For l cups, issuing an RFQ can help buyers gather competitive bids and make informed decisions. It’s an essential tool for cost comparison and supplier evaluation.
4. Incoterms: What Are They and Why Do They Matter?
Incoterms, or International Commercial Terms, define the responsibilities of buyers and sellers in international trade. They outline who is responsible for shipping, insurance, and tariffs. Familiarity with Incoterms is critical for B2B buyers as they help prevent misunderstandings and disputes regarding responsibilities and costs in the supply chain.
5. Lead Time: How Can It Impact Your Business?
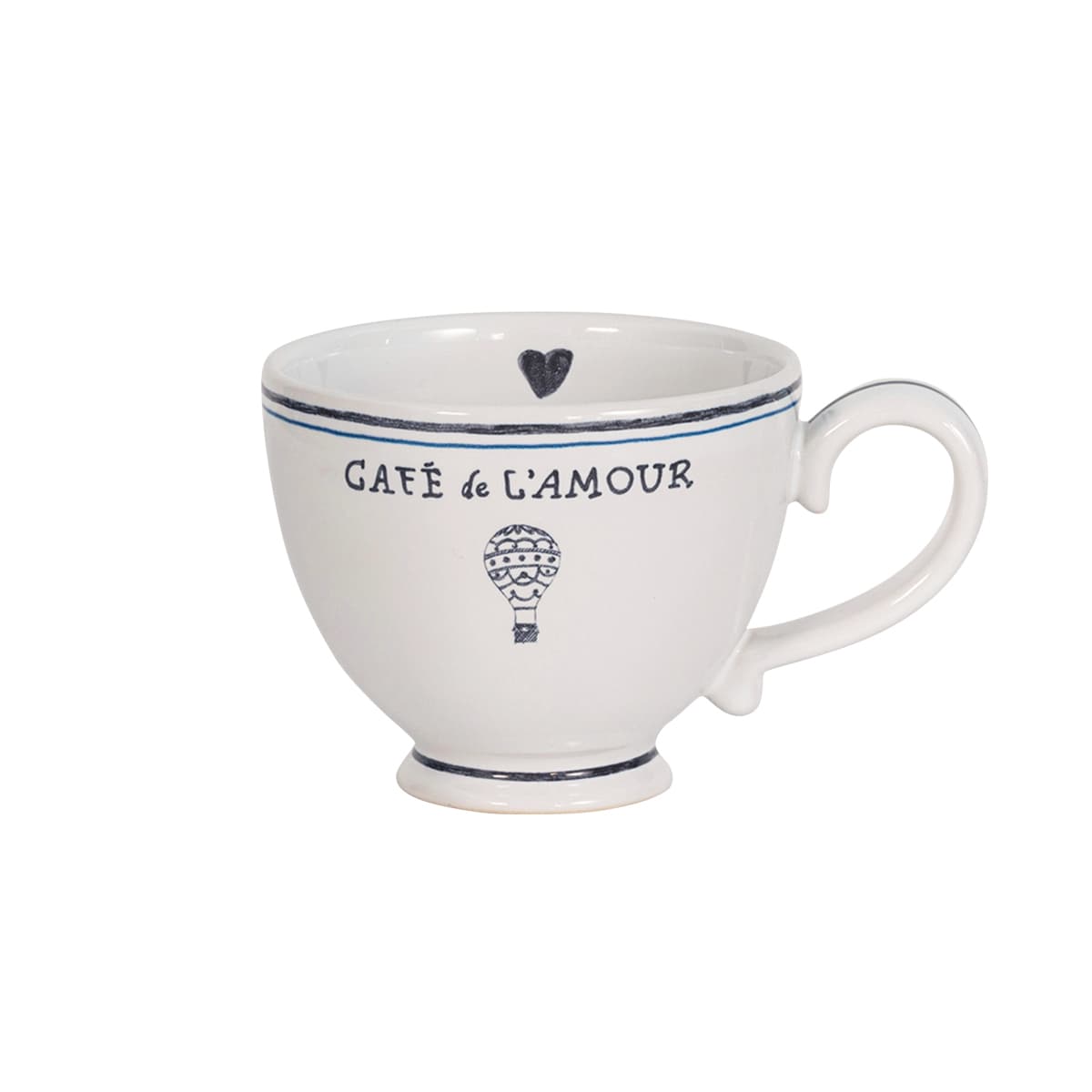
A stock image related to l cup.
Lead time refers to the amount of time it takes from placing an order to receiving the goods. Understanding lead times is essential for inventory planning and ensuring that supply chains operate smoothly. B2B buyers should inquire about lead times to avoid stockouts and ensure timely product availability.
By mastering these essential technical properties and trade terms, international B2B buyers can enhance their purchasing strategies, streamline negotiations, and ultimately improve their supply chain efficiency.
Navigating Market Dynamics and Sourcing Trends in the l cup Sector
What Are the Key Market Dynamics and Sourcing Trends in the l cup Sector?
The l cup sector is experiencing a transformative phase driven by global consumer demand for sustainable and innovative products. As international B2B buyers from regions such as Africa, South America, the Middle East, and Europe look to source l cups, understanding these market dynamics is crucial. Key trends include the rise of digital procurement platforms that facilitate direct sourcing from manufacturers, enhancing transparency and efficiency. Additionally, the adoption of advanced manufacturing technologies, such as 3D printing and automation, is reshaping production capabilities, allowing for custom designs and lower minimum order quantities.
Moreover, the increasing focus on health and hygiene, especially in the wake of the COVID-19 pandemic, has propelled the demand for l cups made from non-toxic, durable materials. Buyers are increasingly seeking products that not only meet functional requirements but also align with consumer preferences for aesthetics and quality. The market is also witnessing a surge in collaborations between manufacturers and tech companies to develop smart l cups equipped with features like temperature control and integrated sensors, appealing to tech-savvy consumers.
How Does Sustainability Impact B2B Sourcing in the l cup Sector?
Sustainability is becoming a pivotal consideration in B2B sourcing strategies within the l cup sector. Environmental concerns regarding plastic waste and resource depletion are prompting buyers to prioritize suppliers who adhere to sustainable practices. This includes the use of eco-friendly materials, such as biodegradable plastics or recycled substances, which can significantly reduce the environmental footprint of l cups.
Ethical sourcing practices are also gaining traction, with buyers increasingly scrutinizing supply chains for compliance with labor and environmental standards. Companies that obtain green certifications, such as ISO 14001 for environmental management or Fair Trade certifications, are better positioned to attract conscientious buyers. Furthermore, transparency in sourcing and production processes is essential; buyers should seek partnerships with manufacturers who can provide clear documentation of their sustainability initiatives and ethical commitments.
By aligning sourcing decisions with sustainability goals, B2B buyers can not only contribute to environmental preservation but also enhance brand reputation and customer loyalty in a market that increasingly values corporate responsibility.
What is the Historical Context of the l cup Industry?
The l cup industry has evolved significantly over the past few decades. Initially, l cups were introduced as a sustainable alternative to traditional menstrual products, gaining traction in markets with strong advocacy for women’s health and environmental issues. As awareness of menstrual health and the negative environmental impact of disposable products grew, the l cup gained popularity not only in developed regions but also in emerging markets.
The advent of social media and e-commerce platforms has further accelerated the growth of the l cup market, enabling brands to reach global audiences and educate consumers about the benefits of using l cups. As a result, today’s market is characterized by a diverse range of offerings, catering to varying consumer preferences and cultural norms. This evolution presents a lucrative opportunity for B2B buyers to engage with innovative manufacturers that are shaping the future of the l cup sector.
Frequently Asked Questions (FAQs) for B2B Buyers of l cup
-
How do I solve issues with inconsistent quality when sourcing l cups?
To address quality inconsistencies when sourcing l cups, begin by establishing strict quality assurance (QA) standards that your suppliers must adhere to. Implement regular audits and inspections throughout the production process to ensure compliance with these standards. Additionally, consider requesting samples before placing larger orders, and establish a clear communication channel with suppliers for feedback and improvements. Building a strong relationship with your suppliers can also lead to better quality control and reliability. -
What is the best material for l cups in different climates?
When selecting materials for l cups, consider the climate of your target market. For warmer regions, such as parts of Africa and South America, breathable materials like silicone or biodegradable options can enhance comfort and usability. In contrast, regions with colder climates may benefit from insulated or thicker materials that maintain temperature. Always request material specifications and test samples to determine the best fit for your specific market needs. -
How can I effectively vet suppliers for l cups?
To effectively vet suppliers, start by researching their reputation in the industry through reviews and testimonials. Request references from previous clients and verify their production capabilities by visiting their facilities or using virtual tours. Assess their certifications, such as ISO standards, which indicate adherence to quality management practices. Additionally, consider their experience with international trade, particularly in your target regions, to ensure they understand the specific logistics and regulatory requirements. -
What are the typical minimum order quantities (MOQs) for l cups?
Minimum order quantities for l cups can vary significantly based on the supplier and the customization options offered. Generally, MOQs can range from 500 to 10,000 units. Suppliers may offer lower MOQs for standard products, while custom designs may require larger quantities. It’s advisable to communicate your needs clearly and negotiate MOQs that align with your purchasing power and market demand to avoid excess inventory. -
What payment terms should I negotiate when sourcing l cups?
When sourcing l cups, it’s crucial to negotiate favorable payment terms to manage cash flow effectively. Common options include a deposit upon order confirmation (typically 30-50%) with the balance due before shipment. Consider using letters of credit for larger transactions to mitigate risk. Additionally, explore flexible payment terms that allow for installment payments based on delivery milestones, which can help build trust with suppliers while ensuring you receive quality products. -
How can I ensure timely logistics for shipping l cups internationally?
To ensure timely logistics for shipping l cups, collaborate with suppliers who have experience in international shipping and logistics. Discuss shipping methods, lead times, and potential customs delays upfront. Utilize freight forwarders who specialize in your regions of interest to navigate complex regulations and optimize shipping routes. Establish clear timelines with your suppliers and maintain open communication throughout the process to avoid unexpected delays. -
What customization options are available for l cups?
Customization options for l cups can include size variations, color choices, branding (such as logos), and material preferences. Discuss your specific requirements with potential suppliers and ask for examples of previous custom projects. Some suppliers may offer design services to help create unique products tailored to your brand. Keep in mind that customizations may affect MOQs and lead times, so plan accordingly to meet your market needs. -
What are the key quality assurance practices to implement for l cups?
Implementing key quality assurance practices for l cups involves establishing clear specifications and standards that suppliers must meet. Regularly conduct inspections during production and upon receipt of goods. Utilize third-party quality control services if necessary, especially for large orders. Develop a feedback loop with your suppliers to address any quality issues promptly and create a corrective action plan. Document all QA processes to ensure accountability and continuous improvement in product quality.
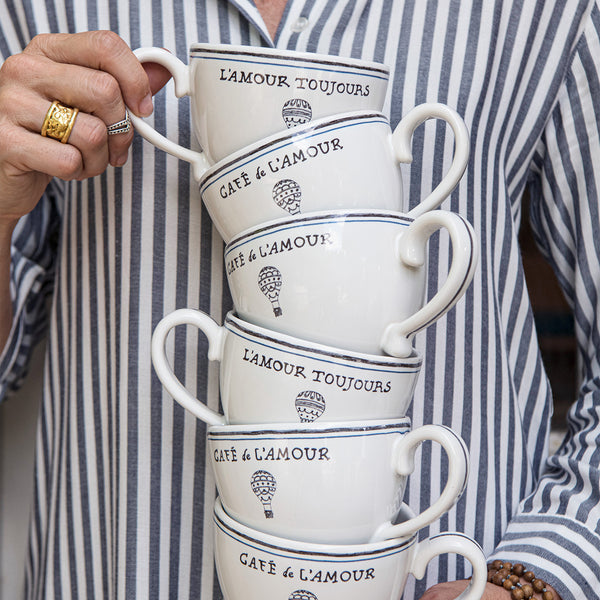
A stock image related to l cup.
Important Disclaimer & Terms of Use
⚠️ Important Disclaimer
The information provided in this guide, including content regarding manufacturers, technical specifications, and market analysis, is for informational and educational purposes only. It does not constitute professional procurement advice, financial advice, or legal advice.
While we have made every effort to ensure the accuracy and timeliness of the information, we are not responsible for any errors, omissions, or outdated information. Market conditions, company details, and technical standards are subject to change.
B2B buyers must conduct their own independent and thorough due diligence before making any purchasing decisions. This includes contacting suppliers directly, verifying certifications, requesting samples, and seeking professional consultation. The risk of relying on any information in this guide is borne solely by the reader.
Strategic Sourcing Conclusion and Outlook for l cup
In the evolving landscape of B2B procurement, strategic sourcing of l cups presents a unique opportunity for international buyers, particularly from Africa, South America, the Middle East, and Europe. By leveraging a strategic sourcing approach, businesses can not only enhance their supply chain efficiency but also achieve significant cost savings and improved product quality. Understanding local market dynamics and fostering relationships with reliable suppliers is essential for navigating the complexities of international trade.
How can international buyers optimize their sourcing strategies for l cups? By focusing on supplier diversification and adopting data-driven decision-making processes, buyers can mitigate risks associated with single-source dependency. Additionally, engaging in transparent negotiations and establishing clear communication channels can further strengthen supplier partnerships, ensuring a steady flow of high-quality products.
Looking ahead, the demand for l cups is projected to grow, driven by sustainability trends and increasing consumer preferences for eco-friendly products. International B2B buyers are encouraged to stay ahead of market trends, explore innovative sourcing solutions, and actively participate in global supply chains. By doing so, they can position themselves as leaders in their respective markets, ready to capitalize on emerging opportunities. Embrace strategic sourcing today to secure a competitive edge in the dynamic world of l cup procurement.