Unlock Cost Savings with Magnesia Carbon Solutions (2025)
Introduction: Navigating the Global Market for magnesia carbon
In the ever-evolving landscape of global materials procurement, sourcing magnesia carbon can present unique challenges for international B2B buyers. This critical material, known for its exceptional thermal stability and resistance to chemical attack, is essential in various industries, including steelmaking, construction, and refractory applications. As businesses in Africa, South America, the Middle East, and Europe—ranging from Kenya to Germany—navigate the complexities of sourcing magnesia carbon, understanding the market dynamics is crucial.
This comprehensive guide is designed to equip B2B buyers with actionable insights into the types and applications of magnesia carbon, effective supplier vetting processes, and cost considerations. By delving into the specifics of this material, the guide empowers decision-makers to make informed purchasing choices that align with their operational needs and budget constraints.
Additionally, it addresses the diverse sourcing challenges faced by international buyers, including supply chain disruptions and varying quality standards across regions. With this guide, businesses can strategically approach their procurement processes, ensuring they select reliable suppliers who meet their unique requirements. By leveraging the insights provided, buyers can enhance their competitive advantage and foster sustainable partnerships in the global market for magnesia carbon.
Understanding magnesia carbon Types and Variations
Type Name | Key Distinguishing Features | Primary B2B Applications | Brief Pros & Cons for Buyers |
---|---|---|---|
Standard Magnesia Carbon | High thermal stability, good slag resistance | Steelmaking, foundries | Pros: Cost-effective; Cons: Limited lifespan under extreme conditions. |
Low Cement Magnesia Carbon | Reduced binder content, enhanced mechanical strength | Refractory linings, high-temperature furnaces | Pros: Improved durability; Cons: Higher initial cost. |
High Purity Magnesia Carbon | Low impurities, superior performance in extreme conditions | Aerospace, advanced manufacturing | Pros: Excellent thermal and chemical resistance; Cons: Expensive. |
Magnesia Carbon Bricks | Pre-formed shapes, easy installation | Cement kilns, incinerators | Pros: Labor-saving; Cons: Limited adaptability on-site. |
Magnesia Carbon Mortars | Flexible application, good adhesion properties | Repair works, maintenance | Pros: Versatile; Cons: Requires skilled application. |
What Are the Characteristics of Standard Magnesia Carbon?
Standard Magnesia Carbon is characterized by its high thermal stability and resistance to slag, making it a popular choice in steelmaking and foundries. This type typically has a balanced composition that allows it to perform well under moderate operational conditions. B2B buyers should consider the cost-effectiveness of this variant, especially for industries where budget constraints are significant. However, it is essential to note that while it offers good performance, its lifespan may be limited when exposed to extreme temperatures or corrosive environments.
How Does Low Cement Magnesia Carbon Enhance Performance?
Low Cement Magnesia Carbon is distinguished by its reduced binder content, which enhances its mechanical strength and durability. This type is particularly suitable for refractory linings and high-temperature furnaces, where performance is critical. B2B purchasers should weigh the initial higher costs against the long-term benefits of improved durability and reduced maintenance needs. Given its advanced properties, it is an ideal choice for businesses looking to minimize downtime and operational disruptions.
Why Choose High Purity Magnesia Carbon for Specialized Applications?
High Purity Magnesia Carbon is known for its low impurity levels, offering superior performance in extreme conditions. This variant is particularly favored in specialized sectors such as aerospace and advanced manufacturing, where reliability and performance are non-negotiable. Buyers should be prepared for a higher price point, but the investment can yield significant returns in terms of operational efficiency and product quality. For companies prioritizing top-tier materials, this type is a must-consider option.
What Are the Advantages of Magnesia Carbon Bricks for Industrial Applications?
Magnesia Carbon Bricks are pre-formed shapes designed for easy installation, making them ideal for applications in cement kilns and incinerators. Their ease of use can lead to significant labor savings, which is a critical consideration for B2B buyers focused on operational efficiency. However, these bricks may have limitations in adaptability for on-site adjustments, which should be factored into purchasing decisions. Understanding the specific requirements of the installation site can help buyers make informed choices.
How Can Magnesia Carbon Mortars Benefit Maintenance Operations?
Magnesia Carbon Mortars offer flexibility in application and possess good adhesion properties, making them suitable for repair works and maintenance tasks. Their versatility allows for use in various industrial settings, which can be advantageous for businesses that require adaptable solutions. However, the application of these mortars often necessitates skilled labor, which can pose a challenge for some companies. Buyers should consider their workforce’s capabilities and training needs when opting for this type of magnesia carbon.
Related Video: Construction process of the converter wall with magnesia carbon bricks
Key Industrial Applications of magnesia carbon
Industry/Sector | Specific Application of magnesia carbon | Value/Benefit for the Business | Key Sourcing Considerations for this Application |
---|---|---|---|
Steel Manufacturing | Lining for Electric Arc Furnaces | Enhances thermal stability and reduces operational costs | Quality certification, sourcing from reputable suppliers |
Cement Production | Refractories for rotary kilns | Increases lifespan of kiln linings, reducing downtime | Compatibility with local materials and environmental regulations |
Foundries | Core and mold production | Improves casting quality and reduces defects | Consistency in properties and local availability |
Glass Manufacturing | Crucibles and furnace linings | High thermal shock resistance, leading to efficiency | Temperature resistance ratings and supplier reliability |
Non-ferrous Metal Smelting | Lining for furnaces in aluminum production | Reduces energy consumption and enhances productivity | Availability of specific grades and compliance with international standards |
How is Magnesia Carbon Used in Steel Manufacturing?
In the steel manufacturing sector, magnesia carbon is primarily utilized for lining electric arc furnaces. This application is critical as it provides enhanced thermal stability and resistance to slag erosion, which are vital for maintaining operational efficiency. International B2B buyers, particularly from regions like Africa and Europe, should prioritize sourcing high-quality magnesia carbon that meets specific industry standards to ensure reduced operational costs and extended service life of the furnace linings.
What Role Does Magnesia Carbon Play in Cement Production?
Magnesia carbon refractories are commonly used in rotary kilns within the cement industry. These materials significantly increase the lifespan of kiln linings, which minimizes unplanned downtimes and maintenance costs. Buyers from South America and the Middle East should consider the compatibility of magnesia carbon with local materials and the environmental regulations that may impact its use, ensuring compliance while optimizing production efficiency.
How is Magnesia Carbon Beneficial for Foundries?
In foundries, magnesia carbon is employed in core and mold production, offering improved casting quality and reduced defects. The material’s thermal properties contribute to better heat retention during the casting process, which is essential for achieving precise dimensions and surface finishes. B2B buyers should focus on suppliers that provide consistent properties and reliable local availability to maintain production schedules and quality standards.
Why is Magnesia Carbon Important in Glass Manufacturing?
The glass manufacturing industry utilizes magnesia carbon in crucibles and furnace linings due to its high thermal shock resistance. This characteristic allows manufacturers to operate at higher temperatures without compromising the integrity of the furnace, leading to improved efficiency and reduced energy costs. Buyers should evaluate the temperature resistance ratings of the magnesia carbon products and ensure supplier reliability to avoid production interruptions.
How Does Magnesia Carbon Enhance Non-ferrous Metal Smelting?
In the non-ferrous metal smelting sector, magnesia carbon is used for lining furnaces, particularly in aluminum production. Its properties help reduce energy consumption and enhance overall productivity, making it a valuable asset for manufacturers. For international buyers, it is crucial to assess the availability of specific grades of magnesia carbon and ensure compliance with international standards to facilitate smooth operations and maintain competitive advantages in the market.
Related Video: The production process of magnesia carbon brick
3 Common User Pain Points for ‘magnesia carbon’ & Their Solutions
Scenario 1: Inconsistent Product Quality Leading to Operational Delays
The Problem:
B2B buyers in industries such as steel manufacturing and refractory production often face the challenge of inconsistent quality in magnesia carbon products. Variability in chemical composition and physical properties can lead to issues during production, resulting in subpar end products and costly operational delays. For buyers in regions like Kenya or Brazil, where local suppliers may not adhere to stringent quality control standards, this inconsistency can severely impact production timelines and profitability.
The Solution:
To mitigate quality issues, international buyers should prioritize sourcing magnesia carbon from suppliers with robust quality assurance processes. Look for manufacturers that provide detailed product specifications, including chemical analyses and performance metrics. Implement a comprehensive vendor evaluation process that includes site visits and audits to assess production facilities and quality control measures. Additionally, consider establishing long-term partnerships with trusted suppliers who demonstrate reliability and consistency. By ensuring that the sourced magnesia carbon meets industry standards, you can significantly reduce the risk of operational disruptions.
Scenario 2: High Cost of Magnesia Carbon Products Impacting Budget
The Problem:
In regions with fluctuating currencies and economic instability, such as parts of South America and the Middle East, the high cost of magnesia carbon can pose a significant financial burden for manufacturers. Buyers may find themselves squeezed between the need for quality materials and the constraints of their operating budgets, leading to difficult decisions that could compromise production quality or project timelines.
The Solution:
To navigate high costs, buyers should explore bulk purchasing agreements with suppliers to secure better pricing. Engaging in long-term contracts can help stabilize costs and provide predictability in budgeting. Additionally, consider evaluating alternative suppliers from different regions, such as Europe, where competitive pricing may be available due to lower transportation costs or favorable trade agreements. It may also be worthwhile to invest in research to identify innovative formulations or blends of magnesia carbon that could provide similar performance at a lower cost. Collaborating with suppliers to understand their production efficiencies can lead to cost-saving opportunities without sacrificing quality.
Scenario 3: Technical Challenges in Application and Performance
The Problem:
B2B buyers often encounter technical challenges when it comes to applying magnesia carbon in specific industrial processes. For instance, the refractory linings in furnaces may not perform as expected due to improper installation or selection of the product, leading to premature failure and increased maintenance costs. Buyers in industries like cement or glass manufacturing may find it particularly challenging to adapt magnesia carbon solutions to their unique operational needs.
The Solution:
To overcome technical hurdles, buyers should invest in training and support from suppliers that offer comprehensive technical assistance. Establishing a direct line of communication with product engineers can provide valuable insights into best practices for installation and usage. Consider conducting trials with different formulations of magnesia carbon to identify the most suitable options for your specific applications. Furthermore, implementing a feedback loop with your operational teams can help identify performance issues early on, enabling timely adjustments and minimizing costly downtime. Leveraging the expertise of suppliers can ensure that the magnesia carbon utilized aligns with operational requirements, enhancing overall performance and longevity.
Strategic Material Selection Guide for magnesia carbon
When selecting materials for magnesia carbon applications, international B2B buyers must consider various factors that influence performance, cost, and regulatory compliance. Below is an analysis of four common materials used in magnesia carbon formulations, focusing on their properties, advantages and disadvantages, and implications for specific markets, particularly in Africa, South America, the Middle East, and Europe.
What Are the Key Properties of Magnesia Carbon Materials?
-
Magnesium Oxide (MgO)
– Key Properties: Magnesium oxide is known for its high melting point (over 2800°C) and excellent thermal stability, making it suitable for high-temperature applications. It also exhibits good resistance to chemical attack, particularly from basic slags.
– Pros & Cons: The durability of MgO is a significant advantage, as it can withstand extreme conditions without degrading. However, its cost can be relatively high compared to other materials, and the manufacturing process can be complex, requiring specialized equipment.
– Impact on Application: MgO’s compatibility with basic slag makes it ideal for steelmaking and other metallurgical processes. Buyers should consider local availability and transportation costs, especially in regions like Africa where logistics can be challenging.
– Specific Considerations: Compliance with ASTM standards is crucial for buyers in Europe and the Middle East, where regulatory frameworks are stringent. In South America, buyers should be aware of local sourcing options to minimize costs. -
Carbon Black
– Key Properties: Carbon black is a reinforcing filler that enhances the mechanical properties of magnesia carbon composites. It also improves thermal conductivity and wear resistance.
– Pros & Cons: The primary advantage of carbon black is its cost-effectiveness and ability to improve product performance. However, it can be less durable than other materials and may require careful handling during manufacturing to avoid contamination.
– Impact on Application: Carbon black is particularly effective in applications requiring enhanced mechanical strength, such as in refractory linings. Buyers should assess the specific requirements of their applications to determine the optimal blend of materials.
– Specific Considerations: Buyers in Europe and the Middle East should ensure that the carbon black used meets environmental regulations regarding emissions and waste. In Africa, sourcing local suppliers can help reduce costs. -
Graphite
– Key Properties: Graphite offers excellent thermal conductivity and resistance to thermal shock, making it suitable for high-temperature applications. It also provides good lubricity, which can enhance the performance of magnesia carbon products.
– Pros & Cons: The key advantage of graphite is its ability to withstand extreme temperatures while maintaining structural integrity. However, it can be expensive, and its sourcing may be limited in certain regions, impacting availability.
– Impact on Application: Graphite is particularly beneficial in applications such as electric arc furnaces and other high-temperature environments. Buyers should consider the specific thermal and mechanical demands of their applications.
– Specific Considerations: Compliance with international standards such as JIS for buyers in Japan and DIN for those in Germany is essential. Buyers in South America should evaluate local suppliers to ensure they meet quality standards. -
Alumina
– Key Properties: Alumina is known for its high hardness and excellent wear resistance. It can enhance the overall mechanical properties of magnesia carbon composites, especially in abrasive environments.
– Pros & Cons: The primary advantage of alumina is its durability and resistance to wear, making it suitable for long-lasting applications. However, the cost of high-purity alumina can be significant, and its processing may require specialized techniques.
– Impact on Application: Alumina is particularly effective in applications where abrasion resistance is critical, such as in foundries and cement kilns. Buyers should assess the specific environmental conditions of their applications to ensure compatibility.
– Specific Considerations: In Europe, compliance with REACH regulations is crucial for buyers to ensure that materials are safe and environmentally friendly. In the Middle East, understanding local regulations can help avoid potential compliance issues.
Summary Table of Material Selection for Magnesia Carbon
Material | Typical Use Case for magnesia carbon | Key Advantage | Key Disadvantage/Limitation | Relative Cost (Low/Med/High) |
---|---|---|---|---|
Magnesium Oxide (MgO) | Steelmaking and metallurgical processes | High thermal stability and durability | High cost and complex manufacturing | High |
Carbon Black | Refractory linings requiring mechanical strength | Cost-effective and enhances performance | Less durable and handling challenges | Med |
Graphite | Electric arc furnaces and high-temperature applications | Excellent thermal conductivity | Expensive and limited sourcing | High |
Alumina | Foundries and cement kilns | High wear resistance | Significant cost for high purity | Med |
This guide provides a comprehensive overview of the strategic material selection for magnesia carbon, equipping international B2B buyers with the insights needed to make informed decisions tailored to their specific regional and application needs.
In-depth Look: Manufacturing Processes and Quality Assurance for magnesia carbon
What Are the Key Manufacturing Stages for Magnesia Carbon?
The manufacturing of magnesia carbon refractories involves several critical stages that ensure the final product meets stringent performance standards. Understanding these stages is essential for B2B buyers seeking to procure high-quality materials.
-
Material Preparation: The first step involves sourcing high-purity magnesia and carbon materials. Buyers should ensure that the raw materials meet specific chemical compositions and physical properties. This phase may also include grinding and milling to achieve the desired particle size, which can significantly influence the product’s performance.
-
Forming: After preparation, the materials undergo forming processes, which can include pressing, casting, or extruding. The method chosen often depends on the intended application and the desired density of the final product. For instance, high-density magnesia carbon bricks are typically produced through pressing techniques that apply significant pressure to ensure uniform density and strength.
-
Assembly: In some cases, especially for complex shapes or larger installations, the assembly of various components may be required. This stage necessitates precise handling to maintain material integrity and performance characteristics.
-
Finishing: The final stage involves cutting, grinding, and treating the products to meet specific dimensional and surface finish requirements. Buyers should inquire about the finishing techniques used, as they can impact the material’s thermal and mechanical properties.
Which Key Techniques Are Used in Magnesia Carbon Manufacturing?
Various advanced techniques are employed throughout the manufacturing process to enhance the properties of magnesia carbon products.
-
Sintering: This technique involves heating the formed materials to a temperature below their melting point, allowing particles to bond and strengthen. This is crucial for achieving the desired durability and thermal resistance.
-
Chemical Bonding: Some manufacturers may introduce chemical additives that react during the curing process, enhancing the bonding between magnesia and carbon. This can lead to improved performance in high-temperature applications.
-
Coating: Applying protective coatings can enhance the performance of magnesia carbon products by providing additional resistance to wear and corrosion.
How Do Quality Assurance Protocols Impact Magnesia Carbon Products?
Quality assurance is vital in ensuring that magnesia carbon products meet international standards and customer expectations. For B2B buyers, understanding these protocols can aid in selecting reliable suppliers.
What International Standards Are Relevant for Magnesia Carbon?
International standards such as ISO 9001 play a crucial role in manufacturing quality assurance. ISO 9001 outlines requirements for a quality management system, ensuring that manufacturers consistently provide products that meet customer and regulatory requirements. Additionally, industry-specific certifications like CE marking and API standards may apply, depending on the end-use applications.
What Are the Key Quality Control Checkpoints in Manufacturing?
Quality control (QC) is typically divided into several checkpoints during the manufacturing process:
-
Incoming Quality Control (IQC): This initial checkpoint involves inspecting raw materials upon arrival. Buyers should verify that suppliers conduct thorough IQC to prevent defects from entering the production line.
-
In-Process Quality Control (IPQC): Throughout the manufacturing process, regular inspections and tests are performed to monitor compliance with specifications. This includes checking dimensions, material consistency, and process parameters.
-
Final Quality Control (FQC): Before products are shipped, FQC ensures that they meet all specified requirements. This may involve mechanical testing, thermal stability tests, and dimensional checks.
What Common Testing Methods Are Used for Magnesia Carbon Products?
Several testing methods are widely utilized to assess the quality of magnesia carbon products:
-
Chemical Analysis: To ensure the correct composition, spectroscopic techniques or X-ray fluorescence (XRF) may be employed.
-
Thermal Conductivity Testing: This assesses how well the material can withstand high temperatures, critical for applications in steelmaking and other industries.
-
Mechanical Testing: Includes compressive strength tests, which determine how much load the material can bear without failure.
How Can B2B Buyers Verify Supplier Quality Control?
When sourcing magnesia carbon products, B2B buyers must ensure that their suppliers adhere to rigorous quality control standards. Here are actionable steps to verify supplier QC:
-
Conduct Supplier Audits: Regular audits can provide insights into a supplier’s manufacturing processes and quality control measures. Buyers should request to participate in or review audit reports.
-
Request QC Reports: Suppliers should be willing to provide documentation detailing their QC processes, results from tests, and compliance with relevant standards.
-
Engage Third-Party Inspectors: Hiring independent inspection agencies can add an extra layer of assurance. These inspectors can perform random checks and ensure that the products meet agreed specifications.
What Are the Quality Control and Certification Nuances for International B2B Buyers?
For international buyers, particularly from Africa, South America, the Middle East, and Europe, navigating the nuances of quality control and certification is critical.
-
Understanding Regional Standards: Different regions may have specific certifications that are mandatory for import. For instance, European buyers should be aware of REACH compliance for chemical safety.
-
Language Barriers: Ensure that all documentation, including QC reports and certifications, are available in a language that the buyer understands to avoid misinterpretations.
-
Cultural Differences in Business Practices: Familiarize yourself with the business practices in the supplier’s country. Some cultures may prioritize relationships over formal agreements, impacting how quality assurance is approached.
By thoroughly understanding the manufacturing processes and quality assurance protocols for magnesia carbon, B2B buyers can make informed decisions that ensure they receive high-quality products that meet their specific needs.
Practical Sourcing Guide: A Step-by-Step Checklist for ‘magnesia carbon’
In the competitive landscape of international trade, sourcing magnesia carbon requires a structured approach to ensure quality, compliance, and cost-effectiveness. This checklist serves as a practical guide for B2B buyers, especially those operating in Africa, South America, the Middle East, and Europe, to streamline their procurement process.
Step 1: Define Your Technical Specifications
Clearly outlining your technical requirements is critical. Magnesia carbon products vary in composition and performance characteristics, which can significantly affect their suitability for your application. Consider factors such as purity levels, particle size, and thermal stability.
- Purity Levels: Ensure the magnesia carbon meets industry standards for your specific use case.
- Performance Characteristics: Understand the thermal and mechanical properties necessary for your operational needs.
Step 2: Identify Reliable Suppliers
Research potential suppliers in regions known for high-quality magnesia carbon production. Focus on those with a proven track record and positive reviews in your sector.
- Supplier Location: Consider the logistical implications of sourcing from various regions, including shipping costs and delivery times.
- Industry Experience: Look for suppliers with experience in supplying your specific industry, as they will better understand your needs.
Step 3: ✅ Verify Supplier Certifications
Ensure that potential suppliers have the necessary certifications to guarantee quality and compliance with international standards. Certifications such as ISO 9001 or industry-specific standards indicate a commitment to quality management.
- Documentation: Request copies of certifications and check their validity.
- Regulatory Compliance: Verify that suppliers comply with local regulations in your region and the supplier’s country.
Step 4: Request Samples for Testing
Before making a bulk purchase, request samples to evaluate the material’s performance. This step is essential to ensure that the magnesia carbon meets your specifications.
- Testing Methods: Conduct tests that reflect your application needs, including thermal conductivity and chemical resistance.
- Feedback Loop: Involve your technical team in the testing phase to gather insights and validate performance.
Step 5: Negotiate Pricing and Terms
Once you have identified a suitable supplier, engage in negotiations to finalize pricing and terms. Understanding the market price for magnesia carbon in your region can give you leverage in negotiations.
- Bulk Discounts: Inquire about discounts for larger orders, which can significantly reduce your overall costs.
- Payment Terms: Clarify payment terms to ensure they align with your financial capabilities and cash flow management.
Step 6: Establish a Clear Communication Channel
Effective communication is key to a successful sourcing relationship. Establish clear lines of communication with your supplier to facilitate timely updates and address potential issues.
- Regular Check-ins: Schedule periodic meetings to discuss order progress and resolve any concerns.
- Point of Contact: Designate a specific individual from both sides to streamline communication and decision-making.
Step 7: Monitor Supplier Performance
After establishing a partnership, continuously monitor your supplier’s performance to ensure they consistently meet your expectations. This step helps in maintaining quality and reliability in your supply chain.
- Performance Metrics: Define key performance indicators (KPIs) relevant to your sourcing needs.
- Feedback Mechanism: Create a system for providing feedback to your supplier, fostering a collaborative relationship that encourages improvement.
By following this checklist, international B2B buyers can navigate the complexities of sourcing magnesia carbon more effectively, ensuring they secure the best products for their needs while fostering strong supplier relationships.
Comprehensive Cost and Pricing Analysis for magnesia carbon Sourcing
Understanding the cost structure associated with sourcing magnesia carbon is crucial for international B2B buyers, particularly those operating in regions like Africa, South America, the Middle East, and Europe. This analysis will delve into the various cost components, pricing influencers, and practical tips for negotiating the best deals.
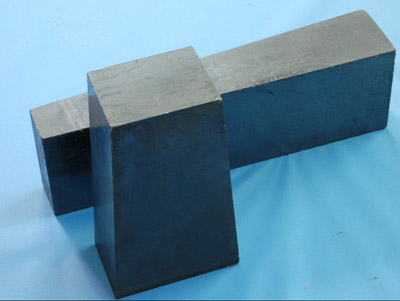
A stock image related to magnesia carbon.
What Are the Key Cost Components in Magnesia Carbon Sourcing?
When evaluating the total cost of sourcing magnesia carbon, several core components must be considered:
-
Materials: The primary raw materials for magnesia carbon include high-purity magnesia and carbonaceous materials. Fluctuations in the prices of these inputs can significantly affect overall costs. Buyers should closely monitor commodity market trends to anticipate price changes.
-
Labor: Labor costs can vary based on geographic location and local wage standards. For instance, sourcing from regions with lower labor costs may seem attractive, but it’s essential to assess the skills and expertise of the workforce involved in production.
-
Manufacturing Overhead: This includes indirect costs associated with production, such as utilities, maintenance, and facility costs. Efficient manufacturing processes can help reduce these overheads, impacting the final price.
-
Tooling: Customization often requires specific tooling, which can be a substantial upfront investment. Buyers should consider whether the tooling costs can be amortized over large production runs to improve overall cost efficiency.
-
Quality Control (QC): Ensuring high-quality standards in magnesia carbon products is vital, especially for industries like steelmaking where performance is critical. Investing in rigorous QC processes can add to initial costs but may prevent costly failures down the line.
-
Logistics: Transportation and handling costs are significant, especially for international shipments. Factors such as distance, shipping mode, and customs duties must be carefully evaluated.
-
Margin: Suppliers will include a margin to cover their risks and profit motives. Understanding typical margins in the industry can aid buyers in negotiating better terms.
How Do Pricing Influencers Affect Magnesia Carbon Costs?
Several factors influence the pricing of magnesia carbon, which can vary significantly across different markets:
-
Volume and Minimum Order Quantity (MOQ): Larger orders often qualify for bulk discounts. Buyers should assess their demand patterns to negotiate favorable pricing based on volume.
-
Specifications and Customization: Customized products typically come at a premium. Buyers should clearly define their specifications to avoid unnecessary costs associated with reworks or adjustments.
-
Materials and Quality Certifications: The quality of materials used directly affects the product’s performance. Buyers should seek suppliers that provide certifications, ensuring that the materials meet industry standards, which can also influence pricing.
-
Supplier Factors: The supplier’s reputation, reliability, and experience can impact pricing. Established suppliers may charge more due to their proven track record, while newer entrants might offer competitive rates to gain market share.
-
Incoterms: The choice of Incoterms can significantly affect total costs. Understanding who bears the responsibility for shipping, insurance, and tariffs is crucial for budgeting.
What Are the Best Buyer Tips for Cost-Efficient Sourcing of Magnesia Carbon?
International B2B buyers should consider the following strategies to enhance cost efficiency when sourcing magnesia carbon:
-
Negotiate Effectively: Leverage your purchasing power by negotiating based on volume and long-term partnership potential. Suppliers may be more inclined to offer discounts to buyers committed to larger, ongoing orders.
-
Evaluate Total Cost of Ownership (TCO): Instead of focusing solely on the purchase price, consider the TCO, which includes maintenance, logistics, and potential downtime costs. This broader perspective can lead to more informed decision-making.
-
Understand Pricing Nuances for Your Region: Buyers from Africa, South America, the Middle East, and Europe should be aware of regional market dynamics and currency fluctuations that can affect pricing. Local economic conditions can also influence supplier pricing strategies.
-
Stay Updated on Market Trends: Continuous monitoring of raw material prices and market developments will enable buyers to make timely purchasing decisions, potentially capitalizing on lower prices.
Conclusion
Sourcing magnesia carbon involves navigating a complex landscape of costs and pricing factors. By understanding these elements and employing strategic negotiation techniques, international B2B buyers can optimize their sourcing processes and achieve better financial outcomes.
Alternatives Analysis: Comparing magnesia carbon With Other Solutions
Understanding the Importance of Alternative Solutions in B2B Procurement
When evaluating materials for high-temperature applications, international B2B buyers often encounter a variety of options. Magnesia carbon (MgO-C) is renowned for its thermal stability and excellent resistance to chemical attack, particularly in steelmaking processes. However, understanding alternatives is critical for making an informed decision that aligns with specific business needs, budget constraints, and operational efficiencies. This section compares magnesia carbon with two viable alternatives: alumina-silica refractories and silicon carbide (SiC) bricks.
Comparison Table
Comparison Aspect | Magnesia Carbon | Alumina-Silica Refractories | Silicon Carbide Bricks |
---|---|---|---|
Performance | High thermal shock resistance, excellent erosion resistance | Good thermal stability, but lower than MgO-C | Superior thermal conductivity, high wear resistance |
Cost | Moderate to high | Generally lower cost | Higher initial investment |
Ease of Implementation | Relatively easy to install with standard practices | Requires specialized installation techniques | Can be complex due to brittleness |
Maintenance | Low maintenance needs, but requires monitoring | Moderate maintenance due to wear over time | Low maintenance, but brittle |
Best Use Case | Steelmaking, ladles, and converters | General industrial applications, kilns | High-performance applications, such as furnaces |
Pros and Cons of Each Alternative
Alumina-Silica Refractories: What Are Their Advantages and Disadvantages?
Alumina-silica refractories are a popular choice for industries requiring good thermal stability at a lower cost. They are particularly effective for general industrial applications, such as kilns and furnaces. However, while they provide decent thermal insulation and resistance to wear, their performance under extreme thermal shock is inferior to that of magnesia carbon. Additionally, they may require more frequent maintenance due to wear and tear, which could lead to increased operational costs over time.
Silicon Carbide Bricks: How Do They Stack Up Against Magnesia Carbon?
Silicon carbide bricks are known for their superior thermal conductivity and high wear resistance, making them ideal for high-performance applications such as furnaces. However, their brittleness can pose challenges during installation and handling, potentially leading to higher installation costs and risk of breakage. The initial investment is often higher than that of magnesia carbon, but their longevity and performance in extreme conditions can justify the cost for certain applications.
Conclusion: How Should B2B Buyers Choose the Right Solution?
Selecting the right refractory material is a critical decision for B2B buyers, particularly in industries such as steelmaking and heavy manufacturing. When comparing magnesia carbon with alternatives like alumina-silica refractories and silicon carbide bricks, buyers should consider performance needs, budget constraints, and operational requirements. For instance, if high thermal shock resistance is paramount, magnesia carbon may be the best choice. Conversely, for applications with budget limitations where moderate performance is acceptable, alumina-silica refractories could be suitable. Ultimately, the decision should align with the specific use case, potential maintenance costs, and the overall operational strategy of the business.
Essential Technical Properties and Trade Terminology for magnesia carbon
What Are the Key Technical Properties of Magnesia Carbon?
When engaging in international B2B transactions for magnesia carbon, understanding its technical properties is crucial for ensuring that the material meets specific operational needs. Here are some of the essential specifications to consider:
1. Material Grade
The grade of magnesia carbon refers to the purity and composition of the product. Higher grades typically contain a greater percentage of magnesium oxide (MgO) and carbon, which enhances performance in high-temperature applications. For buyers, selecting the appropriate grade is essential for applications in steelmaking, refractory linings, and other industrial uses, as it directly impacts durability and efficiency.
2. Thermal Conductivity
Thermal conductivity measures how well heat is transmitted through the material. For magnesia carbon, optimal thermal conductivity is vital, especially in furnace linings where heat resistance is critical. Buyers should assess thermal conductivity to ensure that the material will withstand the operational temperatures of their specific applications, thereby preventing premature failure and enhancing overall efficiency.
3. Density
Density affects the mechanical strength and thermal stability of magnesia carbon. A higher density typically indicates better performance under stress and improved resistance to thermal shock. When sourcing, buyers should consider the density specifications to ensure that the material can support the demands of their operational environments without compromising structural integrity.
4. Compressive Strength
Compressive strength is a critical property that measures the material’s ability to withstand axial loads without failure. This is particularly important in industrial applications where magnesia carbon is subjected to significant pressure. Buyers should evaluate compressive strength specifications to ensure that the material will perform effectively in their specific applications, thereby reducing the risk of operational disruptions.
5. Chemical Resistance
Chemical resistance refers to the material’s ability to withstand corrosive environments, which is essential in applications involving molten metals and slag. Understanding the chemical resistance of magnesia carbon helps buyers anticipate the longevity and maintenance needs of their products, making it easier to calculate total cost of ownership over time.
What Are Common Trade Terms Used in Magnesia Carbon Transactions?
Navigating the trade landscape for magnesia carbon involves familiarizing oneself with key industry terms that can impact negotiations and purchasing decisions. Below are some important terms to know:
1. OEM (Original Equipment Manufacturer)
OEM refers to companies that produce parts or equipment that may be marketed by another manufacturer. In the context of magnesia carbon, knowing if your supplier is an OEM can help determine the quality and reliability of the product. OEMs often maintain stringent quality controls, making them a preferred choice for many buyers.
2. MOQ (Minimum Order Quantity)
MOQ is the minimum quantity of a product that a supplier is willing to sell. Understanding MOQ is critical for budgeting and inventory management, especially for international buyers who may face shipping constraints or higher costs. It’s advisable to negotiate MOQ to align with your purchasing capabilities and operational needs.
3. RFQ (Request for Quotation)
An RFQ is a formal process where buyers request pricing information from suppliers. This document should detail specifications, quantities, and delivery timelines. Crafting a thorough RFQ can lead to better pricing and terms, ensuring that buyers receive competitive offers from multiple suppliers.
4. Incoterms (International Commercial Terms)
Incoterms define the responsibilities of buyers and sellers in international trade, including shipping, insurance, and tariffs. Familiarity with these terms helps buyers understand their obligations and rights throughout the transaction process, mitigating risks related to shipping delays or additional costs.
5. Lead Time
Lead time is the time it takes from placing an order to receiving the product. Understanding lead times is essential for planning and inventory management. Buyers should inquire about lead times to ensure that they can meet their production schedules without delays, especially when sourcing from international suppliers.
By comprehensively understanding these technical properties and trade terms, international B2B buyers can make informed decisions that enhance their procurement strategies and operational efficiency.
Navigating Market Dynamics and Sourcing Trends in the magnesia carbon Sector
What Are the Key Market Trends in the Magnesia Carbon Sector?
The magnesia carbon sector is witnessing significant transformation driven by various global factors. As industries increasingly focus on high-performance materials, the demand for magnesia carbon refractories is growing, particularly in steelmaking and non-ferrous metallurgy. The rise of emerging markets in Africa and South America is contributing to this surge, as these regions expand their industrial capabilities. Moreover, technological advancements in production methods, including the use of advanced manufacturing techniques and automation, are enhancing efficiency and reducing costs, which is appealing to international B2B buyers.
Another notable trend is the shift towards digital sourcing platforms. These platforms enable buyers to streamline procurement processes, compare suppliers, and access a broader range of products. For buyers in regions like Kenya or Germany, embracing these technologies can facilitate smarter purchasing decisions, ensuring competitive pricing and better quality assurance.
In addition, the ongoing volatility in raw material prices is prompting companies to adopt more strategic sourcing approaches. Buyers are increasingly looking for suppliers who can offer flexible pricing models or long-term contracts to mitigate risks associated with price fluctuations. Understanding these market dynamics is crucial for international buyers to navigate the complexities of sourcing magnesia carbon products effectively.
How Can Sustainability and Ethical Sourcing Impact Your Procurement Strategy?
Sustainability and ethical sourcing are becoming paramount in the procurement of magnesia carbon materials. The environmental impact of mining and processing magnesia carbon can be significant, leading to growing scrutiny from regulators and consumers alike. For B2B buyers, particularly in Europe, aligning with suppliers who prioritize sustainable practices is not just a moral obligation but a competitive advantage.
Buyers should seek suppliers with certifications such as ISO 14001, which indicates a commitment to environmental management systems. Additionally, sourcing from suppliers that utilize recycled materials or have a clear sustainability strategy can enhance a company’s brand reputation and appeal to environmentally conscious clients.
Moreover, understanding the supply chain’s ethical implications is essential. Buyers must ensure that their suppliers adhere to fair labor practices and responsible mining operations. This not only safeguards against potential reputational risks but also supports the development of ethical supply chains. By prioritizing sustainability and ethical sourcing, international B2B buyers can contribute positively to the industry while optimizing their procurement strategies.
What Is the Historical Context of the Magnesia Carbon Sector?
The magnesia carbon sector has evolved significantly over the past century, transitioning from traditional refractory materials to advanced composites that meet the demands of modern industries. Initially, magnesia carbon refractories were primarily utilized in steelmaking processes due to their excellent thermal resistance and structural integrity. Over the decades, innovations in material science have led to the development of improved formulations that enhance performance and durability.
In recent years, the sector has faced challenges such as fluctuating raw material availability and increasing environmental regulations. These factors have spurred further innovation and diversification, leading to a broader range of applications for magnesia carbon materials, including in the production of non-ferrous metals and in the cement industry. Understanding this historical context is vital for international buyers, as it sheds light on the ongoing advancements and potential future trends in the magnesia carbon market.
Frequently Asked Questions (FAQs) for B2B Buyers of magnesia carbon
-
How do I solve sourcing challenges for magnesia carbon?
Sourcing magnesia carbon can be complex due to varying quality standards and supplier reliability. To overcome these challenges, start by conducting thorough market research to identify reputable suppliers in your region or globally. Utilize platforms like Alibaba or industry-specific directories to find verified vendors. Consider requesting samples to assess quality before placing larger orders. Establishing direct communication with suppliers can also help clarify specifications, production capabilities, and lead times, ensuring a smoother procurement process. -
What is the best grade of magnesia carbon for high-temperature applications?
For high-temperature applications, particularly in steelmaking and refractory industries, the best grade of magnesia carbon is typically one that contains a higher percentage of magnesia (MgO) combined with carbon. Look for grades with at least 70% MgO content, which enhance thermal stability and resistance to oxidation. When selecting a grade, also consider the specific application requirements, such as thermal shock resistance and slag resistance, to ensure optimal performance. -
How can I ensure the quality of magnesia carbon before purchasing?
To ensure quality, request certificates of analysis (CoA) from suppliers, detailing the chemical composition and physical properties of the magnesia carbon. Additionally, consider third-party testing to verify these claims. Establishing a quality assurance protocol that includes regular inspections and testing of batches can also help maintain standards. Building long-term relationships with trusted suppliers who have a proven track record can further enhance quality assurance in your sourcing strategy. -
What are the typical minimum order quantities (MOQ) for magnesia carbon?
Minimum order quantities for magnesia carbon can vary significantly among suppliers, typically ranging from 1 ton to several tons. Factors influencing MOQ include supplier production capacity, the grade of material, and shipping considerations. When negotiating, clarify your needs and see if suppliers are willing to accommodate smaller orders, especially if you are testing a new product line. Bulk orders may yield better pricing, so consider your long-term needs when determining order sizes. -
What payment terms should I expect when sourcing magnesia carbon internationally?
Payment terms can vary widely, but common practices include upfront payment, partial payment upon order confirmation, and balance upon delivery. For international transactions, using secure payment methods like letters of credit or escrow services can mitigate risks. Always negotiate terms that provide security for both parties, and ensure that payment terms are clearly documented in the contract to avoid misunderstandings. -
How can I vet suppliers of magnesia carbon effectively?
Effective supplier vetting involves several steps: first, verify their business credentials and certifications to ensure compliance with international standards. Conduct background checks and seek references from other clients. Additionally, consider visiting the supplier’s manufacturing facilities if feasible. Online reviews and ratings can provide insights into their reliability. Establishing clear communication and asking detailed questions about their production processes can further gauge their professionalism and capability. -
What logistics considerations should I be aware of when importing magnesia carbon?
Logistics for importing magnesia carbon require careful planning. Key considerations include shipping methods, customs clearance, and potential tariffs. Understand the regulations in your country regarding importing raw materials. Partnering with a freight forwarder experienced in handling industrial materials can streamline the process, ensuring timely delivery. Additionally, factor in lead times and storage capabilities upon arrival to optimize your supply chain.
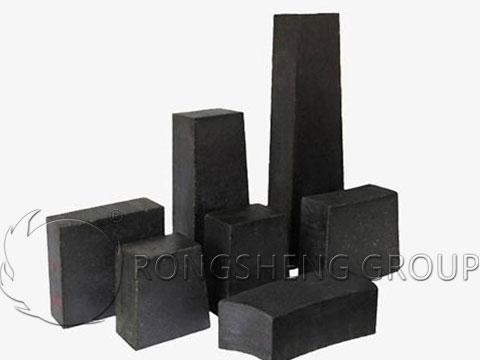
A stock image related to magnesia carbon.
- Can magnesia carbon be customized for specific applications?
Yes, many suppliers offer customization options for magnesia carbon to meet specific application needs. This can include adjustments to the chemical composition, particle size, and packaging. When discussing customization, provide detailed specifications of your requirements and any performance benchmarks you aim to achieve. Collaborating closely with your supplier during the development phase can help create a product tailored to your operational needs, enhancing performance and efficiency.
Important Disclaimer & Terms of Use
⚠️ Important Disclaimer
The information provided in this guide, including content regarding manufacturers, technical specifications, and market analysis, is for informational and educational purposes only. It does not constitute professional procurement advice, financial advice, or legal advice.
While we have made every effort to ensure the accuracy and timeliness of the information, we are not responsible for any errors, omissions, or outdated information. Market conditions, company details, and technical standards are subject to change.
B2B buyers must conduct their own independent and thorough due diligence before making any purchasing decisions. This includes contacting suppliers directly, verifying certifications, requesting samples, and seeking professional consultation. The risk of relying on any information in this guide is borne solely by the reader.
Strategic Sourcing Conclusion and Outlook for magnesia carbon
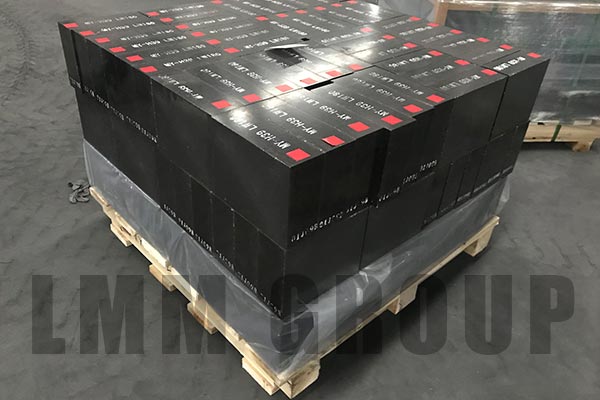
A stock image related to magnesia carbon.
In navigating the complexities of sourcing magnesia carbon, international B2B buyers must prioritize strategic partnerships and a thorough understanding of the supply chain dynamics. The value of strategic sourcing lies in its ability to mitigate risks, optimize costs, and ensure consistent quality of materials crucial for high-performance applications. Buyers from regions such as Africa, South America, the Middle East, and Europe should leverage local suppliers’ expertise while also considering global trends and innovations in the magnesia carbon market.
What are the future trends in magnesia carbon sourcing? As industries evolve, the demand for eco-friendly and efficient materials will drive innovation in sourcing strategies. Embracing sustainable practices and collaborating with suppliers who prioritize environmental responsibility will not only enhance your brand reputation but also align with global sustainability goals.
As you move forward, consider investing in long-term relationships with reliable suppliers who can adapt to changing market conditions and customer needs. By doing so, you position your business to thrive in a competitive landscape. Engage proactively with your suppliers, stay informed about market developments, and continuously evaluate your sourcing strategies to ensure your operations remain resilient and responsive to the demands of the future.