Unlock Quality: The Ultimate Silicon Mold Sourcing Guide (2025)
Introduction: Navigating the Global Market for silicon mold
Navigating the complexities of sourcing high-quality silicon molds can present significant challenges for international B2B buyers, especially in regions like Africa, South America, the Middle East, and Europe. With a growing demand for customized solutions across various industries—from automotive to electronics—understanding the nuances of the silicon mold market is crucial. This guide aims to demystify the procurement process by offering insights into different types of silicon molds, their diverse applications, and effective supplier vetting strategies.
In this comprehensive resource, you will find actionable insights on evaluating costs, identifying reputable suppliers, and optimizing your supply chain for silicon mold production. Whether you are a manufacturer in Colombia looking to enhance your product line or a distributor in the Middle East seeking reliable partners, this guide equips you with the knowledge to make informed purchasing decisions.
By addressing common concerns such as quality assurance, compliance with international standards, and logistical challenges, we empower you to navigate the global market confidently. Additionally, you will learn about emerging trends and technologies that are shaping the future of silicon mold production, enabling you to stay ahead of the competition. With this guide, you will not only enhance your procurement strategy but also foster long-term partnerships that drive business growth in your region.
Understanding silicon mold Types and Variations
Type Name | Key Distinguishing Features | Primary B2B Applications | Brief Pros & Cons for Buyers |
---|---|---|---|
Condensation Silicone | Cures at room temperature, excellent detail reproduction | Prototyping, jewelry, and art casting | Pros: High detail; Cons: Lower heat resistance. |
Addition Silicone | Cures through a chemical reaction, stable and flexible | Medical devices, automotive parts | Pros: Strong dimensional stability; Cons: Higher cost. |
Liquid Silicone Rubber | High elasticity and heat resistance, suitable for complex shapes | Food industry, electronics | Pros: Biocompatible; Cons: Requires specialized equipment. |
Platinum-Cured Silicone | Cured with platinum, offering superior performance and longevity | Aerospace, automotive, and medical | Pros: Durable and non-toxic; Cons: Expensive. |
Two-Part Silicone | Requires mixing two components before use, versatile in applications | Mold making, casting, and prototyping | Pros: Customizable; Cons: More complex application process. |
What are the characteristics of Condensation Silicone Molds?
Condensation silicone molds are known for their ability to cure at room temperature, which makes them particularly user-friendly for various applications. They excel in capturing fine details, making them ideal for prototyping, jewelry making, and artistic casting. For B2B buyers, the key consideration is the mold’s heat resistance; while they are excellent for most applications, they may not withstand high-temperature environments. This type is suitable for businesses focused on detailed work without the need for thermal stability.
How does Addition Silicone differ in its applications?
Addition silicone molds are created through a chemical reaction, which provides a stable and flexible final product. This type is commonly used in the manufacturing of medical devices and automotive parts due to its strong dimensional stability. B2B buyers should consider the cost, as addition silicone tends to be pricier than other options. However, its reliability in critical applications often justifies the investment, particularly for industries where precision is paramount.
Why choose Liquid Silicone Rubber for your business needs?
Liquid silicone rubber (LSR) stands out for its high elasticity and exceptional heat resistance, making it suitable for complex shapes and intricate designs. It finds widespread use in the food industry and electronics due to its biocompatibility and durability. When purchasing LSR, businesses must be aware that it often requires specialized equipment for processing, which can increase upfront costs. However, its long-term benefits in terms of performance and safety can outweigh these initial expenses.
What are the advantages of using Platinum-Cured Silicone?
Platinum-cured silicone molds are renowned for their superior performance and longevity. This type is ideal for industries such as aerospace, automotive, and medical, where durability and non-toxicity are critical. B2B buyers should be prepared for a higher price point, but the benefits of using platinum-cured silicone, including its resistance to extreme temperatures and chemicals, often make it a worthwhile investment for high-stakes applications.
How does Two-Part Silicone benefit manufacturing processes?
Two-part silicone molds require the mixing of two components before use, which allows for great versatility in applications ranging from mold making to prototyping. This type is particularly appealing for businesses that need customized solutions tailored to specific project requirements. However, the complexity of the application process can be a consideration for B2B buyers. Despite this, the ability to fine-tune the properties of the silicone can lead to enhanced product outcomes, making it a valuable option for innovative manufacturers.
Related Video: Silicone Mold Making – Three Different Ways
Key Industrial Applications of silicon mold
Industry/Sector | Specific Application of Silicon Mold | Value/Benefit for the Business | Key Sourcing Considerations for this Application |
---|---|---|---|
Automotive Manufacturing | Production of custom rubber gaskets and seals | Enhanced durability and precision in vehicle components | Ensure high-temperature resistance and compliance with automotive standards |
Electronics | Encapsulation of electronic components | Improved protection against moisture and contaminants | Look for molds that meet specific electrical safety standards and thermal properties |
Medical Devices | Creation of silicone parts for medical devices | Biocompatibility and safety for patient use | Verify certification for medical-grade materials and manufacturing processes |
Construction Materials | Molding of architectural elements and fixtures | Customization and aesthetic appeal in building design | Source molds that allow for detailed finishes and are compatible with various casting materials |
Food and Beverage Packaging | Production of silicone molds for food containers | Non-toxic, reusable options that reduce waste | Ensure compliance with food safety regulations and ease of cleaning |
How is Silicon Mold Used in Automotive Manufacturing?
In the automotive industry, silicon molds are crucial for producing custom rubber gaskets and seals, which are integral to vehicle assembly. These molds facilitate the creation of components that are not only durable but also designed to fit precisely, reducing the risk of leaks and enhancing vehicle performance. B2B buyers in this sector must prioritize sourcing high-temperature resistant molds that comply with stringent automotive industry standards, ensuring longevity and reliability in their applications.
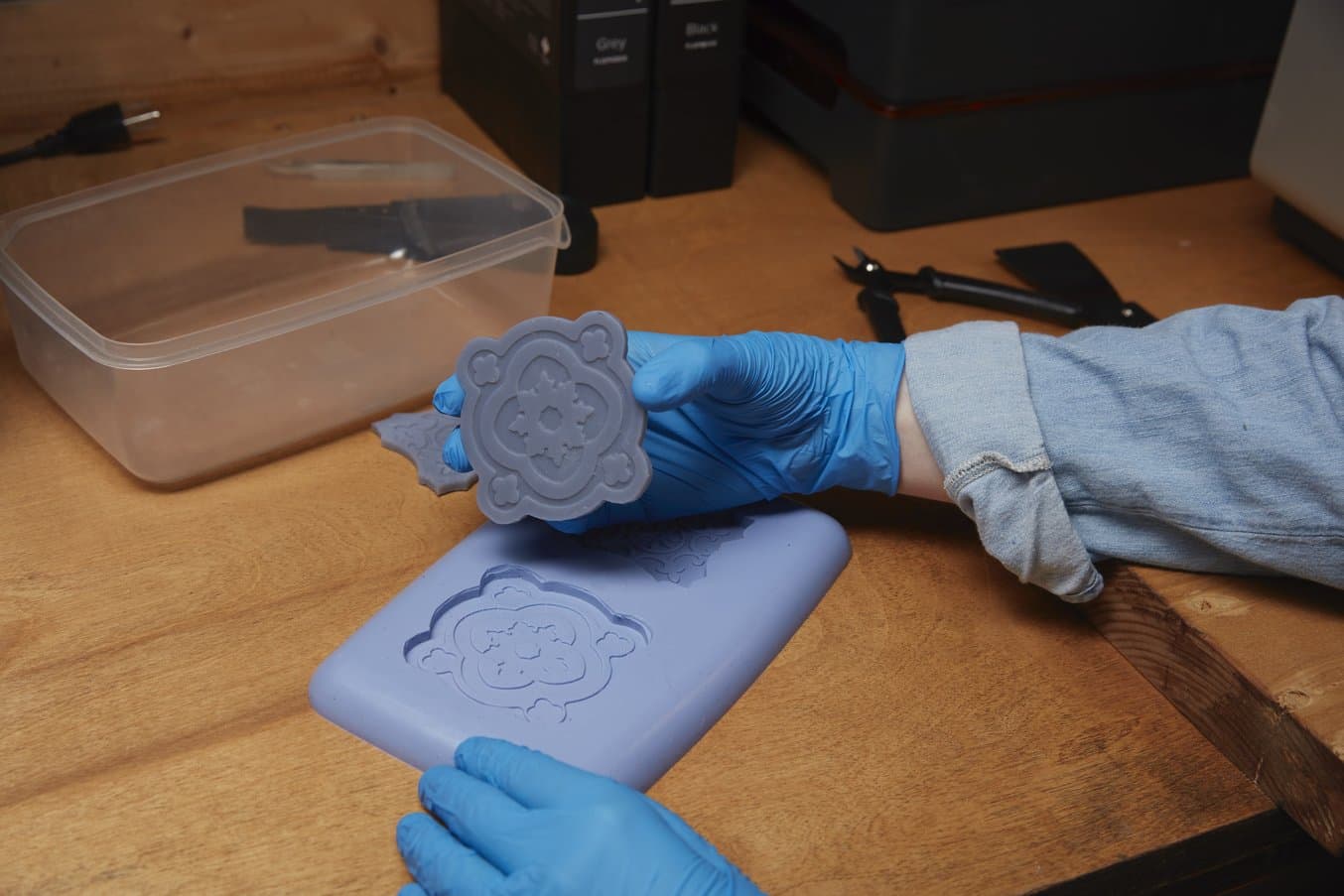
A stock image related to silicon mold.
What Role Does Silicon Mold Play in Electronics?
Silicon molds are employed extensively in the electronics sector for encapsulating components, safeguarding them from moisture and contaminants. This application is vital for maintaining the integrity and performance of electronic devices. Buyers should look for molds that adhere to specific electrical safety standards and possess excellent thermal properties to ensure optimal performance under varying conditions. The right silicon mold can significantly extend the lifespan of electronic products, making it a worthwhile investment.
Why are Silicon Molds Essential for Medical Devices?
In the medical device industry, silicon molds are used to create various silicone parts that must meet high standards of biocompatibility and safety. These molds are essential for producing items such as syringes, catheters, and other patient-contact devices. For international B2B buyers, it is critical to verify that the molds are made from certified medical-grade materials and that the manufacturing processes adhere to regulatory requirements. This ensures that the final products are safe for patient use and compliant with health regulations.
How are Silicon Molds Utilized in Construction Materials?
Silicon molds play a significant role in the construction industry by enabling the molding of architectural elements and fixtures. These molds allow for a high degree of customization, providing architects and builders with the flexibility to design unique and aesthetically appealing structures. Buyers should seek molds that can produce detailed finishes and are compatible with various casting materials, ensuring that the final product meets both functional and design specifications.
What are the Benefits of Using Silicon Molds in Food and Beverage Packaging?
In the food and beverage packaging sector, silicon molds are increasingly used to produce food containers that are non-toxic and reusable. This application not only supports sustainability efforts by reducing waste but also ensures that packaging materials are safe for food contact. B2B buyers must ensure that the molds comply with food safety regulations and are easy to clean, as these factors significantly impact the overall efficiency and safety of food production processes.
3 Common User Pain Points for ‘silicon mold’ & Their Solutions
Scenario 1: Challenges with Consistent Quality in Silicone Mold Production
The Problem:
B2B buyers often face issues with inconsistent quality in silicone mold production, leading to significant delays and increased costs. For instance, a manufacturer in Colombia may source molds from various suppliers, only to discover that the durability and precision of the molds differ markedly. This inconsistency can result in defective products, increased waste, and ultimately, dissatisfied customers. Moreover, poor quality can undermine the reputation of the business, making it difficult to secure future contracts.
The Solution:
To address quality inconsistencies, it is crucial for buyers to conduct thorough supplier evaluations before making a purchase. Start by asking for samples and conducting tests to assess the material properties and manufacturing techniques used. Look for suppliers that have certifications such as ISO 9001, which indicates adherence to quality management standards. Additionally, establishing a clear communication channel with suppliers can facilitate better understanding of quality expectations and production capabilities. Consider entering into long-term contracts with reliable suppliers to ensure consistent quality over time.
Scenario 2: High Costs Associated with Custom Silicone Molds
The Problem:
International buyers, particularly those in regions like the Middle East and Africa, often encounter high costs when ordering custom silicone molds. This can be particularly challenging for small to medium-sized enterprises (SMEs) that have limited budgets but require specialized molds for niche applications. The initial investment for design and production can be prohibitively expensive, leading some businesses to compromise on quality or functionality to save costs.
The Solution:
To mitigate high costs, buyers should explore bulk ordering options or long-term partnerships with silicone mold manufacturers. By committing to larger orders, companies can often negotiate better pricing. Additionally, leveraging technology such as 3D printing for prototype development can minimize initial design costs, allowing businesses to test and refine their molds before full-scale production. It’s also beneficial to engage in collaborative design processes with suppliers to streamline production and reduce costs. By sharing design specifications early, both parties can identify potential cost-saving measures without sacrificing quality.
Scenario 3: Difficulty in Sourcing Silicone Molds with Specific Features
The Problem:
B2B buyers frequently struggle to find silicone molds that meet specific design requirements or unique application needs. For example, a company in South America might need molds that can withstand extreme temperatures or are compatible with particular casting materials. The lack of readily available options can lead to project delays and increased frustration among procurement teams, especially when trying to innovate or meet customer demands.
The Solution:
To effectively source specialized silicone molds, buyers should consider reaching out to manufacturers that offer custom mold solutions. Utilize online platforms and industry directories to identify suppliers that specialize in custom designs. Engaging in discussions with potential suppliers about specific requirements can uncover hidden capabilities and options that may not be advertised. Additionally, networking within industry forums and trade shows can provide valuable insights and connections to suppliers who can deliver tailored solutions. Building a collaborative relationship with a trusted supplier can also lead to more flexible options in mold design and material selection, enabling businesses to innovate more freely.
Strategic Material Selection Guide for silicon mold
When selecting materials for silicon molds, understanding the properties, advantages, and limitations of various materials is essential for optimizing performance and cost-effectiveness. Below, we analyze four common materials used in silicon mold manufacturing, providing actionable insights for international B2B buyers.
What are the Key Properties of Silicone Rubber for Molds?
Silicone Rubber is the most widely used material for silicon molds due to its excellent flexibility and thermal stability. It can withstand temperatures ranging from -60°C to 200°C, making it suitable for various applications. Silicone rubber exhibits good resistance to UV light, ozone, and moisture, which enhances its durability in outdoor applications.
Pros & Cons: The primary advantage of silicone rubber is its ability to produce intricate designs and fine details due to its excellent flow characteristics. However, it can be relatively expensive compared to other materials, which may impact budget-sensitive projects. Additionally, while it is durable, silicone rubber may not be suitable for high-pressure applications.
Impact on Application: Silicone rubber is compatible with a wide range of media, including food-grade applications, making it a preferred choice in industries such as food processing and pharmaceuticals.
Considerations for International Buyers: Buyers should ensure compliance with international standards such as FDA regulations for food applications and ASTM standards for general use. In regions like Africa and South America, sourcing from local suppliers can mitigate import costs and compliance issues.
How Does Polyurethane Compare for Silicon Molds?
Polyurethane is another popular choice, known for its exceptional abrasion resistance and mechanical strength. It can handle temperatures up to 80°C, making it suitable for applications requiring higher durability.
Pros & Cons: The key advantage of polyurethane is its versatility; it can be formulated for varying hardness levels, allowing for tailored applications. However, it may not perform well in extreme temperatures or in prolonged exposure to UV light, leading to degradation over time. The manufacturing complexity can also increase costs.
Impact on Application: Polyurethane molds are ideal for casting resins, concrete, and other materials, making them popular in construction and decorative industries.
Considerations for International Buyers: Buyers should verify compliance with local standards such as DIN in Europe or JIS in Asia. Understanding the local market’s material preferences can also aid in selecting the right formulation.
What Role Does Epoxy Play in Silicon Mold Production?
Epoxy is often used for its strong adhesion and chemical resistance, making it suitable for molds that require high precision and durability. Epoxy can withstand temperatures up to 120°C, which is beneficial for certain industrial applications.
Pros & Cons: The main advantage of epoxy is its ability to produce highly detailed molds with excellent surface finishes. However, it can be more brittle than silicone or polyurethane, leading to potential cracking under stress. The curing process can also be time-consuming, affecting production timelines.
Impact on Application: Epoxy molds are particularly effective in applications where chemical resistance is crucial, such as in the automotive and aerospace industries.
Considerations for International Buyers: Compliance with international standards for chemical safety and environmental impact is essential. Buyers in the Middle East and Europe should be aware of REACH regulations when sourcing epoxy materials.
What are the Benefits of Using Thermoplastic Elastomers (TPE) for Molds?
Thermoplastic Elastomers (TPE) combine the properties of rubber and plastic, offering flexibility and ease of processing. TPE can withstand temperatures up to 100°C and is known for its excellent elasticity.
Pros & Cons: TPE provides a cost-effective solution for high-volume production due to its ease of processing and recyclability. However, it may not offer the same level of detail as silicone or epoxy molds, which could limit its use in intricate designs.
Impact on Application: TPE is suitable for applications in consumer goods and automotive parts, where flexibility and durability are required.
Considerations for International Buyers: Understanding local market demands and preferences for TPE formulations can enhance product acceptance. Buyers should also consider the environmental impact and recyclability of TPE in their sourcing decisions.
Summary Table of Material Selection for Silicon Molds
Material | Typical Use Case for silicon mold | Key Advantage | Key Disadvantage/Limitation | Relative Cost (Low/Med/High) |
---|---|---|---|---|
Silicone Rubber | Food processing, pharmaceuticals | Excellent flexibility and detail | High cost, limited high-pressure use | High |
Polyurethane | Construction, decorative applications | High abrasion resistance | Temperature sensitivity, costly | Medium |
Epoxy | Automotive, aerospace | Strong adhesion, precise detail | Brittle, lengthy curing process | Medium |
Thermoplastic Elastomers | Consumer goods, automotive parts | Cost-effective, recyclable | Limited detail compared to others | Low |
This guide provides a comprehensive overview of material options for silicon molds, empowering international B2B buyers to make informed decisions based on performance, cost, and compliance considerations.
In-depth Look: Manufacturing Processes and Quality Assurance for silicon mold
What Are the Main Stages of Silicon Mold Manufacturing?
Manufacturing silicon molds involves a series of well-defined stages that ensure high-quality output. Understanding these stages is crucial for B2B buyers looking to source reliable molds for their production needs.
Material Preparation: What Are the Key Steps?
The first step in the manufacturing process is material preparation. High-quality silicone rubber is selected based on the specific requirements of the mold, including temperature resistance, flexibility, and durability. This material is then mixed with additives such as curing agents and pigments to achieve the desired properties. B2B buyers should inquire about the sourcing of raw materials and whether suppliers conduct thorough quality checks on incoming materials.
Forming: How Is the Mold Shape Created?
The forming stage involves the actual shaping of the silicone into the desired mold configuration. This is typically done through techniques such as:
- Injection Molding: Silicone material is injected into a pre-made mold, allowing for precise shapes and high production rates.
- Compression Molding: The silicone is placed in a heated mold and compressed, suitable for larger parts with less complexity.
- Liquid Silicone Rubber (LSR) Molding: This involves using a two-part liquid silicone that cures quickly, ideal for intricate designs.
B2B buyers should assess the technology used by suppliers to ensure it meets their production needs. Advanced forming techniques can lead to better precision and shorter lead times.
Assembly: What Are the Key Considerations?
In some cases, molds require assembly, especially if they consist of multiple parts. This stage involves aligning and bonding different components to create a complete mold. Buyers should ensure that suppliers use appropriate adhesives and methods that comply with industry standards to guarantee durability and functionality.
Finishing: What Quality Enhancements Are Made?
The finishing process enhances the mold’s surface quality and overall performance. This may include:
- Surface Treatment: Techniques like polishing or texturing to achieve specific finishes.
- Coating: Application of protective coatings to improve longevity and reduce sticking during the casting process.
Buyers should inquire about the finishing processes employed by suppliers to ensure they align with their product requirements.
What Are the International Standards for Quality Assurance in Silicon Mold Manufacturing?
Quality assurance is critical in the silicon mold manufacturing process to ensure that products meet international standards and customer expectations. Understanding these standards can help B2B buyers make informed decisions.
How Do ISO Standards Apply to Silicon Mold Manufacturing?
ISO 9001 is one of the most recognized international standards for quality management systems (QMS). It emphasizes continuous improvement and customer satisfaction. B2B buyers should look for suppliers certified under ISO 9001, as this indicates a commitment to quality processes and adherence to best practices.
What Are Industry-Specific Certifications to Consider?
In addition to general ISO standards, certain industries may require specific certifications such as:
- CE Marking: Indicates conformity with health, safety, and environmental protection standards for products sold within the European Economic Area.
- API Certification: Relevant for suppliers producing molds for the oil and gas industry, ensuring compliance with industry-specific quality standards.
Buyers should verify that their suppliers hold the necessary certifications to ensure compliance with regulatory requirements in their target markets.
How Is Quality Control (QC) Implemented in Silicon Mold Production?
Quality control (QC) involves systematic processes to monitor and maintain the quality of the manufacturing process. Understanding these checkpoints can help buyers assess supplier capabilities.
What Are the Key QC Checkpoints in the Manufacturing Process?
-
Incoming Quality Control (IQC): This checkpoint involves inspecting raw materials upon arrival to ensure they meet specified standards. Buyers should inquire about the criteria used for IQC and the supplier’s process for rejecting substandard materials.
-
In-Process Quality Control (IPQC): During production, periodic checks are performed to monitor the manufacturing process. This may include measuring mold dimensions and checking for defects. Buyers should ask suppliers about their IPQC methods and how they handle deviations from quality standards.
-
Final Quality Control (FQC): Once the molds are completed, FQC ensures that the finished products meet all specifications and standards. This may involve functional testing and visual inspections. Buyers should request FQC reports to verify the quality of the molds before shipment.
What Common Testing Methods Are Used to Ensure Mold Quality?
Various testing methods are employed to verify the quality and performance of silicon molds. B2B buyers should be familiar with these methods to assess supplier capabilities effectively.
- Tensile Testing: Measures the strength and elasticity of the silicone material.
- Compression Set Testing: Assesses how well the mold returns to its original shape after being compressed.
- Thermal Stability Testing: Evaluates the mold’s ability to withstand high temperatures without degradation.
Buyers should request detailed testing reports from suppliers to ensure that the molds meet their specific application requirements.
How Can B2B Buyers Verify Supplier Quality Control Processes?
Verifying a supplier’s quality control processes is essential for ensuring consistent product quality. Here are some actionable steps that B2B buyers can take:
What Should Buyers Look for in Supplier Audits?
Buyers should conduct regular audits of their suppliers to assess their quality management systems. This includes reviewing documentation related to manufacturing processes, quality control measures, and employee training programs. Auditing helps ensure that suppliers comply with international standards and internal policies.
How Can Buyers Use Reports and Third-Party Inspections?
Requesting quality assurance reports from suppliers can provide insights into their QC processes and results. Additionally, hiring third-party inspection services can provide an unbiased evaluation of the supplier’s production and quality management practices.
What Are the QC and Certification Nuances for International B2B Buyers?
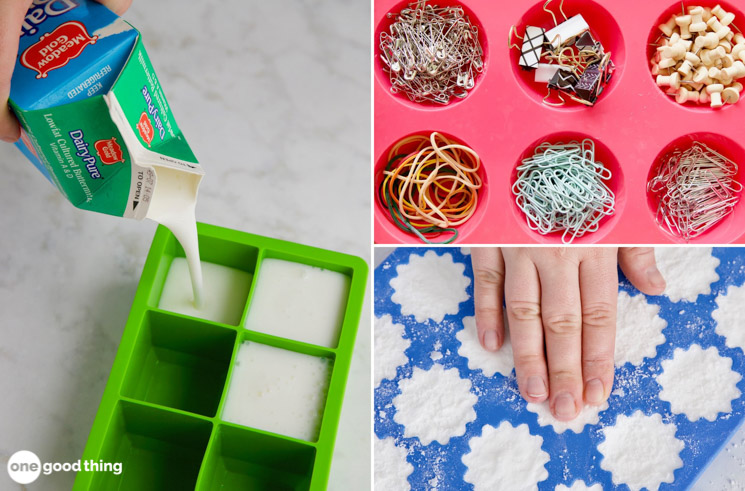
A stock image related to silicon mold.
B2B buyers, particularly from diverse regions such as Africa, South America, the Middle East, and Europe, must navigate various regulatory landscapes. Understanding these nuances is vital for successful procurement.
-
Cultural Differences: Different regions may have varying expectations regarding quality and compliance. Buyers should engage in open communication with suppliers to clarify standards and requirements.
-
Regulatory Compliance: Ensure that the supplier is familiar with the regulations in your target market. This might include specific certifications or compliance with local laws.
By understanding the manufacturing processes and quality assurance practices involved in silicon mold production, B2B buyers can make informed decisions, ensuring that they source reliable products that meet their business needs.
Practical Sourcing Guide: A Step-by-Step Checklist for ‘silicon mold’
Introduction
Sourcing silicone molds can be a complex process, especially for international B2B buyers from diverse regions such as Africa, South America, the Middle East, and Europe. This guide provides a practical checklist designed to simplify your procurement journey, ensuring that you find high-quality suppliers and products that meet your specific needs.
Step 1: Define Your Technical Specifications
Clearly outline the technical specifications of the silicone molds you require. This includes dimensions, material hardness, and any specific design features necessary for your applications. Having precise specifications helps suppliers understand your needs and ensures that the molds produced meet your operational requirements.
Step 2: Research Potential Suppliers
Conduct thorough research to identify potential suppliers specializing in silicone molds. Look for manufacturers with a proven track record in your industry. Utilize online platforms, trade directories, and industry associations to compile a list of suppliers who have experience with international shipping and compliance with regional regulations.
Step 3: Verify Supplier Certifications
Before proceeding, ensure that your chosen suppliers hold relevant certifications. Certifications such as ISO 9001 demonstrate a commitment to quality management systems. Additionally, inquire about compliance with industry-specific standards that may be applicable in your region, as this can greatly influence product reliability and safety.
Step 4: Request Samples for Evaluation
Always request samples of the silicone molds before placing a bulk order. This step allows you to assess the quality and functionality of the molds firsthand. Evaluate aspects such as durability, flexibility, and the precision of the mold design to ensure they align with your production needs.
Step 5: Compare Pricing and Payment Terms
Obtain detailed quotes from multiple suppliers and compare pricing structures. Look beyond the base cost; consider shipping fees, import duties, and payment terms. Negotiating favorable payment terms can improve your cash flow and reduce financial risk in international transactions.
Step 6: Assess Production Capacity and Lead Times
Inquire about the supplier’s production capacity and lead times. Understanding their ability to meet your demand is crucial, particularly if you are operating under tight deadlines. Ask for specific timelines for sample delivery, production runs, and shipping to ensure that they can accommodate your project schedules.
Step 7: Establish Communication Protocols
Effective communication is vital for successful sourcing. Establish clear protocols for updates, feedback, and issue resolution. Specify preferred communication channels (email, phone, or messaging apps) and agree on regular check-ins to keep the project on track and address any potential concerns promptly.
By following these steps, B2B buyers can navigate the sourcing process for silicone molds more effectively, ensuring they make informed decisions that align with their operational objectives and regional requirements.
Comprehensive Cost and Pricing Analysis for silicon mold Sourcing
What Are the Key Cost Components in Silicon Mold Sourcing?
Understanding the cost structure of silicon mold sourcing is crucial for international B2B buyers. The primary cost components include:
- Materials: The type of silicon used significantly impacts cost. High-quality silicon with superior durability and heat resistance may command a higher price but can lead to longer-lasting products.
- Labor: Labor costs vary by region. In areas with higher wage standards, such as parts of Europe, manufacturing costs may increase. However, regions like Africa or South America might offer competitive labor rates, potentially reducing overall expenses.
- Manufacturing Overhead: This encompasses utilities, facility maintenance, and administrative costs. Suppliers with optimized operations can offer more competitive pricing.
- Tooling: Initial setup for molds requires investment in tooling, which can be a major upfront cost. Understanding tooling costs can help buyers negotiate better terms, particularly for larger orders.
- Quality Control (QC): Implementing robust QC processes ensures product reliability but adds to costs. Buyers should weigh the importance of certifications and testing against potential price increases.
- Logistics: Shipping and handling costs must be factored into the total expense. Consideration of Incoterms is vital, as they define the responsibilities of buyers and sellers in shipping arrangements.
- Margin: Supplier margins can vary based on market competition and demand. Understanding typical margins in different regions can aid in negotiating better pricing.
How Do Pricing Influencers Affect Silicon Mold Costs?
Several factors influence the pricing of silicon molds that B2B buyers should consider:
- Volume/MOQ: Larger orders often lead to discounts due to economies of scale. Buyers should assess their needs and negotiate minimum order quantities (MOQs) to maximize savings.
- Specifications and Customization: Custom molds tailored to specific requirements may incur higher costs. Buyers should evaluate whether customization is essential or if standard molds can meet their needs.
- Materials: The choice of silicon grade and additives can affect price. Buyers should seek suppliers who offer various options to balance quality and cost.
- Quality and Certifications: Molds that meet international quality standards or have certifications (e.g., ISO, FDA) might be priced higher. However, these certifications can reduce liability and enhance product credibility.
- Supplier Factors: The reputation and location of the supplier can influence pricing. Established suppliers with a track record of reliability may charge more but can offer peace of mind.
- Incoterms: Understanding the shipping terms (e.g., FOB, CIF) will help buyers anticipate additional costs associated with freight and insurance.
What Tips Can Help Buyers Negotiate Better Prices for Silicon Molds?
International B2B buyers can utilize several strategies to optimize sourcing costs:
- Engage in Negotiation: Don’t hesitate to negotiate pricing based on order size and loyalty. Suppliers may be willing to offer discounts for long-term contracts or repeat business.
- Focus on Cost-Efficiency: Analyze the Total Cost of Ownership (TCO) rather than just the upfront price. Consider factors like durability, maintenance, and potential downtimes to make informed decisions.
- Understand Pricing Nuances: Familiarize yourself with regional pricing trends and practices. For instance, African and South American suppliers may have different cost structures compared to European counterparts, affecting negotiations.
- Build Relationships: Establishing strong relationships with suppliers can lead to better pricing and service. Regular communication can foster trust and result in favorable terms over time.
Disclaimer on Indicative Prices
Prices for silicon molds can vary significantly based on numerous factors including market conditions, specific supplier capabilities, and individual project requirements. It is advisable for buyers to conduct thorough research and obtain multiple quotes to ensure they are getting the best value for their investment.
Alternatives Analysis: Comparing silicon mold With Other Solutions
Understanding the Importance of Evaluating Alternatives in Silicon Mold Solutions
When considering silicon molds for production processes, it’s essential to evaluate various alternatives that can meet specific business needs. Different manufacturing requirements, budget constraints, and desired performance characteristics can influence the decision-making process. This section provides a comprehensive comparison between silicon molds and other viable alternatives, including polyurethane molds and 3D printing technologies.
Comparison Table: Silicon Mold vs. Alternatives
Comparison Aspect | Silicon Mold | Polyurethane Mold | 3D Printing |
---|---|---|---|
Performance | High precision, flexibility | Good detail, less flexible | Variable precision, complex shapes |
Cost | Moderate initial investment | Lower initial cost, higher long-term | High initial cost, variable ongoing |
Ease of Implementation | Requires skilled labor | Easier to use, less expertise | Requires software and technical skills |
Maintenance | Low maintenance | Moderate maintenance | Low maintenance, but equipment-dependent |
Best Use Case | High-volume production | Short runs, prototypes | Custom parts, complex geometries |
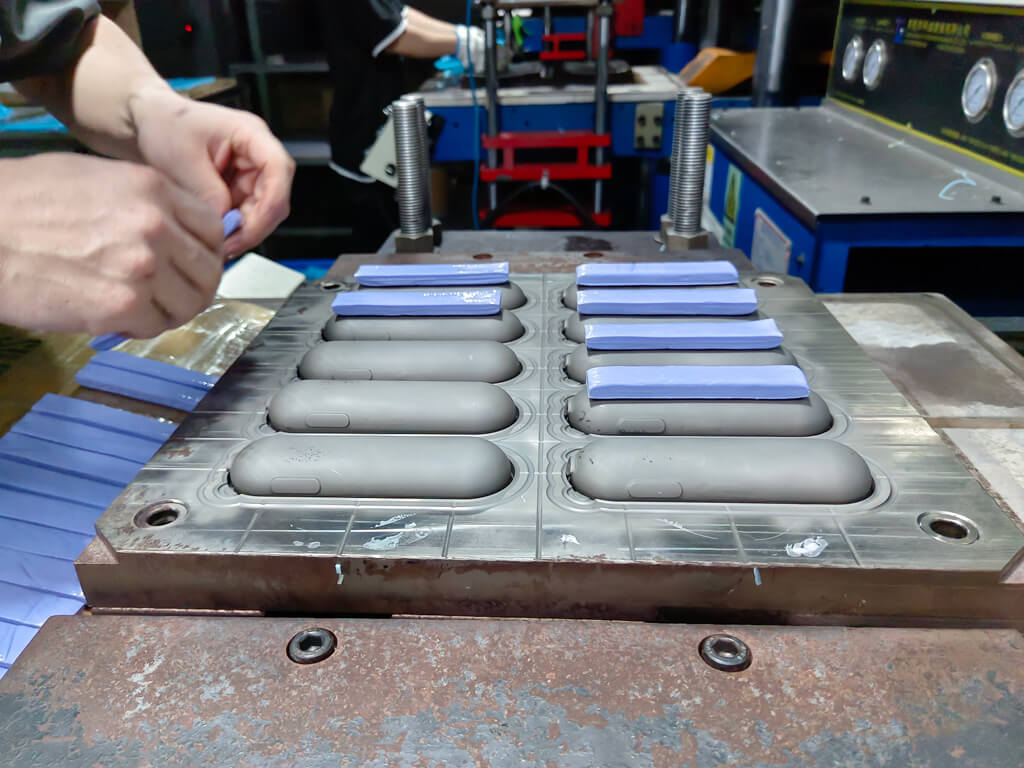
A stock image related to silicon mold.
What Are the Pros and Cons of Polyurethane Molds?
Polyurethane molds are often used as an alternative to silicon molds due to their lower initial cost and versatility in producing various shapes and sizes. They provide good detail and surface finish but may lack the flexibility required for more intricate designs. The ease of implementation makes them suitable for businesses with less skilled labor. However, they may require more maintenance over time, especially if used for longer production runs. Businesses looking for short-run production or prototyping can benefit significantly from polyurethane molds.
How Does 3D Printing Compare to Silicon Molds?
3D printing technology offers a unique approach to manufacturing, allowing for the creation of complex geometries that traditional molds may struggle with. While the initial setup costs can be high, especially for industrial-grade 3D printers, the ability to produce custom parts on demand can reduce waste and lead times. However, 3D printing may present challenges in terms of precision and surface finish, depending on the technology used. Companies that prioritize customization and rapid prototyping might find 3D printing a compelling alternative, while those focusing on high-volume production may prefer the reliability of silicon molds.
Making the Right Choice: How Can B2B Buyers Select the Best Solution?
When evaluating the best solution for your manufacturing needs, consider the specific requirements of your production process. If high-volume production and precision are priorities, silicon molds may be the best choice despite their moderate cost. For short runs or prototypes, polyurethane molds offer a cost-effective and flexible alternative. If customization and complex geometries are essential, 3D printing could be the right fit, provided your budget allows for the initial investment. Conducting a thorough analysis of your needs, budget, and available resources will empower you to make an informed decision that aligns with your business objectives.
Essential Technical Properties and Trade Terminology for silicon mold
What Are the Key Technical Properties of Silicon Molds?
Understanding the essential technical properties of silicon molds is crucial for B2B buyers, especially when sourcing products for manufacturing processes. Here are the key specifications to consider:
1. Material Grade
Silicon molds are typically made from high-grade silicone rubber, which can vary in quality. The material grade affects the mold’s durability, flexibility, and resistance to temperature fluctuations. Buyers should look for silicone with a Shore A hardness rating between 20 and 80, as this range provides a good balance between flexibility and strength, making it suitable for various applications.
2. Tolerance Levels
Tolerance refers to the permissible limit of variation in mold dimensions. Precise tolerance levels are critical in ensuring that the final product meets specifications, particularly in industries like automotive and aerospace. Standard tolerances for silicon molds usually range from ±0.1 mm to ±0.5 mm. Understanding these tolerances helps buyers ensure compatibility with their production processes.
3. Temperature Resistance
Silicone molds are valued for their ability to withstand extreme temperatures. The temperature resistance of silicone can range from -60°C to +200°C, depending on the formulation. Buyers should assess the thermal stability of the silicone mold to ensure it meets the demands of their specific applications, especially when dealing with high-temperature materials.
4. Chemical Resistance
Different applications may involve exposure to various chemicals, making chemical resistance a vital property. Silicon molds generally exhibit good resistance to many oils, solvents, and other chemicals. Buyers need to consider the specific chemicals involved in their processes to select a mold that will not degrade or lose functionality over time.
5. Lifespan and Reusability
The lifespan of a silicon mold can significantly impact overall production costs. High-quality molds can be reused multiple times without significant degradation, which is particularly beneficial for companies looking to maximize their return on investment. Buyers should inquire about the expected number of uses for a given mold to better evaluate its cost-effectiveness.
What Are Common Trade Terms in the Silicon Mold Industry?
Familiarity with trade terminology is essential for navigating the procurement process effectively. Here are several important terms that B2B buyers should know:
1. OEM (Original Equipment Manufacturer)
An OEM refers to a company that produces parts or equipment that may be marketed by another manufacturer. In the silicon mold industry, buyers often deal directly with OEMs to ensure product quality and specifications meet their needs. Understanding this term helps buyers identify reliable suppliers who can provide tailored solutions.
2. MOQ (Minimum Order Quantity)
MOQ is the smallest amount of product a supplier is willing to sell. This term is crucial for budget-conscious buyers, as it can impact overall project costs. Suppliers may impose MOQs based on production costs, and understanding these limits allows buyers to plan their procurement strategies accordingly.
3. RFQ (Request for Quotation)
An RFQ is a formal document sent to suppliers requesting pricing and other pertinent information for a product or service. This is an essential step in the sourcing process, enabling buyers to compare options and negotiate terms effectively. Crafting a detailed RFQ ensures that suppliers provide accurate and relevant quotes.
4. Incoterms (International Commercial Terms)
Incoterms define the responsibilities of buyers and sellers in international trade. They specify who is responsible for shipping, insurance, and tariffs, which can vary significantly depending on the terms chosen. Familiarity with these terms can help buyers mitigate risks associated with international shipping and ensure smooth transactions.
5. Lead Time
Lead time refers to the time taken from placing an order to the delivery of the product. Understanding lead times is critical for B2B buyers, especially in industries where timing can significantly impact production schedules. Buyers should always inquire about lead times to plan their inventory and production processes effectively.
By grasping these technical properties and trade terms, international B2B buyers can make more informed decisions when sourcing silicon molds, ensuring their projects run smoothly and efficiently.
Navigating Market Dynamics and Sourcing Trends in the silicon mold Sector
What Are the Key Trends Driving the Silicon Mold Market?
The silicon mold market is currently experiencing significant growth, driven by various global factors. The demand for precision-engineered products in industries such as automotive, aerospace, and consumer electronics is propelling the need for high-quality silicon molds. This trend is particularly pronounced in emerging markets across Africa and South America, where industrialization is accelerating. International B2B buyers should note that advancements in manufacturing technologies, such as 3D printing and CNC machining, are enhancing production efficiencies, allowing for quicker turnaround times and cost savings.
Furthermore, the rise of smart manufacturing and Industry 4.0 is influencing sourcing strategies. Companies are increasingly looking for suppliers who can integrate digital technologies into their processes, offering better traceability and quality assurance. In regions like the Middle East and Europe, this trend aligns with a broader push towards digital transformation, making it crucial for buyers to partner with suppliers who are not only technologically adept but also responsive to market changes.
How Is Sustainability Shaping Sourcing Practices in the Silicon Mold Sector?
Sustainability is becoming a cornerstone of sourcing strategies within the silicon mold sector. As global concerns about environmental impacts intensify, buyers are prioritizing suppliers who demonstrate a commitment to sustainable practices. This includes the use of eco-friendly materials and processes that minimize waste. For instance, sourcing from manufacturers that utilize recycled silicon or offer “green” certifications can enhance a company’s reputation and appeal to environmentally conscious consumers.
Moreover, ethical sourcing is critical in today’s market landscape. Buyers should conduct thorough due diligence on their suppliers to ensure they adhere to ethical labor practices and environmental regulations. This not only mitigates risks associated with supply chain disruptions but also aligns with the growing consumer demand for transparency and corporate social responsibility. By integrating sustainability and ethical considerations into sourcing decisions, international B2B buyers can position themselves as leaders in responsible business practices.
What Is the Evolution of the Silicon Mold Industry?
The silicon mold industry has evolved significantly over the past few decades, driven by technological advancements and changing market needs. Initially, silicon molds were primarily used for simple applications in the electronics and toy industries. However, as manufacturing processes improved, the applications for silicon molds expanded to more complex and demanding sectors such as automotive and aerospace.
The introduction of advanced materials and manufacturing techniques has enabled the production of molds that are not only more durable but also capable of achieving finer detail and precision. This evolution has opened new avenues for international B2B buyers, allowing them to access a wider range of products tailored to specific industry requirements. As the market continues to innovate, staying informed about these developments will be crucial for making strategic sourcing decisions.
Frequently Asked Questions (FAQs) for B2B Buyers of silicon mold
-
How do I choose the right supplier for silicon molds?
Choosing the right supplier for silicon molds involves several critical factors. Start by researching suppliers’ reputations through online reviews and industry forums. Verify their certifications and quality assurance processes, as compliance with international standards is essential. Request samples to assess the quality of their products firsthand. Additionally, consider their production capacity, lead times, and responsiveness to inquiries. Building a strong relationship with suppliers based on trust and communication can lead to better terms and reliability in the long run. -
What are the typical minimum order quantities (MOQ) for silicon molds?
Minimum order quantities for silicon molds can vary widely depending on the supplier and the complexity of the molds. Many manufacturers may set an MOQ ranging from 50 to 500 units. However, some suppliers might be willing to accommodate smaller orders, particularly for custom designs. It’s important to discuss your specific needs with potential suppliers and negotiate MOQs that align with your business requirements. Always consider the implications of MOQ on your inventory management and cash flow. -
What payment terms should I expect when purchasing silicon molds internationally?
Payment terms for international purchases of silicon molds typically vary by supplier and country. Common terms include 30% upfront payment with the balance due upon shipment or delivery. Some suppliers may offer letter of credit or escrow services for larger transactions to mitigate risks. Always clarify payment methods accepted, such as bank transfers, PayPal, or credit cards. Understanding currency exchange rates and potential additional fees can also help in budgeting for your purchase effectively. -
What quality assurance practices should I look for in a silicon mold supplier?
A reliable silicon mold supplier should have robust quality assurance practices in place. Look for suppliers that adhere to international quality standards, such as ISO certifications. Inquire about their testing processes, including material inspections and mold performance evaluations. Request documentation of past quality audits and customer feedback. Establishing clear quality expectations and regular communication can help ensure that the molds meet your specifications and reduce the risk of defects. -
How can I customize my silicon molds for specific applications?
Customizing silicon molds for specific applications typically involves discussing your requirements with the supplier. Provide detailed specifications, including dimensions, shapes, and intended use cases. Many suppliers offer design assistance and can create prototypes for your approval before mass production. Be prepared to discuss lead times and potential costs associated with customizations. Effective communication and collaboration with your supplier are crucial for achieving the desired results. -
What logistics considerations should I be aware of when sourcing silicon molds internationally?
When sourcing silicon molds internationally, logistics play a crucial role in the overall process. Consider shipping methods, lead times, and costs, which can vary significantly based on the supplier’s location and your destination. Understand customs regulations and potential tariffs that may apply to your shipment. It’s advisable to work with freight forwarders who can navigate these complexities and ensure timely delivery. Additionally, clarify the supplier’s responsibilities regarding packaging and insurance during transit. -
What are the common applications of silicon molds in various industries?
Silicon molds are widely used across several industries, including automotive, aerospace, medical, and consumer goods. They are ideal for creating intricate designs and complex shapes due to their flexibility and heat resistance. Common applications include manufacturing components, prototypes, and artistic products. Understanding the specific requirements of your industry can help you select the right type of silicon mold and supplier who specializes in that area. -
How do I handle potential disputes with my silicon mold supplier?
Handling disputes with a silicon mold supplier requires a proactive approach. Start by maintaining clear communication and documenting all agreements, specifications, and communications. If issues arise, address them directly and professionally with the supplier to seek a resolution. If necessary, refer to the contract terms regarding dispute resolution, which may include mediation or arbitration. Establishing a good relationship from the outset can often prevent conflicts and facilitate smoother negotiations when issues occur.
Important Disclaimer & Terms of Use
⚠️ Important Disclaimer
The information provided in this guide, including content regarding manufacturers, technical specifications, and market analysis, is for informational and educational purposes only. It does not constitute professional procurement advice, financial advice, or legal advice.
While we have made every effort to ensure the accuracy and timeliness of the information, we are not responsible for any errors, omissions, or outdated information. Market conditions, company details, and technical standards are subject to change.
B2B buyers must conduct their own independent and thorough due diligence before making any purchasing decisions. This includes contacting suppliers directly, verifying certifications, requesting samples, and seeking professional consultation. The risk of relying on any information in this guide is borne solely by the reader.
Strategic Sourcing Conclusion and Outlook for silicon mold
As the demand for silicon molds continues to rise across various industries, international B2B buyers must prioritize strategic sourcing to maximize efficiency and cost-effectiveness. Key takeaways emphasize the importance of evaluating suppliers based on their capabilities, production processes, and compliance with quality standards. By establishing long-term partnerships with reputable manufacturers, businesses can ensure a steady supply of high-quality silicon molds tailored to specific needs.
What are the benefits of investing in strategic sourcing for silicon molds? Strategic sourcing not only optimizes procurement costs but also mitigates risks associated with supply chain disruptions. Furthermore, leveraging regional suppliers from Africa, South America, the Middle East, and Europe can enhance responsiveness to market demands while fostering local economic growth.
Looking ahead, the silicon mold market is poised for innovation, driven by advancements in manufacturing technologies and materials. International B2B buyers are encouraged to stay abreast of these trends and consider diversifying their supplier base to remain competitive. By taking proactive steps in their sourcing strategy, businesses can unlock new opportunities and drive sustainable growth in a rapidly evolving landscape.